Что такое композитные материалы
Как и из чего строят яхты, какие технологии используют, что такое композит, чем отличается эпоксидная смола от полиэфирной, и как в этом задействован карбон? Мы решили разом ответить на все вопросы о технологии производства и написали большой лонгрид о том, как строят суда из стеклопластика — какие бывают материалы и методы. А в конце статьи подробно рассказали, что из этого используем мы на верфи Pacifico.Что такое композит
Композиты — группа материалов, состоящих из нескольких компонентов, один из которых выполняет армирующую функцию, а второй связующую.Например, железобетон — это вид композита. В этом соединении железо выполняет армирующую функцию, а бетон — связующую. Композит, который используют в судостроении, называется стеклопластиком или углепластиком. Базово он состоит из стеклоткани или углеткани и смолы.
Особенность композитов, что готовый материал обладает гораздо большей прочностью и жесткостью, чем его ингредиенты по отдельности.
Из чего состоит композит
Композит, из которого строят суда, базово состоит из 4-х типов материалов:- связующее вещество (смола)
- армирующее вещество (ткань)
- средний слой (наполнитель для сэндвича: пена или сотовый материал)
- поверхностный слой (краска/гелькоут)
Если объяснять упрощенно, то композит производят следующим образом — ткань пропитывается жидкой смолой с отвердителем, высыхает и отвердевает. Самые простые композитные конструкции состоят просто из нескольких слоев ткани и смолы. Например, так строят корпуса детских парусных яхт Оптимист. Для более сложных и больших конструкций, например, прогулочных катеров, используют композитный сэндвич.
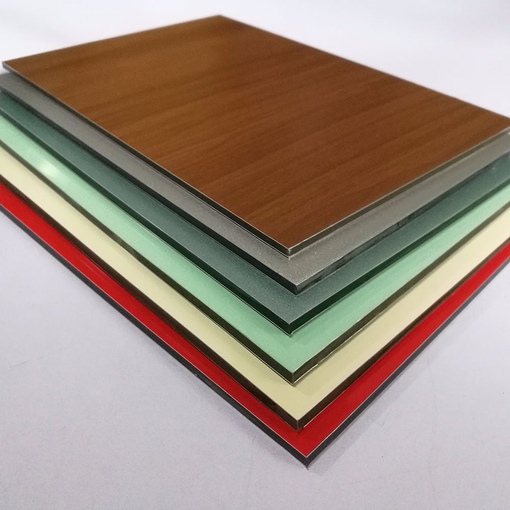
Разберем отдельно каждый тип материалов.
Смола
Смола — связующую вещество, которое пропитывает все слои композита и превращает их в готовую монолитную деталь. В судостроении используется 3 типа смолы:- эпоксидная
- эпоксивинилэфирная
- полиэфирная
Эпоксидная смола — самая прочная и дорогая. За счет повышенной прочности для изготовления детали ее требуется меньше, чем полиэфирной смолы, а значит сама деталь получается легче. Не содержит ядовитого вещества — стирола. Корпус лодки из эпоксидной смолы может эксплуатироваться без ремонта до 30 лет подряд.

Полиэфирная — дешевая и наименее прочная, содержит стирол. Изделия из нее получается тяжелее и со временем начинают впитывать воду. Полиэфирная смола более хрупкая, поэтому корпуса из нее со временем нуждаются в ремонте. Корпус из полиэфирной смолы в среднем служит до 20 лет.
Ткань
Ткань в судостроении выполняет роль армирующего вещества — с помощью нее изделию задается форма, она берет на себя нагрузку на скручивание. Ткань дает конструкции прочность на растяжение или сжатие. В судостроении используется три типа ткани:- стекломат
- стеклоткань
- углеткань
Стекломат — рубленные спресованные волокна стекловолокна. Стекломат максимально гибкий и подвижный, ему можно задать любую форму или изгиб.

Стеклоткань — стекловолокна, которые сплетено таким образом, что у ткани есть конкретное направление. Виды плетения бывают разными и от них зависит под каким углом ткань абсолютно устойчива на растяжение. Грамотный проект яхты учитывает особенности направления ткани и четко регламентирует какой тип плетения надо использовать на конкретных участках конструкции. Благодаря сочетанию разных типов плетения получаются максимально прочные детали, устойчивые к любым видам нагрузок.
Углеткань — тоже самое, что стеклоткань, только из углеволокна. У нее тоже есть разные типы плетения и направления. Углеволокно примерно в 2 раза прочнее, чем стекловолокно — точное соотношение зависит от типа плетения. Но стоит в 20 раз дороже.
Если упрощенно, то благодаря повышенной прочности на одну и ту же деталь углеволокна уходит в 2 раза меньше, чем стекловолокна. В результате деталь из углеволокна получается примерно в 2 раза легче. Готовый материал изделия из углепластика называется карбон. Полностью из карбона строят самые дорогие и быстрые гоночные яхты в мире.
Средний слой
Средний слой нужен, чтобы добавить расстояния между несколькими армирующими слоями ткани, и тем самым повысить поверхностную плотность изделия. Дело в том, что сама по себе ткань дает нужную прочность только на скручивание или сжатие, но не дает необходимой поверхностной прочности — деталь получается слишком тонкой. В теории, увеличить толщину и соответственно поверхностную прочность можно просто наложив больше слоев стеклоткани, но тогда мы получим слишком большой вес, и при этом избыточную прочность к скручивающим нагрузкам.Поэтому, чтобы соблюсти баланс между весом, поверхностной прочностью и устойчивостью к скручиванию, используют принцип сэндвича и прокладывают армирующие слои легким наполнителем. Чаще всего в производстве используют следующие типы наполнителя:
ПХВ — пенополивинилхлорид.

Если нужен максимально легкий и быстрый корпус, лучше использовать ПХВ. Если нужно получить дешевую, но тихоходную лодку — выгоднее использовать coremat.
