Нормы расхода электродов — Таблица 5 из ВСН 452-84
Темы: Нормы расхода материалов ВСН-452-84 в строительстве, Сварные соединения, Сварные швы.
Соединения C18 вертикальных стыков трубопроводов сo скосом кромок нa съемной подкладке.
Таблица 05. Норма расхода электродов нa 1 стык.
Размеры трубы, мм | ll | Масса наплавленного металла, кг | | | Электроды пo группам, кг | ll | Код стрoки | ||||||||
ll | | | I I | I I I | | | I V | l | V | | | V I | ll | ||||
45 ´ 3 | ll | 0,027 | | | 0,06 | l | 0,054 | | | 0,058 | l | 0,061 | | | ll | 1 | |
45 ´ 4 | ll | 0,034 | | | 0,062 | l | 0,066 | | | 0,07 | l | 0,074 | | | 0,079 | ll | 2 |
57 ´ 3 | ll | 0,035 | | | 0,064 | l | 0,069 | | | 0,073 | l | 0,077 | | | 0,082 | ll | 3 |
57 ´ 4 | ll | 0,044 | | | 0,079 | l | 0,085 | | | 0,09 | l | 0,095 | | | 0,1 | ll | 4 |
76 ´ 5 | ll | 0,077 | | | 0,14 | l | 0,149 | | | 0,158 | l | 0,168 | | | 0,177 | ll | 5 |
89 ´ 6 | ll | 0,13 | | | 0,235 | l | 0,251 | | | 0,266 | l | 0,282 | | | 0,298 | ll | 6 |
108 ´ 6 | ll | 0,158 | | | 0,287 | l | 0,306 | | | 0,325 | l | 0,344 | | | 0,363 | ll | 7 |
133 ´ 6 | ll | 0,195 | | | 0,354 | l | 0,377 | | | 0,401 | l | 0,425 | | | 0,448 | ll | |
133 ´ 8 | ll | 0,268 | | | 0,483 | l | 0,516 | | | 0,548 | l | 0,58 | | | 0,613 | ll | 9 |
159 ´ 6 | ll | 0,234 | | | 0,424 | l | 0,453 | | | 0,481 | l | 0,509 | | | 0,537 | ll | 10 |
159 ´ 8 | ll | 0,32 | | | 0,58 | l | 0,619 | | | 0,658 | l | 0,697 | | | 0,735 | ll | 11 |
219 ´ 6 | ll | 0,323 | | | 0,586 | l | 0,625 | | | 0,664 | l | 0,703 | | | 0,742 | ll | 12 |
219 ´ 8 | ll | 0,442 | | | 0,803 | l | 0,856 | | | 0,91 | l | 0,963 | | | 1,017 | ll | 13 |
219 ´ 10 | ll | 0,599 | | | 1,088 | l | 1,16 | | | 1,233 | l | 1,305 | | | 1,376 | ll | 14 |
219 ´ 12 | ll | 0,787 | | | 1,428 | l | 1,523 | | | 1,619 | l | 1,714 | | | 1,809 | ll | 15 |
273 ´ 8 | ll | 0,553 | | | 1,003 | l | 1,071 | | | 1,138 | l | 1,205 | | | 1,272 | ll | 16 |
273 ´ 10 | ll | 0,75 | | | 1,361 | l | 1,452 | | | 1,542 | l | 1,633 | | | 1,724 | ll | 17 |
273 ´ 12 | ll | 0,985 | | | 1,788 | l | 1,907 | | | 2,026 | l | 2,145 | | | 2,265 | ll | 16 |
273 ´ 15 | ll | 1,592 | | | 2,89 | l | 3,082 | | | 3,275 | l | 3,467 | | | 3,66 | ll | 19 |
325 ´ 8 | ll | 0,659 | | | 1,196 | l | 1,276 | | | 1,357 | l | 1,436 | | | 1,516 | ll | 20 |
325 ´ 10 | ll | 0,894 | | | 1,623 | l | 1,731 | | | 1,839 | l | 1,947 | | | 2,055 | ll | 21 |
325 ´ 12 | ll | 1,175 | | | 2,133 | l | 2,275 | | | 2,417 | l | 2,559 | | | 2,701 | ll | 22 |
325 ´ 15 | ll | 1,902 | | | 3,453 | l | 3,683 | | | 3,913 | l | 4,144 | | | 4,374 | ll | 23 |
377 ´ 8 | ll | 0,765 | | | 1,389 | l | 1,482 | | | 1,576 | l | 1,667 | | | 1,76 | ll | 24 |
377 ´ 10 | ll | 1,039 | | | 1,885 | l | 2,01 | | | 2,136 | l | 2,261 | | | 2,387 | ll | 25 |
377 ´ 12 | ll | 1,365 | | | 2,478 | l | 2,643 | | | 2,808 | l | 2,973 | | | 3,138 | ll | 26 |
377 ´ 15 | ll | 2,211 | | | 4,013 | l | 4,281 | | | 4,548 | l | 4,816 | | | 5,083 | ll | 27 |
426 ´ 10 | ll | 1,175 | | | 2,132 | l | 2,274 | | | 2,416 | l | 2,558 | | | 2,7 | ll | 28 |
426 ´ 12 | ll | 1,545 | | | 2,804 | l | 2,99 | | | 3,177 | l | 3,364 | | | 3,551 | ll | 29 |
426 ´ 16 | ll | 2,759 | 4,991 | l | 5,324 | | | 5,655 | l | 5,988 | | | 6,321 | ll | 30 | |
465 ´ 18 | ll | 3,598 | | | 6,531 | l | 6,966 | | | 7,401 | l | 7,836 | | | 8,271 | ll | 31 |
Другие страницы по теме:
- Нормы расхода топлива (Украина).
- Таблица 2 — нормы расхода электродов на 1 метр сварочного шва.
- Таблица 3 — норма электродов на 1 стык труб (С18 -соединения вертикальных стыков трубопроводов).
- Таблица 4 — норма электродов на 1 метр шва
- Таблица 6 — нормы расхода на 1 метр шва (С5 — Соединения вертикальных стыков трубопроводов).
- Таблица 7 — нормы расхода на 1 стык (С5 — Соединения вертикальных стыков трубопроводов).
- Таблица 8 — нормы расхода электродов на 1 метр шва (С10 — Соединения горизонтальных стыков трубопроводов).
- < Нормы расхода электродов — Таблица 6 из ВСН 452-84
- Нормы расхода электродов — Таблица 4 из ВСН 452-84 >
Норма расхода электродов на 1 тонну металлоконструкций
Неотъемлемой частью процесса возведения любой металлоконструкции является грамотное и точное планирование расхода материалов для составления сметы и подсчета предстоящих финансовых затрат. Вычисляется не только количество задействованного в строительстве материала, но и то, сколько электродов потребуется затратить при проведении сварочных работ.
Умение правильно рассчитывать расход электродов на тонну металлоконструкций — одно из приоритетных требований к профессиональным сварщикам, работающим в крупных компаниях. Без проведения правильных расчетов невозможно узнать точную себестоимость металлоконструкции, предполагаемую прибыль. Все эти нюансы важны для фирм, задействованных в сфере возведения металлических конструкций.
Расход электродов при сварке
Оказывает прямое влияние на производительность и продолжительность рабочего процесса. Отработанное присадочное изделие для сварки необходимо заменить новым.
Если под рукой сварщика не окажется нужных электродов, это отразится на сроках проведения сварки в сторону увеличения. Докупить присадочный материал не является основной проблемой. Все усложняется тем, что он требует предварительной подготовки. Электроды надо прокалить и просушить. Это занимает от полутора до двух часов.
Когда электроды нужны для наплавки нескольких килограмм металла, ситуация не столь критична, в отличие от сварки габаритных металлоконструкций. Любой простой чреват и временными, и финансовыми затратами. Чтобы процесс работы ничего не тормозило, предельно важно выполнить правильный расчет того, сколько электродов требуется на одну тонну металлоконструкций.
Методы вычисления
Показатель расхода зависит от вводных параметров:
- массы наплавки;
- длины сварочного шва;
- нормы расхода.
Массой наплавки называют вес металла, который заполняет собой стыковочный шов. Точные данные этого параметра приводятся в технологической карте сварки. Его показатель по грубым подсчетам равен от 1 до 1,5% от массы металлоконструкции.
Габариты шва измеряют рулеткой по стыку. Получаемый результат умножают на общее число швов, присутствующих в разделе. Это обусловлено тем, что глубокие стыки заваривают параллельным либо последовательным накладыванием двух-трех швов.
Нормой расхода является масса наплавки на один метр шва. Она вычисляется как для отдельного узла либо детали, так и в зависимости от типа выполняемой сварочной операции.
Учитывая эти нюансы, расчет расхода присадочных изделий должен проводиться и теоретически, и практически.
Теоретический расчет
Основан на использовании различных формул. На практике наибольшее распространение получили два типа расчета:
- по коэффициенту;
- по физическим характеристикам.
Первый способ охватывает собой различные категории расходных материалов и вычисляется по формуле: H = M * K, где М — масса подвергаемого сварке металла, а K — специальный коэффициент расхода присадки.
Второй способ основан на характеристиках и применяемого электрода, и подвергаемой сварке металлоконструкции, рассчитывается формулой: G = F * L * Масса проволоки, в которой F — это площадь поперечного сечения, а L — длина шва.
Если первая формула позволяет вычислить расход, то вторая — массу наплавленного металла. Оба расчета являются «табличными», то есть основываются на стандартных показателях, соответствующих определенным маркам электрода, типу металла, величине шва.
Расчет расхода электродов по коэффициенту
Чтобы выполнить вычисление, нужно знать точный коэффициент электрода (K) который, как и другие параметры, указан в приложении РДС 82-201-96 «правил разработки норм расхода материалов в строительстве».
Значение коэффициента варьируется от 1,5 и до 1,9. Меньший показатель соответствует второй группе электродов, а наивысшей шестой. Если при работе используется марка ЦТ-28 из второй группы, показатель K равен 1,5.
Используя математический расчет для определения необходимого количества электродов для наплавки тонны металла, получаем значение 1500 кг, то есть H = 1000 * 1,5. Соответственно, расход возрастает, если применяется марка более возрастной группы, к примеру, НЖ-13, имеющая коэффициент, который равен 1,8.
Практический расчет
Подразумевает определение массы металла и проведение сварных тестовых работ. Когда они завершены, выполняют замер огарка, учитывают напряжение и силу тока, длину выполненного шва. Основываясь на этих данных, определяют число требуемых электродов для сварки шва определенной длины.
Точным вычисление будет в том случае, когда и внешние данные, и угол положения при выполнении основных работ останутся аналогичными тем, которые были во время тестирования. Чтобы избежать неточности определения, эксперимент повторяют от трех до четырех раз. Если соблюсти это условие, расчет получится еще точнее, чем при использовании формул.
Погрешность расчета
Никакой метод вычислений не дает стопроцентной точности. Закупать расходный материал для обеспечения полноценного и непрерывного рабочего процесса рекомендуется с запасом. Необходимо учитывать и возможность наличия в партии электродов бракованных и низкокачественных изделий.
Чтобы не приходилось останавливать сварку, следует увеличить полученные при расчетах данные на пять либо семь процентов. Это гарантировано избавит от различного рода форс-мажорных обстоятельств. Учитывают и то, что количество расходного материала зависит как от технологического процесса, так и от типа заполняемого присадками шва.
Как снизить затраты?
Существует несколько условий, которые позволяют сэкономить на расходных материалах для проведения сварочных работ, но при этом никак не отражаются на качестве:
- Наибольшей экономии присадок позволяет добиться использование полуавтоматического либо автоматического сварочного аппарата. Когда работы проводятся вручную, то потери составляют от пяти процентов и выше. При автоматическом и полуавтоматическом процессе этот показатель вдвое ниже. Если и присадки, и аппарат имеют высокое качество, сокращение расходных изделий будет максимальным.
- Показатели силы тока и напряжения должны полностью соответствовать выбираемому присадочному материалу. Поэтому, настраивая сварочный аппарат, нужно уделять особое внимание этим параметрам.
- Количество затрачиваемых электродов при равных условиях может отличаться. Это обусловлено положением расходного изделия при выполнении сварки. Поэтому многие сварщики предпочитают не ограничиваться формулами и прибегают к практическим расчетам, проводя несколько тестов, чтобы найти «идеальное» положение.
Соблюдение этих трех важных условий и грамотный выбор способа сэкономить позволяет сократить количество требуемого присадочного материала практически на тридцать процентов. Это достаточно внушительная сумма в денежном эквиваленте.
Норма расхода электродов на 1-н метр шва: Таблица!
Быстрая навигация по статье (содержание)
- Какие формулы применяются при расчете расхода электродов?
- Как вычислить дополнительные затраты (поправочный коэффициент)?
- Расход электродов на 1 м шва
- Коэффициенты расхода электродов
- Что поможет сэкономить средства?
- Для чего нужны те или иные электроды?
О чем данная статья?
- Основные расчетные формулы
- Вычисление дополнительных затрат (поправочный коэффициент)
- Способы экономии
- Виды электродов и их использование
Для того что бы подсчитать расход электродов на шов, необходимо привлекать знающего человека, который разбирается в сварочном деле, потому что мало применять только формулы нужно учитывать специфику работы от которой могут быть дополнительные расходы. Сварщик должен знать методику применяемую в работе и особенности оборудования. Опыт, навыки и знания мастера должны помочь составить правильную смету на работы.
Н = Нсв + Нпр + Нпр.
Расчет происходит исходя из нужного материала на сварку и дополнительные затраты: прихватки, правку при помощи холостых валиков. Для расчета расхода электродов на 1 м. шва берется наибольшее количество материала, требуемого в работе.
Количество материала, необходимое на прихваточные работы зависит от используемого материала и считается в процентном соотношении от общей суммы работ.
Сталь:
- до 12 мм — 15%
- более 12 мм — 12%
Алюминий:
- до 8 мм — 30%
- более 8 мм — 35%
Титан:
- 35 — 40%
Вычисление количества электродов необходимое на шов длинной 1 метр применяется для подсчета различных нормативов: детальные, узловые, нормы на изделие или на операции. Все нормы расхода электродов на шов тесно связаны друг с другом. Некоторые конкретные типы и размеры считаются исходя из СНиП.
N=M*K
Сумма расхода(N) для 1м вычисляется умножением объема наплавленного материала(M) на величину потерь(K).
M=S*p*L
Объем присадки необходимый для 1 м. шва(M) считается перемножением поперечного сечения — его площади(S) с плотностью материала(p) и длинной шва(L)
Как вычислить дополнительные затраты (поправочный коэффициент)?Данный коэффициент — K зависит от применяемых технологий и сложности работ, используемых материалов, режимов и методов сварки. Кроме этого учитываются затраты на угар, объем разбрызгивания и длину огарков, которые вписываются в прилагаемый к материалу паспорт.
λ = (lэ — 50)/(lэ — lо)
Затраты на огарок рассчитываются исходя из его длинны(lo) и длинны электрода(lэ). Для величин, отличных от стандартных применяют поправку.
При сварке смотрят как расположен шов, что дает понять сложность работы. Коэффициенты сложности работ следующие: 1,05 пишут, если шов находится в наклонной поверхности, 1,10 для вертикальных швов, а 1,2 потолочных. Есть стандартные данные по объему использования электродов в которых приведены значения для разных типов. Но независимо от стандартных данных на практике результаты могут отличаться от заданных.
Расход электродов на метр можно определить и самостоятельно. Он складывается из массы наплавленного металла и потерь (к ним относится разбрызгивание, образование шлака, огарки). Для начала вычислим массу наплавленного металла по формуле:
Масса = площадь поперечного сечения шва * плотность металла * длина шва
Значения плотности легко узнать из справочной литературы (плотность углеродистой стали — 7,85 г/куб.см, никельхромовой стали — 8,5 г/куб.см). Затем по второй формуле рассчитаем суммарный расход электродов при сварке:
Норма расхода = масса наплавленного металла * коэффициент расхода
Коэффициент расхода зависит от конкретной марки электрода. Эти данные приводятся в нормативных документах, таких как ВСН 452-84 (см. следующий раздел). Чтобы вычислить расход в килограммах на погонный метр (кг/м), нужно принять длину шва в первой формуле за 1 метр.
Коэффициенты расхода электродов
Коэффициент | Марки электродов |
1,5 | АНО-1, ОЗЛ-Э6; ОЗЛ-5; ЦТ-28; ОЗЛ-25Б |
1,6 | АНО-5, АНО-13, ЦЛ-17, ОЗЛ-2, ОЗЛ-3, ОЗЛ-6, ОЗЛ-7, ОЗЛ-8, ОЗЛ-21, ЗИО-8, УОНИ-13/55У |
1,7 | ОЗЛ-9А, ГС-1, ЦТ-15, ЦЛ-9, ЦЛ-11, УОНИ-13/НЖ, УОНИ-13/45 |
1,8 | ОЗС-11, ОЗЛ-22, ОЗЛ-20, НЖ-13, ВСЦ-4, К-5А |
1,9 | АНЖР-2, ОЗЛ-28, ОЗЛ-27 |
Поправочные коэффициенты
Для более точного расчета применяют корректирующие коэффициенты. Их полный перечень можно найти в ВСН 452-84. Приводим примеры поправок в зависимости от рабочих задач:
• При сварке поворотных стыков
Тип сварки | Тип электрода | Коэффициент |
MMA-сварка | для покрытых электродов | 0,826 |
TIG-сварка | для электрода плавящегося | 0,930 |
для электрода вольфрамового неплавящегося | 1 |
• При вваривании патрубков, расположенных под углом к основной оси трубы (по умолчанию величина угла принимается за 90°)
Угол соединения | Коэффициент |
60° | 1,1 |
45° | 1,23 |
• При положении патрубков сбоку или снизу по отношению к основной трубе
Тип сварки | Тип электрода | Коэффициент (патрубок сбоку) | Коэффициент (патрубок снизу) |
MMA-сварка | для покрытых электродов | 1,12 | 1,26 |
TIG-сварка | для сварочной проволоки | 1,0 | 1,35 |
Для более точного расчета сметы на работы необходимо проводить практические пробные работы, позволяющие точно сосчитать расход. Но нужно учитывать погрешность и брать запас 5-7%. Для экономии материалов нужно правильно настраивать оборудование: силу тока и его напряжение, и следовать правилам. Сэкономить иногда получается за счет наклона руки под другим углом.
Иногда используются прерывистые швы, где не нужно полного соединения. Они экономят средства и время. Экономия еще может достигаться за счет применения автоматической сварки, которая сокращает объем поперечного сечения. Можно сэкономить на 30%, если следовать вышеуказанным параметрам.
