Все что вас интересует об антикоррозии
Мы проанализировали вопросы пользователей интернета об антикоррозии и решили собрать ответы на них в одном материале. Чтобы вы могли получить сразу все ответы на интересующие вас вопросы в одном месте. Это сэкономит вам время, силы и нервы. А нам будет приятно, что люди, интересующиеся антикоррозией, узнали много полезного и интересного от нас.
1. Как правильно: «антикоррозийный» или «антикоррозионный»?
Если обратиться к словарям, то оба варианта слов не окажутся ошибкой. То есть, правильным является и то, и другое слово. Однако, вариант «антикоррозийный» более популярен, чем «антикоррозионный» (196000 против 127000). Видимо из-за благозвучности.
2. Какими бывают антикоррозийные покрытия для металла?
Антикоррозийные покрытия подразделяются разными способами. По сфере применения: промышленные, декоративные, универсальные. Для разных условий эксплуатации: на открытом воздухе, в химически агрессивной среде, при высоких температурах.
3. Почему нержавеющую сталь также необходимо защищать от коррозии?
Несмотря на название, к сожалению, нержавеющая сталь тоже подвержена коррозии. Хоть и в меньшей степени, чем простое железо. Поэтому, если вы хотите для металлов полной и долговечной защиты от коррозии, то используйте антикоррозийные покрытия даже для нержавеющей стали.
4. Какие антикоррозийные покрытия являются самыми эффективными?
Подбирать антикоррозийное покрытие необходимо в каждом конкретном случае. Нужно учитывать условия нанесения, эксплуатации, удобство применения каждого конкретного метода и состава. Только тогда можно понять – какое антикоррозийное покрытие лучше всего сработает в вашем случае.
5. Для чего нужны антикоррозийные грунты?
Главная задача антикоррозионной грунтовки — остановить процесс коррозии, изолировать поверхность металла от соприкосновения с влагой, обеспечить высокую адгезию грунта с металлом и с последующим декоративным покрытием. Для решения этой задачи, в частности, в состав грунтовки включают ингибиторы коррозии (вещества, замедляющие коррозию металлов).
Некоторые производители, кроме того, добавляют целевые добавки, химически преобразующие ржавчину. В этом случае на этикетке можно увидеть, к примеру, такую надпись: «грунтовка содержит ингибиторы коррозии и целевые добавки, позволяющие наносить ее на плотную ржавчину толщиной до 100мкм». К грунтовкам по металлу обычно не предъявляется высоких требований по стойкости к атмосферным воздействиям, влажности, свету и т.д. По этой причине обработанный металл необходимо перекрывать по слою грунтовки краской или эмалью.
В большинстве случаев антикоррозионные грунтовки перекрываются специальными антикоррозионными красками и эмалями, содержащими в своём составе антикоррозионные пигменты. Если применять грунт (который нужно применять всегда), то металлические конструкции смогут не заржаветь и прослужить вам долгие годы, вплоть до окончания срока эксплуатации самой конструкции.
6. Чем антикоррозийные краски отличаются от антикоррозийных эмалей?
Эмали представляют собой суспензию пигментов в лаках. При высыхании они образуют твердую, блестящую, эластичную пленку. Защитное действие эмалей заключается в механической изоляции поверхности металла от внешней среды, ингибирующим действием пигментов и высоким сопротивлением пленки к перемещению ионов. Механическая изоляция достигается при отсутствии пор в лакокрасочном покрытии.
Однако все краски частично проницаемы по отношению к воде и кислороду воздуха. Кроме того, при старении покрытия изоляция обычно ухудшается, появляются микротрещины и поры, что сильно снижает защитные свойства красочных покрытий. Для повышения механической изоляции поверхности от внешней среды металлическое изделие вначале покрывают слоем грунта, а затем несколькими слоями краски. В этом случае происходит закупорка пор и микротрещин, и покрытие становится практически непроницаемым.
Защитные свойства лакокрасочных материалов в значительной степени зависят от вида применяемого пигмента. Пигмент не только повышает прочность и придает цвет пленке, но и может служить эффективным ингибитором коррозии. Вода, проникающая к поверхности металла через поры в краске, становится менее агрессивной вследствие растворения в ней пигмента-ингибитора, в качестве которых используют свинцовый сурик, хромат цинка, цинковую или алюминиевую пудру.
Отсюда можно сделать выводы, что эмали защищают дольше и надежнее, чем краски. Но, какие бы пигменты не применялись в красках или эмалях, срок службы лакокрасочных покрытий при интенсивном использовании металлических объектов составляет примерно 3-5 лет.
7.
Как сделать защиту от коррозии металлов долговечной?
Для этого необходимо не экономить и каждые 3-5 лет подкрашивать конструкцию, а применить более надежный и долговечный способ защиты от коррозии. Тем более, что его однократное применение в итоге сэкономит вам гораздо больше средств.
Как мы уже писали выше, наиболее долговечным и эффективным способом защиты от коррозии металлов признано цинкование. Именно цинковое покрытие по проведенным исследованиям, лучше всего и дольше (более 50 лет) защищало металлические изделия от коррозии, эксплуатируясь в разных условиях.
8. В чем особенность цинкования? Почему цинк так хорошо защищает?
Существует множество металлов, которые медленно коррозируют: хром, олово, алюминий, медь. Однако цинк выделяется среди этой группы «прочных» металлов тем, что обеспечивает дальнейшую защиту от влаги и кислорода даже при повреждении покрытия, в то время как защита олова или алюминия при нарушении целостности слоя слабеет или даже начинает способствовать коррозии.
Цинк защищает металлы сразу двумя способами — барьерным (пассивным) и катодным (также называемым активным, протекторным или электрохимическим).
9. Что такое катодная или электрохимическая защита?
Катодная защита подразумевает, что цинк при нанесении на железо образует с ним гальваническую пару, в которой железо — менее активный металл, а цинк — более активный. При контакте с влагой и кислородом цинк-анод вступает в реакцию первым, жертвует свои электроны на борьбу с коррозией, а железо — катод принимает электроны, защищается и остается практически не тронутым ржавчиной. Защитный процесс продолжается до полного истощения слоя цинка.1 слоя в 40-60 мкм хватает на 10-25 лет.
Обычно, те покрытия, которые обладают катодным способом защиты, обладают и обычным – барьерным. Сразу 2 способа защиты, которые сменяют друг друга, очень пригождаются металлам с первого дня эксплуатации. Дело в том, что любое покрытие составом не герметично на 100%, а имеет дефекты и поры. Цинковое покрытие также может пропускать некоторое количество кислорода на начальном этапе использования. Именно тогда оно защищает металлы от ржавчины протекторным или электрохимическим способом. В процессе эксплуатации происходит уплотнение структуры покрытия, полное растворение цинковых соединений и вступает в силу барьерная защита, как при горячем цинковании. Если целостность покрытия будет нарушена (царапины, механические повреждения, разъедание химикатами), то за работу снова возьмется катодная защита.
10. Как лучше всего наносить цинковое покрытие? (цинкование)
Для нанесения цинкового покрытия было изобретено немало способов. Некоторые из них применяются и по сей день. В основном, это: горячее цинкование, гальваническое, термодиффузионное, газотермическое цинкование и холодное цинкование. Самыми распространенными сегодня являются горячее и холодное цинкование. Именно эти два способа, можно сказать, борются за место самого эффективного метода защита от коррозии.
Есть сторонники горячего цинкования, так как оно применяется уже более 160 лет и является стандартом в защите металлов от коррозии. Им занимаются специалисты, а применить его самостоятельно нельзя. То есть, вам нужно отвезти конструкцию или изделие в специальную компанию, которая занимается горячим цинкованием, а потом забрать в готовом, защищенном виде. Для кого-то это удобнее.
Холодное цинкование вы можете применять сами, не прибегая к помощи специалистов, прямо там, где используются ваши конструкции или изделия. Холодное цинкование служит тот же срок, что и горячее, а иногда и превосходит его. Подробно обо всех способах цинкования, об их минусах и плюсах вы можете прочитать в нашей статье: Виды цинкования металлов: как защитить от коррозии?
Есть вопросы по выбору состава? Обращайтесь в представительство в вашем городе:
в Санкт-Петербурге: +7 (812) 603-41-53, +7 (921) 927-58-47
в других городах: 8 (800) 707-53-17
e-mail: info@terazinc. ru
А самые эффективные составы для холодного цинкования вы можете посмотреть в разделе каталога Холодное цинкование.
Антикоррозийные защитные покрытия металла: виды, составы
Коррозия – это неизменный процесс разрушения металла, который происходит в результате взаимодействия железа или сплавов металлов с окружающей средой. При столкновении с молекулами воздуха или воды происходит медленное и постепенное ржавление всех металлических изделий. Через некоторое время данные изделия приходят в негодность. Но этого можно избежать. Если использовать специальное антикоррозийное покрытие.
Антикоррозийное покрытиеЧто же происходит с металлом при его соединении с агрессивными средствами, при длительном соприкосновении с водой:
- Он теряет свои твердые свойства и износостойкость.
- Разрушается структура металла.
- Изменяется его цвет.
Поэтому в строительстве используют различные антикоррозийные покрытия для защиты его от деформации.
Зачем нужна антикоррозионная защита
Теперь более подробно разберем зачем нужна антикоррозионная защита. Особенно важна такая защита для автомобилей. Так как противогололедные присадки, которыми посыпают трассу во время гололеда зимой, различные дефекты и царапины, образующиеся в результате попадания камешков и песчинок во время проезда по сельским дорогам, существенно снижают срок службы машины. А именно они позволят проникнуть ржавчине внутрь металла и разъесть его. В таких случаях защитные покрытия очень важны.
Коррозия
А стальные и чугунные предметы со временем теряют герметичные свойства, теплопроводность и прочность без должного антикоррозионного покрытия. Они становятся совершенно непригодны для проведения работ с ними в дальнейшем. Учеными было подсчитано, что около десяти процентов всего добываемого на земле металла уходит затрачивается на то, чтобы залатать дыры, которые появляются из-за промедления нанесения антикоррозионного покрытия. Или вообще не наносится антикоррозионная защита.
Помимо бытовых аварий, коррозия металлов может спровоцировать и экологические катастрофы. Из износившихся трубопроводов в любое время могут вытекать тонны нефти и газа, которые естественно будут загрязнять атмосферу земли, уничтожая флору и фауну.
Вот почему так важно вовремя покрывать все металлические изделия антикоррозионными покрытиями. Конечно, полностью нельзя избежать появления ржавчины и старения стали, железа, чугуна, но можно приостановить это негативное влияние.
В наше время борьба с коррозией была разделена на несколько групп, в которых используются различные методы сопротивления ржавлению.
- Защищают изделия с помощью электрохимии.
- Выпускаются устойчивые к ржавлению материалы.
- Вводятся специальные соединения в среду ржавления.
- Эксплуатируют детали и конструкции из металлов правильно, не подвергая насильственному разрушению.
- Мастика против коррозии
- Обработанные мастикой трубы
Для этого были созданы специальные средства, антикоррозийные материалы и методы их нанесения на металлы.
Методы антикоррозийной защиты
Антикоррозионное покрытие металла защищает от воздействия негативной атмосферы. Методы нанесения таких покрытий тоже различаются как по составу, так и по способу их нанесения.
Самым распространенным способом защиты является покраска антикоррозионными средствами. Жидкое антикоррозионное вещество наносится на поверхность, которую необходимо защитить, с помощью кисти, валика или распыляется. А после того, как краска высохнет, образуется пленка, которая плотно прилегает к изделию и защищает его от коррозии. В использовании такого метода есть некоторые минусы. Например, краска способна пропускать влагу или кислород, которые вызывают коррозию. Поэтому перед тем, как провести покраску, поверхность прежде всего грунтуют.
Антикоррозийное средство KUDO
Итак, вторым методом является грунтовка. Она также наносится на материал, как и краска. Но защищает его гораздо сильнее, так как содержит в себе мелкодисперсный порошок цинка, в который добавлен оксид цинка. Вступая во взаимодействие с железом, такое вещество защищает его от коррозии.
Другим распространенным методом защиты от ржавления металлических конструкций является нанесение металлических антикоррозийных покрытий. Такой способ представляет собой гальванизацию, плазменное напыление или сверхзвуковое, электроискровые способы покрытия. Такая защита более надежна. Она не вызывает тяжелых негативных последствий при повреждении конструкции.
Однако при использовании данного метода необходимо еще и учитывать совместимость элементов, из которых изготовлена продукция.
Еще одним способом для защиты металлических изделий от влаги и кислорода является керамическое покрытие. Но этот метод применяется только при изготовлении высокотемпературных конструкций. Потому что он требует сильного нагрева для создании высокого уровня адгезии керамики к изделию.
Антикоррозийное керамическое покрытие на автомобиле
Виды антикоррозийных покрытий
Типов защиты против ржавчины в современном мире очень много. К видам таких антикоррозионных покрытий относятся:
- Эмаль три в одном. Название этой краски означает, что ее можно наносить прямо на ржавчину. Рекомендуется очистить только верхний, рыхлый слой коррозии.
- Грунтовка. Это специальное антикоррозионное покрытие применяется для металла, точнее используется для предупреждения ржавления перед нанесением слоя обычной краски. Этот вид делится на два подвида:
- Для обычных поверхностей. К ним относятся такие поверхности, которые имеют отличную шероховатость, чтобы грунт мог хорошо сцепиться с поверхностью.
- Для проблемных поверхностей. К ним относят изделия из дюралюминия, алюминия, меди, из сплавов, изготовленных из антикоррозийных материалов.
- Протекторные грунтовки. В таких покрытиях присутствует цинковый порошок, который защищает конструкцию.
- Изолирующие грунтовки.
Они защищают сталь от проникновения влаги.
Грунтовка антикоррозийная
Перед нанесением антикоррозионного покрытия необходимо следовать некоторым правилам, чтобы не повредить изделие (если защитный слой краски наносится на оцинкованную поверхность), чтобы пленка плотно пристала и не отшелушивалась при первом прикосновении вредных атмосферных веществ.