Поверхностный слой
Поверхностный слой — внешний слой корпуса, который дает цвет и защищает от поверхностных повреждений. Обычно его делают из гелькоута или полиуретановой краски.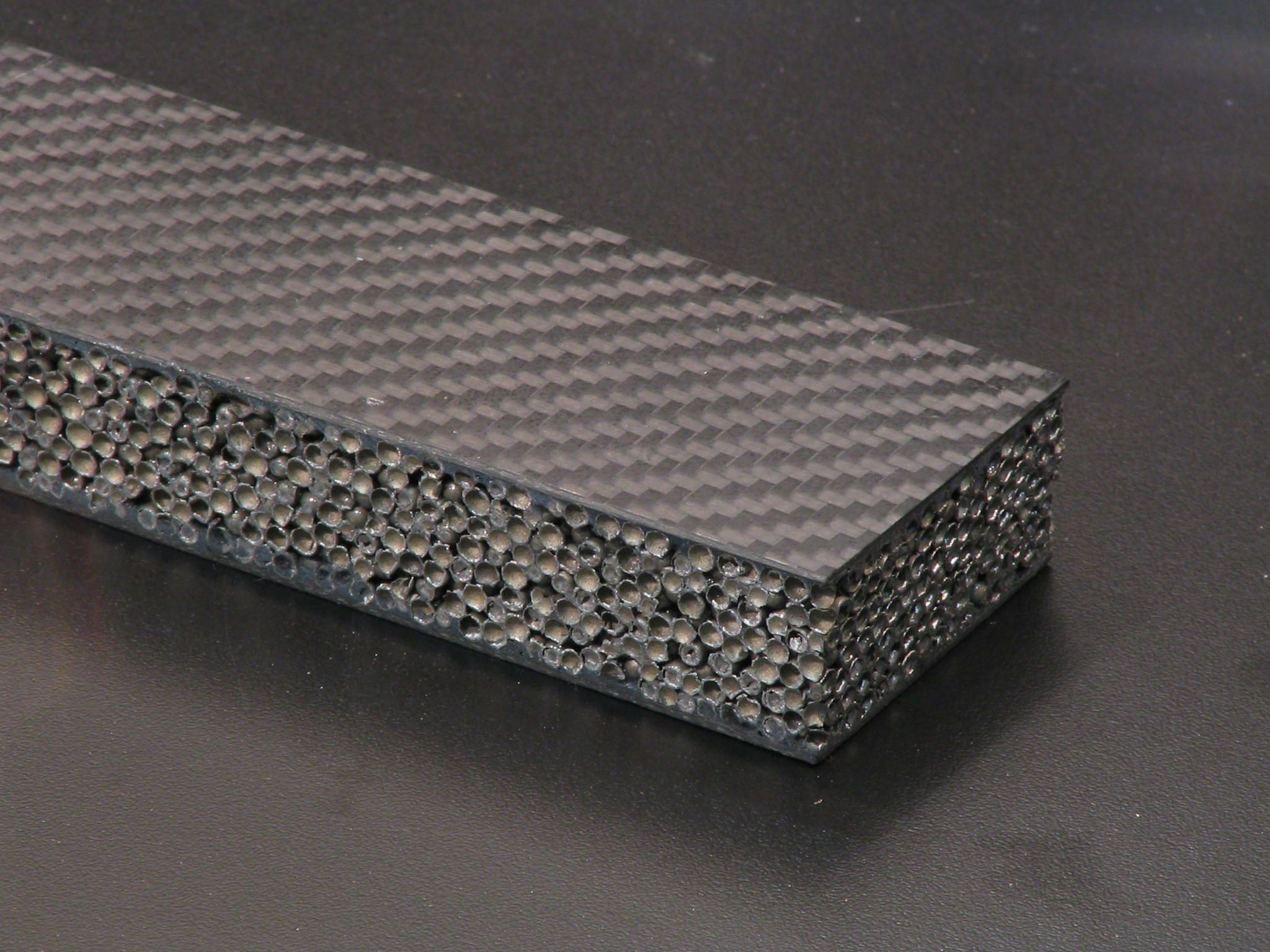
Гелькоут — соединение по составу очень похожее на смолу, оно тоже может быть на полиэфирной, эпоксидной или эпоксивинилэфирной основе. Если упрощенно, это густая смола с конкретным цветом. Гелькоут достаточно устойчив к поверхностным воздействиям. Закладывается в матрицу, как один из слоев монолитного корпуса.
Полиуретановая краска — тип краски, который хорошо защищает от внешних воздействий. Краска предлагает большой выбор цветов и стоит дороже. Наносится сверху на готовое изделие.
Как строят корпус
Чтобы построить яхту из композита, нужна матрица — форма, в которую будут выкладываться слои ткани и смолы, чтобы в итоге получился корпус. Можно сделать одну матрицу для всей нижней части корпуса — тогда он будет полностью монолитный. Можно сделать несколько маленьких матриц и производить детали по отдельности, а потом вручную собирать их в одно целое — такой метод используют при производстве больших корпусов длинной от 20 метров.В любом варианте укладывать слои и добиваться отвердевания можно разными способами.
- ручная формовка
- ручная формовка + вакуумное обжатие
- вакуумная инфузия
- запекание (prepeg)
Ручная формовка — самый трудоемкий и наименее технологичный метод. Рабочие вручную выкладывают ткань в матрицу и пропитывают ее смолой с помощью валика. Для упрощения работы есть специальный инструмент — чоппер. В него загружают смолу и рубленный стекломат, он соединяет внутри эти два компонента и распыляет их как бы из пистолета. Этот метод обычно используют для полиэфирной или эпоксивинилэфирной смолы. Вручную невозможно изготовить композитный сэндвич.
Минусы:
— итоговые изделия получаются тяжелыми из-за избытка смолы
— вручную трудно сделать весь корпус равномерным
Плюсы:
— дешево, просто, не требует специальных знаний и оборудования

Композитный сэндвич можно изготовить только с помощью метода вакуумного обжатия или вакуумной инфузии.
Минусы:
— трудозатратно, долго и дорого
— нужно специальное оборудование
Плюсы:
— метод дает гарантированный результат, трудно что-то испортить в процессе
Вакуумная инфузия — в этом случае все сухие компоненты сэндвича (кроме смолы) выкладываются в форму-матрицу. Потом матрицу накрывают специальным вакуумным мешком, который откачивает весь воздух и сжимает компоненты. Затем вместо вакуума в деталь подается смола. Благодаря вакууму удается максимально точно контролировать количество смолы, а значит производить детали минимального веса. Метод требует высококвалифицированных специалистов и сложного оборудования. Если в производственном процессе допустить ошибку, есть риск испортить весь корпус и все задействованные материалы.
Минусы:
— нужно специальное оборудование
— требует строителей высокой квалификации
Плюсы:
— безупречное качество корпуса при соблюдении технологии
— при работе с большими объектами выгоднее с точки зрения трудозатрат
Запекание (prepeg) — самый высокотехнологичный метод, используется исключительно при работе с углеволокном. Для него необходим специально оборудованный цех-печь, где можно четко контролировать температуру и влажность.
Корпус яхты изготавливают из особого вида углеткани, сразу пропитанной смолой. Такая ткань перевозится в холодильниках и имеет короткий срок хранения. Из нее вручную формуют корпус яхты при температуре около 18 градусов и влажности не больше 60%. Потом конструкция обжимается вакуумным мешком и целиком запекается при температуре около 100 градусов.
Этот метод позволяет создать максимально легкий и прочный корпус. Например, вес яхты длиной 72 фута без оснастки, оборудования и киля получается около 2700 кг. Запекание используют в строительстве самых быстрых в мире гоночных яхт.
Плюсы:
— минимальный вес корпуса при нужной прочности
Минусы:
— очень дорогие материалы
— сложный и трудоемкий технологический процесс
Какие материалы и технологии используют на верфи Pacifico
Создание корпуса на верфи Pacifico Yachts состоит из нескольких этапов. Для каждой модели есть своя матрица и свои особенности производственного процесса в зависимости от технического проекта и итоговых характеристик яхты.Поэтому разбирать этапы будем на конкретном примере — строительстве корпуса Pacifico Voyager 99. Нижняя часть корпуса этого проекта полностью монолитна, поэтому формуется в одной большой матрице.
Этап 1. Работа начинается с подготовки и полировки внутренней поверхности матрицы.
Этап 2. После подготовительных работ, наносят внешний слой — гелькоут. Мы используем гелькоут на полиэфирной основе и наносим его пистолетом.
Этап 3. После этого вручную формуется «корка» из стекломата и эпоксивинилэфирной смолы. «Корка» нужна для того, чтобы основной слой корпуса из эпоксидной смолы крепко соединился с полиэфирным гелькоутом.
Этап 4. После того, как сформирована «корка», начинается формовка основного слоя — вручную укладывается сухая основа композитного сэндвича: стеклоткань + ПХВ + углеткань. Плетение и направление ткани выкладывается строго в соответствии с техническим проектом.
Этап 5. Корпус формуется методом вакуумной инфузии: конструкция обтягивается вакуумный мешком, из детали откачивается воздух, затем подается эпоксидная смола.
Этап 6. Смола отвердевает в течение 24 часов, затем корпус извлекается из матрицы и на нем начинаются технические работы.
В результате мы получаем эпоксидный корпус из стеклопластика, армированный углеволокном. Композитный сэндвич с ПВХ добавляет поверхностной прочности — корпус легко выдерживает удар кувалдой или столкновение с камнем, но все еще остается достаточно легким. Сочетание этих технологий и материалов позволяет нам строить быстрые и относительно экономичные катамараны, но при этом сохранять адекватную стоимость конечного продукта.
