Плазморез из сварочного инвертора своими руками: подробно о самоделке
Отслужившие детали различных машины и инструментов отлично подходят для изготовления полезных в домашнем хозяйстве устройств своими руками. Если есть в наличии ненужный сварочный инвертор, то из него можно сделать самодельный плазморез.
О том, каким образом превратить прибор для сваривания металла в устройство, которое способно разрезать прочный материал, будет подробно рассказано в этой статье.
Преимущество плазмореза перед газовым резаком
Одним из самых простых устройств для резки металла является газовый резак. Такой прибор стоит небольших денег и расходные материалы к нему также недороги. Но при выполнении газосварочных работ происходит нагрев слишком большой площади металла.
По этой причине материалы, обладающие большой теплопроводностью могут покоробиться и изменить цвет. Как в месте плавления металла, так и на значительном удалении от термического воздействия пламени горелки.
Преимущество плазмореза заключается в том, что удаётся получить очень тонкую струю раскалённого газа, которая будет воздействовать на небольшую площадь поверхности, что позволит значительно уменьшить нагрев детали.
Принцип работы плазмореза
Изготовить плазморез самостоятельно, не разбираясь в принципе работы этого устройства практически невозможно.
Процесс образования плазмы происходит в результате:
- Подачи электрического тока в горелку.
- Между электродами (катод и анод) горелки возникает электрическая дуга.
- Воздух под давлением подаётся в горелку и «выдувает» дугу наружу, при этом значительно увеличивая её температуру.
- К разрезаемому металлу подключается кабель «массы», поэтому ионизируемое пламя как бы замыкает о поверхность материала.
В результате получается высокоэффективное устройство для разрезания различных металлов. В том числе тех, которые обладают повышенными показателями теплопроводности.
Смотрите видео, где в доступной форме показано что такое плазменная резка и как она работает:
Детали для самодельного устройства
Плазморез из сварочного инвертора своими руками изготавливается из следующих деталей.
1. Плазмотрон. Эта деталь в конструкции плазмореза является наиболее важной.
Даже при наличии необходимого по силе электрического тока и давления газа, дугу не удастся получить, если внутренние электроды будут неправильно расположены. А отверстие для подачи воздуха будет иметь неподходящий диаметр.
Стоит такая деталь довольно дорого, поэтому домашние мастера предпочитают изготавливать горелки самостоятельно из подручных деталей.
2. Источник тока. В самодельном плазморезе источником тока будет сварочный инвертор.
3. Компрессор. Чтобы обеспечить длительную подачу сжатого воздуха в плазмотрон необходимо приобрести компрессор средней мощности.
Узнайте из этого видео, как выбрать компрессор для плазменной резки:
Также потребуются для самодельного плазмореза купить достаточное количество медных проводов большого диаметра. Для подключения «массы» к разрезаемой детали и обеспечения плазмотрона необходимым количеством электроэнергии.
Самостоятельное изготовление плазмотрона
Горелка или плазмотрон может быть изготовлена из подручных материалов. Чтобы собрать этот элемент самодельного плазмореза понадобятся:
- ручка;
- кнопка пуска;
- специальный электрод;
- сопло;
- изолятор.
Для изготовления самодельного плазмотрона идеально подойдёт ручка от мощного паяльника. Как правило, такая деталь имеет серединное отверстие, через которое и будут подводиться электрический ток и сжатый воздух.
Кнопку лучше использовать достаточно большую, чтобы во время работы пользоваться устройством было максимально комфортно.
Электроды потребуется приобрести в магазине. Для самостоятельного изготовления плазмотрона лучше выбирать изделия, изготовленные из гафния.
Для работы с металлами различной толщины потребуется также купить набор сопл.
Изготавливается плазмотрон в такой последовательности:
- Сразу за ручкой помещается металлическая трубка, покрытая изнутри фторопластом.
- Внутри трубки размещается электрод, который почти по всей длине закрыт высокотемпературной изоляцией.
- За электродом устанавливается с помощью резьбового соединения сопло подходящего диаметра.
Плазмотрон готов к использованию. Ещё для работы устройства потребуется подключить для подачи воздуха шланг от компрессора и электрический провод от инвертора.
Посмотрите видео, где человек рассказывает, как он пытался сделать плазмотрон:
Источник тока
В качестве источника электроэнергии можно использовать сварочный инвертор со следующими показателями:
- напряжение питания – 220 В;
- мощность – от 4 кВт;
- возможность регулировки тока от 20 – 40 А.
Сборка плазмореза
Когда отдельные детали плазмореза будут готовы, можно приступить к сборке. Чтобы работать с самодельным устройством было максимально комфортно, необходимо свести к минимуму количество тянущихся за ручкой проводов и шлангов.
Для более компактного размещения рабочего провода его помещают внутри шланга, по которому производится подача сжатого воздуха. Провод надёжно подсоединяется к электроду, при этом шланг также должен быть подключён к горелке без образования зазоров.
Другой контакт от инвертора будет подключаться к разрезаемой детали в качестве «массы» поэтому его следует оборудовать клеммой типа «крокодил».
Из этого видео вы узнаете, как самому сделать шланг пакет, шлейф для плазмореза:
Процесс разрезания металла с помощью плазменного резака очень прост. После подачи электричества образуется электрическая дуга. Момент образования запала регулируется кнопкой, которая была ранее установлена на ручке плазмотрона. Воздух подаётся от компрессора по шлангу и раздувает дугу, тем самым увеличивая её температуру, которая может достигать 8000ºС.
Для того чтобы затушить дугу достаточно отпустить кнопку на ручке. Таким образом горелка будет работать только в тот момент, когда необходимо разрезать металл, что сведёт к минимуму эффект перегрева, к которому самодельные изделия очень чувствительны.
Интересное видео про плазморез своими руками и из чего он состоит:
Советы и рекомендации
Важно не только знать, как переделать инвертор в плазморез, но и как сделать работу такого устройства максимально эффективной и безопасной.
Далее будут приведены несколько рекомендаций. Придерживаясь которых можно избежать наиболее распространённых ошибок при изготовлении и использовании самодельного устройства:
- Перед тем как приступить к изготовлению из сварочного инвертора устройства для резки металлов, следует наметить на бумаге основные элементы такой системы. Самостоятельно изготовленные чертежи и схемы позволят в процессе работы не допустить досадных ошибок, которые наиболее часто бывают вызваны обычной невнимательностью.
- Несмотря на то, что плазменный резак имеет очень узкое пламя, которое не слишком разогревает даже металлы обладающие повышенной теплопроводностью, рекомендуется при работе с алюминиевыми изделиями использовать в качестве распыляющего газа неон или аргон, которые не позволят окислиться поверхности, подвергнувшейся воздействию высокой температуры.
- Чтобы максимально сократить время на изготовление плазмореза рекомендуется приобрести готовую горелку для газового резака. Такое изделие позволит максимально эффективно и безопасно работать с металлом.
- При использовании самодельного плазмореза необходимо придерживаться основных правил техники безопасности. Прежде всего, следует обеспечить защиту от воздействия электричества и брызг расплавленного металла. Для этой цели используются специальная обувь, перчатки и фартук. Также необходимо надевать защитные очки, которые позволят предохранить зрение от воздействия ультрафиолетовых лучей. В процессе резки металла выделяется большое количество вредных для здоровья веществ, поэтому рекомендуется защищать органы дыхания с помощью респиратора.
О том, как из инвертора сделать плазморез своими руками подробно рассказано в этой статье. Перед началом изготовления плазменного резака рекомендуется проверить работоспособность инвертора.
Загрузка…plavitmetall.ru
самодельный празморез из сварочного инвертора
Плазменные резаки активно используются в мастерских и предприятиях, связанных с цветными металлами. Большинство небольших предприятий применяют в работе плазменный резак, изготовленный своими руками.
