Расчет расхода электродов на 1 м шва
Расход электродов на 1 м шва является важным показателем при составлении сметы на проведение сварочных работ. От точности расчета зависят экономические показатели всего проекта. Расчет расхода электродов должен производить опытный сварщик, хорошо разбирающийся в марках продукции и методиках сварочного процесса. Он должен учесть все нюансы предстоящих работ.
Схема сварочного электрода.
Общие формулы для расчета
За норму расхода принимается максимальное количество материалов, необходимых для производства сварочных работ. Нормирование должно учитывать расход электродов на сварку, прихватки и проведение правки способом «холостых валиков»:
Н = Нсв + Нпр + Нпр.
Норма на прихваточные работы и определяется в процентном отношении от расхода на основные работы:
- при сварке стали толщиной до 12 мм – 15%;
- при сварке стали толщиной более 12 мм – 12%;
- при сварке алюминиевых и титановых сплавов – до 20%.
Норма на правку изделий из алюминиевых и титановых сплавов составляет:
- для алюминия толщиной до 8 мм – 30%;
- для алюминия толщиной более 8 мм – 25%;
- для титана – 35-40%.
Марки электродов и их предназначение.
Расход электродов при изготовлении металлоконструкций определяется поузловыми, подетальными, поиздельными или пооперационными нормами. Все они связаны между собой и вычисляются исходя из расчета затрат материалов на 1 м сварного шва. Для конкретных типоразмеров затраты регламентируются согласно СНиП.
В расходную часть входит масса наплавленного металла и технологические потери:
N = M*K,
где N – норма расхода на 1 м,
M – масса наплавленного металла на 1 м,
K – коэффициент потерь.
Масса присадки на один метр шва (M) рассчитывается как произведение площади поперечного сечения (S), плотности материала (ρ) и длины шва (L = 1 м):
M = S* ρ* L
Площадь поперечного сечения берется по факту, а плотность материала – из справочной литературы.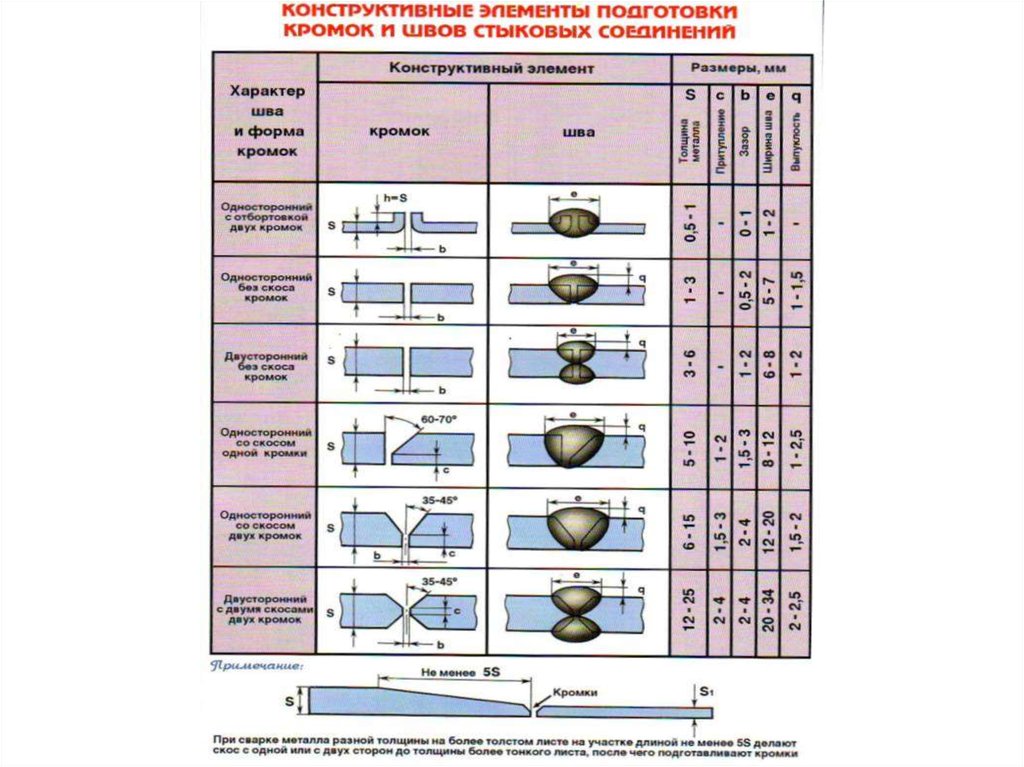
Читайте также:
Как производится сварка алюминия полуавтоматом.
