Из какой стали делают рельсы
Домой > В помощь строителю > Стройматериалы > Из какой стали делают рельсы
27.12.2015 в рубрике «Стройматериалы» Оставить комментарий
Современные рельсы можно изготавливать из разных материалов. Однако они должны быть очень прочными и качественными, ведь на них ежедневно воздействует огромная нагрузка.
Купить детали для железной дороги можно на сайте http://rails.com.ua, ведь там предоставлены варианты, которые соответствуют всем правилам и требованиям.
Но из чего же делают рельсы?
Основные материалы для изготовления рельс
Конечно, дать однозначный ответ на этот вопрос просто невозможно. Дело в том, что рельсы могут выполнять разные функции, поэтому для их изготовления нужно пользоваться соответственными материалами.
Железнодорожные изделия можно назвать наиболее распространенными, ведь потребность в них растет ежедневно. Делают такие рельсы из конверторной стали.
В некоторых случаях можно пользоваться мартеновским материалом. Перед тем, как сделать окончательный выбор, стоит определиться с особенностями местности.
Крановые рельсы тоже требуют соблюдения определенных технологий. Такие изделия изготавливают из высокоуглеродистых сплавов.
Сами крановые рельсы получаются очень прочными и надежными. Именно поэтому они выдерживают огромные нагрузки, которые на них воздействуют.
Последняя разновидность – это контактные рельсы. Этими изделиями пользуются в том случае, когда необходимо снять ток.
Вы сможете увидеть контактные рельсы в метро. Они изготовлены из мягкой стали, так как на них не воздействуют слишком большие нагрузки.
Это основные материалы, которые используются для изготовления разных рельс. На выбор напрямую зависит уровень нагрузки и особенности местности, где они будут установлены.
Преимущества железнодорожных рельс
С основными видами и материалами вы разобрались. А теперь стоит упомянуть о преимуществах железнодорожных рельс:
- благодаря качественным изделиям можно обеспечить безопасность пассажирам и машинистам;
- железнодорожные рельсы дают возможность транспортному средству быстро попасть в точку назначения;
- изделия способны выдержать огромную нагрузку, которая воздействует на них каждый день;
- давление колес поезда распространяется на составные части путей.
Смотрите также:
Кожаный бювар — что это такое http://domkrat.org/kozhanyiy-byuvar-chto-eto-takoe/.
Интересное по теме: Шкафы для одежды
Советы в статье «Как сделать вешалку в прихожую?» здесь.
Это основные моменты, которые касаются использования и изготовления разнообразных видов рельс. Без таких изделий просто невозможно обойтись, ведь железная дорога дает возможность быстро попасть в место назначения, не сталкиваясь с особыми проблемами.
Источник №1: http://rails.com.ua/
Tweet2015-12-27
Предыдущие: Монтаж емкости для дизельного топлива
Следующие: Виды полотенцесушителей
ЖЕЛЕЗНОДОРОЖНЫЕ РЕЛЬСЫ | МОДЕЛИСТ-КОНСТРУКТОР
Рубрики Конвейер
Когда появилась железная дорога, рельсы делали из чугуна или из кованного железа. Чугунные рельсы были очень хрупкими и легко ломались, кованные рельсы были мягкими и быстро изнашивались, потом был найден выход – сталь, из которой делают рельсы до сих пор. Колеса поездов находятся внутри рельсов, чтобы поезд держался на путях.
На этом заводе рельсы делают исключительно из вторсырья из консервных банок и отходов от строительства самой железной дороги. Электромагниты поднимают металлолом и перемещают в плавильный чан. Грузовик перевозит чан и кран отправляет его в топку. Сильный электрический ток плавит стальной лом при температуре 1650 градусов Цельсия, затем сталь сливают в большие прямоугольные чаны, где в нее добавляют углерод, марганец и другие элементы, чтобы сделать сталь более прочной. Затем смесь прогоняют через керамическую трубку, защищающую металл от разрушающего воздействия кислорода.
Потом расплавленный металл сливают в формы, предающие ему вид длинных блоков. Ацетиленовые паяльники отрезают блоки длиной в 3,5 метра. После этого кран переносит блоки на конвейер, где их снова греют еще 5 или 7 часов, это размягчает сталь для дальнейшей обработки. Затем разогретые блоки попадают под каток, который раскатывает каждый блок более чем 4 раза в длину. Потом резак разрезает раскатанные блоки на 4 части. Получившиеся куски снова нагревают, это подготавливает их к следующей раскатке, которая придает им окончательную форму железнодорожных рельсов. Раньше на разных железных дорогах использовались рельсы разной формы и чтобы поезд смог переехать с одной железной дороги на другую на нем меняли колеса, но в начале 20-го века рельсы в виде буквы Т стали стандартными и остаются ими до сих пор.
