ΠΠ°ΡΠΈΡΠ½ΡΠΉ ΡΠ»ΠΎΠΉ Π±Π΅ΡΠΎΠ½Π° Π΄Π»Ρ Π°ΡΠΌΠ°ΡΡΡΡ Π² ΡΡΠ½Π΄Π°ΠΌΠ΅Π½ΡΠ΅
Π‘ΠΎΠ΄Π΅ΡΠΆΠ°Π½ΠΈΠ΅- ΠΠ°Π·Π½Π°ΡΠ΅Π½ΠΈΠ΅ ΠΏΡΠ΅Π΄ΠΎΡ ΡΠ°Π½ΠΈΡΠ΅Π»ΡΠ½ΠΎΠ³ΠΎ ΡΠ»ΠΎΡ
- Π§ΡΠΎ Π²Π»ΠΈΡΠ΅Ρ Π½Π° ΡΠ°Π·ΠΌΠ΅Ρ Π±Π΅ΡΠΎΠ½Π½ΠΎΠΉ ΠΏΡΠΎΡΠ»ΠΎΠΉΠΊΠΈ
- Π’ΠΎΠ»ΡΠΈΠ½Π° ΠΏΠ»Π°ΡΡΠ° Π±Π΅ΡΠΎΠ½Π° Π΄Π»Ρ ΡΠ°Π·Π»ΠΈΡΠ½ΡΡ ΡΠ»ΡΡΠ°Π΅Π²
- ΠΡΠΎΠ±Π΅Π½Π½ΠΎΡΡΠΈ ΡΠ΅ΠΊΠΎΠ½ΡΡΡΡΠΊΡΠΈΠΈ ΠΏΡΠΎΡΠ»ΠΎΠΉΠΊΠΈ
- ΠΠΎΡΠΌΠ°ΡΠΈΠ²Π½ΡΠ΅ ΡΡΠ΅Π±ΠΎΠ²Π°Π½ΠΈΡ
ΠΠ°ΡΠΈΡΠ½ΡΠΉ ΡΠ»ΠΎΠΉ Π±Π΅ΡΠΎΠ½Π° β ΠΎΠ΄Π½Π° ΠΈΠ· Π²Π°ΠΆΠ½ΡΡ Π²Π΅Π»ΠΈΡΠΈΠ½, ΠΏΡΠΎΠΏΠΈΡΠ°Π½Π½ΡΡ Π² ΡΡΡΠΎΠΈΡΠ΅Π»ΡΠ½ΡΡ Π½ΠΎΡΠΌΠ°Ρ . ΠΠΎ ΡΡΡΠΈ ΠΎΠ½ ΡΠ²Π»ΡΠ΅ΡΡΡ ΠΏΠ»Π°ΡΡΠΎΠΌ ΡΠ°ΡΡΠ²ΠΎΡΠ°, Π½Π°ΡΠΈΠ½Π°ΡΡΠΈΠΌΡΡ Ρ Π³ΡΠ°Π½ΠΈ ΠΊΠΎΠ½ΡΡΡΡΠΊΡΠΈΠΈ ΠΈ Π΄ΠΎΡ ΠΎΠ΄ΡΡΠΈΠΌ Π΄ΠΎ Π°ΡΠΌΠ°ΡΡΡΠ½ΠΎΠ³ΠΎ ΠΏΡΡΡΠΊΠ°.
ΠΠ°Π·Π½Π°ΡΠ΅Π½ΠΈΠ΅ ΠΏΡΠ΅Π΄ΠΎΡ ΡΠ°Π½ΠΈΡΠ΅Π»ΡΠ½ΠΎΠ³ΠΎ ΡΠ»ΠΎΡ
Π’ΠΎΡΠ½ΠΎ Π²ΡΠ΄Π΅ΡΠΆΠ°Π½Π½Π°Ρ ΡΠΎΠ»ΡΠΈΠ½Π° ΠΏΡΠΎΡΠ»ΠΎΠΉΠΊΠΈ ΠΎΠ±Π΅ΡΠΏΠ΅ΡΠΈΠ²Π°Π΅Ρ Π΄ΠΎΠ»Π³ΠΎΠ²Π΅ΡΠ½ΠΎΡΡΡ ΠΈ Π½Π°Π΄Π΅ΠΆΠ½ΠΎΡΡΡ ΡΡΡΠΎΠ΅Π½ΠΈΡ. ΠΠ½Π° ΡΠ°ΡΡΡΠΈΡΠ°Π½Π° ΡΠ°ΠΊ, ΡΡΠΎΠ±Ρ:
- ΠΈΡΠΊΠ»ΡΡΠΈΡΡ Π²Π»ΠΈΡΠ½ΠΈΠ΅ Π½Π° Π°ΡΠΌΠ°ΡΡΡΡ Π²Π»Π°Π³ΠΈ, Π°Π³ΡΠ΅ΡΡΠΈΠ²Π½ΡΡ ΡΡΠ΅Π΄ ΠΈ ΡΠ±Π΅ΡΠ΅ΡΡ ΠΎΡ ΠΊΠΎΡΡΠΎΠ·ΠΈΠΉΠ½ΡΡ ΠΈΠ·ΠΌΠ΅Π½Π΅Π½ΠΈΠΉ ΠΈ ΡΠ°Π·ΡΡΡΠ΅Π½ΠΈΡ;
- Π³Π°ΡΠ°Π½ΡΠΈΡΠΎΠ²Π°ΡΡ Π²Π΅ΡΠ½ΡΡ ΡΠΎΠ²ΠΌΠ΅ΡΡΠ½ΡΡ ΡΠ°Π±ΠΎΡΡ ΡΠΎΡΡΠ°Π²Π»ΡΡΡΠΈΡ ΠΆΠ΅Π»Π΅Π·ΠΎΠ±Π΅ΡΠΎΠ½Π°. ΠΠΎΠ·Π½ΠΈΠΊΡΠ΅Π΅ Π² ΠΊΠΎΠ½ΡΡΡΡΠΊΡΠΈΠΈ Π½Π°ΠΏΡΡΠΆΠ΅Π½ΠΈΠ΅ ΠΎΡ Π½Π°Π³ΡΡΠ·ΠΊΠΈ Π±Π΅ΡΠΎΠ½ Π±ΡΠ΄Π΅Ρ ΠΏΠ΅ΡΠ΅Π΄Π°Π²Π°ΡΡ ΠΌΠ΅ΡΠ°Π»Π»ΠΈΡΠ΅ΡΠΊΠΎΠΌΡ ΡΡΠ΅ΡΠΆΠ½Ρ Π±Π΅Π· ΠΏΠΎΡΠ΅ΡΠΈ ΡΠ½Π΅ΡΠ³ΠΈΠΈ;
- ΡΠ²Π΅Π»ΠΈΡΠΈΡΡ ΠΎΠ³Π½Π΅ΡΡΠΎΠΉΠΊΠΎΡΡΡ ΡΡΡΠΎΠ΅Π½ΠΈΠΉ ΠΈΠ· ΠΆΠ΅Π»Π΅Π·ΠΎΠ±Π΅ΡΠΎΠ½Π°;
- ΠΎΠ±Π΅ΡΠΏΠ΅ΡΠΈΡΡ Π°Π½ΠΊΠ΅ΡΠΎΠ²ΠΊΡ ΠΏΡΡΡΠΊΠΎΠ² Π² Π±Π΅ΡΠΎΠ½Π΅ Ρ Π²ΠΎΠ·ΠΌΠΎΠΆΠ½ΠΎΡΡΡΡ ΡΠΎΠ·Π΄Π°Π½ΠΈΡ ΡΡΡΠΊΠΎΠ² ΠΈ Π²ΡΠ²ΠΎΠ΄ΠΎΠ² Π½Π° Π΄ΡΡΠ³ΠΈΠ΅ ΡΡΠΎΠ²Π½ΠΈ.
Π§ΡΠΎ Π²Π»ΠΈΡΠ΅Ρ Π½Π° ΡΠ°Π·ΠΌΠ΅Ρ Π±Π΅ΡΠΎΠ½Π½ΠΎΠΉ ΠΏΡΠΎΡΠ»ΠΎΠΉΠΊΠΈ
ΠΠ΅ΠΏΠΎΠ΄Π²ΠΈΠΆΠ½ΠΎΠ΅, Π΄ΠΎΠ±ΡΠΎΡΠ½ΠΎΠ΅ ΠΈ ΡΠΎΡΠ½ΠΎΠ΅ ΡΠΎΠ΅Π΄ΠΈΠ½Π΅Π½ΠΈΠ΅ ΡΠ°ΡΡΠ²ΠΎΡΠ° ΠΈ Π°ΡΠΌΠ°ΡΡΡΠ½ΡΡ ΡΡΠ΅ΡΠΆΠ½Π΅ΠΉ β Π·Π°Π»ΠΎΠ³ ΠΏΡΠΎΡΠ½ΠΎΡΡΠΈ ΠΆΠ΅Π»Π΅Π·ΠΎΠ±Π΅ΡΠΎΠ½Π½ΠΎΠ³ΠΎ ΡΠΎΠΎΡΡΠΆΠ΅Π½ΠΈΡ. ΠΡΠΈ Π½Π΅Π΄ΠΎΡΡΠ°ΡΠΎΡΠ½ΠΎΠΉ Π²Π΅Π»ΠΈΡΠΈΠ½Π΅ ΠΏΠ»Π°ΡΡΠ° Π±Π΅ΡΠΎΠ½Π° ΠΏΡΡΡΠΊΠΈ Π½Π°ΡΠ½ΡΡ ΡΠ°Π·ΡΡΡΠ°ΡΡΡΡ ΠΈ ΠΏΡΠΎΠΈΠ·ΠΎΠΉΠ΄ΡΡ ΠΈΠ·ΠΌΠ΅Π½Π΅Π½ΠΈΡ Π²ΠΎ Π²ΡΠ΅ΠΉ ΠΊΠΎΠ½ΡΡΡΡΠΊΡΠΈΠΈ ΡΡΡΠΎΠ΅Π½ΠΈΡ.
ΠΠΎΠ»ΡΡΠΎΠΉ ΡΠ»ΠΎΠΉ β Π½Π΅ Π»ΡΡΡΠΈΠΉ Π²Π°ΡΠΈΠ°Π½Ρ. Π‘ΡΠΎΠΈΠΌΠΎΡΡΡ ΡΠΎΠΎΡΡΠΆΠ΅Π½ΠΈΡ Π½Π΅ΠΎΠΏΡΠ°Π²Π΄Π°Π½Π½ΠΎ ΡΠ²Π΅Π»ΠΈΡΠΈΡΡΡ, ΠΏΠΎΡΠ²ΠΈΡΡΡ Π²Π΅ΡΠΎΡΡΠ½ΠΎΡΡΡ ΡΠΌΠ΅ΡΠ΅Π½ΠΈΡ ΠΏΡΡΡΠΊΠΎΠ², ΡΡΠΎ Π² ΡΠ²ΠΎΡ ΠΎΡΠ΅ΡΠ΅Π΄Ρ ΡΠ½ΠΈΠ·ΠΈΡ ΠΏΡΠΎΡΠ½ΠΎΡΡΡ ΠΎΠ±ΡΠ΅ΠΊΡΠ°. ΠΡΠΈ ΠΈΡΠΏΠΎΠ»ΡΠ·ΠΎΠ²Π°Π½ΠΈΠΈ ΡΠΏΠ΅ΡΠΈΠ°Π»ΡΠ½ΡΡ ΡΠΈΠΊΡΠΈΡΡΡΡΠΈΡ ΡΡΡΡΠΎΠΉΡΡΠ² ΡΠ΄Π²ΠΈΠ³ Π°ΡΠΌΠ°ΡΡΡΡ ΠΏΠ΅ΡΠ΅ΡΡΠ°Π» Π±ΡΡΡ ΠΏΡΠΎΠ±Π»Π΅ΠΌΠΎΠΉ.
ΠΡ ΡΠ΅Π³ΠΎ ΠΆΠ΅ Π·Π°Π²ΠΈΡΠΈΡ ΠΎΠΏΡΠΈΠΌΠ°Π»ΡΠ½ΠΎ ΠΏΠΎΠ΄Ρ ΠΎΠ΄ΡΡΠ°Ρ ΡΠΎΠ»ΡΠΈΠ½Π° Π·Π°ΡΠΈΡΠ½ΠΎΠ³ΠΎ ΠΏΠ»Π°ΡΡΠ°? ΠΡΠ° Π²Π΅Π»ΠΈΡΠΈΠ½Π° ΠΏΠΎΠ΄Π±ΠΈΡΠ°Π΅ΡΡΡ Ρ ΡΡΠ΅ΡΠΎΠΌ:
- Π’ΠΈΠΏΠ° ΠΊΠΎΠ½ΡΡΡΡΠΊΡΠΈΠΉ. Π‘ΡΡΠΎΠΈΡΠ΅Π»ΡΠ½ΡΠ΅ Π½ΠΎΡΠΌΠ°ΡΠΈΠ²Ρ ΡΠ΅ΡΠΊΠΎ ΡΠΊΠ°Π·ΡΠ²Π°ΡΡ ΡΠ°Π·ΠΌΠ΅ΡΡ Π·Π°ΡΠΈΡΠ½ΠΎΠ³ΠΎ ΠΏΠ»Π°ΡΡΠ° Π΄Π»Ρ ΡΡΠ΅Π½, ΡΡΠ½Π΄Π°ΠΌΠ΅Π½ΡΠ°, ΠΊΠΎΠ»ΠΎΠ½Π½Ρ, Π±Π°Π»ΠΎΠΊ ΠΈ Π΄ΡΡΠ³ΠΈΡ ΡΠ»Π΅ΠΌΠ΅Π½ΡΠΎΠ²;
- ΠΠΈΠ°ΠΌΠ΅ΡΡΠ° Π°ΡΠΌΠ°ΡΡΡΠ½ΠΎΠ³ΠΎ ΠΏΡΡΡΠΊΠ°. Π§Π΅ΠΌ Π²ΡΡΠ΅ Π΅Π³ΠΎ ΡΠ΅ΡΠ΅Π½ΠΈΠ΅, ΡΠ΅ΠΌ Π±ΠΎΠ»ΡΡΠ΅ ΡΠΎΠ»ΡΠΈΠ½Π° Π±Π΅ΡΠΎΠ½Π½ΠΎΠΉ ΠΏΡΠΎΡΠ»ΠΎΠΉΠΊΠΈ;
- Π ΠΎΠ»ΠΈ ΠΌΠ΅ΡΠ°Π»Π»ΠΈΡΠ΅ΡΠΊΠΈΡ
ΡΠ»Π΅ΠΌΠ΅Π½ΡΠΎΠ² Π² ΠΊΠΎΠ½ΡΡΡΡΠΊΡΠΈΡΡ
.
ΠΡΠΎ ΠΌΠΎΠ³ΡΡ Π±ΡΡΡ ΡΠ°ΡΠΏΡΠ΅Π΄Π΅Π»ΠΈΡΠ΅Π»ΡΠ½ΡΠ΅ ΡΡΠ΅ΡΠΆΠ½ΠΈ ΠΈΠ»ΠΈ ΡΠ°Π±ΠΎΡΠΈΠ΅, Π²ΠΎΡΠΏΡΠΈΠ½ΠΈΠΌΠ°ΡΡΠΈΠ΅ ΠΎΡΠ½ΠΎΠ²Π½ΡΠ΅ Π½Π°Π³ΡΡΠ·ΠΊΠΈ;
- Π£ΡΠ»ΠΎΠ²ΠΈΠΉ ΠΎΠΊΡΡΠΆΠ°ΡΡΠ΅ΠΉ ΡΡΠ΅Π΄Ρ. Π§Π΅ΠΌ ΠΎΠ½Π° Π°Π³ΡΠ΅ΡΡΠΈΠ²Π½Π΅Π΅ Π΄Π»Ρ ΡΠ»Π΅ΠΌΠ΅Π½ΡΠ° ΡΠΎΠΎΡΡΠΆΠ΅Π½ΠΈΡ, ΡΠ΅ΠΌ Π²ΡΡΠ΅ Π½ΠΎΡΠΌΡ Π²Π΅Π»ΠΈΡΠΈΠ½Ρ ΡΠ»ΠΎΡ Π²ΠΏΠ»ΠΎΡΡ Π΄ΠΎ ΠΌΠ°ΠΊΡΠΈΠΌΠ°Π»ΡΠ½ΠΎ Π΄ΠΎΠΏΡΡΡΠΈΠΌΡΡ ;
- ΠΠΈΠ΄Π° Π°ΡΠΌΠ°ΡΡΡΡ. ΠΠ½Π° ΠΌΠΎΠΆΠ΅Ρ Π±ΡΡΡ Π½Π΅Π½Π°ΠΏΡΡΠ³Π°Π΅ΠΌΠΎΠΉ ΠΈ Π½Π°ΠΏΡΡΠ³Π°Π΅ΠΌΠΎΠΉ, ΡΡΡΠ°Π½Π°Π²Π»ΠΈΠ²Π°Π΅ΠΌΠΎΠΉ Π² ΠΌΠ΅ΡΡΠ° Π½Π°ΠΈΠ±ΠΎΠ»ΡΡΠΈΡ Π½Π°Π³ΡΡΠ·ΠΎΠΊ.
Π’ΠΎΠ»ΡΠΈΠ½Π° ΠΏΠ»Π°ΡΡΠ° Π±Π΅ΡΠΎΠ½Π° Π΄Π»Ρ ΡΠ°Π·Π»ΠΈΡΠ½ΡΡ ΡΠ»ΡΡΠ°Π΅Π²
ΠΠ΅Π»ΠΈΡΠΈΠ½Π° ΡΠ»ΠΎΡ Π΄Π»Ρ Π·Π°ΡΠΈΡΡ Π² ΠΆΠ΅Π»Π΅Π·ΠΎΠ±Π΅ΡΠΎΠ½Π½ΡΡ ΠΊΠΎΠ½ΡΡΡΡΠΊΡΠΈΡΡ ΠΏΡΠΎΠΏΠΈΡΠ°Π½Π° Π² Π‘Π 63.13330.2012. Π‘ ΠΏΠΎΠΌΠΎΡΡΡ ΡΡΠΎΠ³ΠΎ Π΄ΠΎΠΊΡΠΌΠ΅Π½ΡΠ° ΠΌΠΎΠΆΠ½ΠΎ ΡΠ·Π½Π°ΡΡ ΡΠΎΡΠ½ΠΎΠ΅ Π·Π½Π°ΡΠ΅Π½ΠΈΠ΅ ΠΏΡΠΎΡΠ»ΠΎΠΉΠΊΠΈ Π΄Π»Ρ ΡΠΎΠ³ΠΎ ΠΈΠ»ΠΈ ΠΈΠ½ΠΎΠ³ΠΎ ΡΠ»ΡΡΠ°Ρ. ΠΠΈΠ½ΠΈΠΌΠ°Π»ΡΠ½ΡΠΉ ΡΠ°Π·ΠΌΠ΅Ρ ΡΠ»ΠΎΡ Π΄Π»Ρ ΡΠ°Π±ΠΎΡΠ΅ΠΉ Π°ΡΠΌΠ°ΡΡΡΡ Π΄ΠΎΠ»ΠΆΠ΅Π½ ΡΠΎΡΡΠ°Π²Π»ΡΡΡ:
- Π² ΡΡΠ½Π΄Π°ΠΌΠ΅Π½ΡΠ΅ Ρ ΡΡΡΡΠΎΠ΅Π½Π½ΠΎΠΉ Π±Π΅ΡΠΎΠ½Π½ΠΎΠΉ ΠΏΠΎΠ΄Π³ΠΎΡΠΎΠ²ΠΊΠΎΠΉ ΠΈ Π² Π³ΡΡΠ½ΡΠ΅ β 40 ΠΌΠΌ;
- Π΄Π»Ρ ΠΊΠΎΠ½ΡΡΡΡΠΊΡΠΈΠΈ, Π½Π°Ρ ΠΎΠ΄ΡΡΠ΅ΠΉΡΡ Π½Π° ΠΎΡΠΊΡΡΡΠΎΠΌ Π²ΠΎΠ·Π΄ΡΡ Π΅ β 30 ΠΌΠΌ;
- Π΄Π»Ρ Π·Π°ΠΊΡΡΡΡΡ Π²Π»Π°ΠΆΠ½ΡΡ ΠΏΠΎΠΌΠ΅ΡΠ΅Π½ΠΈΠΉ β 25 ΠΌΠΌ;
- Π΄Π»Ρ ΠΏΠΎΠΌΠ΅ΡΠ΅Π½ΠΈΠΉ Ρ ΠΏΠΎΠ½ΠΈΠΆΠ΅Π½Π½ΠΎΠΉ ΠΈ Π½ΠΎΡΠΌΠ°Π»ΡΠ½ΠΎΠΉ Π²Π»Π°ΠΆΠ½ΠΎΡΡΡΡ β 10 ΠΌΠΌ.
ΠΡΠΈ ΠΈΡΠΏΠΎΠ»ΡΠ·ΠΎΠ²Π°Π½ΠΈΠΈ ΡΠ°ΡΠΏΡΠ΅Π΄Π΅Π»ΠΈΡΠ΅Π»ΡΠ½ΠΎΠ³ΠΎ ΡΡΠ΅ΡΠΆΠ½Ρ ΠΈ ΡΠ±ΠΎΡΠ½ΡΡ
ΡΠ»Π΅ΠΌΠ΅Π½ΡΠΎΠ² ΡΡΠΈ Π·Π½Π°ΡΠ΅Π½ΠΈΡ ΡΠΌΠ΅Π½ΡΡΠ°ΡΡΡΡ Π½Π° 5 ΠΌΠΌ, Π½ΠΎ Π² Π»ΡΠ±ΠΎΠΌ ΡΠ»ΡΡΠ°Π΅ ΡΠΎΠ»ΡΠΈΠ½Π° ΠΏΡΠΎΡΠ»ΠΎΠΉΠΊΠΈ Π½Π΅ Π΄ΠΎΠ»ΠΆΠ½Π° Π±ΡΡΡ ΠΌΠ΅Π½ΡΡΠ΅ Π΄ΠΈΠ°ΠΌΠ΅ΡΡΠ° Π°ΡΠΌΠ°ΡΡΡΠ½ΠΎΠ³ΠΎ ΡΡΠ΅ΡΠΆΠ½Ρ ΠΈ ΠΊΠ°ΠΊ ΠΌΠΈΠ½ΠΈΠΌΡΠΌ ΡΠ°Π²Π½ΡΡΡΡΡ 10 ΠΌΠΌ. ΠΡΠ»ΠΈ Π΄Π»Ρ ΠΎΠ΄Π½ΠΎΡΠ»ΠΎΠΆΠ½ΡΡ
ΠΊΠΎΠ½ΡΡΡΡΠΊΡΠΈΠΉ ΠΏΡΠΈΠΌΠ΅Π½ΡΠ΅ΡΡΡ ΠΏΠΎΡΠΈΠ·ΠΎΠ²Π°Π½Π½Π°Ρ ΠΈΠ»ΠΈ Π»Π΅Π³ΠΊΠ°Ρ Π±Π΅ΡΠΎΠ½Π½Π°Ρ ΡΠΌΠ΅ΡΡ ΠΊΠ»Π°ΡΡΠ° Π7,5 ΠΈΠ»ΠΈ Π½ΠΈΠΆΠ΅, ΡΠΎ ΠΏΠ»Π°ΡΡ Π±Π΅ΡΠΎΠ½Π° Π΄ΠΎΠ»ΠΆΠ΅Π½ Π±ΡΡΡ Π½Π΅ ΠΌΠ΅Π½ΡΡΠ΅ 20 ΠΌΠΌ. ΠΡΠΈ ΠΈΡΠΏΠΎΠ»ΡΠ·ΠΎΠ²Π°Π½ΠΈΠΈ Π΄Π»Ρ ΡΠ°ΠΊΠΈΡ
ΠΊΠΎΠ½ΡΡΡΡΠΊΡΠΈΠΉ ΡΡΠ΅ΠΈΡΡΠΎΠ³ΠΎ ΡΠ°ΡΡΠ²ΠΎΡΠ° ΠΎΠ½ ΡΠΎΡΡΠ°Π²Π»ΡΠ΅Ρ 25 ΠΌΠΌ. ΠΡΠΎ ΠΆΠ΅ Π·Π½Π°ΡΠ΅Π½ΠΈΠ΅ ΡΡΡΠ°Π½ΠΎΠ²Π»Π΅Π½ΠΎ Π΄Π»Ρ ΡΡΠ΅Π½ΠΎΠ²ΡΡ
ΠΏΠ°Π½Π΅Π»Π΅ΠΉ, ΠΌΠΎΠ½ΡΠΈΡΡΠ΅ΠΌΡΡ
ΡΠ½Π°ΡΡΠΆΠΈ ΠΈ Π±Π΅Π· ΡΠ°ΠΊΡΡΡΠ½ΠΎΠ³ΠΎ ΡΠ»ΠΎΡ.
ΠΠ»Ρ ΡΡΠ΅ΡΠΆΠ½Π΅ΠΉ Π² ΠΏΡΠ΅Π΄Π²Π°ΡΠΈΡΠ΅Π»ΡΠ½ΠΎ Π½Π°ΠΏΡΡΠΆΠ΅Π½Π½ΡΡ ΡΠ»Π΅ΠΌΠ΅Π½ΡΠ°Ρ ΡΠΎΠ»ΡΠΈΠ½Π° Π·Π°ΡΠΈΡΠ½ΠΎΠΉ ΠΏΡΠΎΡΠ»ΠΎΠΉΠΊΠΈ Π΄ΠΎΠ»ΠΆΠ½Π° Π±ΡΡΡ Π½Π΅ ΠΌΠ΅Π½ΡΡΠ΅ 40 ΠΌΠΌ ΠΈΠ»ΠΈ ΡΠ°Π²Π½ΡΡΡΡΡ ΡΡΠ΅ΠΌ Π΄ΠΈΠ°ΠΌΠ΅ΡΡΠ°ΠΌ, Π° ΠΏΡΠΈ ΡΠ°Π·ΠΌΠ΅ΡΠ΅Π½ΠΈΠΈ Π°ΡΠΌΠ°ΡΡΡΠ½ΡΡ ΠΊΠ°Π½Π°ΡΠΎΠ² β Π½Π΅ ΠΌΠ΅Π½ΡΡΠ΅ 20 ΠΌΠΌ. ΠΡΠ»ΠΈ Π½Π°ΠΏΡΡΠ³Π°Π΅ΠΌΡΠΉ ΠΏΡΠΎΠ΄ΠΎΠ»ΡΠ½ΡΠΉ ΠΏΡΡΡΠΎΠΊ Π½Π°ΡΡΠ³ΠΈΠ²Π°Π΅ΡΡΡ Π½Π° Π±Π΅ΡΠΎΠ½ ΠΈ ΡΠ°Π·ΠΌΠ΅ΡΠ°Π΅ΡΡΡ Π² ΠΊΠ°Π½Π°Π»Π°Ρ , ΡΠΎ ΠΏΠΎΡΡΠ΅Π±ΡΠ΅ΡΡΡ Π·Π°Π»ΠΈΠ²ΠΊΠ° ΡΠ°ΡΡΠ²ΠΎΡΠ° ΡΠ»ΠΎΠ΅ΠΌ 40 ΠΌΠΌ ΠΈ Π±ΠΎΠ»Π΅Π΅. ΠΡΠΈ ΡΡΠΎΠΌ ΠΏΠ»Π°ΡΡ ΡΠΌΠ΅ΡΠΈ Π΄ΠΎΠ»ΠΆΠ΅Π½ Π±ΡΡΡ Π½Π΅ ΠΌΠ΅Π½Π΅Π΅ Π΄ΠΈΠ°ΠΌΠ΅ΡΡΠ° ΠΊΠ°Π½Π°Π»Π°, Π° ΠΏΡΠΎΡΡΡΠ°Π½ΡΡΠ²ΠΎ ΠΏΠΎ ΠΊΡΠ°ΡΠΌ Π°ΡΠΌΠ°ΡΡΡΡ β ΠΏΠΎΠ»ΠΎΠ²ΠΈΠ½Π° ΡΠ°ΠΊΠΎΠ³ΠΎ ΡΠ°ΡΡΡΠΎΡΠ½ΠΈΡ.
ΠΡΠΈ ΡΠΊΡΠΏΠ»ΡΠ°ΡΠ°ΡΠΈΠΈ Π² Π°Π³ΡΠ΅ΡΡΠΈΠ²Π½ΡΡ
ΡΡΠ΅Π΄Π°Ρ
ΡΡΠ΅Π½ΠΎΠ²ΡΡ
ΠΏΠ°Π½Π΅Π»Π΅ΠΉ, ΡΠ΅Π±ΡΠΈΡΡΡΡ
ΠΈ ΠΏΠ»ΠΎΡΠΊΠΈΡ
ΠΏΠ»ΠΈΡ Π·Π°ΡΠΈΡΠ½ΡΠΉ ΠΏΠ»Π°ΡΡ ΡΠΎΠ·Π΄Π°ΡΡ ΠΈΠ· Π»Π΅Π³ΠΊΠΎΠ³ΠΎ ΠΈ ΡΡΠΆΠ΅Π»ΠΎΠ³ΠΎ Π±Π΅ΡΠΎΠ½Π°. ΠΠ΅Π·Π°Π²ΠΈΡΠΈΠΌΠΎ ΠΎΡ Π²ΡΠ±ΡΠ°Π½Π½ΠΎΠ³ΠΎ ΠΊΠ»Π°ΡΡΠ° ΡΡΠ°Π»ΠΈ Π΄Π»Ρ Π°ΡΠΌΠ°ΡΡΡΡ ΡΠΎΠ»ΡΠΈΠ½Π° ΡΠ°ΡΡΠ²ΠΎΡΠ° Π΄Π»Ρ ΡΠ»Π°Π±ΠΎ- ΠΈ ΡΡΠ΅Π΄Π½Π΅Π°Π³ΡΠ΅ΡΡΠΈΠ²Π½ΠΎΠΉ ΡΡΠ΅Π΄Ρ ΡΠΎΡΡΠ°Π²Π»ΡΠ΅Ρ 15 ΡΠΌ. ΠΡΠΈ ΡΠΈΠ»ΡΠ½ΠΎΠΉ Π½Π΅Π³Π°ΡΠΈΠ²Π½ΠΎΠΉ ΡΡΠ΅ΠΏΠ΅Π½ΠΈ Π²Π»ΠΈΡΠ½ΠΈΡ β 20 ΠΌΠΌ. ΠΠ΅ΡΠ΅Π΄ΠΊΠΎ Π² ΡΠ°ΠΊΠΈΡ
ΡΠ»ΡΡΠ°ΡΡ
ΠΈΡΠΏΠΎΠ»ΡΠ·ΡΡΡ ΠΊΠΎΠΌΠΏΠΎΠ·ΠΈΡΠ½ΡΠ΅ Π½Π΅ΠΌΠ΅ΡΠ°Π»Π»ΠΈΡΠ΅ΡΠΊΠΈΠ΅ ΡΡΠ΅ΡΠΆΠ½ΠΈ. Π ΡΡΠΈΡ
ΡΠ»ΡΡΠ°ΡΡ
Π²Π΅Π»ΠΈΡΠΈΠ½Π° Π·Π°ΡΠΈΡΠ½ΠΎΠ³ΠΎ ΡΠ»ΠΎΡ ΠΏΠΎΠ΄Π±ΠΈΡΠ°Π΅ΡΡΡ ΡΠ°ΠΊ, ΡΡΠΎΠ±Ρ ΠΎΠ±Π΅ΡΠΏΠ΅ΡΠΈΠ²Π°Π»Π°ΡΡ ΡΠΎΠ²ΠΌΠ΅ΡΡΠ½Π°Ρ ΡΠ°Π±ΠΎΡΠ° ΠΏΡΡΡΠΊΠ° Ρ Π±Π΅ΡΠΎΠ½ΠΎΠΌ. ΠΠ»Ρ ΠΌΠΎΠ½ΠΎΠ»ΠΈΡΠ½ΡΡ
ΠΊΠΎΠ½ΡΡΡΡΠΊΡΠΈΠΉ ΡΠΊΠ°Π·Π°Π½Π½ΡΡ Π²ΡΡΠ΅ ΡΠΎΠ»ΡΠΈΠ½Ρ ΠΏΡΠΎΡΠ»ΠΎΠΉΠΊΠΈ ΡΠ²Π΅Π»ΠΈΡΠΈΠ²Π°ΡΡ Π½Π° 5 ΠΌΠΌ.
ΠΡΠΎΠ±Π΅Π½Π½ΠΎΡΡΠΈ ΡΠ΅ΠΊΠΎΠ½ΡΡΡΡΠΊΡΠΈΠΈ ΠΏΡΠΎΡΠ»ΠΎΠΉΠΊΠΈ
Π ΠΏΡΠΎΡΠ΅ΡΡΠ΅ ΡΠΊΡΠΏΠ»ΡΠ°ΡΠ°ΡΠΈΠΈ ΡΡΡΠΎΠΈΡΠ΅Π»ΡΠ½ΡΠ΅ ΠΊΠΎΠ½ΡΡΡΡΠΊΡΠΈΠΈ ΠΈΡΠΏΡΡΡΠ²Π°ΡΡ ΠΆΠ΅ΡΡΠΊΠΈΠ΅ ΠΏΡΠΈΡΠΎΠ΄Π½ΡΠ΅ Π²ΠΎΠ·Π΄Π΅ΠΉΡΡΠ²ΠΈΡ. Π‘Π°ΠΌΡΠ΅ ΠΎΠΏΠ°ΡΠ½ΡΠ΅ ΠΈΠ· Π½ΠΈΡ β ΠΊΠΎΠ»Π΅Π±Π°Π½ΠΈΡ ΡΠ΅ΠΌΠΏΠ΅ΡΠ°ΡΡΡ ΠΈ ΠΏΠ΅ΡΠΈΠΎΠ΄ΠΈΡΠ΅ΡΠΊΠΎΠ΅ ΡΠ²Π»Π°ΠΆΠ½Π΅Π½ΠΈΠ΅ Π²Π½Π΅ΡΠ½Π΅ΠΉ ΠΏΠΎΠ²Π΅ΡΡ Π½ΠΎΡΡΠΈ Π±Π΅ΡΠΎΠ½Π°. ΠΠΎΡΡΠΎΠΌΡ Π·Π°ΡΠΈΡΠ½ΡΠΉ ΠΏΠ»Π°ΡΡ, Π΄Π°ΠΆΠ΅ Π²Π΅ΡΠ½ΠΎ ΠΏΠΎΠ΄ΠΎΠ±ΡΠ°Π½Π½ΡΠΉ, ΠΏΠΎΡΡΠ΅ΠΏΠ΅Π½Π½ΠΎ ΠΌΠΎΠΆΠ΅Ρ Π½Π°ΡΠ°ΡΡ ΡΠ°Π·ΡΡΡΠ°ΡΡΡΡ. Π’ΡΠ΅ΡΠΈΠ½Ρ ΠΈ ΠΎΡΡΠ»ΠΎΠ΅Π½ΠΈΡ ΡΠΎ Π²ΡΠ΅ΠΌΠ΅Π½Π΅ΠΌ ΠΏΡΠΈΠ²ΠΎΠ΄ΡΡ ΠΊ ΠΎΠ³ΠΎΠ»Π΅Π½ΠΈΡ Π°ΡΠΌΠ°ΡΡΡΠ½ΡΡ ΡΡΠ΅ΡΠΆΠ½Π΅ΠΉ. Π§ΡΠΎΠ±Ρ Π°ΡΠΌΠΈΡΠΎΠ²Π°Π½ΠΈΠ΅ ΠΌΠΎΠ³Π»ΠΎ Π²ΡΠΏΠΎΠ»Π½ΡΡΡ ΡΠ²ΠΎΠΈ ΡΡΠ½ΠΊΡΠΈΠΈ Π½Π° ΡΠ°ΠΊΠΈΡ ΠΊΠΎΠ½ΡΡΡΡΠΊΡΠΈΡΡ Π½Π΅ΠΎΠ±Ρ ΠΎΠ΄ΠΈΠΌΠΎ Π²ΠΎΡΡΡΠ°Π½ΠΎΠ²ΠΈΡΡ ΠΏΡΠΎΡΠ»ΠΎΠΉΠΊΡ.
Π Π°Π±ΠΎΡΡ ΠΏΠΎ ΡΠ΅ΠΊΠΎΠ½ΡΡΡΡΠΊΡΠΈΠΈ ΠΎΠ±ΡΠ΅ΠΊΡΠ° Π½Π°ΡΠΈΠ½Π°ΡΡΡΡ Ρ ΡΡΠ°ΡΠ΅Π»ΡΠ½ΠΎΠ³ΠΎ ΠΎΡΠΌΠΎΡΡΠ° ΠΏΠΎΠ²ΡΠ΅ΠΆΠ΄Π΅Π½ΠΈΠΉ ΠΈ ΠΏΡΠΎΠ²Π΅ΡΠΊΠΈ ΡΠΎΠ»ΡΠΈΠ½Ρ ΠΈΠΌΠ΅ΡΡΠ΅Π³ΠΎΡΡ Π·Π°ΡΠΈΡΠ½ΠΎΠ³ΠΎ ΠΏΠ»Π°ΡΡΠ°. ΠΠ½Π° ΠΈΠ·ΠΌΠ΅ΡΡΠ΅ΡΡΡ ΡΠΏΠ΅ΡΠΈΠ°Π»ΡΠ½ΡΠΌ ΡΡΡΡΠΎΠΉΡΡΠ²ΠΎΠΌ, ΡΠ°Π±ΠΎΡΠ° ΠΊΠΎΡΠΎΡΠΎΠ³ΠΎ ΠΏΠΎΡΡΡΠΎΠ΅Π½Π° Π½Π° ΠΌΠ°Π³Π½ΠΈΡΠ½ΠΎΠΌ ΠΏΡΠΈΠ½ΡΠΈΠΏΠ΅. Π’Π°ΠΊΠΆΠ΅ Π²ΡΡΠ²Π»ΡΡΡΡΡ ΠΏΡΠΈΡΠΈΠ½Ρ Π²ΠΎΠ·Π½ΠΈΠΊΠ½ΠΎΠ²Π΅Π½ΠΈΡ ΠΏΠΎΠ²ΡΠ΅ΠΆΠ΄Π΅Π½ΠΈΡ ΠΈ ΠΈΡ
ΡΡΠ΅ΠΏΠ΅Π½Ρ. ΠΠ΅Π΄Ρ Π΅ΡΠ»ΠΈ Π³Π»ΡΠ±ΠΈΠ½Π½ΡΠ΅ ΡΠ»ΠΎΠΈ ΡΠ»Π΅ΠΌΠ΅Π½ΡΠΎΠ² ΡΡΡΠΎΠ΅Π½ΠΈΡ Π±ΡΠ΄ΡΡ Π·Π°ΡΡΠΎΠ½ΡΡΡ, ΡΠΎ ΠΏΠΎΡΡΠ΅Π±ΡΠ΅ΡΡΡ Π³Π»ΠΎΠ±Π°Π»ΡΠ½ΠΎΠ΅ ΡΡΠΈΠ»Π΅Π½ΠΈΠ΅ ΠΏΡΠΎΡΠ½ΠΎΡΡΠΈ.
Π ΠΏΡΠΎΡΡΡΡ ΡΠ»ΡΡΠ°ΡΡ Π½Π΅ΠΎΠ±Ρ ΠΎΠ΄ΠΈΠΌΠΎ ΠΎΡΠ½ΠΎΠ²Π°ΡΠ΅Π»ΡΠ½ΠΎ Π·Π°Π΄Π΅Π»Π°ΡΡ ΠΎΡΠ΄Π΅Π»ΡΠ½ΡΠ΅ ΡΠ°ΠΊΠΎΠ²ΠΈΠ½Ρ, ΡΠΊΠΎΠ»Ρ ΠΈ ΠΏΠΎΠ΄ΠΎΠ±Π½ΡΠ΅ Π΄Π΅ΡΠ΅ΠΊΡΡ ΠΏΠΎΠ²Π΅ΡΡ Π½ΠΎΡΡΠΈ. Π’Π°ΠΊΠΈΠ΅ ΡΠ΅ΠΌΠΎΠ½ΡΠ½ΡΠ΅ ΡΠ°Π±ΠΎΡΡ Π½Π΅ ΡΡΠ΅Π±ΡΡΡ ΠΌΠ½ΠΎΠ³ΠΎ Π²ΡΠ΅ΠΌΠ΅Π½ΠΈ ΠΈ ΡΠΈΠ». ΠΠΎΠ²ΡΠ΅ΠΆΠ΄Π΅Π½Π½ΡΠ΅ ΡΡΠ°ΡΡΠΊΠΈ ΠΏΠΎΠ΄Π³ΠΎΡΠ°Π²Π»ΠΈΠ²Π°ΡΡ, ΡΠ±ΠΈΡΠ°Ρ ΠΏΡΠ»Ρ, Π³ΡΡΠ·Ρ ΠΈ ΠΎΡΡΠ»ΠΎΠΈΠ²ΡΠΈΠ΅ΡΡ ΡΠ°ΡΡΠΈΡΠΊΠΈ. ΠΠ°ΡΠ΅ΠΌ Π·Π°ΡΠΈΡΠ°ΡΡ ΡΡΠ΅ΡΠΈΠ½Ρ ΠΈ ΡΠ΅Π»ΠΈ ΡΠΆΠ°ΡΡΠΌ Π²ΠΎΠ·Π΄ΡΡ ΠΎΠΌ, Π³ΡΡΠ½ΡΡΡΡ ΠΏΠΎΠ΄Π»Π΅ΠΆΠ°ΡΡΡ ΡΠ΅ΠΌΠΎΠ½ΡΡ ΠΏΠ»ΠΎΡΠΊΠΎΡΡΡ ΠΈ Π²ΡΠ΅ Π΄Π΅ΡΠ΅ΠΊΡΡ Π·Π°ΠΏΠΎΠ»Π½ΡΡΡΡΡ ΡΠ°ΡΡΠ²ΠΎΡΠΎΠΌ. Π‘Π΅ΡΡΠ΅Π·Π½ΡΠ΅ ΡΡΠ΅ΡΠΈΠ½Ρ ΡΡΠΈΠ²Π°ΡΡ ΠΏΠ»ΠΎΡΠΊΠΈΠΌΠΈ Π°Π½ΠΊΠ΅ΡΠ°ΠΌΠΈ; ΠΎΠ½ΠΈ Π΄ΠΎΠ»ΠΆΠ½Ρ Π±ΡΡΡ ΠΏΠΎΠΊΡΡΡΡ Π·Π°ΡΠΈΡΠ½ΡΠΌ ΡΠ»ΠΎΠ΅ΠΌ Π² 20 ΠΌΠΌ. ΠΡΠ΅ ΡΠ°Π±ΠΎΡΡ ΠΏΡΠΎΠ²ΠΎΠ΄ΡΡ ΠΏΡΠΈ Π±Π»Π°Π³ΠΎΠΏΡΠΈΡΡΠ½ΡΡ ΡΠ΅ΠΌΠΏΠ΅ΡΠ°ΡΡΡΠ½ΡΡ ΡΠ΅ΠΆΠΈΠΌΠ°Ρ Π² ΡΡΡ ΡΡ ΠΏΠΎΠ³ΠΎΠ΄Ρ.