хорошо себя показывает при разрезе цветных металлов, поскольку позволяет локально прогревать изделия и не деформировать их. Самостоятельное производство резаков обусловлено высокой стоимостью профессионального оборудования.
В процессе изготовления подобного инструмента используются комплектующие от других электроприборов.
Особенности и назначение плазменного резака
Инвертор используется для выполнения работ как в домашних, так и в промышленных условиях. Существует несколько видов плазморезов для работы с различными типами металлов.
Различают:
- Плазморезы, работающие в среде инертных газов, например, аргона, гелия или азота.
- Инструменты, работающие в среде окислителей, например, кислорода.
- Аппаратура, предназначенная для работы со смешанными атмосферами.
- Резаки, работающие в газожидкостных стабилизаторах.
- Устройства, работающие с водной или магнитной стабилизацией. Это самый редкий вид резаков, который практически невозможно найти в свободной продаже.
или плазматрон – это основная часть плазменной резки, отвечающая за непосредственную нарезку металла.
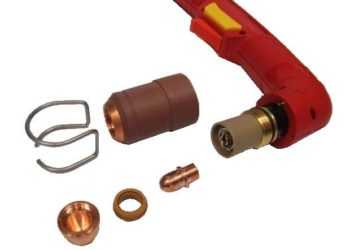
Плазменный резак в разборе.
Большинство инверторных плазменных резаков состоят из:
- форсунки;
- электрода;
- защитного колпачка;
- сопла;
- шланга;
- головки резака;
- ручки;
- роликового упора.
Принцип действия простого полуавтоматического плазмореза состоит в следующем: рабочий газ вокруг плазмотрона прогревается до очень высоких температур, при которых происходит возникновение плазмы, проводящей электричество.
Затем, ток, идущий через ионизированный газ, разрезает металл путем локального плавления. После этого струя плазмы снимает остатки расплавленного металла и получается аккуратный срез.
По виду воздействия на металл различают такие виды плазматронов:
- Аппараты косвенного действия.
Данный вид плазматронов не пропускает через себя ток и пригоден лишь в одном случае – для резки неметаллических изделий. - Плазменная резка прямого действия.
Применяется для разрезки металлов путем образования плазменной струи.
Конструкция плазменного резака и рекомендации по работе с ним серьезно разнятся в зависимости от типа устройства.
Делаем плазменный резак своими руками
Плазменная резка своими руками может быть изготовлена в домашних условиях. Неподъемная стоимость на профессиональное оборудование и ограниченное количество представленных на рынке моделей вынуждают умельцев собирать плазморез из сварочного инвертора своими руками.
Самодельный плазморез можно выполнить при условии наличия всех необходимых компонентов.
Перед тем как сделать плазморежущую установку, необходимо подготовить следующие комплектующие:
- Компрессор.
Деталь необходима для подачи воздушного потока под давлением. - Плазмотрон.
Изделие используется при непосредственной резке металла. - Электроды.
Применяются для розжига дуги и создания плазмы. - Изолятор.
Предохраняет электроды от перегрева при выполнении плазменной резки металла. - Сопло.
Деталь, размер которой определяет возможности всего плазмореза, собранного своими руками из инвертора. - Сварочный инвертор.
Источник постоянного тока для установки. Может быть заменен сварочным трансформатором.
Источник питания устройства может быть либо трансформаторным, либо инверторным.
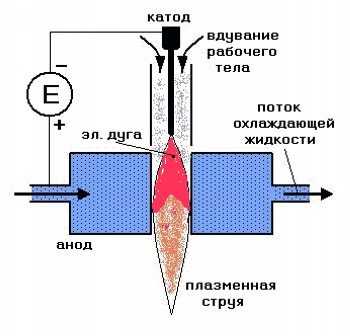
Схема работы плазменного резака.
Трансформаторные источники постоянного тока характеризуются следующими недостатками:
- высокое потребление электрической энергии;
- большие габариты;
- труднодоступность.
К преимуществам такого источника питания можно отнести:
- низкую чувствительность к перепадам напряжения;
- большую мощность;
- высокую надежность.
Инверторы, в качестве блока питания плазмореза можно использовать, если необходимо:
- сконструировать небольшой аппарат;
- собрать качественный плазморез с высоким коэффициентом полезного действия и стабильной дугой.
Благодаря доступности и легкости инверторного блока питания плазморезы на его основе могут быть сконструированы в домашних условиях. К недостаткам инвертора можно отнести лишь сравнительно малую мощность струи. Из-за этого толщина металлической заготовки, разрезаемой инверторным плазморезом, серьезно ограничена.
Одной из главнейших частей плазмореза является ручной резак.
Сборка данного элемента аппаратуры для резки металла осуществляется из таких компонентов:
- рукоять с пропилами для прокладки проводов;
- кнопка запуска горелки на основе газовой плазмы;
- электроды;
- система завихрения потоков;
- наконечник, защищающий оператора от брызг расплавленного металла;
- пружина для обеспечения необходимого расстояния между соплом и металлом;
- насадки для снятия окалин и нагара.
Резка металла различной толщины осуществляется путем смены сопел в плазмотроне. В большинстве конструкций плазмотрона, сопла закрепляются специальной гайкой, с диаметром, позволяющим пропустить конусный наконечник и зажать широкую часть элемента.
После сопла располагаются электроды и изоляция. Для получения возможности усиления дуги при необходимости в конструкцию плазматрона включают завихритель воздушных потоков.
Сделанные своими руками плазморезы на основе инверторного источника питания являются достаточно мобильными. Благодаря малым габаритам такую аппаратуру можно использовать даже в самых труднодоступных местах.
Чертежи
В глобальной сети интернет имеется множество различных чертежей плазменного резака. Проще всего изготовить плазморез в домашних условиях, используя инверторный источник постоянного тока.
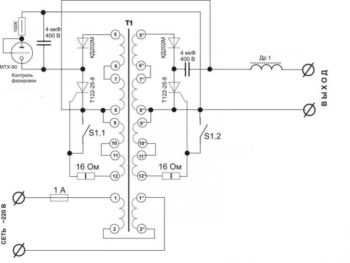
Электрическая схема плазмореза.
Наиболее ходовой технический чертеж резака на основе плазменной дуги включает следующие компоненты:
- Электрод.
На данный элемент подается напряжение от источника питания для осуществления ионизации окружающего газа. Как правило, в качестве электрода используются тугоплавкие металлы, образующие прочный окисел. В большинстве случаев конструкторы сварочных аппаратов используют гафний, цирконий или титан. Лучшим выбором материала электрода для домашнего использования является гафний. - Сопло.
Компонент автоматического плазменный сварочного аппарата формирует струю из ионизированного газа и пропускает воздух, охлаждающий электрод. - Охладитель.
Элемент используется для отвода тепла от сопла, поскольку при работе температура плазмы может достигать 30 000 градусов Цельсия.
Большинство схем аппарата плазменной резки подразумевают такой алгоритм работы резака на основе струи ионизированного газа:
- Первое нажатие на кнопку пуск включает реле, подающее питание на блок управления аппаратом.
- Второе реле подает ток на инвертор и подключает электрический клапан продувки горелки.
- Мощный поток воздуха попадает в камеру горелки и очищает ее.
- Через определенный промежуток времени, задаваемый резисторами, срабатывает третье реле и подает питание на электроды установки.
- Запускается осциллятор, благодаря которому производится ионизация рабочего газа, находящегося между катодом и анодом. На данном этапе возникает дежурная дуга.
- При поднесении дуги к металлической детали зажигается дуга между плазмотроном и поверхностью, называющаяся рабочей.
- Отключение подачи тока для розжига дуги при помощи специального геркона.