Для окончательной обработки каждый рельс несколько раз проезжает через 3 станка. Вот так выглядит станок для придания формы, а вот форма, которую придают стали. Затем, чтобы заровнять концы их обрезают где-то на 30 см и обрезки возвращаются обратно в металлолом. Самим рельсам дают остыть до температуры где-то 500 градусов Цельсия, затем электромагниты перемещают их в боксы, где они остаются еще на 10 часов пока не остынут до 90 градусов. Потом их достают из боксов и прогоняют через 2 роликовых станка. Первый выравнивает рельсы вертикально, а второй – горизонтально. Этот процесс окончательно выпрямляет рельсы, которые немного гнутся во время нагреваний и охлаждений. Затем каждый рельс проезжает над зеркалом, чтобы инспекторы могли осмотреть его не только сверху, но и снизу.
И, наконец, рельсы нарезают такими кусками, какие заказала железная дорога. Стандартной длиной считается 25 метров. После этого служба контроля измеряет случайные образцы, чтобы убедится, что размеры безупречны. На каждый рельс ставят номер, где отмечается партия из которой он выбран. Если обнаруживается проблема, этот номер помогает найти все рельсы, выпущенные в той же партии. Прежде чем они попадут на дорогу, они должны получить стальную гарантию.
Тут можете оценить работу автора:
Производство рельсов — Рельсы :: Trackopedia
Рельсы — это не просто стальные балки; они представляют собой высококачественный и тщательно продуманный технический продукт. Поскольку не все виды стали одинаковы — рельсы в основном сделаны из стали — стальные рельсы имеют определенный состав различных компонентов, чтобы сделать рельсы долговечными. Количество некоторых добавок может существенно повлиять на свойства, поскольку при разработке рельсов было проведено множество исследований и производственных ноу-хау. Общее у всех стальных рельсов только одно: они изготавливаются из стального проката, даже если состав стали может различаться. Так было не всегда. На заре существования железной дороги рельсы были сделаны из чугуна, что приводило к поломке рельсов и другим повреждениям.
Важность рельсов как «особых видов стальных балок» можно объяснить их основными функциями.
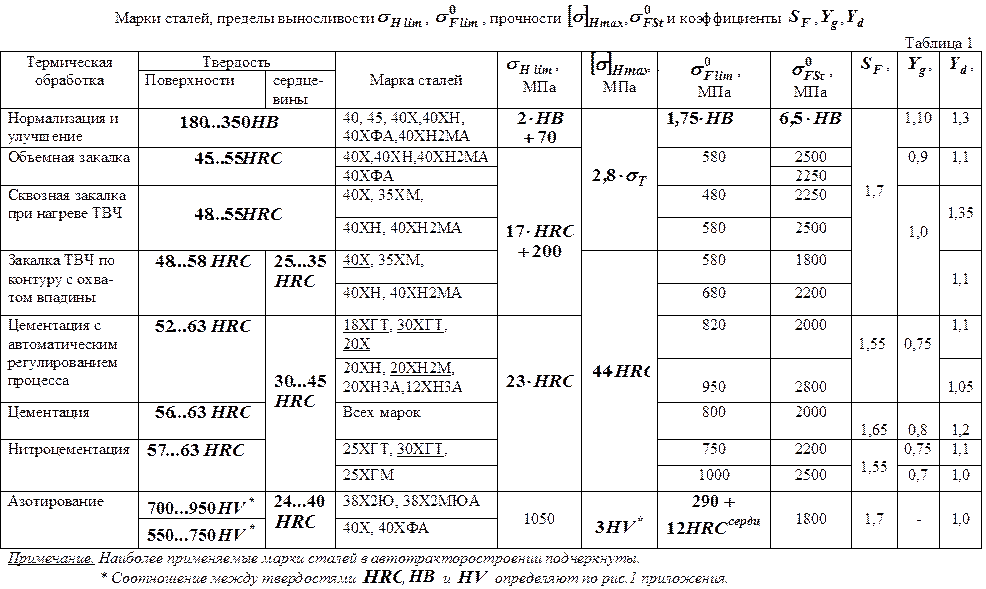
Рельсовый профиль 49E1
© Thorsten Schaeffer
Для изготовления рельсов , сначала необходимо изготовить чугун. Для этого железную руду с известью и коксом нагревают при постоянной подаче свежего воздуха в доменной печи до температуры более 1500 °С. В результате получаются продукты передельный чугун и шлак. Чугун не подходит в качестве строительного материала, но является исходным материалом для производства стали . Он должен быть еще десульфурирован. Сталь производится на втором этапе так называемого процесса рафинирования чистым кислородом. Содержание углерода снижается примерно с 4 % до максимум 1,5 %. Другие добавки определяют последующие свойства материала.