Правила проведения обработки
Перед нанесением антикора необходимо подготовить поверхность. Требования к подготовке поверхности выдвигаются такие.
- Очаги ржавчины или потрескавшиеся краска или лак должны быть удалены.
- Поверхность должна быть очищена от грязи, масел и высушена.
- Нанесение антикоррозийного покрытия проводится с помощью специального пистолета, либо кистью или валиком.
Все работы по нанесению антикора должны проводиться регулярно.
На предприятиях же, где слишком завышено воздействие агрессивной среды, используется снижение ее воздействия путем:
- введения ингибиторов;
- удаления соединений, которые являются проводниками ржавчины.
Существуют также СНиПы. Вот некоторые из них.
- Пропитка металла материалом с высокой химической стойкостью.
- Оклеивание специальной пленкой.
- Использование лакокрасочных материалов, оксидных и металлизированных покрытий.
В правилах по предупреждению конструкций от ржавления всегда указывается состав смесей в зависимости от того, в какой местности будут использоваться защищаемые изделия. Составы могут агрессивными, слабоагрессивными, либо неагрессивными вообще.
Локальная антикоррозийная защита
В правилах также указываются среды биологически активные или химически активные. А также они делятся на жидкие, твердые и газообразные.
В любом случае покраска изделия обязательна, так как она придает ему не только защитные свойства от коррозии, но и внешний эстетический вид.
защитные пленки, краски, лаки, народные средства
Распространенная проблема металлических изделий — образований коррозийного слоя и дальнейшее разрушение детали. Ржавчина появляется из-за длительного воздействия жидкостей или влажного воздуха. Чтобы сохранить целостность изделия, необходимо нанести антикоррозийное покрытие. Для этого используются составы, которые повышают устойчивость металла к коррозии.
Что такое коррозия?
Коррозия — процесс, при котором металлические поверхности разрушаются под воздействием факторов окружающей среды. Если ничего не предпринять, ржавчина приведёт изделие в негодность. Длительное воздействие воды негативно влияет на многие характеристики материала:
- внешний вид поверхности заготовки;
- показатели твердости, износоустойчивости;
- структура материала.
Часто от подобных проблем страдают детали автомобилей, инструменты, которые хранятся в помещениях с высокой влажностью, промышленное оборудование, металлоконструкции. Антикоррозийные составы образуют на поверхности металла защитный слой, который повышает защиту материала от факторов окружающей среды.
Зачем нужна антикоррозионная защита?
Антикоррозионная обработка считается приоритетной задачей для владельцев автомобилей, мастерских, строителей. Связано это с тем, что коррозия внешней поверхности металлических изделий разрушает детали, выводит оборудование из строя. Нарушение целостности металлоконструкций может привести к разрушению зданий. Негативное воздействие влаги и воздуха проявляются на различных деталях, механизмах, изготавливаемых из однородных металлов и сплавов.
Чтобы защитить металл от коррозии, используются химические составы. Они образуют слой, который не позволяет воздуху и влаге разрушить целостность материала.
Средства для антикоррозийной защиты
Существуют различные антикоррозийные покрытия для металла. Их нужно наносить равномерным слоем и не пропускать отдельные участки. Бывают такие виды антикоррозийных покрытий:
- неметаллические;
- металлические;
- неорганические;
- органические.
Борьба с коррозией при помощи органических покрытий
Чтобы защитить металлическую поверхность, используют лакокрасочные составы. Их просто наносить, и они защищают от образования ржавчины.
Преимущества органических соединений:
- Доступная цена.
- Повреждённый защитный слой просто реставрировать.
- Придание заготовке нового оттенка в зависимости от используемого состава.
Недостатки:
- Низкая устойчивость к высоким температурам.
- При длительном воздействии влаги, покрытие смывается.
- Лак не выдерживает сильных ударов, длительного трения.
К органическим соединениям относятся лакокрасочные составы, краски, эмали, пластификаторы, катализаторы, инертные наполнители, пленкообразователи.
Обработка неорганическими средствами
С помощью химической или электрохимической обработки на предприятиях создаются защитные покрытия для металла, которые снижают риск появления коррозии. Существуют растворы на основе химических составляющих, которые применяются для металлов, сплавов.
Ванна для электрохимической обработкиФосфатные пленки
Данный метод защиты от коррозии применяется для черных и цветных металлов. Принцип этого процесса заключается в том, что металлическую заготовку погружают в ёмкость с раствором цинка и кислых фосфорных солей. Перед этим смесь разогревается до 97 градусов по Цельсию.
Фосфатные пленки недолговечны. Они не устойчивы к механическим воздействиям. Чаще всего, этот метод используется при обработке деталей, которые эксплуатируются при высоких температурах или в солёной воде.
Оксидные пленки
Второе название этого метода — воронение. Материал покрывается специальной плёнкой с помощью раствора щелочей, на который воздействует электрический ток. После нанесения защитного слоя поверхность принимает тёмный цвет. Метод оксидирования применяется при покрытии деталей, для которых требуется сохранить изначальные размеры. Связано это с тем, что готовый слой по толщине не превышает 1,5 микрона.
Дополнительные способы
Существуют и другие способы защиты металлических поверхностей:
- эмалирование;
- пассивирование;
- анодирование.
Народные средства
В домашних условиях слой ржавчины с металла можно снять различными составами. К ним относится кока-кола, керосин, пищевая сода, парафин, селитра. Деталь обрабатывается составом снаружи или погружается в емкость с ним. Спустя определённый промежуток времени, ржавчину снимают щеткой или наждачной бумагой. Далее поверхность высушивается, покрывается краской, лаком, эмалью.
Защитные краски
В магазинах лакокрасочная продукция представлена в ассортименте. Бывают такие виды красок и лаков:
- акриловые;
- масляные;
- эпоксидные;.
- алкидные.
Такой способ защиты металла используется на предприятиях и в домашних условиях.
Антикоррозийная краскаПравила проведения обработки
Чтобы в домашних условиях нанести антикоррозийное покрытие и надёжно защитить металл от воздействия факторов окружающей среды, нужно соблюдать ряд правил:
- С металлической поверхности счищается слой ржавчины, грязи, налёта.
- Защитный слой наносится после обезжиривания зачищенного металла и нанесения грунтовки.
Краска от коррозии наносится в два слоя.
Антикоррозийное покрытие защищает металлические изделия от разрушительного воздействия влаги и воздуха. Для его нанесения требуется выбрать химический состав и правильно нанести покрытие.
Антикоррозийные ЛКМ
Тип лакокрасочного материала:
Все типы
Изменить
Состав лакокрасочного материала (тип пленкообразователя ПФ,ГФ,ЭП и т.д.):
Все составыИзменить
Бесплатная служба консультаций 8-800-700-59-09по вопросам покупки краски мелким и крупным оптом
Онлайн консультации по Viber +7 (910) 973-59-09
Лакокрасочные материалы для антикоррозийной защиты условно составляют четверть от всей массы эмалей. Защита конструкции от коррозии основная задача проектировщиков и строителей.
Материал конструкций — бетон, железобетон, сталь, алюминий, дерево, камень, 7 и более типов. Антикоррозийные покрытия для защиты от коррозии каждого типа поверхности требуют от производителя краски создание универсального защитного слоя. Конструкции могут быть впервые возводимые, или сооружения на реконструкции, емкости под нефтепродукты, резервуары под химические вещества, трубы.
Защита трубопроводов от коррозии в воде или почве требует толостослойного покрытия. Например, цинкосодержащего грунта или эпоксидной эмали. Антикоррозийная краска легко наносится на новый метал, бетон и любой из 7 типов поверхности, давая адгезию 1-2 балла.
Кроме развития коррозии от влажности, поверхность корродирует от агрессивного воздействия химических веществ окружающей среды, смеси газов промышленной среды, электрокоррозия от воздействия тока, биологическая коррозия.
При повышенной влажности внутри и снаружи конструкции, с учетом преобладающего направления ветра, степень коррозии увеличивается в разы. Антикоррозийный материал подбирают с учетом вышеизложенных требований. Лакокрасочные материалы: краски, эмали, лаки, грунтовки, шпатлевки, применяемые в строительстве производят в соответствии с требованиями ГОСТ Р 52491.
Антикоррозийные краски по пленкообразователю подразделяют:
Антикоррозийное покрытие металла эмалями и красками проводят на предварительно загрунтованную поверхность. Грунтовка антикоррозийная по металлу позволяет продлить службу лакокрасочного покрытия до 10-15 лет.
Выбирая комплекс для антикоррозийной защиты, следует учитывать особенности эксплуатации конструкции, степень агрессивности среды, ее физическое состояние- жидкое или твердое, среда расположения — атмосфера, грунт, вода и т.п. Антикоррозийных красок множество и следует внимательно отнестись к выбору.
Противокоррозионная защита кузова | Кузов автомобиля
Коррозия — это процесс разрушения металла при его физико-химическом или химическом взаимодействии с окружающей средой.
Кузов автомобиля имеет значительное количество замкнутых (скрытых) полостей, щелей, в которых создаются благоприятные условия для возникновения и развития коррозии, так как они плохо проветриваются и в них скапливается влага. Коррозии подвержены также днище кузова, нижние части дверей, стоек, соединения деталей, в том числе места точечной сварки. Часто и сварные швы не имеют достаточной герметизации и являются очагами ускоренной коррозии.
В целях защиты от коррозии металл кузовов современных автомобилей покрывается односторонним или двухсторонним слоем цинка. Однако во время проведения точечной сварки при изготовлении кузова в местах сварки тонкий слой цинка сгорает, в то же время оголенная сталь образует в местах сварки гальванический элемент с цинком, что приводит к коррозии металла кузова.
Исследования защитной способности заводских покрытий эксперты коррозии автомобилей из института коррозии (Швеция) и практический опыт показывают, что после трех лет эксплуатации следы коррозии можно обнаружить на всех автомобилях, независимо от фирмы производителя. Эти факты свидетельствуют о том, что в процессе эксплуатации автомобиля необходимо проводить противокоррозионную обработку кузова.
Разрушение кузова автомобиля при годичной эксплуатации без осуществления профилактической антикоррозионной защиты может наступить через 4…5 лет.
Факторы, влияющие на скорость коррозии металла под защитным покрытием, многочисленны и разнообразны:
- повреждения дорожными абразивными выбросами
- воздействие воды и соли,
- воздействие продуктов сгорания топлива
- температурные перепады
- периодический характер эксплуатации автомобиля
- контакт разнородных металлов
- и т.д.
Для днищ и кузовов автомобилей опаснейшим фактором является воздействие растворов электролитов, образующихся при растворении в талой и дождевой воде солей и агрессивных газов (продуктов сгорания топлива и деятельности промышленных предприятий, образующих в контакте с водой электролиты).
Установлено, что при прочих равных условиях в городской местности износ днища автомобилей протекает в 3…5 раз быстрее, чем в сельской. В этой связи возникает необходимость в регулярной профилактической антикоррозионной защите автомобиля, которая может быть осуществлена с помощью различных химических средств. Защитные покрытия могут быть использованы как для восстановления старого антикоррозионного покрытия, так и для дополнительного нанесения на соответствующие заводские.
Изолировать металл от доступа кислорода очень трудная задача. Основная концепция систем защиты от коррозии – это изолирование поверхности металла от доступа электролита, например, воды. Для изолирования металлов от внешних воздействий применяют специальные антикоррозионные составы, которые можно условно разделить на три поколения.
- Первое — консервационные, изготовленные на основе загущенных масел с добавками ингибиторов коррозии. На вертикальных поверхностях (двери, пороги) эти материалы держатся недолго. Они стекают вниз, оставляя пленку, нестойкую к механическим воздействиям и проницаемую для паров воды.
- Второе — пленкообразующие ингибированные нефтяные составы (ПИНС), хорошо сцепляющиеся с защищаемым металлом.
Воскообразная пленка механически изолирует его от воздействия атмосферы, а ингибиторы блокируют коррозию. Иногда препараты дополнительно содержат модификаторы ржавчины. Они восстанавливают металл, превращая продукты коррозии в дополнительную защитную пленку толщиной около 100 мкм, схожую с грунтом. Некоторые фирмы предлагают составы, в основу которых введен алюминиевый наполнитель. Наполнитель увеличивает ее абразивостойкость и затрудняет проникновение агрессивных ионов (например, хлора) к защищаемому металлу.Кроме того, в последнее время появились препараты с цинковым наполнителем. Его частички, повышая абразивостойкость покрытия, способствуют замедлению электрохимической коррозии. Поскольку электродный потенциал железа больше (положительнее), цинк разрушается вместо стали.
- Третье поколение – материалы, вместо летучих нефтяных растворителей содержащие воду или высокоочищенные масла. Поэтому такие составы не отравляют окружающую среду.
В качестве примера антикоррозионного защитного покрытия можно привести антикоррозионный состав Dinol. Состав, содержит три основных компонента:
- Ингибитор – предназначен для остановки реакции коррозии. Молекулы ингибитора эффективно покрывают поверхность металла и образуют водонепроницаемый слой, а также увеличивают адгезию пленки к поверхности.
- Пленкообразователь – создает механический барьер на поверхности металла от механического воздействия. Он может формировать масляную, восковую или твердую пленку. Первая обладает наименьшей механической прочностью, последняя – наибольшей.
- Третий компонент содержит специальные химические вещества, такие как обезвоживатель и активаторы поверхности, которые активно вытесняют влагу.
Рис. Состав, замедляющий коррозию
Материалы для антикоррозионной обработки кузовов
Рынок материалов для антикоррозионной обработки кузовов представлен многими фирмами производителями. Ниже рассматриваются некоторые из них.
Автоконсервант “Мовиль” используется для обработки скрытых полостей в процессе эксплуатации. Допускается нанесение автоконсерванта на поверхности, ранее покрытые маслами, а также на ржавую поверхность. Рекомендуется обрабатывать полости через каждые два года. Недостатком автоконсерванта «Мовиль» является его непригодность использования для открытых мест кузова и слабая проникаемость в ржавчину.
