СПРАВОЧНЫЕ ДАННЫЕ О ШЛАКАХ, ШТЕЙНАХ И МЕТАЛЛАХ
Что мы хотим узнать сегодня узнать? Сколько весит 1 куб шлака угольного остатка, шлакового щебня, вес 1 м3 шлака угольного, черного шлакового наполнителя ?
Нет проблем, можно узнать количество килограмм или количество тонн сразу, масса (вес одного кубометра остатка от сгорания угля, вес одного куба шлака угля, шламового отвала, вес одного кубического метра золы угля, вес 1 м3 черного шлака угля) указаны в таблице 1. Если кому-то интересно, можно пробежать глазами небольшой текст ниже, прочесть некоторые пояснения. Как измеряется нужное нам количество вещества, материала, жидкости или газа? За исключением тех случаев, когда можно свести расчет нужного количества к подсчету товара, изделий, элементов в штуках (поштучный подсчет), нам проще всего определить нужное количество исходя из объема и веса (массы). В бытовом отношении самой привычной единицей измерения объема для нас является 1 литр. Однако, количество литров, пригодное для бытовых расчетов, не всегда применимый способ определения объема для хозяйственной деятельности. Кроме того, литры в нашей стране так и не стали общепринятой «производственной» и торговой единицей измерения объема. Один кубический метр или в сокращенном варианте – один куб, оказался достаточно удобной и популярной для практического использования единицей объема. Практически все вещества, жидкости, материалы и даже газы мы привыкли измерять в кубометрах. Это действительно удобно. Ведь их стоимость, цены, расценки, нормы расхода, тарифы, договора на поставку почти всегда привязаны к кубическим метрам (кубам), гораздо реже к литрам. Не менее важным для практической деятельности оказывается знание не только объема, но и веса (массы) вещества занимающего этот объем: в данном случае речь идет о том сколько весит 1 куб золы угольной (1 кубометр остатка от сгорания угля, 1 метр кубический золы, 1 м3 шлака угля). Знание массы и объема, дают нам довольно полное представление о количестве. Посетители сайта, спрашивая сколько весит 1 куб остатка от сгорания угля, черного шлакового наполнителя, углешлама, часто указывают конкретные единицы массы, в которых им хотелось бы узнать ответ на вопрос.
Как мы заметили, чаще всего хотят узнать вес 1 куба золы угольной ( 1 кубометра шлакового щебня буроугольного, 1 кубического метра остатка от сгорания угля, 1 м3 золы угля) в килограммах (кг) или в тоннах (тн). По сути, нужны кг/м3 или тн/м3. Это тесно связанные единицы определяющие количество шламового отвала. В принципе возможен довольно простой самостоятельный пересчет веса (массы) из тонн в килограммы и обратно: из килограммов в тонны. Однако, как показала практика, для большинства посетителей сайта более удобным вариантом было бы
сразу узнать сколько килограмм весит 1 куб (1 м3) шлака угольного остатка, углешлама или сколько тонн весит 1 куб (1 м3) шлака угольного, черного шлакового наполнителя
, без пересчета килограмм в тонны или обратно – количества тонн в килограммы на один метр кубический (один кубометр, один куб, один м3). Поэтому, в таблице 1 мы указали сколько весит 1 куб ( 1 кубометр остатка от сгорания угля, шламового отвала, 1 метр кубический шлакового щебня) в килограммах (кг) и в тоннах (тн). Выбирайте тот столбик таблицы, который вам нужен самостоятельно. Кстати, когда мы спрашиваем сколько весит 1 куб ( 1 м3) шлакового щебня, углешлама мы подразумеваем количество килограмм или количество тонн. Однако, с физической точки зрения нас интересует плотность или удельный вес. Масса единицы объема или количество вещества помещающегося в единице объема – это объемная плотность или удельный вес. В данном случае
объемная плотность золы угольной и удельный вес шлака угольного.
Насыпная плотность углешлама и удельный угольного остатка, шлама буроугольного вес в физике принято измерять не в кг/м3 или в тн/м3, а в граммах на кубический сантиметр: гр/см3. Поэтому в таблице 1 удельный вес золы угольной и плотность шлака (синонимы) указаны в граммах на кубический сантиметр (гр/см3)
Плотность шлака
В процессе выплавки стали непрерывно взаимодействуют две жидкие фазы — металл и шлак. Однако после получения заданного химического состава металла необходимо обеспечить максимальное удаление шлаковой фазы из металла. Подобное отделение основано преимущественно на разности плотности металла и шлака. Плотность твердого железа равна 7,86 г/см 3 , твердой стали в зависимости от ее состава 6,8-8,2 г/см 3 , а плотность жидкой стали колеблется в пределах 6,5—7 г/см 3 .
Плотность шлака зависит от плотности составляющих его компонентов. Ниже приведены значения плотности некоторых оксидов при комнатной температуре.
Плотность шлака прежде всего определяется содержанием тяжелых оксидов: FeO, Fe2O3 и MnO. Зависимость плотности твердого шлака от суммы указанных оксидов приведена на рисунке 4, из которого видно, что даже при высоком содержании тяжелых оксидов плотность шлака примерно в два раза меньше плотности металла.
Граншлак
Каталог статей > Сыпучие материаллы > Граншлак
Перейти к прайс листу на граншлак
Производство шлаков и виды шлаков
Шлаком называют неметаллический многокомпонентный расплав, который покрывает поверхность жидких металлов при металлургических процессах, таких как: плавка исходного сырья, обработка расплавленного промежуточного продукта и рафинирование жидкого расплава. При окончании металлургических процессов шлак имеет затвердевшее камневидное или стекловидное состояние, называемое еще «сплавом оксидов переменного состава». При металлургическом производстве шлаки появляются в сопровождении процесса восстановления руды и извлечения из неё так называемой пустой породы, флюсов и коксовой золы при их химическом взаимодействии с карбонатными породами. Основными компонентами шлака являются: кислотные оксиды SiO2 и TiO2, основные оксиды CaO, FeO, MgO, нейтральные оксиды Al2O3, ZnO. Тем самым в зависимости от количественного преобладания основных или нейтральных оксидов шлаки разделяются на основные и кислые.
Подразделение шлаков в зависимости от вида производства
Шлаки черной металлургии:
— Доменные которые могут быть не гранулированные, гранулированные, пемзы.
Шлаки цветной металлургии
— Медеплавильные, никелевые, алюминиевые (вторичные), прочие.
Шлаки химической промышленности
— Электротермофосновные
Шлаки черной металлургии: доменные и сталелитейные
В строительстве преобладает использование доменных шлаков получаемых при производстве чугуна.
Шлак доменный негранулированный получают путем воздушного охлаждения шлака с последующим его дроблением и грохочением. Использование такого шлака преимущественно наблюдается в дорожном строительстве в качестве замены щебня, как дополнительный наполнитель в асфальтобетон и бетон, в сельском хозяйстве для раскисления почв, а также в качестве железосодержащего материала для вторичной переплавки в доменных печах. Шлак доменный негранулированный гидравлическими свойствами не обладает.
Шлак доменный гранулированный получается при выплавке чугуна путем резкого охлаждения водой на гранустановке. Используется гранулированный доменный шлак преимущественно в качестве активной минеральной добавки в цемент.
Шлаковой пемзой называют литой кислый шлак. Для его создания необходим специфический режим охлаждения. Вяжущими свойства отсутствуют. Используют как утеплитель (подсыпка под перекрытия пола первого этажа домов), звукоизоляционный материал, необходим при производстве легких бетонов и изделий из них (шлакоблоки).
Рис1. Шлак черной металлургии
Основной полезной характеристикой доменного шлака является его основность, тоемть сопротивление измельчению, реакционная способность, химический состав и его стабильность. Плотность шлаков составляет 2,7-3 г/см3 (2700кг/м3-3000кг/м3), насыпная плотность – 1,3-1,5 г/см3 (1300кг/м3-1500кг/м3). Гидравлические свойства доменного граншлака определяются по величине коэффициента качества (К).
В зависимости от коэффициента качества и химического состава гранулированные доменные шлаки разделяются на три сорта:
% Al2O3 (не менее) | % MgO (не более) | % TiO2 (не более) | % MnO (не более) | К | |
I сорт | 8,0 | 15,0 | 4,0 | 2,0 | 1,65 |
II сорт | 7,5 | 15,0 | 4,0 | 3,0 | 1,45 |
III сорт | до 7,2 | 15,0 | 4,0 | 4,0 | 1,20 |
Шлаки цветной металлургии
В строительстве и производстве строительных материалов имеют интерес цветные металлургические шлаки от производства меди и никеля. Отвальные медеплавильные шлаки имеют черный цвет, которые не подвергаются распаду. Плотность таких шлаков шлаков составляет 3300-3800 кг/м3, водопоглощение 0,1-0,6%, предел прочности при сжатии 120-300 МПа.
Никелевые шлаки имеют столь же высокие показатели физико-механических свойств, как и медные. Относятся к кислым по химическому составу. Имеют стекловидную фазу, но не смотря на это практически не обладают гидравлической активностью. Применение шлаков цветной металлургии в настоящий момент не велико, находят место применения в производстве цемента и при получении минеральной ваты и литых изделий.
Рис2. Шлак цветной металлургии
Электротермофосфорные гранулированные шлаки
Являются отходами при производстве фосфора методом электротермической возгонки. Получаются быстрым охлаждением силикатного расплава, образующегося в электропечах при плавке шихты из фосфорной руды, кварцита и кокса.
Рис3. Электротермофосфорный гранулированный шлак
Граншлак
Цена: 14560. 0 руб за 20т
Граншлак
Цена: 8400.0 руб за 10т.
Граншлак
Цена: 12320.0 руб за 15т.
Граншлак в мешке (50кг)
Цена: 90.0 руб за мешок
Граншлак
Цена: 5000.0 руб за 5т
Поверхностное и межфазное натяжение
Между частицами жидкости действуют силы сцепления. Частицы внутренних слоев жидкости окружены со всех сторон такими же частицами, и, следовательно, силы притяжения, действующие на данную частицу с разных сторон, взаимно уравновешиваются (рис. 5, а). В поверхностном слое действуют силы притяжения со стороны внутренних слоев жидкости и со стороны среды, граничащей с поверхностным слоем, которые в общем случае не уравновешиваются.
В связи с отмеченными особенностями поверхностных частиц для увеличения поверхности раздела между фазами требуется затратить некоторую работу. Эту работу, отнесенную к 1 см 2 поверхности, называют поверхностным натяжением и обозначают σ. Размерность σ — МДж/м 2 (эрг/см 2 ). Иногда поверхностное натяжение выражают как силу на единицу длины (дин/см). Численные значения поверхностного натяжения, выраженного в эрг/см 2 и дин/см, совпадают. Если рассматриваются поверхностные явления на границе раздела двух конденсированных фаз, например шлак — металл, то пользуются термином «межфазное натяжение».
Примеси, присутствующие в жидкости, по-разному ведут себя на поверхностях раздела. Если сила связи частиц примеси с частицами растворителя невелика, то частицы примеси выталкиваются на поверхность, уменьшают силы сцепления между поверхностными частицами и уменьшают таким образом поверхностное (межфазное) натяжение (рис. 5, б). Такие примеси называются поверхностно активными веществами и их концентрация в поверхностном слое будет больше, чем в объеме. Вместе с тем, если частицы примеси имеют с частицами растворителя большие силы взаимодействия, чем частицы растворителя между собой, то концентрация этих примесей в поверхностном слое будет меньше, чем в объеме (рис. 5, в). Такие вещества называются поверхностно инактивными.
Поверхностное натяжение жидкого основного и кислого шлаков на границе с газовой фазой составляет соответственно 500—600 и 300—400 эрг/см 2 (0,5—0,6 и 0,3—0,4 мДж/см 2 ). При увеличении в основном шлаке таких оксидов, как MnO, SiO2, P2O5, TiO2, V2O5, FeO, Cr2O3, значение σ уменьшается, т. е. эти оксиды являются по отношению к основному шлаку поверхностно активными. Увеличение содержания CaO, MgO и Al2O3 в основном шлаке приводит к повышению поверхностного натяжения, в данном случае эти оксиды являются поверхностно инактивными.
Межфазное натяжение на границе железо — шлак из CaO, Al2O3 и SiO2 составляет 1—1,1 мДж/см 2 (1000— 1100 эрг/см 2 ). Увеличение содержания CaO и Al2O3 в шлаке повышает межфазное натяжение, а FeO, MnO и Na2O являются и в этом случае поверхностно активными оксидами и снижают межфазное натяжение.
Металлургические шлаки
Металлургическая промышленность ежегодно дает около 50 млн. т. шлаков, а в отвалах их скопилось около 500 млн. т. Это главным образом доменные шлаки, а также мартеновские, ваграночные и др. Так, при выплавке чугуна на каждую тонну основной продукции получают 0,5 … 1 т шлака. Если оценить выход не по массе, а по объему, то шлака получается в 2… 3 раза больше, чем чугуна. Поэтому называть шлаки отходами можно лишь условно. В сущности это не отходы, а тоже ценный, попутно добытый продукт.
Недостаточное использование металлургических шлаков приводит не только к недоизвлечению прибыли, но и к удорожанию основной металлургической продукции за счет больших затрат на вывозку шлаков и содержание огромных отвалов.
Химический состав металлургических шлаков разнообразен. Доменные шлаки состоят в основном из оксидов, а также содержат примеси железа, магния, марганца, серы.
Частично доменные шлаки используют в цементной промышленности. Некоторая их часть применяется для получения шлаковаты, литых изделий и т. д. При этом значительный объем шлаков текущего выхода, а также запасы отвальных шлаков могут быть использованы для получения заполнителей. Щебень из доменного шлака
. Щебень для бетона можно получить из доменных шлаков текущего выхода или дроблением и сортировкой шлаков из старых отвалов.
Шлаки в отвалах неоднородны по составу и свойствам. В зависимости от условий остывания степень их кристаллизации различна. Неодинакова их пористость и прочность. В связи с этим целесообразна выборочная разработка старых отвалов или обогащение шлака после дробления на щебень.
В зависимости от химического и минералогического составов некоторые шлаки могут подвергаться распаду. Иногда кусковой лак самопроизвольно превращается в порошок. Исследованиями установлено, что основной причиной возможного разрушения являются образование в шлаке неустойчивых силикатов кальция, претерпевающих затем объемные деформации. Такое разрушение называют силикатным распадом.
Чтобы проверить стойкость шлакового щебня к силикатному распаду, пробу испытывают пропариванием над кипящей водой или в автоклаве в среде насыщенного водяного пара при давлении. Таким образом процессы распада силиката кальция нестабильной формы интенсифицируются и проявится в измельчении зерен. Шлаковый щебень считается стойким к силикатному распаду, если в результате испытания потеря массе данной фракции, т. е. отсев мелочи на сите, не превышает 5%.
