подробные размеры, фото и описание изготовления
Самодельная ленточная пила сделанная своими руками: подробные размеры, фото и описание изготовления станка.
Приветствую любителей самоделок! Хочу показать интересную конструкцию самодельного станка для домашней мастерской. Конечно готовый станок доступный в продаже, но зуд творчества ничем не унять — делать своими руками это и интереснее и приятнее.
Итак, перед Вами, подробный фото отчёт как сделать ленточную пилу своими руками.
На фото показа размеры заготовок для изготовления станка.
Первым делом собирается станина, это несущий элемент, на котором все остальное – навесное. Из заготовок, напиленных на пиле, выклеивается и стягивается шурупами «П» образная деталь. Склейка делается в перехлест, как бы кирпичная кладка
Доведя шлифовкой поверхность станины, в верхней части выпиливается техническое отверстие, для натяжки пильной ленты. Высверливается отверстие под резьбу. А так же в нижней части, при помощи дрели и фрезера, изготавливается посадка под подшипники вала, на котором крепятся колесо и шкив.
Повторяя вышеперечисленные операции, изготавливается натяжная бабка верхнего узла.
Высверливаются отверстия под крепеж и резьбу натяжки. В крепежное отверстие вставляется резьбовое соединение, я в посадочные отверстия подшипники.
Верхняя бабка вставляется в шахту, укрепляется металлическими пластинами. Регулировка высота осуществляется резьбой-шатуном, которая вращаясь, или подымает, или опускает натяжное колесо.
Колеса под ленточную пилу, делаются фрезером, как циркулем. В них закрепляется подготовленная шпилька под шпонки. В нижнюю часть станины устанавливается электромотор, вал, шкив и колесо.
Начнем собирать. Установили валы с пильными колесами, одели ленточную пилу, она варится по размерам, там где и точится, проверили запустив аппарат. Пила при вращении смещения не имеет. Изготовив опорные направляющие для пилы и регулировку высоты, устанавливает их на свои места.
При помощи простого приспособления протачиваем диски и центруем, чтобы убирать биение при вращении. Из камер детского велосипеда делаем обрезиненную кромку. Это не даст пробуксовки пилы.
Направляющие для ленточной пилы.
И конечно устанавливаем защиту, пилы и соскакивают, и рвутся.
Стол, ставится на место через пропил. Для запуска врезан обыкновенный выключатель на 220 вольт.
С помощью такой ленточной пилы, можно быстро и точно вырезать различные заготовки из древесины.
В этом видео можно посмотреть ленточную пилу в работе:
Ленточная пила своими руками для работы по дереву (фото) | Своими руками
Содержание ✓
- ✓ Основные характеристики моей самодельной ленточной пилы
- ✓
Конструкция ленточной пилы.
Большая часть деталей — из дерева.
- ✓ Изготавливаем раму ленточной пилы
- ✓ Блок крепления верхнего колеса
- ✓ Изготовление колёс пилы
- ✓ Крепление колёс на раму ленточной пилы
- ✓ Настройка направляющих пильного полотна
- ✓ Изготовление рабочего стола для ленточной пилы своими руками
- ✓ Изготовление тумбы для пилы
- ✓ Электропроводка
- ✓ Параллельный упор
- ✓ Ленточная пила по дереву своими руками- все фото
При подборе оборудования для домашней мастерской ленточную пилу редко включают в разряд первоочередного инструмента: большинство операций можно выполнить и без неё. Я долгое время обходился тем, что у меня было, но в результате созрел для изготовления ленточной пилы. В результате поисков я наткнулся на сайт канадского изобретателя Маттиаса Вандела. Он предлагал сделать ленточную пилу практически полностью из дерева. При этом характеристики её были очень приличными, а любую запчасть потом несложно сделать самому.
Основные характеристики моей самодельной ленточной пилы
Моя пила отличается от той, что была в чертежах разработчика, но я и не стремился повторить проект один в один. Многое зависит от выбранного двигателя, пильных лент и заготовок. Я использовал те полотна, что смог найти. Асинхронный электродвигатель подходящей мощности тоже завалялся в закромах. Пильные полотна оказались чуть короче рекомендованных — я решил не рисковать и уменьшил внутренний размер рамы на 10 мм.
Конструкция ленточной пилы. Большая часть деталей — из дерева.
Характеристика | Моя пила | Пила автора |
Высота (без тумбы), мм | 1 200 | 1220 |
Ширина (со столом), мм | 900 | 720 |
Глубина (со столом), мм | 500 | 460 |
Диаметр колеса | 16м (400 мм) | |
Стол (ширина х глубина), мм | 510 х 470 | 490 х 460 |
Наклон стола, градусы | 0-45 | |
Масса (без тумбы), кг | 50 | 45 |
Максимальная толщина заготовки, мм | 260 | 270 |
Отступ полотна от рамы, мм | 400 | 394 |
Длина полотна, мм | 2 667 | 2 700 |
Ширина полотна, мм | 6-16 | 4-18 |
Изготавливаем раму ленточной пилы
Это основной элемент станка. Я использовал сосновую дюймовку, простроганную на рейсмусе до толщины 19 мм. Рама склеена из нескольких слоёв досок с перехлёстом. Нельзя использовать для рамы ДСП, МДФ, фанеру или мебельный щит. Рама имеет С-образную форму, где сверху монтируется основа для направляющей механизма натяжения с верхним колесом, а снизу крепятся две ноги, соединяемые с основанием. Рама состоит из шести основных слоев и дополнительных накладок. Для увеличения жёсткости предусмотрены диагональные элементы. При поэтапном склеивании необходимо контролировать перпендикулярность элементов, чтобы рама получилась плоская (без скручивания). Раму склеивал без основания, оставив под него пустые пазы. Вклеить основание удобнее уже после установки блока оси нижнего колеса. Моего запаса струбцин не хватало, и я дополнительно использовал саморезы. Поверхности готовой рамы отшлифовал и покрыл лаком в два слоя.