Разработчики современных технологий предлагают материалы, которые позволят снизить число последовательных операций и применять меньшее число химических продуктов. Шведская фирма AUSON АВ рекомендует для применения 11 типов материалов «Noxudol», каждый из которых для определенных частей и узлов автомобиля сочетает в себе свойства грунтовки и лакокрасочного покрытия. Так, например, Noxudol 900 — композиция, формирующая жесткие и стойкие к механическим воздействиям покрытия, рекомендуется для нанесения на днища кузовов и колесные арки, где особенно ощутимо влияние дорожных абразивных выбросов. Напротив, Noxudol 750 – воскообразный мягкий материал с высокой проникающей способностью и рекомендуется для изоляции закрытых полостей автомобиля внутри порогов, лонжеронов, стоек. Аналогичные предложения поступают от другой шведской фирмы — «Dinol», выпускающей материалы «Dinitrol». Интерес представляет антикоррозионный материал Dinitrol 4942 RAL «Titan», который основан на восковых компонентах, но дополнительно содержит 20% диспергированного алюминия, что резко повышает устойчивость покрытия не только к антикоррозионному, но и к абразивному износу.
НП 000 «Алкид» (Беларусь) для надежной защиты от коррозии предлагает использовать в комплексе антикоры «Аутокрин» и «Ауокрин-177». Антикор «Аутокрин» обладает высокой эластичностью и механической прочностью и используется для нанесения грунтовочного слоя, обеспечивающего надежную защиту всех подверженных воздействию коррозии деталей и узлов автомобиля; «Аутокрин-177» обладает высокой адгезией к различным материалам, отличной эластичностью и прочностью, наносится вторым слоем, обеспечивающим дополнительную защиту обрабатываемой поверхности.
Защитное пленочное покрытие НГ-216Б используется для покрытия узлов и частей автомобиля под кузовом на период транспортирования.
Пластизоль Д-11А применяется для защиты днища кузова от коррозии, абразивного износа и для шумоизоляции новых автомобилей. Толщина покрытия 1,0-1,5 мм.
Мастика противошумная битумная БПМ-1 используется для защиты от коррозии днища кузова в процессе эксплуатации автомобиля. Мастика наносится слоем толщиной 1,0-1,5 мм. Она хорошо снижает шум, но не обладает достаточными противокоррозионными свойствами и не может длительное время противостоять растворам солей, абразивам и другим веществам.
Более качественны мастики Tectyl и Dinitrol, изготавливаемые на восково-олифитической основе, не растрескиваются и не затвердевают в процессе старения, что выгодно отличает их от мастик на битумно-полимерной основе и очень важно при термодинамической и физической подвижности железа кузова.
Пластизоль Д-4А применяется для герметизации сварных швов и стыков деталей на внешних и внутренних поверхностях кузова.
Невысыхающая мастика 51-Г-7 используется для герметизации сочленений кузова, угловых стыков и зазоров.
Нанесение противокоррозионных составов
Противокоррозионные составы необходимо наносить равномерно, они не должны содержать пор. Для их нанесения в скрытых полостях кузова используют пистолет КРУ-1 со специальным упругим трубчатым пластмассовым удлинителем, который одним концом подсоединяется к пневмопистолету с помощью накидной гайки, а на другом конце имеет форсунку, создающая факел распыла. За счет своей упругости удлинитель обеспечивает проникновение распыливающей форсунки в труднодоступные места кузова.
Противокоррозионный состав наносится на поверхности путем воздушного или безвоздушного распыления. При воздушном распылении требуется сжатый воздух под давлением 0,3-0,4 МПа (3-4 кгс/см2), который подается в пистолет-краскораспылитель с бачком и далее в распыливающую форсунку. Лучшее качество покрытия достигается при безвоздушном распылении под давлением до 16 МПа (160 кгс/см2), которое позволяет распылять материалы значительной вязкости.
Кузов автомобиля имеет скрытые полости различной конфигурации и размера, расположенные в различных местах. Соответственно, в этих полостях различный микроклимат — влажность, температура, концентрация электролита. Некоторые участки кузова благодаря более жёсткому микроклимату более подвержены коррозии. Такие участки называются критическими. Примерами таких участков служат полости с обилием микрозазоров. Чем ниже они расположены и чем ближе к моторному отсеку, тем выше скорость коррозии.
Для автомобиля критическими являются следующие участки:
- пороги
- сварные швы
- ниши наружных световых приборов
- колёсные арки
- крылья
- полости лонжеронов и поперечин кузова
- полости дверей, капота и багажника
- стойки кузова
- детали крепления подвески
В процессе эксплуатации автомобиля требуется проверка состояния противокоррозионного покрытия, а в случае необходимости – дополнительная защита, особенно скрытых полостей, путем нанесения специальных противокоррозионных составов, а соединений деталей – нанесением уплотнительных мастик.
На каждый конкретный автомобиль имеется карта-схема противокоррозионной обработки. На карте-схеме обработки имеются четкие указания по местам сверления, какие детали необходимо демонтировать, где наносить соответствующий продукт и какую насадку использовать. Перед началом подготовки автомобиля необходимо закрыть каталитический нейтрализатор и его датчики. Не допускается попадание продукта на тепловой экран нейтрализатора. Перед подъемом автомобиля для сушки необходимо просверлить все отверстия в коробах, порогах, дверях и т.д., предназначенные для обработки скрытых полостей.
Если автомобиль имеет шумоизоляционные накладки в дверях, необходимо проверить, чтобы они не касались других механизмов во время обработки. В противном случае это может вызвать неисправность в механизме электростеклоподъемника или центрального замка.
Для введения противокоррозионных составов в скрытые полости заводом-изготовителем предусматриваются технологические отверстия или проемы, через которые можно пропускать наконечники пистолетов с удлинительными шлангами.
Рис. Обработка скрытых полостей кузова:
а – передней внутренней части двери; б – порогов (струя с сектором распыления 360″)
При отсутствии таких отверстий в отдельных элементах кузова просверливают отверстия сверлом с центровкой диаметром не более 12 мм, которые обеспечивают необходимый доступ. При сверлении важно правильно выбирать скорость вращения, в противном случае можно вывести сверло из строя. Рекомендуется использовать дрели с малой частотой вращения, максимум на 1000 об/мин. Необходимо быть очень внимательными при сверлении автомобилей с дополнительным оборудованием, например, с центральным замком или боковыми подушками безопасности.
В каждой скрытой полости, не имеющей отверстий, сверлится, по меньшей мере, одно отверстие. Оно должно располагаться в самой нижней точке полости, чтобы обеспечить надлежащий дренаж излишков материала.
После введения состава отверстия закрывают резиновыми заглушками. Особое внимание при эксплуатации автомобиля следует обращать на целостность защитного покрытия на днище кузова, которое подвержено более интенсивным внешним воздействиям, а, следовательно, и коррозии.
Подготовка и противокоррозионная обработка скрытых полостей
Вследствие необходимости сложного технологического оборудования и требования высококачественного проведения работ рекомендуется обработку скрытых полостей выполнять на предприятиях автосервиса. Порядок выполнения операций для защиты скрытых полостей от коррозии следующий:
- устанавливают автомобиль на подъемник, снимают детали и обивку, препятствующие доступу в скрытые полости
- промывают водой с температурой 40…50 «С через технологические и дренажные отверстия скрытые полости, низ кузова и арки задних колес (промывать скрытые полости необходимо до тех пор, пока из отверстия не будет вытекать чистая вода, при этом стекла дверей должны быть подняты)
- удаляют попавшую в салон и багажник влагу, продувают сжатым воздухом все скрытые полости и места нанесения противокоррозионных составов
- перегоняют автомобиль в камеру для нанесения противокоррозионного состава и ставят на подъемник, наносят распылением противокоррозионный состав в местах, указанных на рисунках
- опускают автомобиль с подъемника, очищают от загрязнений лицевые поверхности кузова ветошью, смоченной в уайт-спирите
Рис.
Скрытые полости кузова (вид снизу):
1 – поперечина пола задка; 2 – задние лонжероны; 3 – кронштейны домкрата; 4 – средняя поперечина пола; 5 – передние лонжероны пола; 6 – усилители лонжеронов; 7 – кронштейны буферов передней подвески; 8 – поперечина передней подвески двигателя
Рис. Скрытые полости кузова (вид слева):
1 – кожухи фар; 2 – нижняя поперечина передка; 3 – верхняя поперечина передка; 4 – передние лонжероны; 5 – стойки брызговиков; 6 – полости под передними крыльями; 7 – внутренние и наружные пороги дверей; 8 – центральные стойки; 9 – задняя поперечина пола; 10 – задние стойки
Восстановление противокоррозионного и противошумного покрытия днища кузова и арок колес
В процессе эксплуатации автомобиля покрытие на днище кузова подвергается воздействию гравия, песка, соли, влаги, в результате чего мастика и грунтовка повреждаются и стираются. Оголенный металл подвергается коррозии.
На автозаводе на нижнюю поверхность основания кузова, арку колес и лонжероны для шумоизоляции и защиты от коррозии и абразивного износа наносится слой полихлорвинилового пластиката марки Д-11А толщиной 1,0-1,2 мм по эпоксидной грунтовке ЭФ-083.
При повреждениях слоя пластиката без нарушения слоя грунтовки поврежденные участки очищают от грязи, обезжиривают и на сухую поверхность безвоздушным распылением или кистью наносят пластизоль. Сушат пластизоль при температуре 130 «С в течение 30 мин. Ввиду значительной сложности нагрева покрытия кузова до высокой температуры и необходимости полной разборки автомобиля допускается восстановление покрытия нанесением противошумной мастики БПМ-1, сушка которой может проходить в естественных условиях.
Перед восстановлением покрытия автомобиль устанавливают на подъемник, тщательно осматривают низ кузова и выявляют дефекты покрытия. Очищают низ кузова от грязи, удаляют ржавчину шпателем, шкуркой или преобразователем ржавчины. Обдувают низ кузова сжатым воздухом. Затем устанавливают автомобиль на подъемник в камеру для нанесения мастики и снимают колеса. Закрывают барабаны и диски тормозов защитными кожухами, изолируют плотной бумагой и клейкой лентой карданную передачу, глушители, тросы и части кузова, не подлежащие обработке мастикой. Ветошью, смоченной в уайт-спирите, обезжиривают зачищенные до металла места, наносят на них распылением или кистью грунтовку ГФ-073 и дают подсохнуть в течение 5-10 мин. Затем наносят на дефектные места распылением или вручную (кистью либо шпателем) мастику БПМ-1 слоем толщиной 1,0-1,5 мм. Попадание мастики на соседние участки, не имеющие повреждений, должно быть минимальным. В холодное время года мастику перед употреблением выдерживают в теплом помещении. В случае загрязнения мастики ее разбавляют ксилолом (не более 3 %).
Лакокрасочное покрытие на лицевых панелях при загрязнении мастикой очищают ветошью, смоченной в уайт-спирите. Сушат мастику при температуре 18-20 «С не менее 24 ч. Для ускорения сушки выдерживают покрытие при температуре 100-110 «С в течение 30 мин.
9 Лучших Антикоррозийных Средств – Рейтинг 2021 года
Если автомобилю не уделяется должное внимание, со временем кузов покрывается коррозией, и внешний вид машины ухудшается. Виной тому становятся вредные вещества, находящиеся в воздухе, и повышенная влажность. Чтобы этого не произошло, нужно вовремя позаботиться о состоянии транспортного средства. В обзоре представлены лучшие антикоррозийные средства 2021 года, которые помогут защитить авто от появления ржавчины.
Антикоррозийное средство какой фирмы лучше выбрать
Из-за большого ассортимента даже опытные автомобилисты не всегда могут ответить, какой антикор лучше. В первую очередь покупатели ориентируются на положительные отзывы, качество и цену. Но, по мнению специалистов, средства импортного производства пользуются большим спросом. В рейтинг вошли автомобильные антикоры следующих производителей:
- Runway – компания использует для производства автохимии американское сырье. Заводы располагаются на территории России, Китая и США.
- Valvoline – американский бренд знаменит выпуском качественной автокосметики. Компания первой предложила гарантию с возвратом средств на моторное масло.
- Liqui Moly – немецкая компания по праву считается лучшей в Германии, предлагая качественную автохимию и моторные масла.
- Vanger – линейка предлагает разнообразные антикоррозийные средства для авто. Голландская фирма пользуется большим спросом у автолюбителей.
- Rust Stop – канадская компания A.M.T. Inc. представляет лучшие антикоррозийные средства для борьбы с ржавчиной на кузове и днище.
- Normex – фирма выпускает качественные и недорогие товары для кузовного ремонта автомобиля.
- Dinitrol – немецкая торговая марка на протяжении 60 лет выпускает антикоррозийные продукты, помогая защитить авто от ржавчины.
- Oilright – старейшая российская компания поставляет масла, присадки и смазочные материалы собственного производства.
- ВЭЛВ – продукция северо-западной компании популярна у автолюбителей. В ассортименте фирмы более 300 товаров автохимии.
Рейтинг антикоррозийных средств
В ТОП вошли средства отечественного и зарубежного производства, которые не уступают по качеству. Здесь представлены как недорогие материалы для отделки поверхности машины, так и актикоры премиум-класса. При выборе учитывали цену, состав и мнение экспертов. Чтобы получить хороший результат, нужно обращать внимание на следующие факторы:
- Химический состав. Средства изготавливают из синтетических смол, поливинилхлорида и каучука, масла, парафина и воска.
- Вид. Быстро твердеющая мастика предназначена для внешних элементов, а невысыхающая – для скрытых.
- Гидрофобность. Хороший состав отталкивает влагу и электролиты с поверхности авто.
- Консистенция. Текучий материал заполняет все трещины и повреждения.
- Гладкость. После высыхания на поверхности должна образовываться эластичная защитная пленка.
- Структура. Однородная масса легко ложится и равномерно распределяется по металлу.
- Прочность. Защищенная поверхность легко противостоит ударам гравия и воздействию пыли.
- Надежность. Качественная антикорозийка при нагрузке не трескается и не отслаивается.