В чем особенности аргонной сварки.
О сварке инвертором для начинающих читайте здесь.
Вернуться к оглавлению
Расчет поправочного коэффициента
Значение коэффициента (K) включает в себя технологические потери на угар, разбрызгивание и огарки. Оно зависит от применяемых методов и режимов сварки, типов сварных материалов, сложности условий проведения работ.
Коэффициент отношения расхода материала к наплавленной массе для различных типов электродов приведен в таблице.
Таблица расхода электродов.
Данный показатель учитывает потери на разбрызгивание и угар, а также на огарок. При расчете потерь на огарок был взят огарок длиной 50 мм, остающийся от стандартного электрода длиной 450 мм. Если фактические значения длин отличаются, то применяют поправку.
λ = (lэ – 50)/(lэ – lо),
где lэ – длина электрода,
lо – длина огарка.
Значения потерь на разбрызгивание, угар и огарок указываются в паспортной характеристике сварочных материалов.
Сложность работ определяется расположением сварного шва. В случаях, если оно отличается от нижнего, вносят следующие поправочные коэффициенты:
- для расположенного в наклонной плоскости – 1,05;
- для расположенного в вертикальной плоскости – 1,10;
- для потолочного- 1,20.
Учесть все тонкости работ по сварке металла, основываясь только на теоретических расчетах, достаточно сложно. И хотя в СНиП подробно описаны нормы при различных видах сварки, рекомендуется провести испытательные работы.
Контрольные работы проводятся в тех же условиях и с применением тех же материалов, что и проектируемые. Для обеспечения бесперебойности процесса и предотвращения задержек, связанных с непредвиденными затратами материала, закупку материалов следует проводить с запасом 5-7%.
С целью экономии присадочных материалов необходимо соблюдать соответствующую им настройку напряжения и силы тока. Экономия может быть достигнута и изменением угла наклона руки в процессе сварки.
В изделиях, где не требуется особой плотности соединения, используются прерывистые швы 50-150 мм с расстоянием между ними 100-300 мм и более. За счет этого происходит значительная экономия времени и уменьшается расход электродов.
С целью значительного уменьшения затрат на проведение работ рекомендуется использовать автоматическую сварку, которая обеспечивает высокую производительность и позволяет экономить за счет уменьшения площади поперечного сечения, не уменьшая качество стыка. Комплекс мер может в результате дать экономию до 30%.
О том как сэкономить на быте и хобби читайте здесь: https://lopatnik.info
Расход электродов на 1 м шва: как рассчитать норму?
Главная » Оборудование » Электроды » Нормы расхода электродов при сварочных работах
0
Опубликовано: 13.03.2018
При выполнении сварки на производительность, продолжительность процесса влияет расход электродов, так как отработавший присадочный материал необходимо заменить новым.
Оглавление:
- Основные факторы, влияющие на расход материала
- Вводные параметры
- Как рассчитывается потребность электродов?
- Теоретический расчет
- Практический расчет
- Рекомендация
- Как уменьшить расход присадочного материала
Основные факторы, влияющие на расход материала
Вводные параметры
При проведении расчета потребности электродов для сварки, например, трубопроводов нужно учитывать следующие моменты:
- Массу металла, необходимого для наплавления, полного заполнения шовного соединения.
Для точного расчета наплавления используется технологическая карта сварочного процесса. Приблизительно масса металла, необходимого для наплавления, составляет полтора процента от массы цельной металлической конструкции. - Длину сварного соединения (шва). Для измерения данного параметра можно использовать строительную рулетку. Измеряется длина стыка и умножается на количество швов, так как для заваривания глубоких стыков может понадобиться наложение нескольких швов.
- Нормы расхода электродов на 1 м шва сварки.
- Силу тока. Превышение допустимых пределов способно повлечь за собой при плавлении электродов разбрызгивание металла.
Как рассчитывается потребность электродов?
Для расчета потребности расходного материала используются разные способы, которые предусмотрены для разных условий выполнения сварочных работ.
Наиболее точные расчеты способен, конечно же, выполнить специалист. Он точно определит необходимость замены расходников и способ уменьшения стоимости сварочных работ.