Нежелательные продукты железа, которые имеют особое сродство к кислороду, затем откладываются в виде шлака. «Процедура продувки кислородом», которая является обычной сегодня, была введена в 1949 году (сталь LD, процесс Линца-Донавитца [VOEST]) и является очень экономичным способом производства высококачественной стали с низким уровнем загрязнения [2] и процесс электротехнической стали с дуговой плавкой. Также обычным явлением является добавление значительной доли металлолома в расплав стали. Весь производственный процесс обеспечивает чистый однородный материал с точно определенными свойствами. Немецкие железные дороги, например, требуют минимальной прочности на растяжение 880 Н/мм 2 . Согласно DIN EN 10027 рельсовые стали обозначаются буквой R.
Расплавленную сталь разливают в формы («сляб», «установка непрерывной разливки», «вакуумная разливка») или в специальные вагоны-ковши еще в жидком состоянии, чтобы чтобы его можно было переместить для дальнейшей обработки. Для рельсов от процесс горячей прокатки , он может включать 20 операций прокатки, пока не будет достигнут желаемый профиль. Рельсовую сталь можно прокатывать при температуре около 1250 °С. Эту температуру необходимо поддерживать в процессе прокатки, чтобы получить однородную структуру. Профиль, прокатный стан (производитель) и год выпуска можно прочитать на шейке рельса как выпуклые «
Готовый катаный рельс должен контролируемым образом охлаждаться после процесса прокатки, чтобы избежать повреждения внутренних напряжений и грубой структуры. Однако допускается изгиб. Это будет исправлено роликовыми выпрямителями при температуре около 50 °C. Кроме того, целесообразно провести ультразвуковой контроль для выявления каких-либо производственных ошибок, иначе пустоты и каверны в материале могут иметь непредвиденные последствия, если рельс выйдет из строя в более поздние сроки. Образовавшаяся в процессе производства так называемая скрученная оболочка полностью защищает рельс. На беговой поверхности устраняется только после установки – в основном шлифовкой.
Прокатный стан на заводе VOEST
© voestalpine AG
Основные принципы содержания механизированного пути
Эта книга предназначена для многих людей, занимающихся повседневным планированием и выполнением работ по обслуживанию пути. Предлагая практический подход к повседневным задачам по обслуживанию механизированных путей, он предназначен не только как теоретический подход к путевой системе.
Железные дороги нацелены на безопасную, быструю, регулярную, комфортную и своевременную перевозку людей и грузов из одного места в другое. Эта книга предназначена для отделов инфраструктуры путей, способствующих достижению вышеуказанной цели путем обеспечения надежности, доступности, ремонтопригодности и безопасности инфраструктуры путей, что обозначается аббревиатурой RAMS.
Передовая практика технического обслуживания путей, Том 1 — Управление инфраструктурой
Управление инфраструктурой В томе 1 рассматриваются аспекты управления инфраструктурой с особым упором на единое европейское железнодорожное пространство. На основе передового опыта Центральной Европы представлены меры по целенаправленной модернизации и улучшению обслуживания инфраструктуры существующей сети. Во многих случаях операторы инфраструктуры сталкиваются со сменой поколений, что ускоряет процесс. Современные информационные и коммуникационные технологии могут упростить понимание и представление сложных контекстов. Модифицированные подходы к управлению активами и жизненным циклом позволяют реализовать «прозрачный перманентный путь» или «железную дорогу 4.0».
- [1] Браун, Х. и др.: Fachkunde Metall. Europa-Fachbuchreihe für metalltechnische Berufe.
53. überarbeitete Auflage 1999. Haan-Gruiten, Europa-Lehrmittel Nourney, Vollmer & Co.
- [2] Bargel, H., Schulze, G. (Hrsg.): Werkstoffkunde. 3. Auflage 1983. Дюссельдорф, VDI-Verlag. ISBN 3-18-400595-X
Как изготавливаются стальные рельсы
29 сентября 2017 г.