Современные защитные средства продлевают срок службы автомобиля и повышают комфорт в салоне. Вышеназванные критерии помогут сделать верный выбор, и купить качественный товар, который всегда будет под рукой. Обработку поверхности лучше проводить сразу после приобретения машины.
Лучшие антикоррозийные средства для днища
Антикор для днища автомобиля в первую очередь обеспечивает защиту металлической поверхности от электролитов. Он должен быть эластичным, прочным и выдерживать климатические условия. Чаще всего покупают битумную мастику, которая защищает от механического воздействия и не разрушается при столкновении с препятствиями. Также в продаже есть материалы, замедляющие коррозию.
Runway
В состав средств этой линейки входит полимерная смесь, которая надежно защищает покрытие. Днище становится устойчивым к любому механическому повреждению и воздействию ржавчины. Купить такой антикор можно недорого в любом автосалоне. Особой популярностью пользуется гальваническое покрытие, в состав которого входит цинк. Химическая реакция с механической поверхностью образует крепкую пленку серого оттенка. Также материал используют при грунтовке кузова перед покраской. Это хороший вариант для холодных зим и длительных морозов.
Достоинства
- Низкая цена;
- Эффективно оберегает от коррозии;
- Защищает на три года;
- Моментально сохнет;
- Продается в любых магазинах.
Недостатки
- Плохо изолируют от шума;
- Попадаются аэрозоли низкого качества.
Состав часто покупают в северных городах. Покупателей привлекает доступная цена и приемлемое качество товара.
Valvoline
Лучшим продуктом этой компании считается Tectyl Bodysafe. В состав этой актикоррозийки входит цинк, который выносит тяжелые условия эксплуатации. Состав средней вязкости расфасован в ведрах емкостью 1 и 5 литров. Средство легко наносится и без проблем проникает в щели. По отзывам покупателей, антикор долговечен, ему не страшны резкие перепады температуры. Также он отличается хорошими ингибирующими свойствами. Даже при длительном воздействии соли и отрицательных температур покрытие остается прочным.
Достоинства
- Качественное проникновение в микротрещины;
- Устойчивость к морозам;
- Не разрушается при воздействии соли;
- Стойкое покрытие;
- Большой выбор товаров.
Недостатки
- Высокая цена;
- Низкая шумоизоляция.
Так как у средства слабая защита от ударов камнями, рекомендуется двойная обработка днища автомобиля антикором. Для равномерного нанесения требуется тщательно высушенная поверхность.
Liqui Moly Unterboden-Schutz
Этот антикор для днища кузова популярен как в России, так и у зарубежных покупателей. Изделие от германского бренда славится хорошей адгезией и стабильными свойствами. Слой надолго остается эластичным и прочным. При этом предотвращается появление ржавчины на металле. В продаже имеется баллончик емкостью 1 л черного цвета. Несмотря на высокое качество, цена на изделие оптимальна и доступна каждому автолюбителю. Дополнительно можно приобрести спрей, позволяющий ухаживать за металлическими деталями машины.
Достоинства
- Надежные антикоррозийные свойства;
- Легко ложится на любую поверхность;
- Имеет хорошую эластичность;
- Доступная цена;
- Быстро сцепляется.
Недостатки
- Отсутствуют отталкивающие свойства.
Поверхность восприимчива к грязи и пыли, что может не понравиться. Для получения прочного слоя потребуется дважды обрабатывать днище.
Лучшие антикоррозийные средства для скрытых полостей
Как правило, антикор для скрытых полостей автомобиля изготавливается на масляной основе. Также иногда в состав добавляют парафин. Жидкая основа легко проникает в микротрещины и полностью заполняет поверхность. Такие средства отличаются длительным сроком службы, но образуемый слой менее прочен. По этой причине жидкость подходит только для внутренних поверхностей автомобиля.
ML Zinc Vanger
Составом обрабатывают двери, пороги, лонжероны и другие труднодоступные области. Жидкость хорошо проникает и выталкивает влагу. Обработка антикором защищает салон новой машины или автомобиля с пробегом. Входящий в состав цинк создает дополнительный абразивный слой. После высыхания на поверхности образуется пленка янтарного оттенка. Такое средство в баллончиках емкостью 1 л предпочитают использовать в автосалонах.
Достоинства
- Отталкивает влагу;
- Ровно ложится на поверхность;
- Создает прочный слой;
- Защищает от ржавчины;
- Предотвращает коррозию.
Недостатки
Перед обработкой баллон встряхивают, с поверхности удаляют старое антикоррозийное покрытие, грязь и пыль. Материал наносят ровным слоем пистолетом-распылителем с давлением 2-6 атм. Если нужно обработать труднодоступные места, используют специальную насадку.
Rust Stop
Антикоррозийка произведена в Канаде, где в первую очередь заботятся об экологии. Поэтому у средства отсутствует токсический неприятный запах, что ее отличает от продукции иных компаний. Гелеобразный состав представляет собой жидкий антикор для авто. Его распыляют или наносят кистью. Масса способна заполнять все микротрещины, вытеснять влагу, останавливать окисление металла. Часто ее используют для обработки сварных швов и стыков панели. Антикоррозийный материал для срытых поверхностей продается в виде баллончиков или пластиковых емкостей объемом 1 л.
Достоинства
- Приятный запах;
- Нетоксичный состав;
- Хорошая проникающая способность;
- Легко наносится;
- Экономный расход;
- Образует стойкий слой.
Недостатки
- Долго густеет;
- Требователен к чистоте.
Жидкая текстура долго высыхает, из-за чего вытекает из щелей. Несмотря на то, что производители заявляют возможность нанесения средства на ржавчину, рекомендуется подготовить поверхность к обработке. В противном случае образуется промасленная пыль, которую трудно удалить.
Normex
Антикоррозийное покрытие защищает от образования ржавчины, хорошо заполняет все микротрещины, легко растекается и отличается повышенной эластичностью. Средство продается в жестяных банках и баллончиках объемом 1 л. Для нанесения используют антигравийный пистолет со специальной насадкой для скрытых полостей. Перед применением банку тщательно встряхивают. Наносят массу при температуре 10-30 градусов в несколько подходов, пока слой не будет полностью заполнен. Поверхность сохнет в течение суток.
Достоинства
- Заполняет всю поверхность;
- Быстро наносится;
- Эластичная поверхность;
- Устраняет ржавчину;
- Проникает в микротрещины.
Недостатки
- Токсичный запах.
Во время работы необходимо пользоваться индивидуальными средствами защиты от химических веществ. Предварительно следует тщательно прочистить, обезжирить и высушить поверхность.
Dinitrol ML
Антикор шведского производства отлично справляется со своей задачей. Он прочно удерживается на поверхности, не стекает даже при повышенных температурах. Масса способна вытеснять воду и проникать в покрытые ржавчиной места. Старая коррозия полностью не удалится, но новая появиться не сможет. Если правильно нанести средство, металлическая поверхность будет надежно защищена. Состав отличается наличием сильных ингибиторов, он отлично сцепляется с поверхностью и не подтекает. Несмотря на высокую цену, многие автолюбители делают выбор в пользу этого продукта.
Достоинства
- Обладает высокой проникающей способностью;
- Крепко держится на поверхности;
- Повышенный уровень шумоподавления;
- Герметичность слоя;
- Препятствует образованию ржавчины.
Недостатки
Для надежности производители рекомендуют дополнительно напылять Dinitrol 1000. Образование более толстой и прочной пленки позволит защитить поверхность от повреждения.
Лучшие универсальные антикоррозийные средства
Составы подходят для обработки любых наружных и внутренних поверхностей. Их ассортимент мал, так как производители стараются изготавливать антикоррозийки для конкретных целей. Но покупателям нравится приобретать универсальное средство, не требующее затрат. Такие средства обычно изготавливают в России.
Oilright
Российская компания предлагает несколько составов, которые защищают от коррозии. Антикор Oilright Мовиль и Oilright Пушечное сало продается в пластиковых банках по 2 кг. Им обрабатывают пороги, корпус дверей, лонжероны и другие скрытые полости авто. Также слой временно защищает арки колес и днище кузова. Как заверяет производитель, массу допускается наносить на влажную и покрытую коррозией поверхность. Средство используют в расплавленном виде в качестве консерванта и антикоррозийного покрытия.
Достоинства
- Защищает от ржавчины;
- Имеет повышенную адгезию;
- Не смывается водой;
- Низкая цена;
- Подходит для любых поверхностной.
Недостатки
- Слабая наружная обработка.
Для покрытия днища лучше выбирать твердое Пушечное сало, а внутренние полости желательно покрывать мягким. Это позволит создать максимальную защиту и прочность слоя.
ВЭЛВ “Мовиль-5Э Экстра
Этот состав от российской компании известен еще с советских времен. Он отлично выталкивает воду благодаря олифе и маслу. Многие автолюбители по привычке выбирают отечественный антикор, так как цена на него очень низкая. Масса наносится просто, поэтому особых умений не требуется. Антикоррозийка моментально останавливает развитие ржавчины, но старую коррозию не удаляет. К сожалению, средство не способно полностью высыхать, поэтому постепенно стекает вниз. Химические реагенты быстро разрушают нанесенный состав.
Достоинства
- Обладает гидрофобными свойствами;
- Низкая цена;
- Просто наносится;
- Позволяет наносить краску;
- Останавливает развитие коррозии;
- Доступен в любом магазине.
Недостатки
- Плохо проникает;
- Стекает по стенкам.
По мнению автослесарей, стоит покупать более эффективные и долговечные составы. Крупный очаг коррозии под слоем антикора скорее всего отсыреет и отпадет.
Какое антикоррозийное средство лучше купить
Прежде чем купить антикор для автомобиля, нужно изучить требования. Любой состав должен идеально заполнять труднодоступные места и сколы, отталкивать воду, хорошо сцепляться с поверхностью. Для покрытия внутренних деталей выбирают жидкую однородную консистенцию. Днище обрабатывают эластичным и прочным слоем, который выдержит удары гравия и защитит от царапин.
- Самым лучшим антикоррозийным средством для днища можно назвать Tectyl Bodysafe от Valvoline. Двойной слой позволит усилить прочность и шумоизоляцию.
- Из антикоррозиек для скрытых полостей часто выбирают Dinitrol ML. Товар шведского производства отличают качество и хорошие проникающие способности.
- Если нужен универсальный состав, то лучше выбирать Oilright Мовиль или Oilright Пушечное сало.
Купить его можно в любом автомагазине.
Кроме этого, нужно обращать внимание на климатические особенности региона проживания, предполагаемые условия эксплуатации. Чтобы продлить срок службы автомобиля, важно вовремя обрабатывать авто защитным составом. Сделать это можно самостоятельно или в автосервисе. Мастер посоветует, какой антикор лучше и выгоднее.
Типы антикоррозионных покрытий и их применение
Введение
В этой главе рассматриваются основные типы покрытий, которые в настоящее время доступны для использования, и содержится общая информация о составе покрытий. Он предназначен для предоставления основной информации о покрытиях и не является исчерпывающим руководством по выбору антикоррозионных покрытий. Если требуется информация о конкретном продукте или покрытиях, подходящих для определенных областей, следует проконсультироваться с производителем покрытия.
Покрытия часто делятся на две большие категории:
1) продукты для применения в новостройках и;
2) продукты, подходящие для технического обслуживания и ремонта, включая как капитальный ремонт, так и обслуживание на борту (OBM).
Типы антикоррозионных покрытий, используемых для OBM, часто представляют собой однокомпонентные продукты, поскольку это позволяет избежать трудностей с измерением и смешиванием небольших количеств двухупакованных продуктов, хотя небольшие количества двухупаковочных продуктов иногда доступны от производителей красок.Ремонт, проводимый экипажем находящихся в эксплуатации судов, редко бывает успешным в долгосрочной перспективе из-за трудностей подготовки поверхностей к достаточно высоким стандартам.
Как правило, краски предназначены либо для определенных участков резервуаров и для определенных функций для достижения наилучших характеристик, либо доступны универсальные покрытия для всех областей с компромиссными характеристиками. Во всех случаях необходимо соблюдать баланс между стоимостью, производительностью и сложностью обслуживания. Например, антикоррозионные покрытия, используемые на внешней стороне жилого помещения, имеют другие требования к характеристикам, чем антикоррозионные краски, используемые в балластных танках морской воды, поскольку коррозионное напряжение, оказываемое на последние, намного выше. Балластные цистерны также намного сложнее обслуживать из-за трудностей доступа, и поэтому использование высокоэффективного (и часто более дорогого) покрытия предпочтительнее для поддержания стали в хорошем состоянии.
Напротив, трюмы навалочных судов страдают от абразивного износа из-за удара груза и повреждения захвата, что часто приводит к коррозии. Грузовые трюмы, используемые в качестве балластных танков в тяжелую погоду, могут быть особенно восприимчивыми к коррозии в местах повреждения, и для этого грузового трюма иногда используется другое покрытие.Это также относится к грузовым танкам для нефтеналивных судов с обозначением класса «Чистые продукты», где любой грузовой танк может использоваться для тяжелого погодного балласта.
Состав краски
Краска может быть описана как жидкий материал, который можно наносить или растекать по твердой поверхности, на которой он впоследствии высыхает или затвердевает с образованием сплошной клейкой пленки. Краски в основном состоят из трех основных компонентов и множества добавок, которые включены в незначительных количествах. Основные компоненты:
• Связующее (также называемое наполнителем, средой, смолой, пленкой или полимером)
• Пигмент и наполнитель
• Растворитель
Из них , только первые два образуют окончательную сухую пленку краски. Растворитель необходим только для облегчения нанесения краски и образования начальной пленки, но на практике неизбежно некоторое количество растворителя, в зависимости от уровня вентиляции.