- Проведение резальных или сварочных работ. В случае пропажи дуги, реле геркона вновь включает ток и разжигает дежурную струю плазмы.
- При завершении работ после отключения дуги, четвертое реле запускает компрессор, воздух которого охлаждает сопло и удаляет остатки сгоревшего металла.
Наиболее удачными считаются схемы плазмореза модели АПР-91.
Что нам понадобится?
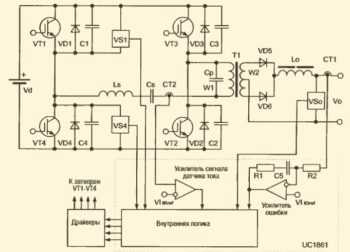
Чертеж плазменного резака.
Для создания аппарата плазменной сварки необходимо обзавестись:
- источником постоянного тока;
- плазмотроном.
В состав последнего входят:
- сопло;
- электроды;
- изолятор;
- компрессор мощностью 2-2.5 атмосферы.
Большинство современных мастеров изготавливают плазменную сварку, подключаемую к инверторному блоку питания. Сконструированный при помощи данных компонентов плазмотрон для ручной воздушной резки работает следующим образом: нажатие на управляющую кнопку зажигает электрическую дугу между соплом и электродом.
После завершения работы, после нажатия на кнопку выключения, компрессор подает струю воздуха и сбивает остатки металла с электродов.
Сборка инвертора
В случае, если фабричного инвертора нет в наличии, можно собрать самодельный.
Инверторы для резаков на основе газовой плазмы, как правило, имеют в строении такие комплектующие:
- блок питания;
- драйвера силовых ключей;
- силовой блок.

Плазменная горелка в разрезе.
для плазморезов или сварочного оборудования не может обойтись без необходимых инструментов в виде:
- набора отверток;
- паяльника;
- ножа;
- ножовки по металлу;
- крепежных элементов резьбового типа;
- медных проводов;
- текстолита;
- слюды.
Блок питания для плазменной резки собирается на базе ферритового сердечника и должен иметь четыре обмотки:
- первичную, состоящую из 100 витков проволоки, толщиной 0.3 миллиметра;
- первая вторичная из 15 витков кабеля с толщиной 1 миллиметр;
- вторая вторичная из 15 витков проволоки 0.2 миллиметра;
- третья вторичная из 20 витков 0.3 миллиметровой проволоки.
Обратите внимание! Для минимизации негативных последствий от перепадов напряжения в электрической сети, намотку следует проводить по всей ширине деревянного основания.
Силовой блок самодельного инвертора должен состоять из специального трансформатора. Для создания данного элемента следует подобрать два сердечника и намотать на них медную проволоку толщиной 0.25 миллиметров.
Отдельного упоминания стоит система охлаждения, без которой инверторный блок питания плазмотрона может быстро выйти из строя.
Рекомендации по работе

Чертеж технологии плазменной резки.
При работе на аппарате для достижения наилучших результатов нужно соблюдать рекомендации:
- регулярно проверять правильность направления струи газовой плазмы;
- проверять правильность выбора аппаратуры в соответствии с толщиной металлического изделия;
- следить за состоянием расходных деталей плазмотрона;
- следить за соблюдением расстояния между плазменной струей и обрабатываемым изделием;
- всегда проверять используемую скорость резки, чтобы избежать возникновения окалин;
- время от времени диагностировать состояние системы подвода рабочего газа;
- исключить вибрацию электрического плазмотрона;
- поддерживать чистоту и аккуратность на рабочем месте.
Заключение
Аппаратура для плазменной резки – это незаменимый инструмент для аккуратной нарезки металлических изделий. Благодаря продуманной конструкции плазмотроны обеспечивают быстрый, ровный и качественный порез металлических листов без необходимости последующей обработки поверхностей.
Большинство рукоделов из небольших мастерских предпочитают своими руками собирать мини резаки для работы с не толстым металлом. Как правило, самостоятельно сделанный плазморез по характеристикам и качеству работы не отличается от заводских моделей.
tutsvarka.ru
Плазморез из инвертора своими руками! Инструкция, схемы и видеоматериал!
Изготовить рабочий плазморез из сварочного инвертора своими руками не такая уж и сложная задача, как на первый взгляд может показаться. Для того чтобы реализовать данную идею, нужно приготовить все необходимые детали такого устройства:
- Резак плазменный (или по другому — плазмотрон)
- Инвертор сварочный или трансформатор
- Компрессор, с помощью которого будет создаваться воздушная струя, необходимая для формирования и охлаждения потока плазмы.
- Кабели и шланги для объединения всех конструктивных элементов устройства в одну систему.
Плазморез, в том числе и самодельный, успешно применяется для выполнения всевозможный работ как на производстве, так и дома. Это устройство незаменимо в тех ситуациях, когда необходимо выполнить точный, тонкий и качественный разрез металлических заготовок. Отдельные модели плазменных резаков с точки зрения их функциональности позволяют применять их в качестве сварочного аппарата. Такая сварка выполняется в защитном газе аргона.
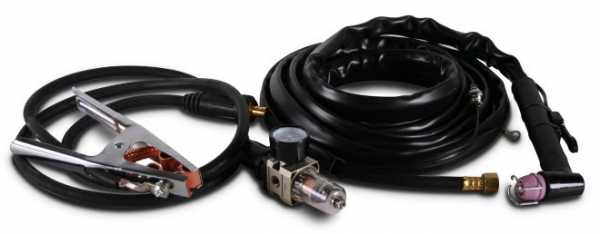
При выборе источника питания для самодельного плазмотрона важно обратить внимание на величину тока, который может генерировать такой источник. Чаще всего для этого выбирают инвертор, который обеспечивает высокую стабильность процесса плазменной резки и позволяет более экономно использовать энергию. В отличие от сварочного трансформатора, обладает компактными размерами и небольшим весом, инвертор удобнее в использовании. Единственным недостатком использования инверторных плазменных резаков является сложность резки слишком толстых заготовок с их помощью.
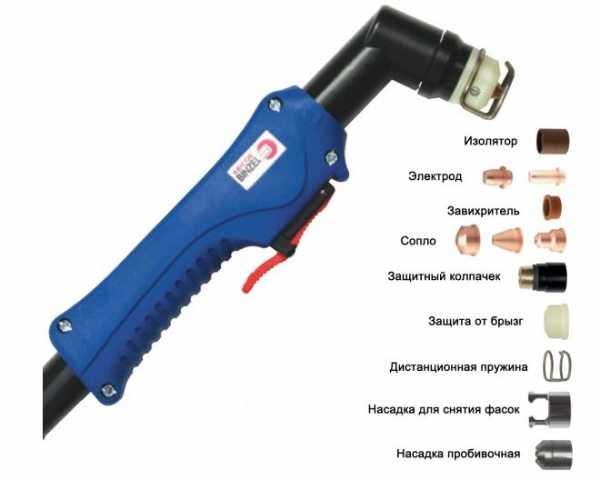
При сборке самодельного агрегата для выполнения плазменной резки вы можете использовать готовые схемы, которые легко найти в Интернете. Кроме того, в Интернете есть видео о том, как изготовить плазморез своими руками. Используя готовую схему при сборке такого устройства, очень важно строго её придерживаться, а также обратить особое внимание на соответствие конструктивных элементов друг другу.
Схемы плазмореза на примере аппарата АПР-91
В качестве примера при изучении принципиальной электрической схемы, мы будем использовать устройство для плазменной резки APR-91.