На сегодняшний день точно рассчитать количество расходного материала можно несколькими способами.
Теоретический расчет
Как точно рассчитать нормативный расход сварочных электродов? Чаще всего подобные расчеты осуществляются по следующей формуле:
Н = МхК
Н – расход металла, кг
М – масса наплавляемого металла, кг
К – коэффициент наплавления
При использовании данной формулы необходимо учитывать следующие нюансы:
- знать площадь поперечного сечения, которая умножается на плотность основного металла, длину стыка;
- обязательно нужно учитывать марку используемого присадочного материала.
Но чтобы в процессе выполнения, к примеру, сварки трубопроводов электроды неожиданно не закончились, и не пришлось бежать в магазин строительных материалов, всегда к произведенным расчетам рекомендуется добавлять дополнительно 5 процентов расходного материала.
Практический расчет
youtube.com/embed/K_sPIcJoii4?feature=oembed&wmode=opaque» frameborder=»0″ allow=»accelerometer; autoplay; encrypted-media; gyroscope; picture-in-picture» allowfullscreen=»»>Чаще всего практический метод расчета необходимого количества электродов используется сварщиками при отсутствии таблицы готовых расходов присадочного материала для разных материалов, их параметров, типа сварки.
Рекомендация
Как уменьшить расход присадочного материала
Условия, которые рекомендуется соблюдать для экономии электродов:
- Сила тока, напряжение сварочного аппарата должны соответствовать используемому расходному материалу.
- Максимальной экономии электродов можно достичь при использовании автоматической/полуавтоматической сварки.
- Добиться минимального расхода сварочных электродов можно путем изменения в процессе сваривания изделий положения электрода.
Сергей Одинцов
tweet
Расчет веса требуемого металла сварного шва
Оценка количества сварочного электрода, необходимого для выполнения работы.

Расчет потребности в металле для сварного шва кажется сложным, но для большинства приложений это не должно быть так. Если не иметь компьютерной программы, которая вычисляет это для вас, самый простой способ — использовать таблицы, найденные в Справочнике по процедурам дуговой сварки. В Таблице 12-1 приведены данные для расчета веса металла сварного шва, необходимого на фут соединения. В нем есть информация об угловых швах (которые также можно использовать для нахлестов) и швах с разделкой кромок. Все, что вам нужно знать, это детали сустава (размер ножки, угол скоса, корень и т. д.). Если у вас нет таблиц из Руководства по процедурам, вы можете относительно легко выполнить все эти расчеты вручную. Взгляните на наш пост о расчете потребности в металле сварного шва вручную
Мы получаем звонки от клиентов, которые интересуются требованиями к металлу сварного шва для работ, которые они запрашивают. Когда мы разговариваем с заказчиком, мы запрашиваем общее количество дюймов (или футов) сварного шва, тип и размеры сварного шва. Нам также необходимо знать процесс, используемый для учета эффективности электродов, когда мы говорим им, сколько продукта нужно купить.
Клиент недавно предоставил нам следующую информацию:
У меня есть сборка, состоящая из сорока пяти угловых сварных швов 3/16 дюйма и длиной 3 дюйма. Он также имеет семнадцать угловых швов ¼ дюйма длиной 4,5 дюйма. По контракту мы должны построить 3200 таких машин. Сколько фунтов проволоки нам нужно для этой работы?
Мы подходим к таблицам в Руководстве по процедурам и видим, что для скругления 3/16 дюйма с плоской поверхностью нам требуется 0,072 фунта металла сварного шва на фут соединения. Мы также видим, что для скругления ¼ дюйма требуется 0,129 фунта на фут сустава. Эти значения включают 10% припуск на сварку. Однако учтите, что это очень маленькая надбавка. Если ваше 3/16-дюймовое скругление окажется ¼-дюймовым, вы переварите на 77%!
Таблица 12-1 в Руководстве по дуговой сварке помогает определить потребность в металле для сварки на основе геометрии соединения.
Итого:
45 сварных швов x 3 дюйма каждый = 135 дюймов = 11,25 фута -> @ 0,072 фунта/фут это дает 0,81 фунта на сборку
17 сварных швов x 4,5 дюйма каждый = 76,5 дюйма = 6,375 фута -> @ 0,129 фунта/фут, что дает 0,82 фунта на сборку.