Предварительная оценка пригодности доменного шлака для производства щебня производится по данным химического анализа.
Устойчивую структуру имеют, как правило, кислые шлаки.
Для стабилизации в шлаки, склонные к распаду, вводят некоторые добавки, растворяющиеся в расплаве и направляющие кристаллизацию в желаемом направлении с образованием устойчивых минералов.
По показателю дробимости при сжатии (раздавливании) в цилиндре щебень из доменного шлака подразделяется на четыре марки: Др45 — для бетона с пределом прочности ниже 20 МПа, Др35 — для бетона с пределом прочности 20 … 30 МПа, Др25 — для бетона с пределом прочности 30 … 40 МПа, Др15 — для бетона с пределом прочности 40 МПа и выше.
Таким образом, на щебне из доменного шлака можно получать высокопрочные бетоны для разнообразных конструкций. Шлаковый щебень в районах сосредоточения металлургической промышленности обходится значительно дешевле других заполнителей, в частности щебня из природного камня, его применение дает большой экономический эффект.
Однако содержащаяся в шлаке сера может вызвать коррозию стальной арматуры. В связи с этим использование шлакового щебня в производстве железобетонных конструкций с предварительно напряженной арматурой должно быть обосновано специальными исследованиями, а если содержание серы больше 2,5%, то требуется специальное исследование бетонов для всех видов конструкций. Насыпная плотность шлакового щебня для тяжелого бетона должна быть не менее 1000 кг/м3. Это плотный и прочный заполнитель черного или темно-серого цвета, шероховатый в изломе. Некоторые виды шлаков, так называемые «газистые», вспучиваются пузырьками выделяющихся газов и застывают в виде пористого материала. Например, пористые отвальные шлаки имеют плотность зерен 0,4… 1,6 г/см3 и предел прочности соответственно 2,5 …40 МПа (пропорциональный квадрату плотности). Насыпная плотность щебня из таких шлаков составляет; 800 кг/м3 и менее, поэтому он может быть применен для легких бетонов. В основном же пористые заполнители для легких бетонов из металлургических шлаков получают искусственной поризацией. Для получения высокопрочного плотного щебня из доменного шлака часто требуется их дегазация. Это может быть достигнуто введением в шлаковый расплав специальных добавок, а также, как показали П. А. Кривилев и другие, путем его виброобработки.
Отвальные пористые шлаки в значительной степени неоднородны.
Гранулированный шлак
. При обработке огненно-жидких металлургических шлаков водой происходит резкое охлаждение (шлакового расплава и его грануляция — дробление на отдельные мелкие зерна. Структура зерен аморфная, стеклообразная.
По зерновому составу гранулированный шлак соответствует крупному песку: размер зерен преимущественно 0,6 … 5 мм, причем примерно 50% (по массе) составляют зерна крупнее 2,5 мм. Нередко имеются более крупные зерна (до 10 мм).
Насыпная плотность гранулированного шлака колеблется в широких пределах — 600 … 1200 кг/м3. Это связано с тем, что в зависимости от свойств шлакового расплава и технологии грануляции зерна гранулированного шлака могут получаться плотными или пористыми. Пустотность гранулированных шлаков велика — до 60 … 70%.
Гранулированные доменные шлаки потребляются главным образом в производстве шлакопоргландцемента, по в значительном объеме они используются также в качестве заполнителя для бетонов.
Температура плавления
Главными компонентами сталеплавильного шлака являются CaO, FeO, SiO2, Al2O3. Температура плавления этих оксидов приведена ниже:
Температура плавления двойных и вообще многокомпонентных оксидных систем, как правило, ниже температуры плавления самого тугоплавкого из оксидов. Например, в расплаве, состоящем из CaO, Al2O3 и SiO2, имеется большая область с температурой плавления 2 ), или пуаз (П, размерность г·см -1 ·с -1 ). Величину, обратную вязкости (Ф = 1/η), называют жидкотекучестью.
Вязкость жидкости зависит от ее природы, состава и температуры. Для сравнения ниже приведена вязкость некоторых веществ:
СПРАВОЧНЫЕ ДАННЫЕ О ШЛАКАХ, ШТЕЙНАХ И МЕТАЛЛАХ
⇐ ПредыдущаяСтр 4 из 42Следующая ⇒
СВОЙСТВА ШЛАКОВ
На металлургических заводах получают главным образом три вида шлаков: рудной плавки, конверторные, рафинировочные. Шлаки рудной плавки выводятся из цикла металлургического производства в отвал, используются для производства шлаковых изделий (вата, шлаковатные теплоизоляционные плиты, шлакоцементные блоки, литые блоки), иногда направляются на доработку для извлечения металлов-спутников, например цинка, свинца, редких металлов, фьюмингованием, вельцеванием или электротермией. Конверторные и рафинировочные шлаки направляют в оборот или на специальную переработку для извлечения основного металла и его спутников. Ниже приведены основные данные о шлаках, в основном рудной плавки.
Состав шлаков
. На 70–90% шлаки состоят из закиси железа (FeO), магнетита (Fe3O4), кремнезема (SiO2) и окиси кальция (СаО). Почти всегда в шлаках присутствует до 8–12% А12О3. Для шлаков свинцовоплавильных заводов характерно высокое содержание окиси цинка (до 30%, обычно 5–25%). Для шлаков никелевых заводов типично повышенное содержание (до 25%) окиси магния (часто 8–20%). Содержание основных окислов в шлаках колеблется в следующих пределах: 18–58% SiO2, 18–55% FeO, 4–30% CaO. Шлаки другого состава встречаются значительно реже. В шлаках обычно, содержится 1–2% S (в шлаках свинцовоплавильных заводов до 4%).
Шлаки представляют собой ионные взаимные растворы (расплавы) силикатов и окислов. Они, как правило, не имеют определенной точки плавления, а расплавляются постепенно в интервале 100–300 0С с длительным периодом размягчения. Первые признаки появления жидкости (частичного расплавления) наблюдаются у самых легкоплавких шлаков при 1000–1050 0С, полное расплавление наступает при 1150–1300 0С. Частично расплавленная (гетерогенная) система имеет повышенную вязкость.
Плавкость шлаков
. Наиболее легкоплавки железистые шлаки (около 50% FeO), содержащие 4–8% СаО и столько же ZnO и А12О3. Эти шлаки легко вытекают из печей при 1150–1200 0С. Кремнеземистые (52–56% SiO2) шлаки становятся жидкотекучими при 1450–1550 0С. Известны случаи работы на высококремнистых шлаках при 1300–1350 0С, но с неудовлетворительными технологическими показателями (в основном низкая производительность). Тугоплавки и магнезиальные (15–25% MgO) шлаки. Их полное расплавление происходит примерно при 1350–1400 0С.
Плотность шлаков
. Основные составляющие шлак окислы имеют следующие плотности: FeO и ZnO от 5,6 до 5,8, MgO и СаО от 3,2 до 3,4, SiO2 2,6, А12О3 –4,0. При нагревании до расплавления плотность FeO снижается до 4,4, SiO2–до 2,2. Плотность MgO и СаО почти не меняется. Для ориентировочных расчетов плотность шлаков можно определить как средневзвешенную для смеси. Но вследствие образования в шлаке химических соединений этот способ расчета не дает точных результатов. Поэтому проф. Н.П. Диев предложил следующую эмпирическую, формулу:
d=(2,2SiO2+3,3СаО+5,2FeO+2,3A12O3)/100
Здесь под символами SiO2, FeO и др. подразумевается процентное содержание этих окислов в шлаке.
Плотность обычных жидких шлаков 2,8–3,4. При перегреве она снижается примерно на 0,2 на каждые 1000С.
Вязкость шлаков
. Вязкость измеряют в пуазах (П). Для лучшего представления об этой единице приведем вязкости часто встречающихся жидкостей при 200С: для воды 0,01; для серной кислоты 0,2; для масла растительного и нефти 1–3; для мазута 5–7 и т. д.
Наилучшие результаты по производительности печи и расходу топлива (электроэнергии) достигаются при работе со шлаками, вязкость которых составляет 5–30 П (железистые шлаки).
Шлаки с вязкостью менее 0,5–1,0 П встречаются редко. Можно работать на шлаках с вязкостью до 250–300 П (кремнистые), но при этом значительно ухудшаются технологические показатели. Видимо, не следует выбирать режимы работы, при которых получаются шлаки, с вязкостью более 70 П. Вязкость сильно зависит от температуры плавки и состава шлака. С повышением температуры до 1200–14000С вязкость изменяется в 10 и даже 100 раз. Резко изменяют вязкость при нагревании магнезиальные (15–25% MgO) шлаки. Наименее вязки железистые шлаки. При содержании 45–55% FeO и 20–30% SiO2 их вязкость равна при 1150–12000С 1–10 П. При снижении содержания FeO до 18–25% и повышении содержания SiO2 до 40–44% следует повышать температуру до 1300–13500С, чтобы получить шлак с вязкостью 10–20 П.
При содержании SiO2 около 55±3,0% шлаки при 13000С имеют вязкость 200–300 П. Нагрев таких шлаков до 1400–14500С (в электропечах) снижает вязкость до 10–70 П и допускает интенсивную работу. Если не предусмотрен нагрев шлака выше 1300–13250С, то не следует допускать повышения содержания в нем СаО > 22–24%, MgO>10%, А12О3>10%. При содержании в шлаке более 42–44% SiO2 следует обогащать дутье кислородом (шахтные и отражательные печи) или применять электроплавку. Без обогащения дутья кислородом производительность шахтных и отражательных печей заметно снижается.
Электропроводность шлаков
. Это свойство шлака приобрело большое значение в связи с развитием электротермии. От электропроводности шлака зависит режим работы электропечи. При электропроводном шлаке, печь рудной плавки работает на большой силе тока (40–50 кА) и сравнительно низком напряжении (250–400 В). Электроды заглублены в шлак на 400–500 мм. Если же шлак имеет низкую электропроводность, то напряжение должно составлять 500–700 В при силе тока 25–30 кА и заглублении электродов 600–700 мм. Второй режим предпочтительнее.
Для реальных шлаков электропроводность колеблется в пределах 0,05–5,0 Ом-1см-1.
Наблюдается значительная зависимость электропроводности от температуры. В интервале 1200–14000С она часто увеличивается в 4–5 раз. При 11000С электропроводность реальных шлаков тройной системы FeO–SiO2–СаО составляет примерно 100 Ом-1см-1.
Типичные шлаки этой системы, содержащие по 40% FeO и SiO2 и около 15% СаО, имеют при 13000С электропроводность около 2 Ом-1см-1.
Наиболее электропроводны при 13500С шлаки, содержащие 50–55% FeO (3–5 Ом-1см-1). Шлаки с высоким содержанием SiO2 (50–55%) имеют при 13500С электропроводность 0,2–0,3 Ом-1см-1, т. е. в 15–20 раз меньшую, чем железистые. Замена FeO (от 70 до 30%) на СаО (от 0 до 40%) при постоянном содержании SiO2 (30%) снижает электропроводность с 4–4,5 до 0,8–0,9 Ом-1см-1, т.е. примерно в 5 раз. Аналогично действует MgO. Замена FeO на ZnO мало сказывается на электропроводности. Глинозем снижает электропроводность шлака примерно как кремнезем. Поэтому допускается суммирование содержаний FeO и ZnO (считают за FeO) и SiO2 с А12О3 (считают за SiO2). Ниже приведена электропроводность заводских шлаков при 13500С, Ом-1см-1.
Свинцово плавильных заводов 2,5–3,0
Медеплавильных 0,5–0,8
Медно-никелевых комбинатов 0,25–0,32
Таким образом, наибольшее влияние на электропроводность оказывают FeO и SiO2.
Энтальпия шлаков
. Основные составляющие шлаков имеют в твердом состоянии следующие теплоемкости (средние в интервале температур 25–13000С), ккал/(кг•0С):
FeO | ZnO | СаО | MgO | SiO2 | Fe2SiО4 | Ca2SiO4 | А12О3 |
0,20 | 0,20 | 0,25 | 0,25 | 0,27 | 0,24 | 0,32 | 0,30 |
Теплота плавления реальных шлаков, по В. И. Бершаку, составляет 65 ккал/кг. Теплоемкость Fe2SiО4 можно вычислить как средневзвешенную между FeO и SiO2. Это указывает на слабую связь между ними. Напротив, теплоемкость Ca2SiO4, прочного химического соединения, значительно отличается от средневзвешенной. На этом основании можно приближенно определять энтальпию шлака как смеси окислов и соединения Ca2SiO4 (уточненный аддитивный способ).
Определим, например, теплоемкость шлака следующего состава: 43% SiO2, 7% ZnO, 5% Al2O3, 40% FeO, 5% СаО. Находим, что в этом шлаке содержится 172/112•5=7,66 кг Ca2SiО4 и условно 7+40=47 кг FeO. Свободного SiO2 в шлаке будет: 43–7,66+5,0=40,34 кг. Рассчитываем теплоемкость шлака:47•0,2=9,4; 5•0,3=1,5; 7,66•0,32=2,5; 40,34•0,27=10,9; итого получаем 24,3 ккал на 100 кг шлака на 10С.
Средняя теплоемкость шлака 0,243 ккал/кг•0С. Его энтальпия при 13000С составит 0,243•1300+65=314+65=379 ккал/кг,
где 65–теплота плавления.
Для конкретных образцов шлаков медеплавильных и свинцовоплавильных заводов В. И. Бершаком были найдены значения энтальпии при 13000С от 332 до 372 ккал/кг. В Гипроникеле при составлении теплового баланса для мощных электропечей принимали (по С.Е. Вайсбурду) теплоемкость конверторного шлака при 1230–13500С, шлака печей обеднения при 1200–13500С и шлака электропечного отвального при 1400–14500С равной 0,32 ккал/(кг-0С). В этом случае усредненная теплоемкость включает и теплоту плавления. Поэтому энтальпия, например, конверторного шлака до 12500С будет равна 1250•0,32=400 ккал/кг. Расчет этой же величины уточненным аддитивным способом дает 375 ккал/кг. В экспериментах X.К. Аветисяна получено около 400 ккал/кг. Таким образом, уточненный аддитивный способ дает цифры, близкие к данным В.И. Бершака. Если учесть, что потери тепла со шлаками составляют часто 30–40%, то различия в результатах разных авторов вносят в баланс ошибку, равную 1,5–2,0%. Поэтому при отсутствии более точных данных для составления тепловых балансов можно пользоваться и уточненным аддитивным методом.