Для чего нужны те или иные электроды?Для сварки сталей содержащих углерод и низколегированных применяют электроды: Э38, Э42, Э46, Э50, Э42 А, Э46 А, Э50 А. У данных электродов на разрыве самая высокая точка прочности — 490 МПа. Для этих работ также применяют электроды приделом прочности более 490 и до 588 МПа Э55,Э60.
для стали легированной более высокой прочности применяют электроды марок: Э70, Э85, Э100, Э125, Э15. Они более 588 МПа.
Для устойчивых к теплу сталей применяют электроды, например, Э-09 М, Э-09МХ, Э-09 Х1.
При сваривании сталей с особыми характеристиками и высокой легированностью нужны электроды Э — 12 Х 13, Э — 06 Х13Н, Э — 10 Х 17Т.
Для припления верхних слоев с нестандартными характеристиками используют 44 вида электродов, например, Э — 10 Г2, Э — 10 Г3, Э — 12 Г4.
таблица, калькулятор, 1 тонну металлоконструкций, норма для сварочных работ
!—www.miralinks.ru —>
Если вам необходимо определить расход электродов или если вы хотите рассчитать сколько необходимо закупить сварочных материалов, то всё это вы найдёте в нашей статье.
Мы подготовили для вас калькуляторы (расчётные программы), подробно описали методику расчёта, описали причины высокого расхода сварочных материалов и способы как их снизить без ущерба для качества.
Содержание
- Параметры влияющие на расход
- Теория и практика расчета
- Погрешность
- Расход электродов на 1 тонну металлоконструкций
- Норма расхода электродов
- Расчет количества электродов на 1 метр шва
- Калькулятор расчет электродов для трубы
- Калькулятор расчет электродов для металлоконструкций
- Расчетные таблицы
- Для соединения без разделки кромок — С2
- Для соединений с V-образной разделкой C17
- Для угловых швов — У6
- Для угловых швов (без разделки кромок) – У4
- Для таврового соединения – Т3
- Для таврового соединения – Т8
- Для ремонта (подварки)
- Поштучный расход электродов
- Расчет расхода при сварке труб
- Расчет расхода при сварке профиля
- Какое количество электродов в 1 кг
- Как уменьшить расход
Параметры влияющие на расход
Основными факторами, от которых зависят потери сварочных материалов являются:
- Конструктивные параметры шва.
- Продолжительность процесса.
- Род тока.
- Полярность (для постоянного тока).
- Физико-химические свойства используемых материалов.
К конструктивным параметрам относятся наличие или отсутствие разделки кромок и её вид. Если при использовании v-образной разделки кромок, расход будет значительно выше нежели чем при сварке без разделки.
Также конструктивным параметрам относятся размеры катета шва для угловых, тавровых и нахлесточных соединений. Размер катета определяется конструктором при проектировании путём расчёта. Его усреднённые значение можно взять из нормативного документа.
Продолжительность выполнение процесса увеличивает потери материалов из-за угара металла. Стараться выполнять операции непродолжительно.
А на этапе проектирования стараться избегать выполнения ручными способами (ручная дуговая сварка) швов большой длинны или толщины, применяя вместо них полуавтоматические или автоматические способы.
Род тока, используемый при сварке, бывает: переменный и постоянный. На переменном токе происходит существенные траты металла потому как происходит разбрызгивание. При наличии выбора на каком токе варить, для экономии сварочных материалов лучше применять постоянный ток.
Полярность при сварке постоянным током бывает: прямой и обратный. При проведении процесса на прямой полярности разбрызгивание металла больше. Потому необходимо применять сварку на обратной полярности.
Физические и химические свойства применяемых электродов во многом влияют на угар металла.
В таблице ниже, приведены коэффициенты расхода в зависимости от используемой марки электродов (от их физико-химических свойств).
Допустимые нормы расхода электродов при сварочных работах определяются различными нормативными документами, в частности, ВСН 452-84. В этом документе указывается нормальный потери электродного металла для различных разделок кромок и категорий конструкций.
Также в нём указывается масса наплавленного металла для различных видов соединений, что необходимо на этапе проектирования.
Черные стали (конструкционные, углеродистые, низколегированные)
79.81%
Нержавейку
15.73%
Цветные металлы (алюминий, медь, титан и т.д.)
2.35%
Прочее
2.11%
Проголосовало: 426
Теория и практика расчета
Разница в теории и практике во многом зависит от условий, в которых будет выполняться сварка, а также от мастерства сварщика которое определяется разрядом. О том что такое разряды сварщиков и какие они бывают читайте в нашей статье по ссылке.
Если процесс будет проходить на ветру или в неудобных условиях (в тесноте, где нету нормального доступа), то сварщик будет жечь больше электродов. Поэтому условия выполнения сварки необходимо учитывать при расчёте.
Если руководствоваться ВСНом, то можно использовать метод расчёта по коэффициенту потерь. Его формула имеет следующий вид:
G=m * K.
К – коэффициент потери, применяемый для различных марок, которые мы приводили выше в таблице (диапазон 1,5 -1,9).
М — это масса наплавляемого металла. Это значение рассчитывают путем перемножение площади сечение наплавляемого металла на его плотность (m = p*F).
В итоге получаем следующую формулу для расчета потерь на 1 м шва:
H= P * F * K.
Если нужно определить потери на конкретную длину, в таком случае формула имеет вид:
H= P * F * K * L.
где L — это значение длинны. В некоторых источниках данные формула имеет другой вид:
Н=G * L
где G= K * m — её называют удельная норма расхода;
L — все так же значение длины шва.
Расчёт потерь на практике определяется не формулами, а экспериментально.
Для этого предварительно производится взвешивание электродов. Далее два сварщика сваривают однотипные соединения (той же толщины, диаметра и разделки кромок), которые будут выполняться при производстве работ.
В результате производится контрольное взвешивание оставшихся сварочных материалов и сравнение полученных результатов с значениями теоретического расчёта. Отсюда и получается коэффициент практического расх.
Расход пр. / Расх. теор. = Коэф. расх. пр.
Далее при заказе материалов значения полученные при теоретическом расчёте умножаются на коэффициент практического расх.
Пример: если при расчете мы получили значение 10 кг, а коэффициент расх. пр. равен 1,42, то для получения практического расхода:
10 кг*1,42 = 14,2 кг. Таким образом получаем реальные потери.
Погрешность
Даже использование данных, полученных практическим путем, не даёт гарантий что потери не увеличатся. Часто при выполнении работ на объекте может быть ветер, скачки напряжения, а также могут применяться не до конца просушенный материалы и множество других факторов, которые повлияют на перерасход.
Также в процессе работы могут быть выявлены бракованные электроды: ржавые, с отколотой или вспучившейся обмазкой. Их нельзя будет использовать.
Хафизов Ильдар
Специалист НАКС IV уровня
Задать вопрос
Исходя из практического опыта, при заказе электродов рекомендую дополнительно закладывать от 3 до 5%, чтобы гарантированно обеспечить непрерывность процесса. Потому как доставка материалов в случае их нехватки требует гораздо больших затрат.
Чтобы не было неприятностей с большим количеством бракованных материалов при покупке необходимо одну пачку из партий вскрыть и произвести сварку пробных образцов. Этим можно определит качество электродов и их пригодность.
Это может существенно сэкономить бюджет, если приобретается большое количество материалов (более 1 тонны).
Если Вам необходима 👉 сварочная документация 👈: техкарты, ПСР или любые другие документы по сварке, резке и контролю обращайтесь к нам. Наша документация по сварке будет разработана специально для решения ваших задач, отвечая всем вашим требованиям.
Расход электродов на 1 тонну металлоконструкций
Подсчитать потери электродов можно исходя из массы свариваемых металлоконструкций — на тонну металла. Это достаточно грубый подсчёт. Его можно использовать в тех случаях, когда предстоит большой объём работ. Полученный результат является верхней планкой по расходу сварочных материалов.
Формула, следующая:
H= 0,011* Mкр.;
H — Требуемое количество электродов
Мкр. — Масса свариваемые металлоконструкции.
Норма расхода электродов
Все основные нормы расхода для различных конструкций указаны в следующих нормативных документах:
- ВСН 416-81;
- ВСН 452-84.
Указанные нормативные документы учитывают: способ сварки, тип соединения, толщину детали.
Расчет количества электродов на 1 метр шва
Чтобы определить затраты материала на 1 м, лучше всего воспользоваться таблицами который вы сможете найти в нашей статье ниже. В таблицах уже указан расход количество только на сварочной операции. При расчете общего количества необходимо учесть и потери материалов на выполнение прихваток.
Для этого необходимо воспользоваться следующей формулой:
Н = Нсв + Нп.
где H — искомое количество электродного металла, который потребуется на сварку длинной 1 м.
Нсв — расход на сварочную операцию — значение из таблицы;
Нп — Расход на выполнение прихватки.
Значение Нп рассчитывают по формуле:
Нп = 0,15*Нсв
Для толщины свариваемых деталей менее 12 мм.
В случае если толщина больше 12 мм, то формула имеет вид:
Нп = 0,12*Нсв
Для удобства расчёта расхода электродов на 1 м шва используйте калькуляторы сделанные нашими специалистами. Их Вы можете скачать себе на компьютер или открыть онлайн.
Калькулятор расчет электродов для трубы
Для расчета при сварке труб
Скачать калькулятор
Калькулятор расчет электродов для металлоконструкций
Для расчета при сварке листов и профильных конструкций
Скачать калькулятор
Полезная статья — Какими электродами варить нержавейку
Расчетные таблицы
Для проведения расчёта необходимого количества исходя из наплавки 1 кг металла следует использовать данные из таблицы ниже.
Пример: для наплавки 1 кг металла ОЗЛ-25Б потребуется 1,4 кг этих электродов, а для АНЖР-2 необходимо 1,9 кг.
Группа | Необходимое количество электродов, кг | Марки |
I | 1,4 | ОЗЛ-25Б, ВСФ-75У; ОЗЛ-25Б; ВСФ-85; ОЗШ-1; ВСЦ-4А; |
II | 1,5 | УОНИ-13/45; ОЗЛ-Э6; ТМУ-21У; ОЗЛ-5; ЦТ-28; ТМЛ-3У ОЗЛ-25Б; АНО-11 |
III | 1,6 | ЦЛ-17, ОЗЛ-7, ОЗЛ-2; ОЗЛ-3; ОЗЛ-21, ЗИО-8; УОНИ-13/55К; ЦУ-5 |
IV | 1,7 | ОЗЛ-9А; ЦТ-15; ОЗЛ-37-1; АНЖР-ЗУ; УОНИ-13/НЖ; ОЗС-24 |
V | 1,8 | ОЗЛ-20, ОЗС-11, НЖ-13 |
VI | 1,9 | АНЖР-2; ОЗЛ-27 |
Если необходимо рассчитать количество исходя из длины шва, то следует использовать данные из таблиц ниже.
Для соединения без разделки кромок — С2
Данные для расчёта необходимого количества материалов для стыковых швов без разделки кромок и без подварки корня с обратной стороны.
Толщина, мм | Требуемое количество, кг/ 1 метр | |||
Нижнее | Вертикальное | Горизонтальное | Потолочное | |
1 | 0,063 | 0,071 | 0,071 | 0,079 |
2 | 0,131 | 0,147 | 0,148 | 0,165 |
3 | 0,144 | 0,161 | 0,163 | 0,181 |
4 | 0,278 | 0,311 | 0,314 | 0,350 |
Для соединений с V-образной разделкой C17
Данные для расчёта необходимого количества материалов для стыковых швов с двухсторонней V-образной разделкой кромок, без подварки корня с обратной стороны.
Толщина деталей, мм | Требуемое количество, кг/ 1 метр | |||
Нижнее | Вертикальное | Горизонтальное | Потолочное | |
3 | 0,188 | 0,211 | 0,212 | 0,237 |
4 | 0,238 | 0,267 | 0,269 | 0,300 |
5 | 0,299 | 0,335 | 0,338 | 0,377 |
6 | 0,413 | 0,463 | 0,467 | 0,520 |
7 | 0,501 | 0,561 | 0,566 | 0,631 |
8 | 0,600 | 0,672 | 0,678 | 0,756 |
9 | 0,751 | 0,841 | 0,849 | 0,946 |
10 | 0,875 | 0,980 | 0,989 | 1,103 |
12 | 1,191 | 1,334 | 1,346 | 1,501 |
14 | 1,525 | 1,708 | 1,723 | 1,922 |
16 | 2,012 | 2,253 | 2,274 | 2,535 |
18 | 2,734 | 3,062 | 3,089 | 3,445 |
20 | 3,210 | 3,595 | 3,627 | 4,045 |
22 | 3,780 | 4,234 | 4,271 | 4,763 |
24 | 4,343 | 4,864 | 4,908 | 5,472 |
26 | 4,998 | 5,598 | 5,648 | 6,297 |
28 | 5,647 | 6,325 | 6,381 | 7,115 |
30 | 6,388 | 7,155 | 7,218 | 8,049 |
32 | 7,122 | 7,977 | 8,048 | 8,974 |
34 | 7,950 | 8,904 | 8,984 | 10,017 |
36 | 8,770 | 9,822 | 9,910 | 11,050 |
38 | 9,695 | 10,858 | 10,955 | 12,216 |
40 | 10,601 | 11,873 | 11,979 | 13,357 |
42 | 11,625 | 13,020 | 13,136 | 14,648 |
44 | 12,617 | 14,131 | 14,257 | 15,897 |
46 | 13,677 | 15,318 | 15,455 | 17,233 |
48 | 14,754 | 16,524 | 16,672 | 18,590 |
50 | 15,900 | 17,808 | 17,967 | 20,034 |
52 | 17,065 | 19,113 | 19,283 | 21,502 |
54 | 18,321 | 20,520 | 20,703 | 23,084 |
56 | 19,570 | 21,918 | 22,114 | 24,658 |
58 | 20,924 | 23,435 | 23,644 | 26,364 |
60 | 22,260 | 24,931 | 25,154 | 28,048 |
Для угловых швов — У6
Данные для расчёта необходимого количества при сварке угловых швов с разделкой кромок У6
Толщина деталей, мм | Требуемое количество, кг/ 1 метр | |||
Нижнее | Вертикальное | Горизонтальное | Потолочное | |
3 | 0,191 | 0,214 | 0,216 | 0,241 |
4 | 0,243 | 0,272 | 0,275 | 0,306 |
5 | 0,308 | 0,345 | 0,348 | 0,388 |
6 | 0,427 | 0,478 | 0,483 | 0,538 |
7 | 0,518 | 0,580 | 0,585 | 0,653 |
8 | 0,624 | 0,699 | 0,705 | 0,786 |
9 | 0,782 | 0,876 | 0,884 | 0,985 |
10 | 0,915 | 1,025 | 1,034 | 1,153 |
12 | 1,258 | 1,409 | 1,422 | 1,585 |
14 | 1,615 | 1,809 | 1,825 | 2,035 |
16 | 2,142 | 2,399 | 2,420 | 2,699 |
18 | 2,941 | 3,294 | 3,323 | 3,706 |
20 | 3,463 | 3,879 | 3,913 | 4,363 |
22 | 4,083 | 4,573 | 4,614 | 5,145 |
24 | 4,700 | 5,264 | 5,311 | 5,922 |
26 | 5,403 | 6,051 | 6,105 | 6,808 |
28 | 6,117 | 6,851 | 6,912 | 7,707 |
30 | 6,916 | 7,746 | 7,815 | 8,714 |
32 | 7,725 | 8,652 | 8,729 | 9,734 |
34 | 8,619 | 9,653 | 9,739 | 10,860 |
36 | 9,523 | 10,666 | 10,761 | 11,999 |
38 | 10,513 | 11,775 | 11,880 | 13,246 |
40 | 11,514 | 12,896 | 13,011 | 14,508 |
42 | 12,636 | 14,152 | 14,279 | 15,921 |
44 | 13,733 | 15,381 | 15,518 | 17,304 |
46 | 14,928 | 16,719 | 16,869 | 18,809 |
48 | 16,119 | 18,053 | 18,214 | 20,310 |
50 | 17,396 | 19,484 | 19,657 | 21,919 |
52 | 18,683 | 20,925 | 21,112 | 23,541 |
54 | 20,068 | 22,476 | 22,677 | 25,286 |
56 | 21,452 | 24,026 | 24,241 | 27,030 |
58 | 22,933 | 25,685 | 25,914 | 28,896 |
60 | 24,412 | 27,341 | 27,586 | 30,759 |
Для угловых швов (без разделки кромок) – У4
Данные для расчёта необходимого количества материалов для угловых швов без разделки кромок.
Толщина деталей, мм | Требуемое количество, кг/ 1 метр | |||
Нижнее | Вертикальное | Горизонтальное | Потолочное | |
1 | 0,135 | 0,151 | 0,153 | 0,170 |
2 | 0,145 | 0,162 | 0,164 | 0,183 |
3 | 0,151 | 0,169 | 0,171 | 0,190 |
4 | 0,315 | 0,353 | 0,356 | 0,397 |
5 | 0,439 | 0,492 | 0,496 | 0,553 |
6 | 0,646 | 0,724 | 0,730 | 0,814 |
7 | 0,816 | 0,914 | 0,922 | 1,028 |
8 | 1,005 | 1,126 | 1,136 | 1,266 |
9 | 1,213 | 1,359 | 1,371 | 1,528 |
10 | 1,441 | 1,614 | 1,628 | 1,816 |
12 | 1,953 | 2,187 | 2,207 | 2,461 |
14 | 2,541 | 2,846 | 2,871 | 3,202 |
16 | 3,204 | 3,588 | 3,621 | 4,037 |
18 | 3,946 | 4,420 | 4,459 | 4,972 |
20 | 4,764 | 5,336 | 5,383 | 6,003 |
22 | 5,658 | 6,337 | 6,394 | 7,129 |
24 | 6,627 | 7,422 | 7,489 | 8,350 |
26 | 7,674 | 8,595 | 8,672 | 9,669 |
28 | 8,797 | 9,853 | 9,941 | 11,084 |
30 | 9,996 | 11,196 | 11,295 | 12,595 |
Для таврового соединения – Т3
Если нужно рассчитать количество электродов для тавровых соединений ниже он приведена таблица с данными для расчёта таврового соединения T3. Этими нормами также можно руководствоваться для сварки нахлесточного соединения Н2.