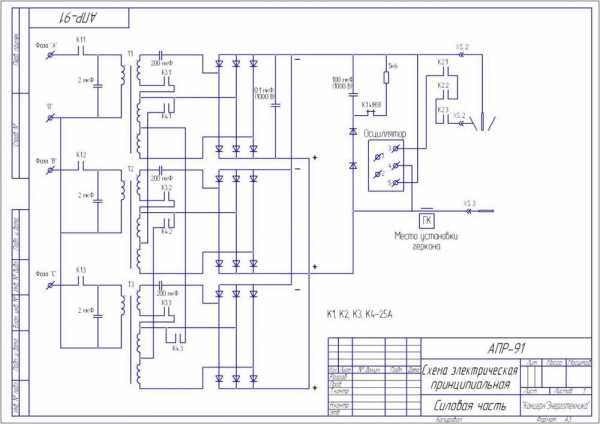
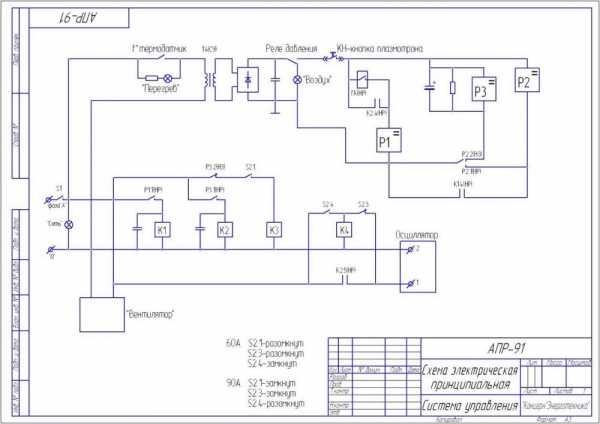
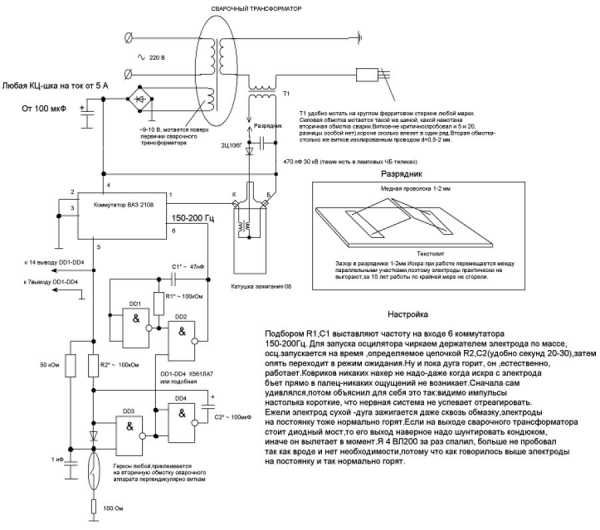
Детали самодельного устройства для плазменной резки
Первое, что вам нужно найти для изготовления самодельного плазменного резака, это источник питания, в котором будет генерировать электрический ток с необходимыми характеристиками. Обычно для этого используют сварочные инверторные аппараты, что объясняется рядом их преимуществ. Благодаря своим техническим характеристикам, подобное оборудование способно обеспечить высокую стабильность генерируемого напряжения, что положительно сказывается на качестве резки. Работать с инверторами гораздо удобнее, что объясняется не только их компактными размерами и небольшим весом, но и простотой настройки и эксплуатации.
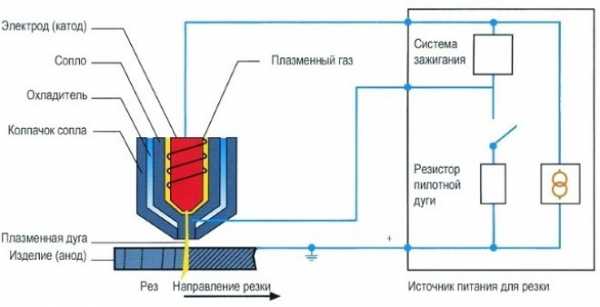
Благодаря своей компактности и малому весу плазменные резаки на основе инверторов могут использоваться при работе даже в самых трудных местах, что исключено для громоздких и тяжелых сварочных трансформаторов. Большим преимуществом инверторных источников питания является их высокая эффективность. Это делает их очень экономичными с точки зрения энергопотребления устройств.
В некоторых случаях источником питания для плазменного резака может быть сварочный трансформатор, но его использование чревато значительным энергопотреблением. Следует также учитывать, что любой сварочный трансформатор характеризуется большими габаритами и значительным весом.
Основным элементом аппарата, предназначенного для резки металла плазменной струей, является плазменный резак. Этот элемент оборудования обеспечивает качество резки, а также эффективность ее выполнения.
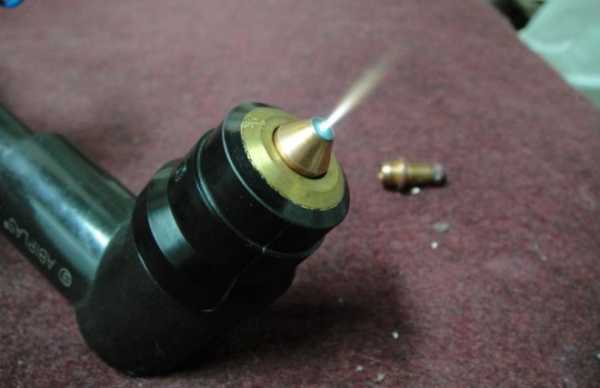
Для формирования воздушного потока, который будет преобразован в высокотемпературную плазменную струю, в конструкции плазменного резака используется специальный компрессор. Электрический ток от инвертора и поток воздуха от компрессора поступают в плазменный резак с помощью пакета кабельных шлангов.
Центральным рабочим элементом плазменного резака является плазменная горелка, конструкция которой состоит из следующих элементов:
- Сопла
- Канала, по которому подается струя воздуха
- Электрода
- Изолятора, который параллельно выполняет функцию охлаждения
Конструкция плазменного резака и советы по его изготовлению
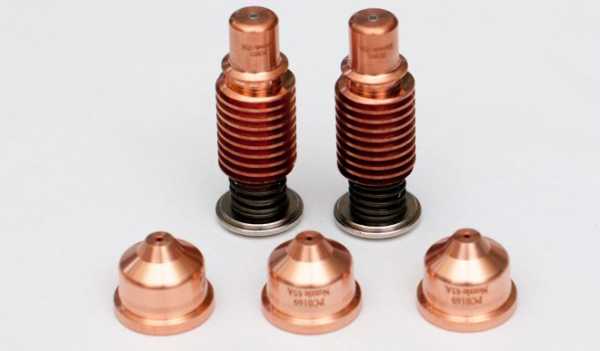
Некоторые из вышеперечисленных материалов при нагревании могут выделять соединения, опасные для здоровья человека, этот момент следует учитывать при выборе типа электрода. Таким образом, при использовании бериллия образуются радиоактивные оксиды, и при испарении тория в сочетании с кислородом образуются опасные токсичные вещества. Совершенно безопасным материалом для изготовления электродов для плазменной горелки является гафний.
За формирование плазменной струи, с помощью которой и производится резка, отвечает сопло. Его производству следует уделить серьезное внимание, так как качество рабочего процесса зависит от характеристик этого элемента.
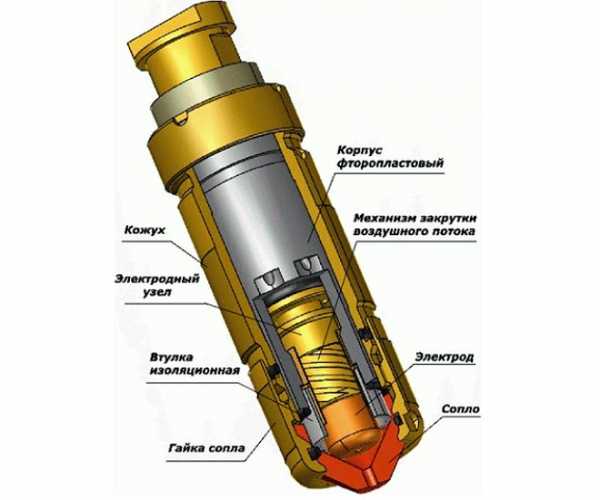
Самым оптимальным является сопло, диаметр которого равен 30 мм. От длины этой детали, зависит аккуратность и качество исполнения реза. Однако слишком длинное сопло также не следует делать, так как в данном случае оно быстро разрушается.