В этой статье мы разобрали большинство материалов и технологий производства. От них во многом зависят качество и технические характеристики готовой лодки: скорость, экономичность, долговечность и, конечно, цена. Но важно понимать, что в этом деле нет черного и белого, нет однозначно правильных или неправильных подходов к производству — каждый из них отвечает определенной задаче.
Композиционные материалы в строительстве: виды, характеристики, свойства, преимущества и особенности
09.03.2016 14:00 | Категория: Материалы для ремонтаСтроительная индустрия постоянно развивается, открываются новые площадки, строятся различные объекты.
Композиционные материалы стали неотъемлемой частью этой сферы, сейчас уже трудно представить масштабные строительные работы без использования композита.
Стойкий, легкий и прочный, он имеет значительные преимущества перед природными материалами, обладающими большим весом и не имеющими значительных способностей к изменению формы.
Композиционные материалы в строительстве
Существуют разные типы композиционных материалов, они различаются по своему составу и свойствам. Наиболее распространены и востребованы в строительстве, например, такие виды, как сэндвич-панели, углепластиковые панели, слоистые материалы, текстолиты, стеклопластики. Все они обладают высокими эксплуатационными характеристиками и декоративным эффектом.
Композит применяется не только при возведении жилых объектов. Трудно представить мост или плотину, где бы не использовались углепластиковые панели. Различные архитектурные элементы, такие как арки или купола, тоже зачастую создаются с применением композиционных материалов. Это выгодно для застройщиков, поскольку обеспечивает им значительную экономию на возведении конструкций, монтаже, хранении и перевозке материала, и при этом надежность, качество и прочие эксплуатационные характеристики будущего здания никак не страдают.
Дизайнеры используют композит в моделизме. Оригинальные расцветки, возможность создавать необычные причудливые формы — все это можно увидеть, если рассмотреть всевозможные композиционные материалы на www.hccomposite.com. С такими ресурсами можно создавать действительно необычные архитектурные сооружения, которые будут еще и надежными и долговечными.
Виды, характеристики и свойства
Все композиционные материалы изготавливаются по похожей структуре — у них есть армирующее вещество и матрица. Арматура — это то, что передает материалу физические и химические свойства, является его основой. А матрица придает изделию форму, фиксируя арматуру определенным образом.
Можно выделить некоторые примеры самых распространенных в строительстве композитов:
- Бетоны.
Их матрица может быть как традиционной, цементной, так и созданной на основе новых технологий — полимерной. Разновидностей бетонов существует огромное множество, они отличаются своими свойствами и областью применения — от обычных до декоративных. Современные бетоны по своей прочности приближаются к металлическим конструкциям.
- Органопластические композиты. Их основным наполнителем являются синтетические волокна, изредка используются и природные материалы. Матрицей обычно служат различные смолы. Органопластики достаточно легкие, хорошо держат удар, сопротивляются динамическим нагрузкам, но при этом плохо выдерживают растяжения и сгибы. Древесные композиционные материалы также относятся к органопластикам по классификации.
- Стеклопластики армируются стеклянными волокнами, а в качестве формирующей матрицы для их изготовления применяют особые синтетические смолы или термопластичные виды полимеров. Материал обладает устойчивостью, прочностью, низкой теплопроводностью, но при этом свободно пропускает радиосигналы.
- Углепластики представляют собой соединение углеводородных волокон и различных полимеров. Обладают более высокой упругостью, чем стеклопластики, легкие и достаточно прочные.
- Текстолиты — это слоистые материалы, армированные тканями на основе различных волокон. Заготовки-полотна заранее пропитывают смолой, а затем прессуют с использованием режима высокой температуры, получая готовый к применению пласт. Поскольку наполнители могут быть очень разными, то и свойства значительно разнятся.
Преимущества, недостатки и применение
Поскольку композиты являются достаточно эффективными, применение в строительстве достаточно распространено благодаря ряду преимуществ этих материалов.
- Изделия получаются очень прочные, некоторые виды композиционных материалов, например, стеклопластики, по своей прочности способны соперничать с металлом. При этом они отличаются гибкостью и хорошо переносят различные воздействия.
- Композиты отличаются своей легкостью, по сравнению с аналогами.
Легкие балки, изготовленные из стекловолокна, гораздо лучше подходят для создания перекрытий в больших помещениях, чем металлические. Получившаяся конструкция не потеряет в прочности и качестве, но при этом требует гораздо меньших усилий во время проведения монтажных работ.
- Материалы отличаются высокой устойчивостью к воздействию агрессивной среды, поэтому из них можно создавать не только внутренние конструкции, но и использовать для внешних, открытых воздействию солнечных лучей, осадков и резкой смене температур.
- Химические реагенты не страшны композитным материалам, поэтому их можно использовать, например, для возведения складов, где будут храниться химикаты.
- Благодаря новым технологиям, современные композиты перестали быть пожароопасными, они не позволяют пламени распространиться, практически не дымят и не выделяют опасных ядовитых веществ.
У композитов есть не только преимущества, но и недостатки, которые сдерживают их распространение на строительном рынке.
- Высокая стоимость — основная проблема композиционных материалов. Для их изготовления необходимо специальное сырье и современное оборудование, поэтому и готовые изделия получаются достаточно дорогими.
- Материалы обладают гигроскопичностью, то есть, легко впитывают влагу, что ведет к дальнейшему разрушению. Поэтому их необходимо дополнительно укреплять при производстве влагостойкими защитными средствами.
- Некоторые композиционные материалы имеют низкую ремонтопригодность, что повышает стоимость их эксплуатации.
Композиционные материалы, как и любые другие, имеют свои достоинства и недостатки.
Насколько оправданным будет использование композитов? Зависит от конкретных целей, условий, общего бюджета. Впрочем, современные технологии позволяют изобретать новые формы и виды таких материалов, поэтому, возможно, в будущем они станут менее дорогими и более распространенными, а также обзаведутся улучшенными характеристиками.
Композитные материалы.
Полимерные композиционные материалы: методы получения.
их отличии от других, традиционных изделий
Без современных инновационных технологий невозможно создать новейшие решения в области строительства, а также в коммерческом и жилом строительстве, в реставрационных работах автомобильных дорог. Раньше в этих технологиях использовались изделия из стали, алюминия, железобетона, но на сегодняшний день нет ничего более современного, прочного и экологичного, чем синтетические композитные изделия из полимерных соединений.
Как правило, состав композитного материала включает в себя два трипа составляющих: связующее (матрица) или армирующий материал. Благодаря матрице изделие обеспечивается определенной формой и фиксирует армирующий материал. За счет этого матрица усиливается и передает свои свойства изделию. Подобное совмещение этих характеристик в веществах гарантированно создает принципиально новый композитный материал.
Тип
армирующего вещества определяет виды композитных материалов. По этой
характеристике они могут быть наполненными, иметь волокнистую, слоистую
структуру, а также быть насыпными и скелетными. Свойства, которыми обладает тот
или иной композитный материал зависит от сочетания физических, механических,
химических характеристик, которыми будет обладать матрица и армирующий
материал. Композитные материалы в последнее время стали очень популярными и
очень часто применяются в разных сферах. Это легко объяснить тем, что у этих
материалов есть целый ряд преимуществ, которые отличают их от других,
традиционных изделий.
К основным достоинствам композитных материалов относятся свойства, благодаря которым синтетические материалы обладают более высокой прочностью и устойчивостью к деформациям, разрывам, сжатиям, срезам и скручиваниям. Помимо этого, полимерные синтетические материалы являются более легкими по массе, удобными для транспортировки и установки. При этом есть хорошая возможность также и оптимизировать затраты на эти позиции.