Толщина деталей, мм | Требуемое количество, кг/ 1 метр | |||
Нижнее | Вертикальное | Горизонтальное | Потолочное | |
1 | 0,040 | 0,045 | 0,045 | 0,050 |
2 | 0,108 | 0,121 | 0,122 | 0,136 |
3 | 0,204 | 0,228 | 0,231 | 0,257 |
4 | 0,322 | 0,361 | 0,364 | 0,406 |
5 | 0,472 | 0,529 | 0,533 | 0,595 |
6 | 0,646 | 0,724 | 0,730 | 0,814 |
7 | 0,844 | 0,945 | 0,954 | 1,063 |
8 | 1,072 | 1,201 | 1,211 | 1,351 |
10 | 1,604 | 1,796 | 1,813 | 2,021 |
12 | 2,244 | 2,513 | 2,536 | 2,827 |
14 | 2,988 | 3,347 | 3,376 | 3,765 |
16 | 3,838 | 4,299 | 4,337 | 4,836 |
18 | 4,450 | 4,984 | 5,029 | 5,607 |
20 | 5,862 | 6,565 | 6,624 | 7,386 |
22 | 7,032 | 7,876 | 7,946 | 8,860 |
24 | 8,306 | 9,303 | 9,386 | 10,466 |
26 | 9,686 | 10,848 | 10,945 | 12,204 |
28 | 11,176 | 12,517 | 12,629 | 14,082 |
30 | 12,770 | 14,302 | 14,430 | 16,090 |
32 | 14,470 | 16,206 | 16,351 | 18,232 |
34 | 15,328 | 17,167 | 17,321 | 19,313 |
36 | 18,186 | 20,368 | 20,550 | 22,914 |
38 | 19,408 | 21,737 | 21,931 | 24,454 |
40 | 22,328 | 25,007 | 25,231 | 28,133 |
Для таврового соединения – Т8
Для таврового соединения с разделкой кромок ниже приведены данные для Т8 с двухсторонней разделкой.
Толщина деталей, мм | Требуемое количество, кг/ 1 метр | |||
Нижнее | Вертикальное | Горизонтальное | Потолочное | |
8 | 0,843 | 0,944 | 0,953 | 1,062 |
10 | 1,119 | 1,253 | 1,264 | 1,410 |
12 | 1,576 | 1,765 | 1,781 | 1,986 |
14 | 1,929 | 2,160 | 2,180 | 2,431 |
16 | 2,470 | 2,766 | 2,791 | 3,112 |
18 | 3,512 | 3,933 | 3,969 | 4,425 |
20 | 4,022 | 4,505 | 4,545 | 5,068 |
22 | 4,840 | 5,421 | 5,469 | 6,098 |
24 | 5,422 | 6,073 | 6,127 | 6,832 |
26 | 6,366 | 7,130 | 7,194 | 8,021 |
28 | 7,022 | 7,865 | 7,935 | 8,848 |
30 | 8,090 | 9,061 | 9,142 | 10,193 |
32 | 8,821 | 9,880 | 9,968 | 11,114 |
34 | 10,015 | 11,217 | 11,317 | 12,619 |
36 | 10,819 | 12,117 | 12,225 | 13,632 |
38 | 12,138 | 13,595 | 13,716 | 15,294 |
40 | 13,017 | 14,579 | 14,709 | 16,401 |
42 | 14,461 | 16,196 | 16,341 | 18,221 |
44 | 15,412 | 17,261 | 17,416 | 19,419 |
46 | 16,983 | 19,021 | 19,191 | 21,399 |
48 | 18,008 | 20,169 | 20,349 | 22,690 |
50 | 19,703 | 22,067 | 22,264 | 24,826 |
52 | 20,803 | 23,299 | 23,507 | 26,212 |
54 | 22,624 | 25,339 | 25,565 | 28,506 |
56 | 23,797 | 26,653 | 26,891 | 29,984 |
58 | 25,743 | 28,832 | 29,090 | 32,436 |
60 | 26,989 | 30,228 | 30,498 | 34,006 |
Полезная статья – Как найти себя по фамилии в реестре сварщиков НАКС
Для ремонта (подварки)
Если необходимо выполнить ремонт сварного соединения и нужно рассчитать количество материалов, Вам необходимо использовать данные из таблицы, приведённой ниже.
Без подварки корня шва | С подваркой корня шва | |||
Толщина деталей, мм | Требуемое количество, кг/ 1 метр | Толщина деталей, мм | Глубина ремонтной выборки, мм | Требуемое количество, кг/ 1 метр |
2-3 | 0,11 | 8-12 | 3 | 0,388 |
4-5 | 0,134 | 12-28 | 4 | 0,539 |
6-8 | 0,179 | св. 30 | 5 | 0,784 |
Ручная дуговая электродами (MMA)
56.16%
В среде аргона неплавящимся электродом (TIG)
8.22%
Полуавтоматическая сварка в СО2 или др. газах (MAG-MIG)
24.66%
Под слоем флюса
2.74%
Газовая
8.22%
Проголосовало: 73
Поштучный расход электродов
Если необходимо посчитать расход количества в штуках, то это можно сделать, воспользовавшись следующей формулой:
N=H/Mэл,
где Н — это общий расход в кг;
Мэл — масса одного электрода (берется из таблицы ниже).
Таблица — Масса 1 шт. — (Мэл)
Диаметр, мм | Масса, кг |
2,5 | 0,02 |
3,0 | 0,032 |
4,0 | 0,053 |
5,0 | 0,083 |
H — берется из таблицы (или рассчитывается по формулам, описанным выше), с учетом длинны шва. Так как данные в таблицы даны на 1 метр сварочного шва.
Пример расчета: если свариваемые детали толщиной 3 мм с разделкой С17 вариться будут в вертикальном положении электродами 2,5 мм, то значение Н по таблице на 1 м шва равняется 0,211 кг. Если сваривать нужно 2 м шва, то Н=2*0,211=0,422 кг.
В этом случае расчет электродов будет такой: N=0,422/0,02=22 шт.;
Полезная статья — Как варить нержавейку электродом
Расчет расхода при сварке труб
Если предстоит сварка труб и нужно посчитать расход электродов при сварке, то можно воспользоваться следующими способами:
- Воспользоваться нашим калькулятором.
- Найти данные в таблицах из ВСН 416-81 и ВСН 452-84 в которых уже приведена норма расхода электродов на 1 стык.
В тех же случаях, когда нужный типоразмер трубы отсутствует в таблицах ВСН можно воспользоваться следующей формулой:
Нт=Н*lшва
где Н — расход на 1 требуемой разделки (данные приведены в таблице ниже)
lшва — длина шва, она считается по формуле длины окружности — lшва=Dтр * 3,14
С2 | |
Толщина деталей, мм | Н, кг/ 1 метр шва трубы |
3 | 0,119 |
4 | 0,162 |
5 | 0,183 |
С17 | С19 | ||
Толщина деталей, мм | Н, кг/ 1 метр шва трубы | Толщина деталей, мм | Н, кг/ 1 метр шва трубы |
4 | 0,382 | 3 | 0,415 |
5 | 0,513 | 4 | 0,535 |
6 | 0,665 | 5 | 0,679 |
7 | 0,834 | 6 | 0,955 |
8 | 1,099 | 8 | 1,378 |
10 | 1,676 | 10 | 2,004 |
12 | 2,18 | 12 | 2,571 |
14 | 2,785 | 15 | 4,137 |
16 | 3,486 | 16 | 4,534 |
18 | 4,157 | 18 | 5,378 |
У18 | У19 | ||
Толщина деталей, мм | Н, кг/ 1 метр шва трубы | Толщина деталей, мм | Н, кг/ 1 метр шва трубы |
6 | 0,511 | 6 | 0,799 |
8 | 0,862 | 8 | 1,183 |
10 | 1,301 | 10 | 1,584 |
12 | 1,831 | 12 | 2,484 |
14 | 2,45 | 14 | 3,123 |
16 | 3,157 | 16 | 3,769 |
18 | 3,956 | 18 | 4,372 |
20 | 4,843 | 20 | 4,833 |
У5 | ||
Толщина деталей, мм | Н, кг/ 1 метр шва трубы — до.![]() | Н, кг/ 1 метр шва трубы — св. Ø194 |
6 | 0,643 | 0,672 |
7 | 0,78 | 0,813 |
8 | 0,933 | 0,969 |
10 | 1,289 | 1,333 |
12 | 1,707 | 1,76 |
14 | 2,19 | 2,249 |
16 | 2,737 | 2,805 |
18 | 3,349 | 3,424 |
20 | 4,024 | 4,107 |
Пример расчета: Для трубы диаметром 89х7, разделка С17, неповоротный стык. Из таблицы приведённых выше для разделки С17 при сварке в потолочном положении выбираем соответствующее значение расхода Н — 0,834. Далее производим расчет Нт=0,089*3,14*0,834= 0,233 кг на 1 стык.
Расчет расхода при сварке профиля
При сварке профиля такого как двутавр, швеллер профильная труба и так далее используются те же нормы что и для сварки листового металла. Их методика приведена в разделе — ЗДЕСЬ.
Важной особенностью, которую стоит учитывать, это длительность проведение процесса. Чем более длинные швы и более продолжительная сварка, тем выше процент угара металла, а соответственно выше потери.
Также зачастую сварка металлоконструкций происходит на высоте что осложняет процесс работы и увеличивает потери. Здесь существует простая закономерность — чем сложнее сварщику работать, тем больше будет затрачено материалов и времени.
Какое количество электродов в 1 кг
Зависимости от диаметра, количество электродов в одном килограмме отличается. Данные для различных диаметров приведены в таблице ниже
Диаметр, мм | Штук в 1 кг |
2,5 | 50 |
3,0 | 31 |
4,0 | 19 |
5,0 | 12 |
Как уменьшить расход
Для уменьшения потерь сварочных материалов без ухудшения качества получаемых изделий, можно использовать следующие рекомендации:
- При покупке крупных партий проводить входной контроль и проверять качество электродов.
Это позволит выявить некачественные материалы, которые будут забракованные или использованы лишь частично.
- Применять полуавтоматические и автоматические методы сварки в тех случаях, где это возможно. При сварке в среде защитных газов использовать в смеси газов, содержащие гелий и аргон для снижения разбрызгивания.
- Проводить процесс на постоянном токе и использовать обратную полярность.
- Выполнять процесс на оптимальных режимах (без завышения силы тока) для уменьшения угара.
Напишите в комментариях как вы считаете, что больше всего влияет на расход.
Расчет расхода электродов при ручной дуговой сварке
Главная » Статьи » Расчет расхода электродов при ручной дуговой сварке
Нормы расхода электродов при сварке – методики и особенности расчета
Сварочное «искусство» в последнее время набирает огромные обороты развития. Появились новые методы сварки, которые вовсе не требуют вмешательства человека, и модернизируются старые и надежные способы ручной сварки. Если вам интересно узнать о сварке тонкого металла и об особенностях электродов для обеспечения сварочных процессов, то рекомендуем прочитать данную статью.
Аппараты для электрической дуговой сварки могут применяться, в том числе, и для резки металлических элементов и конструкций. Для получения лучших результатов рекомендуется использовать специальные электроды для резки металла, различающиеся по конструкции и используемым при их изготовлении материалам.
Расчет режима сварки довольно трудоемкий процесс. Однако эта статья поможет вам пошагово сделать его гораздо легче. Мы детально описали типы режимов расчета сварки в углекислом газе.
stalevarim.ru
Расход электродов
Подсчет расхода сварочных электродов необходим еще на первоначальном этапе, когда вы только начинаете планировать работы по сварке.
Для того чтобы как можно точнее рассчитать нужное количество электродов, вам нужно будет учитывать главные факторы: массу наплавленного металла, норму расхода сварочных электродов и длину шва.
Если все расчеты будут произведены правильно и максимально точно, то и сам процесс сварки будет эффективным.
Норма – максимальная величина абсолютного расхода сварочного материала, других материалов, например, топлива, электроэнергии. В том числе, сюда можно отнести расход энергии живого труда в соотношении на единицу производимой продукции.
Например, если говорить о норме расхода электродов, газов, флюсов, соотношение приходится на производство одного изделия в соответствии со всеми техническими требованиями либо на процесс сваривания одного метра шва металла.
Отмечают классификацию, разработанную на основе степени выполняемой работы. Данная классификация включает в себя пооперационные, подетальные, узловые и поиздельные нормы.
К пооперационной норме относят нормы, которые были установлены в соответствии с выполняемой технологической операции, то есть норма расхода электродов в процессе сварки. Поодетальные нормы – это нормы, которые определяет затраты труда при изготовлении конкретной детали металла.
С помощью узловых и поиздельных норм устанавливаются расходы материалов как на каждый конкретный узел в отдельности, так и на материал в целом. Для разработки поиздельных норм использовали узловые нормы. Последние же, были основаны на подетальных нормах. Как видно, все нормы взаимосвязаны между собой.
Расход электродов при сварке представляет собой определенную величину, расчет которой ведут специалисты. Они же будут выполнять все работы по сварке материала. Это значительно облегчает работу, так как все расчеты будут соответствовать всем нюансам, связанными со сварочными работами.
Для расчета расходов электродов при сварке разработано множество методик. Например, в некоторых странах применяют методику по определению нужного количества электродов с помощью массы металла. Поэтому единицей измерения становятся килограммы. Для того чтобы рассчитать количество электродов необходимо произвести вычисления по данной формуле: Н=М*Красх., где М — масса металла, а сокращенное Красх. — коэффициент расхода электродов.
С целью вычисления массы металла нужно перемножить площадь поперечного сечения металла с плотностью и длиной шва. Рассчитывая коэффициент расхода электродов, помните что угар, разбрызгивание металла, длина огарка существо влияют на выходные данные. Все они непосредственно зависят от марки электрода. Обычно это коэффициент равен 1,6, но в сварке нержавеющих и огнеупорных элементов коэффициент может быть равен 1,8.
Если возникают трудности с расчетом массы в теории, то пора переходить к практике. Для начала нужно выполнить сварочные работы с металлом определенного количества подходящей марки электрода. Необходимо использовать тот же тип соединения, тот же режим сварочного тока и положение в пространстве. Потом определите длину шва и рассчитайте необходимое количество электродов.
Так как расходы сварочных электродов растет, то на ум приходит вопрос о том, как же сэкономить электроды в процессе сварки. Ответ прост: контролируйте полное соответствие типа, показателей силы тока и напряжения электродов.
Кроме того, используйте при расчетах автоматическую/полуавтоматическую сварку. Такие виды сварочных работ способствуют уменьшению расходом электродов при сварочных работах. В процессе ручной сварки процент показателя равен 5%, а при автоматической и полуавтоматической – менее 3 %.
Все необходимые показатели плавления металла напрямую зависят от технологии плавления и глубины емкости печи. Среди всех показателей, основными, определяющие эффективность электроплавки являются производительность, мощность и расход электроэнергии на 1 тонну расплавленной стали, а также расход электродов на тонну металла, в данном случае, стали.
Существуют определенные инженерно-технические нормы расхода сварочных работ. Согласно производственным нормативам указывается расход сварочных электродов при сварке труб из легированных сталей. Сюда относят дуговую ручную сварку, автоматическую, комбинированную и т.д.
Для того чтобы осуществить процесс аргонодуговой, дуговой, комбинированной сварки, необходимо принимать во внимание некоторые особенности сварочных соединений, то есть строгое соответствие государственным стандартам, размеры и нормы. Все электроды принято делить на шесть групп. Первую группу составляют электроды, коэффициент которых равен 1,4. Если электрод не соответствует ни одному коэффициенту, то рассчитывать норму расхода нужно по формуле Н=МхК, где H –это значение расхода электродов, М – как уже было отмечено, масса, K – коэффициент.
Ведя расчеты электродов при ручной дуговой и аргодуговой сварке в горизонтальном пространственном положении стыков, воспользуйтесь поправочными K. Для вольфрамового коэффициента К=1, для аргонового K=1, 43. Кроме того, допустима сварка патрубков, расположенных на поверхности трубопровода перпендикулярно оси трубопровода под углом в 90 градусов. Если патрубок находит снизу или с боковой стороны, коэффициенты будут другими.
Таблица коэффициентов электродов в соотношении к маркам электродов
myfta.ru
Подсчет расхода электродов
- Дата: 29-06-2015
- Просмотров: 375
- Рейтинг: 24
Во время сварки применяются присадочные изделия, они участвуют в расплавлении материала, формировании шва. При подготовке сварочного процесса необходимо учитывать расход электродов. Этот показатель будет зависеть от вида материала, метода сварки. При расчете учитывается норма расхода, для вычисления применяются специальные формулы. Стоит отметить, что применение автоматической или же полуавтоматической сварки в разы выгоднее, так как сокращаются затраты на необходимые материалы.
Схема образования и отрыва капель при сварке без замыкания дугового промежутка.
Как провести расчет?
Расчет расхода электродов может осуществляться несколькими методами, их подбор зависит от условий работы. Лучше всего, если расчет будет проводить специалист, он сможет точно определить, есть ли необходимость замены расходных материалов, какие меры можно принять для сокращения стоимости сварки.
Среди методов следует отметить:
Теоретический расчет. Сегодня существует несколько методик, которые позволяют точно определить количество присадочного материала. Обычно для работы применяется формула:
Н = М * К, где
Положение электрода при сварке.
- М — наплавляемый металл, масса в килограммах;
- К — специальный коэффициент.
Но при использовании такой формулы надо учесть следующее:
- для расчета требуется значение площади поперечного сечения, оно умножается на плотность обрабатываемого материала, на длину сварного шва;
- придется учитывать и марку присадки.
Даже если все расчеты проведены правильно, стоит прибавить 5-7% к полученным данным, чтобы в самый неподходящий момент не пришлось прерывать процесс и отправляться в магазин.
Практический метод расчета. Каким должен быть расход электродов, как его рассчитать? Надо правильно определить массу металла, после чего провести тестовые сварные работы. После их окончания замеряется огарок, учитывается сила тока, напряжение, длина сварного получившегося шва. На основании полученных данных определяется количество присадочных материалов, которое необходимо для получения определенной длины сварного шва. Следует учесть, что все условия работы требуется повторять в точности, включая угол положения и внешние данные. В противном случае данные окажутся бесполезными. Обычно таким методом пользуются, если нет возможности брать табличные данные. Но он ничем не хуже табличного, особенно если повторить эксперимент 3-4 раза. В итоге результаты получатся гораздо точнее.
Как уменьшить расходные данные?
Способы выполнения швов при сварке.
С целью экономии расхода электродов при сварке требуется соблюдать определенные условия:
- Во время настройки аппарата необходимо, чтобы напряжение, сила тока полностью соответствовали выбранному присадочному изделию.
- Если требуется значительная экономия количества электродов, то лучше всего использовать автоматический/полуавтоматический процесс, который при отличном качестве обеспечивает хорошее сокращение объема расходных изделий.
- Сокращение расхода электродов может наблюдаться и при изменении их положения во время сварочного процесса.
Если правильно выбрать метод экономии, то можно добиться примерно 30% сокращения присадочных материалов.