Связующие
Связующие — это пленкообразующие компоненты краски, которые определяют основные характеристики покрытия, как физические, так и химические. Краски обычно называются по их связующему компоненту (например, эпоксидные краски, краски на основе хлорированного каучука, алкидные краски и т. Д.). Связующее образует прочную непрерывную пленку, которая отвечает за адгезию к поверхности и способствует общей стойкости покрытия к окружающей среде.Связующие, используемые при производстве красок, делятся на два класса: термореактивные и термопластические. После высыхания термореактивное покрытие будет отличаться по химическому составу от краски в банке. После отверждения на термоотверждающиеся покрытия не действуют растворители.
В случае термопластичного покрытия сухая пленка и влажная краска различаются только содержанием растворителя и химически, они остаются практически одинаковыми. Если первоначально использованный растворитель наносится на термопластичное покрытие, оно размягчается и может быть повторно растворено в этом растворителе.
Сшитые (термореактивные) покрытия
Эти покрытия обычно поставляются в двух отдельных упаковках, которые смешиваются вместе непосредственно перед нанесением. В жидких красках, где используется растворитель, сушка считается двухэтапным процессом. Обе стадии на самом деле происходят вместе, но с разной скоростью.
Этап первый: растворитель уходит из пленки при испарении, и пленка становится сухой на ощупь.
Этап 2: Пленка постепенно становится более химически сложной с помощью одного из следующих четырех методов:
1) Реакция с кислородом воздуха, известная как окисление.
2) Реакция с добавлением химического отвердителя.
3) Реакция с водой (влажность в атмосфере).
4) Искусственное отопление.
Это преобразование краски известно как высыхание или отверждение. Пленки, сформированные указанными выше способами, химически отличаются от исходных связующих и не будут повторно растворяться в исходном растворителе.
Эпоксидные смолы
Эти смолы имеют особенно важное значение, и их разработка для использования в качестве связующих была одним из наиболее значительных достижений в технологии антикоррозионных покрытий. Скорость сшивания или отверждения зависит от температуры. Ниже 5 ° C скорость отверждения стандартных эпоксидных смол значительно снижается, и для получения оптимальных свойств пленки необходимо полное отверждение. Эпоксидные смолы со специальными отвердителями затвердевают или застывают при температуре до –5 ° C. Важно строго соблюдать рекомендации производителя покрытия по температуре нанесения, чтобы покрытия были эффективными в эксплуатации.
Выбор отвердителя очень важен, так как в случае основы он определяет свойства пленки.Существует широкий выбор как смол, так и отвердителей, что позволяет создавать продукты, подходящие для большинства областей применения. Эпоксидные смолы используются как под водой, так и над водой и демонстрируют хорошую стойкость ко многим морским средам, включая катодную защиту с использованием цинка или других анодов, но они имеют тенденцию к мелу на солнечном свете. Этот процесс происходит, когда связующее разрушается ультрафиолетовым светом с образованием рыхлой и рыхлой поверхности с частицами пигмента, остающимися на поверхности.
Полиуретановые смолы
Это полимеры, образующиеся в результате реакции между гидроксильными соединениями и соединениями, содержащими изоцианаты. В двухкомпонентных системах специальная полиэфирная или полиэфирная смола со свободными гидроксильными группами реагирует с высокомолекулярным изоцианатным отвердителем. Возможная проблема с этими материалами заключается в их чувствительности к воде при хранении и применении. Транспортировка и хранение должны производиться в строгом соответствии с рекомендациями производителей.Из-за их плохих свойств отверждения при низких температурах при нанесении необходимо соблюдать рекомендации производителя.
Полиуретановые смолы обладают превосходной химической стойкостью и стойкостью к растворителям и превосходят стандартные эпоксидные смолы по кислотостойкости. Эпоксидные смолы более устойчивы к щелочам, чем полиуретаны. Полиуретановые финишные покрытия очень твердые и обладают очень хорошим блеском, сохранением блеска и могут не желтеть. Однако в некоторых случаях на них может быть трудно нанести следующий слой после старения, и для оптимальной адгезии требуются очень чистые поверхности.Изоцианатный отвердитель также представляет потенциальную опасность для здоровья при распылении, которую можно преодолеть с помощью соответствующих средств защиты.
Алкидные смолы
Алкидные смолы образуются в результате реакции между специальной органической кислотой (например, фталевой кислотой), специальным спиртом (например, глицерином или пентаэритритом) и растительным маслом или его жирными кислотами. Конечные свойства алкидных масел зависят от процентного содержания масла (называемого «маслянистость»), а также от используемых спирта и органической кислоты.Алкиды не устойчивы к кислотам или щелочам, и многие из приведенных ниже модификаций направлены на улучшение этой слабости, однако ни одна из них не обеспечивает полной устойчивости. Алкидные смолы могут быть дополнительно модифицированы различными смолами для определенных целей.
Неорганические смолы
Эти типы включают силикаты, которые почти всегда используются в сочетании с цинковой пылью. Существуют неорганические силикаты на водной основе на основе силиката лития, калия или натрия и неорганические силикаты на основе растворителей, обычно основанные на этилсиликате.Покрытия на основе этих смол очень твердые, коррозионно-стойкие и термостойкие. Они требуют хорошей подготовки поверхности и часто ремонтируются с использованием органических покрытий. Цинк в неорганических смолах может растворяться в кислотных или щелочных условиях, но покрытия хорошо работают при нейтральном pH и часто используются в качестве покрытий для резервуаров.
Термопластические покрытия
Эти типы связующих для красок представляют собой простые растворы различных смол или полимеров, растворенных в подходящем растворителе (ах), и обычно поставляются в виде одной упаковки, что делает их особенно подходящими для работ по техническому обслуживанию. Сушка происходит просто за счет потери растворителя при испарении. Это называется физической сушкой, поскольку никаких химических изменений не происходит. Таким образом, полученная пленка всегда легко растворяется в исходном растворителе и также может размягчаться при нагревании. Поскольку эти покрытия по определению требуют наличия значительных количеств растворителя, они исчезают с рынков, где регулируется содержание летучих органических соединений, особенно в США и ЕС. Общие типы связующих в этой категории включают:
Смолы хлорированного каучука
Смолы хлорированного каучука обладают хорошей кислотостойкостью и водостойкостью на хорошо подготовленных поверхностях.Их температурная чувствительность может привести к различным дефектам пленки при использовании в очень жарком климате. Кроме того, белые и бледные цвета имеют ярко выраженную тенденцию к желтизне при воздействии яркого солнечного света. Краски на основе хлорированного каучука высыхают при низких температурах и обеспечивают хорошую межслойную адгезию как в свеженанесенных, так и в старых системах, что делает их пригодными для технического обслуживания.
Виниловые смолы
Виниловые смолы основаны на пленкообразующих полимерах, состоящих из поливинилхлорида, поливинилацетата и поливинилового спирта в различных соотношениях.Используемые типы пластификаторов — трикрезилфосфат или диоктилфталат. Твердые материалы большего объема могут быть получены путем смешивания виниловой смолы с другими материалами, такими как акриловые смолы. Обычно свойства пленки и погодоустойчивые характеристики также показывают хорошие характеристики сушки при низких температурах и межслойной адгезии. Каменноугольная смола может быть добавлена для повышения водостойкости.
Пигменты и наполнители
Пигменты и наполнители используются в красках в виде тонких порошков.Они диспергированы в связующем до размеров частиц примерно 5-10 микрон для отделочных красок и примерно 50 микрон для грунтовок.
Антикоррозийные пигменты
(1) Цинк
Металлический цинк широко используется в грунтовках, придающих коррозионную стойкость стали. Первоначальная защита — гальваническое воздействие. Однако по мере того, как покрытие подвергается воздействию атмосферы, происходит прогрессирующее накопление продуктов коррозии цинка, в результате чего образуется непроницаемый барьер с небольшой гальванической защитой или без нее.Чтобы обеспечить хорошую гальваническую и барьерную защиту, требуется высокий уровень цинка, около 85% цинка в сухой пленке по весу. В качестве смол можно рассматривать эпоксидные смолы и силикаты. Очевидно, что для правильного функционирования цинк должен находиться в тесном контакте со стальной подложкой, и поэтому важна хорошая чистота поверхности перед нанесением.
(2) Алюминиевые пигменты
Металлические алюминиевые чешуйки обычно используются в качестве антикоррозийного пигмента и действуют как антикоррозийные средства, создавая обходной путь для воды и ионов вокруг пластинчатых чешуек, а также поглощая кислород для дают оксиды алюминия, которые блокируют поры в покрытии.Там, где алюминий находится в контакте со сталью, также будет действовать ограниченный механизм катодной защиты, хотя при использовании на танкерах и продуктовозах содержание алюминия в сухой пленке не должно превышать 10 процентов, чтобы избежать возможной опасности искры при скоплении горючих газов.
(3) Фосфат цинка
Это также широко используемый антикоррозийный пигмент, и считается, что при нормальных условиях воздействия защита обеспечивается барьерным эффектом, поскольку для обеспечения адекватной защиты от коррозии необходимы высокие уровни пигментации. охрана.Фосфат цинка может быть включен практически в любое связующее, и из-за его низкой непрозрачности или прозрачности можно производить краски любого цвета.
Барьерные пигменты
Наиболее распространенными типами этих пигментов являются алюминий (листовой алюминий) и слюдяной оксид железа (MIO). Оба имеют форму частиц, которые называются пластинчатыми (пластинчатыми). Эти материалы можно использовать в сочетании, при этом алюминий осветляет почти черный оттенок MIO. Пигментированные пленки MIO обладают долговечностью, но для достижения этого необходимы высокие уровни MIO, порядка 80% от общего пигмента.Алюминий уже много лет используется в качестве основного пигмента в красках. Пластинчатая форма делает пленку более водонепроницаемой. Стеклянные хлопья также используются в качестве барьерного пигмента.
Красящие пигменты
Эти пигменты обеспечивают как цвет, так и непрозрачность, и их можно разделить на неорганические и органические типы. Самый распространенный красящий пигмент — диоксид титана белого цвета. В краске все пигменты обычно диспергированы до очень мелких частиц, чтобы обеспечить максимальный цвет и непрозрачность (укрывистость).Традиционно яркие цвета получали с помощью свинцовых и хромовых пигментов. Однако из-за проблем со здоровьем и безопасностью они встречаются реже. Теперь вместо них используются органические пигменты, но непрозрачность этих продуктов не такая высокая.Extender Pigments
Как следует из названия, они в основном регулируют или «расширяют» пигментацию краски до тех пор, пока не будет достигнута требуемая объемная концентрация пигмента (PVC). Пигменты-наполнители представляют собой неорганические порошки с различными формами и размерами частиц. Хотя они вносят незначительный вклад в непрозрачность цвета краски или не вносят ее вообще, они могут иметь значительное влияние на физические свойства. К ним относятся текучесть, степень блеска, противоосадочные свойства, способность к распылению, водо- и химическая стойкость, механическая прочность, твердость и твердость (твердый объем, задерживающая тиксотропия). Смеси наполнителей часто используются для получения желаемых свойств. Они относительно недороги по сравнению со смолами, антикоррозийными пигментами и красящими пигментами.
Растворители
Растворители используются в красках в основном для облегчения нанесения. Их функция заключается в растворении связующего и снижении вязкости краски до уровня, который подходит для различных методов нанесения, таких как кисть, валик, обычное распыление, безвоздушное распыление и т. Д. После нанесения растворитель испаряется и не играет никакой роли. дальнейшая часть в финальной лакокрасочной пленке. Жидкости, используемые в качестве растворителей в красках, можно описать одним из трех способов:
(1) Настоящие растворители — жидкость, которая растворяет связующее и полностью с ним совместима.
(2) Скрытый растворитель — жидкость, которая не является настоящим растворителем. Однако при смешивании с настоящим растворителем смесь обладает более сильными растворяющими свойствами, чем один настоящий растворитель.
(3) Растворитель-разбавитель — жидкость, которая не является настоящим растворителем. Обычно используется в виде смеси с истинным растворителем / смесями скрытого растворителя для снижения стоимости.
Связующие допускают только ограниченное количество разбавителя. В лакокрасочной промышленности используется множество растворителей, отчасти это связано с рядом различных свойств, которые необходимо учитывать при выборе растворителя или смеси растворителей.Помимо коммерческих факторов, таких как цена и доступность, свойства включают токсичность, летучесть, воспламеняемость, запах, совместимость и пригодность. В некоторых странах использование некоторых типов растворителей запрещено. Это особенно верно в США, где Закон о вредных веществах, загрязняющих воздух (HAPS) определяет сроки удаления многих растворителей и наполнителей с покрытий. При реализации этого закона, скорее всего, будут затронуты свойства нанесения, время высыхания и окна перекрытия.
Антикоррозийные краски
За некоторыми исключениями (например, противообрастающие краски, косметические эффекты, антипирены и т. Д.), Большинство покрытий, наносимых на сосуд, используется для защиты от коррозии. Существует много типов антикоррозионных покрытий, но эпоксидные краски обычно покрывают большую площадь на судне, особенно когда они используются в балластных цистернах морской воды. В последние годы ведутся споры о терминологии, используемой для эпоксидных покрытий, и обычно используются следующие термины:
(1) Чистая эпоксидная смола
Чистые эпоксидные покрытия обычно рассматриваются как краски, содержащие только эпоксидные полимеры, сшивающий агент, пигменты, наполнители и растворители. Покрытия содержат большое количество эпоксидного связующего, и поэтому ожидается, что они обеспечат максимально возможные характеристики покрытия с точки зрения защиты от коррозии, длительного срока службы и низких эксплуатационных расходов. Кроме того, некоторые продукты также заявляют о стойкости к истиранию. В чистые эпоксидные покрытия можно добавлять другие пигменты, такие как алюминий, для обеспечения дополнительных антикоррозионных свойств. Эпоксидно-фенольные покрытия могут использоваться в грузовых танках, где требуется высокий уровень дополнительной устойчивости груза, например, на нефтепродуктах и химовозах.Особая осторожность требует подготовки поверхности; может потребоваться отверждение покрытия путем нагревания резервуаров. Производители покрытий сообщат конкретные требования для каждого резервуара.