Композит устойчив к химическому
воздействию агрессивной среды, атмосферные осадки ему тоже не повредят. Материал не боится резких перепадов температур, способен эффективно
использоваться в разных температурных режимах при неблагоприятных климатических
условиях. Ко всему перечисленному, можно сказать, что этот материал целиком
безопасен для окружающей среды и полностью соответствует всем экологическим
требованиям.
Особенности композитов.
Композитные материалы имеют свои особенности, которые очень выгодно отличают их среди традиционных стройматериалов. Новые материалы создаютсяблагодаря естественным стремлениям разработчиков улучшать характеристики конструкций, которые эксплуатируются в данный момент, а также тех, которые вводятся в эксплуатацию. Эти технологии, осваиваясь строителями, дают новую возможность для разработки более современных сооружений и технологий. Одним из максимально ярких проявлений особенностей разработки полимерных материалов, является тот факт, что композит очень широко применяется в разных областях строительства.
Композитные материалы можно весьма справедливо назвать сырьем для строительства двадцать первого века. Они имеют высочайшие физико-механические свойства при невысокой плотности. Они более крепкие, нежели стальные и алюминиевые сплавы.
Композитные материалы являются многосложными гетерогенными (разнородными) структурами, которые образовываются соединением армирующих элементов с изобтропным связующим. Армирующий элемент может иметь вид тонкого волокна, нити, жгута или ткани, обеспечивает физические свойства этого материала, который будет гарантированно прочным и жестким в направлении ориентации волокна, а матрица обеспечит цельность конструкции. Нынешние композитные материалы имеют удельную прочность и жесткость в направлении армирования, и этот показатель более, чем в 4 раза может превышать показатели стальной, алюминиевой арматуры и изделий из титановых сплавов.
При помощи внешней нагрузки на
материал в момент разрушения определяется прочность конструкции. Жесткостью или
модулем упругости называют характеристики материалов, которые определяют
смещение сооружений под воздействием внешнего напряжения. Эта характеристика
прямо пропорциональна явлению потери устойчивости сооружения, в момент, когда в
нем развиваются переменные значения и возникает большая нагрузка на основание.
В такие моменты несущая конструкция может быть разрушена. Удельной прочностью и
удельной жесткостью является отношение предельного напряжения к модулю
упругости в соответствии с плотностью материала. При более высоких удельных
свойствах материалов, конструкция будет более легкой и прочной и порог потери
устойчивости намного выше.
Для армирования материалов, как правило, используют высокопрочные волокна из стекла, базальта, арамида, углеродных, борных, органических соединений, а также из металлической проволоки и нитевидных кристаллов. Эти компоненты для армирования могут применяться в виде моноволокна, нити, проволоки, жгутов, а также ткани или сетки.
В композитном материале матрица является важнейшей составляющей, благодаря которой обеспечивается цельность композиции, фиксируется его форма и расположение армирующего волокна. Благодаря материалу матрицы можно обеспечить оптимальный метод изготовления элементов, а также выбрать соответствующий уровень рабочей температуры композита, стойкость к химическим раздражителям, поведение композита при влиянии атмосферных осадков и повышенных или пониженных температур.
Матрицей могут выступать материалы из эпоксидной, полиэфирной и некоторых других термореактивных, полимерных и термопластичных материалов. В композитных материалах волокнистой структуры, напряжение, которое возникает под воздействием внешних нагрузок, воспринимается высокопрочными волокнами. Они же и обеспечивают прочность сооружения по направлению армирования. Благодаря направленному характеру свойств композитных материалов, они имеют превосходные качества. Из композитных материалов могут создаваться конструкции со свойствами, заданными ранее и максимально соответствующие специфике и свойствам работ. Благодаря многообразию волокон и материалов для матрицы, а также схемы по котором происходит процесс армирования при создании композита, есть возможность целенаправленно производить регулирование прочности, жесткости, уровня рабочей температуры, химической стойкости и других свойств.
Широкие возможности технологического процесса производства материалов разных по форме определяют широкий ассортимент композитных материалов, которые можно сделать. При соблюдении всех технологий, необходимо применение специальных агрегатов и оборудования, оснастки и других станков. С помощью этой техники арматурные стержни можно гнуть в различных направлениях для самых нестандартных строительных решений.
В данном разделе мы можем подробно рассмотреть, что используется для изготовления композитных матери
Композитные материалы. Технология полимерных композиционных материалов.
Химическая промышленность во всем мире старается предложить своим клиентам новейшие разработки, которые нацелены на решение новых задач, возникающих из-за необходимости придания материалам уникальных функциональных свойств, которые формулируются благодаря бурному технологическому прогрессу во всех областях науки и техники.
Одним из основных направлений деятельности компании «ГАММА-ПЛАСТ» является производство полимерных материалов и добавок, а также разработка и производство композиционных материалов.
Современный рынок пластических масс предлагает своим потребителям огромное количество разнообразных полимерных материалов. Причина в том, что полимеры крайне популярны среди производителей, которые работают в различных областях, начиная с производства высокоточного электрооборудования, заканчивая мебельной фурнитурой, благодаря своим уникальным свойствам – низкая плотность, высокая удельная прочность, высокая химическая стойкость, хорошие диэлектрические характеристики и т.д.
На российском рынке представлено много компаний, которые специализируются на переработке полимеров. Именно поэтому прежде чем осуществить закупку, необходимо убедиться в надежности поставщика и качестве материала. Ведь от этого зависит Ваша репутация перед конечным потребителем продукции.
Наша компания уже более 10 лет занимает лидирующие позиции на отечественном рынке производства полимерных компаундов. Мы наладили нашу бизнес-структуру таким образом, чтобы наши клиенты могли чувствовать себя максимально комфортно в работе с нами. Мы организовали производственные цеха, офисы и лаборатории на территории Москвы. Это позволяет нам оперативно реагировать на все ваши пожелания и даже самые сложные запросы мы готовы решать в самые короткие сроки.
ПРЕИМУЩЕСТВА
Основным нашим конкурентным преимуществом является то, что мы изготавливаем полимерные композиционные материалы с теми свойствами, которые необходимы именно Вам.
Композиционные материалы представляют собой искусственно созданные материалы, состоящие из двух и более компонентов, между которыми имеется граница раздела, то есть образуется минимум двухфазная система. В этой системе полимер выступает в роли связующего (матрицы), а наполнитель в роли упрочняющего (армирующего) компонента или функционального наполнителя. Данные материалы обладают уникальными свойствами, которые проектируются специалистами под техническое задание заказчика.
Огромное количество современных научных центров экспериментируют с созданием новых композитных материалов. Цель – создать новые более дешевые и удобные материалы, которые будут соответствовать запросам нынешнего рынка.
ВИДЫ КОМПОЗИЦИОННЫХ МАТЕРИАЛОВ
Полимерные композиционные материалы, как следует из названия, обладают полимерной матрицей. Арматурой могут служить: стеклотекстолит, ткани, пленки и т.д. Существует несколько видов формирования полимерных композиций, среди которых литье под давлением, напыление, прессование, экструзия.
На нашем сайте представлены следующие основные виды композиционных материалов:
• катализатор сшивки;
• ABS PC пластик;
• Композиция ПК/ПБТ.
Катализатор сшивки получил широкое распространение в изготовлении кабельных оболочек и термоусаживаемых соединительных кабельных муфт.
Дело в том, что кабель где данный материал используется в качестве изоляции имеет большую пропускную способность за счет того, что увеличивается температура жилы. По сравнению с кабелями с бумажной изоляцией этот показатель может возрастать на 15-30%. Также можно выделить еще ряд преимуществ использования катализатора сшивки при производстве кабелей:
• высокая термическая устойчивость при коротком замыкании;
• меньший радиус изгиба;
• повышенная стойкость к физическому воздействию;
• небольшие габариты и масса кабеля;
• повышенный показатель влагостойкости;
• сокращение расходов на содержание кабелей;
• пониженные диэлектрические потери.