ВСЕ ЧТО НЕОБХОДИМО ДЛЯ ЭТОЙ СТАТЬИ НАХОДИТСЯ ЗДЕСЬ >>>
На фото:
.jpg)
Блок крепления верхнего колеса
Следующий этап — сборка и установка подвижного блока крепления верхнего колеса. Он должен перемещаться в вертикальном направлении и обеспечивать натяжение пильного полотна.
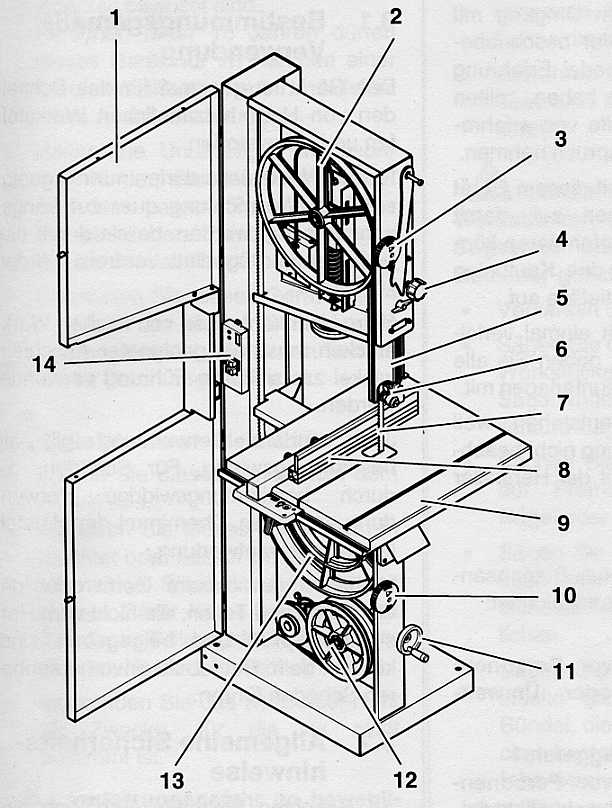
Читайте также: Стол для циркулярной пилы своими руками
Изготовление колёс пилы
Колеса пилы имеют диаметр 400 мм. Их как раз нужно делать из фанеры или МДФ. Колёса у меня вышли толщиной 29 мм. Склеил их из трёх фанерных кругов. Самый ответственный участок здесь — центральная часть колёс. Заготовки вырезал с помощью фрезерной машинки. В центре круга сверлил отверстие 0 6 мм и в него устанавливал центр фрезерного циркуля. Потом это отверстие использовал для совмещения заготовок и склеивания. Вырезал круги с припуском 10 мм под чистовую обработку. Валы 0 25 мм (под приобретённые подшипники) мне изготовил токарь. Они имеют с одной стороны ограничитель, а с другой — внутреннюю резьбу М12. Для изготовления фланцев использовал фанеру. Перед тем как сверлить в них отверстия под подшипник сверлил в центре отверстие 0 6 мм и, совместив его с центром колеса, сверлил по четыре отверстия под шканты. Положение фланца на колесе маркировал. Фланец состоит из двух частей.

12. Когда все детали были готовы, приклеил фланцы к колесу. 13. В качестве держателя использовал блок крепления нижнего вала. 14.Колесо обточил до нужного диаметра придав кромке бочкообразную форму. Скос в каждую сторону — примерно 5 градусов. 15.После предварительной сборки колёса. 16.Направляющая в комплекте с блоками опорных подшипников. 17. Установлена направляющая с верхним опорным подшипником, но пока без «сухарей». На колёса натянуты резиновые камеры (после окончательной сборки их нужно приклеить). 18.Опора рабочего стола оснащена выставил регулировкой в одну плоскость. механизмом наклона
Изготовив оба колеса, на одном из них установил штатный приводной шкив (читайте о подобном решении здесь). Его толщину и форму подгонял под используемый ремень, а диаметр рассчитал так, чтобы скорость движения пильного ленточного полотна была примерно 800 м/мин. Теперь оставалось только отбалансировать колёса. Для этого я взял подшипники с внешним 0 22 мм. Их потом использовал в качестве опорных для пильного полотна. Закрепив горизонтально временную ось и надев на неё подшипники, установил колесо так, чтобы оно легко вращалось, и самая тяжёлая его часть опускалась вниз. Сверлом Форстнера делал небольшие углубления в нижней зоне колеса с тыльной стороны. В результате таких манипуляций я добился, чтобы колесо перестало вращаться в любом положении. На этом балансировка закончилась. Колеса покрыл лаком в два слоя.
Ссылка по теме: Ленточно шлифовальный станок своими руками – фото и конструкция
Затем на колеса натянул разрезанные камеры от 16″ колес детского велосипеда. Резина защищает поверхности колёс от повреждения полотном, снижает шум и предотвращает проскальзывания. Балансировку, правда, пришлось повторить.