Но полученные подсчетом данные следует сверять с экспериментальными данными С.Е. Вайсбурда, согласно которому теплосодержание шлаков, содержащих менее 20% MgO+СаО при 13000С, изменяется в пределах 360–420 ккал/кг (на 30–50 ккал/кг выше, чем у В.И. Бершака). Для шлаков с высоким содержанием MgO и СаО теплосодержание выше (440–460 ккал/кг). В заключение приводим типичный состав шлаков важнейших видов плавок цветной металлургии (таблица 12) и их теплоемкость (таблица 13).
Средняя теплоемкость рассчитана для интервала 25–15000С и включает теплоту плавления.
В пределах точности измерения Ср практически постоянно. Действительно, кроме особых случаев Ср=0,3±0,02 ккал/(кг-0С).
Таблица 12 Состав шлаков, %
Виды шлаков | Cu | Ni | Pb | ZnO | FeO | SiO2 | CaO | Al2O3 | MgO |
Отражательной плавки двух медеплавильных заводов | 0,4-0,6 0,4-0,6 | – – | – 0,3 | 4-8 1,0 | 36-42 26-28 | 36-40 42-45 | 3-7 8-10 | 3-6 7-9 | 0,5-1,0 0,5-1,0 |
Электроплавки: медноникелевого сырья | 0,07-0,1 | 0,08-0,11 | – | – | 24-34 | 42-47 | 3-4 | 6-10 | 8-20 |
медного сырья, железистое | 0,2-0,5 | – | 0,3-1,0 | 4-10 | 28-31 | 28-31 | 15-28 | 5-10 | 3-7 |
медного сырья, кремнистое | 0,3-0,6 | – | 0,5 | 1,0 | 12-24 | 47-52 | 12-18 | 5-9 | — |
Шахтная плавка окисленных никелевых руд | – | 0,15-0,20 | – | – | 18-24 | 42-48 | 16-18 | 6-8 | 8-10 |
Электроплавка окисленных никелевых руд | – | 0,08 | – | – | 8-10 | 48-52 | 20-24 | 6-8 | 6-8 |
Автогенная плавка медных концентратов | 1-2 | 0,1 | 0,1-0,3 | 0,5-4,0 | 51-57 | 26-32 | 1-4 | 3-6 | 1-2 |
Шахтной плавки свинцового агломерата | 0,5-1,0 | – | 1,5-2,5 | 15-25 | 28-34 | 20-24 | 10-16 | 3-7 | 1-2 |
Таблица 13 Средняя теплоемкость шлаков ккал/(кг 0С)
Состав шлака, % (по массе) | CP | Состав шлака, % (по массе) | CP | ||||||||||
SiO2 | FeO | CaO | MgO | Al2O3 | Fe2O3 | SiO2 | FeO | CaO | MgO | Al2O3 | Fe2O3 | ||
23,3 | 55,1 | 0,8 | 1,5 | 4,5 | 8,6* | 0,318 | 44,1 | 21,6 | 3,7 | 19,7 | 6,7 | – | 0,306 |
30,6 | 56,3 | 2,0 | 3,5 | 3,7 | – | 0,324 | 47,5 | 19,0 | 11,5 | 10,0 | 10,0 | – | 0,282 |
34,1 | 36,6 | 6,6 | 11,5 | 8,7 | 2,4 | 0,314 | 60,7 | 13,8 | 3,0 | 14,4 | 6,1 | – | 0,306 |
36,7 | 31,4 | 3,1 | 15,9 | 10,2 | 2,1 | 0,323 | 28,0 | 14,4 | 16,8 | 24,8 | 6,6 | 3,2* | 0,346 |
39,5 | 30,8 | 4,4 | 11,6 | 13,0 | 0,6 | 0,298 | 28,0 | 17,6 | 16,8 | 24,8 | 6,6 | –** | 0,350 |
43,0 | 27,3 | 5,6 | 18,2 | 7,2 | – | 0,311 | 27,0 | 60,0 | 1,8 | 2,6 | 3,2 | – | 0,322 |
*- в железистых шлаках присутствовало 2-3% S, в кремнистых 0,5% S.
** — в шлаке было 5,2% Cr2O3.
СВ0ЙСТВА ШТЕЙНОВ
В настоящее время штейны получают на медеплавильных и никелевых заводах. На свинцовоплавильных заводах получают богатый медно-свинцовый штейн только на переделе рафинирования свинца. На никелевых заводах получают два вида штейнов: никелевые из окисленных руд и медно-никелевые из сульфидных руд. Составы приведены в таблице 14.
Таблица 14 Примерные составы штейнов, %
Штейн | Cu | Ni | S | Fe | Pb | Zn | O |
Медный | 20–50 | 0–0,5 | 24–26 | 20–50 | До 2 | До 6 | 2–6 |
Медно-никелевый | 8–12 | 8–12 | 26–28 | 43–49 | – | – | 4–6 |
Никелевый | 0,3–0,4 | 14–16 | 20–21 | 56–62 | – | – | 2–3 |
Свинцовый | 50–60 | – | 16–19 | 1–4 | 12–24 | 4–6 | 1–2 |
Содержание серы в медных штейнах при расчетах принимают постоянным и равным 25%, в медно-никелевых 27% S. Содержание кислорода в медных штейнах, по В.Я. Мостовичу, соответствует содержанию меди следующим образом (в скобках приведены данные Б.Л. Недвецкого и Л.Ш. Цемехмана для медно-никелевых штейнов по Cu+Ni), %:
Медь | ||||
Кислород | 6,4 (6,12) | 5,0 (4,65) | 3,2 (3,12) | 2,0 (1,54) |
Кислород в штейне связан с железом в форме магнетита. Для расчета рационального состава штейна принимают следующие основные соединения: Ni3S2, Cu2S, PbS, ZnS, FeS, Fe3O4. Свободные металлы содержатся в штейне в виде сплава железа (85–90%) и никеля. В нем может раствориться до 5% Сu.
Заводские штейны полностью расплавляются при 1230–12500С. Штейны с высоким содержанием сплава металлов, начинают выделять ферроникель при 12000С. Неметаллизированные штейны при этой температуре выделяют магнетит. Медные, никелевые и медно-никелевые штейны полностью затвердевают в зависимости от состава при 850–900, 680–800 и 580–6500С соответственно.
Плотность штейнов
зависит от их состава. Основные составляющие штейна имеют следующие плотности: Cu2S 5,8; FeS 4,6; Ni3S2 6,3; Fe3O4 5,0. Поскольку между образующими штейн веществами не происходит химических реакций, то плотность штейнов можно для ориентировки определять как средневзвешенную величину. При расплавлении плотность штейнов уменьшается на 7–9% и составляет 4,2–5,2.
Электропроводность штейнов
значительно (в 100 и даже 10000 раз) больше, чем у шлаков. Наибольшую электропроводность имеют никелевые и медно-никелевые штейны (около 3000 Ом-1см-1), наименьшую — богатые медные (около 300 Ом-1см-1). В расчетах сопротивления цепи шлак — штейн сопротивлением штейнового участка можно пренебречь. Опускать электроды руднотермической электропечи до штейна нельзя. Это равносильно короткому замыканию.
Энтальпию жидких (бедных) штейнов
в пределах содержания 20–30% Сu+Ni допустимо определять в интервале 1000–14000С по средней теплоемкости 0,24 ккал/(кг•0С). Для штейнов, содержащих 40–50% металлов, эту величину следует уменьшить до 0,2 ккал/(кг•0С).
Вязкость штейнов
в жидком состоянии близка к вязкости воды. Это значит, что при их большой плотности они могут легко затекать в зазоры футеровки и, разрушать ее, что приводит к аварийным ситуациям.
Штейны являются коллектором
благородных и драгоценных металлов. В 1 т штейна может раствориться несколько десятков килограммов серебра, золота и платиноидов. Поэтому на практике, когда их содержание измеряется граммами, их извлечение в штейн достигает 97–99%.
Штейны магнитны
. Это объясняется присутствием в них магнетита. Поскольку в чистом штейне весь кислород связан с железом в виде Fe3O4, то можно подсчитать, что в бедных штейнах (18–27% Сu) растворяется 25–18% Fe3O4.
⇐ Предыдущая4Следующая ⇒
Рекомендуемые страницы:
Воспользуйтесь поиском по сайту:
Шлаки в металлургии
Металлургические шлаки
Силикатные материалы, получаемые при выплавке из руд металлов, называются металлическими шлаками. Они обладают разными свойствами, в зависимости от процесса их получения, химического состава руды и других факторов. Эти искусственные силикаты состоят из оксидов железа, алюминия, кремния, магния, кальция, серы, марганца и др. В зависимости от процентного соотношения этих окислов, скорости и условий остывания шлаков, они могут получать свойства вулканической пемзы или твёрдого гранита, а также рассыпаться в порошок. Их цвета бывают подобными горным породам: белые, жёлтые, чёрные, зелёные, серые, розовые, серебристые, сиреневые, перламутровые и др. Они могут быть разной плотности, пористости, тяжёлыми или лёгкими. Их удельный вес близок к природным камням. По химическому составу бывают основные, кислые, нейтральные.
Шлаки чёрной металлургии
• Доменные – получают при выплавке чугуна. Представляют собой расплавы силикатные или алюмосиликатные. Из-за низкой плотности (в 2 раза меньше, чем у чугуна) они образуются сверху над расплавленным слоем чугуна и периодически удаляются через летку. Возможность его использования зависит от химического состава и способа выхода из домны. Он может при охлаждении получить свойства плотного камня или постепенно рассыпаться в порошок. Плотный материал используется в качестве щебня, стоимость которого значительно меньше натурального, а свойства не уступают. Для проверки пригодности доменных шлаков в производство щебня проводится специальный контроль его качества.
• Сталеплавильные – побочный продукт при любом способе получения стали в открытых агрегатах. Состоит из нелетучих различных оксидов с меньшей плотностью, чем сталь, которые собираются на поверхности расплава. Их источники: продукты, полученные при окислении примесей, содержащихся в чугуне и ломе, добавочные окислители и материалы, внесённые загрязнения (миксерный шлак, песок) и др. Содержат большее количество оксидов железа (20 %) и марганца (10 %).
• Ваграночные образуются при плавке чугуна в вагранке из продуктов окисления чугуна, золы кокса, остатков в виде пригара формовочной смеси, флюса. Основные составляющие ваграночного шлака – оксиды (80 – 90 %). При таком способе производства получаются в большинстве кислые шлаки с выделением минералов (рудных, мелилитов, пироксенов, анортитов), алюмокремнезернистого стекла.
• Ферросплавные – получают в процессе производства ферросплавов. Различаются по добавленным к железу химическим элементам: хрому, марганцу, кремнию и др.
Шлаки цветной металлургии
Для них характерны: высокое содержание оксидов железа, пониженный состав оксидов магния и кальция. Свойства шлаков цветной металлургии зависят от их химического состава. Отличаются от шлаков чёрной металлургии большим удельным весом, разнообразием, дополнительным содержанием ценных редких металлов. Если при выплавке чёрных металлов выход шлаков на 1 т металла составляет 0,1 – 0,7 т, то в цветной металлургии при получении 1 т металла – 100 – 200 т шлаков.
Способы переработки и применение
Самый распространённый способ переработки – грануляция. Происходит путём охлаждения массы водой, воздухом, паром.
• Мокрый способ. Обработка вытекающего из доменной печи раскалённого шлака сильной струёй воды, подаваемой через специальные насадки. Шлак дробится под напором воды и отправляется в бункер до окончательного охлаждения. Его продувают воздухом, в результате чего он остывает и обезвоживается.
• Полусухой способ. Вытекающий из домны шлак попадает на лопасти вращающегося барабана. Небольшое количество воды, подаваемой в желоб, резко охлаждает и делает шлак твёрдым. Затем он попадает в барабан, где дробится и окончательно остывает, отлетая в сторону.
Гранулируются в основном доменные шлаки, которые в большинстве используются в цементной промышленности. Также в этой отрасли распространено применение шлаков ферросплавов, сталеплавильных, цветной металлургии. Из них производят обладающий высокой химической стойкостью цемент, который можно применять даже в агрессивных средах. Получают путём совместного помола металлургического шлака, гипса и извести. Шлаки также используют в качестве активных добавок к портландцементному клинкеру или вместо глины. В зависимости от взятых пропорций, получают обычный цемент или с повышенной стойкостью.
Шлакощелочные цементы получают при совместном помоле гранулированных шлаков, каустической или кальцинированной соды, жидкого стекла.
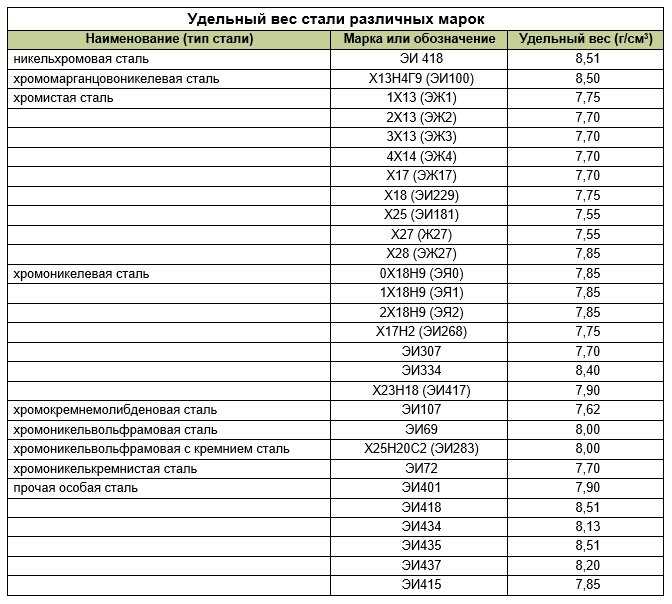
Широко используется в строительстве шлаковый щебень, который успешно заменяет натуральный. Получают его путём дробления отвальных шлаков или литья по специальной технологии. Перед применением он проверяется на устойчивость к распаду.
Материал прочный на истирание, выдерживает высокие и низкие сезонные температуры. Используется в качестве наполнителя для различных видов бетонов.
Для тяжёлых изделий из бетона крупным наполнителем служит отвальный или литой щебень, а для мелкого – гранулированный шлак. Для лёгких изделий предназначен щебень из шлаковой пемзы, которую получают путём вспучивания с применением минеральных газообразователей при быстром охлаждении шлаковой массы. Затем она дробится на фракционный щебень.
Этот материал нашёл широкое применение и в дорожном строительстве как надёжный и при этом дешёвый материал. Используется для подготовки оснований, а также в производстве шлаковых вяжущих для дорожных покрытий, приготовления асфальтобетона.