Если сложить их вместе, получится 1,63 фунта на деталь. А для всего 3200 деталей нам потребуется 5216 фунтов наплавленного металла. Поскольку процесс, который они будут использовать, представляет собой GMAW, и в этом случае они собирались использовать режим короткого замыкания для переноса металла, мы смотрим на эффективность проволоки и видим, что она равна 9.5%. Мы делим весь необходимый сварочный металл на коэффициент полезного действия 5216/0,95, и это дает нам количество сварочной проволоки, которое необходимо приобрести, что в данном случае составляет 5491 фунт.
Если бы эта работа выполнялась с помощью штучного электрода, нам пришлось бы использовать КПД 65% (намного ниже из-за потерь в стержнях, шлака и брызг). В этом случае нам потребуется 8024 фунта. Никогда не забывайте включать эффективность электрода, иначе у вас могут быть проблемы.
Если у вас нет такой таблицы, как в Руководстве по процедурам, и вам нужен быстрый ответ, вы всегда можете использовать карандаш, бумагу и математику средней школы, чтобы получить эту информацию. Взгляните на наш пост о том, как это сделать: Расчет потребности в металле сварного шва вручную
Опубликовано
Категории: Снижение затрат, Затраты на сварку
Раскрытие информации о связи материалов: Некоторые ссылки в посте выше являются «партнерскими ссылками». Это означает, что если вы нажмете на ссылку и купите товар, мы получим партнерскую комиссию. Несмотря на это, мы рекомендуем только продукты или услуги, которыми пользуемся лично, и верим, что они принесут пользу нашим читателям. Я раскрываю это в соответствии с 16 CFR Федеральной торговой комиссии, часть 255: «Руководства по использованию одобрений и отзывов в рекламе».
Стоимость сварки — TWI
Предыдущая статья Connect , номер 95, касалась методов определения веса наплавленного металла в соединении, позволяющих рассчитать стоимость сварочных материалов.
Щелкните здесь , чтобы посмотреть наши последние технические подкасты на YouTube .
Это, очевидно, первый шаг к расчету стоимости фактического изготовления сварного соединения, но есть много других факторов, которые необходимо учитывать, но которые выходят за рамки этих статей.
Наиболее значительными из этих затрат являются накладные расходы; стоимость предоставления сварочного цеха или участка, а также расходы на управление и функционирование организации.
Эти расходы зависят от практики бухгалтерского учета в организации. Они включают в себя такие факторы, как арендная плата, ставки, банковские проценты, стоимость косвенных рабочих, т. е. тех, кто не участвует непосредственно в производстве, амортизация оборудования и т. д. Кроме того, другие учетные решения (например, когда затраты на механическую обработку и сборку поглощается) может повлиять на решение о том, какой метод соединения является наиболее рентабельным.
Одной из наиболее значительных затрат является стоимость рабочей силы, и она неизбежно зависит от отрасли, времени и страны. Упомянутые выше затраты, как правило, не могут зависеть от решений, принимаемых инженером-сварщиком. Поэтому в этих статьях основное внимание будет уделено тем аспектам сварочной деятельности, которые не подлежат учету, накладным расходам или затратам на оплату труда.
Помимо стоимости наплавки металла на сварку, существует множество затрат, которые влияют на цену сварного изделия.
Работа, проделанная проектировщиком по разработке наиболее рентабельного соединения в изделии, которое может быть размещено в наиболее выгодном положении для сварки, будет иметь большое влияние на затраты. Например, тип подготовки шва, который выбирает проектировщик; подготовка с одинарным или двойным V-образным вырезом может быть выполнена пламенной резкой, подготовка J-образной формы требует механической обработки и, как правило, намного дороже. Однако обработанный J-препарат может иметь меньший объем, чем одиночный V-образный, в зависимости от толщины; будет более точным и, следовательно, более быстрым для сборки в пределах допуска и может привести к более низкой скорости ремонта, что приведет к более низкой стоимости, чем подготовка V.
Затраты, на которые непосредственно влияют технические решения по сварке, в дополнение к стоимости фактической наплавки металла шва, следовательно, составляют; подготовка стыка, время сборки (включая размещение в любом приспособлении или приспособлении и прихватку), очистку и зачистку сварного шва, снятие с приспособления или приспособления, термообработку после сварки, затраты на неразрушающий контроль и стоимость ремонта.
Количество наплавленного металла редко совпадает с количеством приобретенного присадочного металла. Это является результатом потерь, когда, например, проволока для сварки GMAW или дуговой сварки под флюсом обрезается до контактного наконечника, когда катушка с проволокой заканчивается, а длина проволоки между приводным роликом и контактным наконечником обрывается, или проволока или катушка повреждена.