Крепление колёс на раму ленточной пилы
Первым установил верхнее колесо. На вал надел шайбы из фторопласта. Колесо крепил болтом с толстой шайбой, вкручивая его в торец вала. Регулировочным болтом выставил верхнее колесо параллельно раме. Блок нижнего колеса закрепил на раме струбцинами и навесил нижнее колесо. С помощью линейки и фторопластовых шайб выставил колёса в одну плоскость. Смещением нижнего блока добился, чтобы линия, соединяющая центры валов, была параллельна вертикальной стойке рамы. Эту операцию выполнял с установленным штатно пильным полотном. После настройки блок крепления нижнего вала зафиксировал. Проверив вращение пилы вручную, решился на пробный пуск. Соблюдая осторожность, включил станок. Испытания прошли успешно. Лента перемещалась посередине колёс, никакой вибрации и подозрительных шумов. Заменив полотно на самое узкое, провёл повторное испытание. Можно было вклеивать основание под двигатель и крепить его к раме. 21. Установлены рабочий стол с пластиной нулевого зазора и вороток механизма натяжения пилы. Станок готов к испытаниям. 22.Рабочий стол можно наклонить под нужным углом. Виден опорный саморез регулировки положения рабочего стола. 23.Прочный каркас мобильной тумбы-подставки.24.Защитный экран двигателя.
Настройка направляющих пильного полотна
Гладкий торец пильной ленты упирается в наружное кольцо подшипника, а с боков её удерживают «сухари». Сначала я сделал «сухари» из фторопласта, но они быстро износились. Поэтому (по совету автора) заменил их на деревянные. В качестве защитного кожуха использовал прямоугольную дюралевую трубу, раскроив её дисковой пилой. Кожух прикрутил к шине саморезами. Шину нужно выставить с высокой точностью, так как при длине 300 мм даже незначительный перекос по отношению к пильному полотну будет ощутим. Для крепления шины в раме выбрал паз. Разметку выполнял по натянутому широкому полотну. Затем уточнил разметку паза по размерам направляющей шины. Но как я ни старался, при выборке паза ошибся на 0,3 мм, что привело к ошибке в нижней точке почти на 4 мм. Поэтому из остатка дюралевой трубы я вырезал уголок, расширил в раме паз на его толщину, а для коррекции положения подклеил несколько кусочков самоклеящейся бумаги толщиной 0,1 мм. Добившись желаемого результата, зафиксировал уголок саморезами. В фиксаторе предусмотрены два отверстия. Одно основное — для максимальной площади прижима шины, второе используется только при очень толстых заготовках, чтобы максимально поднять шину.
Изготовление рабочего стола для ленточной пилы своими руками
Сначала изготовил опору с механизмом наклона стола. Делал её из древесины дуба. К ней крепится нижний блок опорных подшипников. К поворотному механизму стола присоединил подкладку из ЛДСП для повышения жёсткости стола. На сам стол я пустил обрезок столешницы из ДСП. Она довольно толстая и прочная, а поверхность у неё — гладкая и скользкая. Кромки обшил буковыми рейками. В рабочей зоне в столе выпилил прямоугольное отверстие, а затем выфрезеровал выемку под вставку из МДФ. Вставку устанавливал при включенной пиле: заводил вставку в пазы и задвигал до упора, одновременно пропиливая её на нужную длину. При повороте стола под углом вставку либо вообще вынимаю, либо изготавливаю новую под конкретный угол. На гайку механизма натяжения полотен я изготовил вороток. Силу натяжения устанавливаю на глазок — порвать полотно практически невозможно. Чтобы удобнее было выставлять стол перпендикулярно к полотну, изготовил дополнительный упор для стола. Вкрученный в упор само- рез позволяет регулировать положение стола. А чтобы опилки не налипали на колёса, установил обрезанную зубную щётку на нижнее колесо.
Изготовление тумбы для пилы
Размеры тумбы я выбрал исходя из размеров основания пилы, а высоту подгонял так, чтобы стол был на уровне 1 050 мм от пола — для меня это в самый раз. Тумбу сделал из обрезков шпунтованной половой доски толщиной 35 мм. Каркас тумбы собрал на шкантах. Углы изнутри усилил металлическими уголками. Боковые вставки — из ламинированного ДСП. Задняя стенка — из МДФ. В общем, всё из обрезков. Верхний ящик тумбы служит для сбора опилок. Тумба установлена на колесики с возможностью их фиксации.
25. Правая стенка кожуха нижнего колеса скошена вверху для упрощения замены пильных полотен. 26. Задняя стенка защиты нижнего колеса установлена наклонно и направляет опилки в ящик. 27.Параллельный упор закреплён на рабочем столе.. Установка защиты. 28.Так выглядит защита подвижных элементов.. Установлены пусковая кнопка пилы и выключатель подсветки.
Защитные кожухи и элементы корпуса пилы являются одновременно и направляющими для удаления опилок. Все рабочие элементы пилы защищены экранами. В качестве материала для кожухов и экранов использовал МДФ толщиной 8 мм и сосновые доски.
Ссылка по теме: Как сделать своими руками самодельную стационарную циркулярку
Электропроводка
Кроме пусковой кнопки сразу решил установить подсветку рабочей зоны. Для этого использовал светильник с гибким кронштейном, а его выключатель расположил рядом с кнопкой пуска. Провода пропустил сквозь раму и закрепил сзади.
Параллельный упор
Ленточной пилой уже можно было пользоваться, но ощущалась нехватка параллельного упора. Механизм фиксации упора соорудил на базе эксцентрика. Из-за скругленного переднего края стола пришлось дополнительно вырезать подвижный толкатель с полукруглой передней кромкой. Шину упора сделал из лиственницы. С противоположной стороны шины прикрепил захват, который упирается в край стола. На изготовление пилы у меня ушло почти два месяца. Правда, работал над ней я далеко не каждый день. Проект получился очень увлекательным. Работой станка доволен. Сейчас даже не представляю, как раньше обходился без ленточной пилы. В качестве теста для пилы я сделал несколько шкатулок.