Способом шлакового литья получают плитки и камни для мощения тротуаров, изготовления бордюров, напольные покрытия для внутренних помещений, трубы, фасадные плиты и другие изделия. Они по многим качествам не уступают железобетонным и стальным аналогам. Их получают при разливе в формы расплавленных металлургических шлаков, поступаемых прямо из доменных печей. Такой производственный процесс очень экономичен – не требуются дополнительные ресурсы на расплавку сырья, его транспортировку и хранение. Технология изготовления проста, литьё таких изделий экономически выгоднее, чем изготовление искусственного камня, а механические свойства мало чем отличаются.
Из металлургических шлаков получаются превосходные материалы – шлакоситаллы. Они состоят из стекловидной аморфной массы и мельчайших стеклянных кристаллов. Бывают разных видов и цвета. Свойства зависят от исходного сырья и технологии изготовления. Процесс происходит в стекловаренной печи. Сырьём служат металлургические шлаки, песок и другие добавки. Шлакоситаллы отличаются высокой прочностью, близкой к чугуну и стали, но при этом они в 3 раза легче. Эти материалы легко обрабатываются и очень востребованы в строительстве. Они хорошо сверлятся, шлифуются, режутся. Широко используются для изготовления прочных изделий и в качестве отделочных материалов: труб, подшипников, оптических приборов, электроизоляторов, мелющих деталей механизмов, химического оборудования, облицовочных плит для фасадов и внутренних стен, напольных покрытий, подоконников, кровли, ограждений балконов и др.
Из металлургических шлаков изготавливают шлаковую вату, которая идёт на производство теплоизоляционных изделий. Из доменных шлаков получают около 80% минеральной ваты. Используются для этого также шлаки цветной металлургии, мартеновские, ваграночные. Выбирается сырьё с оптимальной вязкостью для получения минерального волокна методом вытягивания. В ванных печах или вагранках получают шлаковый расплав, который затем перерабатывается в волокно. Вату изготавливают 3-х типов: для плит повышенной жёсткости, для полусухого прессования изделий, для горячего прессования. На основе минваты получают различные изделия (плиты, цилиндры), где в качестве связующих применяют битумы, эмульсии, синтетические полимеры.
Шлак. Виды и применение. Плюсы и минусы. Свойства и особенности
Шлак – это вторичное сырье, отходы металлургической промышленности или зола от сжигания ископаемых горючих: углей всех видов, горючего сланца, жидкого топлива. В металлургии – то, что остаётся после выплавки металла из руды. Из шлаков чёрной металлургии получают заполнители для шлакобетонов, шлаковую пемзу, минеральные ваты. Отходы цветной металлургии делятся на передельные и отвальные шлаки.
Гранулированный, или граншлак, получается путём быстрого охлаждения водой горячего шлака в доменном или конвертерном процессе. Имея отличные вяжущие свойства, используется для производства цемента как активная минеральная добавка к нему.
Шлак нельзя рассматривать как простой наполнитель для приготовления бетонных растворов. Он, кроме этой своей функции, несёт ещё одну, которая с течением времени становится всё более важной – экологическую. Если учесть, сколько вредных примесей, от кислот и щелочей до канцерогенных соединений, есть в его составе, связывание его цементными смесями решает задачу его безопасной утилизации.
А при выплавке металла защищающая его шлаковая составляющая предохраняет расплав от воздействия продуктов горения.
Разновидности шлакового продукта
Прежде чем классифицировать отходы металлургического производства, необходимо уточнить важную деталь. В металлургии образуется два типа побочных продуктов, это непосредственно шлаки и золошлаковые отходы. Последний вид вторичного ресурса представляет собой смесь шлака и золы, формирующуюся при сжигании угля и торфа. О ценности этой разновидности отходов поговорим позже, рассмотрев вначале различные типы самого шлака. Классификация шлаковых отходы достаточно глубоко структурировано, хотя основных групп существует только две. Это шлаки черной и цветной металлургии.
Образование и использование золошлаковых отходов
Рассмотрим подробно процесс на примере теплоэлектростанций, где сырьем выступает измельченный уголь, смешиваемый с мазутом. Выбор основан тем фактом, что основной источник, формирующий золошлаковые отходы – ТЭЦ. Процесс горения сопровождается отделением микрочастиц золы, который уносятся тягой вместе с дымом. При этом, дым и пар образуются органикой, тогда как минеральные компоненты сгорающего топлива оседают в шлак и золу. Не улетевший, тяжелый зольный остаток, оседает на подтопки, сплавляясь между собой, что приводит к формирования отдельных кусков. Далее зола перемешивается со шлаком, образуя золошлаковые отходы, которые транспортируются на хранение в специальные отвалы. При этом, золошлаки сортируются отдельно от недожога – частиц несгоревшего угля.
Отходы тэц – золошлаковые отходы
Переработка золошлаковых отходов практически аналогична использованию самих шлаков. Сфера их реализации включает изготовление:
- различных видов бетона – тяжелого, ячеистого и силикатного;
- строительных составов;
- цементного клинкера;
- керамзита;
- керамического кирпича.
Также золошлаковые отходы применяются при прокладке земляного полотна автомагистралей, изоляционного материала на полигонах ТБО.
Видео – о проблемах накопления и утилизации золошлаковых отходов:
Свойства гранулированного шлака
Гранулированный шлак обладает гидравлическими вяжущими свойствами. Они проявляются при действии на тонко измельченный шлак возбудителей твердения щелочных (известь, цементный клинкер) или сульфатных (сернокислый кальций и др.). Эти свойства шлака используются для производства шлаковых цементов посредством совместного размола гранулированного шлака с возбудителями твердения. Таким образом получают известково-шлаковый, сульфатно-шлаковый цементы и шлакопорт-ландцемент. Кроме того, доменный шлак частично используют как сырье для изготовления обыкновенного цементного клинкера, шлакового кирпича, шлакобетона и других материалов.
Производство шлаковых цементов выгодно, так как оно основано на использовании очень дешевого сырья — отходов доменного производства — шлаков, получающихся в громадных количестав на металлгических заводах. Выход доменного шлака составляет в среднем 60% от веса выплавленного чугуна. Кроме того имеются огромные запасы старых отвальных шлаков, пользуемых для изготовления бетона в дорожном строительстве и др.
Как используется цемент ГГБС
Цемент GGBS может быть добавлен в бетон на бетонном заводе производителя вместе с портландцементом, заполнителями и водой. Нормальное соотношение заполнителей и воды к вяжущему материалу в смеси остается неизменным. GGBS используется как прямая замена портландцементу в соотношении один к одному по весу. Уровни замены GGBS варьируются от 30% до 85%. Обычно в большинстве случаев используется от 40 до 50%.
Использование GGBS в дополнение к портландцементу в бетоне в Европе описано в стандарте для бетона EN 206: 2013. Этот стандарт устанавливает две категории добавок к бетону наряду с обычным портландцементом: почти инертные добавки (Тип I) и пуццолановые или скрытые гидравлические добавки (Тип II). Цемент GGBS попадает в последнюю категорию. Поскольку цемент GGBS немного дешевле, чем портландцемент, бетон, изготовленный из цемента GGBS, будет иметь такую же цену, как и бетон, изготовленный из обычного портландцемента.
Используется частично согласно соотношению компонентов смеси.
Стойкие и распадающиеся материалы
Еще один классифицирующий критерий – условия остывания пустой породы. Различие в процессе охлаждения приводит к формированию следующих разновидностей шлаков:
- камневидные;
- гранулированные;
- стекловидные.
Следующий отличительный фактор, характеризующий шлаки металлургических комбинатов, – устойчивость. В этом отношении, альтернативу нераспадающемуся шлаку составляют такие виды распада:
- Силикатный. Характеризуется существенным приростом объема вещества, вследствие перехода кальциевого силиката из бета в гамма форму. Структура шлака покрывается трещинами и далее камень распадается в мучнистый порошок.
- Известковый. Процесс – следствие гидратации извести.
Этот тип распада преимущественно характерен мартеновским шлакам, проявляясь как самопроизвольное растрескивание твердого материала на куски.
- Железистый. Связан с избыточным содержанием неокисленного железа относительно окислов этого металла. Пороговая величина составляет 1.5% от FeO. Превышение указанного значения и воздействие влаги, инициируют реакцию перехода сульфида железа в его гидроксид, сопровождающуюся выделением сероводорода. В результате объем шлака возрастает до 38%, что и приводит к растрескиванию.
- Марганцевый. Активируется при нахождении шлака во влажной среде.
Переработка металлургических шлаков связано преимущественно с устойчивыми к распаду материалами. Их этого вторичного продукта изготавливается щебень, например.
Примечания
- Snellings, R .; Mertens G .; Элсен Дж. (2012). «Дополнительные вяжущие материалы». Обзоры по минералогии и геохимии
.
74
: 211–278. Bibcode:2012RvMG … 74..211S. Дои:10.2138 / RMG.абc
Аскарян, Махья; Фахретаха Аваль, Сиаваш; Джошагани, Алиреза (22 января 2022 г.). «Комплексное экспериментальное исследование характеристик порошка пемзы в самоуплотняющемся бетоне (SCC)».
Журнал устойчивых материалов на основе цемента
.
7
(6): 340–356. Дои:10.1080/21650373.2018.1511486.
Шлаки черной металлургии (доменные)
Сырье этого типа бывает 3 типов:
- Шлак доменный гранулированный, который получают при охлаждении чугуна во время его выплавки. Как правило, полученный граншлак используют в качестве заменителя более дорогостоящих минеральных добавок.
- Доменный шлак не гранулированного типа. Его добывают в процессе воздушного охлаждения отходов металлургии, их дробления и последующего грохочения. Полученный материал чаще всего применяется в качестве наполнителя для асфальтобетона при строительстве дорожных полотен. Кроме этого, не гранулированное сырье нашло применение в сельскохозяйственной области, где отходы используют для раскисления земли.
- Шлаковая пемза отличается тем, что она не обладает вяжущими свойствами. Поэтому это сырье чаще используют в качестве утеплителя, звукоизоляционного материала и при производстве шлакоблоков и прочих изделий из пористых и легких бетонов.
Если говорить о свойствах шлака доменного, то он отличается высоким сопротивлением к измельчению, реакционной способностью и стабильностью. По гидравлическим свойствам гранулированный шлак бывает трех сортов:
Читайте также: Что такое умный дом и как его собрать
- 1 сорт. В таком материале допускается содержание оксида алюминия не менее 8%, магния не больше 15%, титана не более 4% и марганца не больше 2%.
- 2 сорт. Оксид алюминия – 7,5%, магния – 15%, титана – 4%, марганца – 3%.
- 3 сорт. Оксид алюминия – не более 7,2%, магния – 15%, титана – 4%, марганца – 4%.
Производство
Доменный щебень, который также называют шлаковым щебнем, получают путем дробления отвального балластного материала, образующегося в ходе технологического процесса на предприятиях горной промышленности. Существует также литой щебень из балластного шлака, который получают путем переработки огненного жидкого расплава. Благодаря изготовлению щебня расширяется сфера применения побочной продукции горнодобывающих производств.
Для изготовления доменного щебня применяется отвальный шлак. Производят щебень из доменного шлака так:
- В процессе выплавки металла в доменных печах образуется балластный продукт, который в горячем состоянии заливается в специальные емкости и транспортируется в место для отвалов.
- Шлак затвердевает на открытом воздухе. Для ускорения процесса охлаждения шлака, его поливают технической водой. При резком охлаждении балластный материал трескается и распадается на глыбы различной фракции.
- Глыбы застившего отвального шлака дробят в специальных дробильных агрегатах, в результате чего получается измельчённый продукт со специфическими свойствами.
- Далее материал транспортируют на последующее дробление. Сортировка щебня по фракциям осуществляется на виброситах с различным диаметром отверстий.
Разновидности шлака
В качестве утеплителя для потолка допустимо использовать шлаки типов:
- топливного;
- каменноугольного;
- металлургического;
- доменного.
Каждый из этих типов шлака обладает своими особенностями, которые требуют более детального рассмотрения.
Топливный
Шлак топливного типа является сыпучим материалом, в основе которого лежат рыхлые силикатные массы. Образуется такой шлак в результате сгорания каменного угля во фракционном либо пылевом виде слоевым, либо камерным методом. Фракционный шлак обладает неоднородной структурой; в то время, как у пылевого шлака структура тонкопористая и однородная.
В единице объёма топливного шлака может содержать в себе до 40% золы, что указывает на относительно невысокую прочность материала. Помимо этого, в его состав могут входить не выгоревшие остатки топлива, из-за присутствия которых значительно ухудшаются теплоизоляционные свойства шлака.
Способы грануляции
Необходимо знать, что для грануляции отходов производства, то есть шлака, имеются несколько способов, а также устройств, осуществляющих эту операцию. В зависимости от того, какая влажность шлака получается в конечном итоге, и разделяют установки на типы. Бывают установки для мокрой, а также для полусухой грануляции.
Если осуществляется метод мокрой грануляции, то шлак, загружаемый в шлаковозные ковши в раскаленном виде, подается к железобетонным бассейнам, наполненным водой. После этого из ковшей он сливается в эти бассейны по специальным желобам. Небольшое преимущество метода заключается в том, что бассейны разделены на несколько секций. Это позволяет вести процесс охлаждения практически непрерывно. Когда в одну секцию сливается раскаленное вещество, из другой в это же время можно выгружать уже охлажденный доменный шлак. Для отгрузки сырья на заводах имеются грейферные краны, которые подают его сразу в железнодорожные вагоны открытого типа. После этого осуществляется доставка шлака либо на склад, либо сразу к потребителю.
Koranel® от Metallo
kuleuven.sim2.be
Также шлаки можно было бы назвать «рудным побочным продуктом». Почему? Потому что разница с рудами, полученными путем первичной экстракции, небольшая. Ключевым примером в этом контексте является бельгийская компания Metallo, которая эксплуатирует плазменную установку для восстановления цинка в шлаках и одновременного снижения содержания свинца в них с 1% до менее 300 частей на миллион (что соответствует жесткому законодательству).
С 2022 года Metallo производит такой шлак под торговой маркой Koranel®. Во время 14-й Глобальной конференции по шлакам в Аахене Koranel® был удостоен звания «Шлаковый продукт года». В настоящее время такой шлак применяется в основном для пескоструйной обработки, но исследования показывают, что их можно использовать и в других областях, в частности для цементных вяжущих и инженерных продуктов. Были проведены обширные испытания промышленных масштабов, которые открывают путь к широкому использованию шлаков цветной металлургии в строительной промышленности.
Шлаки цветной металлургии
Вторичное сырье этой категории пользуется меньшей популярностью ввиду дороговизны и трудоемкости его получения. В отличие от шлаков черной металлургии, цветное сырье обладает большим удельным весом и повышенным содержанием закиси железа, объем которого может доходить до 40%. Кроме этого, в состав таких материалов входят ценные и редкие металлы.