Процесс будет не таким затратным, но при этом его качество сохранится на должном уровне.
Какими могут быть затраты?
Нормы расхода электродов могут быть различными. Они зависят от вида сварочного процесса, от обрабатываемого металла. Можно отметить следующие значения сварочных электродов:
При сварке нержавеющей, малоуглеродистой стали:
- сварочная проволока: на 1 т — 8,1-9,7 кг, на 100 м² при толщине в 1,2-3 мм — 7,6-23 кг;
- двуокись углерода: на 1 т — 7,2-10 кг, на 100 м² при толщине в 1,2-3 мм — 6,8-24 кг;
- флюс: на 1 т — 8-10 кг, на 100 м² при толщине в 1,2-3 мм — 7,5-23 кг.
Если проводится сварка воздуховодов, то понадобится 28-32 кг материала на каждую тонну.
https://moyasvarka.ru/www.youtube.com/watch?v=v4L8XYbfD9s
При сварке алюминия, сплавов на основе алюминия:
- алюминиевая проволока: на 100 м² — 5-7 кг, на 1 м сварочного шва (на 2-3 мм) — 0,1-1,16 кг;
- при ручной аргоновой: на 100 м² — 1800-2700 л, на 1 м сварочного шва (на 2-3 мм) — 40 л;
- автоматическая/полуавтоматическая: на 100 м² — 700-1100 л, на 1 м шва (на 2-3 мм) — 12-16 л;
- вольфрамовые проволоки: на 100 м² — 10-15 кг, на 1 м шва (на 2-3 мм) — 02 г.
Расход электродов при сварке может быть различным, для вычисления его точного значения необходимо пользоваться специальными таблицами, формулами, нормами, которые позволяют определить все показатели в точности. При выборе оптимального режима и метода можно сэкономить на присадочных изделиях около 5%, а если покупать качественную присадку, то можно смело прибавлять еще пару процентов. Если учесть весь объем проделанных работ, то экономия получается существенной.
moyasvarka.ru
Расчет расхода электродов на 1 м шва
- 19 ноября
- 144 просмотров
- 33 рейтинг
Оглавление: [скрыть]
- Общие формулы для расчета
- Расчет поправочного коэффициента
Расход электродов на 1 м шва является важным показателем при составлении сметы на проведение сварочных работ. От точности расчета зависят экономические показатели всего проекта. Расчет расхода электродов должен производить опытный сварщик, хорошо разбирающийся в марках продукции и методиках сварочного процесса. Он должен учесть все нюансы предстоящих работ.
Схема сварочного электрода.
Общие формулы для расчета
За норму расхода принимается максимальное количество материалов, необходимых для производства сварочных работ. Нормирование должно учитывать расход электродов на сварку, прихватки и проведение правки способом «холостых валиков»:
Н = Нсв + Нпр + Нпр.
Норма на прихваточные работы и определяется в процентном отношении от расхода на основные работы:
- при сварке стали толщиной до 12 мм — 15%;
- при сварке стали толщиной более 12 мм — 12%;
- при сварке алюминиевых и титановых сплавов — до 20%.
Норма на правку изделий из алюминиевых и титановых сплавов составляет:
- для алюминия толщиной до 8 мм — 30%;
- для алюминия толщиной более 8 мм — 25%;
- для титана — 35-40%.
Марки электродов и их предназначение.
Расход электродов при изготовлении металлоконструкций определяется поузловыми, подетальными, поиздельными или пооперационными нормами. Все они связаны между собой и вычисляются исходя из расчета затрат материалов на 1 м сварного шва. Для конкретных типоразмеров затраты регламентируются согласно СНиП.
В расходную часть входит масса наплавленного металла и технологические потери:
N = M*K,
где N — норма расхода на 1 м,
M — масса наплавленного металла на 1 м,
K — коэффициент потерь.
Масса присадки на один метр шва (M) рассчитывается как произведение площади поперечного сечения (S), плотности материала (ρ) и длины шва (L = 1 м):
M = S* ρ* L
Площадь поперечного сечения берется по факту, а плотность материала — из справочной литературы. Для рядовых сталей она равняется 7,85 г/см³.
Вернуться к оглавлению
Значение коэффициента (K) включает в себя технологические потери на угар, разбрызгивание и огарки. Оно зависит от применяемых методов и режимов сварки, типов сварных материалов, сложности условий проведения работ.
Коэффициент отношения расхода материала к наплавленной массе для различных типов электродов приведен в таблице.
Таблица расхода электродов.
Данный показатель учитывает потери на разбрызгивание и угар, а также на огарок. При расчете потерь на огарок был взят огарок длиной 50 мм, остающийся от стандартного электрода длиной 450 мм. Если фактические значения длин отличаются, то применяют поправку.
λ = (lэ — 50)/(lэ — lо),
где lэ — длина электрода,
lо — длина огарка.
Значения потерь на разбрызгивание, угар и огарок указываются в паспортной характеристике сварочных материалов.
Сложность работ определяется расположением сварного шва. В случаях, если оно отличается от нижнего, вносят следующие поправочные коэффициенты:
- для расположенного в наклонной плоскости — 1,05;
- для расположенного в вертикальной плоскости — 1,10;
- для потолочного- 1,20.
Учесть все тонкости работ по сварке металла, основываясь только на теоретических расчетах, достаточно сложно. И хотя в СНиП подробно описаны нормы при различных видах сварки, рекомендуется провести испытательные работы.
Контрольные работы проводятся в тех же условиях и с применением тех же материалов, что и проектируемые. Для обеспечения бесперебойности процесса и предотвращения задержек, связанных с непредвиденными затратами материала, закупку материалов следует проводить с запасом 5-7%.
С целью экономии присадочных материалов необходимо соблюдать соответствующую им настройку напряжения и силы тока. Экономия может быть достигнута и изменением угла наклона руки в процессе сварки.
В изделиях, где не требуется особой плотности соединения, используются прерывистые швы 50-150 мм с расстоянием между ними 100-300 мм и более. За счет этого происходит значительная экономия времени и уменьшается расход электродов.
С целью значительного уменьшения затрат на проведение работ рекомендуется использовать автоматическую сварку, которая обеспечивает высокую производительность и позволяет экономить за счет уменьшения площади поперечного сечения, не уменьшая качество стыка. Комплекс мер может в результате дать экономию до 30%.
expertsvarki.ru
нормы, методики расчета для сварки труб
Главная » Сварка » Сварочные Материалы
Сварочные Материалы
Автор admin На чтение 4 мин. Просмотров 1.8k. Опубликовано
Расход электродов при сварке влияет и на продолжительность, и на производительность рабочего процесса. Ведь отработавший свое штучный электрод нужно заменить новым источником присадочного материала. Поэтому опытные сварщики держат под руками достаточное количество электродов.
Причем электроды еще нужно приготовить, прокалив в сушилке не менее полутора-двух часов. И в этой статье мы расскажем вам, как определяется это «достаточное количество».
Содержание
- Вводные параметры
- Норма расхода электродов на сварку
- Расход электродов при сварке труб – теоретические расчеты
- Сварка электродом — расход на практике
Вводные параметры
В качестве вводных данных при расчете количества расходуемых электродов фигурируют следующие параметры:
- Масса наплавки – вес металла, заполняющего стыковочный шов. Точный расчет наплавки приводится в технологической карте процесса сварки. А согласно грубым расчетам масса наплавки равна 1-1,5 процентам от общего веса металлоконструкции.
- Габариты сварочного шва, а точнее его длина. Ее измеряют с помощью рулетки по длине стыка. Причем результаты измерения нужно умножить на количество швов в разделе. Ведь глубокие стыки заваривают двумя-тремя швами, которые накладываются последовательно или параллельно.
- Нормы расхода на один погонный метр сварочного шва. Этот параметр определяется, исходя из множества критериев. Поэтому подробную методику определения норм мы приведем ниже по тексту.
Норма расхода электродов на сварку
Норма расхода – это масса наплавки в сварочном шве длиной в один метр.
Причем существуют следующие нормы расхода:
- Операционная, которая вычисляется в зависимости от типа сварочной операции.
- Детальная, которую вычисляют по массе наплавки в процессе сварки одной детали.
- Узловая, которую вычисляют по массе наплавки в процессе сварки конкретного узла металлоконструкции.
То есть, на конкретную норму расхода влияет и технология сварки, и форма сварочного шва и общее количество швов в металлоконструкции, и многое другое. Поэтому конкретные нормы расхода нужно определять либо по теоретическим выкладкам (формулам), либо по практическим наблюдениям.
Расход электродов при сварке труб – теоретические расчеты
Теория процесса расчета расхода электродов заключается в вычислении нормы расхода на один метр шва и делении этой величины на вес одного электрода. В итоге мы получаем норму расхода не в килограммах наплавки, а в поштучном исчислении количества электродов. После этого поштучная норма умножается на метраж, и результат округляется до целого значения (в большую сторону).
Норма расхода в килограммах определяется по массе наплавленного металла: объем раздела длинной в один метр умножается на плотность металла. Причем для упрощения расчета объем раздела можно вычислить, как объем цилиндра с диаметром, равным большей (внешней) стороне стыка.
Полученное значение увеличивают в 1,4-1,8 раза (поправка на огарки от электродов). Причем каждая из шести групп электродов имеет свое значение упомянутого коэффициента. Поэтому конкретные цифры стоит поискать в справочнике.
Формула подсчетов расхода выглядит следующим образом:
Н=Мк,
Где Н – это нормированный расход на метровый сварочный шов, М — это масса наплавленного металла в шве, к – это коэффициент поправки на огарки.
Сварка электродом — расход на практике
Если вы не сторонник сложных вычислений, то наилучшим способом определения расхода электрода для вас будет следующая методика:
- Вы берете две детали из нужного вам материала и один электрод нужного вам типа.
- Детали размещаются на сварочном столе в определенном положении, которое будет характерно для реальной сварочной операции. То есть вы имитируете условия формирования нижнего, вертикального или полочного шва.
- После этого вам остается только заварить стык между деталями, используя для этих целей один электрод.
- Далее, вы промеряете длину сварочного шва, который получили с помощью одного электрода.
Полученное значение – длину шва из одного электрода – сопоставляют с общей длиной сварочных швов, выходя на рекомендуемое количество прутков с присадочным материалом.
Указанный способ работает ничуть не хуже, чем табличный расчет. А если повторить этот эксперимент три-четыре раза, то среднее значение окажется намного точнее. Но в любом случае отклонения практического способа от теоретического вычисления расхода – малозначительны.
Testwork повышает производительность графитовых электродов
ТОРОНТО, 16 октября 2019 г. (GLOBE NEWSWIRE) — Hexagon Resources Limited (ASX:HXG) (« Hexagon » или « Company») ключ завершен испытания, направленные на усовершенствование графитовых электродов, используемых в электродуговых печах (ЭДП) по всему миру. Графитированные электроды являются неотъемлемой частью процесса производства стали в ЭДП и составляют значительную часть стоимости. Рынок этих графитовых электродов растет, и любые технологические достижения, которые продлят срок их службы и снизят уровень потребления, имеют значительную рыночную привлекательность.
Компания Hexagon рада сообщить о результатах своей успешной предварительной технической разработки по добавлению обработанного природного графита в качестве добавки к синтетическим графитовым электродам, используемым на быстрорастущем рынке ЭДП для производства стали. Испытания чешуйчатого графита из проекта McIntosh, обработанного запатентованным ингредиентом и обозначенного как « Performance+ », продемонстрировали положительную и прямую корреляцию между добавлением Performance+ и повышенной электропроводностью и долговечностью синтетических графитовых электродов.
Производители стали в ЭДП являются основными потребителями графитированных электродов, на долю которых приходится 90% всего производства (GrafTech International Ltd. , 2019) . При сохраняющемся высоком спросе цены на 135% выше, чем в первом квартале 2017 года (Roskill, 2019) .
Графитированные электроды расходуются каждые 8–10 часов при производстве стали в ЭДП и, следовательно, являются важными затратами, на одну только покупку которых приходится от 3 до 5% затрат на производство стали (GrafTech International Ltd., 2019) . Тестирование показало, что компания Hexagon смогла успешно продлить срок службы графитовых электродов за счет уменьшения поперечного износа/эрозии электрода (окислительной деградации). Это было достигнуто за счет предварительной обработки очищенного графита запатентованным покрытием компании, а затем последующего смешивания добавки для повышения производительности с синтетическим графитом для производства графитовых электродов.
Увеличение срока службы электродов и снижение энергопотребления.
С помощью специальной присадки Hexagon на основе природного графита для графитированных электродов ЭДП Компания смогла продемонстрировать снижение энергопотребления при минимизации расхода электрода при нормальной работе ЭДП.
Электроды графитированные обладают высокой термостойкостью (структурная целостность) и используются для проведения электричества, при сохранении сверхвысоких температур (теплопроводность) расплавленной стали при выплавке стали в ЭДП. Технические разработки Hexagon продемонстрировали последовательное увеличение электропроводности и более низкий коэффициент теплового расширения, что позволило максимально увеличить электрическую эффективность и снизить потребление энергии.
Управляющий директор Hexagon Майк Розенстрайх прокомментировал : «Результаты Performance+ подчеркивают потенциал сокращения времени простоя и снижения энергопотребления, что ведет к снижению затрат и уменьшению углеродного следа в металлургической промышленности. Это существенные проблемы, стоящие перед сталелитейной промышленностью и ведущие к серьезному переходу на ЭДП, например, в Китае. Это решительно подтверждает нашу стратегию поиска ценных возможностей глубокого рынка для нашего природного графита, изложенную в нашем недавнем предварительном исследовании. Действительно, мы сосредоточены на реализации этой стратегии, используя ключевые элементы предварительного исследования и жизненно важные технические ноу-хау, полученные при изучении чешуек природного графита из проекта McIntosh, легированных определенным ингредиентом, которые в совокупности обеспечивают экономическую эффективность в сталеплавильном производстве. ”
КЛЮЧЕВЫЕ ПОЛОЖЕНИЯ
- Компания Hexagon разработала и испытала сверхвысокочистый концентрат природного графита 1 2 , обработанный специальной антиоксидантной добавкой для оптимизации характеристик и снижения стоимости экструдированных синтетических графитовых электродов. Этот материал был обозначен как « Performance+ ».
- Сканирующие электронные микрофотографии («СЭМ» на рисунках 1 и 2) иллюстрируют подробную микроскопическую внутреннюю структуру усовершенствованных электродов, предложенных в ходе этого испытания.
- Компания произвела в общей сложности 38 электродов из экструдированного графита; электроды, изготовленные с добавкой Performance+, продемонстрировали постоянное улучшение характеристик электрода, включая характеристики истинной плотности, объемной плотности и электропроводности, по сравнению с контрольной группой (100% синтетические графитовые электроды) , в частности;
° увеличение истинной плотности на 12 %
° повышение насыпной плотности на 4,5 %
° увеличение электропроводности на 25 % - Эти результаты подчеркивают потенциал повышения электрических характеристик и увеличения долговечности/срока службы графитовых электродов для снижения эксплуатационных расходов. Работа Hexagon по техническим разработкам указывает на потенциально значительные новые рыночные возможности для ее преобразованного графитового материала, что согласуется с результатами ее исследования Downstream Scoping Study, опубликованного в мае 2019 года.
в мире и представляет собой крупнейший рынок графитированных электродов.
- Вся последующая техническая работа выполнялась NAmLab 3 , независимой лабораторией Hexagon в США и коммерческим партнером. Природный графит, используемый для производства Performance+, был получен в рамках проекта McIntosh Graphite Project в Западной Австралии.
- Компания Hexagon ведет переговоры с несколькими потребителями и производителями графитовых электродов в США.
Рисунок 1: https://www.globenewswire.com/NewsRoom/AttachmentNg/9f3a0de1-a458-475b-8ca8-58d1c92827ae
______________________
1 Термически очищенный до ≥ 99,95% Углерод общий процент на вес ( вес. % C).
2 Размер чешуек графита -60/+100 меш.
3 NAmLab — базирующийся в США технический и коммерческий партнер Hexagon, чья личность не может быть раскрыта из-за обязательств по соблюдению конфиденциальности.
1. КОММЕНТАРИЙ
Электродуговые печи («ЭДП») используются для производства стали и считаются наиболее эффективной и экологически безопасной технологией производства, доступной в настоящее время. Благодаря уникальным физическим свойствам графитовые электроды являются критически важным незаменимым промышленным расходным материалом при производстве стали на основе ЭДП.
При средней цене реализации около 10 000 долларов США за тонну мировые мощности по производству графитированных электродов в 2018 году составляли приблизительно 800 000 тонн, а в 2019 году прогнозируется достижение 850 000 тонн ( GrafTech International Ltd., 2019) . В отчете Roskill (2019) сообщается, что в 2018 году на производство электродов было израсходовано около 750 000 тонн синтетического графита, что согласуется с оценками производства Graftech и подтверждает масштабность этой рыночной возможности
Изготовленный из предшественника нефтяного кокса, синтетический графит разработан в соответствии со строгими спецификациями с высокой чистотой и предсказуемыми электрическими, тепловыми и механическими свойствами, но он менее электропроводен и значительно дороже, чем природный графит. В отличие от синтетического графита, природный чешуйчатый графит нельзя спекать (то есть формировать в блоки) и поэтому его можно использовать только в качестве добавки для электродов.
Однако, учитывая значительный размер и высокий, устойчивый профиль спроса в индустрии графитированных электродов, а также в соответствии с заявленным направлением Hexagon на производство узкоспециализированных промышленных и энергетических продуктов из графита, Компания стремилась разработать добавку на основе природного графита для повышения производительности. электрические характеристики синтетических графитовых электродов. В дополнение к повышению электрических характеристик компания Hexagon стремилась продлить срок службы графитовых электродов за счет частичного замедления разложения электрода за счет создания стойкого к окислению слоя. Окисление является основным ограничением срока службы графитовых электродов.
2. «ПРОИЗВОДИТЕЛЬНОСТЬ+» — ЗАДАЧИ РАЗРАБОТКИ
Высококачественные графитовые электроды имеют низкое удельное электрическое сопротивление и высокую износостойкость. Компания Hexagon полагала, что сможет улучшить обе эти рабочие характеристики, смешав добавку природного графита с электродами из синтетического графита.
Очищенный природный чешуйчатый графит имеет гораздо более высокую кристаллическую структуру, чем синтетический, и поэтому обладает большей электро- и теплопроводностью. Чем меньше элементных примесей в графите, тем лучше его электропроводность. Понимая это, компания Hexagon стремилась достичь максимальной электропроводности, используя натуральный чешуйчатый графит сверхвысокой чистоты, а не неочищенные материалы.