ΠΡΠΈ Π·Π½Π°ΡΠΈΡΠ΅Π»ΡΠ½ΠΎΠΌ ΠΎΡΡΠ»ΠΎΠ΅Π½ΠΈΠΈ Π·Π°ΡΠΈΡΠ½ΠΎΠΉ ΠΏΡΠΎΡΠ»ΠΎΠΉΠΊΠΈ, ΠΈΠ·ΠΌΠ΅Π½Π΅Π½ΠΈΠΈ Ρ
Π°ΡΠ°ΠΊΡΠ΅ΡΠΈΡΡΠΈΠΊ ΠΌΠ°ΡΠ΅ΡΠΈΠ°Π»ΠΎΠ² ΠΈ ΠΏΠΎΡΠ°ΠΆΠ΅Π½ΠΈΠΈ Π°ΡΠΌΠ°ΡΡΡΠ½ΡΡ
ΠΏΡΡΡΠΊΠΎΠ² ΠΊΠΎΡΡΠΎΠ·ΠΈΠ΅ΠΉ Π½Π΅ΠΎΠ±Ρ
ΠΎΠ΄ΠΈΠΌΠ° ΠΏΠΎΠ»Π½Π°Ρ Π·Π°ΠΌΠ΅Π½Π° ΠΏΠ»Π°ΡΡΠ°.
- Π°ΠΊΠΊΡΡΠ°ΡΠ½ΠΎ ΡΠ΄Π°Π»ΡΡΡ ΡΡΠ°ΡΡΠΉ ΡΠ»ΠΎΠΉ;
- Π°ΡΠΌΠ°ΡΡΡΡ ΠΎΡΠΈΡΠ°ΡΡ Ρ ΠΈΠΌΠΈΡΠ΅ΡΠΊΠΈΠΌ ΡΠΏΠΎΡΠΎΠ±ΠΎΠΌ ΠΈΠ»ΠΈ Π°ΠΏΠΏΠ°ΡΠ°ΡΠ°ΠΌΠΈ Π²ΡΡΠΎΠΊΠΎΠ³ΠΎ Π΄Π°Π²Π»Π΅Π½ΠΈΡ;
- ΠΏΡΡΡΠΊΠΈ ΠΏΠΎΠΊΡΡΠ²Π°ΡΡ Π°Π½ΡΠΈΠΊΠΎΡΡΠΎΠ·ΠΈΠΉΠ½ΡΠΌΠΈ ΡΠΎΡΡΠ°Π²Π°ΠΌΠΈ;
- ΠΏΡΠΈ Π½Π΅ΠΎΠ±Ρ ΠΎΠ΄ΠΈΠΌΠΎΡΡΠΈ Π²ΠΎΡΡΡΠ°Π½ΠΎΠ²ΠΈΡΡ ΠΏΡΠΎΡΠ½ΠΎΡΡΡ ΠΊΠΎΠ½ΡΡΡΡΠΊΡΠΈΠΈ ΡΡΡΠ°Π½Π°Π²Π»ΠΈΠ²Π°ΡΡ ΡΡΠ°Π»ΡΠ½ΡΠ΅ Π°Π½ΠΊΠ΅ΡΡ;
- ΡΡΠ°ΡΠΎΠ΅ ΠΎΡΠ½ΠΎΠ²Π°Π½ΠΈΠ΅ ΠΎΡΠΈΡΠ°ΡΡ ΠΎΡ Π·Π°Π³ΡΡΠ·Π½Π΅Π½ΠΈΠΉ, ΠΏΡΠ»ΠΈ ΠΈ Π½Π°ΡΡΡΠ°ΡΡ Π²ΠΎΠ΄ΠΎΠΉ;
- ΡΠ΅ΠΌΠΎΠ½ΡΠ½ΡΠΉ ΡΠ°ΡΡΠ²ΠΎΡ Π½Π°Π½ΠΎΡΡΡ ΡΠΎΡΠΊΡΠ΅ΡΠΈΡΠΎΠ²Π°Π½ΠΈΠ΅ΠΌ ΠΈΠ»ΠΈ Π½Π°Π±ΡΡΠ·Π³ΠΎΠΌ. ΠΡΠΈ ΡΡΠΎΠΌ ΠΌΠ°Π»Π΅ΠΉΡΠΈΠ΅ ΡΡΠ΅ΡΠΈΠ½Ρ, ΠΏΠΎΡΡ ΠΈ Π²ΠΏΠ°Π΄ΠΈΠ½Ρ Π·Π°ΠΏΠΎΠ»Π½ΡΡΡΡΡ ΡΠΌΠ΅ΡΡΡ. Π’ΠΎΠ»ΡΠΈΠ½Π° ΠΏΡΠΎΡΠ»ΠΎΠΉΠΊΠΈ ΠΎΠ±ΡΡΠ½ΠΎ ΡΠΎΡΡΠ°Π²Π»ΡΠ΅Ρ ΠΏΠΎΡΡΠ΄ΠΊΠ° 30 ΠΌΠΌ.
ΠΡΠ»ΠΈ Π²Π΅ΡΡΠΈΠΊΠ°Π»ΡΠ½ΡΠ΅ ΡΡΠ°ΡΡΠΊΠΈ Π½Π΅Π·Π½Π°ΡΠΈΡΠ΅Π»ΡΠ½ΡΠ΅, ΡΠΎ ΠΈΡΠΏΠΎΠ»ΡΠ·ΡΡΡ Π½Π°Π½Π΅ΡΠ΅Π½ΠΈΠ΅ ΡΠΌΠ΅ΡΠΈ ΠΏΠΎ ΠΏΡΠΈΠ½ΡΠΈΠΏΡ ΠΎΡΡΡΠΊΠ°ΡΡΡΠΈΠ²Π°Π½ΠΈΡ. ΠΠΎΡΠΈΠ·ΠΎΠ½ΡΠ°Π»ΡΠ½ΠΎΠ΅ ΠΎΡΠ½ΠΎΠ²Π°Π½ΠΈΠ΅ Π²ΠΎΡΡΡΠ°Π½Π°Π²Π»ΠΈΠ²Π°ΡΡ ΠΌΠ΅ΡΠΎΠ΄ΠΎΠΌ ΠΎΠ±ΡΡΠ½ΠΎΠΉ ΡΡΡΠΆΠΊΠΈ.
ΠΠΎΡΠΌΠ°ΡΠΈΠ²Π½ΡΠ΅ ΡΡΠ΅Π±ΠΎΠ²Π°Π½ΠΈΡ
ΠΠ΅ΡΠ΅Π΄ Π½Π°ΡΠ°Π»ΠΎΠΌ ΡΡΡΠΎΠΈΡΠ΅Π»ΡΡΡΠ²Π° ΡΠ»Π΅Π΄ΡΠ΅Ρ ΠΎΠ·Π½Π°ΠΊΠΎΠΌΠΈΡΡΡΡ ΡΠΎ Π²ΡΠ΅ΠΌΠΈ ΡΡΡΠΎΠΈΡΠ΅Π»ΡΠ½ΡΠΌΠΈ Π½ΠΎΡΠΌΠ°ΠΌΠΈ ΠΈ ΠΏΡΠΈΠ΄Π΅ΡΠΆΠΈΠ²Π°ΡΡΡΡ ΠΈΡ
Π² ΠΏΡΠΎΡΠ΅ΡΡΠ΅ ΠΏΡΠΎΠΈΠ·Π²ΠΎΠ΄ΡΡΠ²Π°. ΠΡΠΈ ΠΎΠΏΡΠ΅Π΄Π΅Π»Π΅Π½ΠΈΠΈ ΠΎΠΏΡΠΈΠΌΠ°Π»ΡΠ½ΠΎΠΉ ΡΠΎΠ»ΡΠΈΠ½Ρ Π·Π°ΡΠΈΡΠ½ΠΎΠ³ΠΎ ΠΏΠ»Π°ΡΡΠ° Π½ΡΠΆΠ½ΠΎ ΡΡΠΊΠΎΠ²ΠΎΠ΄ΡΡΠ²ΠΎΠ²Π°ΡΡΡΡ Π²ΡΠ΅ΠΌΠΈ Π΄Π΅ΠΉΡΡΠ²ΡΡΡΠΈΠΌΠΈ ΡΡΠ΅Π±ΠΎΠ²Π°Π½ΠΈΡΠΌΠΈ, Π° Π½Π΅ ΠΈΡΠΏΠΎΠ»ΡΠ·ΠΎΠ²Π°ΡΡ ΡΠΎΠ»ΡΠΊΠΎ ΡΠ°ΡΡΠ΅Ρ Π΄ΠΈΠ°ΠΌΠ΅ΡΡΠ° ΠΏΡΡΡΠΊΠ°. ΠΠ½ Π½Π΅ ΡΡΠΈΡΡΠ²Π°Π΅Ρ ΡΠ°Π·Π»ΠΈΡΠ½ΡΠ΅ ΡΠ°ΠΊΡΠΎΡΡ ΠΈ Π±ΡΠ²Π°Π΅Ρ Π½Π΅ΡΠΎΡΠ½ΡΠΌ.
ΠΡΡΡΡΠΏΠ»Π΅Π½ΠΈΠ΅ ΠΎΡ Π½ΠΎΡΠΌ, ΠΏΡΠΎΠΏΠΈΡΠ°Π½Π½ΡΡ Π² Π΄ΠΎΠΊΡΠΌΠ΅Π½ΡΠ°Ρ , ΠΌΠΎΠΆΠ΅Ρ ΠΏΡΠΈΠ²Π΅ΡΡΠΈ ΠΊ ΠΏΡΠΎΠ±Π»Π΅ΠΌΠ°ΠΌ Π½Π΅ ΡΠΎΠ»ΡΠΊΠΎ ΠΏΠΎΡΠ»Π΅ ΠΎΠΊΠΎΠ½ΡΠ°Π½ΠΈΡ ΡΡΡΠΎΠΈΡΠ΅Π»ΡΡΡΠ²Π°, Π½ΠΎ ΠΈ Π²ΠΎ Π²ΡΠ΅ΠΌΡ Π½Π΅Π³ΠΎ. ΠΠ°ΡΡΡΠ°Π±Π½ΡΠ΅ ΡΡΡΠΎΠ΅Π½ΠΈΡ ΠΊΠΎΠ½ΡΡΠΎΠ»ΠΈΡΡΡΡΡΡ ΡΠΏΠ΅ΡΠΈΠ°Π»ΡΠ½ΡΠΌΠΈ ΠΎΡΠ³Π°Π½Π°ΠΌΠΈ, ΠΏΠΎΡΡΠΎΠΌΡ Π½Π΅ΡΠΎΠΎΡΠ²Π΅ΡΡΡΠ²ΠΈΠ΅ ΡΡΠ΅Π±ΠΎΠ²Π°Π½ΠΈΡΠΌ ΡΡΡΠΎΠΈΡΠ΅Π»ΡΠ½ΡΡ ΠΏΡΠ°Π²ΠΈΠ» ΠΏΠΎΠ²Π»Π΅ΡΠ΅Ρ Π·Π° ΡΠΎΠ±ΠΎΠΉ ΡΡΡΠ΅ΡΡΠ²Π΅Π½Π½ΡΠ΅ Π·Π°ΡΡΠ°ΡΡ. ΠΡΠΎΠΌΠ΅ ΡΠΎΠ³ΠΎ, ΠΎΡ Π²Π΅ΡΠ½ΡΡ Π΄Π΅ΠΉΡΡΠ²ΠΈΠΉ Π·Π°Π²ΠΈΡΠΈΡ ΡΡΠΎΠΊ ΡΠ»ΡΠΆΠ±Ρ Π²ΡΠ΅Π³ΠΎ ΡΠΎΠΎΡΡΠΆΠ΅Π½ΠΈΡ.
ΠΠ°ΡΠΈΡΠ½ΡΠΉ ΡΠ»ΠΎΠΉ Π±Π΅ΡΠΎΠ½Π° Π΄Π»Ρ Π°ΡΠΌΠ°ΡΡΡΡ Π² ΡΡΠ½Π΄Π°ΠΌΠ΅Π½ΡΠ΅
Π€ΡΠ½Π΄Π°ΠΌΠ΅Π½Ρ β ΠΎΡΠ½ΠΎΠ²Π° Π»ΡΠ±ΠΎΠ³ΠΎ Π·Π΄Π°Π½ΠΈΡ, ΠΎΡ ΠΊΠΎΡΠΎΡΠΎΠΉ Π·Π°Π²ΠΈΡΠΈΡ ΠΏΡΠΎΡΠ½ΠΎΡΡΡ ΠΈ Π΄ΠΎΠ»Π³ΠΎΠ²Π΅ΡΠ½ΠΎΡΡΡ Π²ΡΠ΅Π³ΠΎ ΡΡΡΠΎΠ΅Π½ΠΈΡ Π² ΡΠ΅Π»ΠΎΠΌ. Π’ΠΎ Π΅ΡΡΡ Π·Π½Π°ΡΠ΅Π½ΠΈΠ΅ ΡΡΠΎΠ³ΠΎ Β«Π½ΡΠ»Π΅Π²ΠΎΠ³ΠΎ ΡΠΈΠΊΠ»Π°Β» ΡΡΡΠΎΠΈΡΠ΅Π»ΡΡΡΠ²Π° β ΡΠ»ΠΎΠΆΠ½ΠΎ ΠΏΠ΅ΡΠ΅ΠΎΡΠ΅Π½ΠΈΡΡ: Π²ΡΡ Π΄ΠΎΠ»ΠΆΠ½ΠΎ Π±ΡΡΡ Π²ΡΠΏΠΎΠ»Π½Π΅Π½ΠΎ Π½Π° ΠΎΡΠ½ΠΎΠ²Π°Π½ΠΈΠΈ ΡΠ°ΡΡΠ΅ΡΠΎΠ² ΠΈ ΡΠΎ ΡΡΡΠΎΠ³ΠΈΠΌ ΡΠΎΠ±Π»ΡΠ΄Π΅Π½ΠΈΠ΅ΠΌ Π²ΡΠ΅Ρ ΡΡΡΠ°Π½ΠΎΠ²Π»Π΅Π½Π½ΡΡ ΠΏΡΠ°Π²ΠΈΠ».
ΠΠ°ΡΠΈΡΠ½ΡΠΉ ΡΠ»ΠΎΠΉ Π±Π΅ΡΠΎΠ½Π° Π΄Π»Ρ Π°ΡΠΌΠ°ΡΡΡΡ Π² ΡΡΠ½Π΄Π°ΠΌΠ΅Π½ΡΠ΅
ΠΡΠΎ Π²ΠΎΠ²ΡΠ΅ Π½Π΅ ΠΌΠ΅Π»ΠΎΡΡ, ΠΊΠ°ΠΊ ΠΌΠΎΠ³ΡΡ ΠΏΠΎΠ΄ΡΠΌΠ°ΡΡ Π½Π΅ΠΊΠΎΡΠΎΡΡΠ΅ Π½Π°ΡΠΈΠ½Π°ΡΡΠΈΠ΅ ΡΡΡΠΎΠΈΡΠ΅Π»ΠΈ. Π ΡΠΎΠ»ΡΠΈΠ½Π° ΡΡΠΎΠ³ΠΎ ΡΠ»ΠΎΡ ΡΠΎΠΆΠ΅ ΠΏΠΎΠ΄ΡΠΈΠ½ΡΠ΅ΡΡΡ ΠΎΠΏΡΠ΅Π΄Π΅Π»Π΅Π½Π½ΡΠΌ ΠΏΡΠ°Π²ΠΈΠ»Π°ΠΌ, ΠΎ ΠΊΠΎΡΠΎΡΡΡ ΠΊΠ°ΠΊ ΡΠ°Π· ΠΈ ΠΏΠΎΠΉΠ΄Π΅Ρ ΡΠ΅ΡΡ Π² Π½Π°ΡΡΠΎΡΡΠ΅ΠΉ ΠΏΡΠ±Π»ΠΈΠΊΠ°ΡΠΈΠΈ.
ΠΠ»Ρ ΡΠ΅Π³ΠΎ Π½Π΅ΠΎΠ±Ρ ΠΎΠ΄ΠΈΠΌ Π±Π΅ΡΠΎΠ½Π½ΡΠΉ Π·Π°ΡΠΈΡΠ½ΡΠΉ ΡΠ»ΠΎΠΉΠΡΠ»ΠΈ ΠΏΠΎΡΠΌΠΎΡΡΠ΅ΡΡ Π½Π° ΡΠ΅ΡΡΠ΅ΠΆΠΈ ΠΈΠ»ΠΈ ΡΠΎΡΠΎΠ³ΡΠ°ΡΠΈΠΈ ΠΏΡΠ°Π²ΠΈΠ»ΡΠ½ΠΎ ΡΠΌΠΎΠ½ΡΠΈΡΠΎΠ²Π°Π½Π½ΡΡ
Π°ΡΠΌΠΈΡΡΡΡΠΈΡ
ΠΊΠ°ΡΠΊΠ°ΡΠΎΠ² Π±ΡΠ΄ΡΡΠΈΡ
ΠΆΠ΅Π»Π΅Π·ΠΎΠ±Π΅ΡΠΎΠ½Π½ΡΡ
ΠΊΠΎΠ½ΡΡΡΡΠΊΡΠΈΠΉ, ΠΏΠΎΠ΄Π³ΠΎΡΠΎΠ²Π»Π΅Π½Π½ΡΡ
ΠΊ Π·Π°Π»ΠΈΠ²ΠΊΠ΅ ΡΠ°ΡΡΠ²ΠΎΡΠ°, ΡΠΎ ΠΌΠΎΠΆΠ½ΠΎ ΡΡΠ°Π·Ρ Π·Π°ΠΌΠ΅ΡΠΈΡΡ, ΡΡΠΎ Π°ΡΠΌΠ°ΡΡΡΠ½ΡΠ΅ ΠΏΡΡΡΡ Π½ΠΈΠΊΠΎΠ³Π΄Π° Π½Π΅ ΠΊΠ°ΡΠ°ΡΡΡΡ ΡΡΠ΅Π½ΠΎΠΊ ΠΎΠΏΠ°Π»ΡΠ±ΠΊΠΈ. Π’Π°ΠΊΠΈΠΌ ΠΎΠ±ΡΠ°Π·ΠΎΠΌ, ΠΏΠΎΡΠ»Π΅ Π·Π°ΠΏΠΎΠ»Π½Π΅Π½ΠΈΡ Π±Π΅ΡΠΎΠ½ΠΎΠΌ ΠΈ Π΅Π³ΠΎ ΡΠΎΠ·ΡΠ΅Π²Π°Π½ΠΈΡ ΠΌΠ΅ΠΆΠ΄Ρ ΠΌΠ΅ΡΠ°Π»Π»ΠΈΡΠ΅ΡΠΊΠΈΠΌΠΈ Π΄Π΅ΡΠ°Π»ΡΠΌΠΈ ΠΈ ΠΊΡΠ°Π΅ΠΌ ΠΊΠΎΠ½ΡΡΡΡΠΊΡΠΈΠΈ Π²ΡΠ΅Π³Π΄Π° ΠΏΠΎΠ»ΡΡΠ°Π΅ΡΡΡ ΠΏΡΠΎΡΠ»ΠΎΠΉΠΊΠ° ΠΎΠΏΡΠ΅Π΄Π΅Π»Π΅Π½Π½ΠΎΠΉ ΡΠΎΠ»ΡΠΈΠ½Ρ. ΠΠΌΠ΅Π½Π½ΠΎ ΠΎΠ½Π° Π² ΡΠ΅Ρ
Π½ΠΈΡΠ΅ΡΠΊΠΎΠΉ Π΄ΠΎΠΊΡΠΌΠ΅Π½ΡΠ°ΡΠΈΠΈ ΠΈ Π² ΠΏΡΠ°ΠΊΡΠΈΠΊΠ΅ ΡΡΡΠΎΠΈΡΠ΅Π»ΡΡΡΠ²Π° ΠΈ Π½Π°Π·ΡΠ²Π°Π΅ΡΡΡ Β«Π·Π°ΡΠΈΡΠ½ΡΠΌ ΡΠ»ΠΎΠ΅ΠΌΒ».
ΠΡΠΌΠΈΡΡΡΡΠΈΠΉ ΠΊΠ°ΡΠΊΠ°Ρ ΠΊΠΎΠΌΠΏΠ΅Π½ΡΠΈΡΡΠ΅Ρ Π½Π΅Π΄ΠΎΡΡΠ°ΡΠΎΠΊ Π±Π΅ΡΠΎΠ½Π° β Π½ΠΈΠ·ΠΊΡΡ ΠΏΡΠΎΡΠ½ΠΎΡΡΡ ΠΏΡΠΈ Π½Π°Π³ΡΡΠ·ΠΊΠ°Ρ Π½Π° ΡΠ°ΡΡΡΠΆΠ΅Π½ΠΈΠ΅ ΠΈΠ»ΠΈ ΠΈΠ·Π»ΠΎΠΌ. Π’ΠΎ Π΅ΡΡΡ Π½Π°Π΄ΡΠΆΠ½ΠΎΡΡΡ ΠΊΠΎΠ½ΡΡΡΡΠΊΡΠΈΠΈ Π² ΡΠ°Π²Π½ΠΎΠΉ ΠΌΠ΅ΡΠ΅ Π·Π°Π²ΠΈΡΠΈΡ ΠΈ ΠΎΡ ΠΊΠ°ΡΠ΅ΡΡΠ²Π° Π±Π΅ΡΠΎΠ½ΠΈΡΠΎΠ²Π°Π½ΠΈΡ, ΠΈ ΠΎΡ ΠΏΡΠ°Π²ΠΈΠ»ΡΠ½ΠΎΡΡΠΈ Π΅Π΅ Π°ΡΠΌΠΈΡΠΎΠ²Π°Π½ΠΈΡ.
Π‘Π°ΠΌΠΈ ΠΏΠΎ ΡΠ΅Π±Π΅ Π°ΡΠΌΠ°ΡΡΡΠ½ΡΠ΅ ΠΏΡΡΡΡ, ΠΈΠ·Π³ΠΎΡΠΎΠ²Π»Π΅Π½Π½ΡΠ΅ Π² ΡΠΎΠΎΡΠ²Π΅ΡΡΡΠ²ΠΈΠΈ Ρ ΠΠΠ‘Π’, ΠΎΠ±Π»Π°Π΄Π°ΡΡ Π½Π΅ΠΎΠ±Ρ ΠΎΠ΄ΠΈΠΌΡΠΌ Π·Π°ΠΏΠ°ΡΠΎΠΌ ΠΏΡΠΎΡΠ½ΠΎΡΡΠΈ ΠΈ ΡΠ°ΡΡΡΠΈΡΠ°Π½Ρ Π½Π° Π΄Π»ΠΈΡΠ΅Π»ΡΠ½ΡΡ ΡΠΊΡΠΏΠ»ΡΠ°ΡΠ°ΡΠΈΡ. ΠΠ΄Π½Π°ΠΊΠΎ, ΡΡΠ°Π»Ρ Π½Π΅ΡΡΡΠΎΠΉΡΠΈΠ²Π° ΠΊ Π²ΠΎΠ·Π΄Π΅ΠΉΡΡΠ²ΠΈΡ Π½Π° Π½Π΅Π΅ Ρ ΠΈΠΌΠΈΡΠ΅ΡΠΊΠΈΡ ΡΠΎΠ΅Π΄ΠΈΠ½Π΅Π½ΠΈΠΉ ΠΈ Π²Π»Π°Π³ΠΈ β ΠΎΡ ΠΊΠΎΡΡΠΎΠ·ΠΈΠΈ ΠΈΠ·Π±Π°Π²ΠΈΡΡΡΡ ΠΏΠΎΠ»Π½ΠΎΡΡΡΡ Π½Π΅ ΡΠ΄Π°Π΅ΡΡΡ. ΠΡ Π° Π΅ΡΠ»ΠΈ Π΄Π΅Π»Π°ΡΡ ΠΊΠ°ΡΠΊΠ°Ρ ΠΈΠ· ΠΌΠ΅ΡΠ°Π»Π»Π°, Π½Π΅ ΠΏΠΎΠ΄Π²Π΅ΡΠ³Π°ΡΡΠ΅Π³ΠΎΡΡ ΠΊΠΎΡΡΠΎΠ·ΠΈΠΈ, ΡΠΎ ΡΠ°ΠΊΠΎΠ΅ ΡΡΡΠΎΠΈΡΠ΅Π»ΡΡΡΠ²ΠΎ ΡΡΠ°Π½ΠΎΠ²ΠΈΡΡΡ ΡΡΠ΅Π·Π²ΡΡΠ°ΠΉΠ½ΠΎ Π΄ΠΎΡΠΎΠ³ΠΈΠΌ β Π½Π΅ΡΠ΅Π½ΡΠ°Π±Π΅Π»ΡΠ½ΡΠΌ.
Π¦Π΅Π½Ρ Π½Π° Π°ΡΠΌΠ°ΡΡΡΡ
Π°ΡΠΌΠ°ΡΡΡΠ°
ΠΠ»Ρ ΠΌΠ°ΠΊΡΠΈΠΌΠ°Π»ΡΠ½ΠΎ Π²ΠΎΠ·ΠΌΠΎΠΆΠ½ΠΎΠ³ΠΎ ΡΠ½ΠΈΠΆΠ΅Π½ΠΈΡ Π½Π΅Π³Π°ΡΠΈΠ²Π½ΠΎΠ³ΠΎ Π²Π»ΠΈΡΠ½ΠΈΡ Π½Π° ΠΌΠ΅ΡΠ°Π»Π» ΠΈΡΠΏΠΎΠ»ΡΠ·ΡΡΡΡΡ ΡΠΏΠΎΡΠΎΠ±Ρ Π°Π½ΡΠΈΠΊΠΎΡΡΠΎΠ·ΠΈΠΉΠ½ΠΎΠΉ ΠΎΠ±ΡΠ°Π±ΠΎΡΠΊΠΈ Π°ΡΠΌΠ°ΡΡΡΠ½ΠΎΠ³ΠΎ ΠΏΡΡΡΠ° β ΠΎΡΠΈΠ½ΠΊΠΎΠ²Π°Π½ΠΈΠ΅ΠΌ ΠΈ ΠΎΠΊΡΠΈΠ΄ΠΈΡΠΎΠ²Π°Π½ΠΈΠ΅ΠΌ. ΠΠΎ ΠΈ ΠΏΠΎΠ΄ΠΎΠ±Π½ΡΠΉ ΠΏΠΎΠ΄Ρ
ΠΎΠ΄ ΡΠΎΠΆΠ΅ Π΄Π΅ΡΠ΅Π²ΡΠΌ Π½Π΅ Π½Π°Π·ΠΎΠ²Π΅ΡΡ, Π΄Π° ΠΈ Π½Π΅ Π΄Π°Π΅Ρ ΠΎΠ½ Π°Π±ΡΠΎΠ»ΡΡΠ½ΠΎΠΉ Π·Π°ΡΡΡΠ°Ρ
ΠΎΠ²Π°Π½Π½ΠΎΡΡΠΈ ΠΎΡ Π²ΠΎΠ·Π½ΠΈΠΊΠ½ΠΎΠ²Π΅Π½ΠΈΡ ΠΊΠΎΡΡΠΎΠ·ΠΈΠΉΠ½ΡΡ
ΠΏΡΠΎΡΠ΅ΡΡΠΎΠ². ΠΡΠΎ ΡΠ²ΡΠ·Π°Π½ΠΎ Ρ ΡΠ΅ΠΌ, ΡΡΠΎ Π·Π°ΡΠΈΡΠ½Π°Ρ ΠΏΠ»Π΅Π½ΠΊΠ° Π½Π΅ ΠΎΠ±Π»Π°Π΄Π°Π΅Ρ ΡΠ»ΠΈΡΠΊΠΎΠΌ Π²ΡΡΠΎΠΊΠΎΠΉ ΠΏΡΠΎΡΠ½ΠΎΡΡΡΡ, ΡΠ°ΠΊ ΠΊΠ°ΠΊ Π΅Π΅ ΡΠΎΠ»ΡΠΈΠ½Π° ΡΠΎΡΡΠ°Π²Π»ΡΠ΅Ρ Π²ΡΠ΅Π³ΠΎ Π½Π΅ΡΠΊΠΎΠ»ΡΠΊΠΎ ΠΌΠΈΠΊΡΠΎΠ½. ΠΠΎΡΡΠΎΠΌΡ Π½Π΅Π°ΠΊΠΊΡΡΠ°ΡΠ½Π°Ρ ΡΡΠ°Π½ΡΠΏΠΎΡΡΠΈΡΠΎΠ²ΠΊΠ° ΠΈΠ»ΠΈ ΡΠ²Π°ΡΠΊΠ° Π»Π΅Π³ΠΊΠΎ Π½Π°ΡΡΡΠ°ΡΡ ΡΠ΅Π»ΠΎΡΡΠ½ΠΎΡΡΡ ΠΏΠΎΠΊΡΡΡΠΈΡ. Π’Π΅ΡΡΠ΅ΡΡΡ Π·Π°ΡΠΈΡΠ° ΠΈ Π½Π° ΡΠΎΡΡΠ°Ρ
Β Π² ΠΌΠ΅ΡΡΠ°Ρ
ΡΠ΅Π·Π° ΠΏΡΡΡΠΎΠ².
ΠΡΠ΅ ΠΎΠ΄Π½ΠΎΠΉ ΠΎΠΏΠ°ΡΠ½ΠΎΡΡΡΡ Π΄Π»Ρ Π·Π°ΡΠΈΡΠ½ΠΎΠ³ΠΎ ΡΠ»ΠΎΡ Π½Π° Π°ΡΠΌΠ°ΡΡΡΠ΅ ΡΠ²Π»ΡΡΡΡΡ Π½Π°ΠΏΠΎΠ»Π½ΠΈΡΠ΅Π»ΠΈ Π±Π΅ΡΠΎΠ½Π½ΠΎΠ³ΠΎ ΡΠ°ΡΡΠ²ΠΎΡΠ°, ΠΏΡΠ΅Π΄ΡΡΠ°Π²Π»ΡΡΡΠΈΠ΅ ΡΠΎΠ±ΠΎΠΉ ΡΠ΅Π±Π΅Π½Ρ ΠΈΠ»ΠΈ Π³ΡΠ°Π²ΠΈΠΉ. ΠΡΠΈ Π·Π°ΠΏΠΎΠ»Π½Π΅Π½ΠΈΠΈ ΠΎΠΏΠ°Π»ΡΠ±ΠΊΠΈ Ρ ΡΡΡΠ°Π½ΠΎΠ²Π»Π΅Π½Π½ΡΠΌ Π² Π½Π΅ΠΉ Π°ΡΠΌΠ°ΡΡΡΠ½ΡΠΌ ΠΊΠ°ΡΠΊΠ°ΡΠΎΠΌ Π³ΡΡΠ±ΡΠΌ Π±Π΅ΡΠΎΠ½Π½ΡΠΌ ΡΠ°ΡΡΠ²ΠΎΡΠΎΠΌ, ΠΎΡΡΡΡΠ΅ ΠΊΡΠ°Ρ ΠΊΠ°ΠΌΠ½Ρ Π»Π΅Π³ΠΊΠΎ ΠΏΠΎΠ²ΡΠ΅ΠΆΠ΄Π°ΡΡ Π³Π°Π»ΡΠ²Π°Π½ΠΈΡΠ΅ΡΠΊΠΈΠΉ ΠΈΠ»ΠΈ ΡΠΈΠ½ΠΊΠΎΠ²ΡΠΉ ΡΠ»ΠΎΠΉ.
Π ΡΠ°ΠΊ Π»ΠΈ ΠΎΠΏΠ°ΡΠ½Π° ΠΊΠΎΡΡΠΎΠ·ΠΈΡ Π°ΡΠΌΠ°ΡΡΡΠ½ΠΎΠ³ΠΎ ΠΊΠ°ΡΠΊΠ°ΡΠ°? ΠΠΎΠΆΠ΅Ρ, ΠΎΡΠΎΠ±ΠΎΠΉ Π±Π΅Π΄Ρ Π² ΡΡΠΎΠΌ ΠΈ Π½Π΅Ρ?
Π£Π²Ρ, Π½ΠΎ ΠΎΠΏΠ°ΡΠ½ΠΎΡΡΡ Π΄Π΅ΠΉΡΡΠ²ΠΈΡΠ΅Π»ΡΠ½ΠΎ Π²Π΅Π»ΠΈΠΊΠ°. Π Π΄Π΅Π»ΠΎ Π΄Π°ΠΆΠ΅ Π½Π΅ ΡΡΠΎΠ»ΡΠΊΠΎ Π² ΡΠΎΠΌ, ΡΡΠΎ ΡΠ°ΠΌΠΈ ΠΏΡΡΡΡ ΡΠ΅ΡΡΡΡ ΡΠ²ΠΎΠΈ ΠΏΡΠΎΡΠ½ΠΎΡΡΠ½ΡΠ΅ Ρ
Π°ΡΠ°ΠΊΡΠ΅ΡΠΈΡΡΠΈΠΊΠΈ β ΡΡΠΎΠ±Ρ ΡΠ°ΠΊΠ°Ρ ΠΏΠΎΡΠ΅ΡΡ ΡΡΠ°Π»Π° ΠΎΡΡΡΠΈΠΌΠΎΠΉ, ΠΏΠΎΡΡΠ΅Π±ΡΠ΅ΡΡΡ Π½Π΅ΠΌΠ°Π»ΠΎ Π²ΡΠ΅ΠΌΠ΅Π½ΠΈ (Ρ
ΠΎΡΡ ΠΈ ΡΡΠΎΡ Π°ΡΠΏΠ΅ΠΊΡ Π½Π΅Π»ΡΠ·Ρ ΡΠ±ΡΠ°ΡΡΠ²Π°ΡΡ ΡΠΎ ΡΡΠ΅ΡΠΎΠ²).
ΠΠΎ ΠΎΡΠ°Π³ΠΈ ΠΊΠΎΡΡΠΎΠ·ΠΈΠΈ Π²Π½ΡΡΡΠΈ ΠΆΠ΅Π»Π΅Π·ΠΎΠ±Π΅ΡΠΎΠ½Π½ΠΎΠΉ ΠΊΠΎΠ½ΡΡΡΡΠΊΡΠΈΠΈ Π½Π΅ΠΈΠ·Π±Π΅ΠΆΠ½ΠΎ Π²Π΅Π΄ΡΡ ΠΊ ΠΏΠΎΡΠ²Π»Π΅Π½ΠΈΡ Π²Π½ΡΡΡΠ΅Π½Π½ΠΈΡ ΠΏΡΡΡΠΎΡ. Π‘Π½Π°ΡΠ°Π»Π°, Π²ΡΠΎΠ΄Π΅ Π±Ρ, Π½Π΅Π±ΠΎΠ»ΡΡΠΈΡ , Π½ΠΎ Π΄ΠΎΠ²ΠΎΠ»ΡΠ½ΠΎ Π±ΡΡΡΡΠΎ ΡΠ°ΡΡΠΈΡΡΡΡΠΈΡ ΡΡ, ΠΏΡΠ΅Π²ΡΠ°ΡΠ°ΡΡΠΈΡ ΡΡ Π² ΡΡΠ΅ΡΠΈΠ½Ρ, ΠΊΠΎΡΠΎΡΡΠ΅ ΠΏΠΎΠ΄ Π΄Π΅ΠΉΡΡΠ²ΠΈΠ΅ΠΌ Π²Π»Π°Π³ΠΈ ΠΈ ΠΎΡΡΠΈΡΠ°ΡΠ΅Π»ΡΠ½ΡΡ ΡΠ΅ΠΌΠΏΠ΅ΡΠ°ΡΡΡ ΠΏΡΠΈΠ²ΠΎΠ΄ΡΡ ΠΊ ΡΡΠΎΠ·ΠΈΠΈ, ΡΠ°Π·ΡΡΡΠ΅Π½ΠΈΡ, ΠΎΡΡΠΏΠ°Π½ΠΈΡ Π±Π΅ΡΠΎΠ½Π°. Π Π²ΠΎΡ ΡΡΠΎ ΡΠΆΠ΅ β Π±Π΅Π΄Π° ΡΠ΅ΡΡΠ΅Π·Π½Π°Ρ, ΡΡΠ΅Π±ΡΡΡΠ°Ρ ΠΏΡΠΈΠ½ΡΡΠΈΡ ΡΡΠΎΡΠ½ΡΡ ΠΌΠ΅Ρ.
ΠΠΎΡΡΠΎΠ·ΠΈΡ Π°ΡΠΌΠ°ΡΡΡΠ½ΠΎΠ³ΠΎ ΠΊΠ°ΡΠΊΠ°ΡΠ° ΠΏΡΠΈΠ²ΠΎΠ΄ΠΈΡ Π½Π΅ ΡΠΎΠ»ΡΠΊΠΎ ΠΊ ΡΠ½ΠΈΠΆΠ΅Π½ΠΈΡ ΠΏΡΠΎΡΠ½ΠΎΡΡΠ½ΡΡ Ρ Π°ΡΠ°ΠΊΡΠ΅ΡΠΈΡΡΠΈΠΊ ΡΡΠ°Π»ΡΠ½ΡΡ ΠΏΡΡΡΠΎΠ², Π½ΠΎ Π΄ΠΎΠ²ΠΎΠ»ΡΠ½ΠΎ Π±ΡΡΡΡΠΎ ΠΌΠΎΠΆΠ΅Ρ ΠΏΡΠΎΡΠ²ΠΈΡΡΡΡ ΡΡΠΎΠ·ΠΈΠ΅ΠΉ ΠΈ ΡΠ°Π·ΡΡΡΠ΅Π½ΠΈΠ΅ΠΌ ΠΏΠΎΠ²Π΅ΡΡ Π½ΠΎΡΡΠ½ΠΎΠ³ΠΎ ΡΠ»ΠΎΡ Π²ΡΠ΅ΠΉ ΠΆΠ΅Π»Π΅Π·ΠΎΠ±Π΅ΡΠΎΠ½Π½ΠΎΠΉ ΠΊΠΎΠ½ΡΡΡΡΠΊΡΠΈΠΈΠΠΎΡΡΠΎΠΌΡ Π°ΡΠΌΠ°ΡΡΡΠ½ΡΠΉ ΠΊΠ°ΡΠΊΠ°Ρ, Π½Π°Ρ
ΠΎΠ΄ΡΡΠΈΠΉΡΡ Π²Π½ΡΡΡΠΈ Π±Π΅ΡΠΎΠ½Π½ΠΎΠ³ΠΎ ΠΌΠΎΠ½ΠΎΠ»ΠΈΡΠ°, Π½Π΅ΠΎΠ±Ρ
ΠΎΠ΄ΠΈΠΌΠΎ Π² ΠΌΠ°ΠΊΡΠΈΠΌΠ°Π»ΡΠ½ΠΎΠΉ ΡΡΠ΅ΠΏΠ΅Π½ΠΈ ΠΎΡΠ³ΠΎΡΠΎΠ΄ΠΈΡΡ ΠΎΡ ΠΏΡΠΎΠ½ΠΈΠΊΠ½ΠΎΠ²Π΅Π½ΠΈΡ ΠΊ Π½Π΅ΠΌΡ Π²Π»Π°Π³ΠΈ Π² Π»ΡΠ±ΠΎΠΌ Π²ΠΈΠ΄Π΅. ΠΠ΅ΠΎΠ±Ρ
ΠΎΠ΄ΠΈΠΌ Π±Π°ΡΡΠ΅Ρ ΠΎΡ Π°Π³ΡΠ΅ΡΡΠΈΠ²Π½ΠΎΠ³ΠΎ Π²ΠΎΠ·Π΄Π΅ΠΉΡΡΠ²ΠΈΡ ΡΠ°Π·Π»ΠΈΡΠ½ΡΡ
Ρ
ΠΈΠΌΠΈΡΠ΅ΡΠΊΠΈΡ
ΡΠ°ΡΡΠ²ΠΎΡΠΎΠ², ΠΎΠ±ΡΠ°Π·ΡΡΡΠΈΡ
ΡΡ Π²ΡΠ»Π΅Π΄ΡΡΠ²ΠΈΠ΅ ΡΡΠ°Π²ΡΠ΅Π³ΠΎ ΡΠΆΠ΅ ΠΎΠ±ΡΠ΄Π΅Π½Π½ΡΠΌ ΡΠ²Π»Π΅Π½ΠΈΠ΅ΠΌ ΡΠ΅Ρ
Π½ΠΎΠ³Π΅Π½Π½ΠΎΠ³ΠΎ Π·Π°Π³ΡΡΠ·Π½Π΅Π½ΠΈΡ Π²ΠΎΠ·Π΄ΡΡ
Π° ΠΈ Π³ΡΡΠ½ΡΠ°. ΠΡΡΠ°ΡΠΈ, Π½Π΅ΠΌΠ°Π»ΡΡ ΡΠΎΠ»Ρ Π² Π½Π΅ΠΉΡΡΠ°Π»ΠΈΠ·Π°ΡΠΈΠΈ ΠΏΡΠΎΡΠ΅ΡΡΠΎΠ² Ρ
ΠΈΠΌΠΈΡΠ΅ΡΠΊΠΎΠΉ ΠΊΠΎΡΡΠΎΠ·ΠΈΠΈ ΠΈΠ³ΡΠ°Π΅Ρ ΡΠ΅Π»ΠΎΡΠ½Π°Ρ ΡΡΠ΅Π΄Π°, ΠΏΡΠΈΡΡΡΠ°Ρ Π±Π΅ΡΠΎΠ½Ρ.
ΠΠΎΡ Π² ΡΠΎΠ»ΠΈ ΡΠ°ΠΊΠΎΠΉ ΠΏΡΠ΅Π³ΡΠ°Π΄Ρ ΠΈ Π²ΡΡΡΡΠΏΠ°Π΅Ρ ΠΏΡΠΎΡΠ»ΠΎΠΉΠΊΠ°, Π½Π°Π·ΡΠ²Π°Π΅ΠΌΠ°Ρ Β«Π·Π°ΡΠΈΡΠ½ΡΠΉ Π±Π΅ΡΠΎΠ½Π½ΡΠΉ ΡΠ»ΠΎΠΉΒ». ΠΠΎ ΡΡΠΈΠΌ Π΅Π΅ ΡΡΠ½ΠΊΡΠΈΠΈ Π½Π΅ ΠΎΠ³ΡΠ°Π½ΠΈΡΠΈΠ²Π°ΡΡΡΡ. ΠΠΎ ΡΡΡΠΈ, ΠΏΡΠ°Π²ΠΈΠ»ΡΠ½ΠΎ ΡΠΎΠ·Π΄Π°Π½Π½Π°Ρ ΠΏΡΠΎΡΠ»ΠΎΠΉΠΊΠ° ΠΎΠ±Π΅ΡΠΏΠ΅ΡΠΈΠ²Π°Π΅Ρ ΡΡΠ°Π±ΠΈΠ»ΡΠ½ΡΡ ΠΊΠΎΠΌΠΏΠ»Π΅ΠΊΡΠ½ΡΡ Β«ΡΠ°Π±ΠΎΡΡΒ» ΡΡΠ°Π»ΡΠ½ΠΎΠ³ΠΎ ΠΏΡΡΡΠ° ΠΈ Π±Π΅ΡΠΎΠ½Π°.
Π¦Π΅Π½Ρ Π½Π° ΡΠ΅ΠΌΠ΅Π½Ρ
ΡΠ΅ΠΌΠ΅Π½Ρ
ΠΡΠ°ΠΊ, Π·Π°ΡΠΈΡΠ½ΡΠΉ Π±Π΅ΡΠΎΠ½Π½ΡΠΉ ΡΠ»ΠΎΠΉ Π²ΡΠΏΠΎΠ»Π½ΡΠ΅Ρ ΡΠ»Π΅Π΄ΡΡΡΠΈΠ΅ ΡΡΠ½ΠΊΡΠΈΠΈ:
- ΠΠ±Π΅ΡΠΏΠ΅ΡΠΈΠ²Π°Π΅Ρ ΡΡΠ΅Π±ΡΠ΅ΠΌΠΎΠ΅ ΠΏΠΎΠ·ΠΈΡΠΈΠΎΠ½ΠΈΡΠΎΠ²Π°Π½ΠΈΠ΅ Π°ΡΠΌΠ°ΡΡΡΠ½ΠΎΠ³ΠΎ ΠΊΠ°ΡΠΊΠ°ΡΠ° Π²Π½ΡΡΡΠΈ Π±Π΅ΡΠΎΠ½Π½ΠΎΠ³ΠΎ ΠΌΠ°ΡΡΠΈΠ²Π°.