(2) Модифицированная эпоксидная смола
Также известная как эпоксидная мастика, не содержащая смол эпоксидная смола и отбеленная эпоксидная смола, эта группа покрывает широкий спектр продуктов и обеспечивает антикоррозионные свойства. В эксплуатации могут быть эффективны модифицированные эпоксидные смолы. Однако, поскольку существует множество возможных модифицированных эпоксидных составов, невозможно сделать какие-либо обобщения об их антикоррозионных характеристиках.Модифицированные эпоксидные смолы могут содержать неэпоксидные материалы, которые способны образовывать поперечные связи в конечную пленку. Они также могут содержать инертные материалы, твердые или жидкие, которые не участвуют в образовании пленки, но остаются в конечном покрытии как пигменты или наполнители. Если эти материалы растворимы в воде (или грузе), они могут вымываться в течение длительного периода времени, оставляя пористую или хрупкую пленку с пониженными антикоррозийными свойствами.
(3) Каменноугольная смола эпоксидная
Каменноугольная смола является продуктом природного происхождения.Угольные гудроны доступны в широком диапазоне типов от жидких до твердых. Включение каменноугольных смол в покрытие приводит к очень темно-коричневому или черному цвету покрытия, который можно немного осветлить, добавив пигмент в виде чешуек алюминия для более светлых красок. Однако маловероятно, что эпоксидные смолы из каменноугольной смолы будут достаточно светлыми для использования в соответствии с требованиями IMO PSPC 4.4 Таблица 1, пункт 1.2 для окончательного покрытия. Светлый верхний слой эпоксидной смолы без содержания смолы может быть использован поверх первого слоя на основе смолы.Однако «просачивание» смолы может изменить цвет верхнего покрытия. Некоторые компоненты покрытия могут вымываться в течение длительного времени, в результате чего покрытие становится более хрупким и менее защищенным. Эпоксидные смолы каменноугольной смолы имеют долгую историю эксплуатации и в целом хорошо себя зарекомендовали. С 1990-х годов они были выведены из эксплуатации в балластных цистернах из-за проблем со здоровьем и безопасностью нанесения покрытий, а также из-за рекомендаций относительно светлых покрытий для облегчения инспекций балластных танков.
(4) Эпоксидная смола, не содержащая растворителей
Краски, не содержащие растворителей (иногда называемые 100% -ными твердыми частицами), как следует из названия, формулируются и наносятся без необходимости в дополнительных растворителях, тем самым преодолевая проблемы остатки растворителей в покрытии. Вязкость, необходимая для распыления краски, получается путем выбора низкомолекулярного сырья или путем нагрева и использования многокомпонентных систем. Типичные области применения включают балластные и грузовые танки. Иногда они используются там, где удаление летучих органических компонентов (ЛОС) затруднено из-за плохой вентиляции, хотя следует отметить, что ЛОС для систем без растворителей не обязательно равен нулю. Типичные области применения покрытий, не содержащих растворителей, включают внутреннюю часть трубопроводов, некоторые резервуары и другие области, где не может быть обеспечена соответствующая вентиляция, или для областей, где действуют строгие меры контроля выбросов летучих органических соединений.
Типы дефектов антикоррозионного покрытия
Введение
Антикоррозийные покрытия не вечны. Они стареют, слабеют и портятся, и в конечном итоге их полезный срок службы заканчивается. Наиболее частой причиной преждевременного выхода из строя антикоррозионного покрытия является недостаточный уход во время процессов смешивания, нанесения и отверждения.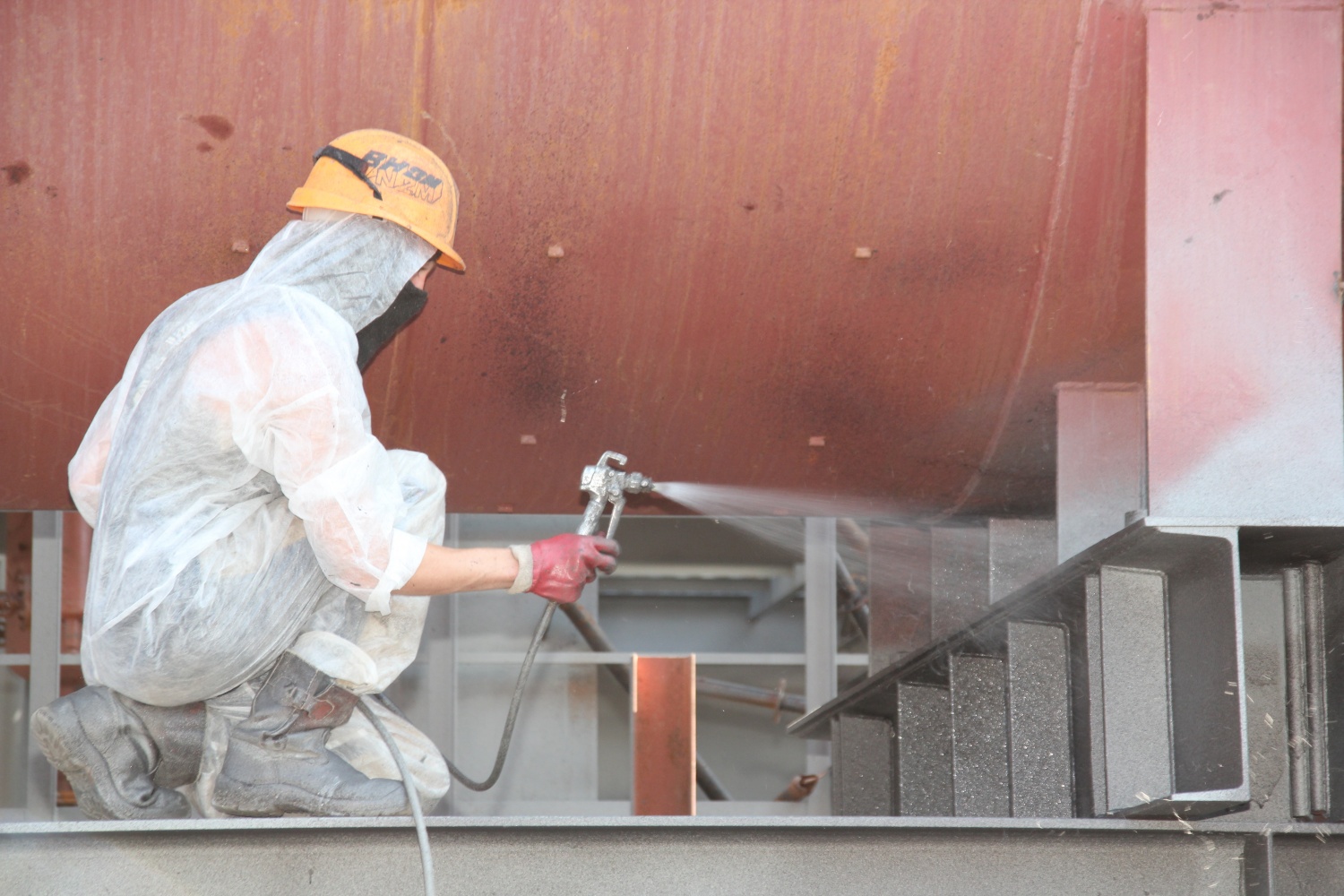
Дефекты покрытия во время нанесения
(1) Провисания
Провисания обычно возникают на вертикальных поверхностях, когда краска наносится слишком толстым слоем на локализованные области, превышающие ТСП.Они также могут быть вызваны тем, что в краску было добавлено слишком много разбавителя, если распылительное сопло удерживается слишком близко к поверхности или если оно удерживается в одном положении слишком долго.
(2) Циклы
Циклы также вызваны чрезмерным разбавлением краски или нанесением толстого слоя краски с низкой вязкостью.(3) Cissing
Это также известно как рыбий глаз. Это небольшие отверстия в антикоррозийном покрытии, которые возникают из-за захваченных пузырьков воздуха, выходящих из краски, или из-за неправильного смачивания поверхности краской.Это вызвано загрязнением поверхности, например, влагой, маслом или жиром.(4) Апельсиновая корка
Обычно поверхность покрыта рябинами и выглядит как апельсиновая корка. Это вызвано использованием неподходящих растворителей, слишком большого количества разбавителя для краски или неправильной техники распыления.(5) Растрескивание или растрескивание грязи
Этот отказ обычно происходит на горизонтальных поверхностях, когда краска была нанесена слишком густо. По мере высыхания и отверждения антикоррозионного покрытия нарастает внутреннее напряжение, вызывая образование трещин.
(6) Избыточная толщина
Избыточная толщина — это когда нанесенный слой антикоррозионного покрытия превышает максимальную толщину, указанную производителем покрытия для этого продукта. Если антикоррозионное покрытие очень толстое, оно может отслоиться от основания.(7) Меньшая толщина
Меньшая толщина — это когда нанесенный слой краски меньше минимума, указанного производителем покрытия и / или правилом 90-10 для этого антикоррозионного покрытия.(8) Избыточное распыление
Избыточное распыление или сухое распыление возникает, когда распыленное покрытие попадает на неподготовленную поверхность. Это может быть связано с влиянием таких факторов, как ветер для внешней окраски корпуса.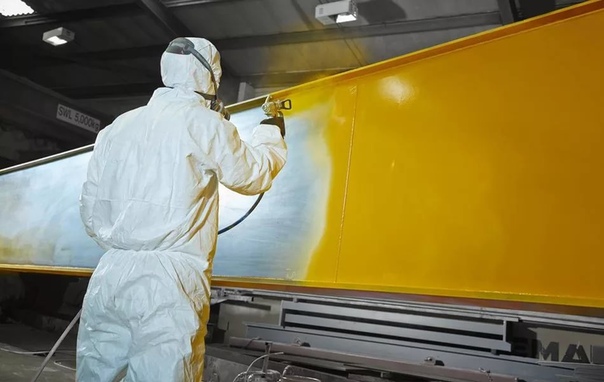
(9) Включения зерен
Зернистость может задерживаться под краской, сквозь краску или поверх нее. Если стальная поверхность не будет должным образом очищена после абразивно-струйной обработки или если пыль и песок оседают на слой краски перед нанесением следующего слоя, зернистость будет задерживаться.Стальная крупа будет корродировать, когда вода проникает сквозь краску, и антикоррозийное покрытие будет локально оттесняться от стали, когда песчинка находится под покрытием. Если между слоями антикоррозионного покрытия попадет песок, то внешний слой краски будет поврежден.
(10) Человеческая ошибка
Человеческая ошибка касается случаев, когда применяется неправильный тип краски, краска плохо перемешивается или наносится краска, срок годности которой истек.Нанесение краски в неподходящих условиях окружающей среды или во время других процессов также может быть отнесено к человеческой ошибке.(a) Плохое проникновение
Антикоррозийные покрытия должны полностью покрывать покрываемый предмет. Неправильная практика нанесения может привести к неполному покрытию. На кромках и сварных швах трудно получить хорошее и равномерное покрытие краски, а также трудно убедиться, что краска была нанесена правильной толщины.(b) Следы
Когда указанное «время ходьбы по времени» не разрешено или если условия отверждения не подходят, операторы, идущие по антикоррозийным покрытиям для проверки ТСП, могут оставлять следы на мягкой краске.
(c) Плохое смешивание
Плохое смешивание краски из-за недостаточного перемешивания или неправильного соотношения двухкомпонентной системы может привести к неравномерному или неполному отверждению антикоррозионного покрытия. Это серьезно скажется на сроке службы антикоррозионного покрытия.(d) Превышение срока жизнеспособности
Жизнеспособность антикоррозийного покрытия указывается производителем краски и зависит от типа краски и условий окружающей среды.Краска, срок жизнеспособности которой превысил срок годности, может показаться подходящей, но от нее следует отказаться, так как при эксплуатации она не дает удовлетворительного антикоррозионного покрытия.(e) Индукционный период не допускается
Для некоторых антикоррозионных покрытий требуется индукционный (выжидательный) период после смешивания перед нанесением. Это должно быть указано в паспорте производителя краски и должно соблюдаться, иначе антикоррозионное покрытие может не прилипать к основанию, удовлетворительно отверждаться или работать приемлемо в эксплуатации.
(f) Превышен срок хранения.
Все антикоррозионные покрытия должны иметь этикетку с датой «использовать до». Не следует наносить устаревшее покрытие, так как это может повлиять на свойства пленкообразования и отверждения.(g) Температура хранения слишком высокая или слишком низкая
В технических паспортах производителей покрытий указаны условия хранения красок, и их следует соблюдать. Хранение вне указанного диапазона температур может серьезно повлиять на нанесение, отверждение и характеристики краски.Коррозионно-стойкие покрытия для различных типов коррозии
Изображение предоставлено: GaViAl / Shutterstock.com
Высокопроизводительные структурные компоненты и технологическое оборудование обычно подвергаются той или иной форме коррозии независимо от того, какой тип материала используется, а коррозионно-стойкие покрытия могут увеличить срок службы детали, а также снизить затраты на техническое обслуживание и замену. Однако, чтобы выбрать подходящее покрытие, важно определить вид коррозии, которой подвержена деталь.В зависимости от того, как используется деталь и в каких условиях она подвергается, вид коррозии может отличаться.
Каковы типы коррозии металла?
Многие металлы, подвергающиеся воздействию сухого воздуха, образуют слой коррозии на своей поверхности, который может защитить лежащий под ними металл, пока воздух остается сухим. Например, алюминий быстро образует на своей поверхности пленку из оксида алюминия, которая плотно прилегает к основному металлу и препятствует дальнейшей коррозии, даже если атмосферные условия меняются.С другой стороны, железо и сталь образуют слой ржавчины в сухих условиях, но по мере увеличения влажности и температуры эта ржавчина будет продолжать формироваться в основном материале. Но железный пруток в сухом воздухе может образовывать слой защитного оксида железа, пока воздух остается сухим.