ABS PC пластик является аморфным ударопрочным материалом. Данный материал характеризуется гораздо большей теплостойкостью, чем АБС. Такая высокая теплостойкость достигается благодаря введению поликарбоната. ABS PC может выдерживать кратковременный нагрев от 130 до 145 градусов. Также, необходимо отметить высокую морозостойкость и ударопрочность.
Кроме того, ABS PC обладает хорошей химической стойкостью. Данный материал отлично перерабатывается, рекомендован для точного литься. Кроме того, он великолепно сваривается.
ПК/ПБТ является высокопрочным, химически стойким материалом. Наша компания предлагает вам самим определиться с цветом и содержанием стеклянного волокна в данном материале. Данный композиционный материал обладает повышенной химической стойкостью благодаря введению полибутилентерефталата.
ПРИМЕНЕНИЕ
Как можно понять, полимерные композиционные материалы применяются повсеместно. Среди основных областей применения можно выделить:
Строительство;
Сельское хозяйство;
Электроника;
Медицина;
Изделия бытового назначения;
И многое-многое другое 123.
Представленные на нашем сайте виды полимерных композиционных материалов обладают рядом характеристик, которые обуславливают широкую популярность. Среди этих качеств можно выделить следующие:
• высокая химическая стойкость;
• термостойкость;
• устойчивость к воздействию статических и вибрационных нагрузок.
ПРОИЗВОДСТВО КОМПОЗИЦИОННЫХ МАТЕРИАЛОВ
Производимые нами материалы уже заслужили доверие десятков клиентов со всей страны. Причиной тому является качество производимой нами продукции, которое подтверждается не только примерами доверия, но и специальной документацией.
Компания «ГАММА-ПЛАСТ» занимает ключевые позиции среди российских предприятий, которые специализируются на производстве ПКМ. Мы обладаем широкой материально-технической базой, которая позволяет предоставлять нашим клиентам услуги на высшем уровне качества. Мы готовы оперативно реагировать даже на самые сложные клиентские запросы.
Именно поэтому, если вы хотите купить композиционные материалы, звоните нам или заполните форму на нашем сайте. Наши высококвалифицированные специалисты свяжутся с вами в ближайшее время и помогут оформить ваш заказ, а также ответят на все интересующие вас вопросы.
Среди большинства материалов наиболее популярными и широко известными являются полимерные композиционные материалы (ПКМ). Они активно применяются практически в каждой сфере человеческой деятельности. Именно данные материалы являются основным компонентом для изготовления различных изделий, применяемых с абсолютно разными целями, начиная от удочек и корпусов лодок, и заканчивая баллонами для хранения и транспортировки горючих веществ, а также лопастей винтов вертолетов. Такая широкая популярность ПКМ связана с возможностью решения технологических задач любой сложности, связанных с получением композитов, и
Композитные материалы Википедия
Композиты формируются путем объединения разнородных материалов в общую структуру, свойства которой сильно отличаются от свойств отдельных компонентов Обычная клеёная фанера является широко распространённым композитным материаломКомпозитный материа́л (КМ), компози́т — многокомпонентный материал, изготовленный из двух или более компонентов с существенно различными физическими и/или химическими свойствами, которые, в сочетании, приводят к появлению нового материала с характеристиками, отличными от характеристик отдельных компонентов и не являющимися простой их суперпозицией. При этом отдельные компоненты остаются таковыми в структуре композитов, отличая их от смесей и твёрдых растворов. В составе композита принято выделять матрицу/матрицы и наполнитель/наполнители. Варьируя состав матрицы и наполнителя, их соотношение, ориентацию наполнителя, получают широкий спектр материалов с требуемым набором свойств. Многие композиты превосходят традиционные материалы и сплавы по своим механическим свойствам и в то же время они легче. Использование композитов обычно позволяет уменьшить массу конструкции при сохранении или улучшении её механических характеристик.
Структура композитных материалов
По структуре композиты делятся на несколько основных классов: волокнистые, дисперсноупрочнённые, упрочнённые частицами и нанокомпозиты. Волокнистые композиты армированы волокнами или нитевидными кристаллами — кирпичи с соломой и папье-маше можно отнести как раз к этому классу композитов. Уже небольшое содержание наполнителя в композитах такого типа приводит к появлению качественно новых механических свойств материала. Широко варьировать свойства материала позволяет также изменение ориентации размера и концентрации волокон. Кроме того, армирование волокнами придаёт материалу анизотропию свойств (различие свойств в разных направлениях), а за счёт добавки волокон проводников можно придать материалу электропроводность вдоль заданной оси.
В слоистых композиционных материалах матрица и наполнитель расположены слоями, как, например, в особо прочном стекле, армированном несколькими слоями полимерных плёнок.
Микроструктура остальных классов композиционных материалов характеризуется тем, что матрицу наполняют частицами армирующего вещества, а различаются они размерами частиц. В композитах, упрочнённых частицами, их размер больше 1 мкм, а содержание составляет 20—25 % (по объёму), тогда как дисперсноупрочненные композиты включают в себя от 1 до 15 % (по объёму) частиц размером от 0,01 до 0,1 мкм. Размеры частиц, входящих в состав нанокомпозитов — нового класса композиционных материалов — ещё меньше и составляют 10—100 нм.
Полимерные композитные материалы (ПКМ)
Композиты, в которых матрицей служит полимерный материал, являются одним из самых многочисленных и разнообразных видов материалов. Их применение в различных областях даёт значительный экономический эффект. Например, использование ПКМ при производстве космической и авиационной техники позволяет сэкономить от 5 до 30 % веса летательного аппарата. А снижение веса, например, искусственного спутника на околоземной орбите на 1 кг приводит к экономии 1000$. В качестве наполнителей ПКМ используется множество различных веществ.
А) Стеклопластики — полимерные композиционные материалы, армированные стеклянными волокнами, которые формируют из расплавленного неорганического стекла. В качестве матрицы чаще всего применяют как термореактивные синтетические смолы (фенольные, эпоксидные, полиэфирные и так далее), так и термопластичные полимеры (полиамиды, полиэтилен, полистирол и так далее). Эти материалы обладают достаточно высокой прочностью, низкой теплопроводностью, высокими электроизоляционными свойствами, кроме того, они прозрачны для радиоволн. Использование стеклопластиков началось в конце Второй мировой войны для изготовления антенных обтекателей — куполообразных конструкций, в которых размещается антенна локатора. В первых армированных стеклопластиках количество волокон было небольшим, волокно вводилось, главным образом, чтобы нейтрализовать грубые дефекты хрупкой матрицы. Однако со временем назначение матрицы изменилось — она стала служить только для склеивания прочных волокон между собой, содержание волокон во многих стеклопластиках достигает 80 % по массе. Слоистый материал, в котором в качестве наполнителя применяется ткань, плетённая из стеклянных волокон, называется стеклотекстолитом.
Стеклопластики — достаточно дешёвые материалы, их широко используют в строительстве, судостроении, радиоэлектронике, производстве бытовых предметов, спортивного инвентаря, оконных рам для современных стеклопакетов и так далее.
Б) Углепластики — наполнителем в этих полимерных композитах служат углеродные волокна. Углеродные волокна получают из синтетических и природных волокон на основе целлюлозы, сополимеров акрилонитрила, нефтяных и каменноугольных пеков и так далее. Термическая обработка волокна проводится, как правило, в три этапа (окисление — 220° С, карбонизация — 1000—1500° С и графитизация — 1800—3000° С) и приводит к образованию волокон, характеризующихся высоким содержанием (до 99,5 % по массе) углерода. В зависимости от режима обработки и исходного сырья полученное углеволокно имеет различную структуру. Для изготовления углепластиков используются те же матрицы, что и для стеклопластиков — чаще всего — термореактивные и термопластичные полимеры. Основными преимуществами углепластиков по сравнению со стеклопластиками является их низкая плотность и более высокий модуль упругости, углепластики — очень лёгкие и, в то же время, прочные материалы. Углеродные волокна и углепластики имеют практически нулевой коэффициент линейного расширения. Все углепластики хорошо проводят электричество, чёрного цвета, что несколько ограничивает области их применения. Углепластики используются в авиации, ракетостроении, машиностроении, производстве космической техники, медтехники, протезов, при изготовлении лёгких велосипедов и другого спортивного инвентаря.