Иногда в строительной сфере применяют отходы цветной металлургии, которые образуются при выплавке никеля и меди. Медеплавное вторсырье отличается черным цветом и не распадается. При этом его плотность составляет от 3 300 до 3 800 кг/м3, а водопоглощение колеблется в пределах 0,1-0,6%.
Никелевое сырье обладает идентичными с медеплавными отходами показателями и свойствами.
Из шлаков такого типа редко изготавливаются строительные материалы, иногда их используют при производстве литых изделий или минваты. Намного чаще на производственную линию попадают доменные шлаки.
Топливные шлаки
Каменноугольные и угольные шлаки, которые также часто называют золошлаками, сегодня широко применяются в промышленном строительстве. Такое сырье отличается от доменного более низким содержанием CaO и повышенным содержанием FeO. При этом угольный шлак отличается повышенной щелочностью.
Золошлак – это шлак гранулированный, который отличается черной окраской. Такой цвет образуется из-за двухвалентного железа, которое содержится в составе сырья. Встречается шлак коричневого, белого, оливкового и зеленого цвета (в зависимости от объема окисла). Для получения песка шлакового сырье измельчается, в этом случае его цвет будет серым.
Золошлаки получают в процессе сжигания различного топлива, в зависимости от типа которого можно определить, сколько вторсырья в нем содержится:
- в буром угле содержание шлака составляет до 15%;
- в каменном – от 3 до 40%;
- в антраците – до 30%
- в горючих сланцах – от 50 до 80%;
- в дровах – порядка 0,5-1,5%;
- в мазуте – не более 0,2%.
Однако стоит учитывать, вреден ли угольный шлак. Дело в том, что в этом материале содержатся радиоактивные вещества, поэтому использовать его в качестве наполнителя для бетонных стен и при организации стяжки для жилых объектов не рекомендуется.
Архитектурные и инженерные преимущества
Эта секция нужны дополнительные цитаты для проверка . Пожалуйста помоги улучшить эту статью к добавление цитат в надежные источники. Материал, не полученный от источника, может быть оспорен и удален. |
Долговечность
Цемент GGBS обычно используется в бетоне для защиты как от сульфатного, так и от хлоридного воздействия. GGBS теперь эффективно заменил сульфатостойкий портландцемент (SRPC) на рынке сульфатостойкости из-за его превосходных характеристик и значительно более низкой стоимости по сравнению с SRPC. Большинство проектов в Доклендс Дублина, включая Спенсер Док, используют GGBS в подповерхностном бетоне для сульфатостойкости.
Объемное электрическое сопротивление — это метод испытаний, с помощью которого можно измерить удельное сопротивление бетонных образцов. (ASTM 1876-19) Более высокое электрическое сопротивление может указывать на более высокое сопротивление ионному переносу и, следовательно, более высокую долговечность. Заменяя до 50% GGBS в бетоне, исследователи показали, что долговечность может быть значительно увеличена.[3]
Для защиты от хлоридной атаки GGBS используется в бетоне при замене 50%. Примеры хлоридов имеют место в железобетоне в морской среде и на дорожных мостах, где бетон подвергается разбрызгиванию от соли для защиты от обледенения дорог. В большинстве NRA проекты в Ирландии GGBS теперь специализируется на конструкционном бетоне для опор мостов и абатменты для защиты от хлоридного нападения. Использование GGBS в таких случаях увеличит срок службы конструкции до 50%, если бы использовался только портландцемент, и исключает необходимость в более дорогих нержавеющая сталь армирование.
GGBS также обычно используется для ограничения повышения температуры при большой заливке бетона. Более постепенная гидратация цемента GGBS генерирует как более низкий пик, так и меньшее общее количество тепла, чем портландцемент. Это уменьшает температурные градиенты в бетоне, что предотвращает возникновение микротрещины который может ослабить бетон и снизить его прочность, и был использован для этой цели при строительстве Туннель Джека Линча в Пробка.
Внешность
В отличие от каменно-серого цвета бетона, сделанного из портландцемента, почти белый цвет цемента GGBS позволяет архитекторам без дополнительных затрат получить более светлый цвет для открытых фасадных бетонных поверхностей. Для достижения более светлого цвета покрытия GGBS обычно указывается с уровнями замещения от 50% до 70%, хотя могут использоваться уровни до 85%. Цемент GGBS также дает более гладкую поверхность без дефектов из-за тонкости частиц GGBS. Грязь не прилипает к бетону GGBS так же легко, как бетон, сделанный с портландцементом, что снижает затраты на обслуживание. Цемент GGBS предотвращает возникновение высол, окрашивание бетонных поверхностей карбонат кальция депозиты. Из-за его гораздо более низкого Лайм содержания и более низкой проницаемости, GGBS эффективен в предотвращении высолов при использовании на уровнях замещения от 50% до 60%.
Сила
Бетон, содержащий цемент GGBS, имеет более высокий предел прочности, чем бетон, сделанный на портландцементе. Он имеет более высокую долю повышающих силу гидраты силиката кальция (CSH), чем бетон, сделанный только с портландцементом, и меньшее содержание свободной извести, что не способствует прочности бетона. Бетон, изготовленный из GGBS, продолжает набирать прочность с течением времени, и было показано, что он удваивает свою 28-дневную прочность за период от 10 до 12 лет.[нужна цитата
]
Оптимальная дозировка измельченного гранулированного доменного шлака (GGBS) для замены в бетоне, как сообщается, составляет 20-30% по массе, чтобы обеспечить более высокую прочность на сжатие по сравнению с бетоном, изготовленным только из цемента.[3]
Устойчивость
Поскольку GGBS является побочным продуктом процесса производства стали, его использование в бетоне признано LEED и т. д., как повышение устойчивости проекта и, следовательно, добавление баллов к сертификации LEED. В этом отношении GGBS может также использоваться для надстройки в дополнение к случаям, когда бетон находится в контакте с хлоридами и сульфатами. Это при условии, что более медленное время схватывания при отливке надстройки оправдано.
Основные требования и критерии выбора
Выбирая шлак для утепления потолка, следует уделить внимание следующим характеристикам данного материала:
- влагопоглощение — чем ниже данный показатель у шлака, тем тоньше можно делать гидроизоляцию;
- звукоизоляция — позволяет обойтись без укладки дополнительных изолирующих слоёв, тем самым сократить не только финансовые затраты, но и нагрузку непосредственно на потолочное перекрытии;
- наличие токсичных компонентов в шлаке — чем таковых меньше, тем безопаснее материал;
- огнеупорность материала;
- содержание острых и гладких частичек во фракциях утепляющего материала, которые оказывают непосредственное влияние на то, насколько сложной будет укладка;
- температура спекания — эта характеристика покажет, при какой температуре шлак начнёт спекаться, из-за чего утратит свои утепляющие свойства;
- теплопроводность — наиболее важная характеристика материала, поскольку именно она определяет, насколько эффективным окажется утепление потолка шлаком;
- устойчивость к биологическому и химическому воздействию.
Соответственно, основные критерии рот выборе утепляющего материала — это гарантированный срок службы и допустимость использования того или иного типа шлака в определённых условиях.
Помимо этого, нельзя оставить без должного внимания диаметр шлаковых гранул, потому как этот показатель напрямую влияет на равномерность характеристики утепляющего слоя и простоту его укладки.
Основные производители утеплителя
Один из производителей шлаковой продукции является «Торговый дом УСК». Эта компания также и реализует утеплитель, выполняет доставку.
Алексинский керамзитовый завод занимается производством и продажей шлака, специализируется большей частью по продаже керамзита. Зачастую реализацией шлака занимаются угольные и металлургические компании, т. к. шлак является отходом производственных процессов и участием этих продуктов.
Таким образом, утепление шлаком имеет много преимуществ. Это недорогой вид утепления, доступный для осуществления своими руками. Материал представлен на рынке, покупка и доставка шлакового утеплителя налажена во многих регионах страны.
Обладая высокими показателями теплопроводности, утепление шлаковыми наполнителями сокращает расходы на строительство за счёт уменьшения основного материала при возведении стен. Этот доступный способ утепления помещений зарекомендовал себя на протяжении многих лет.
Сфера применения и свойства шлака
Говоря о том, что такое шлак, стоит сказать о сфере применения этого материала. Чаще всего в строительстве используется граншлак разного диаметра:
- Более крупные гранулы используются при изготовлении шлакоблоков, отличающихся износоустойчивостью, меньшим весом и повышенными показателями тепло- и влагоизоляции. Также крупный граншлак применяют при возведении фундамента (в качестве подложки), укреплении насыпей, обработке краев водоемов.
- Из шлака более мелкой фракции можно сделать добавку для бетона или асфальта.
- Пыль и самые мелкофракционные частицы применяют в качестве добавок при производстве тротуарной плитки и минваты.
- Крошка добавляется в строительные смеси для повышения прочностных характеристик составов. Также крошку применяют для заполнения пустот в стенах.
По цвету, вторичное сырье может быть самым разным, начиная от насыщенного черного, заканчивая белым цветом. Нередко встречаются материалы перламутрового или сиреневого оттенка.
Плотность шлака колеблется в зависимости от компонентов, входящих в его состав.
Оксид | Плотность, г/см3 |
Кальция | 3,4 |
Магния | 3,65 |
Кремния | 2,26 |
Железа | 5,7 |
Марганца | 5,4 |
Соответственно, если измерять этот показатель в «кубах», то эти значения будут колебаться от 800 до 3 200 кг на метр кубический.
Удельный вес сырья (то есть масса его вещества) составляет от 2,5 до 3,6 г/см3. Приблизительно такими же показателями отличаются природные породы камней. Однако стоит учитывать, что удельный вес шлака может отличаться в зависимости от вида сырья:
- У шлакобетона этот показатель составит порядка 2-2,4 т/м3.
- Удельный вес кускового шлака колеблется от 2,1 до 2,8 т/м3.
- Если используется вторсырье в виде щебенки, то вес материала будет самым наименьшим от 1,05 до 1,6 т/м3.
Кроме этого, свойства вторичного сырья определяются его типом. Сегодня в металлургии выделяют четыре основных вида шлака: черный, цветной, топливный и химический.
Определение и описание шлакопортландцемента
Американское общество по испытанию материалов (ASTM C125) определяет доменный шлак как «неметаллический продукт, состоящий в основном из силикатов и алюминатов кальция, полученный вместе с чугуном в доменной печи в виде расплава».
При производстве чугуна в доменную печь загружают железную руду, флюсовый камень (известняк и/или доломит) и кокс. Получаемая на выходе из печи продукция — расплавленный чугун и шлак. Шлак состоит в основном из кварца и оксидов алюминия (от железной руды) и оксидов кальция и магния (от флюсового камня). Из печи шлак выходит в расплавленном состоянии, причем температура расплава может превышать 1480?C (2700?F). Существует четыре основных способа обработки расплавленного шлака: охлаждение воздухом, быстрое охлаждение холодной водой (вспучивание шлака), дробление и помол. При каждом из данных методов обработки получается уникальный шлаковый материал, обладающий отличительными свойствами.
Химические свойства шлакопортландцемента
Основные составляющие доменного шлака — кварц, оксиды алюминия, кальция и магния, на которые приходится 95% всего состава шлака. Остальные 15% — марганец, соединения железа и серы и следовое количество других элементов. Однако, следует отметить, что основные оксиды, входящие в состав шлака не встречаются в свободной форме. В доменном шлаке, охлажденном воздухом, оксиды объединяются в различные силикаты и алюмосиликатные минералы, такие как мелилит, мервинит, волластонит и др., которые также существуют в виде природных пород. В дробленом и молотом шлаках, данные элементы присутствуют в виде стекла. Химический состав шлаков варьируется в очень узких пределах, поскольку все сырье, загружаемое в доменную печь, очень тщательно отбирается и смешивается.
Типичный химический состав доменного шлака, % | |
кварц(SiO2) | 32-42 |
оксид алюминия(A12O3) | 7-16 |
оксид кальция (CaO) | 32-45 |
окись магния (MgO) | 5-15 |
сера (S)* | 1-2 |
оксид железа (Fe203) | 1-1,5 |
оксид марганца (MnO) | 0,2-1,0 |
* в основном в виде сульфида кальция
Физические свойства шлакопортландцемента
Физические характеристики шлака, такие как вес, размер частиц, структурные свойства и т.д. различаются в зависимости от метода обработки расплавленного шлака. Соответственно, конечное применение обработанного шлака также различается в зависимости от метода обработки.
В последнее время в России и других странах большое внимание уделяется проблеме использования вторичных ресурсов. Одним из наиболее перспективных направлений утилизации промышленных отходов является использование их в производстве строительных материалов.
Металлургия занимает одно из ведущих мест среди других отраслей промышленности. На основных технологических переделах производства черных и цветных металлов образуются побочные продукты – отходы, химико-минералогический состав и физико-механические свойства которых позволяют считать их ценным сырьем для производства строительных материалов. Основная масса отходов металлургических процессов образуется в виде шлаков.
Шлаки – продукты высокотемпературного взаимодействия компонентов исходных материалов – топлива, руды, плавней и газовой среды. Трудно, пожалуй, найти другое сырье, которое обладало бы таким множеством ценных качеств и при этом так долго пробивало бы путь к широкому применению в строительной промышленности, как шлак. Во многих районах страны из шлака построены многоэтажные дома, промышленные здания, возведены мосты и плотины, проложены ленты автострад. Из обременительного отхода он становится признанным сырьем строительной промышленности.
Самая ранняя попытка использования доменного шлака относится к 1589 г. , когда в Германии из него отливали пушечные ядра. В строительстве шлак стали применять только в 18 веке. В Нижнем Тагиле из шлаковых расплавов начали отливать плиты для ступеней, брусчатку для дорог. В Швеции литые шлаковые камни применялись вместо кирпича для кладки верхней части шахт доменных печей. В России и других странах отвальный шлак использовали в качестве щебня при постройке дорог. В последующие годы ценные свойства шлаков еще больше привлекают внимание ученых и практиков во всем мире к проблеме применения шлаков в строительстве.
Негативные качества шлака
Потребитель выделяет некоторые недостатки вторсырья:
- гигроскопичность, материал не подойдет для проведения работ в местах с повышенной влажностью, паводками, обильными осадками, в несколько раз превышающими норму;
- сверхпрочность, из-за которой осуществление прокладки инженерных коммуникаций становится более трудоемким;
- высокая теплопроводность;
- содержание кислоты и серы выше нормы при том, что полное выветривание токсинов происходит через двенадцать месяцев.
Перед тем как окончательно определиться с выбором материала для индивидуального, жилого или промышленного строительства определите достоинства и недостатки этого сырья, ознакомьтесь детальнее со свойствами и применением шлака. Если этот факт для вас не имеет значения, а в приоритете только дешевый материал, то можно сэкономить и приобрести вторсырье.
