монтаж, установка на стройке, подъемный строительный, промышленные, опорных
Автор Михалыч На чтение 3 мин.
Содержание
- Подготовка
- Как устанавливают краны
- Проверка правильности монтажа
На строительных площадках используются механизмы разной высоты и грузоподъемности. Техника дает возможность возводить здания в короткие сроки, перед началом работы специалисты собирают башенный кран.
Подготовка
Башенные краны привозят на строительную площадку в разобранном виде, затем рабочие монтируют их на месте. Конструкции тяжелые, поэтому перед началом установки необходимо подготовить площадку.
Механизм состоит из следующих частей:
- Башня.
- Кабина, предназначенная для машиниста.
- Консоль. Она необходима для противовеса.
- Стрела. Грузоподъемный механизм.
Сначала место, на котором будет стоять агрегат, выравнивают. Чтобы конструкция была более устойчивой, поверхность заливают бетоном. Обязательно делают заземление, к площадке проводят электричество.
Монтировать строительный кран можно с помощью автокрана, но его нужно доставить на место. Следует заранее определить удобные пути подъезда к стройплощадке.
Как устанавливают краны
Монтаж кранов представляет собой достаточно простое дело, которое не требует больших затрат времени и сил. Сначала рабочие сооружают постамент, он необходим для установки механизма. На него устанавливают башенную конструкцию и надежно ее закрепляют.
Вспомогательным краном переносят на место опорно-поворотный механизм, фиксируют его на месте. После этого рабочие переходят к наращиванию остальных частей конструкции. Это башня, поворотная платформа, устройство подъема и опускания груза, механизм изменения вылета стрелы.
Отдельные секции подъемника перемещают и собирают при помощи собственной стрелы механизма. Это позволяет быстро увеличить высоту устройства.
В работе используют монтажное устройство, представляющее собой единую рамную конструкцию. Она отличается тем, что обладает съемной передней частью. Монтажное устройство необходимо как для сборки, так и дальнейшей работы механизма.
Сборка башенного крана осуществляется с помощью пульта монтажной конструкции, также в работе используется вспомогательный выносной пульт. Вместе со сборкой устройства рабочие могут выполнить монтаж опорных кранов.
Промышленные грузоподъемные устройства на строительной площадке позволяют сократить сроки выполнения работ. Строящийся дом будет завершен всего за несколько недель.
Проверка правильности монтажа
Регулярные проверки и профилактическое обслуживание являются залогом бесперебойной работы механизма. Износ и ухудшение технических характеристик можно наблюдать на механизмах, которые эксплуатировались в течение многих лет. При экстремальных нагрузках такое оборудование выходит из строя.
Внеочередная техническая проверка необходима после установки грузоподъемного устройства на новое рабочее место. Во время технического осмотра проверяется работа механического и электрического оборудования, защитных приборов, тормозной системы и агрегатов управления, а также сигнализации.
Во время полного осмотра проверяют следующее:
- В каком состоянии находится металлическая конструкция. Учитывается состояние ее сварных соединений. Специалисты ищут разрывы, деформации, ржавчину и другие повреждения. Они проверяют, в каком состоянии находятся кабины, лестницы, платформы и ограждения.
- Техническое состояние крюка и деталей подвески, при этом учитывается степень их износа.
- Как закреплены грузовые канаты, их состояние.
- Внешний вид блоков и элементов крепления. Проверке подлежат компоненты подвески.
- Заземление электрического крана, питающегося от внешней сети.
- Соотношение между массой противовеса и балластами башенного крана.
Полученные значения сравнивают с теми цифрами, которые указаны в паспорте.
Выполняя монтаж кранов и осуществляя проверку, ориентируются на информацию, указанную в инструкции. Документ составляет производитель башенного механизма.
Читайте также:
Оцените автора
Как собирают башенный кран — ГК ТРАНСПОРТНОЕ СТРОИТЕЛЬСТВО
Без башенного крана не обходится стройка ни одного высотного здания. Именно эти агрегаты видно над высотками самых больших мегаполисов. Как устанавливают башенные краны? Именно об этом мы и поговорим в нашей статье.