Как было упомянуто выше, в конструкцию плазмореза обязательно входит компрессор, который формирует и подает воздух в сопло. Последнее необходимо не только для формирования струи высокотемпературной плазмы, но и для того что бы охлаждать элементов аппарата. Применение сжатого воздуха в качестве рабочей и охлаждающей среды, а также инвертора, который формирует рабочий ток 200 А, позволяет эффективно резать металлические детали, толщина которых не превышает 50 мм.
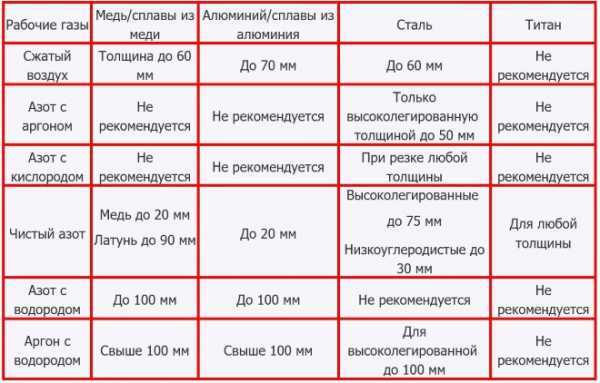
Для подготовки аппарата плазменной резки к работе, нужно соединить плазмотрон с инвертором и компрессором. Для решения этой задачи применяются пакеты кабельных шлангов, который используют следующим образом.
- Кабель, через который будет подаваться электрический ток, соединяет инвертор и электрод плазменной резки.
- Шланг подачи сжатого воздуха соединяет выход компрессора и плазменную горелку, в которой из входящего воздушного потока будет образовываться плазменная струя.
Основные особенности работы плазмореза
Чтобы сделать плазменный резак, используя инвертор для его изготовления, необходимо понять, как работает такое устройство.
После включения инвертора электрический ток от него начинает течь к электроду, что приводит к воспламенению электрической дуги. Температура дуги, горящей между рабочим электродом и металлическим наконечником сопла, составляет около 6000–8000 градусов. После зажигания дуги сжатый воздух подается в камеру сопла, которая проходит строго через электрический разряд. Электрическая дуга нагревает и ионизирует воздушный поток, проходящий через нее. В результате его объем увеличивается в сотни раз, и он становится способным проводить электрический ток.
С помощью сопла плазменного резака из проводящего воздушного потока формируется плазменная струя, температура которой активно поднимается и может достигать 25-30 тысяч градусов. Скорость потока плазмы, благодаря которой осуществляется резка металлических деталей, на выходе из сопла составляет около 2-3 метров в секунду. В тот момент, когда плазменная струя контактирует с поверхностью металлической детали, электрический ток от электрода начинает протекать через нее, и начальная дуга гаснет. Новая дуга, которая горит между электродом и заготовкой, называется резкой.
Характерной особенностью плазменной резки является то, что обрабатываемый металл плавится только в том месте, где на него влияет поток плазмы. Вот почему очень важно, чтобы место плазменного воздействия было строго в центре рабочего электрода. Если мы пренебрегаем этим требованием, то можем столкнуться с тем фактом, что воздушно-плазменный поток будет нарушен, в следствии чего, качество резки значительно ухудшится. Чтобы удовлетворить эти важные требования, используйте специальный (тангенциальный) принцип подачи воздуха к соплу.
Также необходимо следить, что бы два плазменных потока не образовывались одновременно, за места одного. Возникновение такой ситуации, которая приводит к несоблюдению режимов и правил технологического процесса, может привести к выходу из строя инвертора.
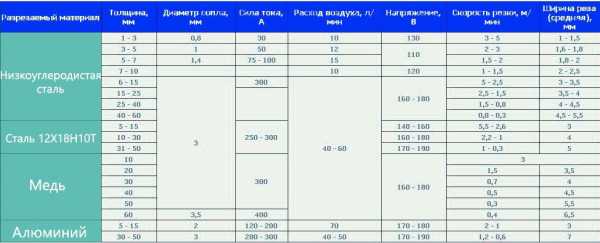
Важным параметром плазменной резки является скорость воздушного потока, которая не должна быть слишком большой. Хорошее качество реза и скорость его выполнения обеспечиваются скоростью воздушной струи, равной 800 м/с. В этом случае ток, протекающий от инверторного блока, не должен превышать 250 А. При выполнении работ на таких режимах следует учитывать тот факт, что в этом случае поток воздуха, используемого для формирования потока плазмы, будет увеличиваться.
Самостоятельно изготовить плазменный резак не так уж и сложно, для этого нужно изучить нужный теоретический материал, просмотреть обучающее видео и правильно подобрать все необходимые детали. При наличии в домашнем пользовании подобного аппарата, изготовленного на основе заводского инвертора, может выполнять не только качественную резку металла, но и плазменную сварку!
В том случае если у вас в пользовании нет инвертора, можно изготовить плазморез, взяв за основу сварочный трансформатор, в таком случае вам придется смириться с его большими габаритами и не малым весом. Так же, плазморез, сделанный на основе трансформатора, будет иметь не очень хорошую мобильностью и переносить его с места на место будет проблематично!
Источник
Похожее
kavmaster.ru
Плазменный резак своими руками: принцип действия, конструкция, сборка
Создавать плазменный резак своими руками весьма выгодно благодаря простой конструкции и применению доступных комплектующих. Они уступают по функциональности промышленным моделям, но позволяют выполнять основные виды резки металла с не меньшей эффективностью и качеством.
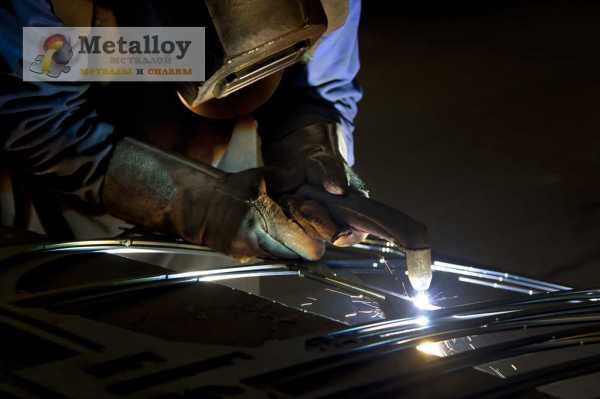
Плазменный резак своими руками
Для чего нужен плазморез?
Плазморез позволяет обрабатывать различные металлы при температурах 25–30 тыс. градусов с высокой скоростью, точностью, качеством. Он является прямым конкурентом лазерной обработки, но имеет более простую конструкцию, неприхотлив в обслуживании, эксплуатации, ремонте.
Плазменная резка используется для нарезания металлических заготовок с формами различной сложности. За счёт защитной газовой атмосферы при нагреве не образуются сложные металлические соединения, свойства которых отличаются от требуемых.
Принцип действия
Работа плазмореза основана на поджиге электрической дуги, в которую подаётся под давлением инертный газ, прогреваемый в замкнутом объёме до состояния плазмы, а затем поступающий прямо на поверхность разрезаемого металла. Направленная струя газа формируется в результате его перегрева внутри закрытой ёмкости при создании избыточного давления.