Расход графитовых электродов во время плавки является значительной составляющей себестоимости производства стали в ЭДП. Повышенная электропроводность позволяет снизить потери потребления в электродах за счет использования более высоких напряжений и более низких токов (работа с длинной дугой) . Для дальнейшего повышения срока службы электродов компания Hexagon разработала антиокислительное покрытие для предварительной обработки с низким расходом, чтобы уменьшить потери электрода из-за бокового окисления. Окислительная деградация включает распад макромолекул под действием кислорода на графитовую подложку электрода.
Окисление вызывает расход или выгорание графита во время использования в процессе плавки. При нагревании на воздухе при повышенных температурах (например, когда графитовые электроды погружаются в расплавленный металл ЭДП) графит сгорает (или окисляется) , что приводит к образованию летучей двуокиси углерода. Эта паразитная потеря углерода в виде летучих газов является основным ограничением срока службы графитовых электродов. Снижая линейный коэффициент теплового расширения («КТР»), антиоксидантное покрытие Hexagon для предварительной обработки натуральных чешуек улучшает структурную целостность электрода за счет увеличения плотности (снижение пористости) . Низкий коэффициент теплового расширения сводит к минимуму потребление электродов за счет максимального эффективного использования электроэнергии в электродуговой печи при сохранении ее структурной целостности.
Рисунок 2: https://www.globenewswire.com/newsroom/attachmentng/d71ac590-51f9-4ceb-b1c3-b92bb4691b49
3. Фон. Из результатов, описанных выше и подробно описанных ниже, полезно дать краткий обзор процесса производства промышленных электродов и использования ЭДП в сталеплавильном производстве, признавая при этом, что другие области применения ЭДП также могут иметь значение.
Производство графитированных электродов представляет собой высокотехнологичный промышленный процесс с очень строгими техническими характеристиками, которые требуют соблюдения для обеспечения эффективной работы ЭДП.
Размеры электродов могут достигать ~81 см (32 дюйма) в диаметре, более ~3,4 м (11 футов) в длину и весить более 2,6 тонн. Срок изготовления от 3 до 6 месяцев.
При эксплуатации расход электрода колеблется от 2 до 3 кг на тонну стали и от 8 до 10 часов производства.
3.1 Производство графитовых электродов
Процесс производства графитовых электродов включает следующие основные процессы, изложенные ниже со ссылкой на испытательные образцы: смешивание с каменноугольным пеком с образованием густой пасты.
Добавка Hexagon’s Performance+ была добавлена к синтетическому графиту.
Пасту пропускали через запатентованный экструдер-смеситель с образованием удлиненных стержней одинакового диаметра.
Экструдированные графитовые стержни Hexagon были прокалены при 900 ̊C в инертной атмосфере (газообразный азот) в течение 15 часов.

После прокаливания графитовые стержни вымачивали в растворе дегтярного пека в течение 1 часа.
3.2 Электросталеплавильная печь
В 2017 году производство стали в ЭДП росло примерно на 14% в год по сравнению с 4% в целом по производству стали. В результате растущей глобальной доступности стального лома и более устойчивой, высокой переменной стоимости и экологически чистой модели ЭДП. Спрос на нефтяной игольчатый кокс в аккумуляторных батареях для электромобилей ограничил предложение и подтолкнул рыночные цены вверх.
Roskill сообщает (2018) , что на производство стали в ЭДП приходится примерно 27% мирового производства, но только 7% производства стали в Китае. Перспективы роста положительны, особенно в Китае, где правительственные инициативы вынуждают переходить на электросталеплавильную печь от традиционного доминирования производителей стали с кислородно-конверторными печами. Эти инициативы являются результатом усилий по устранению избыточных производственных мощностей по производству стали и улучшению состояния окружающей среды. Метод EAF производит примерно 25% углекислого газа (или CO 2 ) выбросов конвертерного производства и не требует плавки первичной железной руды или сжигания угля. Кроме того, в результате значительного увеличения производства стали в Китае с 2000 года ожидается существенное увеличение поставок китайского лома, что может привести к снижению цен на лом и обеспечить китайскую сталелитейную промышленность местным ломом, которого раньше не было. Hexagon считает, что эти тенденции позволят производителям стали из ЭДП увеличить свою долю на рынке и расти более быстрыми темпами, чем производители стали из конвертерного металла, что приведет к увеличению спроса на графитированные электроды, что, в свою очередь, создаст потенциально значительный спрос и коммерческое внедрение усовершенствования электродов для ЭДП. добавки, которые снижают затраты и повышают производительность электродов для ЭДП.
4. РЕЗУЛЬТАТЫ ИСПЫТАНИЙ
Испытания графитовых электродов Performance+ показали прямую зависимость между количеством природного графита, добавленного в электродную матрицу, и улучшенными характеристиками нескольких свойств электрода, включая (см. Таблицы 1-3) :
- повышенная электропроводность
- повышенная насыпная плотность
- улучшенные механические свойства
- потенциал для продления срока службы электрода
По мере увеличения весового процента добавления природного графита к синтетическому плотность электродов увеличилась, достигнув впечатляющих 1,62 г/см 3 при добавлении 2,5 мас.% чешуек в электродную смесь .
Кроме того, тесты постоянно превосходили полностью синтетический контроль по плотности и проводимости.
В следующем разделе обсуждаются три ключевых параметра тестирования; Объемная плотность, истинная плотность и электропроводность.
4.1 Объемная плотность
Объемная плотность также называется кажущейся плотностью или объемной плотностью. Это характеристика объема разделенного материала, такого как порошки, зерна и гранулы.
Наилучшим результатом было улучшение на 4,5% с 1,55 г/см 3 до 1,62 г/см 3 при добавлении 2,5% Performance+.
Плотность может быть как показателем, так и результатом размера частиц, прочности и пористости, присущих конкретному графитовому материалу, поскольку чем больше размер частиц и больше отверстий, заполненных воздухом, тем ниже плотность.
Плотность графита может регулироваться сырьем, рецептурой и производственными процессами, используемыми для создания определенного сорта материала во время начального производства. Плотность готового графитового материала также может быть увеличена за счет использования добавок и пропиток, которые будут заполнять открытую пористость базового графитового материала.
Пористость является нежелательным явлением в электродах, поскольку пористость приводит к снижению плотности электрода и, как правило, к снижению механической прочности и электропроводности.
При сжатии чешуек графита под высоким давлением каждая из них сближается и, следовательно, плотность объемного графита становится выше. Более высокая плотность объемного графита приводит к более высокой электропроводности, потому что электроны имеют большую связь для движения через частицу графита. Напротив, более низкая плотность объемного графита указывает на высокий уровень пустот, который сильно снижает подвижность электронов, что приводит к более низкой электропроводности объемного графита.
Насыпная плотность обычно указывает это значение на большинстве спецификаций графитовых материалов.
Таблица 1: Определение объемной плотности.
Graphite Electrode | Addition of Natural Graphite (%) | Addition of Synthetic Graphite (%) | Weight before Graphitization (g) | Weight after Graphitization (g) | Weight Lost during Graphitization (%) | Specimen Height (cm) | Specimen Volume (cm 3 ) | Electrode Bulk Density (g/cm 3 ) | |
Hexagon P erformance+ additive | 2.![]() | 97.5 | 82.9 | 82.3 | 0.72 % | 10.03 | 50.80 | 1.62 | |
Hexagon P erformance+ additive | 5 | 95 | 64.7 | 63.7 | 1.55% | 8.44 | 42.75 | 1.49 | |
Hexagon P erformance+ additive | 7.5 | 92.5 | 58.1 | 56.6 | 2.58% | 6.98 | 35.38 | 1.60 | |
Hexagon P erformance+ additive | 10 | 90 | 73.5 | 68.6 | 6.67% | 8.![]() | 43.97 | 1.56 | |
Control (100% Synthetic Graphite) | 0 | 100 | 51.1 | 48.5 | 5.09% | 6.18 | 31.29 | 1.55 | |
4.2 Данные истинной плотности
Истинная плотность определяется путем деления массы частицы на ее объем без учета открытых и закрытых пор. Постоянная величина для материи, истинная плотность – это плотность почти чистой формы.
Истинная плотность в данном случае является мерой графитности материала. Лучшим результатом было увеличение на 12% с 1,95 г/см 3 в контрольном образце до 2,18 г/см 3 при добавлении 5% Performance+.
Высокая истинная плотность предполагает, что электроды изготовлены из материала с высоким содержанием графита, который должен быть как можно более проводящим, чтобы обеспечивать наилучший уровень токопроводящей способности. При проверке истинной плотности переменная степень графитации была эффективно устранена.
Наивысшая зарегистрированная плотность была при добавлении 10% Performance+, хотя 5% является идеальным, когда к общему уравнению добавляется компонент механической прочности.
Таблица 2: Определения истинной плотности. Плотность
(г/см 3 )
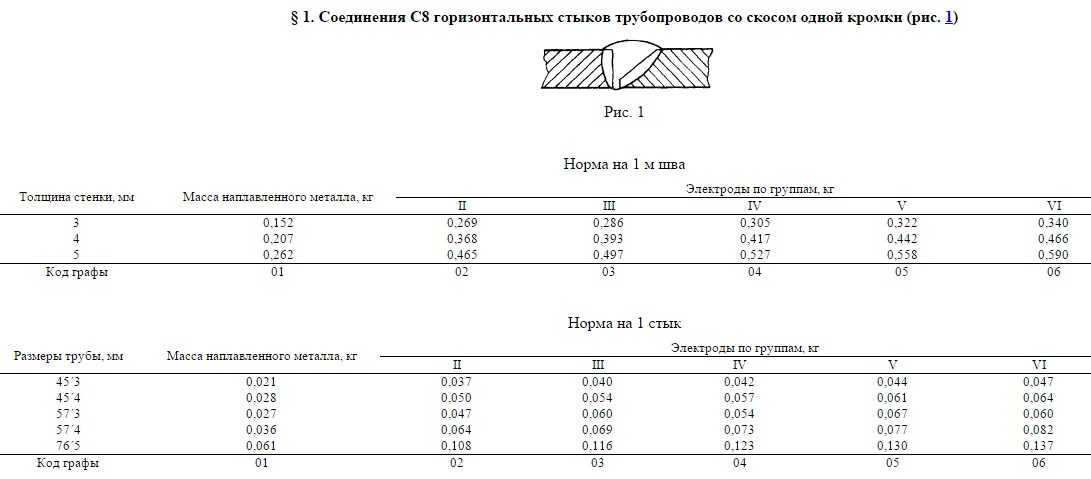
0016, является внутренним свойством, которое количественно определяет, насколько сильно данный материал сопротивляется потоку электрического тока. Низкое удельное сопротивление указывает на то, что материал легко пропускает электрический ток. Электропроводность или удельная проводимость обратны удельному электрическому сопротивлению и измеряют способность материала проводить электрический ток.
Наилучшим результатом было повышение электропроводности на 25 % при снижении удельного сопротивления (обратного электропроводности) с 11,88 мкОм·м в контрольном образце до 90,01 мкОм·м в электроде с добавлением 5% Performance+.
Электропроводность сыпучего графита рассматривается как функция его объемной плотности и температуры. В общем, увеличение давления сжатия механически уменьшает зазоры между углеродными частицами, напрямую улучшая электрический контакт. Электропроводность графита зависит от расстояния между каждой частицей и среднего размера частиц.
Чем выше концентрация природного чешуйчатого графита Hexagon в составе прессованных профилей, тем ниже удельное сопротивление. Это свидетельствует о положительном влиянии добавки Hexagon Performance+ на явление повышения проводимости графитовых электродов. При 5% и выше серия испытаний стала лучше, чем синтетический контроль, при большем процентном добавлении чешуйчатой добавки в рецептуру электрода. Рафинированные чешуйки достигли уровня удельного сопротивления контрольного состава 3PI при 5 мас. % добавления хлопьев к синтетике.
Таблица 3: Определения удельного сопротивления
WT.![]() | Hexagon Natural . Синтетический контроль | ( 2 ИП ) Синтетический контроль | ( 3 |
0 | n/a | 11.88 μΩ·m | 9.24 μΩ·m |
2.5 | 13.60 μΩ·m | ||
5.0 | 9.01 μΩ · m | ||
7.5 | 8.85 μΩ·m | ||
10 | 8.65 μΩ·m | ||
5. Методы испытаний
5.1 Электрод Производство
Графитовые электроды были получены с помощью первого смешанного нефтепровода. графит и легирующая добавка для образования густой пасты. Полученную пасту пропускали через запатентованный экструдер-смеситель NAmLab, чтобы сформировать удлиненные стержни одинакового диаметра, как показано на рис. 3.
Эти стержни прокаливали (т.е. обжигали) при 900°C в инертной атмосфере азота в течение 15 часов. После прокаливания графитовые стержни вымачивали в растворе смолистого пека в течение 1 часа, чтобы пек заполнил любые пустоты, давали высохнуть на воздухе, а затем снова прокаливали для превращения смоляного пека в пековый кокс. В зависимости от конкретных образцов этапы замачивания и прокаливания повторялись еще один-два раза (т. е. 2PI или 3PI), чтобы убедиться, что все зазоры внутри стержней заполнены связующим пековым коксом. Термическая обработка делает электроды более твердыми, но после 2-й и особенно 3-й ИП они также приобретают прочность.
После завершения этапа заключительного прокаливания измеряли сухую массу неграфитированных электродов перед графитированием при 2800°C. После извлечения из печи измеряли массу электродов для оценки потери веса электрода во время процесс графитизации.
Удельное сопротивление полученных графитированных электродов было испытано в соответствии со стандартом ASTM C611, который требовал механической обработки электродов с использованием токарного станка и прецизионных режущих инструментов до отношения длины к диаметру от 6:1 до 4:1.
Истинная плотность 23 электродов была измерена с помощью гелиевого мультипикнометра Quantachrome. Поскольку для этого испытания требовался порошкообразный материал, проверить истинную плотность всего электрода было невозможно. Вместо этого оставшаяся стружка, образовавшаяся при обработке неровных концов электродов, была отложена и измельчена; полученный порошок затем использовали для проверки истинной плотности. Истинная плотность — это мера того, насколько графичен материал; теоретическая истинная плотность чистого кристаллического графита 2,254 г/см 3 , а материал с истинной плотностью 1,9 г/см 3 является синтетическим и умеренно графитизированным. Утверждалось, что теоретическая истинная плотность графита не может быть измерена с помощью гелиевой пикнометрии из-за пористости частиц, но дробление электродов и прессование порошка позволило получить более точные показания истинной плотности.
Рисунок 3: https://www.globenewswire.com/NewsRoom/AttachmentNg/55572589-6a0a-4eb5-9b84-e10baf2c98fd
5.2 Определение объемной плотности
Объемную плотность электродов определяют путем деления массы электрода после графитизации на его объем. При использовании собственного экструдера NAmLab измеренные значения были близки к объемной плотности электродов промышленного производства, хотя некоторые значения плотности были немного ниже. Самая низкая насыпная плотность, зарегистрированная в исследовании, составила 1,31 г/см 3 , а самая высокая – 1,63 г/см 3 (см. соответствующие результаты в таблице 1) . Для справки, объемная плотность промышленных электродов варьируется от 1,58 до 1,65 г/см 3 .
Все электроды, произведенные в этом исследовании, имели фиксированный диаметр 2,54 см и различную длину, на что указывают различные данные по массе в таблице 1. Электроды после однократной пропитки пеком (обозначается как 1PI) и однократного прокаливания, потеряли до 18-23% масс. при графитизации. Эти электроды имели наименьшую плотность в данной серии испытаний, четко обнаруживая значительное количество открытой пористости, и в дальнейшем здесь не упоминаются, поскольку они не имеют отношения к промышленному сектору.
Электроды, обозначенные как 2PI, имели наименьшее снижение массы летучих веществ во время графитизации (обычно от 0,5 до 5 мас.%) . Их результирующие значения насыпной плотности были заметно выше, возможно, вследствие эффективного заполнения пеком пор в экструдированных формах.
Важно отметить, что по мере увеличения массового добавления добавки Performance+ с натуральным чешуйчатым графитом к синтетическому графиту объемная плотность графитированных электродов увеличивалась.
5.3 Определение истинной плотности
В рамках данного исследования. NAmLab стремился определить плотность (удельный вес) графитовых материалов с использованием аналитического метода пикнометрии расширения газа (гелия) . Это широко признанный метод точного определения объема кристаллического вещества, такого как графитовые электроды.
Гелиевый пикнометр работает по принципу вытеснения газа и зависимости объем-давление (закон Бойля) . Ожидается, что гелиевая пикнометрия даст значение 2,266 г/см 9 .0051 3 при 293 К для монокристаллического графита 100%-ной чистоты. В этом исследовании использовался газовый мультипикнометр He/N 2 компании Quantachrome Instruments.
Образцы представляли собой порошки, изготовленные из измельченной машинной стружки 23 протестированных электродов. Для каждого электрода было проведено как минимум два измерения истинной плотности, а плотности усреднены для определения окончательных значений истинной плотности, представленных в таблице 3.
5.4 Удельное электрическое сопротивление
Удельное сопротивление графитированных электродов было оценено в соответствии с методом ASTM C 611-98, озаглавленным: «Удельное электрическое сопротивление изготовленных изделий из углерода и графита при комнатной температуре» .
В соответствии с вышеупомянутым методом испытаний через графитовый электрод пропускают слабый электрический ток, чтобы предотвратить нагрев образца, при этом измеряется напряжение на определенной длине поверхности графитового электрода, чтобы можно было рассчитать удельное сопротивление. Чтобы учесть анизотропию в цилиндрическом графитовом электроде, это измерение повторяется после последовательных 9вращения электрода на 0 градусов и/или испытанием обработанной формы в виде стержня. При тестировании цилиндра эти четыре измерения затем повторяются с использованием обратного потока тока и переключаемой конфигурации электрода вольтметра для учета любых эффектов памяти материала и погрешностей измерения напряжения. Результатом являются 16 отдельных измерений удельного сопротивления, которые при усреднении дают репрезентативную меру удельного сопротивления графитового электрода.
Электроды были подвергнуты испытанию удельного сопротивления по 4 точкам, результаты представлены в таблице 3.
Результаты разведки и оценки минеральных ресурсов
Информация в этом отчете, которая касается результатов разведки, оценок объектов разведки, геологических данных и минеральных ресурсов на проектах McIntosh и Halls Creek, основана на информации, собранной г-ном Майком Розенстрайхом, который сотрудник Компании. Г-н Розенстрайх является научным сотрудником Австралазийского института горного дела и металлургии и имеет достаточный опыт работы с рассматриваемыми типами минерализации и типами месторождений, а также с осуществляемой в настоящее время деятельностью, чтобы квалифицироваться как Компетентное лицо (лица), как это определено в Редакция 2012 года Австралазийского кодекса отчетности о результатах разведки, минеральных ресурсах и запасах руды, и он соглашается на включение этой информации в той форме и контексте, в которых она представлена в этом отчете.