Что такое башенный кран?
Башенным краном называют поворотный агрегат стрелочного типа. Высота таких механизмов достигает 60-70 метров, а вес – примерно 10 тонн. Эта «махина» кажется просто необъятной, поэтому многие задаются вопросом как наращивают его элементы, чтобы он достиг заданной высоты. За счет чего его платформа держит устойчивость? Все не так уж и сложно, как кажется. Зная определенные нюансы, можно быстро установить такое устройство.
Как собирается башенный кран
Монтаж башенного крана берет начало с формирования листов из стали, толщиной 8 мм. С помощью больших фасонно-фрезерных станков формируются главные элементы подъемного механизма.
- Вышина агрегата зависит от его башни. Этот элемент состоит из 4 стояков, которые соединяются между собой балками по диагонали.
- То, на какой радиус работы будет рассчитан кран, зависит от длины его стрелы. Чтобы она была уравновешена, необходимо разместить с ее обратной стороны тяжелый груз.
- По стреле в обе стороны двигается блок, позволяющий крановщику разворачивать кран в нужном направлении.
Вышеописанные элементы определяют схему и внешний вид агрегата. Но они не заработают, если не будет установлено зубчатое колесо, которое еще называют поворотным ободом. Именно эта деталь обеспечивает крану практически ювелирную точность во время поворотов на 360 градусов.
В краны монтируют поворотное колесо, которое является настоящим чудом инженерии.
Особенности установки устройства
Перед тем, как устанавливать элементы крана, все секции башни тщательно окрашивают в цеху двумя слоями краски. После того, как все элементы будут готовы, можно переходить к следующему этапу. Ставят башенный кран всего за пару часов. Почему? Потому, что эти агрегаты способны практически складывать себя самостоятельно.
- На начальном этапе на земле укладываются плиты из бетона, формируя своеобразный постамент, толщиной около полтора метра. Вес такого постамента может достигать больше ста тонн.
- На этих бетонных плитах команде нужно сформировать первую секцию башенного крана. Кругом нее монтируют платформу, высотой 6 метров. Ее называют верхним подъемником.
- Потом в ход идут большегрузные трейлеры. На них подвозят кабину и стрелу, которые собирают на земле.
- Далее с помощью передвижного крана кабину и стрелу поднимают на высоту первой секции.
Применяя четыре гидравлические подъемника, стрелу и кабину очень медленно и плавно поднимают до тех пор, когда они не окажутся над башней. После этого сборщик крана поднимает еще одну секцию башни. Далее снова задействуются гидравлические подъемники, которые поднимают кабину и стрелу. В это время устанавливается следующая часть башни. Этот процесс продолжается, пока башня не станет нужной высоты.
Кран собран. Но теперь его нужно укрепить, чтобы он не упал от сильных порывов ветра. Также плохо на башню влияет дождь – вода может способствовать появлению ржи. Спасти повреждённый кран от катастрофы может умелая команда сварщиков.
Особенности башенного крана
Главный секрет стойкости башни в способе ее сборки. Если швы качественно сварены, это значит, что ни сильные порывы ветра, ни дождь, ни другие неблагоприятные погодные условия не смогут навредить крану. Диагональные балки пересекаются с вертикальными в центральной части в каждой башенной секции, поэтому опорные точки расположены сверху к низу «скелета» крана. Благодаря этому башня приобретает свою прочность и устойчивость.
Если вам интересно, как разбирают башенный кран, тогда скажем, что процесс разбора башни происходит в обратной последовательности к сборке. Башня разбирается по одной секции, как и складывалась.