Явление электрохимической коррозии хорошо известно. Два разнородных металла, таких как медь и цинк, погруженные в воду, быстро установят электрохимическую реакцию, при которой один металл — в данном случае цинк — станет анодом и отдаст электроны другому материалу — меди.Медь в этом случае действует как катод и называется. С химической точки зрения, цинк подвергается процессу окисления, при котором атомы металла теряют один или несколько электронов и становятся ионами металлов. Между тем, поскольку два металла электрически соединяются через водяную баню, медь подвергается процессу реакции и получает ионы цинка. Это принцип, лежащий в основе гальванического элемента.
Любые два разнородных металла в контакте будут испытывать это отношение анод-катод. Чтобы определить склонность любой комбинации разнородных металлов к коррозии, используется понятие электродного потенциала.Он назначает стандартный электродный потенциал (в вольтах) каждому металлу, используя газообразный водородный электрод в качестве нулевого эталона. Ниже приведен список металлов с электродным потенциалом, показанным для двух крайних случаев (магний и золото).
Магний -2,363
Бериллий
Алюминий
Марганец
Цинк
Хром
Утюг
Кадмий
Никель
Олово
Свинец
Водород 0
Медь
Меркурий
Серебро
Палладий
Платина
Золота +1.420
Для любых двух соприкасающихся металлов тот, который находится выше в таблице, станет анодом и корродирует. Таким образом, использование жертвенных цинковых анодов для защиты корпусов судов.
Хотя химические вещества могут вызывать прямую коррозию металлов, большая часть коррозии металлов, которые удерживаются или погружены в воду, или которые подвергаются образованию влагообразующих пленок из-за атмосферного воздействия, имеет электрохимическую природу.
Существует пять основных типов коррозии: гальваническая, растрескивание под напряжением, общая, локализованная, и коррозия, вызванная едким веществом .
Гальваническая коррозия необычайно распространена и возникает, когда два металла с разными электрохимическими зарядами соединяются токопроводящей дорожкой. Коррозия возникает, когда ионы металла перемещаются от анодного металла к катодному. В этом случае будет нанесено антикоррозийное покрытие, чтобы предотвратить перенос ионов или условия, которые его вызывают. Гальваническая коррозия также может возникнуть при наличии одного загрязненного металла. Если металл содержит комбинацию сплавов с разными зарядами, один из металлов может подвергнуться коррозии.Это известно как межкристаллитная коррозия. Анодный металл является более слабым, менее стойким и уступает ионы более сильному, положительно заряженному катодному металлу. Без воздействия электрического тока металл равномерно корродирует; тогда это называется общей коррозией.
Коррозионное растрескивание под напряжением (SCC) может серьезно повредить компонент, не подлежащий ремонту. Под воздействием экстремального растягивающего напряжения металлический компонент может испытывать SCC вдоль границы зерен — образуются трещины, которые затем становятся объектами дальнейшей коррозии.Существует несколько причин SCC, включая напряжение, вызванное холодной работой, сваркой и термической обработкой. Эти факторы в сочетании с воздействием окружающей среды, которая часто увеличивает и усиливает растрескивание под напряжением, могут означать, что деталь переходит от незначительной коррозии под напряжением к отказу или непоправимому повреждению. В латуни разрушение из-за коррозионного растрескивания под напряжением называют «сезонным растрескиванием»; в стали это известно как «едкое охрупчивание». Водородное охрупчивание стали также считается явлением коррозии.
Общая коррозия возникает в результате ржавчины. Когда металл, особенно сталь, подвергается воздействию воды, поверхность окисляется и появляется тонкий слой ржавчины. Как и гальваническая коррозия, общая коррозия также является электрохимической. Чтобы предотвратить окисление, защитное покрытие должно препятствовать реакции.
Локальная коррозия возникает, когда небольшая часть компонента подвергается коррозии или контактирует с определенными вызывающими коррозию напряжениями.Поскольку небольшая «локальная» область корродирует гораздо быстрее, чем остальная часть компонента, а коррозия действует параллельно с другими процессами, такими как напряжение и усталость, конечный результат намного хуже, чем результат одного напряжения или усталости.
Коррозия, вызванная едким веществом возникает, когда загрязненный газ, жидкости или твердые частицы изнашивают материал. Хотя большинство нечистых газов не повреждают металл в сухом виде, при воздействии влаги они растворяются с образованием вредных коррозионных капель.Сероводород является примером одного такого едкого агента.
Коррозионно-стойкие покрытия
Коррозионно-стойкие покрытия для металла различаются в зависимости от типа металла и типа необходимой защиты от коррозии. Чтобы предотвратить гальваническую коррозию в сплавах железа и стали, полезны покрытия из цинка и алюминия. Крупные компоненты, такие как мосты и энергетические ветряные мельницы, часто обрабатываются антикоррозийными покрытиями из цинка и алюминия, поскольку они обеспечивают надежную долгосрочную защиту от коррозии.Крепежные детали из стали и железа, резьбовые соединения и болты часто покрываются тонким слоем кадмия, который помогает блокировать поглощение водорода, что может привести к растрескиванию под напряжением.
Помимо покрытий из кадмия, цинка и алюминия, в качестве коррозионных покрытий часто используются никель-хромовые и кобальто-хромовые покрытия из-за их низкой пористости. Они чрезвычайно влагостойкие и, следовательно, препятствуют развитию ржавчины и возможному разрушению металла. Оксидная керамика и смеси металлокерамики являются примерами покрытий, которые обладают высокой износостойкостью, помимо устойчивости к коррозии.
Цинкование (гальваника) стали — это расходный анод. Цинк разъедает и защищает сталь, на которую он нанесен. Толщина покрытия определяет срок службы стальной детали. Аналогично, расходуемые аноды могут быть размещены на конструкциях для защиты металла. Вместо стали «горит» анод. Для таких конструкций, как трубопроводы, которые слишком велики для защиты с помощью расходуемых анодов, для защиты от коррозии используется так называемый наведенный ток.Здесь отрицательная сторона источника питания постоянного тока подключена к конструкции, а положительная клемма подключена к электродам, которые вставлены рядом со структурой.
Анодирование — это еще один метод покрытия, используемый для предотвращения коррозии, особенно алюминия. В результате оксид алюминия наносится на поверхность более толстым слоем, чем это происходит в естественных условиях.
Стойкость стали к атмосферной коррозии можно улучшить, добавив примерно 0,20% меди. Однако высокопрочные низколегированные (HLSA) стали обладают еще большей стойкостью.
Многие металлы по своей природе устойчивы к коррозионным агентам: сталь устойчива к концентрированной серной кислоте; нержавеющая сталь устойчива к азотной кислоте; олово устойчиво к дистиллированной воде и т. д.
Покрытия, содержащие хроматы и фосфаты, являются эффективными ингибиторами коррозии. Также для защиты от коррозии используются многочисленные покрытия на основе полимеров.
Сводка
В этой статье представлено краткое обсуждение коррозионных и антикоррозионных покрытий. Для получения дополнительной информации о связанных продуктах или процессах обратитесь к другим нашим руководствам или посетите платформу Thomas Supplier Discovery Platform, чтобы найти потенциальные источники поставок или просмотреть подробную информацию о конкретных продуктах.
Прочие изделия из покрытий
Прочие «виды» статей
Больше от Chemicals
Антикоррозионные краски и покрытия | Корпорация NEI
NANOMYTE ® Верхние покрытия
NANOMYTE® TC-1001 »
Самовосстанавливающееся полимерное покрытие для металлов
Самовосстанавливающееся прозрачное покрытие на основе растворителей для стали и алюминия, которое обеспечивает легкий ремонт царапин.
NANOMYTE® TC-3001 »
Расширенная защита металла в чрезвычайно агрессивных условиях
Покрытие на основе растворителей для стали и алюминия с проникающей формулой, которая инкапсулирует металл при нанесении непосредственно на поверхность, устраняя необходимость в пескоструйной очистке.
NANOMYTE® TC-4001 »
Нанокомпозитное барьерное покрытие для превосходной защиты от коррозии
Тонкое твердое барьерное покрытие на основе растворителей для стали и алюминия, которое сцепляется с голыми, предварительно обработанными или окрашенными металлическими поверхностями и обеспечивает превосходную защиту от коррозии.
НАНОМИТ® ТС-4001-УВП »
Нанокомпозитное барьерное покрытие с УФ-защитой
TC-4001-UVP — однокомпонентный состав, разработанный для защиты металлов и других поверхностей от разрушения, сохраняя их структурную целостность и внешний вид.Твердое, прочное покрытие наносится непосредственно на поверхность, образуя плотный барьер, предотвращающий проникновение влаги и коррозию. TC-4001 прочно приклеивается к голому, предварительно обработанному и окрашенному металлу, а также к другим поверхностям, таким как пластмассы и композиты. Покрытие легко наносится погружением, распылением или кистью толщиной от микрон до мил.
Подробнее: UVP Technology ♦ UVP Tech Brief
NANOMYTE® TC-5001 »
Антикоррозийное покрытие для оцинкованной и оцинкованной стали
Тонкое твердое барьерное покрытие на основе растворителей, которое сцепляется с оцинкованной или оцинкованной сталью, с высокой укрывистостью и отличными циклическими характеристиками.
НАНОМИТ® ТС-5001-УВП »
Антикоррозийное покрытие для оцинкованной и оцинкованной стали с УФ-защитой
TC-5001-UVP — однокомпонентный состав, разработанный для защиты оцинкованной и оцинкованной стали от коррозии и разрушения. Продукт представляет собой твердое, плотное нанокомпозитное покрытие, обеспечивающее барьерную защиту поверхности сплава. Покрытие устойчиво к царапинам и сколам, прочно прилегает к основанию. Состав обладает повышенной атмосферостойкостью и разработан с учетом требований клиентов к толщине пленки и условиям отверждения.
Подробнее: UVP Technology ♦ UVP Tech Brief
Меры предосторожности при нанесении антикоррозионного покрытия
Антикоррозийное покрытие широко используется в металлургической промышленности, например, в архитектуре, мебели, автомобилестроении, кораблях и самолетах и т. Д. Это важный процесс для защиты поверхностей в различных рабочих условиях. Существует множество антикоррозионных покрытий для различного применения, обычно доступных в виде однокомпонентных и двухкомпонентных покрытий. В этой статье мы в общих чертах познакомимся с техническим процессом и мерами предосторожности при нанесении.
На что следует обратить внимание при распылении однокомпонентного покрытия?
Использование однокомпонентных покрытий относительно просто, таких как алкидные краски, краски на основе хлорированного каучука, акриловые краски и тому подобное. Однокомпонентные покрытия можно использовать и после открытия ствола. Минимальное требование — перемешивание. Под грунтовкой могут выпадать в осадок антикоррозионные пигменты и наполнители, которые отделяются от смолы. Для финишных покрытий цвет может не распускаться. Равномерно. Путем механического перемешивания смола, пигмент и наполнитель могут быть равномерно смешаны, и цветовой тон верхнего покрытия может быть более однородным.
Покрытие на основе растворителя, такое как антикоррозийная краска на масляной основе, алкидная краска, фенольная краска и т. Д. Самый важный принцип для этих покрытий — не распылять слишком густо. Если необходимая толщина лакокрасочного покрытия большая, его можно наносить несколько раз. На самом деле, эти покрытия могут достичь наилучших результатов только после нескольких построек. Это потому, что после нанесения они вступают в реакцию с кислородом воздуха. Если пленка краски слишком толстая, а поверхностный слой сухой, кислород не может проникнуть глубоко внутрь, что приведет к недостаточному отверждению внутреннего покрытия и ухудшит его долговечность и твердость. Наиболее очевидными дефектами покрытий являются складки, трещины и т.п.
Еще одним конструктивным свойством масляного покрытия является то, что его конструкционные характеристики довольно хороши, поскольку оно имеет лучшую смазывающую способность, чем другие покрытия, что позволяет использовать метод нанесения кистью. Покрытия на основе растворителей хорошо проникают в поверхность и могут полностью смачивать поверхность. Самая большая особенность покрытий из хлорированного каучука и акриловых покрытий в том, что они быстро сохнут. Из-за термопластичных покрытий покрытие становится мягким при температуре выше 40 ° C.Во время строительства это, конечно, не проблема. Проблема в том, что если в воздухе есть грязный плавающий осадок, он приведет к загрязнению поверхности покрытия и его будет нелегко удалить.
На что следует обращать внимание при нанесении двухкомпонентной краски?
Эпоксидные и полиуретановые покрытия — это наиболее часто используемые двухкомпонентные покрытия, наиболее важным из которых является смешивание красок. Эти два компонента обычно делятся на основной материал и отвердитель, и после смешивания происходит химическая реакция с образованием пленки покрытия с соответствующими характеристиками.Если он плохо перемешан, химической реакции будет недостаточно для гарантированной работы.
Двухкомпонентные покрытия необходимо тщательно перемешать и перемешать механическим перемешиванием. Помните, что для перемешивания покрытия нельзя использовать деревянную палочку. Многие отвердители бесцветны и прозрачны, поэтому трудно сказать, хорошо ли отвердитель смешан с основой. В этом случае особенно важно использование электроинструментов. Чтобы решить эту проблему, некоторые продукты для покрытий разработаны как цветные отвердители, поэтому они исчезают после равномерного смешивания.Если при выполнении небольших работ по удалению выступов, таких как ремонт или предварительное покрытие, краска не заканчивается за один раз, оставшуюся краску необходимо загерметизировать. Если основной компонент не загерметизирован, растворитель вытечет, а примеси попадут внутрь; если группа отвердителя плохо запечатана, это повлияет на ее характеристики.
Почему краску в барабане нельзя размешивать деревянной палочкой?
Двухкомпонентные покрытия, такие как эпоксидные покрытия и полиуретановые покрытия, обычно упаковываются в компонент A (основа) и компонент B (отвердитель).Эти два компонента упакованы в определенном соотношении. Для компонента основы А перед смешиванием необходимо хорошее механическое перемешивание. Некоторые строители для удобства перемешивают деревянными палочками, а не механически. Из-за высокого уровня твердых частиц в современных покрытиях некоторые из них составляют до 80%, в то время как другие покрытия не содержат растворителей. Если тело человека перемешать одной деревянной палочкой, невозможно равномерно смешать два компонента, что может привести к недостаточному отверждению, а также к снижению химической стойкости и водостойкости пленки покрытия.