Ленточная пила по дереву своими руками- все фото
©Сергей Головков, г. Новочеркасск
ИНСТРУМЕНТ ДЛЯ МАСТЕРОВ И МАСТЕРИЦ, И ТОВАРЫ ДЛЯ ДОМА ОЧЕНЬ ДЕШЕВО. БЕСПЛАТНАЯ ДОСТАВКА. ЕСТЬ ОТЗЫВЫ.Подпишитесь на обновления в наших группах и поделитесь.
Будем друзьями!
Как сделать ленточнопильный станок
В марте 2010 года я начал этот проект. До этого я с интересом следил за сборкой ленточной пилы Matthias Wandel (первой) и подумал, что попробую собрать свою собственную. Именно так начинаются многие проекты: источник вдохновения для запуска творческого процесса, и именно это, а также собранные ноу-хау делают такие сайты, как Woodgears. ca , такими ценными.
Рамка
Я начал с рамки. Имея умение работать с металлом, захотелось сделать из стали. Сталь может производить прочную раму, которая не будет слишком громоздкой, если она изготовлена правильно. Я изучил некоторые коммерческие конструкции ленточных пил, в основном по габаритным размерам и конструктивным деталям, и придумал базовую конструкцию рамы.
Основной опорный элемент рамы представляет собой кусок прямоугольной трубы с толстыми стенками 2″ x 3″. Это будет стойка, которая проходит вертикально с левой стороны рамы, и к ней будут приварены остальные компоненты рамы. Эта основная опорная стойка обеспечивает большую часть прочности рамы, поэтому было важно, чтобы она была достаточного размера, чтобы выдерживать силы изгиба и скручивания, которые будут испытывать раму.
Для большей части остальной части рамы я использовал толстостенные квадратные трубы размером 1″ x 1″, извлеченные из старой (довольно большой) садовой решетки. Приклад был в грубой форме, и основным препятствием для его использования были толстые слои краски, которые мне пришлось бы стачивать:
Много работы по его очистке, но преимущества двоякие: я экономлю деньги на сырье и избавляюсь от того, что больше не является полезным или привлекательным.
Здесь первый элемент рамы закреплен на месте и готов к сварке:
Точное размещение всех частей рамы имеет решающее значение для сборки. Я сделал зажимной приспособление под углом 90 градусов из фанеры, чтобы удерживать деталь перпендикулярно основной стойке, и использовал другой кусок трубки, чтобы зажать ее на одной линии с лицевой стороной стойки.
При сварке деталей следует помнить о том, что тепло от сварки и усадка остывающего сварного шва деформируют металл, выбивая его из равновесия. Чтобы избежать этого, я привариваю деталь на противоположных сторонах стыка, тем самым сводя к минимуму эту деформацию. Когда деталь прибита со всех четырех сторон, я могу завершить сварку, переходя от одной стороны к другой и проверяя выравнивание по мере продвижения.
Нижняя часть рамы принимает форму:
И с добавлением еще трех элементов нижний каркас готов. Каким бы «деревенским» он ни выглядел, он очень прочный и очень аккуратно сделан.
Добавление металлической «кожи» к нижней раме. Это я прикрутил саморезами для листового металла. Я не хочу рисковать искажать раму, приваривая эту кожу на место. Опять же, я использую переработанную сталь, на этот раз материал из оконных проемов на тяжелой стальной двери:
Получение верхней части каркаса. Нижний элемент расположен под углом, чтобы немного уменьшить свободный пролет основной стойки, а также потому, что он выглядит немного лучше, чем квадратный. Этот угол не снижает общую режущую способность, так как верхняя направляющая лезвия будет висеть под элементом с правой стороны.
Плоская планка посередине — это верхнее крепление оси колеса.
Добавлена кожа и закончено верхнее крепление колеса.
Эта пила отличается от большинства других тем, что натяжение полотна регулируется подъемом или опусканием нижнего узла колеса/двигателя. Верхнее колесо отвечает только за отслеживание, и это делается путем сгибания плоского стального стержня, к которому прикреплена ось, вперед и назад с помощью маховика в задней части устройства:
На этот вал будет установлено ручное колесо для облегчения отслеживания. Механизм очень прост: при отгибании плоского стержня назад ось выходит из горизонтального положения, вытягивая верхнее колесо из вертикального положения, а лезвие направляется к задней части колеса. При сгибании стержня вперед происходит обратное: колесо отклоняется от вертикали вперед, а лезвие движется вперед.
Подрамник двигателя в сборе
Двигатель, который я хотел использовать для этого, был одним из двух двигателей беговой дорожки, которые я купил в магазине излишков. Другой я использовал в своем проекте Disk Sander. Они рассчитаны на 1 л.с. и вращаются со скоростью 1725 об/мин — очень хорошо для ленточной пилы такого размера. Хотя на тот момент это еще не было проверено, я подумал, что стоит рискнуть использовать этот двигатель, поскольку он был очень дешевым.
Для установки двигателя я сконструировал раму с шарниром, позволяющую двигателю раскачиваться вверх и вниз для натяжения клинового ремня:
Затем эта рама была прикреплена к подрамнику основного узла двигателя, частично показана здесь завершенный.
Верхняя часть подрамника поддерживает нижнюю оправку привода колеса. Здесь можно увидеть, что агрегат в основном собран, установлены шкивы нужного размера и установлен клиновой ремень нужной длины:
Ободренный уверенностью в выполнении такой великолепной работы, я включил его, чтобы проверить производительность. Именно тогда я понял, что этот двигатель вращается против часовой стрелки и не может быть реверсирован (вся проводка пусковой обмотки была внутри сварной рамы двигателя, что делало невозможным замену проводки без вскрытия рамы).