- Π‘ΠΏΠΎΡΠΎΠ±ΡΡΠ²ΡΠ΅Ρ ΡΠ°Π²Π½ΠΎΠΌΠ΅ΡΠ½ΠΎΠΌΡ ΡΠ°ΡΠΏΡΠ΅Π΄Π΅Π»Π΅Π½ΠΈΡ Π½Π°Π³ΡΡΠ·ΠΊΠΈ Π½Π° Π°ΡΠΌΠ°ΡΡΡΡ ΠΈ ΠΎΡΠ½ΠΎΠ²Π½ΡΡ ΠΌΠ°ΡΡΡ Π±Π΅ΡΠΎΠ½Π°.
- ΠΠ°ΡΠΈΡΠ°Π΅Ρ ΠΌΠ΅ΡΠ°Π»Π» ΠΎΡ Π²Π»Π°Π³ΠΈ, Ρ ΠΈΠΌΠΈΡΠ΅ΡΠΊΠΈΡ ΡΠ΅Π°Π³Π΅Π½ΡΠΎΠ², ΠΈΠ½ΡΡ Π½Π΅Π³Π°ΡΠΈΠ²Π½ΡΡ Π²Π½Π΅ΡΠ½ΠΈΡ Π²ΠΎΠ·Π΄Π΅ΠΉΡΡΠ²ΠΈΠΉ, Π²ΠΎΠ·Π½ΠΈΠΊΠ°ΡΡΠΈΡ ΠΏΡΠΈ ΡΠ΅Π·ΠΎΠ½Π½ΡΡ ΠΈΠ·ΠΌΠ΅Π½Π΅Π½ΠΈΡΡ ΠΏΠΎΠ³ΠΎΠ΄Π½ΡΡ ΡΡΠ»ΠΎΠ²ΠΈΠΉ.
- Π‘ΠΎΠ·Π΄Π°ΡΡ Π²ΠΎΠ·ΠΌΠΎΠΆΠ½ΠΎΡΡΡ ΠΊΠ°ΡΠ΅ΡΡΠ²Π΅Π½Π½ΠΎΠΉ Π°Π½ΠΊΠ΅ΡΠΎΠ²ΠΊΠΈ (Π·Π°ΠΊΡΠ΅ΠΏΠ»Π΅Π½ΠΈΡ) Π°ΡΠΌΠ°ΡΡΡΡ Π² Π±Π΅ΡΠΎΠ½Π΅ Π΄Π»Ρ ΠΎΠ±ΡΡΡΡΠΎΠΉΡΡΠ²Π° ΡΡΡΠΊΠΎΠ²ΠΊΠΈ Π°ΡΠΌΠ°ΡΡΡΠ½ΡΡ ΠΊΠ°ΡΠΊΠ°ΡΠΎΠ² ΡΠΎΡΠ΅Π΄Π½ΠΈΡ ΠΆ/Π±-ΠΊΠΎΠ½ΡΡΡΡΠΊΡΠΈΠΉ ΠΈΠ»ΠΈ ΠΏΠ΅ΡΠ΅Ρ ΠΎΠ΄ΠΎΠ² Π½Π° Π΄ΡΡΠ³ΠΎΠΉ ΡΡΠΎΠ²Π΅Π½Ρ.
- ΠΠ½Π°ΡΠΈΡΠ΅Π»ΡΠ½ΠΎ ΠΏΠΎΠ²ΡΡΠ°Π΅Ρ ΠΎΠ³Π½Π΅ΡΡΠΎΠΉΠΊΠΎΡΡΡ ΠΆΠ΅Π»Π΅Π·ΠΎΠ±Π΅ΡΠΎΠ½Π½ΠΎΠΉ ΠΊΠΎΠ½ΡΡΡΡΠΊΡΠΈΠΈ.
- Π‘Π»ΡΠΆΠΈΡ Π½Π°Π΄Π΅ΠΆΠ½ΡΠΌ ΠΎΡΠ½ΠΎΠ²Π°Π½ΠΈΠ΅ΠΌ Π΄Π»Ρ ΠΏΠΎΡΠ»Π΅Π΄ΡΡΡΠ΅Π³ΠΎ ΠΌΠΎΠ½ΡΠ°ΠΆΠ° Π΄ΠΎΠΏΠΎΠ»Π½ΠΈΡΠ΅Π»ΡΠ½ΠΎΠΉ Π·Π°ΡΠΈΡΡ (Π³ΠΈΠ΄ΡΠΎβ ΠΈ ΡΠ΅ΡΠΌΠΎΠΈΠ·ΠΎΠ»ΡΡΠΈΠΈ), Π½Π° Π½Π°Π΄Π·Π΅ΠΌΠ½ΡΡ
ΡΡΠ°ΡΡΠΊΠ°Ρ
ΡΡΠ½Π΄Π°ΠΌΠ΅Π½ΡΠ° β ΡΠΎΠΊΠΎΠ»ΡΠ½ΠΎΠΉ ΠΎΡΠ΄Π΅Π»ΠΊΠΈ.
Π’ΠΎΠ»ΡΠΈΠ½Π° ΡΡΠΎΠ³ΠΎ Π·Π°ΡΠΈΡΠ½ΠΎΠ³ΠΎ ΡΠ»ΠΎΡ Π±Π΅ΡΠ΅ΡΡΡ Β«Π½Π΅ Ρ ΠΏΠΎΡΠΎΠΊΠ°Β». ΠΡΠ»ΠΈ ΠΎΠ½Π° Π±ΡΠ΄Π΅Ρ ΠΌΠ΅Π½ΡΡΠ΅ ΡΡΡΠ°Π½ΠΎΠ²Π»Π΅Π½Π½ΠΎΠΉ Π½ΠΎΡΠΌΠ°ΡΠΈΠ²Π°ΠΌΠΈ, ΡΠΎ ΠΌΠ΅ΡΠ°Π»Π» Π²ΡΠ΅ ΡΠ°Π²Π½ΠΎ Π½Π°ΡΠ½Π΅Ρ ΠΏΠΎΡΡΠ΅ΠΏΠ΅Π½Π½ΠΎ ΡΠ°Π·ΡΡΡΠ°ΡΡΡΡ ΠΊΠΎΡΡΠΎΠ·ΠΈΠ΅ΠΉ. Π ΡΠΎ ΠΆΠ΅ Π²ΡΠ΅ΠΌΡ Π²ΡΠ΄Π΅ΡΠΆΠΈΠ²Π°ΡΡ Π΅Π΅ ΡΡΠ΅Π·ΠΌΠ΅ΡΠ½ΠΎ Π±ΠΎΠ»ΡΡΠΎΠΉ (Π½Π΅ Π½Π°ΡΡΡΠ°Ρ ΠΏΡΠΈ ΡΡΠΎΠΌ ΡΠ°ΡΡΠ΅ΡΠ½ΡΡ ΡΠ°Π·ΠΌΠ΅ΡΠ½ΡΡ ΠΏΠ°ΡΠ°ΠΌΠ΅ΡΡΠΎΠ² Π°ΡΠΌΠ°ΡΡΡΠ½ΠΎΠ³ΠΎ ΠΊΠ°ΡΠΊΠ°ΡΠ°) β Π²ΠΎΠ·ΡΠ°ΡΡΡΡ ΠΎΠ±ΡΠΈΠ΅ Π·Π°ΡΡΠ°ΡΡ Π½Π° ΡΡΡΠΎΠΈΡΠ΅Π»ΡΠ½ΡΠ΅ ΠΌΠ°ΡΠ΅ΡΠΈΠ°Π»Ρ. ΠΠΎΡΡΠΎΠΌΡ, Π½Π΅ΠΎΠ±Ρ ΠΎΠ΄ΠΈΠΌΠΎ Π²ΡΠ±ΡΠ°ΡΡ Π΅Π΄ΠΈΠ½ΡΡΠ²Π΅Π½Π½ΠΎ Π²Π΅ΡΠ½ΡΠΉ Π²Π°ΡΠΈΠ°Π½Ρ ΡΡΠΎΠ³ΠΎ ΠΏΠ°ΡΠ°ΠΌΠ΅ΡΡΠ°, ΠΊΠΎΡΠΎΡΡΠΉ, ΠΊΠ°ΠΊ Π³ΠΎΠ²ΠΎΡΠΈΠ»ΠΎΡΡ Π²ΡΡΠ΅, Π½ΠΎΡΠΌΠΈΡΡΠ΅ΡΡΡ Π‘ΠΠΈΠ.
ΠΠ°Π²ΠΈΡΠΈΡ ΡΠΎΠ»ΡΠΈΠ½Π° Π·Π°ΡΠΈΡΠ½ΠΎΠ³ΠΎ ΡΠ»ΠΎΡ ΠΎΡ ΡΠ»Π΅Π΄ΡΡΡΠΈΡ ΠΌΠΎΠΌΠ΅Π½ΡΠΎΠ²:
- ΠΠΈΠ°ΠΌΠ΅ΡΡ ΠΈ ΡΠΈΠΏ Π°ΡΠΌΠ°ΡΡΡΠ½ΠΎΠ³ΠΎ ΠΏΡΡΡΠ°. Π§Π΅ΠΌ Π±ΠΎΠ»ΡΡΠ΅ ΡΠ°Π·ΠΌΠ΅Ρ ΠΏΡΡΡΠ° Π² ΡΠ΅ΡΠ΅Π½ΠΈΠΈ, ΡΠ΅ΠΌ ΡΠΎΠ»ΡΠ΅ Π΄ΠΎΠ»ΠΆΠ΅Π½ Π±ΡΡΡ Π·Π°ΡΠΈΡΠ½ΡΠΉ ΡΠ»ΠΎΠΉ
- Π‘ΠΈΠ»Π° ΠΈ Ρ Π°ΡΠ°ΠΊΡΠ΅Ρ ΠΌΠ΅Ρ Π°Π½ΠΈΡΠ΅ΡΠΊΠΎΠΉ Π½Π°Π³ΡΡΠ·ΠΊΠΈ Π½Π° ΡΡΠ½Π΄Π°ΠΌΠ΅Π½Ρ.
- Π£ΡΠ»ΠΎΠ²ΠΈΡ ΠΎΠΊΡΡΠΆΠ°ΡΡΠ΅ΠΉ ΡΡΠ΅Π΄Ρ, Π² ΠΊΠΎΡΠΎΡΡΠ΅ Π±ΡΠ΄Π΅Ρ ΡΠΊΡΠΏΠ»ΡΠ°ΡΠΈΡΠΎΠ²Π°ΡΡΡΡ ΠΊΠΎΠ½ΡΡΡΡΠΊΡΠΈΡ. ΠΠ°ΠΏΡΠΈΠΌΠ΅Ρ, Π΅ΡΠ»ΠΈ ΡΡΠ½Π΄Π°ΠΌΠ΅Π½Ρ ΡΡΡΠ°Π½Π°Π²Π»ΠΈΠ²Π°Π΅ΡΡΡ Π½Π° Π²Π»Π°ΠΆΠ½ΡΡ
ΠΏΠΎΡΠ²Π°Ρ
, Π½Π΅ΠΎΠ±Ρ
ΠΎΠ΄ΠΈΠΌΠ° Π½Π°Π΄Π΅ΠΆΠ½Π°Ρ Π³ΠΈΠ΄ΡΠΎΠΈΠ·ΠΎΠ»ΡΡΠΈΡ ΠΊΠΎΠ½ΡΡΡΡΠΊΡΠΈΠΈ. Π Π² ΡΡΠΎΠΌ ΡΠ»ΡΡΠ°Π΅ ΡΠΎΠ»ΡΠΈΠ½Π° Π·Π°ΡΠΈΡΠ½ΠΎΠ³ΠΎ Π±Π΅ΡΠΎΠ½Π½ΠΎΠ³ΠΎ ΡΠ»ΠΎΡ Π΄ΠΎΠ»ΠΆΠ½Π° Π±ΡΡΡ ΠΌΠ°ΠΊΡΠΈΠΌΠ°Π»ΡΠ½ΠΎ Π΄ΠΎΠΏΡΡΡΠΈΠΌΠΎΠΉ. ΠΠΎΠ»Π΅Π΅ ΠΏΠΎΠ΄ΡΠΎΠ±Π½Π°Ρ ΠΈΠ½ΡΠΎΡΠΌΠ°ΡΠΈΡ, ΠΊΠ°ΡΠ°ΡΡΠ°ΡΡΡ Π²ΠΎΠ·Π΄Π΅ΠΉΡΡΠ²ΠΈΡ Π½Π° ΠΆΠ΅Π»Π΅Π·ΠΎΠ±Π΅ΡΠΎΠ½Π½ΡΡ ΠΊΠΎΠ½ΡΡΡΡΠΊΡΠΈΡ Π²Π½Π΅ΡΠ½ΠΈΡ
Π°Π³ΡΠ΅ΡΡΠΈΠ²Π½ΡΡ
ΡΡΠ΅Π΄, Π½Π°Ρ
ΠΎΠ΄ΠΈΡΡΡ Π² Π‘ΠΠΈΠ 2.
03.11β85 Β«ΠΠ°ΡΠΈΡΠ° ΡΡΡΠΎΠΈΡΠ΅Π»ΡΠ½ΡΡ ΠΊΠΎΠ½ΡΡΡΡΠΊΡΠΈΠΉ ΠΎΡ ΠΊΠΎΡΡΠΎΠ·ΠΈΠΈΒ» Π² ΠΏΡΠ½ΠΊΡΠ°Ρ 2.18.- 2.29. ΠΈ ΡΠ°Π±Π»ΠΈΡΠ°Ρ β 9β11.
ΠΠΎΠ·Π°Π±ΠΎΡΡΡΠ΅ΡΡ ΠΎ ΡΡΠ½Π΄Π°ΠΌΠ΅Π½ΡΠ΅ β ΠΎΠ½ ΡΡΠ΅Π±ΡΠ΅Ρ ΡΡΠ΅ΠΏΠ»Π΅Π½ΠΈΡ ΠΈ Π³ΠΈΠ΄ΡΠΎΠΈΠ·ΠΎΠ»ΡΡΠΈΠΈ!
Π ΡΠΎΠΆΠ°Π»Π΅Π½ΠΈΡ, ΠΎΡΠ΅Π½Ρ ΠΌΠ½ΠΎΠ³ΠΈΠ΅ Π½Π΅ΠΎΠΏΡΡΠ½ΡΠ΅ ΡΡΡΠΎΠΈΡΠ΅Π»ΠΈ ΠΈΠ³Π½ΠΎΡΠΈΡΡΡΡ Π²ΠΎΠΏΡΠΎΡΡ Π΄ΠΎΠΏΠΎΠ»Π½ΠΈΡΠ΅Π»ΡΠ½ΠΎΠΉ Π·Π°ΡΠΈΡΡ ΠΎΡΠ½ΠΎΠ²Π°Π½ΠΈΡ Π΄ΠΎΠΌΠ° ΠΎΡ Π²ΠΎΠ·Π΄Π΅ΠΉΡΡΠ²ΠΈΡ Π²Π»Π°Π³ΠΈ ΠΈ ΠΎΡΡΠΈΡΠ°ΡΠ΅Π»ΡΠ½ΡΡ ΡΠ΅ΠΌΠΏΠ΅ΡΠ°ΡΡΡ. Π§ΡΠΎΠ±Ρ ΠΎΠ±Π΅ΡΠΏΠ΅ΡΠΈΡΡ ΠΌΠ°ΠΊΡΠΈΠΌΠ°Π»ΡΠ½ΡΡ Π΄ΠΎΠ»Π³ΠΎΠ²Π΅ΡΠ½ΠΎΡΡΡ Π·Π΄Π°Π½ΠΈΡ ΠΈ ΠΊΠΎΠΌΡΠΎΡΡΠ½ΠΎΡΡΡ ΠΏΡΠΎΠΆΠΈΠ²Π°Π½ΠΈΡ Π² Π½Π΅ΠΌ Π½Π΅ΠΎΠ±Ρ ΠΎΠ΄ΠΈΠΌΠΎ ΠΏΡΠΎΠ²Π΅ΡΡΠΈ ΠΊΠΎΠΌΠΏΠ»Π΅ΠΊΡ ΡΠ°Π±ΠΎΡ ΠΏΠΎ Π³ΠΈΠ΄ΡΠΎΠΈΠ·ΠΎΠ»ΡΡΠΈΠΈ ΡΡΠ½Π΄Π°ΠΌΠ΅Π½ΡΠ° ΡΠ΅ΠΌ ΠΈΠ»ΠΈ ΠΈΠ½ΡΠΌ ΡΠΏΠΎΡΠΎΠ±ΠΎΠΌ, Π° Π·Π°ΡΠ΅ΠΌ Π²ΡΠΏΠΎΠ»Π½ΠΈΡΡ ΠΈ ΡΡΠ΅ΠΏΠ»Π΅Π½ΠΈΠ΅ ΡΡΠ½Π΄Π°ΠΌΠ΅Π½ΡΠ°. ΠΠ±ΠΎ Π²ΡΠ΅ΠΌ ΡΡΠΎΠΌ β Π² ΡΠΏΠ΅ΡΠΈΠ°Π»ΡΠ½ΡΡ ΠΏΡΠ±Π»ΠΈΠΊΠ°ΡΠΈΡΡ Π½Π°ΡΠ΅Π³ΠΎ ΠΏΠΎΡΡΠ°Π»Π°.
- Π’ΠΈΠΏ ΡΡΡΠΎΠ΅Π½ΠΈΡ ΠΈΠ»ΠΈ ΠΎΡΠ΄Π΅Π»ΡΠ½ΠΎ ΡΠ°ΡΠΏΠΎΠ»ΠΎΠΆΠ΅Π½Π½ΠΎΠ³ΠΎ ΠΆΠ΅Π»Π΅Π·ΠΎΠ±Π΅ΡΠΎΠ½Π½ΠΎΠ³ΠΎ ΠΈΠ·Π΄Π΅Π»ΠΈΡ. Π Π°Π·ΠΌΠ΅ΡΡ ΡΠ»ΠΎΡ Π΄Π»Ρ ΠΊΠ°ΠΆΠ΄ΠΎΠ³ΠΎ ΠΈΠ· ΡΠΈΠΏΠΎΠ² Π½ΠΎΡΠΌΠΈΡΡΡΡΡΡ ΡΠΏΠ΅ΡΠΈΠ°Π»ΡΠ½ΡΠΌΠΈ Π΄ΠΎΠΊΡΠΌΠ΅Π½ΡΠ°ΠΌΠΈ.
- Π’Π΅Ρ
Π½ΠΈΡΠ΅ΡΠΊΠΈΠ΅ ΡΠΊΡΠΏΠ»ΡΠ°ΡΠ°ΡΠΈΠΎΠ½Π½ΡΠ΅ ΡΡΠ»ΠΎΠ²ΠΈΡ. Π Π°ΡΠΌΠ°ΡΡΡΠ½ΠΎΠΌ ΠΏΡΡΡΠ΅, ΠΈΡΠΏΠΎΠ»ΡΠ·ΡΠ΅ΠΌΠΎΠΌ Π² ΠΊΠΎΠ½ΡΡΡΡΠΊΡΠΈΡΡ
Ρ Π±ΠΎΠ»ΡΡΠΎΠΉ Π½Π°Π³ΡΡΠ·ΠΊΠΎΠΉ, Π²ΠΎΠ·Π½ΠΈΠΊΠ°Π΅Ρ Π±ΠΎΠ»ΡΡΠ΅Π΅ Π½Π°ΠΏΡΡΠΆΠ΅Π½ΠΈΠ΅, ΡΠ΅ΠΌ Π² ΡΠ΅Ρ
, ΠΊΠΎΡΠΎΡΡΠ΅ ΠΈΠΌΠ΅ΡΡ Π½Π΅Π·Π½Π°ΡΠΈΡΠ΅Π»ΡΠ½ΡΡ Π½Π°Π³ΡΡΠ·ΠΊΡ.
Π‘ΡΠ°Π»ΠΎ Π±ΡΡΡ, ΠΈ Π·Π°ΡΠΈΡΠ° Π΄Π»Ρ Π½Π΅Π³ΠΎ Π΄ΠΎΠ»ΠΆΠ½Π° Π±ΡΡΡ Π±ΠΎΠ»Π΅Π΅ ΠΏΠΎΠ»Π½ΠΎΡΠ΅Π½Π½ΠΎΠΉ.
- Π€ΡΠ½ΠΊΡΠΈΠΎΠ½Π°Π»ΡΠ½Π°Ρ Π½Π°Π³ΡΡΠ·ΠΊΠ° Π½Π° ΠΌΠ΅ΡΠ°Π»Π»ΠΈΡΠ΅ΡΠΊΠΈΠ΅ ΠΈΠ·Π΄Π΅Π»ΠΈΡ. ΠΡΠΌΠ°ΡΡΡΠ° Π² ΠΊΠ°ΡΠΊΠ°ΡΠ΅ ΠΌΠΎΠΆΠ΅Ρ Π±ΡΡΡ ΠΊΠΎΠ½ΡΡΡΡΠΊΡΠΈΠ²Π½ΠΎΠΉ, ΡΠ°ΡΠΏΡΠ΅Π΄Π΅Π»ΠΈΡΠ΅Π»ΡΠ½ΠΎΠΉ ΠΈΠ»ΠΈ ΠΆΠ΅ ΡΠ°Π±ΠΎΡΠ΅ΠΉ. ΠΠ°ΠΆΠ΄ΡΠΉ ΡΠΈΠΏ ΠΏΡΡΡΠ° ΠΌΠΎΠ½ΡΠΈΡΡΠ΅ΡΡΡ Π² ΠΊΠ°ΡΠΊΠ°Ρ ΡΠΎΠΎΡΠ²Π΅ΡΡΡΠ²Π΅Π½Π½ΠΎ ΡΠ΅ΠΊΠΎΠΌΠ΅Π½Π΄Π°ΡΠΈΡΠΌ, Π΄Π°Π½Π½ΡΠΌ Π² Π½ΠΎΡΠΌΠ°ΡΠΈΠ²Π½ΡΡ Π΄ΠΎΠΊΡΠΌΠ΅Π½ΡΠ°Ρ ΠΏΠΎ Π²ΠΎΠ·Π²Π΅Π΄Π΅Π½ΠΈΡ ΠΈ ΠΎΠ±ΡΡΡΡΠΎΠΉΡΡΠ²Ρ ΠΆΠ΅Π»Π΅Π·ΠΎΠ±Π΅ΡΠΎΠ½Π½ΡΡ ΠΈ Π±Π΅ΡΠΎΠ½Π½ΡΡ ΠΊΠΎΠ½ΡΡΡΡΠΊΡΠΈΠΉ.
ΠΠΎΠ½ΠΊΡΠ΅ΡΠ½ΡΠ΅ Π·Π½Π°ΡΠ΅Π½ΠΈΡ ΡΠΎΠ»ΡΠΈΠ½Ρ Π·Π°ΡΠΈΡΠ½ΠΎΠ³ΠΎ ΡΠ»ΠΎΡ Π±Π΅ΡΠΎΠ½Π° ΡΡΡΠ°Π½Π°Π²Π»ΠΈΠ²Π°ΡΡΡΡ Π½ΠΎΡΠΌΠ°ΡΠΈΠ²Π½ΡΠΌΠΈ Π΄ΠΎΠΊΡΠΌΠ΅Π½ΡΠ°ΠΌΠΈ β Π‘ΠΠΠ ΠΈ ΡΠΎΠ·Π΄Π°Π½Π½ΡΠΌΠΈ Π½Π° ΠΈΡ ΠΎΡΠ½ΠΎΠ²Π΅ Π‘Π²ΠΎΠ΄Π°ΠΌΠΈ ΠΡΠ°Π²ΠΈΠ». ΠΡΠΈ ΡΡΠΎΠΌ ΠΎΠ±ΡΠ·Π°ΡΠ΅Π»ΡΠ½ΠΎ ΡΡΠΈΡΡΠ²Π°ΡΡΡΡ ΠΎΡΠΎΠ±Π΅Π½Π½ΠΎΡΡΠΈ ΠΆΠ΅Π»Π΅Π·ΠΎΠ±Π΅ΡΠΎΠ½Π½ΠΎΠΉ ΠΊΠΎΠ½ΡΡΡΡΠΊΡΠΈΠΈ, ΠΎ ΠΊΠΎΡΠΎΡΡΡ Π±ΡΠ»ΠΎ ΡΠΊΠ°Π·Π°Π½ΠΎ Π²ΡΡΠ΅.
ΠΠΎΡΠΌΠ°ΡΠΈΠ²Ρ Β«ΡΠ°Π·Π±ΡΠΎΡΠ°Π½ΡΒ» ΠΏΠΎ Π½Π΅ΡΠΊΠΎΠ»ΡΠΊΠΈΠΌ Π΄ΠΎΠΊΡΠΌΠ΅Π½ΡΠ°ΠΌ, ΠΏΠΎΡΡΠΎΠΌΡ ΠΏΠΎΠΏΡΠΎΠ±ΡΠ΅Ρ Π²ΡΠ΅ ΠΆΠ΅ ΡΠ΄Π΅Π»Π°ΡΡ Π½Π΅ΠΊΡΡ Β«ΡΡΠ±Π»ΠΈΠΌΠ°ΡΠΈΡΒ», ΡΡΠΎΠ±Ρ ΠΊΠ°ΡΡΠΈΠ½Π° ΠΏΠΎΠ»ΡΡΠΈΠ»Π°ΡΡ ΠΌΠ°ΠΊΡΠΈΠΌΠ°Π»ΡΠ½ΠΎ Π½Π°Π³Π»ΡΠ΄Π½ΠΎΠΉ.
- ΠΡΠ»ΠΈ ΠΎΠ±ΡΠ°ΡΠΈΡΡΡΡ ΠΊ ΠΏΠΎΠ»ΠΎΠΆΠ΅Π½ΠΈΡΠΌ Π‘ΠΠΈΠ 52β01-2003 Β«ΠΠ΅ΡΠΎΠ½Π½ΡΠ΅ ΠΈ ΠΆΠ΅Π»Π΅Π·ΠΎΠ±Π΅ΡΠΎΠ½Π½ΡΠ΅ ΠΊΠΎΠ½ΡΡΡΡΠΊΡΠΈΠΈΒ», ΠΏΡΠ½ΠΊΡ 7.
3 Β«Π’ΡΠ΅Π±ΠΎΠ²Π°Π½ΠΈΡ ΠΊ Π°ΡΠΌΠΈΡΠΎΠ²Π°Π½ΠΈΡΒ», ΡΠΎ Π² ΠΈΡ ΠΏΠΎΠ΄ΠΏΡΠ½ΠΊΡΠ°Ρ ΠΎ Π·Π°ΡΠΈΡΠ½ΠΎΠΌ ΡΠ»ΠΎΠ΅ ΡΠΊΠ°Π·Π°Π½ΠΎ, ΡΡΠΎ ΡΠΎΠ»ΡΠΈΠ½Π° Π·Π°ΡΠΈΡΠ½ΠΎΠ³ΠΎ ΡΠ»ΠΎΡ Π±Π΅ΡΠΎΠ½Π° Π΄ΠΎΠ»ΠΆΠ½Π° Π±ΡΡΡ Π½Π΅ ΠΌΠ΅Π½ΡΡΠ΅ Π΄ΠΈΠ°ΠΌΠ΅ΡΡΠ° Π°ΡΠΌΠ°ΡΡΡΠ½ΠΎΠ³ΠΎ ΠΏΡΡΡΠ°, Π½ΠΎ ΠΏΡΠΈ ΡΡΠΎΠΌ ΠΈ Π½Π΅ ΠΌΠ΅Π½ΡΡΠ΅ 10 ΠΌΠΌ.
- Π’Π΅ΠΏΠ΅ΡΡ β Π‘Π²ΠΎΠ΄ ΠΡΠ°Π²ΠΈΠ» Π‘Π 50β101-2004 Β«ΠΡΠΎΠ΅ΠΊΡΠΈΡΠΎΠ²Π°Π½ΠΈΠ΅ ΠΈ ΡΡΡΡΠΎΠΉΡΡΠ²ΠΎ ΠΎΡΠ½ΠΎΠ²Π°Π½ΠΈΠΉ ΠΈ ΡΡΠ½Π΄Π°ΠΌΠ΅Π½ΡΠΎΠ² Π·Π΄Π°Π½ΠΈΠΉ ΠΈ ΡΠΎΠΎΡΡΠΆΠ΅Π½ΠΈΠΉΒ». ΠΠ΄Π΅ΡΡ ΡΠΆΠ΅ ΠΈΠ½ΡΠΎΡΠΌΠ°ΡΠΈΡ β Π±ΠΎΠ»Π΅Π΅ ΠΊΠΎΠ½ΠΊΡΠ΅ΡΠ½Π°Ρ:
β ΠΠ»Ρ ΠΏΡΠΎΠ΄ΠΎΠ»ΡΠ½ΠΎΠΉ ΡΠ°Π±ΠΎΡΠ΅ΠΉ Π°ΡΠΌΠ°ΡΡΡΡ ΡΡΠ½Π΄Π°ΠΌΠ΅Π½ΡΠ½ΡΡ Π±Π°Π»ΠΎΠΊ (Π»Π΅Π½ΡΠΎΡΠ½ΡΡ ΡΡΠ½Π΄Π°ΠΌΠ΅Π½ΡΠΎΠ²) ΠΈ ΡΠ±ΠΎΡΠ½ΡΡ ΠΎΡΠ½ΠΎΠ²Π°Π½ΠΈΠΉ ΡΠΎΠ»ΡΠΈΠ½Π° Π·Π°ΡΠΈΡΠ½ΠΎΠ³ΠΎ ΡΠ»ΠΎΡ Π΄ΠΎΠ»ΠΆΠ½Π° Π²ΡΠ΄Π΅ΡΠΆΠΈΠ²Π°ΡΡΡΡ Π½Π΅ ΠΌΠ΅Π½Π΅Π΅ 30 ΠΌΠΌ.
β ΠΠ»Ρ ΠΌΠΎΠ½ΠΎΠ»ΠΈΡΠ½ΡΡ ΡΡΠ½Π΄Π°ΠΌΠ΅Π½ΡΠΎΠ² ΡΠ΅ΠΊΠΎΠΌΠ΅Π½Π΄ΡΠ΅ΡΡΡ Π²ΡΠΏΠΎΠ»Π½ΡΡΡ Π±Π΅ΡΠΎΠ½Π½ΡΡ ΠΏΠΎΠ΄Π³ΠΎΡΠΎΠ²ΠΊΡ ΠΎΡΠ½ΠΎΠ²Π°Π½ΠΈΡ, ΡΠΎΠ»ΡΠΈΠ½ΠΎΠΉ 100 ΠΌΠΌ. ΠΠΎΠΏΡΡΠΊΠ°Π΅ΡΡΡ ΡΡΠ°ΠΌΠ±ΠΎΠ²Π°Π½Π½ΠΎΠ΅ ΠΏΠ΅ΡΡΠ°Π½ΠΎΠ΅ ΠΈΠ»ΠΈ ΡΠ΅Π±Π΅Π½ΡΠ°ΡΠΎΠ΅ Π·Π°ΠΏΠΎΠ»Π½Π΅Π½ΠΈΠ΅ Ρ ΠΏΠΎΡΠ»Π΅Π΄ΡΡΡΠ΅ΠΉ Π·Π°Π»ΠΈΠ²ΠΊΠΎΠΉ ΡΡΡΠΆΠΊΠΈ. Π ΠΎΠ±ΠΎΠΈΡ ΡΡΠΈΡ ΡΠ»ΡΡΠ°ΡΡ ΡΠΎΠ»ΡΠΈΠ½Π° Π·Π°ΡΠΈΡΠ½ΠΎΠ³ΠΎ ΡΠ»ΠΎΡ Π΄Π»Ρ ΠΏΡΠΎΠ΄ΠΎΠ»ΡΠ½ΠΎΠΉ ΡΠ°Π±ΠΎΡΠ΅ΠΉ Π°ΡΠΌΠ°ΡΡΡΡ Π² ΠΎΠ±Π»Π°ΡΡΠΈ ΠΏΠΎΠ΄ΠΎΡΠ²Ρ Π΄ΠΎΠ»ΠΆΠ½Π° ΡΠΎΡΡΠ°Π²Π»ΡΡΡ Π½Π΅ ΠΌΠ΅Π½Π΅Π΅ 35 ΠΌΠΌ.
β ΠΡΠ»ΠΈ ΠΌΠΎΠ½ΠΎΠ»ΠΈΡΠ½ΡΠΉ ΡΡΠ½Π΄Π°ΠΌΠ΅Π½Ρ,Β ΠΏΠΎ ΠΎΠ±ΠΎΡΠ½ΠΎΠ²Π°Π½Π½ΡΠΌ ΡΠΎΠΎΠ±ΡΠ°ΠΆΠ΅Π½ΠΈΡΠΌ, Π±ΡΠ΄Π΅Ρ Π·Π°Π»ΠΈΠ²Π°ΡΡΡΡ Π±Π΅Π· ΡΠΏΠΎΠΌΡΠ½ΡΡΠΎΠΉ Π²ΡΡΠ΅ Π±Π΅ΡΠΎΠ½Π½ΠΎΠΉ ΠΏΠΎΠ΄Π³ΠΎΡΠΎΠ²ΠΊΠΈ, ΡΠΎΠ»ΡΠΊΠΎ Π½Π° ΠΏΠ΅ΡΡΠ°Π½ΠΎ-ΡΠ΅Π±Π΅Π½ΠΎΡΠ½ΡΡ ΠΏΠΎΠ΄ΡΡΠΊΡ, ΡΠΎ Π·Π°ΡΠΈΡΠ½ΡΠΉ ΡΠ»ΠΎΠΉ Π² ΠΎΠ±Π»Π°ΡΡΠΈ ΠΏΠΎΠ΄ΠΎΡΠ²Ρ Π΄ΠΎΠ»ΠΆΠ΅Π½ ΡΠΎΡΡΠ°Π²ΠΈΡΡ Π½Π΅ ΠΌΠ΅Π½Π΅Π΅ 70 ΠΌΠΌ.
- Π‘Π»Π΅Π΄ΡΡΡΠΈΠΉ ΡΠ΅Π³Π»Π°ΠΌΠ΅Π½ΡΠΈΡΡΡΡΠΈΠΉ Π΄ΠΎΠΊΡΠΌΠ΅Π½Ρ β Π‘Π²ΠΎΠ΄ ΠΡΠ°Π²ΠΈΠ» Π‘Π 52β101-2003 Β«ΠΠ΅ΡΠΎΠ½Π½ΡΠ΅ ΠΈ ΠΆΠ΅Π»Π΅Π·ΠΎΠ±Π΅ΡΠΎΠ½Π½ΡΠ΅ ΠΊΠΎΠ½ΡΡΡΡΠΊΡΠΈΠΈ Π±Π΅Π· ΠΏΡΠ΅Π΄Π²Π°ΡΠΈΡΠ΅Π»ΡΠ½ΠΎΠ³ΠΎ Π½Π°ΠΏΡΡΠΆΠ΅Π½ΠΈΡ Π°ΡΠΌΠ°ΡΡΡΡΒ». ΠΠ½ Π΄Π°Π΅Ρ Π½Π°ΠΌ ΡΠ»Π΅Π΄ΡΡΡΡΡ ΠΈΠ½ΡΠΎΡΠΌΠ°ΡΠΈΡ:
β ΠΠ»Ρ ΠΆΠ΅Π»Π΅Π·ΠΎΠ±Π΅ΡΠΎΠ½Π½ΡΡ ΠΊΠΎΠ½ΡΡΡΡΠΊΡΠΈΠΉ, ΡΠ°ΡΠΏΠΎΠ»ΠΎΠΆΠ΅Π½Π½ΡΡ Π² Π·Π°ΠΊΡΡΡΡΡ ΠΏΠΎΠΌΠ΅ΡΠ΅Π½ΠΈΡΡ Ρ Π½ΠΎΡΠΌΠ°Π»ΡΠ½ΡΠΌ ΠΈΠ»ΠΈ ΠΏΠΎΠ½ΠΈΠΆΠ΅Π½Π½ΡΠΌ ΡΡΠΎΠ²Π½Π΅ΠΌ Π²Π»Π°ΠΆΠ½ΠΎΡΡΠΈ, Π΄Π»Ρ ΡΠ°Π±ΠΎΡΠ΅ΠΉ Π°ΡΠΌΠ°ΡΡΡΡ Π΄ΠΎΡΡΠ°ΡΠΎΡΠ½ΠΎ ΡΠΎΠ»ΡΠΈΠ½Ρ Π·Π°ΡΠΈΡΠ½ΠΎΠ³ΠΎ ΡΠ»ΠΎΡ 20 ΠΌΠΌ.
β Π’ΠΎ ΠΆΠ΅, Π½ΠΎ Π΄Π»Ρ ΠΏΠΎΠΌΠ΅ΡΠ΅Π½ΠΈΠΉ Ρ ΠΏΠΎΠ²ΡΡΠ΅Π½Π½ΡΠΌ ΡΡΠΎΠ²Π½Π΅ΠΌ Π²Π»Π°ΠΆΠ½ΠΎΡΡΠΈ ΠΈ Π±Π΅Π· ΠΏΡΠΎΠ²Π΅Π΄Π΅Π½ΠΈΡ Π² Π½ΠΈΡ ΡΠΏΠ΅ΡΠΈΠ°Π»ΡΠ½ΡΡ Π΄ΠΎΠΏΠΎΠ»Π½ΠΈΡΠ΅Π»ΡΠ½ΡΡ Π·Π°ΡΠΈΡΠ½ΡΡ ΠΌΠ΅ΡΠΎΠΏΡΠΈΡΡΠΈΠΉ, ΡΠΎΠ»ΡΠΈΠ½Π° Π·Π°ΡΠΈΡΠ½ΠΎΠ³ΠΎ ΡΠ»ΠΎΡ Π²ΠΎΠ·ΡΠ°ΡΡΠ°Π΅Ρ Π΄ΠΎ 25 ΠΌΠΌ.
β ΠΠ»Ρ ΠΆΠ΅Π»Π΅Π·ΠΎΠ±Π΅ΡΠΎΠ½Π½ΡΡ ΠΊΠΎΠ½ΡΡΡΡΠΊΡΠΈΠΉ, ΡΠ°ΡΠΏΠΎΠ»ΠΎΠΆΠ΅Π½Π½ΡΡ Π½Π° ΠΎΡΠΊΡΡΡΠΎΠΌ Π²ΠΎΠ·Π΄ΡΡ Π΅, Π±Π΅Π· ΠΏΡΠΎΠ²Π΅Π΄Π΅Π½ΠΈΡ Π΄ΠΎΠΏΠΎΠ»Π½ΠΈΡΠ΅Π»ΡΠ½ΡΡ Π·Π°ΡΠΈΡΠ½ΡΡ ΠΌΠ΅ΡΠΎΠΏΡΠΈΡΡΠΈΠΉ, ΠΏΠΎΡΡΠ΅Π±ΡΠ΅ΡΡΡ ΡΠ»ΠΎΠΉ Π² 30 ΠΌΠΌ.
β ΠΠ»Ρ ΠΊΠΎΠ½ΡΡΡΡΠΊΡΠΈΠΉ, ΡΠ°ΡΠΏΠΎΠ»ΠΎΠΆΠ΅Π½Π½ΡΡ Π² Π³ΡΡΠ½ΡΠ΅, Π² ΡΠΎΠΌ ΡΠΈΡΠ»Π΅ ΠΈ Π² ΡΡΠ½Π΄Π°ΠΌΠ΅Π½ΡΠ°Ρ ΠΏΡΠΈ Π²ΡΠΏΠΎΠ»Π½Π΅Π½ΠΈΠΈ Π±Π΅ΡΠΎΠ½Π½ΠΎΠΉ ΠΏΠΎΠ΄Π³ΠΎΡΠΎΠ²ΠΊΠΈ, ΡΡΡΠ°Π½Π°Π²Π»ΠΈΠ²Π°Π΅ΡΡΡ ΠΌΠΈΠ½ΠΈΠΌΠ°Π»ΡΠ½Π°Ρ ΡΠΎΠ»ΡΠΈΠ½Π° ΡΠ»ΠΎΡ Π² 40 ΠΌΠΌ.
ΠΡΠΈ ΠΈΡΠΏΠΎΠ»ΡΠ·ΠΎΠ²Π°Π½ΠΈΠΈ ΡΠ±ΠΎΡΠ½ΡΡ ΡΠ»Π΅ΠΌΠ΅Π½ΡΠΎΠ² ΡΠΎΠ»ΡΠΈΠ½Π° Π·Π°ΡΠΈΡΠ½ΠΎΠ³ΠΎ ΡΠ»ΠΎΡ Π΄Π»Ρ Π½ΠΈΡ ΠΌΠΎΠΆΠ΅Ρ Π±ΡΡΡ ΡΠΌΠ΅Π½ΡΡΠ΅Π½Π° Π½Π° 5 ΠΌΠΌ.
ΠΠ»Ρ ΠΊΠΎΠ½ΡΡΡΡΠΊΡΠΈΠ²Π½ΠΎΠΉ Π°ΡΠΌΠ°ΡΡΡΡ ΠΏΠΎΠΊΠ°Π·Π°ΡΠ΅Π»ΠΈ ΡΠΎΠ»ΡΠΈΠ½Ρ Π·Π°ΡΠΈΡΠ½ΠΎΠ³ΠΎ ΡΠ»ΠΎΡ ΡΠ°ΠΊΠΆΠ΅ ΠΌΠΎΠ³ΡΡ Π±ΡΡΡ ΡΠΌΠ΅Π½ΡΡΠ΅Π½Ρ Π½Π° 5 ΠΌΠΌ ΠΏΠΎ ΡΡΠ°Π²Π½Π΅Π½ΠΈΡ Ρ Π½ΠΎΡΠΌΠ°ΡΠΈΠ²Π°ΠΌΠΈ Π΄Π»Ρ ΡΠ°Π±ΠΎΡΠΈΡ
ΠΏΡΡΡΠΎΠ². ΠΠΎ ΠΏΡΠΈ ΡΡΠΎΠΌ Π²ΡΠ΅ ΡΠ°Π²Π½ΠΎ ΡΠΎΠ±Π»ΡΠ΄Π°Π΅ΡΡΡ ΠΆΠ΅ΡΡΠΊΠΎΠ΅ ΠΏΡΠ°Π²ΠΈΠ»ΠΎ, ΡΡΠΎΠ±Ρ ΡΠΎΠ»ΡΠΈΠ½Π° ΡΠ»ΠΎΡ Π½Π΅ ΡΡΠ°Π»Π° ΠΌΠ΅Π½ΡΡΠ΅ Π΄ΠΈΠ°ΠΌΠ΅ΡΡΠ° ΡΠ°ΠΌΠΎΠΉ Π°ΡΠΌΠ°ΡΡΡΡ.