Результаты металлургических испытаний
Информация в этом отчете, касающаяся результатов металлургических испытаний и обработки материала McIntosh, основана на информации, предоставленной рядом независимых лабораторий. Г-н Розенстрайх (упомянутый выше) руководил и обобщал результаты тестовой работы, указанные в этом объявлении. Высококвалифицированный и опытный исследователь NAmLab планировал, контролировал и интерпретировал результаты тестовой работы NAmLab. Г-н Майкл Чен был штатным сотрудником Hexagon Resources Limited в то время, когда были представлены эти результаты, и он также ознакомился с результатами металлургических испытаний. Г-н Чан является инженером-металлургом и членом Австралазийского института горного дела и металлургии. Г-н Чан и руководители NAmLab имеют достаточный соответствующий опыт, относящийся к рассматриваемому стилю минерализации и типам тестовых работ, а также к деятельности, которая в настоящее время проводится, чтобы получить квалификацию Компетентного лица (лиц), как это определено в издании Австралазийского Кодекс отчетности о результатах разведки, минеральных ресурсах и запасах руды и дал согласие на включение этой информации в той форме и контексте, в которых она представлена в настоящем отчете.
О компании Hexagon Resources Limited
Компания Hexagon Resources Limited зарегистрирована на Австралийской фондовой бирже («ASX») под тиккерным кодом «HXG». Компания владеет 100%-ной долей в графитовом проекте McIntosh в Западной Австралии и 80%-ной долей в графитовом проекте Ceylon в Алабаме, США. Сосредоточившись в настоящее время на последующей переработке графита и других энергетических материалов, компания Hexagon накопила обширные технические знания, основанные на испытательной работе своего чешуйчатого графитового материала в рамках проекта McIntosh, который применим и очень ценен для ряда специальных материалов. Компания сосредоточена на создании устойчивой акционерной стоимости за счет максимального увеличения краткосрочных возможностей роста для коммерциализации перерабатывающего бизнеса в США, где она наладила прочные технические, коммерческие отношения и отношения с инвесторами.
Узнайте больше на www.hexagonresources. com
Прогнозные заявления
другие законы. Прогнозные заявления в этом выпуске могут включать, среди прочего, заявления относительно будущих планов, затрат, целей или результатов деятельности Hexagon Resources Limited или предположения, лежащие в основе любого из вышеизложенного. В этом выпуске новостей такие слова, как «может», «мог бы», «будет», «будет», «вероятно», «верит», «ожидает», «предвидит», «намеревается», «план», «цель », «оценка» и подобные слова, а также их отрицательные формы используются для обозначения прогнозных заявлений. Прогнозные заявления подвержены известным и неизвестным рискам, неопределенностям и другим факторам, которые находятся вне контроля Hexagon Resources Limited и которые могут привести к тому, что фактические результаты, уровень деятельности, производительность или достижения Hexagon Resources Limited будут существенно отличаться от те, которые выражены или подразумеваются такими прогнозными заявлениями. Такие риски и неопределенности могут привести к тому, что фактические результаты, планы и цели Hexagon Resources Limited могут существенно отличаться от тех, которые указаны в прогнозной информации. Hexagon Resources Limited не может гарантировать, что ее планы будут реализованы. Эта и вся последующая письменная и устная прогнозная информация основана на оценках и мнениях руководства Hexagon Resources Limited на даты их составления и во всей своей полноте прямо оговорены в настоящем уведомлении. За исключением случаев, предусмотренных законодательством, Hexagon Resources Limited не берет на себя никаких обязательств по обновлению прогнозной информации в случае изменения обстоятельств, оценок или мнений руководства Hexagon Resources Limited.
Контакт
Hexagon Resources Limited
Mike Rosenstreich
Генеральный директор и управляющий директор
North American Media and Investor Contact:
G & W Communications Inc.
Телефонный [email protected]
Рынок графитовых электродов ожидается до
2024). Основным сырьем, используемым для производства графитовых электродов, является игольчатый кокс (на основе нефти или угля). — Ожидается, что рост производства чугуна и стали в развивающихся странах и увеличение доступности стального лома в Китае, что приведет к увеличению использования электродуговых печей, будут стимулировать спрос на рынке в течение прогнозируемого периода.
| Источник: ReportLinker FR ReportLinker FR
Нью-Йорк, 8 ноября 2019 г. (GLOBE NEWSWIRE) — Reportlinker.com объявляет о выпуске отчета «Рынок графитовых электродов – рост, тенденции и прогноз (2019–2024)» – https://www. reportlinker. com/p05826223/?utm_source=GNW
— Стремительный рост цен на игольчатый кокс, приводящий к дефициту предложения, наряду с другими ограничениями, такими как ограниченный рост производства графитированных электродов UHP в Китае и консолидация производства графитированных электродов, вероятно, будут препятствовать росту рынка.
— Ожидается, что рост производства стали с использованием технологии электродуговых печей в Китае откроет новые возможности для рынка в будущем.
Ключевые тенденции рынка
Увеличение производства стали с помощью технологии электродуговой печи
— Дуговая электропечь принимает стальной лом, ПВЖ, ГБЖ (горячебрикетированное железо, прессованное ПВЖ) или чугун в твердом виде и плавит их для производства стали. На маршруте ЭДП электричество обеспечивает электроэнергию для плавления сырья.
— Графитовый электрод в основном используется в процессе производства стали в электродуговых печах (ЭДП) для плавления стального лома. Электроды изготовлены из графита, благодаря его способности выдерживать высокие температуры. В ЭДП кончик электрода может достигать 3000º по Фаренгейту, что составляет половину температуры поверхности Солнца. Размер электродов широко варьируется: от 75 мм до 750 мм в диаметре и до 2800 мм в длину.
— Резкий рост цен на графитированные электроды привел к росту затрат электросталеплавильных заводов. По оценкам, средняя ЭДП потребляет около 1,7 кг графитированных электродов для производства одной метрической тонны стали. Цены на графитированные электроды в Китае выросли более чем на 700% по сравнению с 2017 годом.
— Рост цен объясняется консолидацией отрасли в глобальном масштабе, остановкой мощностей в Китае, соблюдением природоохранного законодательства и ростом производства ЭДП в глобальном масштабе. По оценкам, это увеличит себестоимость производства ЭДП на 1-5%, в зависимости от практики закупок на комбинате, что, вероятно, ограничит производство стали, поскольку в операциях с ЭДП нет замены графитовому электроду.
— Кроме того, политика Китая по борьбе с загрязнением воздуха была подкреплена жесткими ограничениями поставок не только для сталелитейного сектора, но и для угольной, цинковой и других отраслей, которые производят загрязнение твердыми частицами. В результате производство стали в Китае резко сократилось за последние годы. Однако ожидается, что это окажет положительное влияние на цены на сталь и сталелитейные заводы в регионе, что позволит им получить более высокую маржу.
— Ожидается, что вышеупомянутые факторы будут стимулировать рынок в течение прогнозируемого периода.
Азиатско-Тихоокеанский регион будет доминировать на рынке
— Азиатско-Тихоокеанский регион доминировал на рынке в 2018 году. Китай занимает наибольшую долю с точки зрения потребления и производственных мощностей графитированных электродов в глобальном сценарии. Китай произвел около 520 тысяч метрических тонн графитированного электрода, почти 62% которого было использовано для внутреннего потребления. Производство и спрос на графитированные электроды в Китае демонстрировали стабильный рост до 2015 года.
— В 2015 году производство графитированных электродов сократилось из-за закрытия индукционных дуговых печей и мини-доменных печей мощностью почти 140 миллионов метрических тонн. результат правительственных постановлений о сильно загрязняющих отраслях промышленности, призванных решить проблему экологических проблем.
— Ожидается, что рост производства автомобилей, наряду с расширением отрасли жилищного строительства, поддержит внутренний спрос на цветные сплавы, железо и сталь, что является положительным фактором для роста спроса на графитированные электроды в ближайшие годы. Текущая производственная мощность графитированных электродов UHP в Китае составляет около 50 тысяч метрических тонн в год. Ожидается также значительный рост спроса на электроды UHP в Китае в долгосрочной перспективе, и ожидается, что на более поздних этапах прогнозируемого периода появится дополнительная мощность в размере более 50 тысяч метрических тонн графитированных электродов UHP.
Конкурентная среда
Рынок графитированных электродов консолидирован по своей природе. Что касается доли рынка, то в настоящее время на нем доминируют несколько крупных игроков. Ключевыми игроками на рынке графитовых электродов являются Группа ЭНЕРГОПРОМ, Fangda Carbon New Material Technology Co. Ltd, GrafTech International, Graphite India Limited, HEG Limited, Jilin Carbon Co. Ltd, Kaifeng Carbon Co. Ltd и Nantong Yangzi Carbon Co. Ltd. среди прочих.
Причины для покупки этого отчета:
— лист рыночной оценки (ME) в формате Excel
— Настройка отчета в соответствии с требованиями клиента
— 3 месяца поддержки аналитиков
Прочитать полный отчет: https://www.reportlinker.com/p05826223/?utm_source=GNW
О Reportlinker
ReportLinker — отмеченный наградами рынок исследовательское решение. Reportlinker находит и упорядочивает последние отраслевые данные, чтобы вы могли получить все необходимые исследования рынка — мгновенно и в одном месте.
__________________________
Контактные данные
Клэр: [email protected] США: (339)-368-6001 Международный: +1 339-368-6001
Контакты
Графитовые электроды влияют на производительность и стоимость производства стали в ЭДП
Графитовые электроды с высокой электропроводностью и низким электрическим сопротивлением являются ключевыми расходными материалами для производства стали в ЭДП.
Что такое графитовый электрод?
Графитовый электрод , проводник, высвобождающий электрическую энергию в виде электрической дуги, используется для нагрева и плавления стального лома в электродуговой печи. В настоящее время они являются единственными продуктами с высокой электропроводностью и способны поддерживать чрезвычайно высокое тепловыделение в этих сложных условиях. В связи с растущим спросом на качественную сталь в аэрокосмической, автомобильной и электронной промышленности графитированные электроды также становятся все более популярными.
Почему графитовый электрод?
- Графитовый материал обладает лучшей электрохимической стабильностью. Этот тип электрода имеет низкий коэффициент потерь.
- Графитовый электрод легко обрабатывается, а скорость обработки явно выше, чем у медного электрода. Графит
- имеет малый вес и хорошую тепло- и электропроводность.
Графитовый электрод , обладающий перечисленными выше незаменимыми преимуществами, играет незаменимую роль в высокотемпературной производственной сфере, такой как выплавка чугуна и стали, электролитический алюминий, ферросплав, карбид кальция, промышленный кремний и желтый фосфор.
Классификация графитированных электродов
В зависимости от мощности электропечи, мощности трансформатора, разницы в сырье, используемом в производстве электродов, и физико-химических показателей готовых электродов графитированные электроды делятся на три типа:
Графитовый электрод UHP.
Изготовлен из высококачественного игольчатого кокса и обработан продольной графитизацией (LWG). Температура графитации может достигать 2800°С – 3000°С. Готовые изделия имеют более низкое электрическое сопротивление и линейное расширение, хорошую стойкость к тепловому удару и допускают большую плотность тока.
Подробнее
Графитовый электрод HP.
В качестве сырья используется качественный нефтяной кокс или игольчатый кокс низкого качества. Его физические и механические свойства выше, чем у графитового электрода RP, такие как более низкое электрическое сопротивление и возможность большей плотности тока.
Узнать больше
RP Графитовый электрод.
Принят к производству кокс нефтяной обыкновенный. Этот тип графитового электрода обрабатывается при низкой температуре графитизации. Допустимая плотность тока ниже, чем у графитового электрода HP. Графитовые электроды штатной мощности указаны с допустимой плотностью тока менее 17 А/см 2 .
Подробнее
Основные области применения
Производство стали в ЭДП.
Производство стали в ЭДП является основной областью применения графитированных электродов. Производство стали для электродуговых печей в Китае составляет около 18% нерафинированной стали. 70-80% расхода графитового электрода используется в сталеплавильном производстве в ЭДП. В сталеплавильном производстве в ЭДП графитовый электрод используется для подачи электрического тока в печь. А высокотемпературный источник тепла для плавки генерируется дуговым разрядом между электродом и стальным ломом.
Дуговая печь под флюсом
Дуговая печь под флюсом в основном используется в производстве промышленного желтого фосфора и кремния. Требуется использовать графитовый электрод для погружной электропечи с большой плотностью тока. Для производства 1 т кремния требуется около 100 кг графитового электрода, а для производства 1 т желтого фосфора — около 40 кг графитового электрода.
LF (Печь-ковш)
Печь-ковш установлена на электросталеплавильном заводе ЭДП. После перемешивания шлака печь-ковш используется для выполнения задачи по дальнейшему восстановлению и рафинированию. Обычно графитовые электроды используются для трехфазных печей-ковшей переменного тока.
Основные факторы, влияющие на расход графитированных электродов в электросталеплавильном производстве
- Основными причинами потери и износа графитированных электродов являются перегрузки и простои в работе.
- Низкое качество или неправильная пропорция лома приводит к плохому шлакообразованию и увеличению времени плавки.
- Увеличенное время подачи приводит к более высокой вероятности повреждения и поломки дна электрода.
- Оборудование электропечи не соответствует характеристикам электрода.
- Выбор кривой мощности и редуктора, управление напряжением и током пусковой и стабилизирующей дуг, использование длинных, средних и коротких дуг и конфигурация системы водяного охлаждения важны для срока службы и расхода электродов.
- Качество самого графитового электрода влияет на соотношение расхода. В настоящее время плавка и процесс электродуговых печей предъявляют более высокие требования к антиокислительным характеристикам и термостойкости графитовых электродов. Более того, большое потребление, вызванное колебаниями качества, сильно беспокоит пользователей. Следовательно, однородность и стабильность графитового электрода являются наиболее важными факторами, определяющими расход.
Скачать
Имя файла | Последнее обновление | Размер файла | Скачать |
---|---|---|---|
Имя файла: Каталог графитовых электродов | Последнее обновление: 2018.![]() | Размер файла: 2,09 МБ | Скачать: |
Измерение потребления кислорода митохондриями с помощью электрода Кларка
- Список журналов
- Рукописи авторов HHS
- PMC8711122
Методы Мол Биол. Авторская рукопись; доступно в PMC 2021 27 декабря.
Опубликовано в окончательной редакции как:
Methods Mol Biol. 2012 г.; 837: 63–72.
DOI: 10.1007/978-1-61779-504-6_5
PMCID: PMC8711122
NIHMSID: NIHMS1762806
PMID: 22215541
6
PMID: 22215541
6
. для запуска энергозатратных реакций в эукариотических организмах.
Ключевые слова: Митохондрии, Полярография, Парное дыхание, Скорость потребления кислорода, Окислительное фосфорилирование
Анализ потребления кислорода изолированными митохондриями с помощью полярографии является хорошо зарекомендовавшей себя технологией, которая используется уже более 50 лет (1). Этот подход основан на фундаментальном биохимическом принципе окислительного фосфорилирования (OXPHOS), заключающемся в переносе электронов по дыхательной цепи (заключительной стадией является потребление молекулярного кислорода путем восстановления до H 2 O оксидазой цитохрома c ) функционально связан с фосфорилированием АДФ за счет образования и использования протонного электрохимического градиента через внутреннюю мембрану митохондрий (2). Возможность измерения потребления кислорода интактными митохондриями, выделенными из тканей или клеток человека или из тканей животных, является важным инструментом для функционального анализа OXPHOS в контексте митохондриальной дисфункции и заболеваний (2-4). Митохондриальная полярография включает использование электрода Кларка для измерения содержания растворимого кислорода в замкнутой системе.
В присутствии окисляемых субстратов в систему вводят свежевыделенные митохондрии и измеряют потребление кислорода в присутствии экзогенно добавленных АДФ и/или ингибиторов. В этой главе представлены методы выделения интактных митохондрий из тканей и проведения митохондриальной полярографии.
Приготовьте все растворы, используя сверхчистую воду (приготовленную путем очистки деионизированной воды с помощью обратного осмоса до достижения удельного сопротивления 18 МОм·см при 25°C). Подготовьте и храните все реагенты при комнатной температуре (если не указано иное). При утилизации отходов необходимо соблюдать все правила утилизации отходов.
2.1. Исходные растворы (см. примечание 1)
1 М маннит: растворить 91 г маннита в 300 мл сверхчистой воды и затем добавить воду до конечного объема 0,5 л (см. примечание 2).
0,5 М сахарозы: Растворите 85,6 г сахарозы в 300 мл сверхчистой воды и затем добавьте воды до конечного объема 0,5 л. : Растворите 59,6 г HEPES в 300 мл сверхчистой воды и доведите рН до 7,2 с помощью 10 М КОН. Добавьте воду до конечного объема 0,5 л.
0,4 М ЭГТА (этиленгликольтетрауксусная кислота): добавьте 15,2 г ЭГТА в 90 мл сверхчистой воды. Сначала добавьте 3,5 г гранул NaOH, а затем осторожно титруйте pH до 7,5, добавляя отдельные гранулы NaOH по мере необходимости (см. примечание 3). Добавьте воду до конечного объема 100 мл.
1 М Трис-HCl: Растворите 60,6 г основания Трис в 400 мл сверхчистой воды. Осторожно отрегулируйте pH до 7,2, используя концентрированную HCl. Добавьте воду до конечного объема 0,5 л.
1 М KCl: Растворите 37,3 г KCl в 400 мл сверхчистой воды.
Добавьте воду до конечного объема 0,5 л.
1 M KH 2 PO 4 : Растворите 68 г KH 2 PO 4 в 400 мл ультрачистой воды. Доведите pH до 7,2 с помощью концентрированной HCl. Добавьте воды до конечного объема 0,5 л.
2.2. Оборудование и буфер для выделения митохондрий
Буфер для выделения митохондрий: 5 мМ HEPES (pH 7,2), 210 мМ маннит, 70 мМ сахароза, 1 мМ EGTA и 0,5% (масса/объем) BSA. Для приготовления 1 л соедините 210 мл 1 М маннита, 140 мл 0,5 М сахарозы, 10 мл 0,5 М HEPES, 2,5 мл 0,4 М ЭГТА и 5 г бычьего сывороточного альбумина (БСА, фракция V, не содержит жирных кислот). ). Добавьте ультрачистую воду до конечного объема 1 л. Фильтруйте и стерилизуйте буфер и храните при 4°C.