На основе углеродных волокон и углеродной матрицы создают композитные углеграфитовые материалы — наиболее термостойкие композитные материалы (углепластики), способные долго выдерживать в инертных или восстановительных средах температуры до 3000° С. Существует несколько способов производства подобных материалов. По одному из них углеродные волокна пропитывают фенолформальдегидной смолой, подвергая затем действию высоких температур (2000° С), при этом происходит пиролиз органических веществ и образуется углерод. Чтобы материал был менее пористым и более плотным, операцию повторяют несколько раз. Другой способ получения углеродного материала состоит в прокаливании обычного графита при высоких температурах в атмосфере метана. Мелкодисперсный углерод, образующийся при пиролизе метана, закрывает все поры в структуре графита. Плотность такого материала увеличивается по сравнению с плотностью графита в полтора раза. Из углепластиков делают высокотемпературные узлы ракетной техники и скоростных самолётов, тормозные колодки и диски для скоростных самолётов и многоразовых космических кораблей, электротермическое оборудование.
В) Боропластики — композитные материалы, содержащие в качестве наполнителя борные волокна, внедрённые в термореактивную полимерную матрицу, при этом волокна могут быть как в виде мононитей, так и в виде жгутов, оплетённых вспомогательной стеклянной нитью или лентой, в которых борные нити переплетены с другими нитями. Благодаря большой твёрдости нитей, получающийся материал обладает высокими механическими свойствами (борные волокна имеют наибольшую прочность при сжатии по сравнению с волокнами из других материалов) и большой стойкостью к агрессивным условиям, но высокая хрупкость материала затрудняет их обработку и накладывает ограничения на форму изделий из боропластиков. Кроме того, стоимость борных волокон очень высока (порядка 400 $/кг) в связи с особенностями технологии их получения (бор осаждают из хлорида на вольфрамовую подложку, стоимость которой может достигать до 30 % стоимости волокна). Термические свойства боропластиков определяются термостойкостью матрицы, поэтому рабочие температуры, как правило, невелики.
Применение боропластиков ограничивается высокой стоимостью производства борных волокон, поэтому они используются главным образом в авиационной и космической технике в деталях, подвергающихся длительным нагрузкам в условиях агрессивной среды.
Г) Органопластики — композиты, в которых наполнителями служат органические, синтетические и реже — природные и искусственные волокна в виде жгутов, нитей, тканей, бумаги и так далее. В термореактивных органопластиках матрицей служат, как правило, эпоксидные, полиэфирные и фенольные смолы, а также полиимиды. Материал содержит 40—70 % наполнителя. Содержание наполнителя в органопластиках на основе термопластичных полимеров — полиэтилена, ПВХ, полиуретана и так далее — варьируется в значительно больших пределах — от 2 до 70 %. Органопластики обладают низкой плотностью, они легче стекло- и углепластиков, относительно высокой прочностью при растяжении; высоким сопротивлением удару и динамическим нагрузкам, но, в то же время, низкой прочностью при сжатии и изгибе.
Важную роль в улучшении механических характеристик органопластика играет степень ориентации макромолекул наполнителя. Макромолекулы жесткоцепных полимеров, таких, как полипарафенилтерефталамид (кевлар) в основном ориентированы в направлении оси полотна и поэтому обладают высокой прочностью при растяжении вдоль волокон. Из материалов, армированных кевларом, изготавливают пулезащитные бронежилеты.
Органопластики находят широкое применение в авто-, судо-, машиностроении, авиа- и космической технике, радиоэлектронике, химическом машиностроении, производстве спортивного инвентаря и так далее.
Д) Полимеры, наполненные порошками. Известно более 10000 марок наполненных полимеров. Наполнители используются как для снижения стоимости материала, так и для придания ему специальных свойств. Впервые наполненный полимер начал производить доктор Бейкеленд (Leo H.Baekeland, США), открывший в начале 20 в. способ синтеза фенолформальдегидной (бакелитовой) смолы. Сама по себе эта смола — вещество хрупкое, обладающее невысокой прочностью. Бейкеленд обнаружил, что добавка волокон, в частности, древесной муки к смоле до её затвердевания, увеличивает её прочность. Созданный им материал — бакелит — приобрёл большую популярность. Технология его приготовления проста: смесь частично отверждённого полимера и наполнителя — пресс-порошок — под давлением необратимо затвердевает в форме. Первое серийное изделие произведено по данной технологии в 1916, это — ручка переключателя скоростей автомобиля «Роллс-Ройс». Наполненные термореактивные полимеры широко используются по сей день.
Сейчас применяются разнообразные наполнители как термореактивных, так и термопластичных полимеров. Карбонат кальция и каолин (белая глина) дёшевы, запасы их практически неограничены, белый цвет даёт возможность окрашивать материал. Применяют для изготовления жёстких и эластичных поливинилхлоридных материалов для производства труб, электроизоляции, облицовочных плиток и так далее, полиэфирных стеклопластиков, наполнения полиэтилена и полипропилена. Добавление талька в полипропилен существенно увеличивает модуль упругости и теплостойкость данного полимера. Сажа больше всего используется в качестве наполнителя резин, но вводится и в полиэтилен, полипропилен, полистирол и так далее. По-прежнему широко применяют органические наполнители — древесную муку, молотую скорлупу орехов, растительные и синтетические волокна. Большую популярность приобрел полимерно-песчаный композит на основе полиэтиленов с наполнителем из речного песка. Для создания биоразлагающихся композитов в качестве наполнителя используют крахмал.
Е) Текстолиты — слоистые пластики, армированные тканями из различных волокон. Технология получения текстолитов была разработана в 1920-х на основе фенолформальдегидной смолы. Полотна ткани пропитывали смолой, затем прессовали при повышенной температуре, получая текстолитовые пластины. Роль одного из первых применений текстолитов — покрытия для кухонных столов — трудно переоценить.
Основные принципы получения текстолитов сохранились, но сейчас из них формуют не только пластины, но и фигурные изделия. И, конечно, расширился круг исходных материалов. Связующими в текстолитах является широкий круг термореактивных и термопластичных полимеров, иногда даже применяются и неорганические связующие — на основе силикатов и фосфатов. В качестве наполнителя используются ткани из самых разнообразных волокон — хлопковых, синтетических, стеклянных, углеродных, асбестовых, базальтовых и так далее. Соответственно разнообразны свойства и применение текстолитов.
Композитные материалы с металлической матрицей
При создании композитов на основе металлов в качестве матрицы применяют алюминий, магний, никель, медь и так далее. Наполнителем служат или высокопрочные волокна, или тугоплавкие, не растворяющиеся в основном металле частицы различной дисперсности.
Свойства дисперсноупрочненных металлических композитов изотропны — одинаковы во всех направлениях. Добавление 5-10% армирующих наполнителей (тугоплавких оксидов, нитридов, боридов, карбидов) приводит к повышению сопротивляемости матрицы нагрузкам. Эффект увеличения прочности сравнительно невелик, однако ценно увеличение жаропрочности композита по сравнению с исходной матрицей. Так, введение в жаропрочный хромоникелевый сплав тонкодисперсных порошков оксида тория или оксида циркония позволяет увеличить температуру, при которой изделия из этого сплава способны к длительной работе, с 1000° С до 1200° С. Дисперсноупрочненные металлические композиты получают, вводя порошок наполнителя в расплавленный металл, или методами порошковой металлургии.