Когда электроды прикладываются к поверхности металла, создаётся вторая дуга, мощность которой превышает первоначальную в несколько раз. В ней плазменный поток ускоряется до 1,5 км/с. Комбинация высокой температуры дуги с потоком плазмы позволяет резать металлические заготовки, толщина разреза которых зависит от параметров сопла.
В плазморезах косвенного действия создаётся только плазменная направленная струя, способная резать не только металлы, но и непроводящие ток материалы. Однако их самостоятельное изготовление сложно, так как требуется точный расчёт параметров конструкции, подбора характеристик, настройки.
Инвертор или трансформатор
Чтобы получить плазму, нужно подключать качественные источники питания. Это могут быть трансформаторы или инверторы.
Сделать плазморез из инвертора выгодно благодаря компактности, точности подстроек тока, напряжения, контроля электрических параметров, экономному потреблению электроэнергии. Он имеет ограничение по току до 70 А, но мощности хватает для выполнения типичных работ по обработке металла.
Недостатком инвертора являются высокие требования к качеству питания, что не позволяет их применять в сетях с перепадами напряжения без подключения к стабилизаторам.
Трансформаторы лишены недостатка инвертора, более надёжны в эксплуатации, неприхотливы в обслуживании. Но при этом они имеют большие габариты, вес, высокое потребление электроэнергии. Ограничение по току достигает 180 А, в зависимости от количества витков, диаметра используемой проволоки.
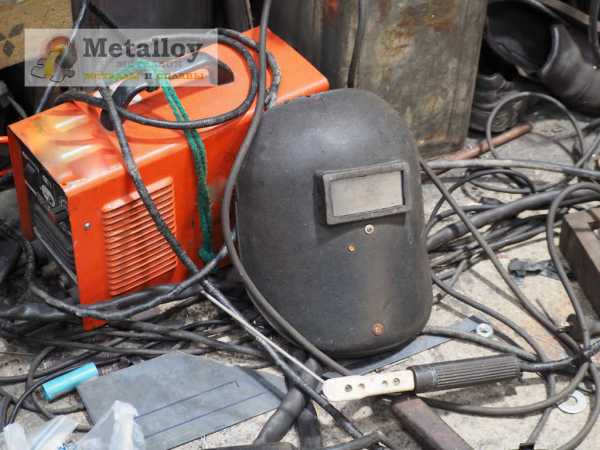
Инвертор для плазменного резака
Конструкция
Конструкция плазменного резака состоит из следующих компонент:
- Плазмотрон, предназначенный для формирования плазменной струи. Имеет сложную конструкцию, изготавливается из тугоплавкого металла. Требуется подбор таких параметров: диаметра сопла, длины резака, угла подачи сжатого воздуха в область формирования плазмы.
- Источник питания предназначен для поджига дуги. Должен иметь стабильные параметры по току и напряжению. Подбирают в зависимости от максимальной величины выходного тока, габаритов, размеров и веса.
- Осциллятор, используемый для упрощения розжига дуги, стабилизации её горения. Имеет простую схему, поэтому может быть собран самостоятельно либо приобретён в сборе.
- Компрессор для создания потока воздуха, подаваемого для охлаждения горелки, формирования направленного потока плазмы. Подходит практически любая модель. Чтобы не попала влага, потребуется установить осушитель.
- Медный кабель с зажимом на конце для подключения массы.
- Кабель-шланг, предназначенный для подключения горелки и поджига электрической дуги, а также для подачи сжатого воздуха. Может быть изготовлен путём укладки кабеля и кислородной трубки внутри поливочной гибкой трубки.
Необходимые комплектующие
Перед сборкой резака потребуется подготовить следующие комплектующие:
- источник питания;
- резак или плазмотрон;
- компрессор с осушителем или фильтром;
- осциллятор;
- электроды;
- шланги;
- кабели.
Подбор блока питания
Выбор источника электроэнергии для плазменной установки выполняется с учётом следующих критериев:
- максимальной толщины и типа разрезаемого металла;
- длительности проведения работ, времени горения дуги;
- требований к параметрам плазмы;
- стабильности тока, напряжения питающей сети;
- требований безопасности;
- необходимости расширения функциональности плазмореза.
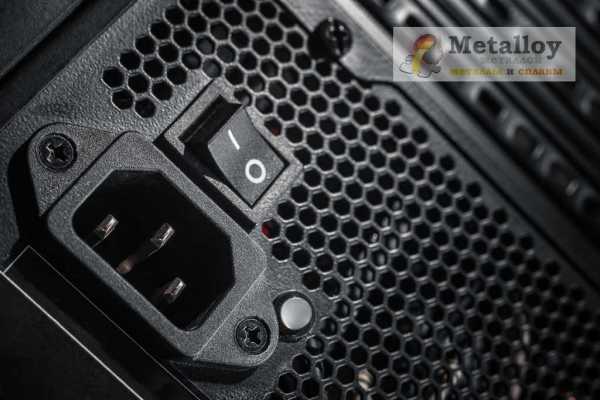
Блок питания
Плазмотрон
Поскольку плазмотрон используется для генерации плазмы, к подбору его параметров нужно подходить грамотно. Важные параметры:
- стойкость к рабочим температурам;
- удобство пуска, настройки, остановки работы оборудования;
- небольшой вес, компактные размеры;
- срок службы;
- требования к обслуживанию;
- ремонтопригодность.
По типу стабилизации дуги плазмотроны бывают газового, водяного и магнитного вида.
При работе важно своевременно заменять электроды, чтобы максимально продлить срок службы сопла. Понять необходимость данной процедуры можно по ухудшению качества резки: нарушение точности, появлению поверхностных волн. Важно не перегревать плазмотрон, поскольку это может повлечь серьёзные поломки.
Для создания плазмотрона потребуются следующие детали:
- рукоятка из материала с низкой теплопроводностью, в которой есть отверстия под провода для электрода, трубок для газа;
- пусковая кнопка;
- подходящие по параметрам электроды;
- сопло нужного диаметра;
- изолятор;
- пружина для соблюдения расстояния от сопла до разрезаемого металла;
- наконечник с защитой от брызг расплавленного металла;
- завихритель потока;
- специальная насадка.
Осциллятор
Осциллятор применяется для выработки токов высокой частоты. Работает в режимах коротких импульсов или постоянного горения дуги. Предназначен для быстрого запуска плазмореза.
Конструктивно состоит из следующих элементов:
- выпрямителя;
- конденсаторов;
- блока питания;
- управляющей микросхемы;
- импульсного модуля;
- повышающего трансформатора;
- контроллера напряжения.
Электроды
Выбор электродов определяется на основе рабочих режимов резки, типа металла, требований к качеству работ. Для эксплуатации в небольших мастерских рекомендуется приобретать гафниевые электроды. Бериллиевые или ториевые могут формировать токсичные соединения.
Компрессор и кабель шланги
Модель компрессора подбирается на основе его технических параметров, требований к конструкции плазмореза. Он используется для создания воздушных потоков внутри рабочих каналов, охлаждения компонентов оборудования при непрерывной работе. Для регулировки подачи воздуха на выходе из компрессора устанавливается электрический клапан.
Внутри шлангов размещают кабель, трубку для сжатого воздуха. На массовом кабеле располагают щуп для обеспечения контакта с разрезаемым металлом и поджига стабильной дуги.
Достоинства самодельного аппарата
Преимущества создания плазмореза своими руками:
- простота конструкции;
- лёгкость обслуживания;
- подбор оптимальных параметров оборудования;
- ремонтопригодность.
Самодельные аппараты отличаются высокой скоростью сборки, так как существует много доступных для освоения схем. Они неприхотливы в эксплуатации, позволяют резать практически любые виды металлов, могут быть легко разобраны для транспортировки или хранения.
Сборка
Пошаговая сборка выполняется в такой последовательности:
- К источнику питания подключается кабель питания электродов.