Стеклянный гомогенизатор Dounce (Kontes): Полезно иметь как минимум два размера гомогенизаторов Dounce (с соответствующими «плотными» и «свободными» стеклянными пестиками) для облегчения гомогенизации различного количества тканей.
По нашему опыту, размеры 15, 7 и 2 мл обеспечивают достаточную емкость и гибкость для гомогенизации тканей млекопитающих, тканей мух и клеточных гранул.
Центрифуга с охлаждением и микроцентрифуга (настроенная на 4°C), центрифужные пробирки Oak Ridge на 50 мл и микроцентрифужные пробирки на 1,5 мл.
2.3. Реагенты для полярографии
Буфер для дыхания: 225 мМ маннит, 75 мМ сахароза, 10 мМ KCl, 10 мМ Трис-HCl (pH 7,2) и 5 мМ KH 2 PO 4 . Чтобы получить 0,5 л, соедините 112,5 мл 1 М маннита, 75 мл 0,5 М сахарозы, 5 мл 1 М KCl, 5 мл 1 М трис-HCl (pH 7,2) и 2,5 мл 1 М KH 2 . PO 4 (pH 7,2). Добавить ультрачистую воду до конечного объема 0,5 л. Профильтровать, стерилизовать, разлить на аликвоты по 50 мл и хранить при -20°C.
Исходные растворы малата, глутамата, пирувата и сукцината (0,65 М): приготовьте 20 мл 0,65 М исходных растворов каждого, доведя рН до 7,2 с помощью 10 М КОН.
Разлить на аликвоты по 150 мкл и хранить при температуре -80°C. Эти исходные растворы обычно стабильны в течение нескольких лет при хранении при температуре -80°C. Все они используются в рабочей концентрации 5 мМ (см. примечание 4).
АДФ (25 мМ): Приготовьте 20 мл исходного раствора 25 мМ АДФ (214 мг в общем объеме 20 мл) и используйте разбавленный (1 М) КОН для доведения рН до 6,0–6,8, чтобы обеспечить длительную стабильность срока. Немедленно разделите на аликвоты по 150 мкл и храните при температуре -80°C (см. примечание 5). Обычно для стимуляции дыхания используют 125 нмоль АДФ на 200–300 мкг изолированных митохондрий.
6,5 мМ ДНФ (2,4-динитрофенол): Приготовьте 20 мл исходного раствора 6,5 мМ, поместив 24 мг ДНФ в 4 мл 1 М NaOH в полипропиленовой пробирке на 15 мл и полностью растворив нагреванием при 50°С. С в течение 20 мин. Отрегулируйте pH до нейтрального с помощью 1 M HCl, добавив ~ 3 мл. Проверяйте рН до достижения 7,2 (раствор ДНФ должен иметь полупрозрачный желтый цвет).
Добавьте сверхчистую воду, чтобы получить окончательный объем 20 мл, разлейте на аликвоты по 150 мкл и храните при -80°C (см. примечание 6).
2.4. Оборудование для полярографии
Микрокислородный зонд Кларка (YSI LifeSciences, Yellow Springs, OH).
Микрокислородная камера с водяной рубашкой (0,65 мл) с магнитной мешалкой (YSI LifeSciences, Yellow Springs, OH) и стандартной водяной баней с циркуляцией.
Кислородный монитор (модель YSI 5300A, YSI LifeSciences, Yellow Springs, OH).
Электронный самописец PowerLab 4/30 плюс программное обеспечение для анализа LabChart (ADInstruments, Колорадо-Спрингс, Колорадо).
3.1. Выделение митохондрий из ткани
Препарируйте или соберите нужную ткань (см. примечание 7) и дважды промойте 2–5 мл либо ледяного PBS, либо буфера для выделения, чтобы удалить любой связанный мусор (см. примечание 8).
Измельчите ткань лезвием бритвы и поместите в предварительно охлажденный гомогенизатор Dounce.
Добавьте до 10 мл буфера для выделения, затем гомогенизируйте, используя восемь-десять ручных проходов стеклянным пестиком (см. примечания 9 и 10).
Перенесите гомогенат в центрифужную пробирку на 50 мл (см. примечание 11).
Центрифуга при 1500 × g в течение 5 мин при 4°C.
Осторожно перелейте надосадочную жидкость в свежую пробирку, избегая переноса свободного материала из осадка, и отцентрифугируйте при 8000 × г в течение 15 мин при 4°C.
Удалите супернатант и промойте митохондриальную фракцию, суспендировав осадок в 25 мл буфера для выделения и повторив центрифугирование при 8000 × г в течение 15 мин при 4°С.
Суспензируйте промытый митохондриальный осадок в буфере для выделения (используйте 0,1 мл на грамм используемой ткани) и держите на льду при подготовке полярографической камеры (см. Подзаголовок 3.2 ниже). Определите концентрацию белка, используя любой из стандартных колориметрических методов, таких как анализ Брэдфорда (5) (см.
примечание 12).
3.2. Подготовка оборудования для полярографии
Разберите и очистите микрокамеру, состоящую из пластиковой камеры объемом 650 мкл с магнитной мешалкой, входного и выходного портов для промывки камеры, порта для кислородного электрода, порта для введения образцов/ подложки в камеру и вращающийся запорный кран с прозрачным смотровым окном, прикрепленный к камере с помощью силиконовой смазки. Чтобы облегчить очистку от старой смазки, используйте ватный тампон, смоченный органическим растворителем, таким как ксилол или метанол. После очистки снова соберите камерный аппарат, включите циркуляционную водяную баню, чтобы нагреть и поддерживать температуру в камере с водяной рубашкой при 30°C, а также включите кислородный монитор, электронный самописец и компьютер.
Разморозьте аликвоту 50 мл дыхательного буфера и убедитесь, что она насыщается комнатным воздухом, встряхивая колбу на водяной бане при 30°C в течение не менее 30 мин.
Подготовьте кислородный зонд, покрыв кончик зонда каплей свежего раствора KCl (наполовину насыщенного путем растворения 5,25 г KCl в 16 мл сверхчистой воды), затем накройте полиэтиленовую мембрану и закрепите уплотнительным кольцом, как указано в инструкции производителя (см. примечание 13).
Откалибруйте кислородный монитор и электронный регистратор данных, сначала сняв разъем датчика с монитора и установив нулевую точку для регистратора данных. Вставьте штекер зонда обратно в монитор, промойте чистую камеру несколькими миллилитрами уравновешенного буфера, затем заполните камеру буфером, закройте кран камеры и включите магнитную мешалку (см. примечание 14). Как только сигнал стабилизируется, откалибруйте кислородный монитор для 100% насыщения воздухом и установите максимальную точку на диаграммном самописце для правильного преобразования единиц измерения содержания кислорода (см. примечание 15).
3.3. Проведение митохондриальной полярографии
На льду оттаивают аликвоты субстратов (глутамат, малат, пируват и сукцинат), АДФ и ДНП.
Заполните камеру свежим дыхательным буфером и, как только стабилизируется исходный уровень (обычно через 1–3 мин), добавьте 5 мкл каждого из желаемых субстратов (см. примечание 4) и наблюдайте за записью в течение 2–5 мин. пока исходный уровень не стабилизируется.
Добавьте в камеру 200–500 мкг свежевыделенных митохондрий (см. примечание 16). Должна быть низкая скорость потребления кислорода (состояние IV или АДФ-лимитирующая скорость), в первую очередь вызванная исходной эндогенной утечкой протонов через внутреннюю мембрану изолированных митохондрий (4).
Добавьте 5 мкл (125 нмоль) АДФ. Добавление АДФ должно стимулировать высокую скорость потребления кислорода (состояние III или скорость стимуляции АДФ), которая вернется к скорости исходного состояния IV, как только экзогенно добавленная АДФ будет поглощена OXPHOS (см. Примечание 17). Для хорошо сопряженных митохондрий скорость состояния III должна быть по крайней мере в три раза выше, чем скорость состояния IV (-) (см.
примечание 18). После возобновления дыхания в состоянии IV в течение 1–2 минут (достаточно времени для точного измерения частоты дыхания) можно сделать второе добавление АДФ, что должно привести к такой же частоте дыхания в состоянии III и переходу обратно в состояние IV (пусть работает в течение 1 –2 мин).
Открыть в отдельном окне
Идеализированный след полярографического сеанса. В момент времени «0» субстрат (5 мкМ глутамата + малата или сукцината) добавляют в камеру, полную насыщенного воздухом буфера для дыхания, и наблюдают стабильный базовый уровень. ( a ) Изолированные митохондрии добавляют до конечной концентрации 0,3 мг/мл. ( b ) Добавляется 125 нмоль АДФ, стимулируя скорость состояния III, которое переходит в состояние IV, как только экзогенный АДФ поглощается OXPHOS. ( c ) DNP (50 мкМ) добавляют для стимуляции максимальной скорости разобщения (UC).
Открыть в отдельном окне
Типичный полярографический след митохондрий личинок Drosophila с глутаматом + малатом в качестве субстрата.
Показан полярографический эксперимент с использованием митохондрий, выделенных из личинок третьего возраста Drosophila melanogaster дикого типа . ( a ) Добавляют глутамат + малат (по 5 мкМ каждого). ( b ) Добавлены митохондрии личинок мух (0,3 мг/мл). ( c ) Добавляют 125 нмоль АДФ. ( d ) Добавляют ДНФ (50 мкМ).
Добавьте ДНФ до конечной концентрации 50 мкМ (см. примечание 6) и измерьте частоту несвязанного дыхания в течение не менее 2–3 минут, чтобы завершить анализ (см. примечание 19).
3.4. Анализ данных
Типичные параметры, определяемые с помощью митохондриальной полярографии, включают скорость в состоянии III, скорость в состоянии IV, RCR, несвязанную скорость и отношение АДФ/О (). RCR (коэффициент контроля дыхания или скорость состояния III/скорость состояния IV) является хорошим индикатором целостности внутренней мембраны изолированных митохондрий и чувствителен к выявлению дефектов OXPHOS, в то время как отношение АДФ/О является прямым отражением фосфорилирования. эффективности и может указывать на аномалии АТФ-синтазы или связывания (2, 4). Несвязанная скорость (UC) отражает максимальную дыхательную способность митохондрий, и в митохондриях дикого типа отношение скорости состояния III/скорости UC обычно составляет от 0,85 до 0,9.5 (4).
С помощью аналитического программного обеспечения LabChart, прилагаемого к цифровому самописцу, скорости потребления кислорода (т. е. состояние III, состояние IV и UC) измеряются по линейным фазам и нормализуются к содержанию белка (скорости выражены в нг атомарного кислорода). /мин/мг митохондриального белка).
Для соотношения АДФ/О количество АДФ, потребляемое в состоянии III (125 нмоль), делится на количество кислорода, потребляемого в состоянии III (нг атомарного кислорода).
Открыть в отдельном окне
Типичная полярографическая кривая митохондрий сердца крысы с сукцинатом в качестве субстрата. Показан полярографический эксперимент с использованием митохондрий, выделенных из сердца крысы дикого типа. ( a ) Добавляется сукцинат (5 мкМ). ( b ) Добавлены митохондрии сердца крысы (0,9 мг/мл). ( c ) Добавляют 125 нмоль АДФ. ( d ) Добавляют ДНФ (50 мкМ).
1. Стерилизовать все исходные растворы фильтрованием через вакуумный фильтр с размером пор 0,22 мкм и хранить при 4°C в течение 1–2 месяцев. Растворы также можно автоклавировать, за исключением растворов, содержащих сахарозу, которая карамелизуется и окрашивает раствор в коричневый цвет.
2. При хранении при температуре 4°C исходный раствор маннита (или другие растворы, содержащие маннит) может осаждаться из раствора. В этом случае просто нагрейте на водяной бане до 65°C, чтобы кристаллы растворились непосредственно перед использованием.
3. ЭГТА не растворяется должным образом без добавления основания. Как только pH достаточно повышается, EGTA быстро переходит в раствор. Будьте осторожны при титровании до pH 7,5, чтобы не перескочить.
4. Исходные растворы имеют концентрацию 0,65 М, так что добавление 5 мкл исходного раствора в микрокамеру дает конечную концентрацию 5 мМ. Наиболее часто используемые субстраты включают малат, глутамат, пируват и сукцинат, и они окисляются с высокой скоростью во многих тканях и типах клеток млекопитающих (3, 4, 6-9).). Как правило, малат + глутамат или малат + пируват используются для анализа дыхания, специфичного для комплекса I, тогда как сукцинат используется для анализа дыхания, специфичного для комплекса II. Пальмитоилкарнитин (0,4 мМ) плюс малат (1 мМ) представляет собой пару субстратов, подходящую для оценки окисления жирных кислот. Аскорбат в сочетании с тетраметилфенилендиамином (ТМФД) для восстановления внутримитохондриального цитохрома c можно использовать для тестирования дыхания непосредственно через комплекс IV (3, 4). Важно следить за тем, чтобы рН субстратов и буфера оставался в пределах от 7,2 до 7,4. Большинство субстратов, используемых для полярографии, представляют собой органические кислоты, и добавление субстратов с ненейтральным pH может разъединить митохондрии.
5. Точность концентрации АДФ важна, поскольку расчет отношения АДФ/О основан на предположении, что каждый микролитр АДФ содержит 25 нмоль.
6. Разобщители разрушают функциональную связь между дыхательной цепью и АТФ-синтазой, рассеивая протонный электрохимический градиент. Мы обычно используем DNP для полярографии, но другие протонные ионофоры, такие как карбонилцианид m -хлорфенилгидразон (CCCP) или карбонилцианид-9Также можно использовать 0015 p -трифторметоксифенилгидразон (FCCP). Исходный раствор ДНП составляет 6,5 мМ; поэтому добавление 5 мкл ДНФ к полному объему микрокамеры приведет к конечной концентрации 50 мкМ.
7. В целом, 1 г ткани млекопитающих обеспечивает выход 0,5–2 мг изолированных митохондрий, в зависимости от конкретной ткани. Для Drosophila , 100 взрослых мух или достаточно личинок третьего возраста, чтобы заполнить 1,5 мл Эппендорф до 0,5 мл даст примерно 0,5 мг митохондрий.
8. Чрезвычайно важно постоянно хранить все реагенты и образцы при температуре 4°C или на льду.
9. Оптимальное отношение объема буфера к массе ткани составляет 10 мл/г ткани. При использовании меньшего количества ткани можно пропорционально уменьшить количество используемого буфера для изоляции.
10. Ткани печени и головного мозга имеют минимальное количество соединительной ткани, поэтому восемь-десять движений пестиком B («плотно прилегающим») обычно приводят к полной гомогенизации. Для тканей с более значительной соединительной тканью, таких как легкие, сердце, скелетные мышцы и почки, можно использовать лезвие бритвы для измельчения ткани на мелкие кусочки, чтобы облегчить гомогенизацию и улучшить выход митохондрий. Кроме того, для сердца и скелетных мышц пестик А («пестик со свободной посадкой») следует использовать для пяти начальных проходов, чтобы гарантировать полное разрушение соединительной ткани, после чего следует пять-шесть дополнительных проходов с использованием пестика В для завершения гомогенизации. Для легочной ткани, которая может быть все еще частично надута после вскрытия, сначала добавьте половину объема необходимого буфера для первых двух ударов из-за захваченного воздуха, содержащегося в образце легочной ткани, чтобы избежать утечки.
11. Для выделения митохондрий из взрослых особей дрозофилы или личинок мы используем пропитанную буфером марлю для фильтрации остатков экзоскелета взрослых особей или жира личинок из гомогената перед центрифугированием.
12. Обязательно учитывайте 0,5% BSA при определении концентрации белка. Либо вычтите его из общей концентрации, либо промойте и ресуспендируйте небольшую аликвоту митохондриального осадка в буфере, не содержащем BSA, перед измерением концентрации белка.
13. Требуется полиэтиленовая мембрана, обеспечивающая диффузию кислорода, но не метаболитов. Пластик из любого обычного пластикового пакета для сэндвичей на самом деле очень хорошо работает в качестве мембраны. Избегайте использования насыщенного раствора KCl, так как выпадающие в осадок кристаллы нарушат оптимальную работу зонда. После нескольких дней использования серебряный анод станет неровным из-за AgCl, что приведет к нестабильности зонда. Таким образом, если датчик демонстрирует нестабильное поведение, которое не устраняется заменой мембраны, старый слой хлорида с анода следует осторожно удалить путем осторожного истирания с помощью прилагаемого абразивного диска (избегайте стирания платинового катода в центре наконечника датчика). Как только наконечник анода станет яркого и чистого серебристого цвета, добавьте новый слой хлорида путем гальванического покрытия раствора KCl с помощью «хлороводорода», поставляемого с зондом.
14. Избегайте попадания пузырьков воздуха в камеру, так как пузырьки вытесняют объем, уменьшая полезный объем камеры.
15. При объеме камеры 650 мкл, постоянной температуре 30°C и высоте над уровнем моря (давление 1 атм.) насыщенный воздухом буфер в камере будет содержать 312 нг атомарного кислорода (10 ).
16. Как правило, митохондрии следует добавлять до конечной концентрации белка 0,3–0,8 мг/мл, а выделенная суспензия митохондрий должна иметь минимальную концентрацию 10 мг/мл, чтобы свести к минимуму объем, добавляемый к камера.
17. Следует добавить достаточное количество митохондрий, чтобы обычный анализ занимал примерно 10–15 мин. Избегайте добавления слишком большого количества митохондрий, что приводит к тому, что анализ занимает менее 5 минут, и это слишком быстро, чтобы удобно добавлять АДФ или ингибиторы. Если анализ занимает более 20–25 минут, митохондрии дикого типа могут демонстрировать функциональное ухудшение. Оптимальное количество митохондрий должно быть определено эмпирически для каждой ткани. По нашему опыту оптимальная концентрация для митохондрий млекопитающих составляет 0,3–0,6 мг/мл, а для митохондрий дрозофилы составляет 0,45–0,9 мг/мл.
18. Отношение частоты в состоянии III к частоте в состоянии IV выражается как коэффициент контроля дыхания (RCR) и должно быть больше 3,0 для хорошо связанных митохондрий дикого типа (4). RCR менее 3,0 для митохондрий дикого типа чаще всего предполагает субоптимальную концентрацию митохондрий или техническую проблему с изоляцией митохондрий, которая повреждает целостность внутренней мембраны.
19. ДНП следует добавлять, пока в микрокамере остается не менее 30% от общего содержания кислорода. Это гарантирует, что максимальное несвязанное дыхание происходит в течение достаточного периода времени, чтобы можно было точно определить скорость (т. е. не менее 2 мин).