Такие потери, как правило, довольно малы, но это не относится к электродам с покрытием. Поврежденные флюсовые покрытия, неправильно хранящиеся электроды и заглушки, выброшенные сварщиком, — все это приводит к тому, что треть покупного веса ручных электродов для дуговой сварки утилизируется. В каталогах некоторых производителей электродов приведены значения этих потерь, которые могут варьироваться в зависимости от типа и диаметра электрода.
Для помощи в расчете количества закупаемых сварочных материалов В таблице 1 приведены некоторые коэффициенты умножения для наиболее распространенных процессов дуговой сварки. Вес металла шва в соединении следует умножить на этот коэффициент, чтобы получить количество требуемого сварочного материала. Эти цифры предполагают хорошее ведение хозяйства и дисциплину в цехе, чтобы расходные материалы не тратились впустую или не выбрасывались без необходимости.
Таблица 1 Коэффициент умножения. Вес металла сварного шва для получения требуемого веса присадочного металла.
Процесс дуговой сварки | Множитель |
---|---|
ММА (SMAW) | 1,5 |
ВИГ (GTAW) | 1,1 |
МИГ/МАГ (GMAW) | 1,05 |
Поддуга (SAW) | 1,02 |
FCAW | 1,2 |
MCAW | 1,1 |
Другими расходными материалами в этом уравнении стоимости являются защитные газы или флюс.
Обычный газовый баллон для сварки на уровне плеча содержит около 10 000 литров защитного газа при давлении 200 бар. Поскольку расход газа, обычно используемый в производстве, составляет от 12 до 15 литров в минуту, этот типичный баллон должен обеспечивать от 10 до 12 часов времени сварки с учетом потерь в начале и в конце периода горения дуги.
Норма расхода флюса при дуговой сварке под флюсом составляет примерно 1 кг флюса на каждый 1 кг наплавленного металла. Это предполагает хорошее ведение хозяйства и эффективную систему рециркуляции флюса. Таким образом, расчет необходимого количества (и, следовательно, стоимости) этих расходных материалов является относительно простым.
Стоимость времени, затрачиваемого сварщиком на сварку соединения, зависит не только от скорости наплавки в процессе. Наиболее важным фактором в определении времени, необходимого сварщику, является то, что известно как «рабочий цикл» или «рабочий фактор». Это процентное значение, показывающее количество времени, в течение которого горит дуга и наплавляется металл сварного шва, по сравнению с общим временем работы сварщика.
В таблице 2 приведены некоторые цифры для наиболее распространенных процессов дуговой сварки. Обратите внимание, что они НЕ включают время на настройку или сборку, а отдельные обстоятельства могут увеличивать или уменьшать эти цифры.
Таблица 2 Рабочий цикл для процессов дуговой сварки
Процесс дуговой сварки | Рабочий цикл % |
---|---|
79 M | 15 — 30 |
ВИГ (GTAW) | 25 — 40 |
Механизированная сварка TIG | 80 — 90 |
МИГ/МАГ (GMAW) | 30 — 45 |
Механизированная сварка MIG/MAG | 80 — 90 |
Поддуга (SAW) | 80 — 95 |
FCAW | 25 — 45 |
Механизированный FCAW | 70 — 85 |
MCAW | 30 — 45 |
Потеря времени на этом рисунке может быть учтена с учетом всех других действий, которые выполняет сварщик. При сварке ММА, например, требуется время для прихватки, удаления шлака и очистки сварочного прохода, для смены электродов, для изменения положения, для перерывов и для снятия изделия с приспособления. Аналогичные действия должны быть выполнены с использованием других сварочных процессов.
Таким образом, увеличение рабочего цикла является одним из методов повышения производительности либо за счет организации цеха таким образом, чтобы сократить потери времени, либо за счет использования процесса с более высоким рабочим циклом. Однако помните, что время горения дуги может составлять лишь очень небольшую долю от общего времени производства, и внимание к другим аспектам производственного цикла может дать большую отдачу, чем простое увеличение рабочего цикла сварки.
Ссылка на таблицу 2 также предполагает, что механизация является одним из способов увеличения рабочего цикла. Однако необходимо соблюдать осторожность, если необходимо сократить общее время (от этажа до этажа).