Итак, у меня был выбор: либо перевернуть двигатель (на это мне указал Матиас Вандель, хотя в то время было уже слишком поздно)
, либо приобрести другой двигатель, реверсивный. Поскольку эти двигатели беговой дорожки все еще были неизвестного качества, я решил приобрести новый двигатель:
Новый (в продаже) двигатель мощностью 1 л.с., который я подключил для работы по часовой стрелке. Пришлось добавить пару штук к мотораме, но это не составило особых хлопот. Мне также пришлось использовать более короткий ремень, поскольку новый двигатель устанавливался на подрамнике выше, чем двигатель беговой дорожки.
Затем я сделал монтажную раму для подрамника и прикрутил ее к раме пилы (слишком много рам?). Между монтажной рамой и узлом подрамника двигателя я использовал выдвижные направляющие, чтобы узел двигателя мог двигаться вверх и вниз для натяжения лезвия. Оглядываясь назад, могу сказать, что делать это таким образом было не очень хорошей идеей. Заставить верхнее колесо двигаться вверх и вниз для натяжения полотна было бы немного проще:
Теперь пила готова к установке колес.
Говоря о колесах, я снял с пилы подрамник двигателя, чтобы «повернуть» колеса, и надел на них корону (таким же образом я сделал и верхнее колесо). Колеса сделаны из меламина 5/8″, а обод утолщен вторым слоем, чтобы сделать колеса толщиной 1-1/4″. Несмотря на тяжелый вес, они очень плоские и устойчивые:
Когда рама готова, я покрасил ее. Это базовый слой плоской ржавчинной краски Tremclad (белый), поверх которого нанесен прозрачный сатиновый полиуретан на водной основе. В результате получается очень прочное и долговечное покрытие. Внешний вид сильно меняется, хорошо чистится.
Подрамник двигателя в сборе я покрасил в матовый черный цвет. Снова краска по ржавчине Tremclad, но на этот раз в баллончике:
Я сделал кожух ремня и шкива из листового металла и прикрутил его на место. На этом рисунке показан увеличенный монтажный фланец, который я сделал и приварил к валу оправки, чтобы лучше поддерживать нижнее колесо.
С установленными колесами:
К сожалению (или нет, кто знает) в это время в процессе сборки у меня случился «выгорание» — мне просто нужно было отдохнуть от проекта, так как я работал над ним ( и думать об этом) постоянно. Я решил на время приостановить проект, чтобы восстановить мотивацию довести дело до конца.
Я и не подозревал, сколько времени пройдет, прежде чем эта мотивация вернется.
Полтора года спустя…
Перенесемся на семнадцать месяцев вперед. Пила все это время стояла у меня в магазине нетронутая и пылилась. К настоящему времени у меня есть этот веб-сайт, и я закончил много других проектов, некоторые из которых представлены здесь, и я чувствую желание, наконец, закончить пилу.
Первый шаг — заново ознакомиться с ним — соответствующие детали туманны: какой длины будет клинок? Насколько быстро работает пила? Поэтому я трачу время на изготовление «лезвия» из кромочного материала общей длиной 120 дюймов. Примеряю это на пилу и снял короткое видео действия:
Это подтверждает длину полотна, и я заказываю один из R&D Bandsaws – ширина 3/4″, 3 tpi, шведский кремний. Наличие лезвия в руке — это мотивация, на которую мне нужно двигаться дальше.
Когда он прибудет, я не могу не попробовать:
youtube.com/embed/u8st-gU4GLo?wmode=transparent»/> Разрезание на 6 дюймов очень твердого клена. Я просто немного опасаюсь, не в восторге от своих шансов остаться невредимым, если лезвие сломается или отвалится, поэтому я отношусь к этому спокойно. Даже без направляющих лезвия или шин в настоящее время, кажется, он хорошо режет.
Тем не менее, эти два теста выявили некоторые проблемы: верхнее колесо, кажется, имеет шумный подшипник, 8-дюймовый шкив на ведущей оправке ослаб, и мне не нравятся подшипники для оправки — это (дешевая) смазанная втулка. подшипники, и я бы предпочел закрытые шарикоподшипники.
Первая проблема, с которой я столкнулся, — это шпиндель. Я снимаю его с подрамника двигателя и осматриваю, обнаружив, что установочный винт на 8-дюймовом шкиве ослаб. Я все очистил и использовал PL Premium в качестве фиксатора резьбы на всех установочных винтах и даже между фланцем шпинделя, шкивом и стопорным кольцом. Я не хочу, чтобы это снова развалилось!
Далее я
обращаюсь к оправке подшипников. Я покупаю четыре новых закрытых подшипника и делаю две подушки для них. Первый шаг – просверлить отверстия немного меньшего размера:
Эти отверстия расположены близко друг к другу, и на моей шлифовальной станции не требуется много времени, чтобы сделать их идеально подходящими:
2 герметичных подшипника, и этого должно хватить для опоры вала оправки:
Затем переустановил двигатель на подрамник в сборе.
Как оказалось, натяжение лезвия вытолкнет узел двигателя наружу, в результате чего нижнее колесо выйдет из вертикального положения. Это вызвано провисанием направляющих ящика, которые я использовал для перемещения узла двигателя вверх и вниз. Чтобы противодействовать этому, я добавил прокладки к блоку задней подушки, а позже изменил его, чтобы сделать его регулируемым. Это одна из лучших причин, чтобы не делать что-то таким образом. Живи и учись.
Решив проблему с валом/подшипником, я перехожу к той части проекта, над которой я застопорился несколько месяцев назад – натяжителю.
Натяжитель имеет две цели: во-первых, создать рабочее напряжение на лезвии. Во-вторых, чтобы разрешить смену лезвия. В моем случае мне пришлось сделать так, чтобы он прижимался к подрамнику узла двигателя для натяжения лезвия, а также имел возможность поднимать его, чтобы облегчить замену лезвия. Для этого я использовал ходовой винт 3/8″ и редуктор от сломанной мини-шлифовальной машины. У него передаточное число примерно 2:1 (выход медленнее, чем вход), что идеально подходит для этого.