- С компрессором соединяется шланг для подачи сжатого воздуха.
- Кабель массы подключается к соответствующей клемме источника питания.
- Плазмотрон подсоединяется к кабелю и шлангу.
Когда изготовление плазмореза завершено, необходимо убедиться в правильности сборки, плотности контактов, соблюдении правил техники безопасности.
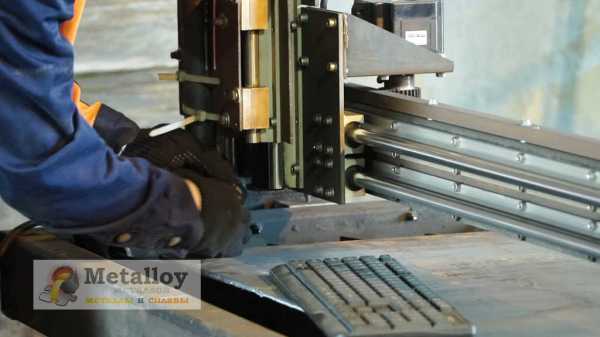
Сборка плазменного резака
Проверка плазмореза
Проверка станка для плазменной резки, изготовленного своими руками, выполняется в несколько этапов:
- принимаются необходимые меры безопасности — одевается защитная одежда, обеспечивается хорошая проветриваемость места, убираются возгораемые материалы;
- подаётся питание на электрод, проверяется формирование дуги, стабильность, размер;
- включается компрессор, подаётся через шланг сжатый воздух, при наличии утечек производится герметизация;
- после формирования плазмы выполняется резка металла толщиной 2 мм — в случае успеха сборка считается завершённой, обнаруженные проблемы устраняются.
Доработка инвертора
Доработать инвертор до плазмореза можно путём подключения в электрическую цепь осциллятора. Существует два способа подсоединения:
- параллельное, используемое для сварки на токах различной величины;
- последовательное, ток сварки ограничен параметрами устанавливаемого блокировочного конденсатора.
Недостатками параллельного подключения являются:
- чтобы получить высокое напряжение, требуется применять осциллятор соответствующей мощности;
- при падении напряжения на обмотке трансформатора, используемого в качестве источника питания, велика вероятность повреждения всех подключённых устройств;
- высокочастотные токи в обмотках трансформатора создают помехи в электросетях.
Выбор подключения зависит от типа свариваемых металлов, их параметров, ограничений подключённого источника питания. То есть учитываются возможные негативные последствия.
metalloy.ru
Рекомендации, как изготовить плазменный резак из инвертора своими руками
Как правило, плазмой листовой металл режется на крупных производствах, и делается это при изготовлении деталей сложной конфигурации. На промышленных станках режутся любые металлы: сталь, медь, латунь, алюминий, сверхтвердые сплавы. Примечательно, что плазменный резак вполне можно сделать собственноручно, хотя возможности устройства в этом случае будут несколько ограниченными. В крупносерийном производстве самодельный ручной плазморез непригоден, но вырезать им детали в своей мастерской, цехе или гараже удастся. В отношении конфигурации и твердости обрабатываемых заготовок ограничений практически нет. Однако они касаются скорости резания, размеров листа и толщины металла.
Описание самодельного плазмореза из инвертора
Плазморез своими руками легче смастерить, взяв за основу инверторный сварочный аппарат. Такой агрегат будет простым по конструкции, функциональным, с доступными основными узлами и деталями. Если какие-то детали не продаются, их тоже можно изготовить самостоятельно в мастерской с оборудованием средней сложности.
Самодельный аппарат не оборудуется ЧПУ, в чем его недостаток и преимущество одновременно. Минус ручного управления в невозможности изготовления двух совершенно одинаковых деталей: мелкие серии деталей в чем-то будут отличаться. Плюс в том, что не придется покупать дорогостоящее ЧПУ. Для мобильного плазмореза ЧПУ не нужно, так как того не требуют выполняемые на нем задачи.
Главные составные части самодельного агрегата:
- плазмотрон;
- осциллятор;
- источник постоянного тока;
- компрессор или баллон со сжатым газом;
- кабели питания;
- шланги подключения.
Итак, сложных элементов в конструкции нет. Однако все элементы должны иметь определенные характеристики.
Источник тока
Плазменная резка требует того, чтобы сила тока была, по крайней мере, как для сварочного аппарата средней мощности. Ток такой силы вырабатывается обыкновенным сварочным трансформатором и инверторным аппаратом. В первом случае конструкция получается условно мобильной: из-за большого веса и габаритов трансформатора ее перемещение затруднено. Вместе с баллоном сжатого газа или компрессором система получается громоздкой.
Трансформаторы имеют невысокий КПД, из-за чего расход электроэнергии при резке металла получается повышенным.
Схема с инвертором несколько проще и удобнее, а еще более выгодна в плане затрат энергии. Из сварочного инвертора выйдет довольно компактный резак, который разрежет металл толщиной до 30 мм. Промышленные установки режут металлические листы такой же толщины. Плазменный резак на трансформаторе способен разрезать даже более толстые заготовки, хотя подобное требуется не так часто.
Плюсы плазменной резки видны как раз на тонких и сверхтонких листах.
- Гладкость кромок.
- Точность линии.
- Отсутствие брызг металла.
- Отсутствие перегретых зон около места взаимодействия дуги и металла.
Самодельный резак собирается на базе инверторного сварочного аппарата любого типа. Неважно, какое количество рабочих режимов, нужен лишь постоянный ток силой больше 30 А.
Плазмотрон
Вторым по важности элементом является плазмотрон. Плазменный резак состоит из основного и добавочного электродов, первый сделан из тугоплавкого металла, а второй представляет собой сопло, обычно медное. Основной электрод служит катодом, а сопло – анодом, и во время работы это – обрабатываемая токопроводящая деталь.
Если рассматривать плазмотрон прямого действия, дуга возникает между заготовкой и резаком. Плазмотроны косвенного действия режут плазменной струей. Аппарат из инвертора рассчитан на прямое действие.
Электрод и сопло являются расходными материалами и заменяются по мере износа. Кроме них, в корпусе имеется изолятор, который разделяет катодный и анодный узлы, еще есть камера, где вихрится подаваемый газ. В сопле, коническом или полусферическом, сделано тонкое отверстие, через которое вырывается газ, раскаленный до 3000-5000°C .
В камеру газ поступает из баллона или подается из компрессора по шлангу, который совмещен с кабелями питания, образующими пакет из шлангов и кабелей. Элементы соединены в изоляционном рукаве либо соединены жгутом. Газ идет в камеру через прямой патрубок, который находится сверху или сбоку вихревой камеры, обеспечивающей перемещение рабочей среды лишь в одну сторону.
Принцип работы плазмотрона
Газ, поступающий под давлением в пространство между соплом и электродом, проходит в рабочее отверстие, удаляясь после в атмосферу. С включением осциллятора – устройства, которое вырабатывает импульсный высокочастотный ток, – между электродами появляется предварительная дуга и нагревает газ в ограниченном пространстве камеры сгорания. Поскольку температура нагрева очень высокая, газ превращается в плазму. В этом агрегатном состоянии ионизированы, то есть электрически заряжены, практически все атомы. Давление в камере резко повышается, и газ вырывается наружу раскаленной струей.
При поднесении к детали плазмотрона возникает вторая, более мощная, дуга. Если сила тока осциллятора – 30-60 А, рабочая дуга возникает при силе в 180-200 А. Она дополнительно разогревает газ, разгоняющийся под действием электричества до 1500 м/с. Комбинированное действие плазмы высокой температуры и скорости движения режет металл по тончайшей линии. Толщину разреза определяют свойства сопла.