- ΠΡΠ΅ ΠΎΠ΄ΠΈΠ½ ΠΎΡΠ΅Π½Ρ ΠΈΠ½ΡΠ΅ΡΠ΅ΡΠ½ΡΠΉ Π΄ΠΎΠΊΡΠΌΠ΅Π½Ρ. ΠΡΠ»ΠΈ ΠΏΠΎΡΠ΅ΡΠΈΡΡ ΡΠΎΡΡΠΌΡ ΠΏΡΠΎΡΠ΅ΡΡΠΈΠΎΠ½Π°Π»ΡΠ½ΡΡ ΡΡΡΠΎΠΈΡΠ΅Π»Π΅ΠΉ, ΡΠΎ ΠΌΠΎΠΆΠ½ΠΎ Π·Π°ΠΌΠ΅ΡΠΈΡΡ ΠΌΠ°ΡΡΡ ΠΏΠΎΠ»ΠΎΠΆΠΈΡΠ΅Π»ΡΠ½ΡΡ ΠΎΡΠ·ΡΠ²ΠΎΠ² ΠΎ ΡΠΏΡΠ°Π²ΠΎΡΠ½ΠΎΠΌ ΠΏΠΎΡΠΎΠ±ΠΈΠΈ Β«ΠΡΠΎΠ΅ΠΊΡΠΈΡΠΎΠ²Π°Π½ΠΈΠ΅ ΠΆΠ΅Π»Π΅Π·ΠΎΠ±Π΅ΡΠΎΠ½Π½ΡΡ ΠΊΠΎΠ½ΡΡΡΡΠΊΡΠΈΠΉΒ» ΠΏΠΎΠ΄ ΡΠ΅Π΄Π°ΠΊΡΠΈΠ΅ΠΉ Π΄ΠΎΠΊΡΠΎΡΠ° ΡΠ΅Ρ Π½ΠΈΡΠ΅ΡΠΊΠΈΡ Π½Π°ΡΠΊ Π. Π. ΠΠΎΠ»ΡΡΠ΅Π²Π°. ΠΡΠ° ΠΊΠ½ΠΈΠ³Π° Π²ΡΡΠ»Π° Π΅ΡΠ΅ Π² 1985 Π³ΠΎΠ΄Ρ Π² ΠΠΈΠ΅Π²ΡΠΊΠΎΠΌ ΠΈΠ·Π΄Π°ΡΠ΅Π»ΡΡΡΠ²Π΅ Β«ΠΡΠ΄iΠ²Π΅Π»ΡΠ½ΠΈΠΊΒ», Π·Π°ΡΠ΅ΠΌ Π½Π΅ΠΎΠ΄Π½ΠΎΠΊΡΠ°ΡΠ½ΠΎ ΠΏΠ΅ΡΠ΅ΠΈΠ·Π΄Π°Π²Π°Π»Π°ΡΡ. Π, ΠΏΠΎ ΠΌΠ½Π΅Π½ΠΈΡ ΠΌΠ½ΠΎΠ³ΠΈΡ ΠΏΡΠΎΡΠ΅ΡΡΠΈΠΎΠ½Π°Π»ΠΎΠ² β Π½ΠΈΡΠ΅Π³ΠΎ Π»ΡΡΡΠ΅ Π΄ΠΎ ΡΠΈΡ ΠΏΠΎΡ Π΄Π»Ρ ΠΏΡΠ°ΠΊΡΠΈΡΠ΅ΡΠΊΠΈΡ ΡΠ°ΡΡΠ΅ΡΠΎΠ² Π½Π΅ ΠΏΡΠ΅Π΄Π»ΠΎΠΆΠ΅Π½ΠΎ. ΠΡΡΡ ΡΠΌΡΡΠ» ΠΎΠ·Π½Π°ΠΊΠΎΠΌΠΈΡΡΡΡ ΠΈ Ρ ΡΠ΅ΠΊΠΎΠΌΠ΅Π½Π΄Π°ΡΠΈΡΠΌΠΈ ΡΡΠΎΠ³ΠΎ ΡΠΏΡΠ°Π²ΠΎΡΠ½ΠΎΠ³ΠΎ ΠΏΠΎΡΠΎΠ±ΠΈΡ:
β Π’ΠΎΠ»ΡΠΈΠ½Π° Π·Π°ΡΠΈΡΠ½ΠΎΠ³ΠΎ ΡΠ»ΠΎΡ Π΄Π»Ρ ΡΠ±ΠΎΡΠ½ΡΡ ΡΡΠ½Π΄Π°ΠΌΠ΅Π½ΡΠΎΠ² ΠΈ ΡΡΠ½Π΄Π°ΠΌΠ΅Π½ΡΠ½ΡΡ Π±Π°Π»ΠΎΠΊ, Π²Π½Π΅ Π·Π°Π²ΠΈΡΠΈΠΌΠΎΡΡΠΈ ΠΎΡ ΡΠ΅ΡΠ΅Π½ΠΈΡ β 30 ΠΌΠΌ.
β ΠΠ»Ρ ΠΌΠΎΠ½ΠΎΠ»ΠΈΡΠ½ΡΡ ΡΡΠ½Π΄Π°ΠΌΠ΅Π½ΡΠΎΠ², ΡΡΡΡΠ°ΠΈΠ²Π°Π΅ΠΌΡΡ Π½Π° Π±Π΅ΡΠΎΠ½Π½ΠΎΠΉ ΠΏΠΎΠ΄Π³ΠΎΡΠΎΠ²ΠΊΠ΅, ΠΈΠ»ΠΈ Π±Π΅Π· Π½Π΅Π΅, Π½ΠΎ Π½Π° ΡΠΊΠ°Π»ΡΠ½ΠΎΠΉ Π³ΡΡΠ½ΡΠ΅ β 35 ΠΌΠΌ.
β ΠΠΎΠ½ΠΎΠ»ΠΈΡΠ½ΡΠ΅ ΡΡΠ½Π΄Π°ΠΌΠ΅Π½ΡΡ Π±Π΅Π· ΠΏΡΠ΅Π΄Π²Π°ΡΠΈΡΠ΅Π»ΡΠ½ΠΎΠ³ΠΎ Π²ΡΠΏΠΎΠ»Π½Π΅Π½ΠΈΡ Π±Π΅ΡΠΎΠ½Π½ΠΎΠΉ ΠΏΠΎΠ΄Π³ΠΎΡΠΎΠ²ΠΊΠΈ β 70 ΠΌΠΌ.
β ΠΠ»Ρ ΠΏΠΎΠΏΠ΅ΡΠ΅ΡΠ½ΠΎΠΉ, ΡΠ°ΡΠΏΡΠ΅Π΄Π΅Π»ΠΈΡΠ΅Π»ΡΠ½ΠΎΠΉ ΠΈ ΠΊΠΎΠ½ΡΡΡΡΠΊΡΠΈΠ²Π½ΠΎΠΉ Π°ΡΠΌΠ°ΡΡΡΡ, Π΅ΡΠ»ΠΈ ΠΌΠΈΠ½ΠΈΠΌΠ°Π»ΡΠ½ΡΠΉ ΡΠ°Π·ΠΌΠ΅Ρ ΡΠ΅ΡΠ΅Π½ΠΈΡ (Π²ΡΡΠΎΡΠ° ΠΈΠ»ΠΈ ΡΠΈΡΠΈΠ½Π°) ΠΊΠΎΠ½ΡΡΡΡΠΊΡΠΈΠΈ ΠΌΠ΅Π½Π΅Π΅ 250 ΠΌΠΌ, ΡΠΎΠ»ΡΠΈΠ½Π° Π·Π°ΡΠΈΡΠ½ΠΎΠ³ΠΎ ΡΠ»ΠΎΡ Π΄ΠΎΠ»ΠΆΠ½Π° ΡΠΎΡΡΠ°Π²Π»ΡΡΡ Π½Π΅ ΠΌΠ΅Π½Π΅Π΅ 10 ΠΌΠΌ. ΠΡΠΈ ΡΠ°Π·ΠΌΠ΅ΡΠ°Ρ
ΡΠ΅ΡΠ΅Π½ΠΈΡ Π±ΠΎΠ»Π΅Π΅ 250 ΠΌΠΌ ΡΡΠΎΡ ΠΏΠ°ΡΠ°ΠΌΠ΅ΡΡ Π²ΠΎΠ·ΡΠ°ΡΡΠ°Π΅Ρ Π΄ΠΎ 15 ΠΌΠΌ. ΠΠΎΠ½ΡΡΠ½ΠΎ, ΡΡΠΎ ΠΈΠΌ Π² ΡΡΠΎΠΌ ΡΠ»ΡΡΠ°Π΅ Π΄Π΅ΠΉΡΡΠ²ΡΠ΅Ρ Π΅Π΄ΠΈΠ½ΠΎΠ΅ ΠΏΡΠ°Π²ΠΈΠ»ΠΎ β ΡΠΎΠ»ΡΠΈΠ½Π° Π½Π΅ ΠΌΠΎΠΆΠ΅Ρ Π±ΡΡΡ ΠΌΠ΅Π½ΡΡΠ΅ Π΄ΠΈΠ°ΠΌΠ΅ΡΡΠ° Π°ΡΠΌΠ°ΡΡΡΠ½ΠΎΠ³ΠΎ ΠΏΡΡΡΠ°.
ΠΡΠΈΠΌ ΠΆΠ΅ ΠΏΠΎΡΠΎΠ±ΠΈΠ΅ΠΌ ΡΠ΅ΠΊΠΎΠΌΠ΅Π½Π΄ΡΠ΅ΡΡΡ ΡΠΎΠ»ΡΠΈΠ½Π° Π·Π°ΡΠΈΡΠ½ΠΎΠ³ΠΎ ΡΠ»ΠΎΡ Ρ ΡΠΎΡΡΠ΅Π²ΡΡ ΡΡΠΎΡΠΎΠ½ ΠΏΡΠΎΠ΄ΠΎΠ»ΡΠ½ΡΡ ΠΈ ΠΏΠΎΠΏΠ΅ΡΠ΅ΡΠ½ΡΡ Π°ΡΠΌΠ°ΡΡΡΠ½ΡΡ ΠΏΡΡΡΡΠ΅Π², ΠΏΡΠΎΡ ΠΎΠ΄ΡΡΠΈΠΉ ΠΏΠΎ Π²ΡΠ΅ Π΄Π»ΠΈΠ½Π΅ ΠΈΠ»ΠΈ ΡΠΈΡΠΈΠ½Π΅ ΠΆΠ΅Π»Π΅Π·ΠΎΠ±Π΅ΡΠΎΠ½Π½ΠΎΠΉ ΠΊΠΎΠ½ΡΡΡΡΠΊΡΠΈΠΈ.
β ΠΠ»Ρ ΡΠ±ΠΎΡΠ½ΡΡ ΡΠ»Π΅ΠΌΠ΅Π½ΡΠΎΠ² Π΄Π»ΠΈΠ½ΠΎΠΉ Π΄ΠΎ 9 ΠΌΠ΅ΡΡΠΎΠ² Π²ΠΊΠ»ΡΡΠΈΡΠ΅Π»ΡΠ½ΠΎ β 10 ΠΌΠΌ.
β ΠΠ»Ρ ΠΌΠΎΠ½ΠΎΠ»ΠΈΡΠ½ΡΡ ΡΠ»Π΅ΠΌΠ΅Π½ΡΠΎΠ² Π΄Π»ΠΈΠ½ΠΎΠΉ Π΄ΠΎ 6 ΠΌΠ΅ΡΡΠΎΠ², ΠΏΡΠΈ Π΄ΠΈΠ°ΠΌΠ΅ΡΡΠ΅ Π°ΡΠΌΠ°ΡΡΡΡ Π΄ΠΎ 40 ΠΌΠΌ β 15 ΠΌΠΌ.
β ΠΠ»Ρ ΠΌΠΎΠ½ΠΎΠ»ΠΈΡΠ½ΡΡ ΡΠ»Π΅ΠΌΠ΅Π½ΡΠΎΠ² Π΄Π»ΠΈΠ½ΠΎΠΉ ΡΠ²ΡΡΠ΅ 6 ΠΌΠ΅ΡΡΠΎΠ² ΠΏΡΠΈ Π΄ΠΈΠ°ΠΌΠ΅ΡΡΠ΅ Π°ΡΠΌΠ°ΡΡΡΠ½ΡΡ ΠΏΡΡΡΠΎΠ² Π΄ΠΎ 40 ΠΌΠΌ, Π° ΡΠ°ΠΊΠΆΠ΅ Π΄Π»Ρ ΠΊΠΎΠ½ΡΡΡΡΠΊΡΠΈΠΉ Π»ΡΠ±ΠΎΠΉ Π΄Π»ΠΈΠ½Ρ ΠΏΡΠΈ Π΄ΠΈΠ°ΠΌΠ΅ΡΡΠ΅ ΠΏΡΡΡΠΎΠ² Π±ΠΎΠ»Π΅Π΅ 40 ΠΌΠΌ β 20 ΠΌΠΌ.
- ΠΠ°ΠΊΠΎΠ½Π΅Ρ, ΡΡΠΎΠΈΡ ΠΏΠΎΡΠΌΠΎΡΡΠ΅ΡΡ Π΅ΡΠ΅ ΠΈ Π½Π° Π‘ΠΠΈΠ 3.03.01β87 Β«ΠΠ΅ΡΡΡΠΈΠ΅ ΠΈ ΠΎΠ³ΡΠ°ΠΆΠ΄Π°ΡΡΠΈΠ΅ ΠΊΠΎΠ½ΡΡΡΡΠΊΡΠΈΠΈΒ», Π² ΠΊΠΎΡΠΎΡΠΎΠΌ ΠΎΠ³ΠΎΠ²ΠΎΡΠ΅Π½Ρ Π²ΠΎΠ·ΠΌΠΎΠΆΠ½ΡΠ΅ ΠΎΡΠΊΠ»ΠΎΠ½Π΅Π½ΠΈΡ ΠΎΡ Π·Π°Π΄Π°Π½Π½ΡΡ ΠΏΠ°ΡΠ°ΠΌΠ΅ΡΡΠΎΠ² ΡΠΎΠ»ΡΠΈΠ½Ρ Π·Π°ΡΠΈΡΠ½ΠΎΠ³ΠΎ Π±Π΅ΡΠΎΠ½Π½ΠΎΠ³ΠΎ ΡΠ»ΠΎΡ:
ΠΡΠΎΠ±Π΅Π½Π½ΠΎΡΡΠΈ ΠΆΠ΅Π»Π΅Π·ΠΎΠ±Π΅ΡΠΎΠ½Π½ΠΎΠΉ ΠΊΠΎΠ½ΡΡΡΡΠΊΡΠΈΠΈ | ΠΠΎΠΏΡΡΡΠΈΠΌΠ°Ρ Π²Π΅Π»ΠΈΡΠΈΠ½Π° ΠΎΡΠΊΠ»ΠΎΠ½Π΅Π½ΠΈΡ ΠΎΡ ΡΠ΅ΠΊΠΎΠΌΠ΅Π½Π΄ΡΠ΅ΠΌΠΎΠΉ ΡΠΎΠ»ΡΠΈΠ½Ρ Π·Π°ΡΠΈΡΠ½ΠΎΠ³ΠΎ ΡΠ»ΠΎΡ |
---|---|
ΠΡΠΈ ΡΡΡΠ°Π½ΠΎΠ²Π»Π΅Π½Π½ΠΎΠΉ ΡΠΎΠ»ΡΠΈΠ½Π΅ Π·Π°ΡΠΈΡΠ½ΠΎΠ³ΠΎ ΡΠ»ΠΎΡ Π΄ΠΎ 15 ΠΌΠΌ, ΠΈ Π»ΠΈΠ½Π΅ΠΉΠ½ΡΡ ΡΠ°Π·ΠΌΠ΅ΡΠ°Ρ ΠΏΠΎΠΏΠ΅ΡΠ΅ΡΠ½ΠΎΠ³ΠΎ ΡΠ΅ΡΠ΅Π½ΠΈΡ ΠΊΠΎΠ½ΡΡΡΡΠΊΡΠΈΠΈ: | |
— Π΄ΠΎ 100 ΠΌΠΌ | +4 ΠΌΠΌ |
— ΠΎΡ 101 Π΄ΠΎ 200 ΠΌΠΌ | +5 ΠΌΠΌ |
ΠΡΠΈ ΡΡΡΠ°Π½ΠΎΠ²Π»Π΅Π½Π½ΠΎΠΉ ΡΠΎΠ»ΡΠΈΠ½Π΅ Π·Π°ΡΠΈΡΠ½ΠΎΠ³ΠΎ ΡΠ»ΠΎΡ ΠΎΡ 16 Π΄ΠΎ 20 ΠΌΠΌ, ΠΈ Π»ΠΈΠ½Π΅ΠΉΠ½ΡΡ ΡΠ°Π·ΠΌΠ΅ΡΠ°Ρ ΠΏΠΎΠΏΠ΅ΡΠ΅ΡΠ½ΠΎΠ³ΠΎ ΡΠ΅ΡΠ΅Π½ΠΈΡ ΠΊΠΎΠ½ΡΡΡΡΠΊΡΠΈΠΈ: | |
— Π΄ΠΎ 100 ΠΌΠΌ | + 4 ΠΌΠΌ; -3 ΠΌΠΌ |
— ΠΎΡ 101 Π΄ΠΎ 200 ΠΌΠΌ | + 8 ΠΌΠΌ; -3 ΠΌΠΌ |
— ΠΎΡ 201 Π΄ΠΎ 300 ΠΌΠΌ | + 10 ΠΌΠΌ; -3 ΠΌΠΌ |
— ΡΠ²ΡΡΠ΅ 300 ΠΌΠΌ | + 15 ΠΌΠΌ; -3 ΠΌΠΌ |
ΠΡΠΈ ΡΡΡΠ°Π½ΠΎΠ²Π»Π΅Π½Π½ΠΎΠΉ ΡΠΎΠ»ΡΠΈΠ½Π΅ Π·Π°ΡΠΈΡΠ½ΠΎΠ³ΠΎ ΡΠ»ΠΎΡ ΡΠ²ΡΡΠ΅ 20 ΠΌΠΌ, ΠΈ Π»ΠΈΠ½Π΅ΠΉΠ½ΡΡ ΡΠ°Π·ΠΌΠ΅ΡΠ°Ρ ΠΏΠΎΠΏΠ΅ΡΠ΅ΡΠ½ΠΎΠ³ΠΎ ΡΠ΅ΡΠ΅Π½ΠΈΡ ΠΊΠΎΠ½ΡΡΡΡΠΊΡΠΈΠΈ: | |
— Π΄ΠΎ 100 ΠΌΠΌ | + 4 ΠΌΠΌ; -5 ΠΌΠΌ |
— ΠΎΡ 101 Π΄ΠΎ 200 ΠΌΠΌ | + 8 ΠΌΠΌ; -5 ΠΌΠΌ |
— ΠΎΡ 201 Π΄ΠΎ 300 ΠΌΠΌ | + 10 ΠΌΠΌ; -5 ΠΌΠΌ |
— ΡΠ²ΡΡΠ΅ 300 ΠΌΠΌ | + 15 ΠΌΠΌ; -5 ΠΌΠΌ |
ΠΡΠ°ΠΌΠΎΡΠ½ΠΎ ΠΈΡΠΏΠΎΠ»ΡΠ·ΡΡ ΡΠ΅ΠΊΠΎΠΌΠ΅Π½Π΄Π°ΡΠΈΠΈ Π²ΡΠ΅Ρ
ΠΏΠ΅ΡΠ΅ΡΠΈΡΠ»Π΅Π½Π½ΡΡ
Π²ΡΡΠ΅ ΡΡΠΊΠΎΠ²ΠΎΠ΄ΡΡΠΈΡ
Π΄ΠΎΠΊΡΠΌΠ΅Π½ΡΠΎΠ², ΠΌΠΎΠΆΠ½ΠΎ ΠΏΡΠ°Π²ΠΈΠ»ΡΠ½ΠΎ ΡΠΏΠ»Π°Π½ΠΈΡΠΎΠ²Π°ΡΡ ΠΊΠΎΠ½ΡΡΡΡΠΊΡΠΈΡ Π°ΡΠΌΠΈΡΡΡΡΠ΅Π³ΠΎ ΠΊΠ°ΡΠΊΠ°ΡΠ° Π΄Π»Ρ ΡΡΠ½Π΄Π°ΠΌΠ΅Π½ΡΠ°. ΠΠΈΠΊΠ°ΠΊΠΈΡ
ΠΏΠΎΡΠ»Π°Π±Π»Π΅Π½ΠΈΠΉ Π½Π° ΡΡΠΎΡ ΡΡΠ΅Ρ (ΠΊΡΠΎΠΌΠ΅ ΡΠΊΠ°Π·Π°Π½Π½ΡΡ
Π² ΠΏΠΎΡΠ»Π΅Π΄Π½Π΅ΠΉ ΡΠ°Π±Π»ΠΈΡΠ΅) Π±ΡΡΡ Π½Π΅ Π΄ΠΎΠ»ΠΆΠ½ΠΎ. Π ΠΏΡΠΎΡΠΈΠ²Π½ΠΎΠΌ ΡΠ»ΡΡΠ°Π΅ ΡΠΎΡ
ΡΠ°Π½Π½ΠΎΡΡΡ ΠΈ Π΄ΠΎΠ»Π³ΠΎΠ²Π΅ΡΠ½ΠΎΡΡΡ ΡΠΎΠ·Π΄Π°Π²Π°Π΅ΠΌΠΎΠ³ΠΎ ΡΡΠ½Π΄Π°ΠΌΠ΅Π½ΡΠ° Π³Π°ΡΠ°Π½ΡΠΈΡΠΎΠ²Π°ΡΡΡΡ Π½ΠΈΡΠ΅ΠΌ Π½Π΅ Π±ΡΠ΄Π΅Ρ.
Π Π΄Π°Π½Π½ΠΎΠΉ ΠΏΡΠ±Π»ΠΈΠΊΠ°ΡΠΈΠΈ ΠΌΡ Π½Π΅ ΡΡΠ°Π½Π΅ΠΌ ΠΏΠΎΠ΄ΡΠΎΠ±Π½ΠΎ ΠΎΡΡΠ°Π½Π°Π²Π»ΠΈΠ²Π°ΡΡΡΡ Π½Π° ΠΈΠ½ΡΡ ΠΏΡΠ°Π²ΠΈΠ»Π°Ρ ΠΌΠΎΠ½ΡΠ°ΠΆΠ° Π°ΡΠΌΠ°ΡΡΡΠ½ΠΎΠ³ΠΎ ΠΊΠ°ΡΠΊΠ°ΡΠ° Π΄Π»Ρ ΡΡΠ½Π΄Π°ΠΌΠ΅Π½ΡΠ°. ΠΡΠΎ β ΠΎΡΠ΅Π½Ρ ΠΎΠ±ΡΠΈΡΠ½Π°Ρ ΡΠ΅ΠΌΠ°, ΠΈ ΠΎΠ½Π° Ρ ΠΎΡΠΎΡΠΎ ΡΠ°ΡΡΠΌΠΎΡΡΠ΅Π½Π° Π² Π΄ΡΡΠ³ΠΈΡ ΡΡΠ°ΡΡΡΡ Π½Π°ΡΠ΅Π³ΠΎ ΠΏΠΎΡΡΠ°Π»Π°.
ΠΠ°ΡΠ΅ΡΡΠ²ΠΎ ΠΈ ΠΏΡΠ°Π²ΠΈΠ»ΡΠ½ΠΎΡΡΡ ΠΌΠΎΠ½ΡΠ°ΠΆΠ° Π°ΡΠΌΠΈΡΡΡΡΠ΅Π³ΠΎ ΠΊΠ°ΡΠΊΠ°ΡΠ° β Π·Π°Π»ΠΎΠ³ Π½Π°Π΄Π΅ΠΆΠ½ΠΎΡΡΠΈ ΠΈ Π΄ΠΎΠ»Π³ΠΎΠ²Π΅ΡΠ½ΠΎΡΡΠΈ ΡΡΠ½Π΄Π°ΠΌΠ΅Π½ΡΠ°
Π‘ΠΎΠ·Π΄Π°Π½ΠΈΠ΅ Π°ΡΠΌΠΈΡΡΡΡΠ΅ΠΉ ΠΊΠΎΠ½ΡΡΡΡΠΊΡΠΈΠΈ Π΄ΠΎΠ»ΠΆΠ½ΠΎ ΠΎΡΠ½ΠΎΠ²ΡΠ²Π°ΡΡΡΡ Π½Π° ΠΏΡΠΎΠ²Π΅Π΄Π΅Π½Π½ΡΡ ΡΠ°ΡΡΠ΅ΡΠ°Ρ ΠΈ Π²ΡΠΏΠΎΠ»Π½ΡΡΡΡΡ Π² ΡΡΡΠΎΠ³ΠΎΠΌ ΡΠΎΠΎΡΠ²Π΅ΡΡΡΠ²ΠΈΠΈ Ρ ΡΡΡΠ°Π½ΠΎΠ²Π»Π΅Π½Π½ΡΠΌΠΈ Π½ΠΎΡΠΌΠ°ΡΠΈΠ²Π°ΠΌΠΈ. ΠΠΎΠΏΡΠΎΡΠ°ΠΌ Π°ΡΠΌΠΈΡΠΎΠ²Π°Π½ΠΈΡ Π»Π΅Π½ΡΠΎΡΠ½ΠΎΠ³ΠΎ ΡΡΠ½Π΄Π°ΠΌΠ΅Π½ΡΠ° ΠΏΠΎΡΠ²ΡΡΠ΅Π½Π° ΡΠΏΠ΅ΡΠΈΠ°Π»ΡΠ½Π°Ρ ΠΏΠΎΠ΄ΡΠΎΠ±Π½Π°Ρ ΡΡΠ°ΡΡΡ Π½Π°ΡΠ΅Π³ΠΎ ΠΏΠΎΡΡΠ°Π»Π°, Π² ΠΊΠΎΡΠΎΡΠΎΠΉ ΠΏΡΠΈΠ²Π΅Π΄Π΅Π½Ρ ΠΈ ΠΏΡΠΈΠΌΠ΅ΡΡ ΡΠ°ΡΡΠ΅ΡΠΎΠ², ΠΈ Π±Π°Π·ΠΎΠ²ΡΠ΅ ΡΠ΅ΡΡΠ΅ΠΆΠΈ Π½Π°ΠΈΠ±ΠΎΠ»Π΅Π΅ ΡΠ»ΠΎΠΆΠ½ΡΡ ΡΠ·Π»ΠΎΠ².
Π’Π΅Ρ Π½ΠΎΠ»ΠΎΠ³ΠΈΠΈ Π²ΡΠ·ΠΊΠΈ Π°ΡΠΌΠ°ΡΡΡΡ ΠΏΠΎΠ΄ Π»Π΅Π½ΡΠΎΡΠ½ΡΠΉ ΡΡΠ½Π΄Π°ΠΌΠ΅Π½Ρ ΡΠ΄Π΅Π»Π΅Π½Π° ΠΎΡΠ΄Π΅Π»ΡΠ½Π°Ρ ΠΏΡΠ±Π»ΠΈΠΊΠ°ΡΠΈΡ. ΠΡ Π° Π΅ΡΠ»ΠΈ Π² ΠΏΠ»Π°Π½Π°Ρ β ΡΠΎΠ·Π΄Π°Π½ΠΈΠ΅ ΠΌΠΎΠ½ΠΎΠ»ΠΈΡΠ½ΠΎΠ³ΠΎ ΠΏΠ»ΠΈΡΠ½ΠΎΠ³ΠΎ ΡΡΠ½Π΄Π°ΠΌΠ΅Π½ΡΠ° β ΡΠΎ ΠΈ Π½Π° ΡΡΠΎΡ ΡΡΠ΅Ρ Π½Π°ΠΉΠ΄Π΅ΡΡΡ Π½Π΅ΠΌΠ°Π»ΠΎ ΠΏΠΎΠ»Π΅Π·Π½ΠΎΠΉ ΠΈΠ½ΡΠΎΡΠΌΠ°ΡΠΈΠΈ.
ΠΡΠ»ΠΈ ΠΎΠ·Π½Π°ΠΊΠΎΠΌΠΈΡΡΡΡ Ρ ΡΠ΅ΠΊΠΎΠΌΠ΅Π½Π΄ΡΠ΅ΠΌΡΠΌΠΈ ΠΈΠ½ΡΡΡΡΠΊΡΠΈΡΠΌΠΈ (ΠΊ ΠΊΠΎΡΠΎΡΡΠΌ Π²Π΅Π΄ΡΡ ΡΡΡΠ»ΠΊΠΈ), ΡΠΎ ΡΡΠ°Π½ΠΎΠ²ΠΈΡΡΡ ΠΏΠΎΠ½ΡΡΠ½ΠΎ, ΡΡΠΎ Π²Π΅Π»ΠΈΡΠΈΠ½Π° Π·Π°ΡΠΈΡΠ½ΠΎΠ³ΠΎ ΡΠ»ΠΎΡ Π·Π°ΠΊΠ»Π°Π΄ΡΠ²Π°Π΅ΡΡΡ ΡΠΆΠ΅ ΠΏΡΠΈ ΠΏΡΠΎΠ²Π΅Π΄Π΅Π½ΠΈΠΈ ΡΠ°ΡΡΠ΅ΡΠΎΠ² ΠΊΠ°ΡΠΊΠ°ΡΠ° ΠΈ ΡΠΎΡΡΠ°Π²Π»Π΅Π½ΠΈΠΈ ΡΠ΅ΡΡΠ΅ΠΆΠ΅ΠΉ Π±ΡΠ΄ΡΡΠ΅ΠΉ Π°ΡΠΌΠ°ΡΡΡΠ½ΠΎΠΉ ΠΊΠΎΠ½ΡΡΡΡΠΊΡΠΈΠΈ. ΠΠΎ ΠΊΠ°ΠΊ ΡΠΎΠ±Π»ΡΡΡΠΈ ΡΡΠΎ ΡΠΆΠ΅ Π½Π° ΠΏΡΠ°ΠΊΡΠΈΠΊΠ΅?
ΠΠΎΠ½ΡΡΠ½ΠΎ, ΡΡΠΎ Π½ΠΈΠΆΠ½ΠΈΠΉ ΡΡΡΡ Π°ΡΠΌΠ°ΡΡΡΡ Π΄ΠΎΠ»ΠΆΠ΅Π½ Π±ΡΡΡ ΠΏΡΠΈΠΏΠΎΠ΄Π½ΡΡ Π½Π°Π΄ ΡΡΠΎΠ²Π½Π΅ΠΌ Π΄Π½Π° ΡΡΠ°Π½ΡΠ΅ΠΈ (ΠΊΠΎΡΠ»ΠΎΠ²Π°Π½Π°) Π½Π° Π½Π΅ΠΎΠ±Ρ ΠΎΠ΄ΠΈΠΌΡΡ Π²ΡΡΠΎΡΡ. ΠΠΎΠ»Π½ΡΡ Π±Π΅Π·Π³ΡΠ°ΠΌΠΎΡΠ½ΠΎΡΡΡ ΠΏΡΠΎΡΠ²Π»ΡΡΡ ΡΠ΅ Β«ΠΌΠ°ΡΡΠ΅ΡΠ°Β», ΠΊΠΎΡΠΎΡΡΠ΅ ΠΈΡΠΏΠΎΠ»ΡΠ·ΡΡΡ Π² ΠΊΠ°ΡΠ΅ΡΡΠ²Π΅ ΠΏΠΎΠ΄ΠΏΠΎΡΠΎΠΊ ΠΎΡΡΠ°Π²ΡΠΈΠ΅ΡΡ ΠΏΠΎΡΠ»Π΅ ΠΌΠΎΠ½ΡΠ°ΠΆΠ° ΠΎΠΏΠ°Π»ΡΠ±ΠΊΠΈ ΠΎΠ±ΡΠ΅Π·ΠΊΠΈ Π΄ΠΎΡΠΊΠΈ ΠΈΠ»ΠΈ Π±ΡΡΡΠ°. ΠΠ΅ΡΠ΅Π²ΠΎ, Π²ΠΎ-ΠΏΠ΅ΡΠ²ΡΡ , Π½Π΅Π΄ΠΎΠ»Π³ΠΎΠ²Π΅ΡΠ½ΠΎ, Π° Π²ΠΎ-Π²ΡΠΎΡΡΡ β Π½Π΅ ΡΡΠ°Π½Π΅Ρ ΠΏΡΠ΅Π³ΡΠ°Π΄ΠΎΠΉ Π΄Π»Ρ ΠΏΡΠΎΠ½ΠΈΠΊΠ½ΠΎΠ²Π΅Π½ΠΈΡ Π²Π»Π°Π³ΠΈ. Π Π² ΠΌΠ΅ΡΡΠ°Ρ ΡΠ°ΠΊΠΈΡ ΠΎΠΏΠΎΡ ΠΏΠΎΠ΄ ΠΏΠΎΠ΄ΠΎΡΠ²ΠΎΠΉ Π½Π΅ΠΈΠ·Π±Π΅ΠΆΠ½ΠΎ ΠΏΠΎΡΠ²ΡΡΡΡ ΠΎΡΠ°Π³ΠΈ ΡΠ°ΡΠΏΡΠΎΡΡΡΠ°Π½Π΅Π½ΠΈΡ ΠΊΠΎΡΡΠΎΠ·ΠΈΠΈ ΡΡΠ°Π»ΡΠ½ΠΎΠΉ Π°ΡΠΌΠ°ΡΡΡΡ.
ΠΠΎΠΏΡΡΡΠΈΠΌΡΠΉ, Π½ΠΎ, ΡΠΊΠ°ΠΆΠ΅ΠΌ ΠΏΡΡΠΌΠΎ, Π½Π΅ ΡΠ°ΠΌΡΠΉ ΠΈΠ΄Π΅Π°Π»ΡΠ½ΡΠΉ Π²Π°ΡΠΈΠ°Π½Ρ β ΠΈΡΠΏΠΎΠ»ΡΠ·ΠΎΠ²Π°ΡΡ Π΄Π»Ρ ΠΏΠΎΠ΄ΠΊΠ»Π°Π΄ΠΎΠΊ ΠΎΠ±Π»ΠΎΠΌΠΊΠΈ ΠΊΠΈΡΠΏΠΈΡΠ° ΠΈΠ»ΠΈ Π±Π΅ΡΠΎΠ½Π°. ΠΡΠ΅ ΡΠ°Π²Π½ΠΎ Β«Π³Π΅ΡΠΌΠ΅ΡΠΈΡΠ½ΠΎΡΡΡΒ» Π·Π°ΡΠΈΡΠ½ΠΎΠ³ΠΎ ΡΠ»ΠΎΡ Π² ΡΠΎΡΠΊΠ°Ρ
ΠΎΠΏΠΎΡΡ Π±ΡΠ΄Π΅Ρ Π½Π΅Π΄ΠΎΡΡΠ°ΡΠΎΡΠ½ΠΎΠΉ.
Π¦Π΅Π½Ρ Π½Π° Π±Π΅ΡΠΎΠ½ΠΎΠΌΠ΅ΡΠ°Π»ΠΊΡ
Π±Π΅ΡΠΎΠ½ΠΎΠΌΠ΅ΡΠ°Π»ΠΊΠ°
ΠΠΏΡΠΈΠΌΠ°Π»ΡΠ½ΡΠΌ Π²Π°ΡΠΈΠ°Π½ΡΠΎΠΌ Π²ΠΈΠ΄ΠΈΡΡΡ ΠΏΡΠΈΠΌΠ΅Π½Π΅Π½ΠΈΠ΅ ΡΠΏΠ΅ΡΠΈΠ°Π»ΡΠ½ΡΡ ΠΏΠΎΠ»ΠΈΠΌΠ΅ΡΠ½ΡΡ ΡΡΠΎΠ΅ΠΊ. ΠΠ½ΠΈ Π²ΡΠΏΡΡΠΊΠ°ΡΡΡΡ ΡΠ°Π·Π»ΠΈΡΠ½ΠΎΠΉ Π²ΡΡΠΎΡΡ, ΡΠΎ Π΅ΡΡΡ ΠΈΠΌΠ΅Π΅ΡΡΡ Π²ΠΎΠ·ΠΌΠΎΠΆΠ½ΠΎΡΡΡ ΠΏΠΎΠ΄ΠΎΠ±ΡΠ°ΡΡ ΠΈΠΌΠ΅Π½Π½ΠΎ ΡΠ°ΠΊΠΈΠ΅, ΠΊΠ°ΠΊΠΈΠ΅ ΡΡΠ΅Π±ΡΡΡΡΡ Π΄Π»Ρ Π΄Π°Π½Π½ΠΎΠΉ ΠΊΠΎΠ½ΡΡΡΡΠΊΡΠΈΠΈ. Π‘ΡΠΎΠΈΠΌΠΎΡΡΡ ΠΈΡ , ΠΎΡΠΎΠ±Π΅Π½Π½ΠΎ Π½Π° ΡΠΎΠ½Π΅ ΠΎΠ±ΡΠΈΡ Π·Π°ΡΡΠ°Ρ Π½Π° ΡΠΎΠ·Π΄Π°Π½ΠΈΠ΅ ΡΡΠ½Π΄Π°ΠΌΠ΅Π½ΡΠ° β ΡΠΎΠ²ΡΠ΅ΠΌ Π½Π΅Π²Π΅Π»ΠΈΠΊΠ°. ΠΠΎ Π·Π°ΡΠΎ ΠΎΠ½ΠΈ ΠΈΠΌΠ΅Ρ ΠΏΠΎΠ»ΡΡ ΠΊΠΎΠ½ΡΡΡΡΠΊΡΠΈΡ, ΠΊΠΎΡΠΎΡΠ°Ρ ΡΠ°ΠΊΠΆΠ΅ Π·Π°ΠΏΠΎΠ»Π½ΠΈΡΡΡ Π±Π΅ΡΠΎΠ½ΠΎΠΌ ΠΏΡΠΈ Π·Π°Π»ΠΈΠ²ΠΊΠ΅, ΠΈ Π°ΡΠΌΠ°ΡΡΡΠ° Π±ΡΠ΄Π΅Ρ Β«Π·Π°ΠΏΠ΅ΡΠ°ΡΠ°Π½Π°Β» Π±Π΅ΡΠΎΠ½ΠΎΠΌ ΠΏΠΎ Π²ΡΠ΅ Π΄Π»ΠΈΠ½Π΅.
Π‘ΠΏΠ΅ΡΠΈΠ°Π»ΡΠ½ΡΠΉ ΡΠ»Π΅ΠΌΠ΅Π½Ρ β ΠΏΠ»Π°ΡΡΠΈΠΊΠΎΠ²Π°Ρ ΡΡΠΎΠΉΠΊΠ°-Β«ΡΡΠ°ΠΊΠ°Π½Β», ΠΎΠ±Π΅ΡΠΏΠ΅ΡΠΈΠ²Π°ΡΡΠ°Ρ ΡΡΠ΅Π±ΡΠ΅ΠΌΡΡ ΡΠΎΠ»ΡΠΈΠ½Ρ Π·Π°ΡΠΈΡΠ½ΠΎΠ³ΠΎ ΡΠ»ΠΎΡ ΡΠΎ ΡΡΠΎΡΠΎΠ½Ρ ΠΏΠΎΠ΄ΠΎΡΠ²Ρ ΡΡΠ½Π΄Π°ΠΌΠ΅Π½ΡΠ°. ΠΠ°Π²Π΅ΡΠ½ΠΎΠ΅, ΡΠ°ΠΌΠΎΠ΅ ΠΏΡΠ°ΠΊΡΠΈΡΠ½ΠΎΠ΅ ΠΈ Π½Π°Π΄Π΅ΠΆΠ½ΠΎΠ΅ ΡΠ΅ΡΠ΅Π½ΠΈΠ΅ ΠΏΡΠΎΠ±Π»Π΅ΠΌΡ.ΠΠ½Π°Π»ΠΎΠ³ΠΈΡΠ½ΡΠΌ ΠΎΠ±ΡΠ°Π·ΠΎΠΌ ΡΠ΄ΠΎΠ±Π½Π΅Π΅ Π²ΡΠ΅Π³ΠΎ ΠΏΠΎΡΡΡΠΏΠΈΡΡ ΠΈ Π΄Π»Ρ ΡΠΎΠ·Π΄Π°Π½ΠΈΡ Π½Π΅ΠΎΠ±Ρ
ΠΎΠ΄ΠΈΠΌΠΎΠ³ΠΎ ΠΏΡΠΎΡΠ²Π΅ΡΠ° ΠΌΠ΅ΠΆΠ΄Ρ Π²Π½Π΅ΡΠ½ΠΈΠΌΠΈ ΠΏΡΠΎΠ΄ΠΎΠ»ΡΠ½ΡΠΌΠΈ ΠΏΡΡΡΡΡΠΌΠΈ ΠΈ ΡΡΠ΅ΠΊΠ°ΠΌΠΈ ΠΎΠΏΠ°Π»ΡΠ±ΠΊΠΈ. ΠΡΠΈ Π·Π°Π»ΠΈΠ²ΠΊΠ΅ Π²Π΅ΡΡΠΌΠ° ΡΡΠΆΠ΅Π»ΠΎΠ²Π΅ΡΠ½ΠΎΠ³ΠΎ Π±Π΅ΡΠΎΠ½Π½ΠΎΠ³ΠΎ ΡΠ°ΡΡΠ²ΠΎΡΠ° ΠΊΠ°ΡΠΊΠ°Ρ ΠΌΠΎΠΆΠ΅Ρ ΡΠΌΠ΅ΡΡΠΈΡΡΡΡ, ΠΈ Π΅Π³ΠΎ ΡΡΠ΅Π±ΡΠ΅ΡΡΡ Π½Π°Π΄Π΅ΠΆΠ½ΠΎ Π·Π°ΡΠΈΠΊΡΠΈΡΠΎΠ²Π°ΡΡ Π² ΠΎΠΏΡΠ΅Π΄Π΅Π»Π΅Π½Π½ΠΎΠΌ ΠΏΠΎΠ»ΠΎΠΆΠ΅Π½ΠΈΠΈ. ΠΠ»Ρ ΡΡΠΎΠ³ΠΎ ΠΏΡΠΈΠΌΠ΅Π½ΡΡΡΡΡ ΡΠΏΠ΅ΡΠΈΠ°Π»ΡΠ½ΡΠ΅ ΡΠΈΠΊΡΠ°ΡΠΎΡΡβΒ«Π·Π²Π΅Π·Π΄ΠΎΡΠΊΠΈΒ» ΡΡΠ΅Π±ΡΠ΅ΠΌΠΎΠ³ΠΎ ΡΠ°Π΄ΠΈΡΡΠ°. Π£ΡΡΠ°Π½Π°Π²Π»ΠΈΠ²Π°ΡΡΡΡ ΠΎΠ½ΠΈ Π±ΡΠΊΠ²Π°Π»ΡΠ½ΠΎ ΠΎΠ΄Π½ΠΈΠΌ Π΄Π²ΠΈΠΆΠ΅Π½ΠΈΠ΅ΠΌ, ΠΈ ΠΏΡΠΎΠ±Π»Π΅ΠΌΠ° ΡΠ΅ΡΠ°Π΅ΡΡΡ ΡΠ°ΠΌΠ° ΡΠΎΠ±ΠΎΠΉ.
Π§ΡΠΎ ΠΌΠΎΠΆΠ΅Ρ Π±ΡΡΡ ΠΏΡΠΎΡΠ΅ β ΡΡΡΠ°Π½ΠΎΠ²ΠΈΡΡ Β«Π·Π²Π΅Π·Π΄ΠΎΡΠΊΠΈΒ»-ΡΠΈΠΊΡΠ°ΡΠΎΡΡ, ΠΈ Π½Π΅ΠΎΠ±Ρ ΠΎΠ΄ΠΈΠΌΡΠΉ ΠΏΡΠΎΡΠ²Π΅Ρ ΠΌΠ΅ΠΆΠ΄Ρ Π°ΡΠΌΠ°ΡΡΡΠΎΠΉ ΠΈ ΠΎΠΏΠ°Π»ΡΠ±ΠΊΠΎΠΉ Π½Π΅ Π½Π°ΡΡΡΠΈΡΡΡ ΠΏΡΠΈ Π·Π°Π»ΠΈΠ²ΠΊΠ΅ Π±Π΅ΡΠΎΠ½Π½ΠΎΠ³ΠΎ ΡΠ°ΡΡΠ²ΠΎΡΠ°.ΠΠ·Π½Π°ΠΊΠΎΠΌΡΡΠ΅ΡΡ Ρ ΠΎΡΠΎΠ±Π΅Π½Π½ΠΎΡΡΡΠΌΠΈ Π²ΡΠΏΠΎΠ»Π½Π΅Π½ΠΈΡ ΡΠ°Π±ΠΎΡ, ΠΊΠ°ΠΊ Π·Π°Π»ΠΈΠ²Π°ΡΡ ΡΡΠ½Π΄Π°ΠΌΠ΅Π½Ρ Π·ΠΈΠΌΠΎΠΉ, ΠΈΠ· Π½Π°ΡΠ΅ΠΉ Π½ΠΎΠ²ΠΎΠΉ ΡΡΠ°ΡΡΠΈ Π½Π° Π½Π°ΡΠ΅ΠΌ ΠΏΠΎΡΡΠ°Π»Π΅.