Пружин нет, только направленная вниз сила, приложенная резьбовым стержнем 3/8″ между редуктором кофемолки и подрамником двигателя. Это работает безупречно, и это было просто и довольно легко сделать, как только я проработал детали.
Имеется регулируемый ограничитель натяжения и подъема колеса для смены полотна. Это назначение 2 пар двойных гаек над и под поперечиной подрамника (синие стрелки):
Я определил наилучшее натяжение лезвия, затем установил нижний комплект двойных гаек, чтобы остановить натяжитель в этой точке. Точно так же я провернул колесо так, чтобы можно было снять лезвие, и зафиксировал верхние гайки в этом положении. Это полезно, так как между верхней частью нижнего колеса и нижней частью стола не так много места.
Затем я добавил опору на раму и маховик для легкого поворота.
Ход очень плавный и нет необходимости в каком-либо блокировочном механизме – настройка остается неизменной и не будет расшатываться.
В конце концов, мои опасения по поводу этой части сборки оказались напрасными.
Иногда мы можем превратить легко решаемую проблему в непреодолимую, обычно путем обдумывания. Лучше погрузиться, четко определить, что нужно сделать, и выяснить, как лучше всего это сделать.
Направляющие лезвия
Сначала я сделал нижнюю направляющую лезвия, так как она крепится к раме и, следовательно, ее легче построить. Я хотел использовать это, чтобы проверить идею, которая у меня была: использовать пластик UHMW для направляющих блоков. Пластик со сверхвысокой молекулярной массой представляет собой материал с низким коэффициентом трения, используемый (в деревообработке) для приспособлений и других приспособлений, изготовленных в заводских условиях, поверхности которых должны плавно скользить. Например: направляющая планка на угловом упоре или салазки для поперечной резки, которые входят в прорезь настольной пилы. Я использовал кусочки этого для направляющих блоков:
Это 3/8″ x 3/4″ и около 3/4″ в длину. Они не показывают никаких признаков износа после моего тестирования. По общему признанию, мой тестовый период был коротким, но также был более напряженным для этих блоков, чем нормальная работа пилы. Я уверен, учитывая первые результаты, что они будут очень хорошо работать для этой цели.
Закончив нижнюю направляющую, я обратил внимание на верхнюю. Изначально я собирался сделать и эту стационарной – эта ленточная пила предназначена только для повторного использования, поэтому я подумал, что подвижная верхняя направляющая полотна не оправдана. Однако, подумав еще немного, я отказался от этого решения и начал собирать детали для направляющей.
Начиная с пары цельных кленовых креплений, они имеют толщину 1-1/4″ и имеют точные отверстия 1-1/4″, прорезанные в них для установки направляющей стойки диаметром 1-1/4″ узла направляющей верхнего лезвия. :
Полностью готовые к установке болты с квадратным подголовком 4-1/2″ x 1/4″ крепят их к раме пилы. Нижнее крепление имеет ручку для затягивания, чтобы зафиксировать направляющую стойку на месте.
Аккуратно разметив и просверлив отверстия в раме, я использую ступенчатое сверло для увеличения направляющих отверстий:
Крепления установлены и направляющая стойка для пробной посадки.
Первая часть верхней направляющей лезвия приварена на месте, она изготовлена из низкоуглеродистой стали толщиной 1/8″, полностью приварена к концу направляющей стойки и имеет надрез вокруг лезвия. Как и в нижней, в верхней будут использоваться блоки UHMW, зажатые таким же образом:
После добавления других стальных деталей просверливаются и нарезаются отверстия для зажимных винтов направляющего блока. Это крепежные винты № 10 x 24, и они будут зажимать губки держателя, сомкнутые вокруг пластиковых блоков.
Упорный подшипник регулируется внутрь и наружу и фиксируется контргайкой:
Я снял нижнюю направляющую для покраски вместе с верхним и монтажным блоками направляющей стойки. Краска действительно очищает внешний вид сварных деталей.
Вот вся сборка, готовая и установленная:
Пылесборник и задний обтекатель
Изучив несколько коммерческих моделей, я придумал конструкцию пылесборника. С этого момента большая часть работы — это наращивание, вырезание одной детали по размеру ранее установленной детали. Пылесборник это хорошо иллюстрирует.
Первый кусок дерева обрезается так, чтобы он помещался в пространство между элементами рамы, и привинчивается сзади:
Следующий обрезается поверх первого и ввинчивается в него. Он скошен, чтобы создать наклон как вперед, так и в сторону.
Следующая деталь имеет насечку под лезвие и ввинчена, на ней лучше виден наклон вперед. Эта часть снимается для замены лезвия:
И, наконец, последние детали прикручиваются на место. Это должно отвести большую часть пыли. Конечно, он не полный — передняя крышка составляет его часть, а также есть резиновая шайба, которую нужно установить вокруг слота для лезвия, но об этом позже.
Снова обращая внимание на заднюю часть машины, вот некоторые детали коленчатого вала натяжителя:
«Подшипник» для вала представляет собой кусок алюминиевой трубки, отрезанный чуть длиннее, чем толщина блока, на котором он установлен. идет через. Это позволяет ему свободно вращаться при затяжке гаек:
Добавлена пластиковая рукоятка от сломанной настольной пилы. Он имеет соответствующую маркировку «вверх-вниз», и поворот его в направлении «вверх» увеличивает натяжение лезвия.
Задний обтекатель собран и надет. Сделанный в основном из фанеры 1/4″, он съемный, чтобы получить доступ к блоку двигателя:
Цель этого обтекателя — защитить двигатель от пыли и улучшить внешний вид — он очищает внешний вид задней части пилы. там. Функционально он также обеспечивает поддержку стола.