Шлак — Строительные материалы — СтройТехСервис
Доменные шлаки являются продуктами взаимодействия флюсов (карбонатов кальция и магния) с пустой породой железной руды и золой кокса. Различия в составах железных руд и кокса в разных регионах страны обусловливают соответствующие различия в составе шлаков. Металлургические заводы южных и центральных районов производят шлаки с низким содержанием А1203 (6–10%) и сравнительно высоким содержанием СаО (до 50%) и сульфидной серы (до 3–4%). В металлургии Урала и Кузнецкого бассейна, применяющей железные руды, богатые глиноземом, и малосернистый кокс, выплавляют шлаки с содержанием А1203 до 20% и сульфидной серы — до 1%. Для шлаков первой группы М0 > 1, второй — М0 < 1, что объясняет существенные различия в их гидравлической активности и других свойствах.
В общем случае основные шлаковые стекла имеют большую гидравлическую активность, чем кислые.
Наиболее распространенным способом переработки шлаков является грануляция, сущность которой заключается в резком охлаждении шлаковых расплавов водой, паром или воздухом и образовании в результате этого стекловидных зерен размером до 10 мм. Применяют два способа грануляции: мокрый и полусухой.
Мокрая грануляция заключается в резком охлаждении расплавленного шлака обычно в железобетонных резервуарах объемом до 800 м3, наполненных водой, и диспергировании его образующимся паром, а также газами, выделяющимися из расплава. Установки мокрой грануляции несложны ( 2.1), имеют высокую производительность, а выполнение технологического процесса требует небольших затрат труда. Однако шлаки мокрой грануляции имеют высокую влажность (10–30%), что приводит к смерзанию их в зимнее время, повышению стоимости транспортирования, вызывает необходимость значительных затрат тепла на их сушку.
Более эффективна полусухая грануляция, основанная на комбинированном охлаждении шлаков: сначала водой, а затем воздухом. Конечная влажность гранулированного шлака при этом достигает 4–7%.
Из многочисленных установок для полусухой грануляции наиболее прогрессивны в настоящее время гидрожелобные (2.2), которые можно сооружать как вне доменного цеха, так и непосредственно у доменной печи. В таких установках расплав первоначально поступает в приемную ванну, а затем на наклонный желоб, где охлаждается водой, подаваемой под давлением 0,7–0,8 МПа. Гранулированный шлак отбрасывается водой на расстояние до 20 м и выносится в приемник пульпы, а затем по трубопроводам поступает в систему обезвоживающих бункеров, откуда подается на склад. Гранулировать шлак полусухим способом можно также на барабанных, гидроударных установках и в грануляционных мельницах.
Максимальное содержание стеклофазы наблюдается в шлаках мокрой грануляции, полученных на бассейновых и желобных установках из сильно перегретых расплавов (температура более 1600 °С).
Способ переработки и режим охлаждения шлаков влияют на их физико-механические свойства.
Меньшая механическая прочность гранулированных шлаков по сравнению с отвальными объясняет их лучшую размалываемость. На тонкое измельчение гранулированных шлаков требуется в 1,3–1,5 раза меньше энергии, чем на измельчение отвальных шлаков.
В большинстве стран гранулируют в основном доменные шлаки. Основная масса гранулированных доменных шлаков поступает в производство шлакопортландцемента. Их применяют также для получения местных бесклинкерных вяжущих, шлакощелочных бетонов, минеральной ваты, шлакоситалловых изделий, в качестве заполнителя в цементных и асфальтовых бетонах.
Сталеплавильные шлаки характеризуются высоким модулем основности, поэтому при их охлаждении они практически полностью кристаллизируются и почти не содержат стекла. Эти шлаки не гранулируются, а сливаются в отвалы, где медленно остывают.
Мартеновские шлаки обычно содержат включение металла (1–3%), поэтому их не гранулируют, а сливают в отвалы. Для мартеновских шлаков характерна высокая основность, что способствует их полной кристаллизации. Этот вид шлаков имеет плотную или ноздреватопористую структуру.
Основные шлаки, находясь в отвалах, распадаются на куски вследствие известкового распада. Прочность мартеновских шлаков 80— 150 МПа, они выдерживают более 200 циклов испытаний на морозостойкость. Конвертерные и электроплавильные шлаки обычно содержат продукты распада. Кусковые шлаки имеют плотную структуру, среднюю плотность 3100–3400 кг/м3. Прочность при сжатии 60–130 МПа.
При плавке литейного чугуна в вагранках образуются ваграночные шлаки, модуль основности которых довольно низкий и, как правило, не превышает 0,8. В этих шлаках, как гранулированных, так и в отвальных, присутствует стекло. Из шлаков производства ферросплавов наибольший интерес представляют шлаки от выплавки феррохрома и феррованадия, имеющие высокий модуль основности (1,6–1,8), а также кислые ферромолибденовые шлаки. В основных ферросплавных шлаках преобладает ортосиликат кальция в у-модификации, и они обычно при охлаждении рассыпаются в шлаковую муку. Шлаки ферросплавов содержат остаточные количества соответствующих элементов (Сг, V, Мо и т. п.) в виде металлов, оксидов или других соединений.
Более 60% сталеплавильных шлаков составляют шлаки мартеновского производства и более 35% — конвертерного. Перерабатывается около 30% сталеплавильных шлаков, а также шлакоб ферросплавного производства, из которых получают в основном щебень, шлаковая мука используется в качестве минерального удобрения. Из шлаков производства ферросплавов для производства строительных материалов наибольший интерес представляет феррохромовый шлак, получаемый при производстве феррохрома, применяемого для раскисления и легирования стали. Этот шлак представляет собой порошкообразный материал с высокой дисперсностью, вследствие распада при полиморфном Р <— у превращения двухкальциевого силиката. Исследования показали, что использование феррохромового шлака в качестве алюмосиликатного и окрашивающего компонента сырьевой шихты позволяет получить портландцементный клинкер зеленого цвета, что существенно снижает себестоимость цветного цемента.
Из шлаков цветной металлургии наибольшее значение для строительства имеют медеплавильные и никелевые шлаки. Отвальные медеплавильные шлаки имеют черный цвет. Они не подвержены распаду. Средняя плотность шлаков составляет 3300–3800 кг/м3, водопоглощение 0,1–0,6%, предел прочности при сжатии 120–300 МПа. Никелевые шлаки обладают такими же высокими показателями физико-механических свойств, как и медные. По химическому составу они относятся к кислым. Никелевые гранулированные шлаки, несмотря на стекловатое строение, практически не обладают гидравлической активностью.
При переплавке алюминиевых сплавов получают алюминиевые (вторичные) шлаки. Химический состав их следующий: КС1 — 38— 59%, NaCJ- 11,4-34,1, СаС12 — 3,0-4,2, MgO — 6,2-7,2, А1203 −6,5–12,6, Si02 — 1,8–3,5%. Водорастворимые соединения в шлаке составляют 75–85% массы. При длительном нахождении шлаков в воде водорастворимые соединения выщелачиваются. Средняя плотность шлаков 1800–2000 кг/м3. Предел прочности их 40–45 МПа.
Используется в качестве заполнителя габионных конструкций при благоустройстве водоохраной зоны:
- для укрепления берегов рек, озёр, водохранилищ, морей;
- для выпремления русел;
- для стабилизации почвенной эрозии;
- для создания водопропускных сооружений, отстойников;
- для укрепления склонов автомобильных дорог и ж/д насыпей;
- для облицовки каналов и дамб и др.
Щебень из доменного шлака по большинству характеристик не уступает гранитному, гравийному или известковому. В настоящее время продажа доменного щебня в г.
Улучшение грунта : Продукты из шлака из чугуна и стали : NIPPON SLAG ASSOCIATION
ГЛАВНАЯ > О шлаке из чугуна и стали > Продукты из шлака из чугуна и стали > Улучшение грунта
|
Влияние различного содержания летучей золы и гранулированного доменного шлака на свойства бетона: эксперименты и моделирование
1. Рамезани М. Докторская диссертация. Университет Луисвилля; Луисвилл, Кентукки: 2019 г.. Проектирование и прогнозирование характеристик цементных материалов, армированных углеродными нанотрубками: механические свойства и характеристики дисперсии. [CrossRef] [Google Scholar]
2. Цао З., Шен Л., Лю Л., Чжун С. Анализ основных факторов потребления цемента в процессе урбанизации в Китае. Дж. Чистый. Произв. 2016; 133:304–313. doi: 10.1016/j.jclepro.2016.05.130. [CrossRef] [Google Scholar]
3. Chen W., Hong J., Xu C. Загрязнители, образующиеся при производстве цемента в Китае, их воздействие и возможности улучшения состояния окружающей среды. Дж. Чистый. Произв. 2015;103:61–69. doi: 10.1016/j.jclepro.2014.04.048. [CrossRef] [Google Scholar]
4. Ramezani M., Kim Y.H., Sun Z. Моделирование механических свойств вяжущих материалов, содержащих УНТ. Цем. Конкр. Композиции 2019;104:103347. doi: 10.1016/j.cemconcomp.2019.103347. [CrossRef] [Google Scholar]
5. Ramezani M., Kim Y.H., Sun Z. Вероятностная модель прочности на изгиб материалов на основе цемента, армированных углеродными нанотрубками. Композиции Структура 2020;253:112748. doi: 10.1016/j.compstruct.2020.112748. [Перекрестная ссылка] [Академия Google]
6. Ramezani M., Kim Y.H., Sun Z. Формулировка модуля упругости вяжущих материалов, содержащих углеродные нанотрубки: вероятностный подход. Констр. Строить. Матер. 2020;274:122092. doi: 10.1016/j.conbuildmat.2020.122092. [CrossRef] [Google Scholar]
7. Ramezani M., Kim Y., Sun Z. Вероятностная модель прочности на изгиб цементных материалов, содержащих УНТ; Материалы Международной конференции по материалам на основе цемента, разработанным для устойчивого будущего; Стамбул, Турция. 27–29Май 2021 г. [Google Scholar]
8. Xue Y., Liu X. Детоксикация, отверждение и переработка летучей золы при сжигании твердых бытовых отходов: обзор. хим. англ. Дж. 2021; 420:130349. doi: 10.1016/j.cej.2021.130349. [CrossRef] [Google Scholar]
9. Натх С.К., Рандхава Н.С., Кумар С. Обзор характеристик силикомарганцевых шлаков и их использование в строительных материалах. Ресурс. Консерв. Переработка 2021;176:105946. doi: 10.1016/j.resconrec.2021.105946. [Перекрестная ссылка] [Академия Google]
10. Xing Y., Guo F., Xu M., Gui X., Li H., Li G., Xia Y., Han H. Отделение несгоревшего углерода от летучей золы угля: обзор. Порошковая технология. 2019; 353:372–384. doi: 10.1016/j.powtec.2019.05.037. [CrossRef] [Google Scholar]
11. Zhang J., Zhang S., Liu B. Технологии и механизмы деградации диоксинов в летучей золе при сжигании твердых бытовых отходов: Обзор. Дж. Чистый. Произв. 2019;250:119507. doi: 10.1016/j.jclepro.2019.119507. [CrossRef] [Google Scholar]
12. Голампур А., Озбаккалоглу Т. Характеристики устойчивых бетонов, содержащих очень большое количество летучей золы класса F и молотого гранулированного доменного шлака. Дж. Чистый. Произв. 2017; 162:1407–1417. doi: 10.1016/j.jclepro.2017.06.087. [Перекрестная ссылка] [Академия Google]
13. Де Мейер П.К., Крайе Б., Снеллингс Р., Каземи-Камьяб Х., Лутс М., Янссенс К., Найтс Г. Влияние ультрадисперсной золы-уноса на характеристики и долговечность бетона. Констр. Строить. Матер. 2020;263:120493. doi: 10.1016/j. conbuildmat.2020.120493. [CrossRef] [Google Scholar]
14. Могхаддам Ф., Сирививатнанон В., Вессалас К. Влияние крупности летучей золы на теплоту гидратации, микроструктуру, текучесть и прочность на сжатие смешанных цементных паст. Кейс Стад. Констр. Матер. 2019;10:e00218. doi: 10.1016/j.cscm.2019.e00218. [CrossRef] [Google Scholar]