ΠΡΡΠ°ΡΠΈ, ΠΌΠΎΠΆΠ½ΠΎ ΠΏΠΎΡΠΌΠΎΡΡΠ΅ΡΡ ΠΈΠ½ΡΠ΅ΡΠ΅ΡΠ½ΡΠΉ Π²ΠΈΠ΄Π΅ΠΎΡΡΠΆΠ΅Ρ, Π² ΠΊΠΎΡΠΎΡΠΎΠΌ ΠΌΠ°ΡΡΠ΅Ρ Π΄Π΅Π»ΠΈΡΡΡ ΡΠ΅ΠΊΡΠ΅ΡΠΎΠΌ ΡΠ°ΠΌΠΎΡΡΠΎΡΡΠ΅Π»ΡΠ½ΠΎΠ³ΠΎ ΠΈΠ·Π³ΠΎΡΠΎΠ²Π»Π΅Π½ΠΈΡ Π±Π΅ΡΠΎΠ½Π½ΡΡ ΡΠΈΠΊΡΠ°ΡΠΎΡΠΎΠ² Π΄Π»Ρ Π°ΡΠΌΠ°ΡΡΡΡ. ΠΡΠ΅Π½Ρ Π½Π΅ΠΏΠ»ΠΎΡ ΠΎΠΉ Π²Π°ΡΠΈΠ°Π½Ρ Π² ΡΠ΅Ρ ΡΠ»ΡΡΠ°ΡΡ , ΠΊΠΎΠ³Π΄Π° Π½Π΅Ρ Π²ΠΎΠ·ΠΌΠΎΠΆΠ½ΠΎΡΡΠΈ ΠΏΡΠΈΠΎΠ±ΡΠ΅ΡΡΠΈ ΡΠΏΠ΅ΡΠΈΠ°Π»ΡΠ½ΡΠ΅ Β«ΡΡΠ°ΠΊΠ°Π½ΡΒ» ΠΈΠ»ΠΈ Β«Π·Π²Π΅Π·Π΄ΠΎΡΠΊΠΈΒ».
ΠΠΈΠ΄Π΅ΠΎ: ΠΠ°ΠΊ ΠΌΠΎΠΆΠ½ΠΎ ΡΠ°ΠΌΠΎΡΡΠΎΡΡΠ΅Π»ΡΠ½ΠΎ ΠΈΠ·Π³ΠΎΡΠΎΠ²ΠΈΡΡ ΡΠΈΠΊΡΠ°ΡΠΎΡΡ Π΄Π»Ρ Π·Π°Π΄Π°Π½ΠΈΡ Π·Π°ΡΠΈΡΠ½ΠΎΠ³ΠΎ Π±Π΅ΡΠΎΠ½Π½ΠΎΠ³ΠΎ ΡΠ»ΠΎΡΠΠ΅ΠΏΠΎΡΡΠ΅Π΄ΡΡΠ²Π΅Π½Π½ΠΎ ΠΏΠ΅ΡΠ΅Π΄ Π·Π°Π»ΠΈΠ²ΠΊΠΎΠΉ Π±Π΅ΡΠΎΠ½Π°, ΠΏΠΎΡΠ»Π΅ ΠΎΠΊΠΎΠ½ΡΠ°Π½ΠΈΡ ΠΌΠΎΠ½ΡΠ°ΠΆΠ° Π°ΡΠΌΠ°ΡΡΡΠ½ΠΎΠ³ΠΎ ΠΊΠ°ΡΠΊΠ°ΡΠ°, ΠΈΠΌΠ΅Π΅Ρ ΡΠΌΡΡΠ» Π΅ΡΠ΅ ΡΠ°Π· Π²Π½ΠΈΠΌΠ°ΡΠ΅Π»ΡΠ½ΠΎ ΠΎΡΠΌΠΎΡΡΠ΅ΡΡ ΡΠΎΠ·Π΄Π°Π½Π½ΡΡ ΠΊΠΎΠ½ΡΡΡΡΠΊΡΠΈΡ. Π‘Π»ΡΡΠ°Π΅ΡΡΡ, ΡΡΠΎ ΠΊΠ°ΠΊΠΎΠΉ-Π»ΠΈΠ±ΠΎ ΠΏΠΎΠΏΠ΅ΡΠ΅ΡΠ½ΡΠΉ ΠΊΠΎΠ½ΡΡΡΡΠΊΡΠΈΠ²Π½ΡΠΉ ΠΏΡΡΡ ΡΠ²ΠΎΠΈΠΌ ΡΠΎΡΡΠΎΠΌ Β«ΠΎΠΏΠ°ΡΠ½ΠΎ ΠΏΡΠΈΠ±Π»ΠΈΠΆΠ°Π΅ΡΡΡΒ» ΠΊ ΡΡΠ΅Π½ΠΊΠ°ΠΌ ΠΎΠΏΠ°Π»ΡΠ±ΠΊΠΈ. ΠΡΡΡΠ΅ ΡΡΠΎ ΡΡΡΡΠ°Π½ΠΈΡΡ ΡΡΠ°Π·Ρ β ΠΏΠΎΠ΄ΡΠ΅Π·Π°ΡΡ Π΅Π³ΠΎ Π΄Π»Ρ Π·Π°Π΄Π°Π½ΠΈΡ ΡΡΠ΅Π±ΡΠ΅ΠΌΠΎΠ³ΠΎ ΠΏΡΠΎΡΠ²Π΅ΡΠ°. Π ΠΏΡΠΎΡΠΈΠ²Π½ΠΎΠΌ ΡΠ»ΡΡΠ°Π΅ ΠΈΠΌΠ΅Π½Π½ΠΎ Π² ΡΡΠΎΠΉ ΡΠΎΡΠΊΠ΅ ΠΌΠΎΠΆΠ΅Ρ ΠΎΠ±ΡΠ°Π·ΠΎΠ²Π°ΡΡΡΡ ΡΠΊΠΎΠ» Π±Π΅ΡΠΎΠ½Π½ΠΎΠΉ ΠΏΠΎΠ²Π΅ΡΡ
Π½ΠΎΡΡΠΈ, ΠΏΠΎΡΠ²ΠΈΡΡΡΡ ΠΏΠΎΠ²Π΅ΡΡ
Π½ΠΎΡΡΠ½Π°Ρ ΡΡΠ΅ΡΠΈΠ½Π°. Π Ρ
ΠΎΡΠΎΡΠΎ, Π΅ΡΠ»ΠΈ ΡΡΠΈΠΌ Π²ΡΠ΅ ΠΎΠ³ΡΠ°Π½ΠΈΡΠΈΡΡΡ β Ρ
ΡΠΆΠ΅, ΠΊΠΎΠ³Π΄Π° ΡΠ°ΠΊΠΎΠΉ ΡΡΠ°ΡΡΠΎΠΊ ΡΡΠ°Π½ΠΎΠ²ΠΈΡΡΡ ΠΎΡΠ°Π³ΠΎΠΌ ΡΠ°ΡΠΏΡΠΎΡΡΡΠ°Π½Π΅Π½ΠΈΡ ΠΌΠ°ΡΡΡΠ°Π±Π½ΠΎΠΉ ΡΡΠΎΠ·ΠΈΠΈ Π±Π΅ΡΠΎΠ½Π°.
* Β *Β *Β *Β *Β *Β *
ΠΡΠ°ΠΊ, Π΄Π»Ρ ΡΠΎΠ³ΠΎ ΡΡΠΎΠ±Ρ ΡΠΎΠ·Π΄Π°ΡΡ ΡΠ°Π²Π½ΠΎΠΌΠ΅ΡΠ½ΡΠΉ Π·Π°ΡΠΈΡΠ½ΡΠΉ Π±Π΅ΡΠΎΠ½Π½ΡΠΉ ΡΠ»ΠΎΠΉ, Π½Π΅ΠΎΠ±Ρ
ΠΎΠ΄ΠΈΠΌΠΎ Π²ΡΡΡΠ°Π²ΠΈΡΡ Π°ΡΠΌΠΈΡΡΡΡΠΈΠΉ ΠΊΠ°ΡΠΊΠ°Ρ Ρ ΡΡΠ΅ΡΠΎΠΌ ΡΡΡΠ°Π½ΠΎΠ²Π»Π΅Π½Π½ΡΡ
Π½ΠΎΡΠΌ, ΡΠΎ Π΅ΡΡΡ ΡΠ°Π·ΠΌΠ΅ΡΡΠΈΡΡ Π°ΡΠΌΠ°ΡΡΡΠ½ΡΠ΅ ΠΏΡΡΡΡ Π½Π° Π·Π°Π΄Π°Π½Π½ΠΎΠΌ ΡΠ°ΡΡΡΠΎΡΠ½ΠΈΠΈ ΠΎΡΠΎ Π΄Π½Π° ΠΈ ΠΎΡ ΡΡΠ΅Π½ΠΎΠΊ ΠΎΠΏΠ°Π»ΡΠ±ΠΊΠΈ. ΠΡΠΈ Π·Π°Π»ΠΈΠ²ΠΊΠ΅ Π±Π΅ΡΠΎΠ½Π½ΠΎΠ³ΠΎ ΡΠ°ΡΡΠ²ΠΎΡΠ°, Π΅Π³ΠΎ Π½Π΅ΠΎΠ±Ρ
ΠΎΠ΄ΠΈΠΌΠΎ ΠΌΠ°ΠΊΡΠΈΠΌΠ°Π»ΡΠ½ΠΎ ΡΠ°Π²Π½ΠΎΠΌΠ΅ΡΠ½ΠΎ ΠΈ ΠΏΠ»ΠΎΡΠ½ΠΎ ΡΠ°ΡΠΏΡΠ΅Π΄Π΅Π»ΠΈΡΡ ΠΏΠΎ Π²ΡΠ΅ΠΉ Π΅ΠΌΠΊΠΎΡΡΠΈ ΠΎΠΏΠ°Π»ΡΠ±ΠΊΠΈ. ΠΡΠΈΠΌ ΠΎΠ±Π΅ΡΠΏΠ΅ΡΠΈΡΡΡ ΡΠ°Π²Π½ΠΎΠΌΠ΅ΡΠ½ΠΎΠ΅ ΡΠ°ΡΠΏΡΠ΅Π΄Π΅Π»Π΅Π½ΠΈΠ΅ Π½Π°Π³ΡΡΠ·ΠΎΠΊ, Π° ΠΌΠ΅ΡΠ°Π»Π» Π°ΡΠΌΠ°ΡΡΡΠ½ΠΎΠ³ΠΎ Β«ΡΠΊΠ΅Π»Π΅ΡΠ°Β» Π±ΡΠ΄Π΅Ρ Π΄ΠΎΠ»ΠΆΠ½ΡΠΌ ΠΎΠ±ΡΠ°Π·ΠΎΠΌ Π·Π°ΡΠΈΡΠ΅Π½ ΠΎΡ Π²Π½Π΅ΡΠ½ΠΈΡ
Π²ΠΎΠ·Π΄Π΅ΠΉΡΡΠ²ΠΈΠΉ, Π° Π·Π½Π°ΡΠΈΡ β ΠΈ ΠΎΡ Π²ΠΎΠ·Π½ΠΈΠΊΠ½ΠΎΠ²Π΅Π½ΠΈΡ ΠΎΡΠ°Π³ΠΎΠ² ΠΊΠΎΡΡΠΎΠ·ΠΈΠΈ. Π ΡΡΠΎ, Π² ΡΠ²ΠΎΡ ΠΎΡΠ΅ΡΠ΅Π΄Ρ β Π·Π°Π»ΠΎΠ³ ΠΎΠ±ΡΠ΅ΠΉ Π΄ΠΎΠ»Π³ΠΎΠ²Π΅ΡΠ½ΠΎΡΡΠΈ ΠΈ Π½Π°Π΄Π΅ΠΆΠ½ΠΎΡΡΠΈ Π²ΡΠ΅Π³ΠΎ ΡΡΠ½Π΄Π°ΠΌΠ΅Π½ΡΠ° Π² ΡΠ΅Π»ΠΎΠΌ.
ΠΠΈΠ½ΠΈΠΌΠ°Π»ΡΠ½ΠΎΠ΅ Π±Π΅ΡΠΎΠ½Π½ΠΎΠ΅ ΠΏΠΎΠΊΡΡΡΠΈΠ΅ Π΄Π»Ρ Π°ΡΠΌΠΈΡΠΎΠ²Π°Π½ΠΈΡ
π ΠΡΠ΅ΠΌΡ ΡΡΠ΅Π½ΠΈΡ: 1 ΠΌΠΈΠ½ΡΡΠ°
ΠΠ΅ΡΠΎΠ½Π½ΠΎΠ΅ ΠΏΠΎΠΊΡΡΡΠΈΠ΅ Π΄Π»Ρ Π°ΡΠΌΠΈΡΠΎΠ²Π°Π½ΠΈΡ ΡΡΠ΅Π±ΡΠ΅ΡΡΡ Π΄Π»Ρ Π·Π°ΡΠΈΡΡ Π°ΡΠΌΠ°ΡΡΡΡ ΠΎΡ ΠΊΠΎΡΡΠΎΠ·ΠΈΠΈ ΠΈ ΠΎΠ±Π΅ΡΠΏΠ΅ΡΠ΅Π½ΠΈΡ ΠΎΠ³Π½Π΅ΡΡΠΎΠΉΠΊΠΎΡΡΠΈ. Π’ΠΎΠ»ΡΠΈΠ½Π° ΠΏΠΎΠΊΡΡΡΠΈΡ Π·Π°Π²ΠΈΡΠΈΡ ΠΎΡ ΡΡΠ»ΠΎΠ²ΠΈΠΉ ΠΎΠΊΡΡΠΆΠ°ΡΡΠ΅ΠΉ ΡΡΠ΅Π΄Ρ ΠΈ ΡΠΈΠΏΠ° ΡΠ»Π΅ΠΌΠ΅Π½ΡΠ° ΠΊΠΎΠ½ΡΡΡΡΠΊΡΠΈΠΈ. ΠΠΈΠ½ΠΈΠΌΠ°Π»ΡΠ½Π°Ρ ΡΠΎΠ»ΡΠΈΠ½Π° Π·Π°ΡΠΈΡΠ½ΠΎΠ³ΠΎ ΡΠ»ΠΎΡ Π°ΡΠΌΠ°ΡΡΡΡ ΡΠΊΠ°Π·Π°Π½Π° Π½Π° ΡΠ΅ΡΡΠ΅ΠΆΠ°Ρ ΠΈΠ»ΠΈ Π΄ΠΎΠ»ΠΆΠ½Π° Π±ΡΡΡ ΠΏΠΎΠ»ΡΡΠ΅Π½Π° ΠΈΠ· ΡΠΎΠΎΡΠ²Π΅ΡΡΡΠ²ΡΡΡΠΈΡ ΡΠ²ΠΎΠ΄ΠΎΠ² ΠΏΡΠ°Π²ΠΈΠ». ΠΠΈΠΆΠ΅ ΠΏΡΠΈΠ²Π΅Π΄Π΅Π½Ρ Ρ Π°ΡΠ°ΠΊΡΠ΅ΡΠΈΡΡΠΈΠΊΠΈ Π°ΡΠΌΠ°ΡΡΡΠ½ΠΎΠ³ΠΎ ΠΏΠΎΠΊΡΡΡΠΈΡ Π΄Π»Ρ ΡΠ°Π·Π»ΠΈΡΠ½ΡΡ ΡΠ»Π΅ΠΌΠ΅Π½ΡΠΎΠ² ΠΊΠΎΠ½ΡΡΡΡΠΊΡΠΈΠΈ Π² ΡΠ°Π·Π»ΠΈΡΠ½ΡΡ ΡΡΠ»ΠΎΠ²ΠΈΡΡ . Π°) ΠΠ° ΠΊΠ°ΠΆΠ΄ΠΎΠΌ ΠΊΠΎΠ½ΡΠ΅ Π°ΡΠΌΠ°ΡΡΡΠ½ΠΎΠ³ΠΎ ΡΡΠ΅ΡΠΆΠ½Ρ Π΄ΠΎΠ»ΠΆΠ½ΠΎ Π±ΡΡΡ ΠΏΡΠ΅Π΄ΡΡΠΌΠΎΡΡΠ΅Π½ΠΎ Π·Π°ΡΠΈΡΠ½ΠΎΠ΅ ΠΏΠΎΠΊΡΡΡΠΈΠ΅ ΡΠΎΠ»ΡΠΈΠ½ΠΎΠΉ Π½Π΅ ΠΌΠ΅Π½Π΅Π΅ 25 ΠΌΠΌ ΠΈΠ»ΠΈ ΠΌΠ΅Π½Π΅Π΅ ΡΠ΅ΠΌ Π² Π΄Π²Π° ΡΠ°Π·Π° Π±ΠΎΠ»ΡΡΠ΅ Π΄ΠΈΠ°ΠΌΠ΅ΡΡΠ° ΡΡΠ΅ΡΠΆΠ½Ρ. Π±) ΠΠ»Ρ ΠΏΡΠΎΠ΄ΠΎΠ»ΡΠ½ΠΎΠ³ΠΎ Π°ΡΠΌΠ°ΡΡΡΠ½ΠΎΠ³ΠΎ ΡΡΠ΅ΡΠΆΠ½Ρ Π² ΠΊΠΎΠ»ΠΎΠ½Π½Π΅ ΡΠ»Π΅Π΄ΡΠ΅Ρ ΠΏΡΠ΅Π΄ΡΡΠΌΠ°ΡΡΠΈΠ²Π°ΡΡ Π·Π°ΡΠΈΡΠ½ΡΠΉ ΡΠ»ΠΎΠΉ Π±Π΅ΡΠΎΠ½Π° Π½Π΅ ΠΌΠ΅Π½Π΅Π΅ 40 ΠΌΠΌ ΠΈ Π½Π΅ ΠΌΠ΅Π½Π΅Π΅ Π΄ΠΈΠ°ΠΌΠ΅ΡΡΠ° ΡΠ°ΠΊΠΎΠ³ΠΎ ΡΡΠ΅ΡΠΆΠ½Ρ. Π ΡΠ»ΡΡΠ°Π΅ ΠΊΠΎΠ»ΠΎΠ½Π½ ΠΌΠΈΠ½ΠΈΠΌΠ°Π»ΡΠ½ΠΎΠ³ΠΎ ΡΠ°Π·ΠΌΠ΅ΡΠ° 20 ΡΠΌ ΠΈΠ»ΠΈ ΠΌΠ΅Π½Π΅Π΅, Ρ ΠΊΠΎΡΠΎΡΡΡ Π°ΡΠΌΠ°ΡΡΡΠ½ΡΠ΅ ΡΡΠ΅ΡΠΆΠ½ΠΈ Π½Π΅ ΠΏΡΠ΅Π²ΡΡΠ°ΡΡ 12 ΠΌΠΌ, Π΄Π»Ρ Π°ΡΠΌΠΈΡΠΎΠ²Π°Π½ΠΈΡ ΡΠ»Π΅Π΄ΡΠ΅Ρ ΠΈΡΠΏΠΎΠ»ΡΠ·ΠΎΠ²Π°ΡΡ Π±Π΅ΡΠΎΠ½Π½ΠΎΠ΅ ΠΏΠΎΠΊΡΡΡΠΈΠ΅ ΡΠΎΠ»ΡΠΈΠ½ΠΎΠΉ 25 ΠΌΠΌ.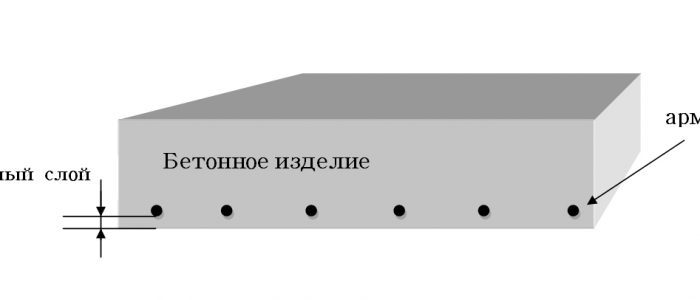
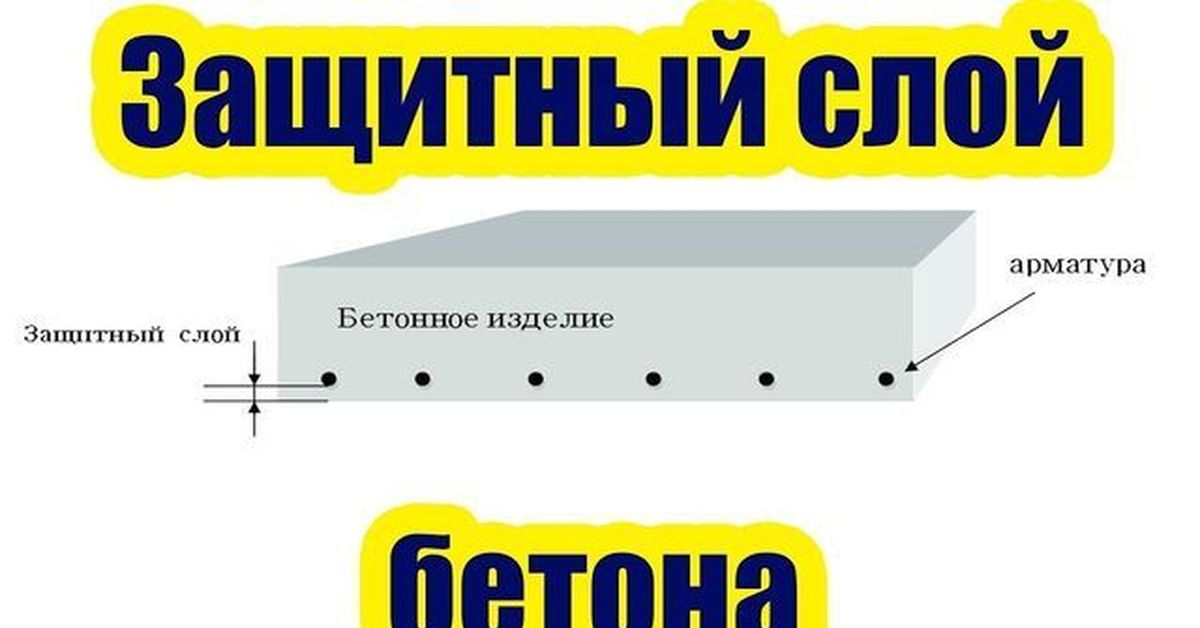
ΠΠ΅ΡΠΎΠ½Π½ΡΠ΅ Π·Π°ΡΠΈΡΠ½ΡΠ΅ ΠΏΠΎΠΊΡΡΡΠΈΡ Π΄Π»Ρ ΠΆΠ΅Π»Π΅Π·ΠΎΠ±Π΅ΡΠΎΠ½Π½ΡΡ ΠΊΠΎΠ½ΡΡΡΡΠΊΡΠΈΠΉ
Π.
ΠΠ²Π΅Π΄Π΅Π½ΠΈΠ΅
ΠΠ΅Π»Π΅Π·ΠΎΠ±Π΅ΡΠΎΠ½ β ΠΊΠΎΠΌΠΏΠΎΠ·ΠΈΡΠ½ΡΠΉ ΠΌΠ°ΡΠ΅ΡΠΈΠ°Π». ΠΠ³ΠΎ ΡΡΡΡΠΊΡΡΡΠ½ΡΠ΅ Ρ Π°ΡΠ°ΠΊΡΠ΅ΡΠΈΡΡΠΈΠΊΠΈ ΡΠ΅Π°Π»ΠΈΠ·ΡΡΡΡΡ ΡΠΎΠ»ΡΠΊΠΎ ΡΠΎΠ³Π΄Π°, ΠΊΠΎΠ³Π΄Π° Π±Π΅ΡΠΎΠ½ ΠΈ ΡΡΠ°Π»Ρ Π΄Π΅ΠΉΡΡΠ²ΡΡΡ Π² ΡΠ½ΠΈΡΠΎΠ½ Π² ΡΠ΅ΡΠ΅Π½ΠΈΠ΅ ΡΡΠΎΠΊΠ° ΡΠ»ΡΠΆΠ±Ρ ΠΊΠΎΠ½ΡΡΡΡΠΊΡΠΈΠΈ. Π‘ΠΆΠΈΠΌΠ°ΡΡΠΈΠ΅ ΠΈ ΡΠ°ΡΡΡΠ³ΠΈΠ²Π°ΡΡΠΈΠ΅ Π½Π°Π³ΡΡΠ·ΠΊΠΈ Π²ΠΎΡΠΏΡΠΈΠ½ΠΈΠΌΠ°ΡΡΡΡ Π±Π΅ΡΠΎΠ½ΠΎΠΌ ΠΈ ΡΡΠ°Π»ΡΡ ΡΠΎΠΎΡΠ²Π΅ΡΡΡΠ²Π΅Π½Π½ΠΎ. Π‘ΡΠ°Π»Ρ Π·Π°ΡΠΈΡΠ°Π΅Ρ Π±Π΅ΡΠΎΠ½ ΠΎΡ ΡΠ°ΡΡΡΠ΅ΡΠΊΠΈΠ²Π°Π½ΠΈΡ ΠΏΠΎΠ΄ Π΄Π΅ΠΉΡΡΠ²ΠΈΠ΅ΠΌ ΡΠ°ΡΡΡΠ³ΠΈΠ²Π°ΡΡΠΈΡ Π½Π°Π³ΡΡΠ·ΠΎΠΊ, Π° Π±Π΅ΡΠΎΠ½ Π·Π°ΡΠΈΡΠ°Π΅Ρ ΡΡΠ°Π»Ρ ΠΎΡ ΠΊΠΎΡΡΠΎΠ·ΠΈΠΈ, ΡΠΎΠ·Π΄Π°Π²Π°Ρ Π²ΠΎΠΊΡΡΠ³ Π½Π΅Π΅ ΡΠ΅Π»ΠΎΡΠ½ΡΡ ΡΡΠ΅Π΄Ρ. ΠΠΎΠΊΠ° ΡΡΠΎ ΠΏΡΠΎΠΈΡΡ ΠΎΠ΄ΠΈΡ, ΠΆΠ΅Π»Π΅Π·ΠΎΠ±Π΅ΡΠΎΠ½Π½ΡΠ΅ ΠΊΠΎΠ½ΡΡΡΡΠΊΡΠΈΠΈ ΡΠ°Π±ΠΎΡΠ°ΡΡ ΡΠ΄ΠΎΠ²Π»Π΅ΡΠ²ΠΎΡΠΈΡΠ΅Π»ΡΠ½ΠΎ. ΠΠ΅ΡΠΌΠΎΡΡΡ Π½Π° ΡΠΎ, ΡΡΠΎ Π±Π΅ΡΠΎΠ½ ΠΌΠΎΠΆΠ΅Ρ Π±ΡΡΡ ΠΎΡΠ΅Π½Ρ ΠΏΡΠΎΡΠ½ΡΠΌ ΠΌΠ°ΡΠ΅ΡΠΈΠ°Π»ΠΎΠΌ, ΠΎΠ½ ΡΠ°ΠΊΠΆΠ΅ ΠΏΠΎΠ΄Π²Π΅ΡΠΆΠ΅Π½ ΠΈΠ·Π½ΠΎΡΡ. ΠΠ΅ΡΠΎΠ½ ΠΌΠΎΠΆΠ΅Ρ Π±ΡΡΡ ΠΏΠΎΡΠΈΡΡΡΠΌ, ΠΏΠΎΡΡΠΎΠΌΡ Ρ ΠΈΠΌΠΈΡΠ΅ΡΠΊΠΈΠ΅ Π²Π΅ΡΠ΅ΡΡΠ²Π° ΠΌΠΎΠ³ΡΡ ΠΏΡΠΎΠ½ΠΈΠΊΠ°ΡΡ Π² ΠΏΠΎΡΡ ΠΈ Π²ΠΎΠ·Π΄Π΅ΠΉΡΡΠ²ΠΎΠ²Π°ΡΡ Π½Π° ΠΏΠ°ΡΡΡ. ΠΠ°ΡΡΠ° ΠΈ Π·Π°ΠΏΠΎΠ»Π½ΠΈΡΠ΅Π»Ρ ΡΠ°ΠΊΠΆΠ΅ ΠΌΠΎΠ³ΡΡ ΠΈΠ·Π½Π°ΡΠΈΠ²Π°ΡΡΡΡ ΠΏΡΠΈ ΡΠΈΠ·ΠΈΡΠ΅ΡΠΊΠΎΠΌ Π²ΠΎΠ·Π΄Π΅ΠΉΡΡΠ²ΠΈΠΈ ΠΈ ΠΈΡΡΠΈΡΠ°Π½ΠΈΠΈ. ΠΠΎΠ΄Π° ΠΌΠΎΠΆΠ΅Ρ ΠΏΡΠΎΠ½ΠΈΠΊΠ°ΡΡ Π² Π±Π΅ΡΠΎΠ½, Π·Π°ΠΌΠ΅ΡΠ·Π°ΡΡ ΠΈ ΡΠ°ΡΡΠΈΡΡΡΡΡΡ Π²Π½ΡΡΡΠΈ Π½Π΅Π³ΠΎ ΠΏΡΠΈ ΠΏΠΎΠ½ΠΈΠΆΠ΅Π½ΠΈΠΈ ΡΠ΅ΠΌΠΏΠ΅ΡΠ°ΡΡΡΡ ΠΈ Π² ΠΊΠΎΠ½Π΅ΡΠ½ΠΎΠΌ ΠΈΡΠΎΠ³Π΅ ΠΎΡΠ»Π°Π±Π»ΡΡΡ Π±Π΅ΡΠΎΠ½ ΠΈΠ·Π½ΡΡΡΠΈ.
Β
Π Π°Π·Π»ΠΈΡΠ½ΡΠ΅ Π²Π½Π΅ΡΠ½ΠΈΠ΅ Π°Π³ΡΠ΅ΡΡΠΈΠ²Π½ΡΠ΅ Π²Π΅ΡΠ΅ΡΡΠ²Π° ΠΎΠΊΡΡΠΆΠ°ΡΡΠ΅ΠΉ ΡΡΠ΅Π΄Ρ, ΡΠ°ΠΊΠΈΠ΅ ΠΊΠ°ΠΊ Π²ΠΎΠ΄Π°, ΡΠ³Π»Π΅ΠΊΠΈΡΠ»ΡΠΉ Π³Π°Π·, ΠΊΠΈΡΠ»ΠΎΡΠΎΠ΄, Ρ Π»ΠΎΡΠΈΠ΄Ρ, ΡΡΠ»ΡΡΠΈΠ΄Ρ ΠΈ Π±ΠΈΠΎΠ»ΠΎΠ³ΠΈΡΠ΅ΡΠΊΠΈΠ΅ ΠΎΡΠ³Π°Π½ΠΈΠ·ΠΌΡ ΠΏΠ΅ΡΠ΅Π½ΠΎΡΡΡΡΡ ΠΈΠ· Π°ΡΠΌΠΎΡΡΠ΅ΡΡ Π² Π±Π΅ΡΠΎΠ½ ΠΈ Π²ΠΎΠ·Π΄Π΅ΠΉΡΡΠ²ΡΡΡ Π½Π° ΡΡΠ°Π»Ρ ΠΈ Π±Π΅ΡΠΎΠ½ ΡΠ°Π·Π»ΠΈΡΠ½ΡΠΌΠΈ ΠΌΠ΅Ρ Π°Π½ΠΈΠ·ΠΌΠ°ΠΌΠΈ, Π²ΡΠ·ΡΠ²Π°Ρ ΠΏΡΠ΅ΠΆΠ΄Π΅Π²ΡΠ΅ΠΌΠ΅Π½Π½ΡΠΉ ΠΈΠ·Π½ΠΎΡ ΠΆΠ΅Π»Π΅Π·ΠΎΠ±Π΅ΡΠΎΠ½Π°, Π²ΡΠ·ΡΠ²Π°Ρ Π΅Π³ΠΎ Π΄ΠΎΠ»Π³ΠΎΠ²Π΅ΡΠ½ΠΎΡΡΡ ΠΈ ΠΏΡΠΈΠ²ΠΎΠ΄ΡΡΠΈΠ΅ ΠΊ ΠΏΡΠ΅ΠΆΠ΄Π΅Π²ΡΠ΅ΠΌΠ΅Π½Π½ΠΎΠΌΡ Π²ΡΡ ΠΎΠ΄Ρ ΠΈΠ· ΡΡΡΠΎΡ ΠΊΠΎΠ½ΡΡΡΡΠΊΡΠΈΠΉ. ΠΠΎΡΡΡΠΏΠ»Π΅Π½ΠΈΠ΅ Π²ΡΠ΅Π΄Π½ΡΡ Π²Π΅ΡΠ΅ΡΡΠ² ΠΌΠΎΠΆΠ½ΠΎ ΠΎΠ³ΡΠ°Π½ΠΈΡΠΈΡΡ ΠΈΠ»ΠΈ ΠΈΠ·Π±Π΅ΠΆΠ°ΡΡ, Π½Π°Π½Π΅ΡΡ Π½Π° Π±Π΅ΡΠΎΠ½ Π±Π°ΡΡΠ΅ΡΠ½ΡΠ΅ ΠΏΠΎΠ²Π΅ΡΡ Π½ΠΎΡΡΠ½ΡΠ΅ ΠΏΠΎΠΊΡΡΡΠΈΡ. Π’Π°ΠΊΠΈΠΌ ΠΎΠ±ΡΠ°Π·ΠΎΠΌ, ΠΌΠΎΠΆΠ½ΠΎ Π΄ΠΎΠ±ΠΈΡΡΡΡ ΡΠΎΡ ΡΠ°Π½Π΅Π½ΠΈΡ ΡΡΡΡΠΊΡΡΡΠ½ΠΎΠΉ ΡΠ΅Π»ΠΎΡΡΠ½ΠΎΡΡΠΈ Π² ΡΠ΅ΡΠ΅Π½ΠΈΠ΅ Π²ΡΠ΅Π³ΠΎ ΡΡΠΎΠΊΠ° ΡΠ»ΡΠΆΠ±Ρ. ΠΠΎΡΡΠΎΠ·ΠΈΡ Π°ΡΠΌΠ°ΡΡΡΠ½ΠΎΠΉ ΡΡΠ°Π»ΠΈ ΠΈΠ·-Π·Π° ΠΊΠ°ΡΠ±ΠΎΠ½ΠΈΠ·Π°ΡΠΈΠΈΠΠ΅Ρ Π°Π½ΠΈΠ·ΠΌ ΠΈΠ·Π½ΠΎΡΠ°
Π‘ΡΡΠ΅ΡΡΠ²ΡΡΡ ΡΠ°Π·Π»ΠΈΡΠ½ΡΠ΅ ΠΌΠ΅Ρ Π°Π½ΠΈΠ·ΠΌΡ ΠΈΠ·Π½ΠΎΡΠ° Π±Π΅ΡΠΎΠ½Π°.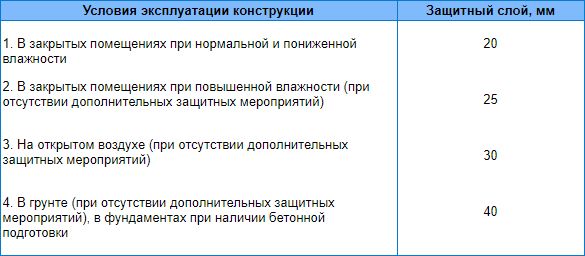
Β
ΠΠ°ΡΠΈΡΠ½ΡΠ΅ ΠΏΠΎΠΊΡΡΡΠΈΡ
Π‘ΡΠ»ΡΡΠ°ΡΠ½Π°Ρ Π°ΡΠ°ΠΊΠ° Π΄Π»Ρ Π±Π΅ΡΠΎΠ½Π° ΠΠ°ΡΠΈΡΠ° Π±Π΅ΡΠΎΠ½Π° Π΄ΠΎΠ»ΠΆΠ½Π° ΡΠ°ΠΊΡΠΈΡΠ΅ΡΠΊΠΈ Π½Π°ΡΠΈΠ½Π°ΡΡΡΡ Π½Π° ΠΊΠΎΠ½ΡΠ΅ΠΏΡΡΠ°Π»ΡΠ½ΠΎΠΉ ΡΡΠ°Π΄ΠΈΠΈ, ΠΈ Π΄ΠΎΠ»ΠΆΠ½Ρ Π±ΡΡΡ ΠΏΡΠΈΠ½ΡΡΡ ΡΡΠ°ΡΠ΅Π»ΡΠ½ΡΠ΅ ΡΡΡΠ°ΡΠ΅Π³ΠΈΠΈ Π΄Π»Ρ Π·Π°ΡΠΈΡΡ Π±Π΅ΡΠΎΠ½Π° ΠΊΠ°ΠΊ ΠΎΡ Π²Π½ΡΡΡΠ΅Π½Π½Π΅ΠΉ, ΡΠ°ΠΊ ΠΈ ΠΎΡ Π²Π½Π΅ΡΠ½Π΅ΠΉ ΡΡΠ΅Π΄Ρ. Π Π°Π·ΡΠ°Π±ΠΎΡΠ°Π½Ρ ΡΠ°Π·Π»ΠΈΡΠ½ΡΠ΅ ΠΌΠ°ΡΠ΅ΡΠΈΠ°Π»Ρ ΠΏΠΎΠΊΡΡΡΠΈΠΉ ΠΈ ΠΌΠ΅ΡΠΎΠ΄Ρ ΠΈΡ Π½Π°Π½Π΅ΡΠ΅Π½ΠΈΡ Π΄Π»Ρ ΡΠ΅ΠΌΠΎΠ½ΡΠ° ΠΈ ΡΠΊΡΠ΅ΠΏΠ»Π΅Π½ΠΈΡ Π±Π΅ΡΠΎΠ½Π½ΡΡ ΠΏΠΎΠ²Π΅ΡΡ Π½ΠΎΡΡΠ΅ΠΉ. ΠΠ΄Π½Π°ΠΊΠΎ ΠΊΡΠΈΡΠ΅ΡΠΈΠΉ Π²ΡΠ±ΠΎΡΠ° ΡΡΠΈΡ ΠΌΠ°ΡΠ΅ΡΠΈΠ°Π»ΠΎΠ² Π΅ΡΠ΅ Π½Π΅ ΡΡΡΠ°Π½ΠΎΠ²Π»Π΅Π½. ΠΡΠΎΡΠ΅Π΄ΡΡΡ Π²ΡΠ±ΠΎΡΠ° ΠΌΠ°ΡΠ΅ΡΠΈΠ°Π»ΠΎΠ² Π±Π΅ΡΠΎΠ½Π½ΠΎΠ³ΠΎ ΠΏΠΎΠΊΡΡΡΠΈΡ Π΄ΠΎΠ»ΠΆΠ½Ρ Π±ΡΡΡ ΡΠΎΡΡΠ΅Π΄ΠΎΡΠΎΡΠ΅Π½Ρ Π½Π° ΠΌΠ΅Ρ Π°Π½ΠΈΠ·ΠΌΠ°Ρ ΡΡ ΡΠ΄ΡΠ΅Π½ΠΈΡ, ΡΡΠ°ΡΠ΅Π»ΡΠ½ΠΎ Π΄ΠΈΠ°Π³Π½ΠΎΡΡΠΈΡΡΠ΅ΠΌΡΡ Π² Π·Π°Π²ΠΈΡΠΈΠΌΠΎΡΡΠΈ ΠΎΡ ΡΠΎΡΡΠΎΡΠ½ΠΈΡ ΡΠ΅Π»Π΅Π²ΡΡ ΠΊΠΎΠ½ΡΡΡΡΠΊΡΠΈΠΉ. ΠΠ°ΠΏΡΠΈΠΌΠ΅Ρ, Π² ΡΠ»ΡΡΠ°Π΅ ΠΏΠΎΠ²ΡΠ΅ΠΆΠ΄Π΅Π½ΠΈΡ ΡΠΎΠ»ΡΡ, ΠΏΠΎΠ»ΠΈΡΠΈΠΊΠ° ΡΠ΅ΠΌΠΎΠ½ΡΠ° Π΄ΠΎΠ»ΠΆΠ½Π° ΡΡΠΈΡΡΠ²Π°ΡΡ ΠΊΠΎΡΡΠΎΠ·ΠΈΠΎΠ½Π½ΡΡ ΡΡΠ΅Π΄Ρ ΠΈ ΡΡ ΡΠ΄ΡΠ°ΡΡΠ΅Π΅ΡΡ ΡΠΎΡΡΠΎΡΠ½ΠΈΠ΅, ΡΡΠΎΠ±Ρ ΠΎΠΏΡΠ΅Π΄Π΅Π»ΠΈΡΡ ΡΠΈΠΌΠΏΡΠΎΠΌΠ°ΡΠΈΡΠ΅ΡΠΊΠΈΠ΅ ΠΏΡΠΈΠ·Π½Π°ΠΊΠΈ, ΡΠ°ΠΊΠΈΠ΅ ΠΊΠ°ΠΊ (1) ΡΠ΄Π°Π»Π΅Π½ΠΈΠ΅ ΠΏΡΠΎΠ½ΠΈΠΊΡΠΈΡ ΠΈΠΎΠ½ΠΎΠ² Ρ Π»ΠΎΡΠΈΠ΄Π° (2) Π±Π»ΠΎΠΊΠΈΡΠΎΠ²Π°Π½ΠΈΠ΅ ΠΏΡΠΎΠ½ΠΈΠΊΠ½ΠΎΠ²Π΅Π½ΠΈΡ ΠΈΠΎΠ½ΠΎΠ² Ρ Π»ΠΎΡΠΈΠ΄Π°, Π²Π»Π°Π³ΠΈ ΠΈ ΠΊΠΈΡΠ»ΠΎΡΠΎΠ΄Π° (3) ΡΠ΄Π°Π»Π΅Π½ΠΈΠ΅ ΡΠΆΠ°Π²ΡΠΈΠ½Ρ Ρ Π°ΡΠΌΠ°ΡΡΡΡ (4) ΠΌΠ΅ΡΠΎΠ΄ Π·Π°ΡΠΈΡΡ ΠΎΡ ΠΊΠΎΡΡΠΎΠ·ΠΈΠΈ (ΠΏΠΎΠΊΡΡΡΠΈΠ΅ ΠΈΠ»ΠΈ ΠΊΠΎΠ½ΡΡΠΎΠ»Ρ ΠΏΠΎΡΠ΅Π½ΡΠΈΠ°Π»Π°).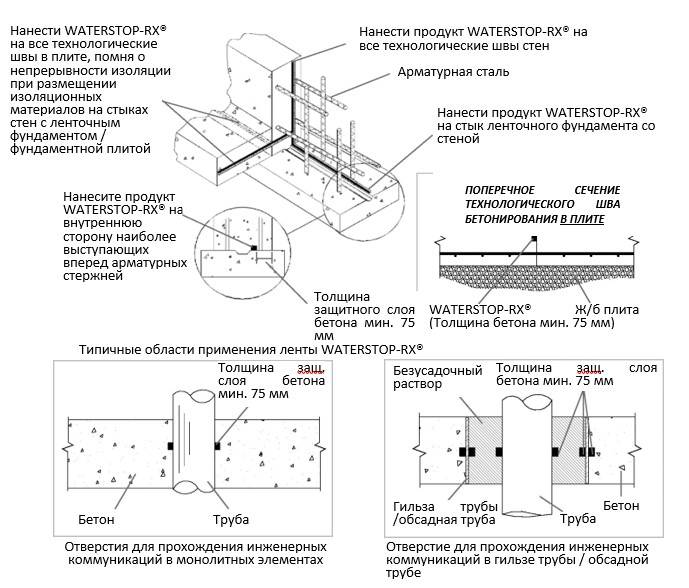
ΠΠΎΠΌΠΏΠΎΠ½Π΅Π½ΡΡ ΠΏΠΎΠΊΡΡΡΠΈΠΉ
ΠΡΠ΅ ΠΎΡΠ³Π°Π½ΠΈΡΠ΅ΡΠΊΠΈΠ΅ ΠΏΠΎΠΊΡΡΡΠΈΡ ΡΠΎΡΡΠΎΡΡ ΠΈΠ· ΡΡΠ΅Ρ ΠΎΡΠ½ΠΎΠ²Π½ΡΡ ΠΊΠΎΠΌΠΏΠΎΠ½Π΅Π½ΡΠΎΠ²:- Π Π°ΡΡΠ²ΠΎΡΠΈΡΠ΅Π»Ρ
- Π‘ΠΌΠΎΠ»Π°
- ΠΠΈΠ³ΠΌΠ΅Π½Ρ.