Стол
Стол этой ленточной пилы фиксированный, не наклоняется. Учитывая, что эта пила в основном будет использоваться для распиловки заготовок, не было большого смысла усложнять конструкцию, делая наконечник стола. В маловероятном случае, если я захочу отрезать что-то под углом этой пилой, я могу сделать наклон под правильным углом.
Что я считаю очень важным для этой пилы, так это то, что стол должен быть прочным и не двигаться и не прогибаться, когда я кладу на него тяжелый кусок дерева для резки. Правильно укрепить стол намного проще, когда он зафиксирован на месте.
Начав с куска фанеры из балтийской березы толщиной 1/2″ размером 30″ x 24″, я сделал надрезы вокруг основной опорной стойки и вокруг лезвия:
Я использовал 1/2″ для увеличения перепилил емкость (каждая мелочь помогает), и у меня уже был кусок такого размера. Немного подумав, я решил, что лучший способ получить доступ к лезвию и нижней направляющей лезвия — сделать весь этот угол стола съемным. Я бы сделал так, чтобы он скользил внутрь и наружу, удерживаясь на месте двумя болтами с ручками.
Основная часть стола крепится болтами к раме и имеет один винт сзади, в крышке блока двигателя.
Установив основной стол, я начинаю собирать боковую опору. Изготовленный из массива клена, он приклеен и прикручен к деревянной планке на краю нижней рамы. Он должен быть как можно более жестким, чтобы поддерживать эту сторону стола:
Прежде чем двигаться дальше, я проверил, чтобы лезвие находилось под углом 90 градусов к столу в обоих направлениях:
Теперь, пока клей не схватился, достаточно легко отрегулировать. К счастью, лезвие правильно ориентировано по отношению к столу, и мне не нужно вносить никаких изменений.
Для добавления дополнительных деталей к основному столу требуется несколько зажимов. Передняя кромка из цельного дерева, а также заготовка на дне для формирования прорези для съемной части стола:
Съемная часть обрезается по размеру и устанавливается на место. Прорезь для лезвия я вырезал ленточной пилой. Это создает паз с нулевым зазором для лезвия, которое должно очень хорошо держаться.
Кромка из цельного дерева приклеена, а снятие пластиковых накладок с пружинных зажимов позволяет мне более точно определить усилие зажима:
Чтобы удерживать угол на месте, сзади используется болт с квадратным подголовком.
Еще один спереди помогает держать верхнюю часть на одной линии. Оба утоплены под поверхностью стола:
Выдвижение секции для снятия. На картинке вы можете видеть язычок, который входит в прорезь сбоку. Это обеспечивает полную поддержку этой части верха.
Передняя крышка
Передняя крышка проста, но сложна. Он должен быть прочным и легким, и он должен преодолевать препятствия. Поэтому я подумал, что лучший способ построить его будет на месте, по одной части за раз.
Начав с куска пихты 2″ x 3″, я установил три обычные петли встык, врезанные в древесину достаточно глубоко, чтобы установить другую створку петли на раму:
Я использовал самосверлящий листовой металл винты, чтобы прикрепить другую створку к стальной стойке.
Затем я начал добавлять детали, подгоняя их по ходу дела. Преимущество в том, что вы можете легко увидеть, если что-то не в том месте или не попадает в другую часть пилы:
Небольшая, но важная деталь, крышка диска, которая крепится к основной опорной стойке.
Немного фанеры для утолщения крышки в нужном месте. Поскольку внешняя обшивка крышки будет выполнена из фанеры толщиной 1/4″, рекомендуется добавить ребра жесткости там, где это необходимо:
Проявите творческий подход к зажимам. Здесь я приклеиваю направляющие планки для скользящего защитного кожуха. Использование пружинных зажимов удобно, но их досягаемость ограничена. Мне помогают деревянные планки и гаечный ключ.
Нижняя половина усложнена пылесборником:
Его нужно сделать так, чтобы он поместился вокруг него и в закрытом состоянии запечатал мило из нижнего отсека.
С прикрепленной фанерной обшивкой толщиной 1/4″. Я использовал клей, гвозди и зажимы, чтобы зафиксировать кожу на месте. Она была вырезана чуть больше по размеру цельным куском, из цельного листа. Это помогает повысить прочность крышки за счет устранения стыков:
Вставляется последний элемент. Он совмещается с защитным кожухом на стойке, чтобы закрыть зазор, когда крышка закрыта.
Наконец, я подравниваю края насадкой для ламината:
Готово к шлифовке и покраске.
Сбор пыли
Эффективный сбор пыли очень важен для меня, и мне нравится, чтобы он был простым. Для ленточной пилы будет очень мало переносимой по воздуху пыли – большая ее часть будет стягиваться вместе с лезвием. Пылесборник был спроектирован так, чтобы улавливать как можно больше пыли, и для этого ему требовалось место для ее размещения.
Я нашел решение, которое хорошо работает. Это длинная коробка, открытая сверху и сделанная из 1/4″ фанеры. Одной из его изящных особенностей является то, что он также удерживает нижнюю половину передней крышки закрытой, зацепляясь за ножку и надвигаясь на переднюю крышку:
Вот вид сверху вниз, показывающий, как это сделано. Стороны расширяются, и это то, что удерживает переднюю крышку закрытой. Коробка просто строится с помощью клея и гвоздей. Для внутренней панели был вырезан неглубокий выступ, чтобы обеспечить хорошее выравнивание.
Вот как он цепляется за ногу:
После установки деревянный зажим удерживает его закрытым. Зажим завинчивается глубже, чтобы он мог подпрыгнуть, чтобы освободить коробку для опорожнения. Все это довольно плотно закрывается, когда находится на месте, и просто сидит там, заполняясь пылью.