Армирование металлов волокнами, нитевидными кристаллами, проволокой значительно повышает как прочность, так и жаростойкость металла. Например, сплавы алюминия, армированные волокнами бора, можно эксплуатировать при температурах до 450—500° С, вместо 250—300° С. Применяют оксидные, боридные, карбидные, нитридные металлические наполнители, углеродные волокна. Керамические и оксидные волокна из-за своей хрупкости не допускают пластическую деформацию материала, что создаёт значительные технологические трудности при изготовлении изделий, тогда как использование более пластичных металлических наполнителей позволяет переформование. Получают такие композиты пропитыванием пучков волокон расплавами металлов, электроосаждением, смешением с порошком металла и последующим спеканием и так далее.
В 1970-х появились первые материалы, армированные нитевидными монокристаллами («усами»). Нитевидные кристаллы получают, протягивая расплав через фильеры. Используются «усы» оксида алюминия, оксида бериллия, карбидов бора и кремния, нитридов алюминия и кремния и так далее длиной 0,3—15 мм и диаметром 1-30 мкм. Армирование «усами» позволяет значительно увеличить прочность материала и повысить его жаростойкость. Например, предел текучести композита из серебра, содержащего 24% «усов» оксида алюминия, в 30 раз превышает предел текучести серебра и в 2 раза — других композиционных материалов на основе серебра. Армирование «усами» оксида алюминия материалов на основе вольфрама и молибдена вдвое увеличило их прочность при температуре 1650° С, что позволяет использовать эти материалы для изготовления сопел ракет.
Композитные материалы на основе керамики
Армирование керамических материалов волокнами, а также металлическими и керамическими дисперсными частицами позволяет получать высокопрочные композиты, однако, ассортимент волокон, пригодных для армирования керамики, ограничен свойствами исходного материала. Часто используют металлические волокна. Сопротивление растяжению растёт незначительно, но зато повышается сопротивление тепловым ударам — материал меньше растрескивается при нагревании, но возможны случаи, когда прочность материала падает. Это зависит от соотношения коэффициентов термического расширения матрицы и наполнителя.
Армирование керамики дисперсными металлическими частицами приводит к новым материалам (керметам) с повышенной стойкостью, устойчивостью относительно тепловых ударов, с повышенной теплопроводностью. Из высокотемпературных керметов делают детали для газовых турбин, арматуру электропечей, детали для ракетной и реактивной техники. Твёрдые износостойкие керметы используют для изготовления режущих инструментов и деталей. Кроме того, керметы применяют в специальных областях техники — это тепловыделяющие элементы атомных реакторов на основе оксида урана, фрикционные материалы для тормозных устройств и так далее.
Керамические композитные материалы получают методами горячего прессования (таблетирование с последующим спеканием под давлением) или методом шликерного литья (волокна заливаются суспензией матричного материала, которая после сушки также подвергается спеканию).
Примечания
Литература
- Кербер М. Л., Полимерные композиционные материалы. Структура. Свойства. Технологии. — СПб.: Профессия, 2008. — 560 с.
- Васильев В. В., Механика конструкций из композиционных материалов. — М.: Машиностроение, 1988. — 272 с.
- Карпинос Д. М., Композиционные материалы. Справочник. — Киев, Наукова думка
- СП 164.1325800.2014 Усиление железобетонных конструкций композитными материалами. Правила проектирования.
- Техническое заключение по результатам лабораторных испытаний арматурных выпусков из стеклопластика, установленных в монолитный бетон, на действие продольных относительно оси выпуска усилий // Tekhnicheskoe zaklyuchenie po rezul’tatam laboratornyh ispytaniy armaturnyh vypuskov iz stekloplastika, ustanovlennyh v monolitnyy beton, na deystvie prodol’nyh otnositel’no osi vypuska usiliy
- Высокопрочные системы усиления ITECWRAP/ITECRESIN. Екатеринбург: ООО НИИ Высокопрочные системы усиления ИНТЕР/ТЭК, 2010. 69 с. // Vysokoprochnye sistemy usileniya ITECWRAP/ITECRESIN. Yekaterinburg: OOO NII Vysokoprochnye sistemy usileniya INTER/TEK, 2010. 69.
- Коршунов, Я. Бурейская ГЭС: сверхпроектные работы/ Я. Коршунов // Газета «Вестник РусГидро».№ 4 — 2014. С.8. // Korshunov, Ya. Bureyskaya GES: sverhproektnye raboty/Ya. Korshunov//Gazeta «Vestnik RusGidro» #4-2014. P.8
- Усиление железобетонных конструкций (Пособие П 1-98 к СНиП 2.03.01-84*). Минск, 1998. // Usilenie zhelezobetonnyh konstrukciy (Posobie P 1-98 k SNiP 2.03.01-84*). Minsk, 1998.
- Хозин В. Г., Пискунов А. А., Гиздатуллин А. Р., Куклин А. Н.//Сцепление полимеркомпозитной арматуры с цементным бетоном / Известия КГАСУ № 1(23) — 2013. С.1-8
- Хозин В. Г., Пискунов А. А., Гиздатуллин А. Р., Куклин А. Н.//Сцепление полимеркомпозитной арматуры с цементным бетоном / Известия КГАСУ № 1(23) — 2013. С. 1-9
Ссылки
Что такое композиты? — Композиты 101
Проще говоря, композиты — это комбинация компонентов. В нашей отрасли композиты — это материалы, изготовленные из двух или более природных или искусственных элементов (с разными физическими или химическими свойствами), которые сильнее в команде, чем в индивидуальном исполнении. Материалы компонентов не смешиваются полностью и не теряют своей индивидуальности; они объединяют и вносят свои самые полезные черты для улучшения результата или конечного продукта. Композиты обычно разрабатываются с учетом конкретного использования, такого как дополнительная прочность, эффективность или долговечность.
Композиты, также известные как композиты из армированного волокном полимера (FRP), изготавливаются из полимерной матрицы, армированной искусственным, искусственным или натуральным волокном (например, стекло, углерод или арамид) или другим армирующим материалом. Матрица защищает волокна от воздействия окружающей среды и внешних повреждений и передает нагрузку между волокнами. Волокна, в свою очередь, обеспечивают прочность и жесткость, укрепляя матрицу и помогая ей противостоять трещинам и изломам.
Во многих продуктах нашей отрасли полиэфирная смола является матрицей, а стекловолокно — армированием.Но в композитах используется множество комбинаций смол и армирования, и каждый материал вносит свой вклад в уникальные свойства готового продукта: волокно, мощное, но хрупкое, обеспечивает прочность и жесткость, а более гибкая смола придает форму и защищает волокно. Композиты FRP могут также содержать наполнители, добавки, материалы сердцевины или отделки поверхности, предназначенные для улучшения производственного процесса, внешнего вида и характеристик конечного продукта.
Композиты могут быть натуральными или синтетическими.Дерево, природный композит, представляет собой комбинацию целлюлозных или древесных волокон и вещества, называемого лигнином. Волокна придают дереву прочность; лигнин — это матрица или природный клей, который связывает и стабилизирует их. Другие композиты являются синтетическими (искусственными).
Фанера — это искусственный композит, в котором сочетаются натуральные и синтетические материалы. Тонкие слои шпона склеиваются вместе с помощью клея, образуя плоские листы ламинированной древесины , которые прочнее натурального дерева.
Не все пластмассы являются композитами.Фактически, большинство пластиков — из тех, что используются в игрушках, бутылках с водой и других привычных предметах — представляют собой композиты , а не . Это чистый пластик. Но многие виды пластика можно усилить, чтобы сделать их прочнее. Такое сочетание пластика и армирования позволяет производить одни из самых прочных и универсальных материалов (для своего веса), когда-либо разработанных технологиями.