Краны используются на стройках уже около шестидесяти лет. За это время они совершенствуются, становятся более маневренными, простыми в установке и сборке. Тем не менее башенный кран сейчас, как и много лет назад, пользуется огромным спросом на стройках многоэтажных домов. Они облегчают доставку и подъем груза на любую высоту.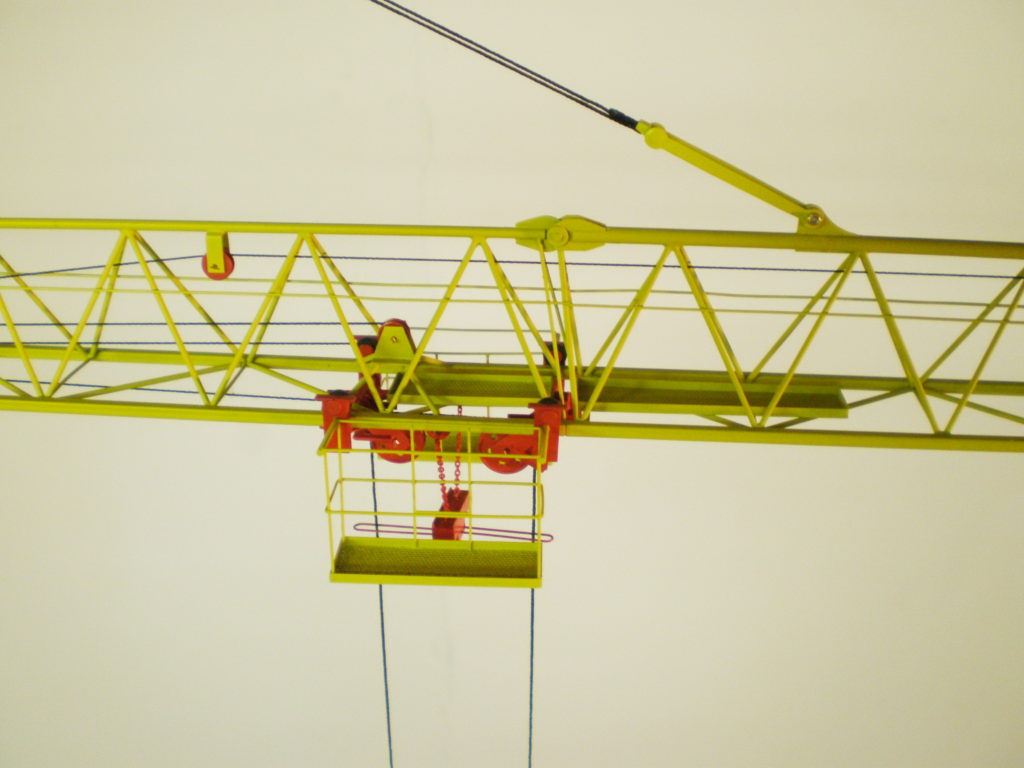
Как производятся смесители? – Керовит Блог
| Керовит
Краны — это приспособления, помогающие регулировать поток воды из трубы. Он состоит из отверстия, которое открывается и закрывается и регулирует поток воды. Смесители используются в ванных комнатах и на кухнях для эффективного использования воды. Смесители состоят из следующих компонентов:
– Форсунка
– Ручка(и)
– Подъемная штанга
– Картридж
– Впускные отверстия для воды
– Смесительная камера
Процесс производства смесителя включает несколько этапов, каждый из которых одинаково важен, так как качество конечного продукта зависит от Это. Мы составили список этапов изготовления смесителя. Давайте приступим прямо к делу.
Этап 1. Сырье
Латунь — это сплав меди и цинка, который обычно используется для изготовления смесителей благодаря своей устойчивости к коррозии и кальцификации в жесткой воде. Компоненты крана могут быть изготовлены из металлов, отличных от меди и цинка. Они получены в виде готовых компонентов от других производителей.
Этап 2 — Литье и формовка
Стержень — это устройство, которое используется в процессах литья и формования. Он используется для создания входящих углов и полостей в кране, и после того, как он выполнил свою задачу, он разрушается, чтобы извлечь его из детали. Это может быть дорогостоящим, но он используется для предоставления деталей, которые не могут быть интегрированы в дизайн без использования ядра.
Основной корпус смесителя получается либо литьем под давлением, либо его форма вырезается из высококачественных латунных стержней. При литье под давлением латунь плавится при высоких температурах, ок. 1150°С и разливается в формы нужной формы.