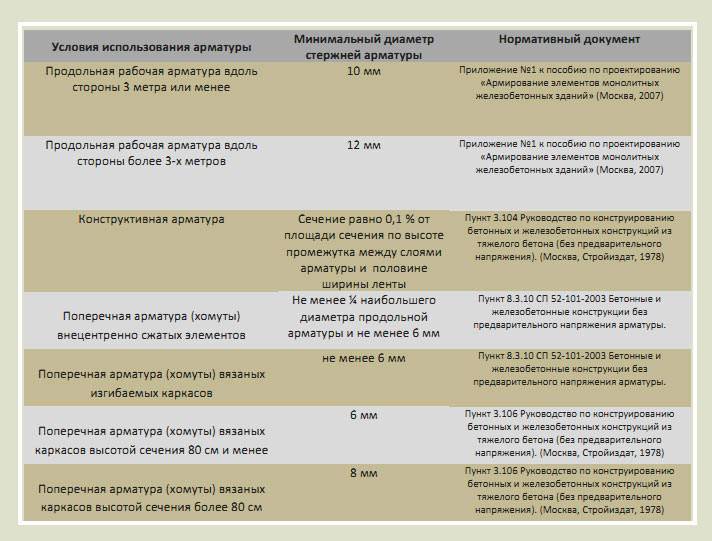
Π Π°ΡΡΠ²ΠΎΡΠΈΡΠ΅Π»Ρ
ΠΡΠ³Π°Π½ΠΈΡΠ΅ΡΠΊΠΈΠ΅ ΡΠ°ΡΡΠ²ΠΎΡΠΈΡΠ΅Π»ΠΈ Π²Ρ ΠΎΠ΄ΡΡ Π² ΡΠΎΡΡΠ°Π² ΠΏΠΎΠΊΡΡΡΠΈΠΉ Π΄Π»Ρ Π²ΡΠΏΠΎΠ»Π½Π΅Π½ΠΈΡ ΡΡΠ΅Ρ ΠΎΡΠ½ΠΎΠ²Π½ΡΡ ΡΡΠ½ΠΊΡΠΈΠΉ:
- Π Π°ΡΡΠ²ΠΎΡΠΈΡΡ ΠΊΠΎΠΌΠΏΠΎΠ½Π΅Π½Ρ ΡΠΌΠΎΠ»Ρ
- ΠΠΎΠ½ΡΡΠΎΠ»Ρ ΠΈΡΠΏΠ°ΡΠ΅Π½ΠΈΡ Π΄Π»Ρ ΠΎΠ±ΡΠ°Π·ΠΎΠ²Π°Π½ΠΈΡ ΠΏΠ»Π΅Π½ΠΊΠΈ
- Π£ΠΌΠ΅Π½ΡΡΠΈΡΠ΅ Π²ΡΠ·ΠΊΠΎΡΡΡ ΠΏΠΎΠΊΡΡΡΠΈΡ Π΄Π»Ρ ΠΎΠ±Π»Π΅Π³ΡΠ΅Π½ΠΈΡ Π½Π°Π½Π΅ΡΠ΅Π½ΠΈΡ.
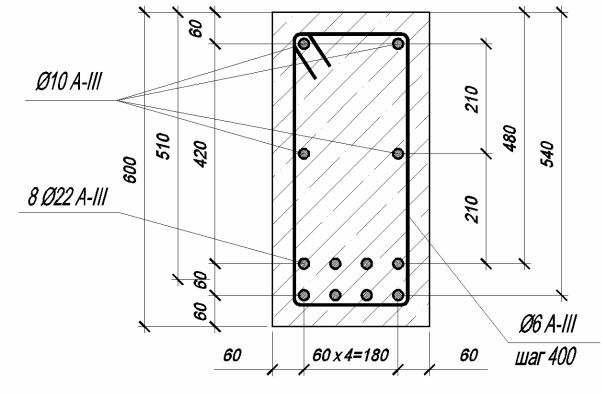
Π‘ΠΌΠΎΠ»Π°
Π‘ΠΌΠΎΠ»Π° (ΡΠ°ΡΡΠΎ Π½Π°Π·ΡΠ²Π°Π΅ΠΌΠ°Ρ ΡΠ²ΡΠ·ΡΡΡΠΈΠΌ) ΡΠ²Π»ΡΠ΅ΡΡΡ ΠΏΠ»Π΅Π½ΠΊΠΎΠΎΠ±ΡΠ°Π·ΡΡΡΠΈΠΌ ΠΊΠΎΠΌΠΏΠΎΠ½Π΅Π½ΡΠΎΠΌ ΠΏΠΎΠΊΡΡΡΠΈΡ. Π‘ΠΌΠΎΠ»Ρ ΠΎΠ±ΡΡΠ½ΠΎ ΠΏΡΠ΅Π΄ΡΡΠ°Π²Π»ΡΡΡ ΡΠΎΠ±ΠΎΠΉ ΡΠ²Π΅ΡΠ΄ΡΠ΅ ΠΏΠΎΠ»ΠΈΠΌΠ΅ΡΡ Ρ Π²ΡΡΠΎΠΊΠΎΠΉ ΠΌΠΎΠ»Π΅ΠΊΡΠ»ΡΡΠ½ΠΎΠΉ ΠΌΠ°ΡΡΠΎΠΉ, ΠΊΠΎΡΠΎΡΡΠ΅ ΠΎΠ±ΡΠ°Π·ΡΡΡ Π±ΠΎΠ»ΡΡΠΈΠ΅ ΠΏΠΎΠ²ΡΠΎΡΡΡΡΠΈΠ΅ΡΡ ΠΌΠΎΠ»Π΅ΠΊΡΠ»Ρ Π² ΠΎΡΠ²Π΅ΡΠΆΠ΄Π΅Π½Π½ΠΎΠΉ ΠΏΠ»Π΅Π½ΠΊΠ΅. ΠΡΠ½ΠΎΠ²Π½ΠΎΠΉ ΡΠ΅Π»ΡΡ ΡΠΌΠΎΠ»Ρ ΡΠ²Π»ΡΠ΅ΡΡΡ ΡΠΌΠ°ΡΠΈΠ²Π°Π½ΠΈΠ΅ ΡΠ°ΡΡΠΈΡ ΠΏΠΈΠ³ΠΌΠ΅Π½ΡΠ° ΠΈ ΡΠ²ΡΠ·ΡΠ²Π°Π½ΠΈΠ΅ ΡΠ°ΡΡΠΈΡ ΠΏΠΈΠ³ΠΌΠ΅Π½ΡΠ° Π²ΠΌΠ΅ΡΡΠ΅ ΠΈ Ρ ΠΏΠΎΠ΄Π»ΠΎΠΆΠΊΠΎΠΉ (ΠΎΡΡΡΠ΄Π° ΠΈ ΡΠ΅ΡΠΌΠΈΠ½ Β«ΡΠ²ΡΠ·ΡΡΡΠ΅Π΅Β»). Π‘ΠΌΠΎΠ»Π° ΠΏΡΠΈΠ΄Π°Π΅Ρ Π±ΠΎΠ»ΡΡΡΡ ΡΠ°ΡΡΡ ΡΠ²ΠΎΠΉΡΡΠ² ΠΏΠΎΠΊΡΡΡΠΈΡ. Π Π°Π·Π»ΠΈΡΠ½ΡΠ΅ ΡΠΈΠΏΡ ΡΠΌΠΎΠ», Π²Ρ ΠΎΠ΄ΡΡΠΈΠ΅ Π² ΡΠΎΡΡΠ°Π² ΠΏΠΎΠΊΡΡΡΠΈΡ, ΠΎΠ±Π»Π°Π΄Π°ΡΡ ΡΠ°Π·Π»ΠΈΡΠ½ΡΠΌΠΈ ΡΠ²ΠΎΠΉΡΡΠ²Π°ΠΌΠΈ. ΠΡΠΈ ΡΠ²ΠΎΠΉΡΡΠ²Π°:
- ΠΠ΅Ρ Π°Π½ΠΈΠ·ΠΌ ΠΈ Π²ΡΠ΅ΠΌΡ ΠΎΡΠ²Π΅ΡΠΆΠ΄Π΅Π½ΠΈΡ
- ΠΠΊΡΠΏΠ»ΡΠ°ΡΠ°ΡΠΈΠΎΠ½Π½ΡΠ΅ Ρ Π°ΡΠ°ΠΊΡΠ΅ΡΠΈΡΡΠΈΠΊΠΈ ΡΠΈΠΏΠ° ΡΠΊΡΠΏΠΎΠ·ΠΈΡΠΈΠΈ
- ΠΡΠΎΠΈΠ·Π²ΠΎΠ΄ΠΈΡΠ΅Π»ΡΠ½ΠΎΡΡΡ Π½Π° ΡΠΈΠΏΠ΅ ΠΏΠΎΠ΄Π»ΠΎΠΆΠΊΠΈ
- Π‘ΠΎΠ²ΠΌΠ΅ΡΡΠΈΠΌΠΎΡΡΡ Ρ Π΄ΡΡΠ³ΠΈΠΌΠΈ ΠΏΠΎΠΊΡΡΡΠΈΡΠΌΠΈ
- ΠΠΈΠ±ΠΊΠΎΡΡΡ ΠΈ ΠΏΡΠΎΡΠ½ΠΎΡΡΡ
- ΠΠ½Π΅ΡΠ½ΡΡ Π·Π°ΡΠΈΡΠ° ΠΎΡ Π°ΡΠΌΠΎΡΡΠ΅ΡΠ½ΡΡ Π²ΠΎΠ·Π΄Π΅ΠΉΡΡΠ²ΠΈΠΉ
- ΠΠ΄Π³Π΅Π·ΠΈΡ
- ΠΠΎΠ·Π΄ΡΡ ΠΎΠΏΡΠΎΠ½ΠΈΡΠ°Π΅ΠΌΠΎΡΡΡ (ΠΏΡΠΎΠ½ΠΈΡΠ°Π΅ΠΌΠΎΡΡΡ Π²ΠΎΠ΄ΡΠ½ΠΎΠ³ΠΎ ΠΏΠ°ΡΠ°)

ΠΠΈΠ³ΠΌΠ΅Π½Ρ
ΠΠΈΠ³ΠΌΠ΅Π½ΡΡ Π½Π΅ΡΠ°ΡΡΠ²ΠΎΡΠΈΠΌΡ ΠΈ ΠΏΡΠ΅Π΄ΡΡΠ°Π²Π»ΡΡΡ ΡΠΎΠ±ΠΎΠΉ Π±ΠΎΠ»Π΅Π΅ ΡΡΠΆΠ΅Π»ΡΡ ΡΠ²Π΅ΡΠ΄ΡΡ ΡΠ°ΡΡΡ ΠΏΠΎΠΊΡΡΡΠΈΡ, ΠΊΠΎΡΠΎΡΠ°Ρ ΠΎΠ±ΡΡΠ½ΠΎ ΠΎΡΠ΅Π΄Π°Π΅Ρ Π½Π° Π΄Π½ΠΎ ΠΊΠΎΠ½ΡΠ΅ΠΉΠ½Π΅ΡΠ°. ΠΠΈΠ³ΠΌΠ΅Π½ΡΡ β ΡΡΠΎ Π΄ΠΎΠ±Π°Π²ΠΊΠΈ ΠΊ ΡΠΎΡΡΠ°Π²Ρ ΠΏΠΎΠΊΡΡΡΠΈΡ, ΠΊΠΎΡΠΎΡΡΠ΅ ΠΏΡΠΈΠ΄Π°ΡΡ ΠΎΠΏΡΠ΅Π΄Π΅Π»Π΅Π½Π½ΡΠ΅ ΡΠ²ΠΎΠΉΡΡΠ²Π° Π΄Π»Ρ Π΄ΠΎΡΡΠΈΠΆΠ΅Π½ΠΈΡ ΠΆΠ΅Π»Π°Π΅ΠΌΡΡ ΡΠ²ΠΎΠΉΡΡΠ² ΠΏΠ»Π΅Π½ΠΊΠΈ. ΠΠΈΠ³ΠΌΠ΅Π½ΡΡ ΠΏΡΠΈΠ΄Π°ΡΡ ΡΠ²Π΅Ρ ΠΈ ΡΡΡΠ΅ΡΠΈΠΊΡ ΠΏΠΎΠΊΡΡΡΠΈΡ.
Π’ΠΈΠΏΡ ΠΏΠΎΠΊΡΡΡΠΈΠΉ
Π’ΠΈΠΏΡ ΠΏΠΎΠΊΡΡΡΠΈΠΉ ΠΌΠΎΠΆΠ½ΠΎ ΡΠ°Π·Π΄Π΅Π»ΠΈΡΡ Π½Π° ΡΡΠΈ ΡΠΈΡΡΠ΅ΠΌΡ. Π ΠΎΡΠ»ΠΈΡΠΈΠ΅ ΠΎΡ ΠΏΠΎΠΊΡΡΡΠΈΠΉ Π΄Π»Ρ ΡΡΠ°Π»ΡΠ½ΡΡ
ΠΏΠΎΠ΄Π»ΠΎΠΆΠ΅ΠΊ, Π·Π°ΡΠΈΡΠ½ΡΠ΅ ΠΏΠΎΠΊΡΡΡΠΈΡ Π΄Π»Ρ Π±Π΅ΡΠΎΠ½Π° Π² Π±ΠΎΠ»ΡΡΠΈΠ½ΡΡΠ²Π΅ ΡΠ»ΡΡΠ°Π΅Π² Π½Π΅ ΡΡΠ΅Π±ΡΡΡ ΠΈ Π½Π΅ ΡΠΎΠ΄Π΅ΡΠΆΠ°Ρ ΠΈΠ½Π³ΠΈΠ±ΠΈΡΡΡΡΠΈΡ
ΠΈΠ»ΠΈ ΡΠ°ΡΡ
ΠΎΠ΄ΡΠ΅ΠΌΡΡ
ΠΏΠΈΠ³ΠΌΠ΅Π½ΡΠΎΠ² Π΄Π»Ρ ΠΎΠ±Π΅ΡΠΏΠ΅ΡΠ΅Π½ΠΈΡ Π·Π°ΡΠΈΡΡ. ΠΠΎΠΊΡΡΡΠΈΡ, Π½Π°Π½ΠΎΡΠΈΠΌΡΠ΅ Π½Π° Π±Π΅ΡΠΎΠ½, ΠΎΠ±ΡΡΠ½ΠΎ ΠΏΡΠ΅Π΄ΡΡΠ°Π²Π»ΡΡΡ ΡΠΎΠ±ΠΎΠΉ Π±Π°ΡΡΠ΅ΡΠ½ΡΠ΅ ΠΏΠΎΠΊΡΡΡΠΈΡ. ΠΠ½ΠΈ ΠΎΠ±Π΅ΡΠΏΠ΅ΡΠΈΠ²Π°ΡΡ Π·Π°ΡΠΈΡΡ, ΡΡΠ°Π½ΠΎΠ²ΡΡΡ ΡΠΈΠ·ΠΈΡΠ΅ΡΠΊΠΈΠΌ Π±Π°ΡΡΠ΅ΡΠΎΠΌ ΠΈΠ»ΠΈ ΡΠΈΡΠΎΠΌ, ΠΈΠ·ΠΎΠ»ΠΈΡΡΡ Π±Π΅ΡΠΎΠ½ ΠΎΡ ΠΎΠΊΡΡΠΆΠ°ΡΡΠ΅ΠΉ ΡΡΠ΅Π΄Ρ. ΠΠ°ΡΡΠ΅ΡΠ½ΠΎΠ΅ ΠΏΠΎΠΊΡΡΡΠΈΠ΅ Π΄ΠΎΠ»ΠΆΠ½ΠΎ ΠΏΡΠ΅ΠΏΡΡΡΡΠ²ΠΎΠ²Π°ΡΡ ΠΏΡΠΎΡ
ΠΎΠΆΠ΄Π΅Π½ΠΈΡ Π°Π³ΡΠ΅ΡΡΠΈΠ²Π½ΡΡ
ΠΆΠΈΠ΄ΠΊΠΎΡΡΠ΅ΠΉ ΠΈ Π³Π°Π·ΠΎΠ² ΠΊ Π±Π΅ΡΠΎΠ½Ρ.
ΠΠ°ΡΡΠ΅Ρ β ΠΠΎΠΊΡΡΡΠΈΠ΅, ΠΎΠ±ΡΠ°Π·ΡΡΡΠ΅Π΅ Π±Π°ΡΡΠ΅Ρ ΠΌΠ΅ΠΆΠ΄Ρ ΠΏΠΎΠ²Π΅ΡΡ
Π½ΠΎΡΡΡΡ Π±Π΅ΡΠΎΠ½Π° ΠΈ ΠΏΡΠ΅Π΄ΠΎΡΠ²ΡΠ°ΡΠ°ΡΡΠ΅Π΅ ΠΏΠΎΠΏΠ°Π΄Π°Π½ΠΈΠ΅ Π²ΡΠ΅Π΄Π½ΠΎΠ³ΠΎ Π²Π΅ΡΠ΅ΡΡΠ²Π° Π² ΡΠ΅Π»ΠΎ Π±Π΅ΡΠΎΠ½Π° ΠΏΠΎΡΡΠ΅Π΄ΡΡΠ²ΠΎΠΌ ΠΌΠ½ΠΎΠ³ΠΈΡ
ΡΡΠ°Π½ΡΠΏΠΎΡΡΠ½ΡΡ
ΠΌΠ΅Ρ
Π°Π½ΠΈΠ·ΠΌΠΎΠ², ΡΠ°ΠΊΠΈΡ
ΠΊΠ°ΠΊ Π°Π±ΡΠΎΡΠ±ΡΠΈΡ, ΠΊΠ°ΠΏΠΈΠ»Π»ΡΡΠ½ΠΎΠ΅ Π²ΡΠ°ΡΡΠ²Π°Π½ΠΈΠ΅, Π΄ΠΈΡΡΡΠ·ΠΈΡ ΠΈ Ρ. Π΄., ΠΏΠΎ ΡΡΡΠ΅ΡΡΠ²Ρ ΡΠ²Π»ΡΠ΅ΡΡΡ ΠΏΠ»Π΅Π½ΠΊΠΎΠΎΠ±ΡΠ°Π·ΡΡΡΠΈΠΌ Π°Π³Π΅Π½ΡΠΎΠΌ ΠΏΡΠΈ ΠΎΡΠ²Π΅ΡΠΆΠ΄Π΅Π½ΠΈΠΈ. . ΠΡΠΈΠΌΠ΅ΡΠ°ΠΌΠΈ ΡΠ²Π»ΡΡΡΡΡ Π°ΠΊΡΠΈΠ»ΠΎΠ²ΡΠ΅ ΠΊΡΠ°ΡΠΊΠΈ, ΡΠΏΠΎΠΊΡΠΈΠ΄Π½ΡΠ΅ ΡΠΌΠΎΠ»Ρ, ΡΠΏΠΎΠΊΡΠΈΠ΄Π½ΡΠ΅ ΡΠΌΠΎΠ»Ρ ΠΈΠ· ΠΊΠ°ΠΌΠ΅Π½Π½ΠΎΡΠ³ΠΎΠ»ΡΠ½ΠΎΠΉ ΡΠΌΠΎΠ»Ρ ΠΈ Ρ. Π΄. ΠΠ΄Π½ΠΈΠΌ ΠΈΠ· Π²Π°ΠΆΠ½ΡΡ
ΡΠ²ΠΎΠΉΡΡΠ² Π±Π°ΡΡΠ΅ΡΠ½ΠΎΠ³ΠΎ ΠΏΠΎΠΊΡΡΡΠΈΡ ΡΠ²Π»ΡΠ΅ΡΡΡ ΠΏΡΠΎΠ½ΠΈΡΠ°Π΅ΠΌΠΎΡΡΡ. ΠΡΠΎΠ½ΠΈΡΠ°Π΅ΠΌΠΎΡΡΡ ΠΏΠ»Π΅Π½ΠΊΠΈ Π±Π°ΡΡΠ΅ΡΠ½ΠΎΠ³ΠΎ ΠΏΠΎΠΊΡΡΡΠΈΡ Π·Π°Π²ΠΈΡΠΈΡ ΠΎΡ ΡΠΊΠΎΡΠΎΡΡΠΈ ΠΏΡΠΎΠΏΡΡΠΊΠ°Π½ΠΈΡ ΠΏΠ°ΡΠΎΠ² Π²Π»Π°Π³ΠΈ (ΠΠΠ). Π‘ΠΊΠΎΡΠΎΡΡΡ MVT ΠΎΠΏΡΠ΅Π΄Π΅Π»ΡΠ΅ΡΡΡ ΡΠ΅ΠΌ, Π½Π°ΡΠΊΠΎΠ»ΡΠΊΠΎ Π±ΡΡΡΡΠΎ ΠΌΠΎΠ»Π΅ΠΊΡΠ»Ρ Π²ΠΎΠ΄Ρ ΠΏΡΠΎΡ
ΠΎΠ΄ΡΡ ΠΈ ΠΏΠ΅ΡΠ΅ΠΌΠ΅ΡΠ°ΡΡΡΡ Π² ΠΏΡΠΎΡΡΡΠ°Π½ΡΡΠ²Π΅ ΠΌΠ΅ΠΆΠ΄Ρ ΠΌΠΎΠ»Π΅ΠΊΡΠ»Π°ΠΌΠΈ ΡΠΌΠΎΠ»Ρ. ΠΡΡΠ΅ΠΊΡΠΈΠ²Π½ΠΎΡΡΡ ΠΏΠΎΠΊΡΡΡΠΈΡ Π² ΠΏΡΠ΅Π΄ΠΎΡΠ²ΡΠ°ΡΠ΅Π½ΠΈΠΈ ΠΏΡΠΎΠ½ΠΈΠΊΠ½ΠΎΠ²Π΅Π½ΠΈΡ Π·Π°Π²ΠΈΡΠΈΡ ΠΎΡ ΡΠΎΠ³ΠΎ, Π½Π°ΡΠΊΠΎΠ»ΡΠΊΠΎ ΡΠ΅ΡΠ½ΠΎ ΠΈ ΠΏΡΠΎΡΠ½ΠΎ ΡΠ²ΡΠ·Π°Π½Ρ ΠΌΠΎΠ»Π΅ΠΊΡΠ»Ρ ΡΠΌΠΎΠ»Ρ Π΄ΡΡΠ³ Ρ Π΄ΡΡΠ³ΠΎΠΌ. ΠΡΡΠ΅ΠΊΡΠΈΠ²Π½ΠΎΡΡΡ ΠΏΠΎΠΊΡΡΡΠΈΡ ΡΠ°ΠΊΠΆΠ΅ Π·Π°Π²ΠΈΡΠΈΡ ΠΎΡ ΡΠΈΠΏΠ° ΠΌΠΎΠ»Π΅ΠΊΡΠ»Ρ ΡΠΌΠΎΠ»Ρ ΠΈ ΠΊΠΎΠ»ΠΈΡΠ΅ΡΡΠ²Π° ΠΈ ΡΠΈΠΏΠ° ΠΏΠΈΠ³ΠΌΠ΅Π½ΡΠ°. Π‘ΡΠΈΠ²ΠΊΠ° ΡΠ²Π»ΡΠ΅ΡΡΡ ΠΌΠ΅ΡΠΎΠΉ ΡΡΠ΅ΠΏΠ΅Π½ΠΈ ΠΈΠ½ΡΠ΅Π½ΡΠΈΠ²Π½ΠΎΠ³ΠΎ ΡΠ²ΡΠ·ΡΠ²Π°Π½ΠΈΡ ΡΠΌΠΎΠ» ΠΏΠΎΠΊΡΡΡΠΈΡ. Π§Π΅ΠΌ Π½ΠΈΠΆΠ΅ ΠΏΡΠΎΠ½ΠΈΡΠ°Π΅ΠΌΠΎΡΡΡ Π±Π°ΡΡΠ΅ΡΠ½ΠΎΠ³ΠΎ ΠΏΠΎΠΊΡΡΡΠΈΡ, ΡΠ΅ΠΌ Π²ΡΡΠ΅ Π΅Π³ΠΎ Π·Π°ΡΠΈΡΠ½ΡΠ΅ ΡΠ²ΠΎΠΉΡΡΠ²Π°. Π ΠΎΡΠ½ΠΎΠ²Π½ΠΎΠΌ, ΡΠ΅ΠΌ Π²ΡΡΠ΅ ΡΡΠ΅ΠΏΠ΅Π½Ρ ΡΡΠΈΠ²ΠΊΠΈ ΡΠΌΠΎΠ»Ρ ΠΏΠΎΠΊΡΡΡΠΈΡ, ΡΠ΅ΠΌ Π½ΠΈΠΆΠ΅ ΠΏΡΠΎΠ½ΠΈΡΠ°Π΅ΠΌΠΎΡΡΡ, ΡΠ΅ΠΌ Π»ΡΡΡΠ΅ ΡΡΠ΅ΠΏΠ»Π΅Π½ΠΈΠ΅ ΠΏΠΎΠΊΡΡΡΠΈΡ Ρ ΠΏΠΎΠ²Π΅ΡΡ
Π½ΠΎΡΡΡΡ ΠΈ Π²ΡΡΠ΅ ΠΎΠ±ΡΠΈΠΉ Π·Π°ΡΠΈΡΠ½ΡΠΉ Π±Π°ΡΡΠ΅Ρ. ΠΡΠΈ ΠΌΠ΅ΠΆΠΌΠΎΠ»Π΅ΠΊΡΠ»ΡΡΠ½ΡΠ΅ ΠΏΡΠΎΡΡΡΠ°Π½ΡΡΠ²Π° ΠΌΠ΅ΠΆΠ΄Ρ ΠΌΠΎΠ»Π΅ΠΊΡΠ»Π°ΠΌΠΈ ΡΠΌΠΎΠ»Ρ Π½Π°ΠΌΠ½ΠΎΠ³ΠΎ Π±ΠΎΠ»ΡΡΠ΅, ΡΠ΅ΠΌ ΠΌΠΎΠ»Π΅ΠΊΡΠ»Ρ Π²ΠΎΠ΄Ρ, ΠΈ ΠΈΡ
Π½Π΅ ΡΠ»Π΅Π΄ΡΠ΅Ρ ΠΏΡΡΠ°ΡΡ Ρ ΡΠΈΠ·ΠΈΡΠ΅ΡΠΊΠΈΠΌΠΈ ΠΎΡΠ²Π΅ΡΡΡΠΈΡΠΌΠΈ (ΡΠΎΡΠ΅ΡΠ½ΡΠΌΠΈ ΠΎΡΠ²Π΅ΡΡΡΠΈΡΠΌΠΈ) Π² ΠΏΠ»Π΅Π½ΠΊΠ΅ ΠΏΠΎΠΊΡΡΡΠΈΡ. ΠΡΠΎΠΊΠΎΠ»Ρ Π² ΠΏΠ»Π΅Π½ΠΊΠ΅ ΠΏΠΎΠΊΡΡΡΠΈΡ ΠΎΠ±ΡΡΠ½ΠΎ ΡΡΠΈΡΠ°ΡΡΡΡ Π΄Π΅ΡΠ΅ΠΊΡΠ°ΠΌΠΈ ΠΈ Π΄ΠΎΠ»ΠΆΠ½Ρ Π±ΡΡΡ ΡΡΡΡΠ°Π½Π΅Π½Ρ. ΠΡΠΎΡΡΡΠ°Π½ΡΡΠ²Π° ΠΌΠ΅ΠΆΠ΄Ρ ΠΌΠΎΠ»Π΅ΠΊΡΠ»Π°ΠΌΠΈ ΡΠΌΠΎΠ»Ρ Π½Π΅ ΡΠ²Π»ΡΡΡΡΡ Π΄Π΅ΡΠ΅ΠΊΡΠ°ΠΌΠΈ. ΠΠ°ΡΡΠ΅ΡΠ½ΡΠ΅ ΡΠ²ΠΎΠΉΡΡΠ²Π° ΠΏΠΎΠΊΡΡΡΠΈΠΉ ΠΌΠΎΠΆΠ½ΠΎ ΡΠ»ΡΡΡΠΈΡΡ ΠΏΡΡΠ΅ΠΌ Π΄ΠΎΠ±Π°Π²Π»Π΅Π½ΠΈΡ Π² ΡΠΌΠΎΠ»Ρ Π°ΡΠΌΠΈΡΡΡΡΠΈΡ
Π½Π°ΠΏΠΎΠ»Π½ΠΈΡΠ΅Π»Π΅ΠΉ. ΠΠ°ΠΏΠΎΠ»Π½ΠΈΡΠ΅Π»ΠΈ Π±ΡΠ²Π°ΡΡ ΡΠ°Π·Π»ΠΈΡΠ½ΡΡ
ΡΠΎΡΠΌ, ΡΠ°ΠΊΠΈΡ
ΠΊΠ°ΠΊ ΡΠΈΠ»ΠΈΠΊΠ°ΡΠ½ΡΠ΅ Π·Π°ΠΏΠΎΠ»Π½ΠΈΡΠ΅Π»ΠΈ (ΠΏΠ΅ΡΠΎΠΊ), Ρ
Π»ΠΎΠΏΡΡ ΡΡΠ΅ΠΊΠ»ΠΎΠ²ΠΎΠ»ΠΎΠΊΠ½Π° ΠΈΠ»ΠΈ ΡΠ»ΡΠ΄Ρ, Π²ΠΎΠ»ΠΎΠΊΠ½Π°, ΡΠΊΠ°Π½ΠΎΠ΅ ΡΡΠ΅ΠΊΠ»ΠΎΠ²ΠΎΠ»ΠΎΠΊΠ½ΠΎ (Π²ΠΊΠ»ΡΡΠ°Π΅ΠΌΠΎΠ΅ Π² Π²ΠΈΠ΄Π΅ ΠΌΠ°ΡΠ° Π² ΡΠΈΡΡΠ΅ΠΌΡ ΡΠΌΠΎΠ»Ρ ΠΏΠΎ ΠΌΠ΅ΡΠ΅ Π΅Π΅ ΠΎΡΠ²Π΅ΡΠΆΠ΄Π΅Π½ΠΈΡ). ΠΠΎΠ±Π°Π²Π»Π΅Π½ΠΈΠ΅ Π½Π°ΠΏΠΎΠ»Π½ΠΈΡΠ΅Π»Π΅ΠΉ ΡΠΈΠ·ΠΈΡΠ΅ΡΠΊΠΈ ΡΠ²Π΅Π»ΠΈΡΠΈΠ²Π°Π΅Ρ Π΄Π»ΠΈΠ½Ρ ΠΏΡΡΠΈ, ΠΊΠΎΡΠΎΡΡΠΉ Π΄ΠΎΠ»ΠΆΠ½Ρ ΠΏΡΠΎΠΉΡΠΈ ΠΏΡΠΎΠ½ΠΈΠΊΠ°ΡΡΠΈΠ΅ ΠΌΠΎΠ»Π΅ΠΊΡΠ»Ρ ΠΆΠΈΠ΄ΠΊΠΎΡΡΠΈ ΠΈΠ»ΠΈ Π³Π°Π·Π°, ΡΡΠΎΠ±Ρ ΠΏΡΠΎΠ½ΠΈΠΊΠ½ΡΡΡ Π² ΠΏΠΎΠΊΡΡΡΠΈΠ΅. Π§Π΅ΡΡΠΉΡΠ°ΡΡΠ΅ ΠΌΠ°ΡΠ΅ΡΠΈΠ°Π»Ρ ΠΎΠ±ΡΠ°Π·ΡΡΡ ΡΠ»ΠΎΠΈ ΠΏΠ΅ΡΠ΅ΠΊΡΡΠ²Π°ΡΡΠΈΡ
ΡΡ ΠΏΠ»Π°ΡΡΠΈΠ½, ΠΏΠ°ΡΠ°Π»Π»Π΅Π»ΡΠ½ΡΡ
Π±Π΅ΡΠΎΠ½Π½ΠΎΠΉ ΠΏΠΎΠ²Π΅ΡΡ
Π½ΠΎΡΡΠΈ, ΡΡΠΎ-ΡΠΎ Π²ΡΠΎΠ΄Π΅ ΡΠ΅ΡΠ΅ΠΏΠΈΡΡ Π½Π° ΠΊΡΡΡΠ΅.
Π’Π°ΠΊΠΆΠ΅ ΠΌΠΎΠ³ΡΡ Π±ΡΡΡ Π΄ΠΎΠ±Π°Π²Π»Π΅Π½Ρ Π½Π°ΠΏΠΎΠ»Π½ΠΈΡΠ΅Π»ΠΈ ΠΈ ΠΌΠ°Ρ ΠΈΠ· ΡΡΠ΅ΠΊΠ»ΠΎΠ²ΠΎΠ»ΠΎΠΊΠ½Π° Π΄Π»Ρ ΡΠ»ΡΡΡΠ΅Π½ΠΈΡ ΡΠΈΠ·ΠΈΡΠ΅ΡΠΊΠΈΡ
ΡΠ²ΠΎΠΉΡΡΠ² Π±Π°ΡΡΠ΅ΡΠ½ΠΎΠ³ΠΎ ΠΏΠΎΠΊΡΡΡΠΈΡ, ΡΠ°ΠΊΠΈΡ
ΠΊΠ°ΠΊ ΡΠ΄Π°ΡΠΎΠΏΡΠΎΡΠ½ΠΎΡΡΡ ΠΈ ΡΠΎΠΏΡΠΎΡΠΈΠ²Π»Π΅Π½ΠΈΠ΅ ΠΈΡΡΠΈΡΠ°Π½ΠΈΡ.
ΠΠ½Π³ΠΈΠ±ΠΈΡΠΎΡ — ΠΠ΅Π½Π΅ΡΡΠ°Π½Ρ ΠΈΠ»ΠΈ Π³ΡΡΠ½ΡΠΎΠ²ΠΊΠ°, ΡΠ»Π°Π±ΠΎ ΡΠ°ΡΡΠ²ΠΎΡΠΈΠΌΠ°Ρ Π² Π²ΠΎΠ΄Π΅ ΠΈΠ»ΠΈ ΡΠ°ΡΡΠ²ΠΎΡΠΈΡΠ΅Π»Π΅, ΠΎΠ±ΡΠ°Π·ΡΡΡΠ°Ρ Ρ ΠΈΠΌΠΈΡΠ΅ΡΠΊΠΈΠΉ ΠΈΠ½Π³ΠΈΠ±ΠΈΡΠΎΡ ΠΈ ΡΡΡΠ΅ΠΊΡΠΈΠ²Π½ΠΎ ΠΏΠΎΠΊΡΡΠ²Π°ΡΡΠ°Ρ ΡΡΠ΅Π½ΠΊΠΈ ΠΊΠ°ΠΏΠΈΠ»Π»ΡΡΠΎΠ² Π² Π±Π΅ΡΠΎΠ½Π΅. ΠΠ°ΠΊ ΠΏΡΠ°Π²ΠΈΠ»ΠΎ, ΠΎΠ½ΠΈ ΠΏΡΠΈΠ΄Π°ΡΡ Π±Π΅ΡΠΎΠ½Ρ ΡΠ°ΠΊΠΈΠ΅ ΡΠ²ΠΎΠΉΡΡΠ²Π°, ΠΊΠ°ΠΊ Π³ΠΈΠ΄ΡΠΎΡΠΎΠ±Π½ΠΎΡΡΡ, Π½ΠΎ ΠΏΡΠΎΠΏΡΡΠΊΠ°ΡΡ ΡΠ΅ΡΠ΅Π· ΡΠ΅Π±Ρ Π²ΠΎΠ΄ΡΠ½ΠΎΠΉ ΠΏΠ°Ρ. ΠΡΠΈΠΌΠ΅ΡΠ°ΠΌΠΈ ΡΠ²Π»ΡΡΡΡΡ ΡΠΈΠ»Π°Π½-ΡΠΈΠ»ΠΎΠΊΡΠ°Π½Ρ ΠΈ Ρ.Π΄.
ΠΠ°Π»ΡΠ²Π°Π½ΠΈΠΊΠ° — Π¦ΠΈΠ½ΠΊΡΠΎΠ΄Π΅ΡΠΆΠ°ΡΠΈΠ΅ Π³ΡΡΠ½ΡΠΎΠ²ΠΊΠΈ, ΠΎΠ±Π΅ΡΠΏΠ΅ΡΠΈΠ²Π°ΡΡΠΈΠ΅ Π³Π°Π»ΡΠ²Π°Π½ΠΈΡΠ΅ΡΠΊΡΡ ΠΈΠ»ΠΈ ΠΊΠ°ΡΠΎΠ΄Π½ΡΡ Π·Π°ΡΠΈΡΡ ΡΠ΅ΡΠ½ΠΎΠ³ΠΎ ΠΌΠ΅ΡΠ°Π»Π»Π° (ΡΠΈΠ½ΠΊ ΠΆΠ΅ΡΡΠ²ΡΠ΅Ρ ΡΠΎΠ±ΠΎΠΉ, ΡΡΠΎΠ±Ρ Π·Π°ΡΠΈΡΠΈΡΡ ΡΠ΅ΡΠ½ΡΠΉ ΠΌΠ΅ΡΠ°Π»Π»). ΠΠ°Π»ΡΠ²Π°Π½ΠΈΡΠ΅ΡΠΊΠΈΠ΅ ΠΏΠΎΠΊΡΡΡΠΈΡ ΡΡΡΠ΅ΠΊΡΠΈΠ²Π½Ρ ΡΠΎΠ»ΡΠΊΠΎ ΠΏΡΠΈ Π½Π°Π½Π΅ΡΠ΅Π½ΠΈΠΈ Π½Π΅ΠΏΠΎΡΡΠ΅Π΄ΡΡΠ²Π΅Π½Π½ΠΎ Π½Π° Π³ΠΎΠ»ΡΠΉ ΠΌΠ΅ΡΠ°Π»Π». ΠΠ½ΠΈ ΠΏΡΠ΅Π΄ΠΎΡΠ²ΡΠ°ΡΠ°ΡΡ ΠΎΠ±ΡΠ°Π·ΠΎΠ²Π°Π½ΠΈΠ΅ Π·Π°ΡΠΎΠΆΠ΄Π°ΡΡΠΈΡ ΡΡ Π°Π½ΠΎΠ΄ΠΎΠ² Π² Π°ΡΠΌΠ°ΡΡΡΠ½ΠΎΠΉ ΡΡΠ°Π»ΠΈ Π² ΡΠΈΠΏΠΈΡΠ½ΠΎΠΉ ΡΠΈΡΡΠ°ΡΠΈΠΈ Π»Π°ΡΠ°ΡΠΈΠΎΠ½Π½ΠΎΠ³ΠΎ ΡΠ΅ΠΌΠΎΠ½ΡΠ°.
Π‘Π»Π΅Π΄ΡΡΡΠΈΠ΅ ΠΎΠ±ΡΠΈΠ΅ ΠΏΠΎΠΊΡΡΡΠΈΡ ΠΈ ΠΎΠ±ΡΠΈΠ΅ ΠΎΠΏΠΈΡΠ°Π½ΠΈΡ ΠΎΠ±ΡΡΠ½ΠΎ ΡΠΊΠ°Π·ΡΠ²Π°ΡΡΡΡ ΠΊΠΎΠ½ΡΡΠ»ΡΡΠ°Π½ΡΠ°ΠΌΠΈ.
ΠΠΊΡΠΈΠ»ΠΎΠ²ΡΠ΅ ΠΊΡΠ°ΡΠΊΠΈ — Π Π²ΠΎΠ΄ΠΎΡΠ°Π·Π±Π°Π²Π»ΡΠ΅ΠΌΡΡ
Π°ΠΊΡΠΈΠ»ΠΎΠ²ΡΡ
ΠΏΠΎΠΊΡΡΡΠΈΡΡ
ΡΠΌΠΎΠ»Ρ Π΄ΠΈΡΠΏΠ΅ΡΠ³ΠΈΡΡΡΡΡΡ Π² Π²ΠΎΠ΄Π΅ Ρ ΠΎΠ±ΡΠ°Π·ΠΎΠ²Π°Π½ΠΈΠ΅ΠΌ Π²ΠΎΠ΄Π½ΠΎΠΉ ΡΠΌΡΠ»ΡΡΠΈΠΈ.
ΠΠΎΠ΄ΠΎΡΠ°Π·Π±Π°Π²Π»ΡΠ΅ΠΌΡΠ΅ Π°ΠΊΡΠΈΠ»ΠΎΠ²ΡΠ΅ ΠΊΡΠ°ΡΠΊΠΈ ΠΏΡΠ΅Π΄Π½Π°Π·Π½Π°ΡΠ΅Π½Ρ Π΄Π»Ρ Π°ΡΠΌΠΎΡΡΠ΅ΡΠ½ΠΎΠ³ΠΎ Π²ΠΎΠ·Π΄Π΅ΠΉΡΡΠ²ΠΈΡ Π² ΠΊΠ°ΡΠ΅ΡΡΠ²Π΅ Π³ΡΡΠ½ΡΠΎΠ²ΠΊΠΈ ΠΈΠ»ΠΈ Π²Π΅ΡΡ Π½Π΅Π³ΠΎ ΡΠ»ΠΎΡ ΠΈ ΠΎΠ±Π»Π°Π΄Π°ΡΡ ΠΏΡΠ΅Π²ΠΎΡΡ ΠΎΠ΄Π½ΡΠΌ ΡΠΎΡ ΡΠ°Π½Π΅Π½ΠΈΠ΅ΠΌ ΡΠ²Π΅ΡΠ° ΠΈ Π±Π»Π΅ΡΠΊΠ°. ΠΠΊΡΠΈΠ»ΠΎΠ²ΡΠ΅ ΠΏΠΎΠ»ΠΈΠΌΠ΅ΡΡ ΠΎΡΠ²Π΅ΡΠΆΠ΄Π°ΡΡΡΡ ΠΏΡΡΠ΅ΠΌ ΠΊΠΎΠ°Π»Π΅ΡΡΠ΅Π½ΡΠΈΠΈ. ΠΠ½ΠΈ Π²ΠΎΠ·Π΄ΡΡ ΠΎΠΏΡΠΎΠ½ΠΈΡΠ°Π΅ΠΌΡ, ΡΡΡΠΎΠΉΡΠΈΠ²Ρ ΠΊ ΡΠ»ΡΡΡΠ°ΡΠΈΠΎΠ»Π΅ΡΠΎΠ²ΠΎΠΌΡ ΠΈΠ·Π»ΡΡΠ΅Π½ΠΈΡ ΠΈ ΡΠ²Π»ΡΡΡΡΡ Ρ ΠΎΡΠΎΡΠΈΠΌ Π±Π°ΡΡΠ΅ΡΠΎΠΌ Π΄Π»Ρ ΡΠ³Π»Π΅ΠΊΠΈΡΠ»ΠΎΠ³ΠΎ Π³Π°Π·Π°.