Что такое время созревания или время загрузки при нанесении двухкомпонентной краски?
Продукт эпоксидной смолы также предусматривает, что индуктивное время после смешивания иногда переводится во время выполнения заказа. На этот раз перед постройкой необходимо провести химическую реакцию двух компонентов, прежде чем они смогут быть сконструированы для достижения оптимальных характеристик. Температура влияет на время отверждения. Чем выше температура, тем короче время отверждения. Покрытие на основе поли-отвержденной эпоксидной смолы со временем отверждения 15-30 минут (23 ℃).
На что следует обратить внимание при использовании акрилово-полиуретанового верхнего покрытия во время строительства?
Акрилово-полиуретановое верхнее покрытие является лучшим выбором для современных покрытий для тяжелых условий эксплуатации и широко используется. По сравнению с другими двухкомпонентными верхними покрытиями, у него есть свои особые требования к конструкции.
В качестве изоцианатного компонента отвердителя он очень чувствителен к влаге. Крышку необходимо закрыть и хранить в сухом месте. В противном случае это приведет к попаданию влаги и ухудшению качества.В частности, при нанесении небольшого количества краски обратите на это внимание при использовании разных цветов. Следует отметить, что в атмосфере, содержащей серу и хлор, некоторые бессвинцовые красные и желтые цвета легко обесцвечиваются. При температуре выше 100 градусов Цельсия пленка краски будет слегка обесцвечиваться, особенно белая. Для длительного сохранения цвета не используйте температуру выше 80 ° C. Обычное воздушное распыление улучшает блеск и внешний вид. При использовании безвоздушного распыления рекомендуется добавлять 5-15% разбавителя для обеспечения образования пленки, а иногда может потребоваться добавить 20%.Сначала нанесите слой тумана, а через 2-15 минут нанесите его на всю пленку краски, чтобы добиться наилучшего образования пленки.
Относительная влажность во время строительства ограничена до 85%, но, чтобы избежать потери света, лучше контролировать в пределах 80%, температура конструкции может быть от -5% до -10% ° C. Но при температуре ниже 5 ° C для получения твердой сухой пленки требуется более длительное время отверждения. Верхние покрытия из модифицированного акрилом полиуретана не так быстро, как верхние покрытия из модифицированного полиэфиром, создают твердую пленку краски, которая выглядит мягкой и термопластичной. Если необходимо проверить адгезию, она может быть не идеальной, но в последующие недели она может полностью затвердеть в течение 30 дней. Поскольку изоцианатный компонент очень чувствителен к влаге, помимо контроля относительной влажности во время строительства также необходимо прогнозировать погоду. Например, конденсация или дождь могут произойти не скоро, или пленка краски может потерять свет или даже вспениться.
Более важной особенностью акрилово-полиуретанового верхнего покрытия является то, что он не имеет максимального интервала перекрытия при перекрытии.Благодаря относительно низкой степени сшивки акрилата, на него можно хорошо наносить покрытие даже после длительного периода старения. Сфокусируйся на. Конечно, эта адгезия вряд ли достигнет прочности при повторном покрытии через 24 часа.
Что делать, если двухкомпонентное покрытие наносится на металлическую поверхность без добавления отвердителя?
Двухкомпонентные покрытия, такие как эпоксидные покрытия, полиуретановые покрытия и т. Д., Иногда из-за ошибки рабочего, распыляемые на поверхность без добавления отвердителя, что следует делать?
Некоторые люди думают, что добавление одного или двух разбавленных отвердителей для покрытия нормально отрегулированного покрытия может в основном решить эту проблему, а также определить соотношение разбавителя к отвердителю и процедуру распыления.По сути, это способ обмануть себя и других. Невозможно полностью проникнуть внутрь покрытия для добавления отвердителя, не говоря уже о равномерном проникновении, а затем и полном отверждении. Следовательно, после распыления двухкомпонентного покрытия без отвердителя единственный возможный метод — удалить неотвержденное покрытие и затем распылить двухкомпонентное покрытие, смешанное с нормальным действием.
Можно ли отполировать покрытие из неорганического силиката цинка до поверхности ST3?
При нанесении покрытий из неорганического силиката цинка частичный ремонт неизбежен.По общему способу ремонта местно полируется до марки СТ3, а затем краска наносится кистью или распылителем. Однако покрытия из неорганического силиката цинка не подходят для ремонта полированных поверхностей. Опыт показал, что у таких покрытий плохая адгезия, и вскоре они снова станут ржавчиной. Поэтому ремонт неорганического силиката цинка предпочтительно проводить пескоструйной очисткой до достижения Sa2,5, имеет определенную шероховатость и не подходит для окраски полированной поверхности.(Тщательный ручной и электроинструмент ST2 для удаления ржавчины без наблюдения, на поверхности не должно быть видимых следов жира и грязи, и почти не должно быть прилипания к окалине, ржавчине, остаткам лакокрасочного покрытия.) (St3 Очень тщательный ручной и электроинструмент. ржавые с St2, но обработка поверхности намного тщательнее, поверхность должна иметь блеск металлической основы) (на поверхности не должно быть видимых следов жира и грязи при просмотре без увеличения, а также без окалины, ржавчины, лакокрасочного покрытия и инородное вещество.Любые следы остатков должны быть только пятнами или полосами с небольшим пятном.
)
В многослойных системах на основе неорганической цинксиликатной краски часто необходимо частично отшлифовать или обработать пескоструйным аппаратом, а затем отремонтировать грунтовку. Лучше избегать использования неорганического силиката цинка в качестве ремонтной грунтовки. Поскольку при распылении он естественным образом распыляется на окружающее органическое покрытие, это вызывает проблемы с адгезией. Решением является использование цинкового материала с высоким содержанием эпоксидной смолы. Типичная схема подбора: грунтовка из неорганического силиката цинка 80 мкм.эпоксидная герметизирующая краска 30 мкм. густая паста эпоксидная краска с облаком железа промежуточная краска 100 мкм. акрилово-полиуретановое финишное покрытие 60 мкм. Обработка стальной поверхности после строительства этой системы покрытия, в связи с окончанием периода Разрушение и местная ржавчина, или в будущем структурном обслуживании, если не вся пескоструйная очистка до Sa2,5, а только частичная струйная очистка или частичная шлифовка до уровня Sa3 , то обслуживание на этот раз не может использовать оригинальную систему Неорганическая цинкосиликатная грунтовка, в этом случае использование эпоксидной цинкосодержащей грунтовки является лучшим выбором, нет необходимости использовать герметик,
Таким образом, схема установки следующая:
- Эпоксидная грунтовка с высоким содержанием цинка 80 мкм
- Высокослойная эпоксидная промежуточная краска железо-железо> 120 мкм
- Акрилово-полиуретановое верхнее покрытие 60 мкм
Каковы требования к смешиванию и перемешиванию покрытий из неорганического силиката цинка?
Покрытия из неорганического силиката цинка обычно представляют собой две упаковки порошка цинка и жидких компонентов. При перемешивании порошок цинка медленно добавляют к жидкому компоненту и одновременно перемешивают. Не выполняйте обратную операцию, добавление жидкого компонента к цинковому порошку может легко привести к агломерации и не может быть перемешано равномерно. После смешивания и равномерного перемешивания его фильтровали через фильтр 60-80 меш и использовали. Во время распыления продолжайте помешивать, чтобы предотвратить осаждение цинкового порошка. После смешивания его необходимо израсходовать в течение определенного периода времени. Это время называется временем после смешивания.Если это время превышает это время, поскольку вязкость неорганического силиката цинка изменяется очень медленно, краску нельзя использовать, даже если она не менялась, иначе это приведет к образованию пленки. Растрескивание.
Каковы требования к способу строительства неорганического цинкосиликатного покрытия?
Для создания неорганического силиката цинка можно использовать как воздушное, так и безвоздушное распыление. Валиковое покрытие не подходит, а нанесение кистью используется только для ремонта небольших участков. Строительная скорость воздушного напыления низкая.Следует отметить, что многие строители используют инструменты для распыления воздуха всасывающим типом, которые не подходят для распыления неорганических цинксиликатных грунтовок. Он большой, и его нелегко достичь указанной толщины сухой пленки. Рекомендуемое оборудование для распыления воздуха — это напорный бак. Напорный бак вмещает 20 л краски. Сжатый воздух используется для вытеснения краски из дула. Распылитель этого типа оборудования можно свободно и гибко распылять, потому что он не ограничен окрашенным маленьким горшком, а количество красочного тумана невелико, а время покраски не требуется часто добавлять, что сокращает конструкцию время.
Если используется безвоздушное распыление, необходимо отметить, что давление распыления не должно быть слишком большим, а контроль должен быть в пределах 110 = 150 кгс / см2 (в зависимости от материала и вязкости), в противном случае распыление будет чрезмерным из-за к чрезмерному давлению, сухому распылению и т. д.
Как судить об отверждении пленки неорганического силиката цинка?
Отверждение покрытий из неорганического силиката цинка зависит от относительной влажности и температуры. Обычные покрытия из неорганического силиката цинка требуют около 24-72 часов для отверждения при 20 ° C и относительной влажности 65-75%, а время отверждения после корректировки составляет 16-24 часа, поэтому время отверждения продуктов варьируется от производителя к производителю. .Обратите внимание на описание товара при строительстве. В условиях низкой температуры и низкой влажности время отверждения лакокрасочной пленки будет увеличено, относительная влажность должна поддерживаться выше 65%, а самая низкая температура может достигать -10 ° C. Распыление воды может решить проблему отверждения при низкой влажности. После завершения строительства 2-4H можно распылить чистую воду, чтобы поверхность краски оставалась влажной и способствовала отверждению.
Метод обнаружения неорганической цинкосиликатной пленки отверждения пленки — это метод испытания MEK.Согласно Astm4752, белую хлопчатобумажную ткань натирают реагентом MEK и протирают взад и вперед 50 раз. Если изменение цвета серьезное, это означает, что отверждение не завершено.
Насколько контролируется пленка из неорганического силиката цинка при распылении? Какие советы по опрыскиванию?
Толщина пленки неорганического цинкосиликатного покрытия обычно составляет 60-80 мкм в многослойной усиленной антикоррозийной системе в Китае в качестве грунтовки. Чрезмерная толщина сухой пленки может вызвать растрескивание лакокрасочной пленки, и обычно считается безопасным значение 150 мкм или меньше.Растрескивание пленки краски происходит только из-за усадки пленки краски во время высыхания и затвердевания, и это также называется грязевой трещиной из-за потрескавшейся формы, такой как илистая земля, которая высыхает и трескается под палящим солнцем. Причины появления трещин следующие:
- пленка краски слишком толстая;
- шероховатость поверхности слишком низкая, особенно на сварном шве, из-за высокой твердости пескоструйная обработка также затруднена, что приводит к недостаточной шероховатости;
- относительная влажность При слишком высокой вентиляции поверхностный слой затвердевает слишком быстро, что также приводит к растрескиванию пленки.
- Состав краски неоднороден из-за осаждения цинкового порошка. В реальной конструкции проблемы с растрескиванием легко возникают на углах конструкции. Когда для достижения минимальных требований к пленке маляр сделает еще несколько снимков в углу, что приведет к слишком толстой пленке и неравномерной усадке пленки в углу, легко образовать грязевую трещину. Для сложных конструкций часто используются маленькие форсунки, что, в свою очередь, вызывает распыление нескольких выстрелов, что может усугубить проблемы.Поэтому распыляйте на внутренний угол, вы можете использовать большое сопло, распыляйте до двух раз, не распыляйте конструкцию.
Какую краску можно наносить непосредственно на оцинкованную сталь?
На оцинкованные детали можно нанести множество покрытий, и иногда этот выбор зависит от метода обработки поверхности. Однако некоторые покрытия нельзя использовать для оцинкованных деталей, особенно масляные алкидные краски. Существует много видов эпоксидных красок, их необходимо использовать исключительно для оцинкованных деталей, обычно с полиамидно-эпоксидными покрытиями.Эпоксидные покрытия будут распыляться на солнце, поэтому верхние покрытия следует покрывать алифатическим полиуретановым верхним слоем, который хорошо выглядит и устойчив к химическим веществам.
Акриловые покрытия на водной основе быстро сохнут, являются хорошими финишными покрытиями и легко наносятся. Однако латексные краски на водной основе быстро сохнут, но для полного высыхания требуется 2-4 недели. Следовательно, при первоначальном строительстве конструкции могут возникнуть повреждения при манипулировании. Хлорированный каучук и виниловые покрытия использовались в оцинкованных деталях в прошлом, но Закон об охране окружающей среды содержит положения о ЛОС, которые ограничивают их использование.Поверхность оцинкованных деталей после пескоструйной обработки и фосфатирования грунтовками имеет хорошую адгезию.
Акриловую краску можно наносить непосредственно на поверхность оцинкованных деталей, конечно, лучше иметь низкую фосфатирующую лакокрасочную основу. Некоторые акриловые краски содержат аммиак, и при высоком значении HP покрытие отслаивается. Если оцинкованная деталь находится под землей, ее обычно можно покрыть эпоксидным асфальтом или покрытием из чистого кислорода, и лучше всего нанести его на поверхность пескоструйной или фосфатирующей грунтовки.Эпоксидные краски с высоким содержанием цинка обычно можно наносить непосредственно на поверхность оцинкованных деталей, но не все эпоксидные краски с высоким содержанием цинка доступны. Пожалуйста, проверьте описание продукта покрытия поставщика. Если для обработки поверхности используется пескоструйная очистка, ее необходимо окрасить в течение 24 часов, поскольку свежий слой цинка начинает окисляться. Сначала нанесение слоя фосфатирующей грунтовки или очистителя на основе акриловой кислоты дает нам достаточно времени для нанесения.
В описании указан срок годности или время смешанного использования?
В инструкции по эксплуатации, особенно для двухкомпонентного покрытия, дается понятие срока службы наполнения, которое относится к времени, в течение которого двухкомпонентное покрытие может быть использовано после смешивания.