Этап 3. Обработка
Это управляемый компьютером процесс, который гарантирует, что все поверхности отлитого под давлением изделия будут обработаны с высокой степенью эффективности и гладкости. Проход, через который будет проходить вода, также сглаживается с помощью процесса механической обработки.
Этап 4 – Полировка
Этап 5. Проверка на наличие дефектов
Следующим процессом является гальваническое покрытие, но перед этим продукты физически проверяются на наличие дефектов, таких как асимметричные линии и кривые, ошибки полировки и геометрические ошибки. Это гарантирует, что следующий процесс будет более эффективным.
Этап 6 – гальваническое покрытие
В этом процессе сначала на изделие наносится гальваническое покрытие из никеля. После этого наносится тонкое покрытие из гальванического хрома. Слой хрома делает его прочным и устойчивым к коррозии. После покрытия смеситель устанавливается с различными компонентами, что представляет собой компьютеризированный процесс. Смеситель и комплектующие некоторое время хранятся для того, чтобы их настроить перед отправкой на сборку и установку.
Этап 7. Линия сборки
Сборка может включать как ручные, так и автоматизированные процессы. Этот процесс происходит на вращающихся сборочных машинах, которые точно контролируются. Форсунка, если она отдельная, устанавливается первой. Картридж и рычаги управления устанавливаются после насадки.
Этап 8-Тестирование
Созданные смесители затем тщательно тестируются как на воде, так и на сжатом воздухе. Образцы испытывают на критические размеры и прочность. Смесители также должны соответствовать нескольким экологическим нормам.
Этап 9 – Исследования и разработки
Производители смесителей продолжают повышать ценность и качество, чтобы соответствовать постоянно меняющимся требованиям рынка.
Этап 10. Переработка
В ходе различных процессов производства смесителей могут образовываться отходы, которые необходимо перерабатывать или эффективно утилизировать. В процессе механической обработки и ковки могут образовываться отходы в виде металлолома, который перерабатывается.
Завершающим этапом производства смесителей является транспортировка. После того, как изготовленные смесители проходят все испытания, они отправляются на рынок.
Вот и все, мы подробно рассмотрели процесс изготовления смесителей. Мы надеемся, что этот блог был полезен.
Поделиться на
так изготавливаются смесители Oras
Производство смесителей Oras представляет собой сложный многоэтапный процесс, большинство из которых выполняется вручную. Уровень качества контролируется на каждом этапе. Мы вместе с менеджером по продажам Nordic Марко Сундхольмом посетили завод Oras в Рауме, где ежедневно производится около 3000 смесителей.
Марко Сундхольм, менеджер по продажам Nordic в Oras, расскажет о процессе производства смесителей
Производство смесителей Oras по-прежнему частично автоматизировано, в то время как большинство стадий производства смесителей Oras по-прежнему частично автоматизированы. Вкратце, этапы работы: изготовление стержня, литье, распиловка, механическая обработка, шлифовка, полировка, хромирование, сборка и испытание. Однако до этого уже проделана большая работа: разработано новое изделие и смоделировано его производство на компьютере, после чего отливка испытана и отрегулирована до совершенства. Oras производит все инструменты, оболочковые формы и стержневые ящики, необходимые для литья.
Литье заготовок из латунных прутков и стержней
Важнейшим компонентом в производстве смесителей является латунь, из которой методом литья изготавливается корпус смесителя. Сердечник является центральной частью производственного процесса, так как во время отливки он образует каналы для воды в корпусе крана. Твердый сердечник изготавливается из мелкого песка и отвердителя путем нагревания в стержневом ящике.
Сердцевина изготовлена из мелкозернистого песка и образует водоводы для корпуса крана при литье
Паллетные партии латунных прутков доставляются в литейный цех завода. Стержни изготовлены из специальной латуни, устойчивой к обесцинкованию.
Латунные стержни, используемые в смесителях Oras, изготовлены из специальной латуни, устойчивой к обесцинкованию. Несмотря на то, что его можно безопасно использовать каждый день, он химически агрессивен. Вот почему обычная латунь нам не подходит», — говорит 9.0025 Марко Сундхольм , менеджер по продажам в странах Северной Европы.