ΠΠ»ΠΊΠΈΠ΄Ρ — ΠΠ»ΠΊΠΈΠ΄Ρ ΠΎΠ±ΡΡΠ½ΠΎ ΠΏΡΠ΅Π΄ΡΡΠ°Π²Π»ΡΡΡ ΡΠΎΠ±ΠΎΠΉ Π½Π°ΡΡΡΠ°Π»ΡΠ½ΡΠ΅ ΠΌΠ°ΡΠ»Π° (ΡΠΎΠ΅Π²ΠΎΠ΅, ΡΡΠ½Π³ΠΎΠ²ΠΎΠ΅, ΡΡΠΈΡΠΎΠ»ΠΎΠ²ΠΎΠ΅), Ρ ΠΈΠΌΠΈΡΠ΅ΡΠΊΠΈ ΠΌΠΎΠ΄ΠΈΡΠΈΡΠΈΡΠΎΠ²Π°Π½Π½ΡΠ΅ Π΄Π»Ρ ΡΠ»ΡΡΡΠ΅Π½ΠΈΡ ΡΠΊΠΎΡΠΎΡΡΠΈ ΠΎΡΠ²Π΅ΡΠΆΠ΄Π΅Π½ΠΈΡ, Ρ ΠΈΠΌΠΈΡΠ΅ΡΠΊΠΎΠΉ ΡΡΠΎΠΉΠΊΠΎΡΡΠΈ ΠΈ ΡΠ²Π΅ΡΠ΄ΠΎΡΡΠΈ. ΠΠ»ΠΊΠΈΠ΄Ρ, ΠΌΠΎΠ΄ΠΈΡΠΈΡΠΈΡΠΎΠ²Π°Π½Π½ΡΠ΅ ΡΠ΅Π½ΠΎΠ»ΠΎΠΌ, ΠΈΡΠΏΠΎΠ»ΡΠ·ΡΡΡΡΡ Π² ΠΊΠ°ΡΠ΅ΡΡΠ²Π΅ Π³ΡΡΠ½ΡΠΎΠ²ΠΊΠΈ, Π° ΡΠΈΠ»ΠΈΠΊΠΎΠ½ΠΎΠ²ΡΠ΅ Π°Π»ΠΊΠΈΠ΄Ρ ΠΈΡΠΏΠΎΠ»ΡΠ·ΡΡΡΡΡ Π² ΠΊΠ°ΡΠ΅ΡΡΠ²Π΅ Π²Π΅ΡΡ Π½Π΅Π³ΠΎ ΡΠ»ΠΎΡ Π³ΡΡΠ½ΡΠΎΠ²ΠΊΠΈ Π΄Π»Ρ Π°ΡΠΌΠΎΡΡΠ΅ΡΠ½ΡΡ ΡΡΠ»ΠΎΠ²ΠΈΠΉ ΡΠΊΡΠΏΠ»ΡΠ°ΡΠ°ΡΠΈΠΈ, Π° ΡΠ°ΠΊΠΆΠ΅ Π² ΠΊΠ°ΡΠ΅ΡΡΠ²Π΅ Π²Π΅ΡΡ Π½Π΅Π³ΠΎ ΡΠ»ΠΎΡ Π΄Π»Ρ Π°ΡΠΌΠΎΡΡΠ΅ΡΠ½ΡΡ ΡΡΠ»ΠΎΠ²ΠΈΠΉ ΡΠΊΡΠΏΠ»ΡΠ°ΡΠ°ΡΠΈΠΈ, ΠΎΡΠΎΠ±Π΅Π½Π½ΠΎ Π΄Π»Ρ ΠΌΠ΅ΡΠ°Π»Π»ΠΎΠ². ΠΠ½ΠΈ Π½Π΅ ΠΏΠΎΠ΄Ρ ΠΎΠ΄ΡΡ Π΄Π»Ρ ΡΠ΅Π»ΠΎΡΠ½ΡΡ (Π±Π΅ΡΠΎΠ½Π½ΡΡ ΠΈΠ»ΠΈ ΠΊΠ°ΠΌΠ΅Π½Π½ΡΡ ) ΠΏΠΎΠ²Π΅ΡΡ Π½ΠΎΡΡΠ΅ΠΉ ΠΈΠ»ΠΈ ΡΡΠ΅Π΄. ΠΠ»ΠΊΠΈΠ΄Ρ ΠΎΡΠ²Π΅ΡΠΆΠ΄Π°ΡΡΡΡ ΠΏΡΡΠ΅ΠΌ ΠΎΠΊΠΈΡΠ»Π΅Π½ΠΈΡ ΠΎΠ»ΠΈΡΡ Π²ΠΎΠ·Π΄ΡΡ ΠΎΠΌ.
ΠΠΈΡΡΠΌΠ½ΡΠ΅ — ΠΠΈΡΡΠΌΠ½ΡΠ΅ ΠΏΠΎΠΊΡΡΡΠΈΡ ΠΏΡΠ΅Π΄ΡΡΠ°Π²Π»ΡΡΡ ΡΠΎΠ±ΠΎΠΉ ΡΡΠΆΠ΅Π»ΡΠ΅ ΠΌΠ°ΡΠ΅ΡΠΈΠ°Π»Ρ, Π½Π°Π½ΠΎΡΠΈΠΌΡΠ΅ ΡΠ°Π·Π±Π°Π²Π»Π΅Π½Π½ΡΠΌ ΡΠ°ΡΡΠ²ΠΎΡΠΈΡΠ΅Π»Π΅ΠΌ. ΠΠ½ΠΈ ΠΎΠ±Π»Π°Π΄Π°ΡΡ Ρ
ΠΎΡΠΎΡΠ΅ΠΉ Π²Π»Π°Π³ΠΎΠ½Π΅ΠΏΡΠΎΠ½ΠΈΡΠ°Π΅ΠΌΠΎΡΡΡΡ ΠΈ Ρ
ΠΈΠΌΠΈΡΠ΅ΡΠΊΠΎΠΉ ΡΡΠΎΠΉΠΊΠΎΡΡΡΡ ΠΎΡ ΡΡΠ΅Π΄Π½Π΅ΠΉ Π΄ΠΎ Ρ
ΠΎΡΠΎΡΠ΅ΠΉ, Π½ΠΎ Π½Π΅ ΡΡΡΠΎΠΉΡΠΈΠ²Ρ ΠΊ ΡΠ°ΡΡΠ²ΠΎΡΠΈΡΠ΅Π»ΡΠΌ. ΠΠΎΠΌΠΌΠ΅ΡΡΠ΅ΡΠΊΠΈΠ΅ Π±ΠΈΡΡΠΌΠ½ΡΠ΅ ΠΏΡΠΎΠ΄ΡΠΊΡΡ Π½Π°Π·Π½Π°ΡΠ°ΡΡΡΡ ΠΊΠΎΠ½ΡΡΠ»ΡΡΠ°Π½ΡΠ°ΠΌΠΈ Π² ΠΎΠ³ΡΠ°Π½ΠΈΡΠ΅Π½Π½ΠΎΠΌ ΠΊΠΎΠ»ΠΈΡΠ΅ΡΡΠ²Π΅ Π΄Π»Ρ Π·Π°ΡΠΈΡΡ Π°Π»ΡΠΌΠΈΠ½ΠΈΠ΅Π²ΡΡ
ΠΏΠΎΠ²Π΅ΡΡ
Π½ΠΎΡΡΠ΅ΠΉ, ΠΊΠΎΠ½ΡΠ°ΠΊΡΠΈΡΡΡΡΠΈΡ
Ρ ΡΠ΅ΠΌΠ΅Π½ΡΠ½ΡΠΌ ΠΌΠ°ΡΠ΅ΡΠΈΠ°Π»ΠΎΠΌ ΠΈΠ»ΠΈ ΡΠ²Π°ΡΠ½ΡΠΌΠΈ ΡΠΎΠ΅Π΄ΠΈΠ½Π΅Π½ΠΈΡΠΌΠΈ ΡΡΠ°Π»ΡΠ½ΡΡ
ΠΈ ΠΌΠ΅Π΄Π½ΡΡ
ΠΊΠ°Π±Π΅Π»Π΅ΠΉ. ΠΠΈΡΡΠΌΠ½ΡΠ΅ ΠΏΠΎΠΊΡΡΡΠΈΡ ΠΎΡΠ²Π΅ΡΠΆΠ΄Π°ΡΡΡΡ ΠΏΡΡΠ΅ΠΌ ΠΈΡΠΏΠ°ΡΠ΅Π½ΠΈΡ ΡΠ°ΡΡΠ²ΠΎΡΠΈΡΠ΅Π»Ρ.
ΠΠΏΠΎΠΊΡΠΈΠ΄Π½Π°Ρ ΡΠΌΠΎΠ»Π°, Π°ΠΌΠΈΠ½ — ΠΠΌΠΈΠ½ΠΎΠ²ΡΠ΅ ΡΠΏΠΎΠΊΡΠΈΠ΄Π½ΡΠ΅ ΡΠΌΠΎΠ»Ρ ΠΏΡΠ΅Π΄ΡΡΠ°Π²Π»ΡΡΡ ΡΠΎΠ±ΠΎΠΉ Π΄Π²ΡΡ ΠΊΠΎΠΌΠΏΠΎΠ½Π΅Π½ΡΠ½ΡΠ΅ ΠΏΠΎΠΊΡΡΡΠΈΡ, ΠΊΠΎΡΠΎΡΡΠ΅ ΠΊΠ°ΡΠ°Π»ΠΈΠ·ΠΈΡΡΡΡΡΡ (ΠΎΡΠ²Π΅ΡΠΆΠ΄Π°ΡΡΡΡ) Π°ΠΌΠΈΠ½Π½ΡΠΌ ΠΎΡΠ²Π΅ΡΠ΄ΠΈΡΠ΅Π»Π΅ΠΌ Ρ ΠΏΠΎΠ»ΡΡΠ΅Π½ΠΈΠ΅ΠΌ ΡΠ²Π΅ΡΠ΄ΠΎΠ³ΠΎ, ΠΏΡΠΎΡΠ½ΠΎ ΡΠ²ΡΠ·Π°Π½Π½ΠΎΠ³ΠΎ, Ρ ΠΈΠΌΠΈΡΠ΅ΡΠΊΠΈ ΡΡΠΎΠΉΠΊΠΎΠ³ΠΎ (ΡΠ΅Π»ΠΎΡΠΈ, ΠΊΠΈΡΠ»ΠΎΡΡ ΠΈ ΡΠ°ΡΡΠ²ΠΎΡΠΈΡΠ΅Π»Ρ) ΠΏΡΠΎΠ΄ΡΠΊΡΠ°, Π½ΠΎ ΠΏΡΠΈ Π½Π°Π½Π΅ΡΠ΅Π½ΠΈΠΈ ΠΎΠ½ΠΈ ΡΡΠ²ΡΡΠ²ΠΈΡΠ΅Π»ΡΠ½Ρ ΠΊ Π²Π»Π°Π³Π΅ ΠΈ ΡΠ΅ΠΌΠΏΠ΅ΡΠ°ΡΡΡΠ΅. ΠΠ½ΠΈ ΠΏΡΠ΅Π΄Π½Π°Π·Π½Π°ΡΠ΅Π½Ρ Π΄Π»Ρ Π·Π°Ρ ΠΎΡΠΎΠ½Π΅Π½ΠΈΡ ΠΈ ΠΏΠΎΠ³ΡΡΠΆΠ΅Π½ΠΈΡ Π² Π²ΠΎΠ΄Ρ, Π½ΠΎ ΠΎΠ½ΠΈ Π²ΡΡΠ²Π΅ΡΠ°ΡΡ ΠΈ ΠΌΠ΅Π»Π΅ΡΡ ΠΏΠΎΠ΄ ΠΏΡΡΠΌΡΠΌΠΈ ΡΠΎΠ»Π½Π΅ΡΠ½ΡΠΌΠΈ Π»ΡΡΠ°ΠΌΠΈ. ΠΠΌΠΈΠ½ΠΎΠ²ΡΠ΅ ΡΠΏΠΎΠΊΡΠΈΠ΄Π½ΡΠ΅ ΡΠΌΠΎΠ»Ρ ΠΎΡΠ²Π΅ΡΠΆΠ΄Π°ΡΡΡΡ Ρ ΠΈΠΌΠΈΡΠ΅ΡΠΊΠΎΠΉ ΡΠ΅Π°ΠΊΡΠΈΠ΅ΠΉ.
ΠΠΏΠΎΠΊΡΠΈΠ΄, ΠΏΠΎΠ»ΠΈΠ°ΠΌΠΈΠ΄ — ΠΠΎΠ»ΠΈΠ°ΠΌΠΈΠ΄Π½ΡΠ΅ ΡΠΏΠΎΠΊΡΠΈΠ΄Ρ ΠΏΡΠ΅Π΄ΡΡΠ°Π²Π»ΡΡΡ ΡΠΎΠ±ΠΎΠΉ Π΄Π²ΡΡ
ΠΊΠΎΠΌΠΏΠΎΠ½Π΅Π½ΡΠ½ΡΠ΅ ΠΏΠΎΠΊΡΡΡΠΈΡ, ΠΊΠ°ΡΠ°Π»ΠΈΠ·ΠΈΡΡΠ΅ΠΌΡΠ΅ ΠΏΠΎΠ»ΠΈΠ°ΠΌΠΈΠ΄Π½ΡΠΌ ΠΎΡΠ²Π΅ΡΠ΄ΠΈΡΠ΅Π»Π΅ΠΌ Π΄Π»Ρ ΠΎΠ±Π΅ΡΠΏΠ΅ΡΠ΅Π½ΠΈΡ ΠΏΡΠ΅Π²ΠΎΡΡ
ΠΎΠ΄Π½ΠΎΠΉ ΡΡΡΠΎΠΉΡΠΈΠ²ΠΎΡΡΠΈ ΠΊ Π²ΠΎΠ΄Π΅ ΠΈ ΡΠ°ΡΡΠ²ΠΎΡΠ°ΠΌ ΡΠΎΠ»Π΅ΠΉ, Π½ΠΎ ΠΎΠ½ΠΈ Π½Π΅ ΠΎΠ±Π΅ΡΠΏΠ΅ΡΠΈΠ²Π°ΡΡ Ρ
ΠΈΠΌΠΈΡΠ΅ΡΠΊΠΎΠΉ ΡΡΠΎΠΉΠΊΠΎΡΡΠΈ Π°ΠΌΠΈΠ½ΠΎΡΠΏΠΎΠΊΡΠΈΠ΄Π½ΠΎΠΉ ΡΠΌΠΎΠ»Ρ. ΠΠΎΠ»ΠΈΠ°ΠΌΠΈΠ΄Ρ ΠΎΠ±Π»Π°Π΄Π°ΡΡ Π±ΠΎΠ»ΡΡΠ΅ΠΉ Π³ΠΈΠ±ΠΊΠΎΡΡΡΡ, ΡΠ΅ΠΌ Π°ΠΌΠΈΠ½ΠΎΠ²ΡΠ΅ ΡΠΏΠΎΠΊΡΠΈΠ΄Π½ΡΠ΅ ΡΠΌΠΎΠ»Ρ. ΠΠ½ΠΈ ΠΏΡΠ΅Π΄Π½Π°Π·Π½Π°ΡΠ΅Π½Ρ Π΄Π»Ρ Π·Π°Ρ
ΠΎΡΠΎΠ½Π΅Π½ΠΈΡ ΠΈ ΠΏΠΎΠ³ΡΡΠΆΠ΅Π½ΠΈΡ Π² Π²ΠΎΠ΄Ρ, Π½ΠΎ ΠΎΠ½ΠΈ Π²ΡΡΠ²Π΅ΡΠ°ΡΡ ΠΈ ΠΌΠ΅Π»Π΅ΡΡ ΠΏΠΎΠ΄ ΠΏΡΡΠΌΡΠΌΠΈ ΡΠΎΠ»Π½Π΅ΡΠ½ΡΠΌΠΈ Π»ΡΡΠ°ΠΌΠΈ. ΠΠΎΠ»ΠΈΠ°ΠΌΠΈΠ΄Π½ΡΠ΅ ΡΠΏΠΎΠΊΡΠΈΠ΄Π½ΡΠ΅ ΡΠΌΠΎΠ»Ρ ΠΎΡΠ²Π΅ΡΠΆΠ΄Π°ΡΡΡΡ Π² ΡΠ΅Π·ΡΠ»ΡΡΠ°ΡΠ΅ Ρ
ΠΈΠΌΠΈΡΠ΅ΡΠΊΠΎΠΉ ΡΠ΅Π°ΠΊΡΠΈΠΈ.
ΠΠΏΠΎΠΊΡΠΈΠ΄Π½Π°Ρ ΡΠΌΠΎΠ»Π°, ΠΊΠ°ΠΌΠ΅Π½Π½ΠΎΡΠ³ΠΎΠ»ΡΠ½Π°Ρ ΡΠΌΠΎΠ»Π° — ΠΠΏΠΎΠΊΡΠΈΠ΄Π½ΡΠ΅ ΡΠΌΠΎΠ»Ρ Π½Π° ΠΎΡΠ½ΠΎΠ²Π΅ ΠΊΠ°ΠΌΠ΅Π½Π½ΠΎΡΠ³ΠΎΠ»ΡΠ½ΠΎΠΉ ΡΠΌΠΎΠ»Ρ ΠΎΠ±ΡΡΠ½ΠΎ ΠΏΡΠ΅Π΄ΡΡΠ°Π²Π»ΡΡΡ ΡΠΎΠ±ΠΎΠΉ Π°ΠΌΠΈΠ½ΠΎΠ²ΡΠ΅ ΠΈΠ»ΠΈ ΠΏΠΎΠ»ΠΈΠ°ΠΌΠΈΠ΄Π½ΡΠ΅ ΡΠΏΠΎΠΊΡΠΈΠ΄Π½ΡΠ΅ ΡΠΌΠΎΠ»Ρ, ΠΌΠΎΠ΄ΠΈΡΠΈΡΠΈΡΠΎΠ²Π°Π½Π½ΡΠ΅ ΡΠΌΠΎΠ»ΠΎΠΉ Π½Π° ΠΎΡΠ½ΠΎΠ²Π΅ ΠΊΠ°ΠΌΠ΅Π½Π½ΠΎΡΠ³ΠΎΠ»ΡΠ½ΠΎΠΉ ΡΠΌΠΎΠ»Ρ Π΄Π»Ρ ΠΏΠΎΠ»ΡΡΠ΅Π½ΠΈΡ ΡΠΎΠ»ΡΡΠΎΡΠ»ΠΎΠΉΠ½ΠΎΠΉ ΠΏΠ»Π΅Π½ΠΊΠΈ, ΠΎΠ±Π»Π°Π΄Π°ΡΡΠ΅ΠΉ Ρ ΠΎΡΠΎΡΠ΅ΠΉ Ρ ΠΈΠΌΠΈΡΠ΅ΡΠΊΠΎΠΉ ΡΡΠΎΠΉΠΊΠΎΡΡΡΡ ΠΈ ΠΎΡΠ»ΠΈΡΠ½ΠΎΠΉ Π²ΠΎΠ΄ΠΎΡΡΠΎΠΉΠΊΠΎΡΡΡΡ. ΠΠ½ΠΈ ΠΈΠΌΠ΅ΡΡ ΡΠ΅Π½Π΄Π΅Π½ΡΠΈΡ ΡΡΠ°Π½ΠΎΠ²ΠΈΡΡΡΡ Π»ΠΎΠΌΠΊΠΈΠΌΠΈ Ρ Π²ΠΎΠ·ΡΠ°ΡΡΠΎΠΌ ΠΈ ΡΠ°ΡΡΠ»Π°ΠΈΠ²Π°ΡΡΡΡ ΠΌΠ΅ΠΆΠ΄Ρ ΡΠ»ΠΎΡΠΌΠΈ ΠΈΠ»ΠΈ ΠΏΠΎΠ΄ ΡΠ΅ΠΌΠΎΠ½ΡΠ½ΡΠΌΠΈ Π·Π°ΠΏΠ»Π°ΡΠ°ΠΌΠΈ. ΠΠ½ΠΈ ΠΏΡΠ΅Π΄Π½Π°Π·Π½Π°ΡΠ΅Π½Ρ Π΄Π»Ρ Π·Π°Ρ ΠΎΡΠΎΠ½Π΅Π½ΠΈΡ ΠΈ ΠΏΠΎΠ³ΡΡΠΆΠ΅Π½ΠΈΡ Π² Π²ΠΎΠ΄Ρ, Π½ΠΎ ΠΏΠΎΠ΄ ΠΏΡΡΠΌΡΠΌΠΈ ΡΠΎΠ»Π½Π΅ΡΠ½ΡΠΌΠΈ Π»ΡΡΠ°ΠΌΠΈ ΠΎΠ½ΠΈ Π²ΡΡΠ²Π΅ΡΠ°ΡΡ ΠΈ ΠΌΠ΅Π»Π΅ΡΡ. ΠΠΏΠΎΠΊΡΠΈΠ΄Π½ΡΠ΅ ΡΠΌΠΎΠ»Ρ Π½Π° ΠΎΡΠ½ΠΎΠ²Π΅ ΠΊΠ°ΠΌΠ΅Π½Π½ΠΎΡΠ³ΠΎΠ»ΡΠ½ΠΎΠΉ ΡΠΌΠΎΠ»Ρ ΠΎΡΠ²Π΅ΡΠΆΠ΄Π°ΡΡΡΡ Π² ΡΠ΅Π·ΡΠ»ΡΡΠ°ΡΠ΅ Ρ ΠΈΠΌΠΈΡΠ΅ΡΠΊΠΎΠΉ ΡΠ΅Π°ΠΊΡΠΈΠΈ.
ΠΠΏΠΎΠΊΡΠΈΠ΄Π½Π°Ρ ΡΠΌΠΎΠ»Π°, ΡΠ²ΡΠ·Π°Π½Π½Π°Ρ ΠΏΠ»Π°Π²Π»Π΅Π½ΠΈΠ΅ΠΌ — ΠΠΏΠΎΠΊΡΠΈΠ΄Π½ΡΠ΅ ΡΠΌΠΎΠ»Ρ, ΡΠ²ΡΠ·Π°Π½Π½ΡΠ΅ ΠΏΠ»Π°Π²Π»Π΅Π½ΠΈΠ΅ΠΌ (ΠΎΠ±ΡΡΠ½ΠΎ Π½Π°Π·ΡΠ²Π°Π΅ΠΌΡΠ΅ ΠΏΠΎΡΠΎΡΠΊΠΎΠ²ΡΠΌΠΈ ΠΏΠΎΠΊΡΡΡΠΈΡΠΌΠΈ), ΠΏΡΠ΅Π΄ΡΡΠ°Π²Π»ΡΡΡ ΡΠΎΠ±ΠΎΠΉ Π³ΠΎΡΠΎΠ²ΡΠ΅ ΠΏΠΎΠΊΡΡΡΠΈΡ Π² Π²ΠΈΠ΄Π΅ ΠΏΠΎΡΠΎΡΠΊΠ°. Π‘ΡΡΠ΅ΡΡΠ²ΡΠ΅Ρ Π΄Π²Π° ΠΌΠ΅ΡΠΎΠ΄Π° Π½Π°Π½Π΅ΡΠ΅Π½ΠΈΡ: ΠΊΠΈΠΏΡΡΠΈΠΉ ΡΠ»ΠΎΠΉ ΠΈ ΡΠ»Π΅ΠΊΡΡΠΎΡΡΠ°ΡΠΈΡΠ΅ΡΠΊΠΈΠΉ. Π ΠΌΠ΅ΡΠΎΠ΄Π΅ ΠΊΠΈΠΏΡΡΠ΅Π³ΠΎ ΡΠ»ΠΎΡ ΠΌΠ΅ΡΠ°Π»Π»ΠΈΡΠ΅ΡΠΊΠΈΠ΅ ΠΈΠ·Π΄Π΅Π»ΠΈΡ ΠΏΡΠ΅Π΄Π²Π°ΡΠΈΡΠ΅Π»ΡΠ½ΠΎ Π½Π°Π³ΡΠ΅Π²Π°ΡΡ Π΄ΠΎ ΡΠ΅ΠΌΠΏΠ΅ΡΠ°ΡΡΡΡ ΠΏΠ»Π°Π²Π»Π΅Π½ΠΈΡ ΠΈ ΠΏΠΎΠ³ΡΡΠΆΠ°ΡΡ Π² ΠΏΠΎΡΠΎΡΠΊΠΎΠ²ΠΎ-ΡΠΏΠΎΠΊΡΠΈΠ΄Π½ΡΠΉ ΡΠ°ΡΡΠ²ΠΎΡ. Π ΡΠ»Π΅ΠΊΡΡΠΎΡΡΠ°ΡΠΈΡΠ΅ΡΠΊΠΎΠΌ ΠΌΠ΅ΡΠΎΠ΄Π΅ ΡΠ°ΡΡΠΈΡΡ ΡΠΏΠΎΠΊΡΠΈΠ΄Π½ΠΎΠ³ΠΎ ΠΏΠΎΡΠΎΡΠΊΠ° Π·Π°ΡΡΠΆΠ°ΡΡΡΡ Π²ΡΡΠΎΠΊΠΈΠΌ Π½Π°ΠΏΡΡΠΆΠ΅Π½ΠΈΠ΅ΠΌ, Π° Π·Π°ΡΠ΅ΠΌ ΠΌΠ΅ΡΠ°Π»Π»ΠΈΡΠ΅ΡΠΊΠΎΠ΅ ΠΈΠ·Π΄Π΅Π»ΠΈΠ΅ ΡΠ°ΡΠΏΡΠ»ΡΠ΅ΡΡΡ. ΠΠΎΡΠ»Π΅ ΡΠ°ΡΠΏΡΠ»Π΅Π½ΠΈΡ ΠΈΠ·Π΄Π΅Π»ΠΈΠ΅ ΠΏΠΎΠΌΠ΅ΡΠ°ΡΡ Π² ΠΏΠ΅ΡΡ Π΄Π»Ρ ΠΎΡΠ²Π΅ΡΠΆΠ΄Π΅Π½ΠΈΡ ΠΏΡΠΈ ΡΠ΅ΠΌΠΏΠ΅ΡΠ°ΡΡΡΠ΅ ΠΎΡ 180Β°C Π΄ΠΎ 350Β°C. ΠΠΏΠΎΠΊΡΠΈΠ΄Π½ΡΠ΅ ΡΠΌΠΎΠ»Ρ, ΡΠ²ΡΠ·Π°Π½Π½ΡΠ΅ ΠΏΠ»Π°Π²Π»Π΅Π½ΠΈΠ΅ΠΌ, ΠΏΡΠ΅Π΄Π½Π°Π·Π½Π°ΡΠ΅Π½Ρ Π΄Π»Ρ Π°ΡΠΌΠΈΡΠΎΠ²Π°Π½ΠΈΡ ΡΡΠ°Π»ΠΈ, Π½ΠΎ ΠΎΠ½ΠΈ ΡΡΠ°Π½ΠΎΠ²ΡΡΡΡ Ρ
ΡΡΠΏΠΊΠΈΠΌΠΈ ΠΈ Π½Π΅ ΠΌΠΎΠ³ΡΡ Π·Π°ΡΠΈΡΠΈΡΡ ΡΡΠ°Π»Ρ Π² Π΄ΠΎΠ»Π³ΠΎΡΡΠΎΡΠ½ΠΎΠΉ ΠΏΠ΅ΡΡΠΏΠ΅ΠΊΡΠΈΠ²Π΅. ΠΠ½ΠΈ Π΄Π΅ΠΉΡΡΠ²ΡΡΡ ΠΊΠ°ΠΊ Π±Π°ΡΡΠ΅Ρ Π΄Π»Ρ ΠΏΡΡΠΌΠΎΠ³ΠΎ ΠΊΠΎΠ½ΡΠ°ΠΊΡΠ° ΡΡΠ°Π»ΠΈ ΡΠΎ ΡΠ΅Π»ΠΎΡΠ½ΡΠΌ Π±Π΅ΡΠΎΠ½ΠΎΠΌ ΠΈ Π»ΠΈΡΠ°ΡΡ Π°ΡΠΌΠ°ΡΡΡΠ½ΡΡ ΡΡΠ°Π»Ρ Π΅ΡΡΠ΅ΡΡΠ²Π΅Π½Π½ΠΎΠΉ Π·Π°ΡΠΈΡΡ ΠΎΡ ΡΠ΅Π»ΠΎΡΠ½ΠΎΠ³ΠΎ Π±Π΅ΡΠΎΠ½Π°.
ΠΠ΅ΠΎΡΠ³Π°Π½ΠΈΡΠ΅ΡΠΊΠΈΠ΅ ΡΠΈΠ½ΠΊΠΎΠ²ΡΠ΅ Π³ΡΡΠ½ΡΠΎΠ²ΠΊΠΈ β ΠΠ΅ΠΎΡΠ³Π°Π½ΠΈΡΠ΅ΡΠΊΠΈΠ΅ ΡΠΈΠ½ΠΊΠΎΠ²ΡΠ΅ Π³ΡΡΠ½ΡΠΎΠ²ΠΊΠΈ ΠΏΡΠ΅Π΄ΡΡΠ°Π²Π»ΡΡΡ ΡΠΎΠ±ΠΎΠΉ Π³ΡΡΠ½ΡΠΎΠ²ΠΊΠΈ Ρ Π²ΡΡΠΎΠΊΠΈΠΌ ΡΠΎΠ΄Π΅ΡΠΆΠ°Π½ΠΈΠ΅ΠΌ (ΠΊΠ³ Π½Π° Π»ΠΈΡΡ) ΠΌΠ΅ΡΠ°Π»Π»ΠΈΡΠ΅ΡΠΊΠΎΠ³ΠΎ ΡΠΈΠ½ΠΊΠ° Π΄Π»Ρ ΠΏΠΈΠ³ΠΌΠ΅Π½ΡΠ°ΡΠΈΠΈ (ΠΎΡΡΡΠ΄Π° ΡΠ΅ΡΠΌΠΈΠ½ Β«Π±ΠΎΠ³Π°ΡΡΠ΅ ΡΠΈΠ½ΠΊΠΎΠΌΒ») ΠΈ ΠΎΡΠ½ΠΎΠ²Π°Π½Π½ΡΠ΅ Π»ΠΈΠ±ΠΎ Π½Π° ΡΠ°ΡΡΠ²ΠΎΡΠΈΡΠ΅Π»Π΅, Π»ΠΈΠ±ΠΎ Π½Π° Π²ΠΎΠ΄Π½ΠΎΠΉ ΠΎΡΠ½ΠΎΠ²Π΅. Π Π·Π°Π²ΠΈΡΠΈΠΌΠΎΡΡΠΈ ΠΎΡ ΠΈΡΠΏΠΎΠ»ΡΠ·ΡΠ΅ΠΌΠΎΠ³ΠΎ ΡΠ°ΡΡΠ²ΠΎΡΠΈΡΠ΅Π»Ρ ΠΈ ΡΠΌΠΎΠ» ΠΏΠΎΠΊΡΡΡΠΈΠ΅ ΠΌΠΎΠΆΠ΅Ρ ΠΏΡΠ΅Π΄ΡΡΠ°Π²Π»ΡΡΡ ΡΠΎΠ±ΠΎΠΉ ΡΠΏΠΎΠΊΡΠΈΠ΄Π½ΡΡ ΡΠΌΠΎΠ»Ρ Ρ Π²ΡΡΠΎΠΊΠΈΠΌ ΡΠΎΠ΄Π΅ΡΠΆΠ°Π½ΠΈΠ΅ΠΌ ΡΠΈΠ½ΠΊΠ° ΠΈΠ»ΠΈ ΡΡΠ΅ΡΠ°Π½. ΠΡΠΈ ΠΏΠΎΠΊΡΡΡΠΈΡ ΡΠ²Π»ΡΡΡΡΡ ΠΈΡΠΊΠ»ΡΡΠΈΡΠ΅Π»ΡΠ½ΠΎ Π³ΡΡΠ½ΡΠΎΠ²ΠΎΡΠ½ΡΠΌΠΈ, ΠΏΠΎΡΠΊΠΎΠ»ΡΠΊΡ ΠΎΠ±Π΅ΡΠΏΠ΅ΡΠΈΠ²Π°ΡΡ Π³Π°Π»ΡΠ²Π°Π½ΠΈΡΠ΅ΡΠΊΡΡ ΠΈΠ»ΠΈ ΠΊΠ°ΡΠΎΠ΄Π½ΡΡ Π·Π°ΡΠΈΡΡ ΡΡΠ°Π»ΡΠ½ΠΎΠΉ ΠΏΠΎΠ΄Π»ΠΎΠΆΠΊΠΈ. ΠΠ΅ΠΎΡΠ³Π°Π½ΠΈΡΠ΅ΡΠΊΠΈΠ΅ ΡΠΈΠ½ΠΊΠΎΠ²ΡΠ΅ ΡΠΏΠ»Π°Π²Ρ ΠΏΡΠ΅Π΄Π½Π°Π·Π½Π°ΡΠ΅Π½Ρ Π΄Π»Ρ ΡΠΊΡΠΏΠ»ΡΠ°ΡΠ°ΡΠΈΠΈ Π² Π°ΡΠΌΠΎΡΡΠ΅ΡΠ½ΡΡ
ΡΡΠ»ΠΎΠ²ΠΈΡΡ
ΠΈ ΠΏΡΠΈ ΠΏΠΎΠ³ΡΡΠΆΠ΅Π½ΠΈΠΈ Π² Π²ΠΎΠ΄Ρ, Π½ΠΎ Π½Π° Π½ΠΈΡ
ΠΌΠΎΠΆΠ½ΠΎ Π½Π°Π½ΠΎΡΠΈΡΡ Π²Π΅ΡΡ
Π½Π΅Π΅ ΠΏΠΎΠΊΡΡΡΠΈΠ΅ Π΄Π»Ρ ΠΏΡΠΎΠ΄Π»Π΅Π½ΠΈΡ ΡΡΠΎΠΊΠ° ΠΈΡ
ΡΠ»ΡΠΆΠ±Ρ. ΠΡΠ±ΠΎΡ ΠΏΠΎΠ΄Ρ
ΠΎΠ΄ΡΡΠ΅Π³ΠΎ ΠΌΠ°ΡΠ΅ΡΠΈΠ°Π»Π° Π΄Π»Ρ Π²Π΅ΡΡ
Π½Π΅Π³ΠΎ ΠΏΠΎΠΊΡΡΡΠΈΡ Π½Π΅ΠΎΠ±Ρ
ΠΎΠ΄ΠΈΠΌ Π΄Π»Ρ ΠΏΡΠ΅Π΄ΠΎΡΠ²ΡΠ°ΡΠ΅Π½ΠΈΡ Π²ΡΠ΄Π΅Π»Π΅Π½ΠΈΡ Π³Π°Π·Π° ΠΈΠ· Π½Π΅ΠΎΡΠ³Π°Π½ΠΈΡΠ΅ΡΠΊΠΎΠ³ΠΎ ΡΠΈΠ½ΠΊΠ°, ΡΡΠΎ ΠΏΡΠΈΠ²ΠΎΠ΄ΠΈΡ ΠΊ ΠΎΠ±ΡΠ°Π·ΠΎΠ²Π°Π½ΠΈΡ Π½Π΅Π±ΠΎΠ»ΡΡΠΈΡ
ΠΎΡΠ²Π΅ΡΡΡΠΈΠΉ Π² Π²Π΅ΡΡ
Π½Π΅ΠΌ ΠΏΠΎΠΊΡΡΡΠΈΠΈ. ΠΠΎΠ΄Ρ
ΠΎΠ΄ΠΈΡ Π΄Π»Ρ ΡΡΠ°Π»ΡΠ½ΡΡ
ΡΡΠ΅ΡΠΆΠ½Π΅ΠΉ ΠΈ ΠΏΡΠΎΡΠΈΠ»Π΅ΠΉ ΠΊΠΎΠ½ΡΡΡΡΠΊΡΠΈΠΎΠ½Π½ΠΎΠΉ ΡΡΠ°Π»ΠΈ, Π·Π°Π³Π»ΡΠ±Π»Π΅Π½Π½ΡΡ
Π² Π±Π΅ΡΠΎΠ½, Π·Π°Π³ΡΡΠ·Π½Π΅Π½Π½ΡΠΉ Ρ
Π»ΠΎΡΠΈΠ΄Π°ΠΌΠΈ.
ΠΠΎΠ»ΠΈΡΡΠ΅ΡΠ°Π½ — Π’Π΅Ρ
Π½ΠΈΡΠ΅ΡΠΊΠΈ ΠΏΠΎΠ»ΠΈΡΡΠ΅ΡΠ°Π½ ΡΠ²Π»ΡΠ΅ΡΡΡ ΠΏΠΎΠ΄ΠΊΠ»Π°ΡΡΠΎΠΌ ΡΡΠ΅ΡΠ°Π½Π°. ΠΠ²ΡΡ
ΠΊΠΎΠΌΠΏΠΎΠ½Π΅Π½ΡΠ½ΡΠΉ ΠΏΠΎΠ»ΠΈΡΡΠ΅ΡΠ°Π½ ΡΠΎΠ·Π΄Π°Π΅ΡΡΡ ΠΏΡΡΠ΅ΠΌ Ρ
ΠΈΠΌΠΈΡΠ΅ΡΠΊΠΎΠ³ΠΎ ΠΎΠ±ΡΠ΅Π΄ΠΈΠ½Π΅Π½ΠΈΡ ΠΏΠΎΠ»ΠΈΠΈΠ·ΠΎΡΠΈΠ°Π½Π°ΡΠ° ΠΈ ΠΏΠΎΠ»ΠΈΠΎΠ»Π° Ρ ΠΏΠΎΠ»ΡΡΠ΅Π½ΠΈΠ΅ΠΌ ΠΈΠ·ΠΎΡΠΈΠ°Π½Π°ΡΠ°, ΠΈΠΌΠ΅ΡΡΠ΅Π³ΠΎ Π΄Π²ΡΡ
ΡΠ΅ΠΆΠΈΠΌΠ½ΡΠΉ ΠΌΠ΅Ρ
Π°Π½ΠΈΠ·ΠΌ ΠΎΡΠ²Π΅ΡΠΆΠ΄Π΅Π½ΠΈΡ: ΠΈΡΠΏΠ°ΡΠ΅Π½ΠΈΠ΅ ΡΠ°ΡΡΠ²ΠΎΡΠΈΡΠ΅Π»Ρ ΠΈ Ρ
ΠΈΠΌΠΈΡΠ΅ΡΠΊΠ°Ρ ΡΠ΅Π°ΠΊΡΠΈΡ. ΠΠ°ΠΊ ΠΏΡΠ°Π²ΠΈΠ»ΠΎ, ΠΏΠΎΠ»ΠΈΡΡΠ΅ΡΠ°Π½Ρ ΠΏΡΠ΅Π΄Π½Π°Π·Π½Π°ΡΠ΅Π½Ρ Π΄Π»Ρ ΡΠΎΠ²ΠΌΠ΅ΡΡΠΈΠΌΡΡ
Ρ Π²Π΅ΡΡ
Π½ΠΈΠΌ ΠΏΠΎΠΊΡΡΡΠΈΠ΅ΠΌ (ΡΠΎ Π΅ΡΡΡ ΠΎΠ΄Π½ΠΎΠ³ΠΎ ΠΈ ΡΠΎΠ³ΠΎ ΠΆΠ΅ ΠΏΡΠΎΠΈΠ·Π²ΠΎΠ΄ΠΈΡΠ΅Π»Ρ) Π°ΠΌΠΈΠ½ΠΎ- ΠΈ ΠΏΠΎΠ»ΠΈΠ°ΠΌΠΈΠ΄Π½ΡΡ
ΡΠΏΠΎΠΊΡΠΈΠ΄Π½ΡΡ
ΡΠΌΠΎΠ» Π΄Π»Ρ Π·Π°ΡΠΈΡΡ ΠΎΡ ΠΏΡΡΠΌΠΎΠ³ΠΎ ΡΠΎΠ»Π½Π΅ΡΠ½ΠΎΠ³ΠΎ ΡΠ²Π΅ΡΠ° ΠΈΠ»ΠΈ Π£Π€-ΠΈΠ·Π»ΡΡΠ΅Π½ΠΈΡ ΠΈ Π΄Π»Ρ ΠΏΡΠΈΠ΄Π°Π½ΠΈΡ ΠΎΠΏΡΠ΅Π΄Π΅Π»Π΅Π½Π½ΡΡ
ΡΠ²Π΅ΡΠΎΠ². ΠΠΎΠ»ΠΈΡΡΠ΅ΡΠ°Π½Ρ ΠΏΡΠ΅Π΄Π½Π°Π·Π½Π°ΡΠ΅Π½Ρ Π΄Π»Ρ ΡΠΊΡΠΏΠ»ΡΠ°ΡΠ°ΡΠΈΠΈ Π² ΡΡΠ»ΠΎΠ²ΠΈΡΡ
Π°ΡΠΌΠΎΡΡΠ΅ΡΠ½ΠΎΠ³ΠΎ Π²ΠΎΠ·Π΄Π΅ΠΉΡΡΠ²ΠΈΡ ΠΈ ΡΠ°ΡΡΠΈΡΠ½ΠΎΠ³ΠΎ ΠΈΠ»ΠΈ ΠΏΠ΅ΡΠ΅ΠΌΠ΅Π½Π½ΠΎΠ³ΠΎ ΠΏΠΎΠ³ΡΡΠΆΠ΅Π½ΠΈΡ Π² Π²ΠΎΠ΄Ρ.
Π£ΡΠ΅ΡΠ°Π½ — Π£ΡΠ΅ΡΠ°Π½ΠΎΠ²ΡΠ΅ ΠΏΠΎΠΊΡΡΡΠΈΡ ΡΠΈΡΠΎΠΊΠΎ ΡΠ°Π·Π»ΠΈΡΠ°ΡΡΡΡ ΠΏΠΎ ΡΠΎΡΡΠ°Π²Ρ Π΄Π»Ρ ΠΊΠΎΠ½ΠΊΡΠ΅ΡΠ½ΡΡ ΡΡΠ»ΠΎΠ²ΠΈΠΉ ΡΠΊΡΠΏΠ»ΡΠ°ΡΠ°ΡΠΈΠΈ ΠΈ ΡΡΠ΅Π±ΠΎΠ²Π°Π½ΠΈΠΉ ΠΊ ΠΏΡΠΈΠΌΠ΅Π½Π΅Π½ΠΈΡ. ΠΠ½ΠΎΠ³ΠΎ ΡΠ°Π· ΠΎΠ΄Π½ΠΎΠΊΠΎΠΌΠΏΠΎΠ½Π΅Π½ΡΠ½ΡΠΉ; ΡΠΊΠ°Π·Π°Π½Ρ Π²Π»Π°Π³ΠΎΠΎΡΠ²Π΅ΡΠΆΠ΄Π°Π΅ΠΌΡΠ΅ ΡΡΠ΅ΡΠ°Π½Ρ. ΠΠ½ΠΈ ΠΎΡΠ²Π΅ΡΠΆΠ΄Π°ΡΡΡΡ ΠΎΡ Π²Π»Π°Π³ΠΈ Π² Π°ΡΠΌΠΎΡΡΠ΅ΡΠ΅ ΠΈ ΠΌΠΎΠ³ΡΡ Π½Π°Π½ΠΎΡΠΈΡΡΡΡ Π½Π° Π²Π»Π°ΠΆΠ½ΡΠ΅ ΠΏΠΎΠ²Π΅ΡΡ Π½ΠΎΡΡΠΈ, Π½Π° ΠΊΠΎΡΠΎΡΡΡ ΠΎΡΡΡΡΡΡΠ²ΡΠ΅Ρ ΡΠ²ΠΎΠ±ΠΎΠ΄Π½Π°Ρ Π²Π»Π°Π³Π°. ΠΡΠΈ ΡΡΠ΅ΡΠ°Π½Ρ ΡΠΎΠ΄Π΅ΡΠΆΠ°Ρ ΡΠ°Π·Π»ΠΈΡΠ½ΡΠ΅ ΠΏΠΈΠ³ΠΌΠ΅Π½ΡΡ ΠΈ ΠΏΡΠ΅Π΄ΡΡΠ°Π²Π»Π΅Π½Ρ Π² Π½Π΅ΡΠΊΠΎΠ»ΡΠΊΠΈΡ ΠΊΠΎΠΌΠ±ΠΈΠ½Π°ΡΠΈΡΡ Π² ΡΠΎΠΎΡΠ²Π΅ΡΡΡΠ²ΠΈΠΈ Ρ ΠΏΡΠ΅Π΄ΠΏΠΎΠ»Π°Π³Π°Π΅ΠΌΡΠΌΠΈ ΡΠΊΡΠΏΠ»ΡΠ°ΡΠ°ΡΠΈΠΎΠ½Π½ΡΠΌΠΈ ΡΡΠ»ΠΎΠ²ΠΈΡΠΌΠΈ. ΠΡΠΈ ΡΡΠ΅ΡΠ°Π½Ρ ΠΏΡΠ΅Π΄Π½Π°Π·Π½Π°ΡΠ΅Π½Ρ Π΄Π»Ρ Π°ΡΠΌΠΎΡΡΠ΅ΡΠ½ΠΎΠ³ΠΎ Π²ΠΎΠ·Π΄Π΅ΠΉΡΡΠ²ΠΈΡ, Π·Π°Ρ ΠΎΡΠΎΠ½Π΅Π½ΠΈΡ ΠΈ ΠΏΠΎΠ³ΡΡΠΆΠ΅Π½ΠΈΡ.