1. Chance B, and Williams GR (1955) Простой и быстрый анализ окислительного фосфорилирования, Nature 175, 1120–1121. [PubMed] [Google Scholar]
2. Brand MD, and Nicholls DG (2011) Оценка митохондриальной дисфункции в клетках, Biochem. Дж 435, 297–312. [Бесплатная статья PMC] [PubMed] [Google Scholar]
3. Barrientos A (2002) Оценка активности OXPHOS in vivo и in organello, методы 26, 307–316. [PubMed] [Google Scholar]
4. Траунс И.А., Ким Ю.Л., Джун А.С. и Уоллес Д. К. (1996) Оценка митохондриального окислительного фосфорилирования в биоптатах мышц, лимфобластах и трансмитохондриальных клеточных линиях пациентов, Методы Энзимол
264, 484–509. [PubMed] [Google Scholar]
5. Bradford MM (1976) Быстрый и чувствительный метод количественного определения количества белка в микрограммах с использованием принципа связывания белка с красителем, Anal Biochem. 72, 248–254. [PubMed] [Академия Google]
6. Пухович М.А., Варнес М.Е., Коэн Б.Х., Фридман Н.Р., Керр Д.С. и Хоппель С.Л. (2004) Анализ окислительного фосфорилирования: оценка интегрированной функциональной активности митохондрий скелетных мышц человека – тематические исследования, Митохондрия 4, 377–385. [PubMed] [Google Scholar]
7. Rasmussen UF, and Rasmussen HN (2000) Митохондрии четырехглавой мышцы человека: функциональная характеристика, Mol Cell Biochem 208, 37–44. [PubMed] [Google Scholar]
8. Rossignol R, Letellier T, Malgat M, Rocher C, and Mazat JP (2000) Тканевые вариации в контроле окислительного фосфорилирования: значение для митохондриальных заболеваний, Biochem J
347
Ч. 1, 45–53. [Бесплатная статья PMC] [PubMed] [Google Scholar]
9. Wenchich L, Drahota Z, Honzik T, Hansikova H, Tesarova M, Zeman J, and Houstek J (2003) Полярографическая оценка активности митохондриальных ферментов в изолированных митохондриях и пермеабилизированных мышечных клетках человека с наследственными митохондриальными дефектами, Physiol Res 52, 781–788. [PubMed] [Google Scholar]
10. Трусдейл Г.А. и Даунинг А.Л. (1954) Растворимость кислорода в воде, природа. 173, 1236. [Google Scholar]
Доля рынка графитовых электродов, прогноз (2022–27)
Доля рынка графитовых электродов, прогноз (2022–27) | Анализ отраслиОбзор рынка
Период обучения: | 2017-2027 гг. |
Базисный год: | 2021 |
Самый быстрорастущий рынок: | Азиатско-Тихоокеанский регион |
Самый большой рынок: | Азиатско-Тихоокеанский регион |
CAGR: | 4,6 % |
Нужен отчет, отражающий, как COVID-19 повлиял на этот рынок и его рост?
Обзор рынка
Рынок графитированных электродов оценивался в 8 791,65 млн долларов США в 2021 году, и ожидается, что в течение прогнозируемого периода (2022–2027 годы) среднегодовой темп роста составит 4,6%.
Вспышка COVID-19 в 2020 г. негативно повлияла на рынок графитированных электродов. Однако с возобновлением работы в основных отраслях конечных пользователей рынок значительно восстановился в 2021 г.
- Ожидается, что в краткосрочной перспективе сильный рост производства стали в странах с развивающейся экономикой и увеличение доступности стального лома в Китае будут стимулировать рост рынка.
- С другой стороны, рост цен на игольчатый кокс, вероятно, будет препятствовать росту исследуемого рынка.
- Ожидается, что рост производства стали с использованием технологии электродуговых печей (ЭДП) в Китае откроет новые возможности для рынка в ближайшие годы.
- Ожидается, что Азиатско-Тихоокеанский регион будет доминировать на рынке из-за высокого спроса со стороны Китая.
Объем отчета
Графитированные электроды широко используются в электродуговых печах и плавильных печах на сталелитейных заводах, кремниевых заводах и других предприятиях. Рынок сегментирован по марке электродов, применению и географии. В отчете также рассматриваются размер и прогноз рынка графитированных электродов в 15 странах по регионам. Для каждого сегмента размер рынка и прогнозы были сделаны на основе объема (килотонны) и дохода (млн долларов США).
Electrode Grade | |
Ultra High Power (UHP) | |
High Power (SHP) | |
Regular Power (RP) |
Application | |
Дуговая электродуговая печь | |
Кислородная печь | |
Применение без стали |
| |||||||
| |||||||
| |||||||
| |||||||
|
Объем отчета может быть
настроены в соответствии с вашими требованиями. Кликните сюда.
Ключевые тенденции рынка
Сегмент электродуговых печей будет доминировать на рынке
- Электродуговая печь (ЭДП) плавит стальной лом, ЖПВ (железо прямого восстановления), ГБЖ (горячее брикетированное железо, прессованное ЖПВ) или чугун в твердой форме для производства стали. На маршруте ЭДП электричество обеспечивает необходимую мощность для плавления сырья.
- Графитовый электрод в основном используется в процессе производства стали в электродуговых печах (ЭДП) для плавления стального лома. Электроды изготовлены из графита из-за их способности выдерживать высокие температуры. В ЭДП кончик электрода может достигать 3000ºF, что составляет половину температуры поверхности Солнца. Размер электродов широко варьируется от 75 мм до 750 мм в диаметре и до 2800 мм в длину. В электродуговых печах (ЭДП) на сталелитейных и чугунолитейных заводах обычно используются электроды UHP (обычно 350 мм и больше) и электроды HP и UHP (обычно 400 мм и меньше) соответственно.
- Резкий скачок цен на графитированные электроды в недавнем прошлом привел к увеличению затрат электросталеплавильных заводов. В Китае цены на графитированные электроды в 2019 году выросли более чем на 700% по сравнению с 2017 годом. По состоянию на 16 февраля 2022 года средняя цена графитированных электродов в Китае составляла 20 818 юаней за тонну, что на 5,17% больше, чем в 2017 году. начала года и 44,48% к аналогичному периоду прошлого года.
- В Китае на сталь ЭДП приходится около 10% от общей доли в текущем сценарии. Однако ожидается, что ситуация изменится из-за растущей доступности стального лома в стране и государственной политики, поддерживающей использование стального лома. Ожидается, что из-за таких факторов спрос на графитированные электроды, используемые для применения в ЭДП, будет неуклонно расти в течение прогнозируемого периода.
- Графитированные электроды на сталелитейных заводах находятся в состоянии восстановления. Запас графитовых электродов недостаточен по сравнению с предыдущими годами.
Ожидается, что с возобновлением работы сталелитейных заводов спрос на него возрастет.
- В заключение, в связи с благоприятным спросом, ограниченным предложением и высокой стоимостью ожидается рост цен на графитированные электроды, что повысит спрос на них в течение прогнозируемого периода.
Чтобы понять основные тенденции, загрузите образец Отчет
Китай будет доминировать на рынке Азиатско-Тихоокеанского региона
- Китай занимает наибольшую долю в потреблении и производственных мощностях графитированных электродов в мире. В настоящее время в Китае насчитывается более 40 официальных производителей графитированных электродов, а за последние 2-3 года было замечено 30 новых участников, производящих другие огнеупорные изделия, наряду с электродами.
- Китайские производители поспешили установить мощности для графитированных электродов, когда в 2017 году страна начала активно увеличивать темпы производства стали с использованием электродуговых печей.
Директивные органы Китая активно поощряли технологии производства стали в ЭДП для сокращения выбросов углерода и добиться устойчивости в металлургической отрасли страны. Производство автомобилей в 2021 году составило 2 60 82 220 единиц.
- В марте 2022 года Xinyu Steel приступила к строительству своего проекта ЭДП мощностью 100 метрических тонн. Новый завод будет иметь мощность по производству жидкой стали 1 миллион метрических тонн в год.
- Китайские производители графитированных электродов прилагают постоянные усилия для закупки качественного игольчатого кокса либо за счет импорта, либо за счет внутренних закупок, обеспечивая при этом технологии для повышения качества. Китайские производители электродов также сосредоточены на производстве большего количества графитовых электродов класса UHP размером более 700 мм.
- Доля производства электростали в Китае ниже, чем в среднем по миру. В связи с политическими факторами ожидается, что в будущем эта доля увеличится, что может повысить спрос на сверхмощные графитовые электроды.
- Таким образом, ожидается, что вышеупомянутые факторы будут способствовать росту рынка графитированных электродов в Китае.
Чтобы понять тенденции географии, загрузите образец Отчет
Конкурентная среда
Рынок графитированных электродов частично консолидирован: на пять крупнейших игроков приходится примерно 37% всего рынка с точки зрения производственных мощностей в 2021 году. Некоторые из ключевых игроков включают SHOWA DENKO KK, GrafTech International, Fangda Carbon New Material Co. . Ltd, ZHONGZE GROUP и Дэн Карбон.
Основные игроки
- ГрафТех Интернэшнл
- ЧЖОНГЗЭ ГРУППА
- Дэн Карбон
- ШОВА ДЕНКО КК
- Fangda Carbon New Material Co. Ltd
СОДЕРЖАНИЕ
1. ВВЕДЕНИЕ
1.1. 4. ДИНАМИКА РЫНКА
4.1 Факторы
4.1.1 Уверенный рост производства стали в развивающихся странах
4.
1.2 Увеличение доступности стального лома в Китае
4.2 Restraints
4.2.1 Soaring Prices of Needle Coke
4.2.2 Other Restraints
4.3 Industry Value Chain Analysis
4.4 Porter’s Five Forces Analysis
4.4.1 Рыночная власть поставщиков
4.4.2 Рыночная власть покупателей
4.4.3 Угроза новых участников
4.4.4 Угроза заместительных продуктов и услуг
4.4.5 Степень конкуренции
4.5 Производственная мощность стали по стране
5. Электрик
- .
.
5.1.1 Сверхвысокая мощность (UHP)
5.1.2 Высокая мощность (SHP)
5.1.3 Обычная мощность (RP)
- 9 Применение0012
5.2.1. Электрическая дуга печь
5.
2.2 Основная кислородная печь
5.2.3. Неустубка
5.3 Geography
5.3
5.3
5.3.
5.3.1.1 Китай
5.3.1.2 Индия
5.3.1.3 Япония
5.3.1.4 Южная Корея
5.3.1.1.4.0231
5.3.2 North America
5.3.2.1 United States
5.3.2.2 Canada
5.3.2.3 Mexico
5.3.3 Europe
5.3. 3.1 Германия
5.3.3.2 Соединенное Королевство
5.3.3.3 Франция
5.3.3.4 Италия
5.3.3.5 Остальная Европа
31505.3.4.1 Brazil
5.3.4.2 Argentina
5.3.4.3 Rest of South America
5.3.3.5.0012
5.3.5 Middle-East and Africa
5.
3.5.1 Saudi Arabia
5.3.3.2.2 Южная Африка
5.3.5.3 Остальная часть Среднего Востока и Африки
6. Соревновательный ландшай
6. Соревновательный средний. , и соглашения
6.2 Доля рынка (%)/ Анализ ранжирования
6.3 Стратегии, принятые ведущими игроками
6.4 Профили компании
6.4.1 DAN
6.4.1 DAN
6.4.1.
6.4.3 Fangda Carbon New Material Technology Co. Ltd
6.4.4 GrafTech International
6.4.5 Graphite India Limited
6.4.6 HEG Limited 6.4.60012
6.4.7 Kaifeng Pingmei New Carbon Material Co. Ltd
6.4.8 Nantong Yangzi Carbon Co. Ltd
6.4.9 Nippon Carbon Co. Inc.
6.4.11 SEC CARBON LTD
6.4.12 SHOWA DENKO KK
6.
4.13 Tokai Carbon Co. Ltd
6.4.14 ZHONGZE GROUP
*List Не исчерпывающий
7. Рыночные возможности и будущие тенденции
7.1 Рост производства стали через технологию EAF в Китае
** С учетом доступности
. Вы хотите проверить раздел мудро прайс-лист?
Часто задаваемые вопросы
Каков период изучения этого рынка?
Рынок графитовых электродов изучается с 2017 по 2027 год.
Каковы темпы роста рынка Графитовый электрод?
Рынок графитовых электродов будет расти в среднем на 4,6% в течение следующих 5 лет.
Какой регион имеет самые высокие темпы роста рынка Графитовый электрод?
Азиатско-Тихоокеанский регион демонстрирует самый высокий среднегодовой темп роста в 2021–2026 годах.
Какой регион имеет наибольшую долю рынка Графитовый электрод?
Азиатско-Тихоокеанский регион будет иметь наибольшую долю в 2021 году.
Кто является ключевыми игроками на рынке Графитовый электрод?
GrafTech International, ZHONGZE GROUP, Dan Carbon, SHOWA DENKO KK, Fangda Carbon New Material Co. Ltd — основные компании, работающие на рынке графитовых электродов.
80% наших клиентов ищут отчеты на заказ. Как ты хотите, чтобы мы подогнали вашу?
Пожалуйста, введите действительный адрес электронной почты!
Пожалуйста, введите корректное сообщение!
Скачать бесплатный образец сейчас
Имя
Г-н/Г-жаГ-жаГ-жаДоктор-Г-жа
Фамилия
Ваш адрес электронной почты
Отправляя, вы подтверждаете, что согласны с наша политика конфиденциальности
Скачать бесплатный образец сейчас
Ваш адрес электронной почты
Отправляя, вы подтверждаете, что согласны с наша политика конфиденциальности
Сообщение
Отправляя, вы подтверждаете, что согласны с нашей конфиденциальностью политика
Спасибо!
Спасибо за покупку. Ваш платеж прошел успешно. Отчет будет предоставлен в течение 2-4 часов. Наш торговый представитель свяжется с вами в ближайшее время и сообщит подробности.
Не забудьте также проверить папку со спамом.
Извините
«Извините! Платеж не прошел. Для получения дополнительной информации обратитесь в свой банк.»
Антиоксидант для графитового электрода «CERACOAT EL-300» | Сталеплавильный материал | Продукция
Антиоксидант для графитового электрода «CERACOAT EL-300» | Сталеплавильный материал | Продукты | ШИНТО промышленная компания, ООО- Дом
- Продукты
- Материал для производства стали
- Антиоксидант для графитового электрода «CERACOAT EL-300»
Антиоксидант импрегнированного типа для графитовых электродов «CERACOAT® EL-300», разработанный нашей компанией, высокоэффективен в снижении расхода на окисление графитированных электродов, улучшении удельного расхода электродов, снижении удельной себестоимости электроды.
Этот новый антиоксидантный агент графитового электрода может значительно снизить окисление «сбоку» за счет простого процесса пропитки погружением.
Он был принят крупными отечественными и европейскими сталелитейными заводами и получил высокую оценку.
Характеристики CERACOAT® EL-300
Отличная защита от окисления
EL-300 легко проникает в микроотверстия, имеющиеся в электродах, благодаря низкой вязкости и образует пропитанный и покрытый толстый слой от 15 до 30 мм от поверхности.
Когда электрод не охлаждается водой (распылением), вы можете получить наибольшее преимущество, сократив потребление электрода примерно на 15% с помощью нашего EL-300. В частности, EL-300 обладает превосходными характеристиками в случае непригодного для использования процесса водяного охлаждения, такого как плавка нержавеющей стали и специальной легированной стали, а также рафинирование в печи-ковше, что позволяет избежать водородного охрупчивания.
Компания (в Японии) | Печь/Производство (Тонн/Месяц) | Продукты | Электрод | Норма расхода (Электрод (кг)/Сталь (кг)) | |||
---|---|---|---|---|---|---|---|
С водяным охлаждением или без | Размер | Непропитанный (Обычный) | Пропитанный (После обработки) | Коэффициент уменьшения (%) | |||
А | ЭДП (AC) AC 150 т/тепло 80 000 т/месяц | Легированная сталь (основная) Нержавеющая сталь (иногда) | С водяным охлаждением | UHP (сделано в Японии) φ610×2800 мм (средний вес = 1450 кг) | 1,586[100%] | 1,430[90,16%] | 9,84% |
Б | LF AC 70 т/нагрев 40 000 т/месяц | Углеродистая сталь | без водяного охлаждения | (сделано в Китае) RP φ400 x 1800 мм (средний вес = 375 кг) | 0,235[100%] | 0,192[81,70%] | 18,30% |
С | ЭДП (AC) AC 80 т/нагрев 48 000 т/месяц | Нержавеющая сталь | без водяного охлаждения | UHP (сделано в Японии) φ510 x 2400 мм (средний вес = 870 кг) | 3,468[100%] | 3,002[86,56%] | 13,44% |
Низкая стоимость пропитки
Наиболее подходящий объем пропитки EL-300 составляет от 0,6 до 1,0% от веса электрода.
В случае диаметра 20 дюймов (внешний диаметр 510 мм) x длина 1800 мм (прибл. 6 футов) 625 кг будет израсходовано только от 4 до 6 кг EL-300. Это очень экономично.
Без потери проводимости
Электропроводность электродов после пропитки ЭЛ-300 оставляют без изменений. EL-300 никогда не препятствует проводимости.
Поскольку EL-300 высыхает после пропитки, внешний вид после обработки EL-300 такой же, как и до обработки, и с электродом с покрытием можно обращаться как обычно.
Стоимость обработки может быть снижена, поскольку не требуется специального оборудования или технологий.
Метод пропитки очень прост: просто погрузите электрод в ванну на определенное время, затем высушите естественным образом на воздухе в течение 5-10 дней, что снизит затраты на покрытие.
Предотвращено расшатывание ниппеля
EL-300, пропитавший зазор между внутренней резьбой электрода и наружной резьбой ниппеля, при температуре выше 300 ℃ превращается в прочную керамику.
Прочная адгезия при высоких температурах предотвращает расшатывание и поломку ниппелей.
Не подвержено влиянию водяного охлаждения
EL-300 нельзя снимать и портить проточной водой на поверхности электродов. Производительность стабильна независимо от того, используется водяное охлаждение или нет.
Методы пропитки
Метод естественной пропитки
Это метод пропитки погружением в атмосферу. Это самый простой способ пропитки электрода, просто окуните вкладку EL-300 и подождите от 10 до 30 минут.
Подходит для обработки небольшого количества. Не говоря уже о том, что требуется сушка.
Метод декомпрессионной пропитки
Это метод пропитки путем погружения в атмосферу с пониженным давлением (макс. 400 мм рт. ст.). Его можно обрабатывать за короткое время, примерно в десять раз меньше, чем при пропитке при атмосферном давлении, но для этого требуется резервуар, выдерживающий пониженное давление, и вакуумный насос.