При литье оболочковая форма погружается в раствор воды и графита. Разливщик (лицо, ответственное за литье) помещает стержни в форму и удаляет рыхлый песок из формы с помощью сжатого воздуха.
Стержни помещаются внутрь формы.
Форма герметизируется и помещается в раскаленную литейную камеру литейной печи. Три тонны расплавленной латуни вытекают из литейной печи в литейные формы. Сердечник поддерживает открытыми водоводы внутри формы, к которым устанавливаются технические компоненты и по которым вода течет через кран.
Расплавленная латунь стекает в оболочковые формы
После кратковременного охлаждения литейщик использует щипцы для перемещения отливки для охлаждения. Далее из корпуса крана извлекают сердечник, вращая его в мельнице, снабженной металлическими шариками.
Краны распиливаются и шлифуются до окончательной формы
Охлажденные корпуса кранов, доставленные из литейного цеха, отделяются друг от друга распиловкой, и удаляются все детали, которые были необходимы при литье, но не входили в комплектные краны. В Oras процесс распиловки включает в себя как автоматизированные, так и ручные этапы.
Корпуса смесителей из латуни готовы к дальнейшей обработке
«Мы повысили уровень автоматизации на этом этапе работы, но некоторые сложные компоненты усложняют этот процесс», — говорит Сандхольм.
Корпуса смесителей затем помещаются на конвейерную ленту, которая перемещает их через автоматизированные процессы механической обработки, шлифовки и полировки. Первоначально полученная шероховатая поверхность становится гладкой в ходе сложного процесса шлифования. Шлифованная металлическая поверхность безупречно отполирована. Наконец, сотрудники проверяют уровень качества визуально и вручную. Небольшие партии специальных изделий можно шлифовать и полировать вручную. Мелкий ремонт также можно выполнить своими руками.
Небольшие партии специальных продуктов и ремонт по-прежнему выполняются вручную, чтобы гарантировать безупречный результат.
«Латунь, оставшаяся после распиловки и обработки, не превращается в отходы. Вместо этого драгоценное сырье возвращается в производство. Отходы распиловки переплавляются в литейной печи и снова отливаются. Стружка после механической обработки возвращается поставщику латуни, который использует ее для производства новых прутков. Доставленные нам слитки содержат лишь небольшое количество новой латуни», — говорит Сандхольм.
Хромирование не допускает ошибок
Наконец, смесители хромированы. Хром делает поверхность твердой, блестящей и износостойкой.
После полировки к корпусам смесителей нельзя прикасаться голыми руками во избежание появления отпечатков пальцев на хромированном покрытии.
«Перед хромированием поверхность изделия должна быть безупречной, поскольку хром — безжалостный материал. Он не покрывает, а скорее подчеркивает даже мельчайшие ошибки», — говорит Сундхольм. Все видимые пластиковые и композитные детали также хромированы. Пластиковые и композитные детали изготавливаются в производственном цехе компании Oras.
Ассортимент хромированных деталей смесителя.
Пластик является более сложным материалом для хромирования, чем латунь: «Пластик должен быть электропроводным, чтобы сделать возможным хромирование. Пластиковые детали покрывают слоем меди, а затем слоем никеля, чтобы сформировать гибкий слой под покрытием для защиты поверхности от теплового расширения», — объясняет Сундхольм.
Хромирование занимает примерно два часа, в течение которых изделия проходят различные этапы замачивания и стирки 40 раз. После хромирования изделия проверяются перед сборкой. На этом этапе добавляются любые маркировки, такие как логотип бренда. В настоящее время продукция в основном маркируется с помощью лазера.
Технические компоненты устанавливаются внутри корпуса смесителя
Компания Oras производит компоненты, устанавливаемые внутри корпуса смесителя. Они регулируют поток воды и температуру, среди прочего.
«Душа рычажного смесителя называется картриджем, и он остается одинаковым и неизменным во всех моделях Oras с 1982 года. Картридж регулирует расход и температуру воды, чтобы обеспечить нужное количество воды нужной температуры. Картриджи производятся в Рауме. Каждый компонент маркируется, чтобы его можно было отследить», — говорит Сандхольм.