Электрооборудование
Я сделал защитные кожухи для крышки выключателя и приклеил их на место:
Это просто куски фанеры толщиной 1/4″, вырезанные по размеру, отшлифованные и приклеенные для предотвращения случайного включения пилы. Небольшая вещь, которую нужно сделать, но время, потраченное на то, чтобы сделать то, что увеличивает запас прочности, стоит потраченного времени и усилий.
Приведение в порядок проводки. Я использую старый трехжильный удлинитель для проводки, сохраняя его аккуратным и безопасным. Проволочные гайки (маретты) не работают лучше всего на многожильных проводах, поэтому я обмотал их изолентой, чтобы убедиться, что они не болтаются от вибрации:
Металлическая крышка для закрытия. Чтобы все это сделать, требуется некоторое время, но торопиться с этой частью не стоит риска.
Шнур выходит из пилы снизу. Я завязал узел на шнуре, чтобы его нельзя было выдернуть. Шнур питания имеет длину около 12 футов, что удобно для прямого подключения без использования удлинителей:
Выключатель на месте. Я покрасил коробку и крышку в черный цвет, чтобы он соответствовал остальной части пилы. Я использовал обычный выключатель света, и этот выключатель может со временем выйти из строя (пусковой ток для запуска двигателя превышает его номинал), но они дешевы и их легко заменить.
Попользовавшись пилой несколько раз, могу сказать, что это, пожалуй, идеальное место для выключателя питания. Легкий доступ из положения резки.
Детали
Некоторые детали можно купить, некоторые придется изготовить. Другие, например защелку, удерживающую переднюю крышку закрытой сверху, можно купить, но она может работать лучше, если вы сможете сделать ее самостоятельно.
Я решил изготовить эту деталь самостоятельно, начав с куска толстого листового металла:
Первые надрезы определяют ручку, а затем ее сгибают с помощью приспособления для гибки. Также подойдут плоскогубцы или тиски.
Вырезана остальная часть формы и просверлено отверстие под ось:
Усовершенствуйте деталь, обтачивая острые края.
И готовое изделие покрашено и установлено. Внешний вид, который я хочу, идеальный размер, который мне нужен, и точная функция:
К ноге добавлены ролики. Они позволяют мне перемещать пилу, опуская ее обратно на колеса. Затем я могу свернуть его туда, где мне нужно. Когда пила снова окажется в вертикальном положении, колеса оторвутся от пола.
Резиновая прокладка изготовлена и помещена в пылесборник:
Это уменьшает количество пыли, попадающей на дно. После большого использования он зарекомендовал себя и не показывает признаков износа.
Вид сзади готовой пилы:
Рукоятка регулировки натяжения полотна.
Маховик для перемещения полотна:
И готовая пила.
Большой проект, на его выполнение ушло много часов. В какой-то момент, увидев, что он пролежал в моем магазине нетронутым более года, я почувствовал, что никогда не сделаю этого.
Рад, что ошибся.
Чертежи ленточнопильного станка для широкого распила – Matt Cremona
- Описание
- Отзывы (39)
Matt Cremona, LLC («Продавец») — компания с ограниченной ответственностью, Миннесота, с основным местом деятельности 3505 Admiral Lane North, Brooklyn Center, Minnesota 55429. Продавцом («Планы лесопилки») в соответствии с положениями, условиями и ограничениями, изложенными в настоящем документе.
ПРОДАВЕЦ ОТКАЗЫВАЕТСЯ ОТ ВСЕХ ГАРАНТИЙ ЛЮБОГО РОДА, ЯВНЫХ, ПОДРАЗУМЕВАЕМЫХ И/ИЛИ ЗАКОННЫХ, ВКЛЮЧАЯ, ПОМИМО ПРОЧЕГО, ПОДРАЗУМЕВАЕМЫЕ ГАРАНТИИ КОММЕРЧЕСКОЙ ПРИГОДНОСТИ И ПРИГОДНОСТИ ДЛЯ ОПРЕДЕЛЕННОЙ ЦЕЛИ, НЕНАРУШЕНИЯ ПРАВ И ПРАВА. ЛЕСОПРОВОДНЫЕ ПЛАНЫ ПРОДАЮТСЯ «КАК ЕСТЬ».
Продавец не гарантирует, что лесопильные чертежи соответствуют или соответствуют требованиям какого-либо конкретного кодекса безопасности или государственных требований. Продавец оставляет за собой право время от времени изменять конструкцию своих лесопильных схем без предварительного уведомления и без обязательств по внесению соответствующих изменений в свои ранее проданные лесопильные планы. Любые действия, предпринимаемые Покупателем в отношении информации, содержащейся в Схемах лесопилки, осуществляются исключительно на собственный риск Покупателя.
Ни при каких обстоятельствах Продавец, включая его должностных лиц, агентов, сотрудников, представителей, поверенных, а также материнские, дочерние и аффилированные компании, не несет ответственности за убытки любого характера, включая, помимо прочего, особые, прямые, косвенные, случайные, штрафные, штрафные, или косвенные убытки или убытки, включая, помимо прочего, независимо от того, связаны ли они или каким-либо образом вытекают из любого несоответствия Чертежей лесопилки, любого дефекта Чертежей лесопильного завода и качества изготовления, любого исполнения или неисполнения Продавцом любое из обязательств или задержка поставки или невыполнение поставки по какой-либо причине, и независимо от единоличной, совместной и / или одновременной небрежности, нарушения контракта, нарушения гарантии, строгой ответственности в гражданском правонарушении или законном требовании, или другой юридической ошибки или ответственности Продавца.