ΠΡΡΠ°ΡΠΈΠ΅ ΠΏΠΎΠΊΡΡΡΠΈΡ
ΠΠ°ΠΊ ΠΎΠ±ΡΡΠΆΠ΄Π°Π»ΠΎΡΡ ΡΠ°Π½Π΅Π΅, ΠΎΡΠ²Π΅ΡΠΆΠ΄Π΅Π½ΠΈΠ΅ Π½ΠΎΠ²ΠΎΠ³ΠΎ Π±Π΅ΡΠΎΠ½Π° ΡΠ°ΡΡΠΎ ΠΏΡΠΈΠ²ΠΎΠ΄ΠΈΡ ΠΊ Π²ΡΠ΄Π΅Π»Π΅Π½ΠΈΡ Π·Π½Π°ΡΠΈΡΠ΅Π»ΡΠ½ΠΎΠ³ΠΎ ΠΊΠΎΠ»ΠΈΡΠ΅ΡΡΠ²Π° Π²ΠΎΠ΄Ρ.
Π€ΡΠ½ΠΊΡΠΈΠΎΠ½Π°Π»ΡΠ½ΡΠ΅ ΡΡΠ΅Π±ΠΎΠ²Π°Π½ΠΈΡ
ΠΠΎΠΊΡΡΡΠΈΡ Π²ΡΠΏΠΎΠ»Π½ΡΡΡ Π΄Π²Π΅ ΠΎΡΠ½ΠΎΠ²Π½ΡΠ΅ ΡΡΠ½ΠΊΡΠΈΠΈ: ΠΎΠ±Π΅ΡΠΏΠ΅ΡΠΈΠ²Π°ΡΡ Π·Π°ΡΠΈΡΡ ΠΎΡ Π²ΡΠ΅Π΄Π½ΡΡ Π²Π΅ΡΠ΅ΡΡΠ², ΡΠ΅ΠΌ ΡΠ°ΠΌΡΠΌ ΡΠ²Π΅Π»ΠΈΡΠΈΠ²Π°Ρ Π΄ΠΎΠ»Π³ΠΎΠ²Π΅ΡΠ½ΠΎΡΡΡ, ΠΈ ΠΏΡΠΈΠ΄Π°ΡΡ ΠΊΠΎΠ½ΡΡΡΡΠΊΡΠΈΠΈ ΡΡΡΠ΅ΡΠΈΡΠ΅ΡΠΊΠΈΠΉ Π²ΠΈΠ΄.
- Π₯ΠΎΡΠΎΡΠ°Ρ Π°Π΄Π³Π΅Π·ΠΈΡ ΠΊ ΠΎΠΊΡΠ°ΡΠΈΠ²Π°Π΅ΠΌΠΎΠΉ ΠΏΠΎΠ²Π΅ΡΡ Π½ΠΎΡΡΠΈ
- Π£ΡΡΠΎΠΉΡΠΈΠ² ΠΊ ΡΠ΅Π»ΠΎΡΠ°ΠΌ, ΡΠ°ΠΊ ΠΊΠ°ΠΊ ΠΏΠΎΠΊΡΡΡΠΈΡ Π½Π°Π½ΠΎΡΡΡΡΡ Π½Π° ΡΠ΅Π»ΠΎΡΠ½ΠΎΠΉ Π±Π΅ΡΠΎΠ½
- Π£ΡΡΠΎΠΉΡΠΈΠ²ΠΎΡΡΡ ΠΊ CO2, ΡΡΠ»ΡΡΠ°ΡΠ°ΠΌ ΠΈ Ρ Π»ΠΎΡΠΈΠ΄Π°ΠΌ Π΄Π»Ρ ΠΎΠ±Π΅ΡΠΏΠ΅ΡΠ΅Π½ΠΈΡ Π±Π°ΡΡΠ΅ΡΠ½ΡΡ ΡΠ²ΠΎΠΉΡΡΠ²
- Π₯ΠΎΡΠΎΡΠ°Ρ Π³ΠΈΠ±ΠΊΠΎΡΡΡ, ΡΠ°ΠΊ ΠΊΠ°ΠΊ ΡΠ»Π΅ΠΌΠ΅Π½ΡΡ ΠΊΠΎΠ½ΡΡΡΡΠΊΡΠΈΠΈ ΠΏΠΎΠ΄Π²Π΅ΡΠΆΠ΅Π½Ρ ΠΈΠ·ΠΌΠ΅Π½Π΅Π½ΠΈΡ ΡΠ°Π·ΠΌΠ΅ΡΠΎΠ² ΠΈΠ·-Π·Π° ΡΠΈΠΊΠ»ΠΈΡΠ΅ΡΠΊΠΈΡ Π½Π°Π³ΡΡΠ·ΠΎΠΊ
- ΠΡΠ»ΠΈΡΠ½Π°Ρ ΡΡΡΠΎΠΉΡΠΈΠ²ΠΎΡΡΡ ΠΊ Π°ΡΠΌΠΎΡΡΠ΅ΡΠ½ΡΠΌ Π²ΠΎΠ·Π΄Π΅ΠΉΡΡΠ²ΠΈΡΠΌ
- ΠΠΎΠ·Π΄ΡΡ ΠΎΠΏΡΠΎΠ½ΠΈΡΠ°Π΅ΠΌΠΎΡΡΡ Π΄ΠΎΠ»ΠΆΠ½Π° ΠΏΠΎΠ·Π²ΠΎΠ»ΡΡΡ ΠΏΡΠΎΠ½ΠΈΠΊΠ½ΠΎΠ²Π΅Π½ΠΈΠ΅ Π²ΠΎΠ΄ΡΠ½ΠΎΠ³ΠΎ ΠΏΠ°ΡΠ° ΡΠ΅ΡΠ΅Π· ΠΏΠΎΠΊΡΡΡΠΈΠ΅ Π²ΠΎ ΠΈΠ·Π±Π΅ΠΆΠ°Π½ΠΈΠ΅ ΠΎΠ±ΡΠ°Π·ΠΎΠ²Π°Π½ΠΈΡ ΠΏΡΠ·ΡΡΠ΅ΠΉ Π½Π° ΠΏΠΎΠΊΡΡΡΠΈΠΈ; ΡΡΠ΅Π±ΠΎΠ²Π°Π½ΠΈΠ΅ Π΄ΠΎΠ»Π³ΠΎΠ²Π΅ΡΠ½ΠΎΡΡΠΈ.
- Π£ΡΡΠΎΠΉΡΠΈΠ²ΠΎΡΡΡ ΠΊ ΡΠ»ΡΡΡΠ°ΡΠΈΠΎΠ»Π΅ΡΠΎΠ²ΠΎΠΌΡ ΠΈΠ·Π»ΡΡΠ΅Π½ΠΈΡ ΡΠ²Π»ΡΠ΅ΡΡΡ ΡΡΠ΅Π±ΠΎΠ²Π°Π½ΠΈΠ΅ΠΌ Π΄ΠΎΠ»Π³ΠΎΠ²Π΅ΡΠ½ΠΎΡΡΠΈ
- ΠΠΈΠ·ΠΊΠ°Ρ Π²ΠΎΡΠΏΡΠΈΠΈΠΌΡΠΈΠ²ΠΎΡΡΡ ΠΊ ΠΎΠΊΡΠ°ΡΠΈΠ²Π°Π½ΠΈΡ
- Π₯ΠΎΡΠΎΡΠ°Ρ ΡΡΡΠΎΠΉΡΠΈΠ²ΠΎΡΡΡ ΠΊ ΡΠΎΡΡΡ Π³ΡΠΈΠ±ΠΊΠΎΠ², Π²ΠΎΠ΄ΠΎΡΠΎΡΠ»Π΅ΠΉ ΠΈ Ρ. Π΄.

ΠΠ°ΡΡΠ΅Ρ ΠΌΠΎΠΆΠ΅Ρ ΠΏΠΎΠ΄Π²Π΅ΡΠ³Π°ΡΡΡΡ ΠΏΠΎΡΡΠΎΡΠ½Π½ΠΎΠΌΡ Π²ΠΎΠ·Π΄Π΅ΠΉΡΡΠ²ΠΈΡ ΠΈΠ»ΠΈ ΠΏΡΠ΅ΡΡΠ²ΠΈΡΡΠΎΠΌΡ ΠΊΠΎΠ½ΡΠ°ΠΊΡΡ, Π²ΡΠ·Π²Π°Π½Π½ΠΎΠΌΡ Π±ΡΡΠ·Π³Π°ΠΌΠΈ, Π±ΡΡΠ·Π³Π°ΠΌΠΈ ΠΈΠ»ΠΈ ΡΠ»ΡΡΠ°ΠΉΠ½ΡΠΌ ΠΏΠΎΠΏΠ°Π΄Π°Π½ΠΈΠ΅ΠΌ Π°Π³ΡΠ΅ΡΡΠΈΠ²Π½ΡΡ
Π²Π΅ΡΠ΅ΡΡΠ². ΠΠ±ΡΡΠ½ΠΎ Ρ
ΠΈΠΌΠΈΡΠ΅ΡΠΊΠ°Ρ/ΡΠΈΠ·ΠΈΡΠ΅ΡΠΊΠ°Ρ Π΄Π΅Π³ΡΠ°Π΄Π°ΡΠΈΡ ΠΈ ΠΎΡΡΠ»ΠΎΠ΅Π½ΠΈΠ΅ ΠΏΠΎΠΊΡΡΡΠΈΠΉ ΡΠ²Π»ΡΡΡΡΡ ΠΎΡΠ½ΠΎΠ²Π½ΠΎΠΉ ΠΏΡΠΎΠ±Π»Π΅ΠΌΠΎΠΉ ΠΈΠ·Π½ΠΎΡΠ°, Π²Π΅Π΄ΡΡΠ΅ΠΉ ΠΊ ΠΈΡ
ΡΠ°ΡΡΡΠ΅ΡΠΊΠΈΠ²Π°Π½ΠΈΡ ΠΈ ΠΎΡΡΠ»ΠΎΠ΅Π½ΠΈΡ. ΠΠ° ΠΎΡΠ½ΠΎΠ²Π΅ ΠΏΡΠΎΡΠ΅ΡΡΠΎΠ² Π΄Π΅Π³ΡΠ°Π΄Π°ΡΠΈΠΈ ΠΌΠΎΠΆΠ½ΠΎ ΡΡΠΎΡΠΌΡΠ»ΠΈΡΠΎΠ²Π°ΡΡ ΠΎΡΠ½ΠΎΠ²Π½ΡΠ΅ ΡΡΠ΅Π±ΠΎΠ²Π°Π½ΠΈΡ ΠΊ Π·Π°ΡΠΈΡΠ½ΡΠΌ ΠΏΠΎΠΊΡΡΡΠΈΡΠΌ Π±Π΅ΡΠΎΠ½Π½ΡΡ
ΠΊΠΎΠ½ΡΡΡΡΠΊΡΠΈΠΉ Π² Π°Π³ΡΠ΅ΡΡΠΈΠ²Π½ΡΡ
ΡΡΠ΅Π΄Π°Ρ
. ΠΠ½ΠΈ ΡΠ»Π΅Π΄ΡΡΡΠΈΠ΅:
- Π‘ΡΠΎΠΉΠΊΠΎΡΡΡ ΠΊ Ρ ΠΈΠΌΠΈΡΠ΅ΡΠΊΠΈΠΌ/ΡΠΈΠ·ΠΈΡΠ΅ΡΠΊΠΈΠΌ Π²ΠΎΠ·Π΄Π΅ΠΉΡΡΠ²ΠΈΡΠΌ
- ΠΠΈΠ·ΠΊΠ°Ρ ΠΏΡΠΎΠ½ΠΈΡΠ°Π΅ΠΌΠΎΡΡΡ Π΄Π»Ρ Π²ΠΎΠ΄Ρ, ΡΠ°ΡΡΠ²ΠΎΡΠΎΠ² ΠΈ Π³Π°Π·ΠΎΠ²
- Π₯ΠΎΡΠΎΡΠ΅Π΅ ΡΡΠ΅ΠΏΠ»Π΅Π½ΠΈΠ΅ Ρ Π±Π΅ΡΠΎΠ½ΠΎΠΌ
- ΠΠΎΡΡΠ°ΡΠΎΡΠ½Π°Ρ Π³ΠΈΠ±ΠΊΠΎΡΡΡ, ΡΡΠΎΠ±Ρ ΠΈΠ·Π±Π΅ΠΆΠ°ΡΡ ΡΠ°ΡΡΡΠ΅ΡΠΊΠΈΠ²Π°Π½ΠΈΡ, Π²ΡΠ·Π²Π°Π½Π½ΠΎΠ³ΠΎ ΡΠ΅ΠΏΠ»ΠΎΠ²ΡΠΌΠΈ ΠΈΠ»ΠΈ ΠΌΠ΅Ρ Π°Π½ΠΈΡΠ΅ΡΠΊΠΈΠΌΠΈ Π΄Π²ΠΈΠΆΠ΅Π½ΠΈΡΠΌΠΈ
- Π‘Ρ ΠΎΠ΄Π½ΡΠ΅ ΡΠΈΠ·ΠΈΡΠ΅ΡΠΊΠΈΠ΅ ΡΠ²ΠΎΠΉΡΡΠ²Π° ΠΌΠ°ΡΠ΅ΡΠΈΠ°Π»Π° Π²Π΅ΡΡ Π½Π΅Π³ΠΎ ΡΠ»ΠΎΡ ΠΈ Π½ΠΈΠΆΠ΅Π»Π΅ΠΆΠ°ΡΠ΅Π³ΠΎ Π±Π΅ΡΠΎΠ½Π°
- ΠΠΎΡΡΠ°ΡΠΎΡΠ½Π°Ρ ΡΡΠΎΠΉΠΊΠΎΡΡΡ ΠΊ ΠΈΡΡΠΈΡΠ°Π½ΠΈΡ ΠΈΠ»ΠΈ ΡΠΊΠΎΠ»ΡΠΆΠ΅Π½ΠΈΡ.
- Π‘ΡΠΎΠΉΠΊΠΎΡΡΡ Π±Π΅ΡΠΎΠ½Π° ΠΊ Ρ ΠΈΠΌΠΈΡΠ΅ΡΠΊΠΎΠΌΡ Π²ΠΎΠ·Π΄Π΅ΠΉΡΡΠ²ΠΈΡ ΠΈ Π²Π»Π°ΠΆΠ½ΠΎΡΡΠΈ Π² Π±Π΅ΡΠΎΠ½Π΅.
- ΠΠ°Π΄Π΅Π»ΠΊΠ° ΠΌΠ΅Π»ΠΊΠΈΡ ΡΡΠ΅ΡΠΈΠ½ Π² Π±Π΅ΡΠΎΠ½Π΅
ΠΡΠΈΠ½ΡΠΈΠΏΡ Π·Π°ΡΠΈΡΠ½ΡΡ ΠΏΠΎΠΊΡΡΡΠΈΠΉ (Π΄ΠΈΠ·Π°ΠΉΠ½)
Π Π°Π·ΡΠ°Π±ΠΎΡΠΊΠ° ΠΏΠΎΠ΄Ρ ΠΎΠ΄ΡΡΠ΅ΠΉ ΡΠΈΡΡΠ΅ΠΌΡ Π·Π°ΡΠΈΡΡ Π΄Π»Ρ Π½ΠΎΠ²ΡΡ ΠΈΠ»ΠΈ ΡΡΡΠ΅ΡΡΠ²ΡΡΡΠΈΡ ΠΊΠΎΠ½ΡΡΡΡΠΊΡΠΈΠΉ ΠΏΡΠ΅Π΄ΡΡΠ°Π²Π»ΡΠ΅Ρ ΡΠΎΠ±ΠΎΠΉ ΡΠ»ΠΎΠΆΠ½ΡΠΉ ΠΏΡΠΎΡΠ΅ΡΡ, Π²ΠΊΠ»ΡΡΠ°ΡΡΠΈΠΉ:- ΠΠ΄Π΅Π½ΡΠΈΡΠΈΠΊΠ°ΡΠΈΡ ΡΡΠ΅Π΄Ρ ΠΎΠ±ΡΠ»ΡΠΆΠΈΠ²Π°Π½ΠΈΡ ΠΊΠΎΠ½ΠΊΡΠ΅ΡΠ½ΠΎΠΉ ΠΊΠΎΠ½ΡΡΡΡΠΊΡΠΈΠΈ Π² ΠΈΡΡ ΠΎΠ΄Π½ΠΎΠΌ ΠΏΡΠΎΠ΅ΠΊΡΠ΅
- ΠΠ΄Π΅Π½ΡΠΈΡΠΈΠΊΠ°ΡΠΈΡ ΠΈ ΠΎΡΠ΅Π½ΠΊΠ° ΡΠΎΡΡΠΎΡΠ½ΠΈΡ ΠΈ ΠΈΠ·Π½ΠΎΡΠ° (Π΅ΡΠ»ΠΈ Π΅ΡΡΡ) ΡΡΡΠ΅ΡΡΠ²ΡΡΡΠ΅ΠΉ ΠΊΠΎΠ½ΡΡΡΡΠΊΡΠΈΠΈ
- ΠΡΠ±ΠΎΡ ΡΠΎΠΎΡΠ²Π΅ΡΡΡΠ²ΡΡΡΠ΅ΠΉ ΡΠΈΡΡΠ΅ΠΌΡ Π·Π°ΡΠΈΡΡ
- ΠΠΏΡΠ΅Π΄Π΅Π»Π΅Π½ΠΈΠ΅ ΠΏΠ°ΡΠ°ΠΌΠ΅ΡΡΠΎΠ² ΠΏΠΎΠΊΡΡΡΠΈΡ: ΡΠΈΠΏ ΡΠ²ΡΠ·ΡΡΡΠ΅Π³ΠΎ, ΡΠ΅ΡΠ΅ΠΏΡΡΡΠ°, ΡΠΎΠ»ΡΠΈΠ½Π° ΠΏΠΎΠΊΡΡΡΠΈΡ
- ΠΠΆΠΈΠ΄Π°Π΅ΠΌΠΎΠ΅ Π²ΡΠ΅ΠΌΡ ΠΌΠ΅ΠΆΠ΄Ρ ΠΏΠ΅ΡΠΈΠΎΠ΄ΠΈΡΠ΅ΡΠΊΠΈΠΌΠΈ ΠΏΠΎΠ²ΡΠΎΡΠ½ΡΠΌΠΈ ΠΏΠΎΠΊΡΡΡΠΈΡΠΌΠΈ.
g(t) = R(t) β S(t) = R0 R (t)ΞΈR β S(t)ΞΈS β₯ 0, g(t) = tΞΈt β td β₯ 0, Π΄Π»Ρ Π²ΡΠ΅Ρ 0 < t β€ td
ΠΠ΄Π΅
g(t) β Π·Π°ΠΏΠ°Ρ ΠΏΡΠΎΡΠ½ΠΎΡΡΠΈ, Π³Π΄Π΅
g(t) > 0 ΠΎΠ·Π½Π°ΡΠ°Π΅Ρ Π±Π΅Π·ΠΎΠΏΠ°ΡΠ½ΠΎΡΡΡ, Π°
g(t) β€ 0 β ΠΎΡΠΊΠ°Π·;
R0 β Π·Π°ΡΠΈΡΠ½Π°Ρ Π±Π°ΡΡΠ΅ΡΠ½Π°Ρ ΡΠΏΠΎΡΠΎΠ±Π½ΠΎΡΡΡ Π² Π½Π΅ΡΠ°Π·ΡΡΡΠ΅Π½Π½ΠΎΠΌ (ΠΈΡΡ
ΠΎΠ΄Π½ΠΎΠΌ) ΡΠΎΡΡΠΎΡΠ½ΠΈΠΈ;
R(t) β ΡΡΠ½ΠΊΡΠΈΡ Π΄Π΅Π³ΡΠ°Π΄Π°ΡΠΈΠΈ;
ΞΈ β Π½Π΅ΠΎΠΏΡΠ΅Π΄Π΅Π»Π΅Π½Π½ΠΎΡΡΡ ΡΠ°ΡΡΠ΅ΡΠ½ΡΡ
ΠΌΠΎΠ΄Π΅Π»Π΅ΠΉ ΠΈ ΠΏΠΎΠ³ΡΠ΅ΡΠ½ΠΎΡΡΠΈ Π½Π°Π±Π»ΡΠ΄Π΅Π½ΠΈΡ ΠΈ ΡΠ΅Π³ΠΈΡΡΡΠ°ΡΠΈΠΈ Π΄Π°Π½Π½ΡΡ
;
t β Π²ΡΠ΅ΠΌΡ ΠΎΡΠ΅Π½ΠΊΠΈ;
ΡΠ΄ β ΡΠ°ΡΡΠ΅ΡΠ½ΡΠΉ ΠΈΠ»ΠΈ ΡΠ°ΡΡΠ΅ΡΠ½ΡΠΉ ΡΡΠΎΠΊ ΡΠ»ΡΠΆΠ±Ρ.
ΠΠΎΡΠ»Π΅ ΡΠ°Π·ΡΠ°Π±ΠΎΡΠΊΠΈ ΡΡΠ½ΠΊΡΠΈΠΉ ΠΏΡΠ΅Π΄Π΅Π»ΡΠ½ΠΎΠ³ΠΎ ΡΠΎΡΡΠΎΡΠ½ΠΈΡ ΠΌΠΎΠΆΠ½ΠΎ ΠΎΡΠ΅Π½ΠΈΡΡ Π½Π°Π΄Π΅ΠΆΠ½ΠΎΡΡΡ ΠΏΠΎΠΊΡΡΡΠΈΡ. ΠΡΠΎΠ²Π΅ΡΠΊΠ° Π½Π°Π΄Π΅ΠΆΠ½ΠΎΡΡΠΈ ΠΏΠΎΠΊΡΡΡΠΈΡ ΠΏΠΎ ΠΎΡΠ½ΠΎΡΠ΅Π½ΠΈΡ ΠΊ Π΄Π°Π½Π½ΠΎΠΌΡ Π²ΠΈΠ΄Ρ ΡΠ°Π·ΡΡΡΠ΅Π½ΠΈΡ Π² Π·Π°Π΄Π°Π½Π½ΡΠΉ ΠΏΠ΅ΡΠΈΠΎΠ΄ Π²ΡΠ΅ΠΌΠ΅Π½ΠΈ ΠΌΠΎΠΆΠ΅Ρ Π±ΡΡΡ ΠΎΠΏΡΠ΅Π΄Π΅Π»Π΅Π½Π° ΠΊΠ°ΠΊ:
P{t} = P{g(t) β₯ 0} = P{R0, R (t)
ΞΈR β₯ S(t)ΞΈS} β₯ Pt arg, Π΄Π»Ρ Π²ΡΠ΅Ρ 0 < t β€ td, (29)
ΠΠ΄Π΅, Pt arg β ΠΏΡΠΈΠ΅ΠΌΠ»Π΅ΠΌΡΠΉ ΡΡΠΎΠ²Π΅Π½Ρ Π½Π°Π΄Π΅ΠΆΠ½ΠΎΡΡΠΈ ΠΊΠΎΠ½ΡΡΡΡΠΊΡΠΈΠΈ. Π‘ΡΠΎΠΊ ΡΠ»ΡΠΆΠ±Ρ ΠΏΠΎΠΊΡΡΡΠΈΡ ΠΎΠΏΡΠ΅Π΄Π΅Π»ΡΠ΅ΡΡΡ ΠΏΡΠΈ ΡΠ½ΠΈΠΆΠ΅Π½ΠΈΠΈ Π½Π°Π΄Π΅ΠΆΠ½ΠΎΡΡΠΈ Π½ΠΈΠΆΠ΅ Π΄ΠΎΠΏΡΡΡΠΈΠΌΠΎΠ³ΠΎ ΡΡΠΎΠ²Π½Ρ. Π Π°Π·Π½ΡΠ΅ ΡΠΌΠΎΠ»Ρ ΠΏΠΎ-ΡΠ°Π·Π½ΠΎΠΌΡ ΡΠ΅Π°Π³ΠΈΡΡΡΡ Π½Π° Π²ΠΎΠ·Π΄Π΅ΠΉΡΡΠ²ΠΈΠ΅ Π°Π³ΡΠ΅ΡΡΠΈΠ²Π½ΡΡ ΡΡΠ΅Π΄. ΠΠ°Π²ΠΈΡΠΈΠΌΠ°Ρ ΠΎΡ Π²ΡΠ΅ΠΌΠ΅Π½ΠΈ ΠΌΠΎΠ½ΠΎΡΠΎΠ½Π½ΠΎ ΡΠ±ΡΠ²Π°ΡΡΠ°Ρ ΡΡΠ½ΠΊΡΠΈΡ Π΄Π΅Π³ΡΠ°Π΄Π°ΡΠΈΠΈ R(t) ΠΌΠΎΠΆΠ΅Ρ Π±ΡΡΡ Π²ΡΡΠ°ΠΆΠ΅Π½Π° Π² ΡΠ°Π·Π»ΠΈΡΠ½ΡΡ ΡΠΎΡΠΌΠ°Ρ (Π»ΠΈΠ½Π΅ΠΉΠ½ΠΎΠΉ, ΠΏΠ°ΡΠ°Π±ΠΎΠ»ΠΈΡΠ΅ΡΠΊΠΎΠΉ, ΠΊΠ²Π°Π΄ΡΠ°ΡΠΈΡΠ½ΠΎΠΉ ΠΈ Ρ. Π΄.) ΡΠΎ ΡΠ»Π΅Π΄ΡΡΡΠΈΠΌΠΈ Π³ΡΠ°Π½ΠΈΡΠ½ΡΠΌΠΈ ΡΡΠ»ΠΎΠ²ΠΈΡΠΌΠΈ.
ΠΏΡΠΈ t = t0, R(t0) = 1,0, ΠΏΡΠΈ t = td, R(td) = ΠΌΠΈΠ½.
ΠΠΎΠ½ΡΡΡΡΠΊΡΠΈΡ ΠΏΠΎΠ»ΠΈΠΌΠ΅ΡΠ½ΡΡ ΠΏΠΎΠΊΡΡΡΠΈΠΉ ΡΡΠ΅Π±ΡΠ΅Ρ ΠΏΡΠΎΠ²Π΅ΡΠΊΠΈ ΠΈΡ Ρ Π°ΡΠ°ΠΊΡΠ΅ΡΠΈΡΡΠΈΠΊ Π² ΡΠ΅Π»ΠΎΠΌ Ρ ΠΈΡΠΏΠΎΠ»ΡΠ·ΠΎΠ²Π°Π½ΠΈΠ΅ΠΌ ΡΠ»Π΅Π΄ΡΡΡΠΈΡ ΡΠ΅ΡΡΡΠ΅Ρ ΡΡΠ»ΠΎΠ²ΠΈΠΉ:
- Π£ΡΠ»ΠΎΠ²ΠΈΠ΅, ΠΎΠΏΡΠ΅Π΄Π΅Π»ΡΡΡΠ΅Π΅ Ρ
ΠΈΠΌΠΈΡΠ΅ΡΠΊΡΡ/ΡΠΈΠ·ΠΈΡΠ΅ΡΠΊΡΡ ΡΡΠΎΠΉΠΊΠΎΡΡΡ Ρ R(t)
= R0ΟR(c0;t) ΠΈ S(t) = Rmin, Π³Π΄Π΅ R0 ΠΈ Rmin β Π½Π°ΡΠ°Π»ΡΠ½ΠΎΠ΅ ΠΈ ΠΌΠΈΠ½ΠΈΠΌΠ°Π»ΡΠ½ΠΎ Π΄ΠΎΠΏΡΡΡΠΈΠΌΠΎΠ΅ ΡΠΎΠΏΡΠΎΡΠΈΠ²Π»Π΅Π½ΠΈΠ΅ ΠΏΠΎΠΊΡΡΡΠΈΡ ΡΠΎΠΎΡΠ²Π΅ΡΡΡΠ²Π΅Π½Π½ΠΎ; ΟR(c0, t) β ΡΡΠ½ΠΊΡΠΈΡ Π΄Π΅Π³ΡΠ°Π΄Π°ΡΠΈΠΈ ΠΏΠΎΠΊΡΡΡΠΈΡ ΠΏΡΠΈ Π·Π°Π΄Π°Π½Π½ΠΎΠΌ Π²ΠΎΠ·Π΄Π΅ΠΉΡΡΠ²ΠΈΠΈ c0 ΡΠ΅ΡΠ΅Π· Π²ΡΠ΅ΠΌΡ t; - Π£ΡΠ»ΠΎΠ²ΠΈΠ΅, ΠΎΠΏΡΠ΅Π΄Π΅Π»ΡΡΡΠ΅Π΅ ΠΏΡΠΎΠ½ΠΈΠΊΠ°ΡΡΡΡ ΡΠΏΠΎΡΠΎΠ±Π½ΠΎΡΡΡ ΠΏΠΎΠΊΡΡΡΠΈΡ ΠΏΡΠΈ R(t) = cΠΊΡ ΠΈ S(t) = c(dpc,t), Π³Π΄Π΅ cΠΊΡ ΠΈ c(dpc;t) β ΠΊΡΠΈΡΠΈΡΠ΅ΡΠΊΠ°Ρ ΠΈ ΠΎΠΆΠΈΠ΄Π°Π΅ΠΌΠ°Ρ ΠΊΠΎΠ½ΡΠ΅Π½ΡΡΠ°ΡΠΈΡ Π°Π³ΡΠ΅ΡΡΠΈΠ²Π½ΡΡ Π²Π΅ΡΠ΅ΡΡΠ² ΡΠΎΠΎΡΠ²Π΅ΡΡΡΠ²Π΅Π½Π½ΠΎ Π°ΠΊΡΠΈΠ²Π½ΠΎ, Π½Π° ΠΏΠΎΠ²Π΅ΡΡ Π½ΠΎΡΡΠΈ Π±Π΅ΡΠΎΠ½Π°;
- Π£ΡΠ»ΠΎΠ²ΠΈΠ΅, ΠΎΠΏΡΠ΅Π΄Π΅Π»ΡΡΡΠ΅Π΅ ΡΠ°ΡΡΡΠ΅ΡΠΊΠΈΠ²Π°Π½ΠΈΠ΅ ΠΏΠΎΠΊΡΡΡΠΈΡ ΠΏΡΠΈ R(t) = fpt(t) [Ξ΅pt(t)] ΠΈ S(t) = Οmax (Ξ΅max), Π³Π΄Π΅ fpt(t) [Ξ΅pt(t)] β ΠΏΡΠ΅Π΄Π΅Π» ΠΏΡΠΎΡΠ½ΠΎΡΡΠΈ ΠΏΡΠΈ ΡΠ°ΡΡΡΠΆΠ΅Π½ΠΈΠΈ (Π΄Π΅ΡΠΎΡΠΌΠ°ΡΠΈΡ) ΡΠΌΠΎΠ»Ρ ΠΈ Οmax (Ξ΅max) β ΠΌΠ°ΠΊΡΠΈΠΌΠ°Π»ΡΠ½ΠΎΠ΅ Π½Π°ΠΏΡΡΠΆΠ΅Π½ΠΈΠ΅ (Π΄Π΅ΡΠΎΡΠΌΠ°ΡΠΈΡ) Π² ΠΏΠΎΠΊΡΡΡΠΈΠΈ;
- Π£ΡΠ»ΠΎΠ²ΠΈΠ΅, ΠΎΠΏΡΠ΅Π΄Π΅Π»ΡΡΡΠ΅Π΅ ΠΎΡΡΠ»ΠΎΠ΅Π½ΠΈΠ΅ (ΠΎΡΡΠ»ΠΎΠ΅Π½ΠΈΠ΅) ΠΏΠΎΠΊΡΡΡΠΈΡ ΠΏΡΠΈ R(t) = Οcon [KIc(t)] ΠΈ S(t) = Οmax [KIcor(t)] ΠΈΠ»ΠΈ R(t) = Dcr ΠΈ S(t) = D(t), Π³Π΄Π΅ KIc(t) ΠΈ KIcor(t) β ΠΊΡΠΈΡΠΈΡΠ΅ΡΠΊΠΈΠ΅ ΠΊΠΎΡΡΡΠΈΡΠΈΠ΅Π½ΡΡ ΠΈΠ½ΡΠ΅Π½ΡΠΈΠ²Π½ΠΎΡΡΠΈ ΠΈΡΡ
ΠΎΠ΄Π½ΠΎΠ³ΠΎ ΠΈ ΠΏΠΎΡΠ»Π΅ Π²ΠΎΠ·Π΄Π΅ΠΉΡΡΠ²ΠΈΡ Π°Π³ΡΠ΅ΡΡΠΈΠ²Π½ΡΡ
ΡΡΠ΅Π΄ ΡΠΎΠΎΡΠ²Π΅ΡΡΡΠ²Π΅Π½Π½ΠΎ; Dcr ΠΈ D(t) β ΠΊΡΠΈΡΠΈΡΠ΅ΡΠΊΠ°Ρ ΠΈ ΠΎΠΆΠΈΠ΄Π°Π΅ΠΌΠ°Ρ ΡΡΠ΅ΠΏΠ΅Π½Ρ (ΠΏΠ»ΠΎΡΠ°Π΄Ρ ΠΈΠ»ΠΈ %) ΡΠ°ΡΡΠ»ΠΎΠ΅Π½ΠΈΡ ΡΠΎΠΎΡΠ²Π΅ΡΡΡΠ²Π΅Π½Π½ΠΎ.
ΠΠ°ΠΊΠ»ΡΡΠΈΡΠ΅Π»ΡΠ½ΡΠ΅ Π·Π°ΠΌΠ΅ΡΠ°Π½ΠΈΡ
- ΠΠ΅ΡΠΎΠ½ ΠΏΡΠ΅Π΄ΡΡΠ°Π²Π»ΡΠ΅Ρ ΡΠΎΠ±ΠΎΠΉ ΠΏΠΎΡΠΈΡΡΡΠΉ ΠΌΠ°ΡΠ΅ΡΠΈΠ°Π» Ρ Π²ΡΡΠΎΠΊΠΎΠΉ Π³Π°Π·ΠΎ-, ΠΏΠ°ΡΠΎ- ΠΈ ΠΆΠΈΠ΄ΠΊΠΎΡΡΠ½ΠΎΠΉ ΠΏΡΠΎΠ½ΠΈΡΠ°Π΅ΠΌΠΎΡΡΡΡ, ΠΏΡΠΈΠ²ΠΎΠ΄ΡΡΠΈΠΉ ΠΊ ΠΈΠ·Π½ΠΎΡΡ ΠΆΠ΅Π»Π΅Π·ΠΎΠ±Π΅ΡΠΎΠ½Π½ΡΡ ΠΊΠΎΠ½ΡΡΡΡΠΊΡΠΈΠΉ. ΠΠ΄Π½ΠΈΠΌ ΠΈΠ· ΡΠΏΠΎΡΠΎΠ±ΠΎΠ² Π·Π°ΡΠΈΡΡ ΠΆΠ΅Π»Π΅Π·ΠΎΠ±Π΅ΡΠΎΠ½Π½ΡΡ ΠΊΠΎΠ½ΡΡΡΡΠΊΡΠΈΠΉ ΠΎΡ ΠΊΠΎΡΡΠΎΠ·ΠΈΠΈ ΡΠ²Π»ΡΠ΅ΡΡΡ ΠΈΡΠΏΠΎΠ»ΡΠ·ΠΎΠ²Π°Π½ΠΈΠ΅ Π·Π°ΡΠΈΡΠ½ΡΡ ΠΏΠΎΠΊΡΡΡΠΈΠΉ. Π§Π°ΡΡΠΎ ΠΏΠΎΠΊΡΡΡΠΈΠ΅ ΡΠ²Π»ΡΠ΅ΡΡΡ ΠΎΡΠ½ΠΎΠ²Π½ΡΠΌ ΡΡΠ΅Π΄ΡΡΠ²ΠΎΠΌ Π·Π°ΡΠΈΡΡ Π±Π΅ΡΠΎΠ½Π½ΡΡ ΠΊΠΎΠ½ΡΡΡΡΠΊΡΠΈΠΉ Π² ΠΏΡΠΎΡΠ΅ΡΡΠ΅ ΡΠΊΡΠΏΠ»ΡΠ°ΡΠ°ΡΠΈΠΈ. ΠΠ½ΠΎΠ³ΠΈΠ΅ Π»Π°ΠΊΠΎΠΊΡΠ°ΡΠΎΡΠ½ΡΠ΅ ΠΌΠ°ΡΠ΅ΡΠΈΠ°Π»Ρ Π½Π΅ ΠΎΠ±Π»Π°Π΄Π°ΡΡ Π°Π±ΡΠΎΠ»ΡΡΠ½ΠΎΠΉ ΡΡΠΎΠΉΠΊΠΎΡΡΡΡ ΠΈ Π½Π΅ΠΏΡΠΎΠ½ΠΈΡΠ°Π΅ΠΌΠΎΡΡΡΡ Π΄Π»Ρ Π²ΡΠ΅Ρ Π°Π³ΡΠ΅ΡΡΠΈΠ²Π½ΡΡ ΡΡΠ΅Π΄. ΠΠ΅ΠΎΠ±Ρ ΠΎΠ΄ΠΈΠΌΠΎ Ρ ΠΎΡΠΎΡΠΎ ΠΏΠΎΠ½ΠΈΠΌΠ°ΡΡ ΠΌΠ΅Ρ Π°Π½ΠΈΠ·ΠΌ Π΄Π΅Π³ΡΠ°Π΄Π°ΡΠΈΠΈ ΠΌΠ°ΡΠ΅ΡΠΈΠ°Π»ΠΎΠ² ΠΏΠΎΠΊΡΡΡΠΈΠΉ, ΡΡΠΎΠ±Ρ ΠΈΠΌΠ΅ΡΡ Π²ΠΎΠ·ΠΌΠΎΠΆΠ½ΠΎΡΡΡ ΡΠΎΠ·Π΄Π°Π²Π°ΡΡ ΠΏΠΎΠΊΡΡΡΠΈΡ Ρ ΡΡΠ΅Π±ΡΠ΅ΠΌΡΠΌΠΈ Π±Π°ΡΡΠ΅ΡΠ½ΡΠΌΠΈ ΡΠ²ΠΎΠΉΡΡΠ²Π°ΠΌΠΈ.
- ΠΠ΅ΡΡΡΡΠΊΡΠΈΡ ΠΏΠΎΠ»ΠΈΠΌΠ΅ΡΠΎΠ² ΠΏΡΠ΅Π΄ΡΡΠ°Π²Π»ΡΠ΅Ρ ΡΠΎΠ±ΠΎΠΉ ΡΠ»ΠΎΠΆΠ½ΠΎΠ΅ Π²Π·Π°ΠΈΠΌΠΎΠ΄Π΅ΠΉΡΡΠ²ΠΈΠ΅ ΡΠΈΠ·ΠΈΡΠ΅ΡΠΊΠΈΡ ΠΈ Ρ ΠΈΠΌΠΈΡΠ΅ΡΠΊΠΈΡ ΠΏΡΠΎΡΠ΅ΡΡΠΎΠ², ΠΏΡΠΈΠ²ΠΎΠ΄ΡΡΠ΅Π΅ ΠΊ Π½Π°ΡΡΡΠ΅Π½ΠΈΡ Π΅Π³ΠΎ Ρ ΠΈΠΌΠΈΡΠ΅ΡΠΊΠΎΠΉ ΡΡΡΡΠΊΡΡΡΡ, Π° ΡΠ°ΠΊΠΆΠ΅ ΠΊ ΡΠ°ΡΡΡΠ΅ΡΠΊΠΈΠ²Π°Π½ΠΈΡ ΠΈ ΠΎΡΡΠ»ΠΎΠ΅Π½ΠΈΡ Π·Π°ΡΠΈΡΠ½ΡΡ ΠΏΠΎΠΊΡΡΡΠΈΠΉ. ΠΠ»Π°ΡΡΠΈΡΠΈΠΊΠ°ΡΠΈΡ Π΄Π΅Π³ΡΠ°Π΄Π°ΡΠΈΠΈ ΠΏΠΎΠΊΡΡΡΠΈΡ Π±ΡΠ»Π° ΡΠ΄Π΅Π»Π°Π½Π° Π½Π° ΠΎΡΠ½ΠΎΠ²Π΅ Ρ Π°ΡΠ°ΠΊΡΠ΅ΡΠ° Π΄Π΅ΠΉΡΡΠ²ΠΈΡ.
- ΠΠ΅Ρ
Π°Π½ΠΈΠ·ΠΌΡ Π΄Π΅Π³ΡΠ°Π΄Π°ΡΠΈΠΈ ΠΏΠΎΠΊΡΡΡΠΈΠΉ, Π²ΡΠ·Π²Π°Π½Π½ΡΠ΅ Π°Π³ΡΠ΅ΡΡΠΈΠ²Π½ΡΠΌΠΈ Π²ΠΎΠ·Π΄Π΅ΠΉΡΡΠ²ΠΈΡΠΌΠΈ, Ρ
ΠΎΡΠΎΡΠΎ ΠΈΠ·ΡΡΠ΅Π½Ρ, ΠΈ Π±ΡΠ»ΠΈ ΡΠ°Π·ΡΠ°Π±ΠΎΡΠ°Π½Ρ ΠΏΡΠΎΠ³Π½ΠΎΡΡΠΈΡΠ΅ΡΠΊΠΈΠ΅ ΠΌΠΎΠ΄Π΅Π»ΠΈ ΠΈΠ·Π½ΠΎΡΠ° Ρ ΡΠ΅ΡΠ΅Π½ΠΈΠ΅ΠΌ Π²ΡΠ΅ΠΌΠ΅Π½ΠΈ, ΠΊΠΎΡΠΎΡΡΠ΅ ΠΌΠΎΠΆΠ½ΠΎ ΠΏΡΠΈΠΌΠ΅Π½ΡΡΡ Π΄Π»Ρ ΠΏΡΠΎΠ΅ΠΊΡΠΈΡΠΎΠ²Π°Π½ΠΈΡ ΠΏΠΎΠ²Π΅ΡΡ
Π½ΠΎΡΡΠ½ΡΡ
ΠΏΠΎΠ»ΠΈΠΌΠ΅ΡΠ½ΡΡ
ΠΏΠΎΠΊΡΡΡΠΈΠΉ Π΄Π»Ρ Π·Π°ΡΠΈΡΡ Π±Π΅ΡΠΎΠ½Π½ΡΡ
ΠΊΠΎΠ½ΡΡΡΡΠΊΡΠΈΠΉ ΠΎΡ ΠΈΠ·Π½ΠΎΡΠ°.