15. Саха А.К. Влияние золы-уноса класса F на прочностные свойства бетона. Поддерживать. Окружающая среда. Рез. 2018;28:25–31. doi: 10.1016/j.serj.2017.09.001. [CrossRef] [Google Scholar]
16. Моффатт Э.Г., Томас М.Д., Фахим А. Характеристики бетона с большим объемом летучей золы в морской среде. Цем. Конкр. Рез. 2017; 102:127–135. doi: 10.1016/j.cemconres.2017.09.008. [CrossRef] [Google Scholar]
17. Кристиаван С.А., Адитья М.Т.М. Влияние больших объемов летучей золы на усадку самоуплотняющегося бетона. Procedia англ. 2015; 125:705–712. doi: 10.1016/j.proeng.2015.11.110. [Перекрестная ссылка] [Академия Google]
18. Невилл А. Свойства бетона. Пирсон; Harlow, UK: 2011. [Google Scholar]
19. Hussain S., Bhunia D., Singh S.B. Сравнительное исследование ускоренной карбонизации простого цемента и зольного бетона. Дж. Билд. англ. 2017;10:26–31. doi: 10.1016/j.jobe.2017.02.001. [CrossRef] [Google Scholar]
20. Хефни Ю., Эль Захер Ю.А., Вахаб М.А. Влияние активации летучей золы на механические свойства бетона. Констр. Строить. Матер. 2018; 172: 728–734. doi: 10.1016/j.conbuildmat.2018.04.021. [Перекрестная ссылка] [Академия Google]
21. Sun J., Shen X., Tan G., Tanner J.E. Прочность на сжатие и характеристики гидратации высокообъемного зольного бетона, приготовленного из летучей золы. Дж. Терм. Анальный. 2018; 136: 565–580. doi: 10.1007/s10973-018-7578-z. [CrossRef] [Google Scholar]
22. Озбай Э., Эрдемир М., Дурмуш Х.И. Использование и эффективность молотого гранулированного доменного шлака на свойства бетона. Обзор. Констр. Строить. Матер. 2016;105:423–434. doi: 10.1016/j.conbuildmat. 2015.12.153. [Перекрестная ссылка] [Академия Google]
23. Луковский П., Салих А. Стойкость растворов, содержащих грунтовый гранулированный доменный шлак в кислой и сульфатной среде. Procedia англ. 2015;108:47–54. doi: 10.1016/j.proeng.2015.06.118. [CrossRef] [Google Scholar]
24. Аль-Хамрани А., Кучуквар М., Алнахал В., Махди Э., Онат Н. Зеленый бетон для экономики замкнутого цикла: обзор устойчивости, долговечности и структурных свойств. Материалы. 2021;14:351. doi: 10.3390/ma14020351. [Бесплатная статья PMC] [PubMed] [CrossRef] [Google Scholar]
25. Li K., Zeng Q., Luo M., Pang X. Влияние самовысыхания на пористую структуру пасты и строительного раствора, содержащих 70% GGBS. Констр. Строить. Матер. 2014;51:329–337. doi: 10.1016/j.conbuildmat.2013.10.063. [CrossRef] [Google Scholar]
26. Мохан А., Мини К.М. Исследования прочности и долговечности SCC, включающего микрокремнезем и ультрадисперсный GGBS. Констр. Строить. Матер. 2018; 171:919–928. doi: 10.1016/j. conbuildmat.2018.03.186. [CrossRef] [Google Scholar]
27. Эль-Чабиб Х., Сайед А. Свойства самоуплотняющегося бетона, изготовленного с использованием больших объемов дополнительных вяжущих материалов. Дж. Матер. Гражданский англ. 2013;25:1579–1586. doi: 10.1061/(ASCE)MT.1943-5533.0000733. [CrossRef] [Google Scholar]
28. Даркенн А., Розьер Э., Хохар М., Туркри П., Лукили А., Грондин Ф. Длительные деформации и риск растрескивания бетона с высоким содержанием минеральных добавок. Матер. Структура 2012; 45:1705–1716. doi: 10.1617/s11527-012-9867-5. [CrossRef] [Google Scholar]
29. Zhao Y., Gong J., Zhao S. Экспериментальное исследование усадки КВД, содержащих летучую золу и измельченный гранулированный доменный шлак. Констр. Строить. Матер. 2017; 155:145–153. doi: 10.1016/j.conbuildmat.2017.07.020. [Перекрестная ссылка] [Академия Google]
30. Ramezani M., Kim Y.H., Sun Z. Механические свойства цементных материалов, армированных углеродными нанотрубками: база данных и статистический анализ. Маг. Конкр. Рез. 2020; 72: 1047–1071. doi: 10.1680/jmacr.19.00093. [CrossRef] [Google Scholar]
31. Проектирование железобетонных конструкций Часть 1-1. Общие правила и правила для зданий. Европейский комитет по стандартизации; Брюссель, Бельгия: 2004 г. [Google Scholar]
32. FIB . Код модели FIB для бетонных конструкций. Wiley-VCH Verlag GmbH & Co. KGaA; Вайнхайм, Германия: 2010. [Google Scholar]
33. Сингх П., Бхардвадж С., Диксит С., Шоу Р.Н., Гош А. Инновации в электротехнике и электронной технике. Спрингер; Сингапур: 2021 г. Разработка моделей прогнозирования для определения прочности на сжатие и удобоукладываемости устойчивого бетона с помощью ANN; стр. 753–769. Конспект лекций по электротехнике. [CrossRef] [Google Scholar]
34. Бхаскара Г.С.В., Рао К.Б., Ануп М.Б. Модель изменения прочности на сжатие бетона OPC и бетона с летучей золой во времени. Маг. Конкр. Рез. 2018;70:541–557. doi: 10.1680/jmacr.17.00203. [Перекрестная ссылка] [Академия Google]
35. Лю М.Х., Ван Ю.Ф. Прогноз развития прочности зольного бетона. Доп. Матер. Рез. 2010; 150–151:1026–1033. doi: 10.4028/www.scientific.net/AMR.150-151.1026. [CrossRef] [Google Scholar]
36. Общий портландцемент. Инспекция по надзору за качеством и карантин Китайской Народной Республики и Управление по стандартизации Китайской Народной Республики; Пекин, Китай: 2020. [Google Scholar]
37. Летучая зола, используемая для производства цемента и бетона. Инспекция по надзору за качеством и карантин Китайской Народной Республики и Управление по стандартизации Китайской Народной Республики; Пекин, Китай: 2017. [Google Scholar]
38. Молотый гранулированный доменный шлак, используемый для производства цемента, раствора и бетона. Инспекция по надзору за качеством и карантин Китайской Народной Республики и Управление по стандартизации Китайской Народной Республики; Пекин, Китай: 2017. [Google Scholar]
39. Стандарт на методы испытаний физико-механических свойств бетона. Инспекция по надзору за качеством и карантин Китайской Народной Республики и Управление по стандартизации Китайской Народной Республики; Пекин, Китай: 2019 г.. [Google Scholar]
40. Ван С.-Ю., Пак К.-Б. Анализ развития прочности на сжатие бетона, содержащего большое количество летучей золы. Констр. Строить. Матер. 2015; 98: 810–819. doi: 10.1016/j.conbuildmat.2015.08.099. [CrossRef] [Google Scholar]
41. Лю З., Такасу К., Коямада Х., Суяма Х. Исследование инженерных свойств и воздействия устойчивого бетона с золой-уносом или GGBS на окружающую среду. Констр. Строить. Матер. 2021;316:125776. doi: 10.1016/j.conbuildmat.2021.125776. [Перекрестная ссылка] [Академия Google]
42. Хан С.-Х., Ким Дж.-К., Пак Ю.-Д. Прогноз прочности на сжатие зольного бетона с помощью новой функции кажущейся энергии активации. Цем. Конкр. Рез. 2003; 33: 965–971. doi: 10.1016/S0008-8846(03)00007-3. [CrossRef] [Google Scholar]
43. Хван К., Томосава Ф., Ногучи Т. Модель прогнозирования развития прочности на сжатие зольного бетона. Цем. Конкр. Рез. 2004; 34: 2269–2276. doi: 10.1016/j.cemconres.2004.04.009. [CrossRef] [Google Scholar]
44. Рамезани М., Дегани А., Шериф М.М. Цементные композиты, армированные углеродными нанотрубками: всесторонний обзор. Констр. Строить. Матер. 2021;315:125100. doi: 10.1016/j.conbuildmat.2021.125100. [Перекрестная ссылка] [Академия Google]
45. Шарик М., Прасад Дж., Масуд А. Влияние GGBFS на зависящую от времени прочность бетона на сжатие. Констр. Строить. Матер. 2010; 24:1469–1478. doi: 10.1016/j.conbuildmat.2010.01.007. [CrossRef] [Google Scholar]
46. Брукс Дж., Аль-Каиси А. Раннее развитие прочности бетонов на портландцементе и шлакоцементе, отвержденных при повышенных температурах. АКИ Матер. Дж. 1990; 87: 503–507. [Google Scholar]
47. Ван Д., Чен З. О прогнозировании прочности на сжатие растворов с тройными смесями цемента, GGBFS и летучей золы. Цем. Конкр. Рез. 1997;27:487–493. doi: 10.1016/S0008-8846(97)00039-2. [CrossRef] [Google Scholar]
48. Zhang H., Bai L., Qi Y., Hong H., Neupane A., Pan Q. Влияние свойств расщепления на растяжение и динамическая конститутивная модель бетона с летучей золой. Дж. Матер. Гражданский англ. 2020;32:04020225. doi: 10.1061/(ASCE)MT.1943-5533.0003302. [CrossRef] [Google Scholar]
49. Shen D., Jiao Y., Kang J., Feng Z., Shen Y. Влияние измельченного гранулированного доменного шлака на способность высокопрочного бетона внутреннего отверждения к растрескиванию на ранней стадии. Констр. Строить. Матер. 2019;233:117083. doi: 10.1016/j.conbuildmat.2019.117083. [CrossRef] [Google Scholar]
50. Güneyisi E., Gesoglu M. Исследование свойств долговечности высокоэффективных бетонов с высоким уровнем замещения шлака. Матер. Структура 2007; 41: 479–493. doi: 10.1617/s11527-007-9260-y. [CrossRef] [Google Scholar]
51. Атис К.Д., Карахан О., Ари К., Сола О.К., Билим К. Связь между прочностными свойствами (изгиб и сжатие) и сопротивлением истиранию волокна (сталь и полипропилен) -Армированный зольный бетон. Дж. Матер. Гражданский англ. 2009 г.;21:402–408. doi: 10.1061/(ASCE)0899-1561(2009)21:8(402). [CrossRef] [Google Scholar]
52. Нили М., Тадайон М. Взаимосвязь между временем схватывания и начальной прочностью бетона, содержащего микрокремнезем, летучую золу и шлак; Материалы Третьей международной конференции по устойчивым строительным материалам и технологиям; Киото, Япония. 18–22 августа 2013 г. [Google Scholar]
53. Пейн И., Хансен В. Исследование ключевых свойств, контролирующих развитие напряжений в раннем возрасте в цементном бетоне с добавками. Цем. Конкр. Рез. 2008; 38: 1325–1335. doi: 10.1016/j.cemconres.2008.05.002. [Перекрестная ссылка] [Академия Google]
54. Zhang Y., Afroz S., Nguyen Q.D., Kim T., Eisenträger J., Castel A., Xu T. Аналитическая модель, прогнозирующая развитие напряжения растяжения в бетоне при испытании кольца с ограниченной усадкой. Констр. Строить. Матер. 2021;307:124930. doi: 10.1016/j.conbuildmat.2021.124930. [CrossRef] [Google Scholar]
55. Се Л. Влияние минеральных добавок на первоначальную автогенную усадку высокопрочного бетона. заявл. мех. Матер. 2013; 457–458: 318–322. doi: 10.4028/www.scientific.net/AMM.457-458.318. [Перекрестная ссылка] [Академия Google]
56. Афроз С., Чжан Ю., Нгуен К.Д., Ким Т., Кастель А. Влияние известняка в цементе общего назначения на автогенную усадку высокопрочного бетона и паст GGBFS. Констр. Строить. Матер. 2022;327:126949. doi: 10.1016/j.conbuildmat.2022.126949. [CrossRef] [Google Scholar]
57. Нгуен К.Д., Афроз С., Чжан Ю., Ким Т., Ли В., Кастель А. Автогенная и полная усадка бетонов на известняково-кальцинированном глиняном цементе (LC3). Констр. Строить. Матер. 2021;314:125720. doi: 10.1016/j.conbuildmat.2021.125720. [Перекрестная ссылка] [Академия Google]
58. Австралийский стандарт для бетонных конструкций. Стандарты Австралии; Сидней, Австралия: 2018. [Google Scholar]
59. Петруниас П., Рогкала А., Джаннакопулу П.П., Кристогероу А., Лампропулу П., Лиогрис С. , Куцовитис П., Кукузас Н. Использование промышленных ферроникелевых шлаков в качестве Переработанные бетонные заполнители. заявл. науч. 2022;12:2231. doi: 10.3390/app12042231. [CrossRef] [Google Scholar]
60. Фаридмер И., Шарик М., Плеврис В., Алимахмуди Н. Новая гибридная информационная модель для прогнозирования ползучести и усадки железобетонных балок, содержащих GGBFS. Нейронные вычисления. заявл. 2022; 31: 157–169. doi: 10.1007/s00521-022-07150-3. [CrossRef] [Google Scholar]
61. Джахангир Х., Эйдгахи Д.Р. Новый и надежный алгоритм гибридной искусственной пчелиной семьи — модель ANN для оценки прочности связи FRP-бетона. Композиции Структура 2020;257:113160. doi: 10.1016/j.compstruct.2020.113160. [CrossRef] [Google Scholar]
Прочтите дополнительные материалы — вес на кубический фут и удельный вес (типичный)
Вес на кубический фут и удельный вес (типовой):
Материал | Удельный вес | фунта на см- |
Уксусная кислота, 90% | 1,06 | 66,3 |
Спирт этиловый | 0,789 | 49,0 |
Спирт метиловый | 0,791 | 49,0 |