Стальной рельс, который мы также называем рельсами, гусеницами, является важным элементом рельсовой системы. Стальной рельс используется с рельсовым стыком и железнодорожными крепежными элементами, такими как рельсовые зажимы, рельсовые стяжки, стрелочные переводы, чтобы поезд двигался быстро и устойчиво без рулевого управления.
Как известно, рельсовая система состоит из двух параллельных рельсов и шпал. На шпалах закреплены стальные рельсы, а под шпалой находится балласт железнодорожного пути. Стальной рельс может выдерживать гораздо больший вес по сравнению с рельсами из других материалов. Из-за огромного давления для изготовления стального рельса требуется высококачественная сталь.
В настоящее время мы хотели бы сделать часть стального рельса китайским иероглифом «工». И стальные рельсы имеют свою судьбу в зависимости от использования. Некоторые стальные рельсы используются для контакта с колесами, которые называются головками рельсов. Некоторые стальные рельсы в середине пути, которые называются решеткой рельсов, и некоторые стальные рельсы внизу, которые называются фланцами рельсов. Различные способы предъявляют разные требования к прочности, стабильности и стойкости к истиранию стального рельса. Таким образом, существует множество стандартов стальных рельсов.
Типы железнодорожных путей выражаются в километрах на метр. Чем тяжелее стальной рельс на метр, тем больший вес может выдержать рельс.
Что касается размеров железнодорожных путей, то между странами существуют некоторые различия. Общие стандарты в Европе: 40 кг/м, 50 кг/м и 60 кг/м. Стандарты Common Rail в Китае: 43 кг, 50 кг, 60 кг и 75 кг. Как правило, наиболее распространенными стандартами рельсов являются 43 кг, 60 кг/м и 75 кг/м . Соединенные Штаты предпочитают более тяжелые рельсы. Например, угольная линия применялась к рельсам 75 кг/м в США. Конечно, упомянутые рельсы относятся к категории тяжелых стальных рельсов. Где можно купить железнодорожный рельс? Если вы хотите найти производителей легкорельсового транспорта, вы можете выбрать AGICO Rail.
Процесс производства стальных рельсов прост. Самое главное прокатка стали. После выбора подходящей стальной заготовки следующим шагом является прокатка стали.
Утилизация стальной заготовки
Принять блюм непрерывного литья для улучшения макроструктуры стальной заготовки. Кроме того, применяется технология вакуумной дегазации и вторичного рафинирования для обеспечения внутреннего качества стальной заготовки. Эта технология может контролировать содержание остаточного элемента и газа и обеспечивать чистоту стали.
Прокат
Как известно, стальную заготовку путем прокатки, охлаждения и правки можно превратить в рельсы. Во время процесса жизненно важная часть катится. Существует два метода прокатки: калибровочная прокатка и универсальная прокатка .
Накатка желобков проще, чем универсальная прокатка. Деформация металла устойчивая. Прокатка в канавках подходит для черновой деформации из-за простой системы управления. Но рисунок отверстий имеет асимметричный дизайн, поэтому симметрия стальной секции рельса не очень хорошая. Кроме того, точность контроля не является жесткой, поэтому качество поверхности нельзя контролировать должным образом.
В мире популярна универсальная прокатка, которая является лучшей технологией производства стального рельса. Универсальная система прокатки состоит из пары активных горизонтальных валков и пары пассивных горизонтальных валков. Эти четыре ролика работают на одном уровне. Плоский валок обрабатывает полотно рельса. Вертикальный валок и плоский валок вместе обрабатывают головку рельса и гребень рельса.
Направляющая балка прокатного стана установлена непосредственно на опоре подшипника, которая может двигаться как целая система, а процесс прокатки полностью автоматизирован.
Отопление
Нагрев лучше для резкого улучшения механических свойств. Наиболее распространенными технологиями нагрева являются закалка и отпуск, термическая обработка и медленная закалка. Между тем, используйте печь с шагающими балками для нагрева стальных заготовок, которая может контролировать газофракционирование и предотвращать обезуглероживание и неравномерную температуру.
Выпрямление
Мы хотели бы использовать длинный стержень для прокатки, охлаждения и правки. Эта технология лучше подходит для увеличения выхода продукции, снижения остаточного напряжения и увеличения срока службы стального рельса.
Проверка
Через онлайн-центр проверки качества используйте ультразвуковые волны, вихревые и лазерные волны для проверки внутреннего качества стали, качества поверхности рельса и размеров железнодорожного пути.