Полимерные смолы (например, полиэфирные, винилэфирные, эпоксидные или фенольные) иногда называют пластиком.
Для определения композитов FRP используется множество терминов.Модификаторы использовались для идентификации определенного волокна, такого как полимер, армированный стекловолокном (GFRP), полимер, армированный углеродным волокном (CFRP), и полимер, армированный арамидным волокном (AFRP). Другой известный термин — это пластмассы, армированные волокном. Кроме того, с годами были разработаны и другие сокращения, и их использование зависело от географического положения или рынка. Например, композиты, армированные волокном (FRC), стеклопластики (GRP) и композиты с полимерной матрицей (PMC), можно найти во многих источниках.Каждый из вышеупомянутых терминов означает одно и то же: композиты FRP.
Композитные материалы — определение композитных материалов по The Free Dictionary
Ирвинг, Техас, 18 декабря 2014 г. — (PR.com) — Композитные материалы в основном используются во внутренних и внешних компонентах в мировой железнодорожной отрасли. Согласно соглашению, Strata передает на аутсорсинг центральную функцию в обработке композитных материалов для производства. обтекателей направляющих закрылков A380 на PCT. Производство композитных деталей требует процесса резки, формовки и отверждения современных композитных материалов, а не использования металлических компонентов.Композитные материалы, армированные волокнами, были объектом постоянных исследований из-за сочетания свойств, которые они представляют; нейлон — это тип волокна, используемого в качестве армирующего материала в композитных материалах, особенно в броне коммерческих и военных транспортных средств, из-за его подходящих свойств, таких как прочность на механическое напряжение, модуль упругости, твердость, способность поглощать энергию удара, термостойкость и низкая плотность [ 1] Особые свойства нейлона обусловлены его молекулярной структурой, разработанной в процессе производства, особенно в процессе прядения нити, когда молекулярные цепи выровнены, оставаясь параллельными оси волокон, что увеличивает кристалличность материала и, следовательно, , его механическая прочность [2] [3].Конечно-элементный анализ композитных материалов с использованием ANSYS, 2-е издание Предприятие, получившее название Samsung SGL Carbon Composite Materials, будет базироваться в Ульсане, на предприятии Samsung Petrochemical, с офисом маркетинга и продаж A в Сеуле, Южная Корея. 16 июля одобрил предложение о приобретении Umeco, британского производителя и дистрибьютора современных композитных материалов, американской компанией Cytec, специализирующейся на химии и материалах. Глава производственной академии Airbus в Великобритании Гейнор Грин заявил: «Авиакомпании требуя более экономичных и легких самолетов, а композитные материалы представляют собой легкую, но надежную альтернативу традиционным материалам, используемым в производстве самолетов.Композиционные материалы широко используются в авиационной и космической технике; автомобильный, железнодорожный и водный транспорт; и другие типы оборудования из-за ряда преимуществ композитных материалов. Композитные материалы состоят из армирования и матрицы, двух материалов, которые в сочетании работают лучше, чем любой из них, используемый по отдельности. Технология композитных материалов; приложения нейронных сетей. Royal Ten Cate (TenCate) (Euronext: KTC) (Другой OTC: KNKCF.PK), голландская компания, которая разрабатывает и производит передовые композитные материалы для космической и аэрокосмической промышленности, сообщила 7 апреля, что производитель самолетов Airbus недавно продлил Меморандум о взаимопонимании с TenCate, Stork Fokker AESP и Нидерландской аэрокосмической группой в отношении композитных материалов.Руководство по композитам — Exel Composites
- Используйте следующие ссылки для быстрого перехода к разделам веб-сайта
- Перейти к поиску по сайту
- Перейти к навигации по сайту
- Перейти к содержанию
Поиск Поиск
Поиск
Купить онлайн- О нас
- Наша компания
- Люди и культура
- Карьера
- Сертификаты
- Устойчивое развитие
- Кодекс поведения
- Кодекс поведения поставщика
- Композитные решения
- Композитные решения
- Транспорт
- Транспорт
- Автобусы
- Профиль для поездов и трамваев
- Профили для грузовиков и прицепов
- Композиты для автомобильных профилей
- Композиты в ветроэнергетике
- Здание из композитов
- Дом из композитов
- Профили оконные и дверные композитные
- Конструкционные композиты из стекловолокна
- Солнцезащитные козырьки, зонты и навесы
- Инфраструктура
- Инфраструктура
- Композитные хрупкие опорные конструкции
- Системы очистки воды и сточных вод
- Передача и распределение коммунальной энергии
- Композитные рельсовые решения
- Оборона
- Композиты в телекоммуникационных приложениях
- Машинное и электрическое оборудование
- Оборудование и другие отрасли
- Оборудование и другие отрасли промышленности
- Трубки композитные
- Опоры телескопические композитные
- Ручки инструментальные композитные
- Композиты в сельском хозяйстве
- Нефть и газ
- Спортивные товары композитные
- Композиты в фотографиях
- Примеры из практики
- Новости компании
- События и аналитика
- Новости компании
- Центр знаний
- Центр знаний
- Вторичная обработка
- Эстетика
- Руководство по композитам
- Руководство по композитам
- Заводской ремонт
- Методы изготовления
Руководство по композитным материалам: армирование — NetComposites
Роль армирования в композитном материале заключается в улучшении механических свойств чистой полимерной системы.Все различные волокна, используемые в композитах, имеют разные свойства и поэтому по-разному влияют на свойства композитов. Свойства и характеристики обычных волокон описаны ниже.
Однако отдельные волокна или пучки волокон могут использоваться только сами по себе в некоторых процессах, таких как намотка волокон (описанных ниже). Для большинства других применений волокна должны быть скомпонованы в лист какой-либо формы, известный как ткань, чтобы можно было манипулировать им. Различные способы сборки волокон в листы и разнообразие возможных ориентаций волокон приводят к тому, что существует множество различных типов тканей, каждый из которых имеет свои особенности.Эти различные типы тканей и конструкции будут объяснены позже.
Опубликовано с разрешения Дэвида Криппса, Gurit
Start
Ткань для развязки
Эти ткани обеспечивают сверхлегкое усиление ткани для композитных материалов.
Узнать большеСвойства волокна
Охватывает механические свойства армирующих волокон.
Узнать большеСвойства ламината
Охватывает механические свойства волокон с точки зрения прочности и жесткости.
Узнать большеУдарный ламинат
Обращает внимание на проблемы, вызванные ударным повреждением.
Узнать большеСтоимость волокна
Графическая информация о стоимости различных типов волокон.
Узнать большеСтекловолокно
Объясняет, как формируется стекловолокно и какие варианты доступны.
Узнать большеАрамидное волокно
Объясняет, как производится арамид и его различные торговые наименования.
Узнать большеУглеродное волокно
Объясняет производственные процессы, связанные с изготовлением углеродного волокна.
Узнать большеСравнение волокон
Обозначает преимущества и недостатки типов волокон.
Узнать большеВолокна прочие
Охватывает несколько других широко используемых типов волокон.
Узнать большеВолокнистая отделка
Объясняет различные виды обработки поверхности волокон.
Узнать большеКалибровочная химия
Обзор химического состава проклейки и матрицы, подлежащей усилению.
Узнать большеТипы тканей
Объясняет типы волокна, категории ориентации волокна и методы построения.
Узнать большеТкани
Объясняет обычно используемые типы переплетений.
Узнать большеГибридные ткани
Объясняет, что подразумевается под термином «гибридная ткань».
Узнать большеМультиаксиальные ткани
Объясняет основные характеристики мультиаксиальных тканей.
Узнать большеПрочие ткани
Покрывает циновку из рубленых прядей, салфетки и тесьму.
Узнать большеПоделиться статьей
Twitter Facebook LinkedIn Электронная почта
Перейти к основным материалам Вернуться к покрытиям .