Люцерна молотая | 0,26 | 16,0 |
Квасцы кусковые | 0,88 | 55,0 |
Квасцы измельченные | 0,75 | 47,0 |
Глинозем | 0,96 | 60,0 |
Алюминий, цельный | 2,64 | 165,0 |
Алюминий, оксид | 1,52 | 95 |
Аммиак газообразный | 0,00 | 0,048 |
Сульфат аммония | 0,83 | 52 |
Андезит твердый | 2,77 | 173 |
Сурьма литая | 6,70 | 418 |
Древесина яблони, сухая | 0,71 | 44 |
Яблоки | 0,64 | 40 |
Мышьяк | 5,67 | 354 |
Асбест измельченный | 0,35 | 22 |
Асбест твердый | 2,45 | 153 |
Ясень, черный, сухой | 0,54 | 34 |
Ясень, белый, сухой | 0,67 | 42 |
Пепел | 0,66 | 41 |
Осина | 0,42 | 26 |
Асфальт дробленый | 0,72 | 45 |
Баббит | 7,28 | 454 |
Багасса | 0,12 | 7,5 |
Бакелит, твердый | 1,36 | 85 |
Разрыхлитель | 0,72 | 45 |
Барий | 3,78 | 236 |
Кора, древесные отходы | 0,24 | 15 |
Ячмень | 0,61 | 38 |
Барит дробленый | 2,88 | 180 |
Базальт битый | 1,96 | 122 |
Базальт твердый | 3.![]() | 188 |
Бокситы дробленые | 1,28 | 80 |
Фасоль, клещевина | 0,58 | 36 |
Бобы, какао | 0,59 | 37 |
Фасоль, темно-синяя | 0,80 | 50 |
Фасоль соевая | 0,72 | 45 |
Пчелиный воск | 0,96 | 60 |
Свекла | 0,72 | 45 |
Бентонит | 0,59 | 37 |
бикарбонат соды | 0,69 | 43 |
Береза, желтая | 0,71 | 44 |
Висмут | 9,79 | 611 |
Кости измельченные | 0,88 | 55 |
Бура мелкая | 0,85 | 53 |
Отруби | 0,26 | 16 |
Литая латунь | 8,56 | 534 |
Латунь, катаная | 8,56 | 534 |
Пивное зерно | 0,43 | 27 |
Кирпич обычный красный | 1,92 | 120 |
Кирпич огнеупорный | 2,40 | 150 |
Кирпич силикатный | 2,05 | 128 |
Кирпич, хром | 2,80 | 175 |
Кирпич магнезиальный | 2,56 | 160 |
Бронза | 8.![]() | 509 |
Гречка | 0,66 | 41 |
Масло сливочное | 0,87 | 54 |
Кадмий | 8,65 | 540 |
Карбид кальция | 1,20 | 75 |
Калише | 1,44 | 90 |
Углерод, твердый | 2,15 | 134 |
Уголь, порошкообразный | 0,08 | 5 |
Углекислый газ | 0,00 | 0,1234 |
Окись углерода | 0,00 | 0,0781 |
Картон | 0,69 | 43 |
Кедр, красный | 0,38 | 24 |
Цемент портланд | ~1,5 | 1506 кг/куб.![]() |
Цемент, раствор | ~2,65 | 2162 кг/куб.м |
Цемент, раствор | ~1,44 | 1442 кг/куб.м |
Мел твердый | 2,50 | 156 |
Мел кусковой | 1,44 | 90 |
Мел мелкий | 1,12 | 70 |
Древесный уголь | 0,21 | 13 |
Древесина вишни, сухая | 0,56 | 35 |
Древесина каштана, сухая | 0,48 | 30 |
Хлороформ | 1,52 | 95 |
Шоколад, порошок | 0,64 | 40 |
Кислота хромовая, чешуйчатая | 1,20 | 75 |
Хром | 6,86 | 428 |
Хромовая руда | 2,16 | 135 |
Зола, печь | 0,91 | 57 |
Пепел, уголь, зола | 0,64 | 40 |
Глина, вынутая в сухом виде | 1,09 | 68 |
Глина мокрая извлеченная | 1,83 | 114 |
Глина, сухая комковая | 1,07 | 67 |
Глина огнеупорная | 1,36 | 85 |
Глина сырая комовая | 1,60 | 100 |
Глина уплотненная | 1,75 | 109 |
Семена клевера | 0,77 | 48 |
Уголь, антрацит, твердый | 1,51 | 94 |
Уголь, антрацит, дробленый | 1.![]() | 69 |
Уголь битуминозный твердый | 1,35 | 84 |
Уголь битуминозный дробленый | 0,83 | 52 |
Кобальт | 8,75 | 546 |
Кокос, шрот | 0,51 | 32 |
Кокос, тертый | 0,35 | 22 |
Кофе, свежие зерна | 0,56 | 35 |
Кофе, обжаренные зерна | 0,43 | 27 |
Кокс | 0,42 | 26 |
Бетон, асфальт | 2,24 | 140 |
Бетон, гравий | 2,40 | 150 |
Бетон, известняк с портландцементом | 2,37 | 148 |
Медь литая | 8,69 | 542 |
Медь в прокате | 8,91 | 556 |
Сульфат меди молотый | 3,60 | 225 |
Копра, средний размер | 0,53 | 33 |
Копра, мука молотая | 0,64 | 40 |
Копра, молотый жмых | 0,51 | 32 |
Копра, жмых измельченный | 0,46 | 29 |
Пробка, твердая | 0,24 | 15 |
Пробка молотая | 0,16 | 10 |
Кукуруза в початках | 0,72 | 45 |
Кукуруза, очищенная | 0,72 | 45 |
Кукуруза, крупа | 0,67 | 42 |
Хлопковое семя, сухое, безворсовое | 0,56 | 35 |
Хлопковое семя, сухое, без ворса | 0,32 | 20 |
Семена хлопчатника, жмых, кусковой | 0,67 | 42 |
Семена хлопчатника, шелуха | 0,19 | 12 |
Семена хлопчатника, шрот | 0,59 | 37 |
Семена хлопка, мясо | 0,64 | 40 |
Тополь | 0,42 | 26 |
Криолит | 1,60 | 100 |
Стеклобой | 1,60 | 100 |
Стебель | 0,75 | 47 |
Древесина кипариса | 0,51 | 32 |
Доломит твердый | 2,90 | 181 |
Доломит, измельченный | 0,74 | 46 |
Доломит кусковой | 1,52 | 95 |
Земля суглинистая сухая, извлеченная | 1,25 | 78 |
Земля влажная, извлеченная | 1,44 | 90 |
Земля влажная, извлеченная | 1,60 | 100 |
Земля плотная | 2,00 | 125 |
Земля, мягкий рыхлый ил | 1,73 | 108 |
Земля в упаковке | 1,52 | 95 |
Земля, фуллерова, необработанная | 0,67 | 42 |
Эбеновое дерево | 0,96 | 60 |
Вяз сухой | 0,56 | 35 |
Эмери | 4.![]() | 250 |
Эфир | 0,74 | 46 |
Полевой шпат, твердый | 2,56 | 160 |
Полевой шпат, измельченный | 1,23 | 77 |
Удобрение, кислый фосфат | 0,96 | 60 |
Фир, Дуглас | 0,53 | 33 |
Рыба, лом | 0,72 | 45 |
Рыба, мука | 0,59 | 37 |
Льняное семя, цельное | 0,72 | 45 |
Мука пшеничная | 0,59 | 37 |
Плавиковый шпат твердый | 3,21 | 200 |
Плавиковый шпат, куски | 1,60 | 100 |
Плавиковый шпат, порошкообразный | 1,44 | 90 |
Мусор | 0,48 | 30 |
Стекло оконное | 2,58 | 161 |
Клей животного происхождения, чешуйчатый | 0,56 | 35 |
Клей растительный порошкообразный | 0,64 | 40 |
Глютен, мука | 0,63 | 39 |
Гнейс, пласт на месте | 2,87 | 179 |
Гнейс разбитый | 1,86 | 116 |
Золото чистое 24 карата | 19,29 | 1204 |
Гранит твердый | 2,69 | 168 |
Гранит разбитый | 1,65 | 103 |
Графит пластинчатый | 0,64 | 40 |
Гравий сыпучий, сухой | 1,52 | 95 |
Гравий с песком, природный | 1,92 | 120 |
Гравий сухой от 1/4 до 2 дюймов | 1,68 | 105 |
Гравий влажный от 1/4 до 2 дюймов | 2,00 | 125 |
Гипс твердый | 2,79 | 174 |
Гипс битый | 1,81 | 113 |
Гипс дробленый | 1,60 | 100 |
Гипс измельченный | 1,12 | 70 |
Галит (соль), твердый | 2,32 | 145 |
Галит (соль), измельченный | 1,51 | 94 |
Кислота соляная 40% | 1,20 | 75 |
Лед, твердый | 0,92 | 57,4 |
Лед дробленый | 0,59 | 37 |
Ильменит | 2,31 | 144 |
Иридиум | 22.![]() | 1383 |
Чугун литой | 7,21 | 450 |
Железо кованое | 7,77 | 485 |
Железооксидный пигмент | 0,40 | 25 |
Слоновая кость | 1,84 | 115 |
Каолин зеленый измельченный | 1,03 | 64 |
Каолин, измельченный | 0,35 | 22 |
Свинец, литой | 11.35 | 708 |
Свинец прокатанный | 11,39 | 711 |
Свинец, красный | 3,69 | 230 |
Свинец, белый пигмент | 4,09 | 255 |
Кожа | 0,95 | 59 |
Бурый уголь сухой | 0,80 | 50 |
Lignum Vitae, сухой | 1,28 | 80 |
Известь комовая негашеная | 0,85 | 53 |
Известь негашеная мелкая | 1,20 | 75 |
Известь каменная крупная | 2,69 | 168 |
Известь каменная, комовая | 1,54 | 96 |
Известь гашеная | 0,48 | 30 |
Лимонит, твердый | 3,80 | 237 |
Лимонит, разбитый | 2,47 | 154 |
Известняк твердый | 2,61 | 163 |
Известняк дробленый | 1,55 | 97 |
Известняк измельченный | 1,39 | 87 |
Льняное семя, цельное | 0,75 | 47 |
Льняное семя, шрот | 0,51 | 32 |
Саранча сухая | 0,71 | 44 |
Магнезит, твердый | 3.![]() | 188 |
Магний твердый | 1,75 | 109 |
Сульфат магния кристаллический | 1,12 | 70 |
Магнетит твердый | 5,05 | 315 |
Магнетит, разбитый | 3,29 | 205 |
Красное дерево, испанское, сухое | 0,85 | 53 |
Красное дерево, Гондурас, сухое | 0,54 | 34 |
Солод | 0,34 | 21 |
Марганец твердый | 7,61 | 475 |
Оксид марганца | 1,92 | 120 |
Навоз | 0,40 | 25 |
Клен сухой | 0,71 | 44 |
Мрамор, твердый | 2,56 | 160 |
Мрамор разбитый | 1,57 | 98 |
Мергель мокрый, извлеченный из грунта | 2,24 | 140 |
Меркурий при 32oF | 13,61 | 849 |
Слюда, твердая | 2,88 | 180 |
Слюда дробленая | 1,60 | 100 |
Молоко сухое | 0,45 | 28 |
Молибден | 10.![]() | 636 |
Раствор влажный | 2,40 | 150 |
Шлам упакованный | 1,91 | 119 |
Грязь, жидкость | 1,73 | 108 |
Никель прокатанный | 8,67 | 541 |
Нейзильбер | 8,45 | 527 |
Кислота азотная, 91% | 1,51 | 94 |
Азот | 0,00 | 0,0784 |
Дуб живой, сухой | 0,95 | 59 |
Дуб, красный | 0,71 | 44 |
Овес | 0,43 | 27 |
Овес плющеный | 0,30 | 19 |
Жмых | 0,79 | 49 |
Масло льняное | 0,94 | 58,8 |
Нефть, нефть | 0,88 | 55 |
Кислород | 0,00 | 0,0892 |
Раковины устриц, молотые | 0,85 | 53 |
Бумага, стандартная | 1,20 | 75 |
Парафин | 0,72 | 45 |
Арахис очищенный | 0,64 | 40 |
Арахис неочищенный | 0,27 | 17 |
Торф сухой | 0,40 | 25 |
Торф влажный | 0,80 | 50 |
Торф влажный | 1,12 | 70 |
Древесина ореха пекан | 0,75 | 47 |
Фосфатная руда, дробленая | 1,76 | 110 |
Фосфор | 2,34 | 146 |
Сосна белая, сухая | 0,42 | 26 |
Сосна желтая северная, сухая | 0,54 | 34 |
Сосна желтая южная, сухая | 0,72 | 45 |
Шаг | 1,15 | 72 |
Гипс | 0,85 | 53 |
Платина | 21,51 | 1342 |
Фарфор | 2,40 | 150 |
Порфир твердый | 2,55 | 159 |
Порфир битый | 1,65 | 103 |
Калий | 1,28 | 80 |
Хлорид калия | 2,00 | 125 |
Картофель, белый | 0,77 | 48 |
Пемза, камень | 0,64 | 40 |
Кварц, твердый | 2,64 | 165 |
Кварц, кусковой | 1,55 | 97 |
Кварцевый песок | 1,20 | 75 |
Редвуд, Калифорния, сухой | 0,45 | 28 |
Смола синтетическая, дробленая | 0,56 | 35 |
Рис очищенный | 0,75 | 47 |
Рис необработанный | 0,58 | 36 |
Крупа рисовая | 0,69 | 43 |
Рип-Рэп | 1,60 | 100 |
Канифоль | 1,07 | 67 |
Резина, каучук | 0,95 | 59 |
Резина промышленная | 1,52 | 95 |
Резина, молотый лом | 0,48 | 30 |
Рожь | 0,71 | 44 |
Солёный жмых | 1,44 | 90 |
Соль, курс | 0,80 | 50 |
Соль мелкая | 1,20 | 75 |
Селитра | 1,20 | 75 |
Песок мокрый | 1,92 | 120 |
Песок мокрый, упакованный | 2,08 | 130 |
Песок сухой | 1,60 | 100 |
Песок сыпучий | 1,44 | 90 |
Песок утрамбованный | 1,68 | 105 |
Песок, наполненный водой | 1,92 | 120 |
Песок с гравием, сухой | 1,73 | 108 |
Песок с гравием, влажный | 2,00 | 125 |
Песчаник твердый | 2,32 | 145 |
Песчаник дробленый | 1,51 | 94 |
Опилки | 0,27 | 17 |
Сточные воды, шлам | 0,72 | 45 |
Сланец твердый | 2,68 | 167 |
Сланец дробленый | 1,59 | 99 |
Серебро | 10,46 | 653 |
Шлак твердый | 2.![]() | 132 |
Шлак дробленый | 1,76 | 110 |
Шлак, измельченный, 1/4 дюйма | 1,19 | 74 |
Шлак мех. гранулированный | 0,96 | 60 |
Сланец сплошной | 2,69 | 168 |
Шифер, разбитый | 1,67 | 104 |
Шифер, измельченный | 1,36 | 85 |
Снег свежевыпавший | 0,16 | 10 |
Снег утрамбованный | 0,48 | 30 |
Мыло твердое | 0,80 | 50 |
Мыло, чипсы | 0,16 | 10 |
Мыло, хлопья | 0,16 | 10 |
Мыло порошкообразное | 0,37 | 23 |
Сода кальцинированная, тяжелая | 0,96 | 60 |
Сода кальцинированная, светлая | 0,43 | 27 |
Натрий | 0,98 | 61 |
Алюминат натрия молотый | 1,15 | 72 |
Нитрат натрия, молотый | 1,20 | 75 |
Соевые бобы, целые | 0,75 | 47 |
Ель калифорнийская сухая | 0,45 | 28 |
Крахмал порошкообразный | 0,56 | 35 |
Сталь литая | 7,85 | 490 |
Сталь прокатная | 7,93 | 495 |
Камень дробленый | 1,60 | 100 |
Сахар коричневый | 0,72 | 45 |
Сахарная пудра | 0,80 | 50 |
Сахар гранулированный | 0,85 | 53 |
Сахар сырой тростниковый | 0,96 | 60 |
Жом сахарной свеклы, сухой | 0,21 | 13 |
Жом сахарной свеклы, влажный | 0,56 | 35 |
Сахарный тростник | 0,27 | 17 |
Сера твердая | 2,00 | 125 |
Сера комовая | 1,31 | 82 |
Сера порошкообразная | 0,96 | 60 |
Кислота серная, 87% | 1,79 | 112 |
Платан, сухой | 0,59 | 37 |
Таконит | 2,80 | 175 |
Тальк твердый | 2,69 | 168 |
Тальк измельченный | 1,75 | 109 |
кора дуба молотая | 0,88 | 55 |
Резервуар | 0,96 | 60 |
Смола | 1,15 | 72 |
Жесть литая | 7,36 | 459 |
Табак | 0,32 | 20 |
Ловушка твердая | 2,88 | 180 |
Ловушка, разбитая | 1,75 | 109 |
Вольфрам | 19,62 | 1224 |
Газон | 0,40 | 25 |
Скипидар | 0,87 | 54 |
Ванадий | 5,50 | 343 |
Орех, черный, сухой | 0,61 | 38 |
Вода чистая | 1,00 | 62,4 |
Вода, море | 1,03 | 64,08 |
Пшеница | 0,77 | 48 |
Пшеница дробленая | 0,67 | 42 |
Древесина ивы | 0,42 | 26 |
Шерсть | 1,31 | 82 |
Цинк, литой | 7,05 | 440 |
Оксид цинка | 0,40 | 25 |
1) Если вы заинтересованы в дополнительной информации о любом из этих продуктов, пожалуйста, обратитесь к:
ПРОЧТИТЕ технические страницы продукта или свяжитесь с READE
2) Важный комментарий:
Вышеуказанная информация предоставляется бесплатно компанией ПРОЧИТАЙТЕ и делайте все возможное, чтобы быть точным.