Плазмотрон косвенного действия работает иначе. Роль главного анода в нем играет сопло. Из резака вместо дуги вырывается струя плазмы, режущая не токопроводящие материалы. Самодельное оборудование данного типа работает крайне редко. В связи со сложностью устройства плазмотрона и тонких настроек сделать его в кустарных условиях практически невозможно, хотя чертежи найти нетрудно. Он работает под высокими температурами и давлениями и становится опасным, если что-то сделано неправильно!
Осциллятор
Если некогда заниматься сборкой электрических схем и поиском деталей, возьмите осцилляторы заводского изготовления, к примеру, ВСД-02. Характеристики этих устройств более всего подходят для работы с инвертором. Осциллятор подсоединяется в схему питания плазмотрона последовательно или параллельно, в зависимости от того, что диктует инструкция конкретного прибора.
Рабочий газ
Перед тем, как приступить к изготовлению плазмореза, продумайте сферу его применения. Если предстоит работа исключительно с черными металлами, обойтись можно одним лишь компрессором. Для меди, латуни и титана потребуется азот, а алюминий режется в смеси азота с водородом. Высоколегированные стали режут в аргоновой атмосфере, здесь аппарат рассчитывают и под сжатый газ.
Транспортировка устройства
Ввиду сложности конструкции устройства и многочисленности составляющих его компонентов, аппарат плазменной резки трудно разместить в ящике или переносном корпусе. Рекомендуется использовать складскую тележку для перемещения товаров. На тележке компактно расположится:
- инвертор;
- компрессор или баллоны;
- кабельно-шланговая группа.
В пределах мастерской или цеха с перемещением проблем не будет. Когда аппарат потребуется транспортировать на какой-либо объект, он загружается в прицеп легковой машины.
tokar.guru
Плазмотрон своими руками —
Главная страница » Своими руками » Плазмотрон своими руками
Принцип работы любого плазмотрона достаточно прост, и настолько, что изготовить его своими руками не составит большого труда. Между катодом, который необходимо изготавливать из тугоплавких материалов, и охлаждаемым анодом образуется электрическая дуга. Образующий плазму газ (рабочее тело) продувается через дугу. В процессе происходит ионизация рабочего тела, и на выходе из плазмотрона получаем плазму, четвертое агрегатное состояние материи. В зависимости от интенсивности продувки рабочего тела и от вида рабочего тела, в роли которого может выступать обычный воздух, пары спирта или воды или другая жидкость, плазмотроном можно выполнять работы по резке или свариванию металла.
Основные моменты изготовления плазмотрона
- Обычно изготовленный плазмотрон своими руками имеет анод, изготовленный из меди с диаметром отверстия сопла от 1,8 и до 2мм. Анодный блок собирается из двух деталей при помощи пайки, которую необходимо выполнять с высоким качеством, исключая зазоры, так как половинки деталей образуют полость, в которую подается охлаждающая жидкость. В качестве охлаждающей жидкости для самодельного плазмотрона используют обычно тосол или воду. Для увеличения мощности аппарата вдоль сопла необходимо поставить электромагнитную катушку, которая стабилизирует поток плазмы по оси и уменьшает износ анода. Узнать больше про сопло плазмореза (анод).
- В качестве катода для плазмотрона легко можно приспособить вольфрамовый стержень сварочного электрода с диаметром 4мм, если его предварительно заострить. Охлаждение катод получает от потока рабочего тела с давлением 0,5-1,5атм. Электропитание подается на анод непосредственно по трубкам системы охлаждения, а на катод – через прикрепленный к держателю провод. В качестве балластного сопротивления можно использовать любые бытовые электронагревательные приборы с мощностью 3-5кВт. Узнать больше про электрод плазмореза (катод).
- Зажигание дуги (запуск) осуществляется закручиванием ручки подачи катодного стержня до момента его соприкосновения с анодом, после чего катод необходимо сразу же отвести от анода на расстояние 2-4мм (около двух оборотов ручки), а дуга между ними остается в зажженном состоянии.
Смотрите также:
Плазменная резка металла
Оборудование для плазменной резки металла
Ручная плазменная резка металла (оборудование)
Установка плазменной резки металла
Комплектующие для плазменной резки
plazmen.ru
схема, видео, самодельный для плазмы
Главная страница » Своими руками » Плазморез » Осциллятор
Осциллятор для плазмореза — это устройство для бесконтактного возбуждения дуги и стабилизации её горения. Эти опции он получает благодаря преобразованию параметров электроэнергии.
Самодельный осциллятор для плазмореза: немного теории
Внешний вид электронного блока осциллятора заводского изготовления представлен на рисунке.
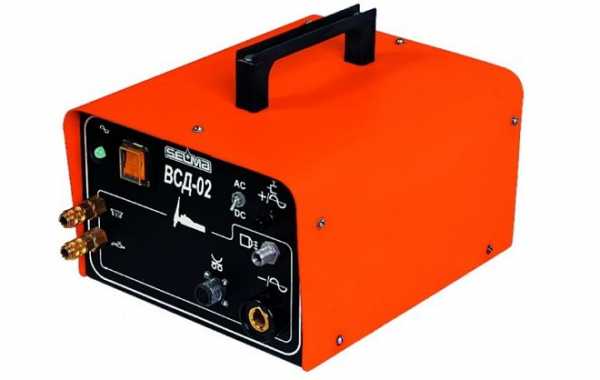
Сварочный осциллятор марки ВСД-02, используемый для стабилизации горения дуги. Ист. http://met-all.org/oborudovanie/svarochnye/svarochnyj-oscillyator-svoimi-rukami.html.
Современные осцилляторы делятся на два класса действия:
- непрерывного действия. Этот класс к сварочному току добавляется ток высокой частоты (150…250 КГц) и с большим значением напряжения (3000…6000 В). В таких условиях дуга будет зажигаться даже без прикосновения электрода к поверхности соединяемых заготовок. Более того, она будет гореть очень устойчиво даже при небольших значениях сварочного тока (благодаря высокой частоте тока, вырабатываемого осциллятором). И, что тоже не маловажно, электроэнергия с такими характеристиками не опасна для здоровья рабочего, работающего на этом устройстве;
- импульсные. Электрическая схема этого класса может предусматривать его параллельное или последовательное подключение.
Примеры электрических схем указаны на рисунке.
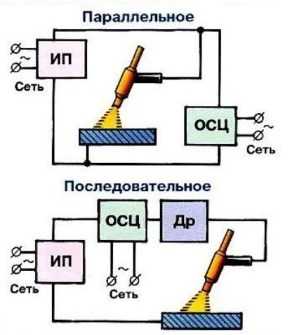
Параллельное и последовательное подключение осциллятора. Ист. http://met-all.org/oborudovanie/svarochnye/svarochnyj-oscillyator-svoimi-rukami.html.
Большую эффективность имеет устройства, которые подключены к электрической цепи плазмореза последовательно. Объясняется это тем, что в их схеме не применяется, за ненадобностью, защита от высокого напряжения. Применение осциллятора, кроме того, позволяет расширить опции плазмореза и обрабатывать «проблемные» металлы или сплавы:
- алюминий;
- «нержавейка» и т. п.
Осциллятор для плазмореза своими руками
Осциллятор, который при желании нетрудно изготовить своими руками, чаще всего, относится к устройствам непрерывного действия. Рассмотрим конструкцию гаджета.
В общем случае осциллятор состоит из следующих основных узлов:
- колебательный контур. Он играет роль искрового генератора затухающих колебаний. Колебательный контур состоит из следующих компонентов:
- накопительный конденсатор;
- катушка индуктивности. Её роль выполняет, как правило, обмотка высокочастотного трансформатора;
- разрядник;
- дроссельные катушки;
- трансформатор высокой частоты.
Если у вас есть необходимый инструмент, навыки работы с электронной техникой и желание собрать осциллятор для плазмореза своими руками, то вам предстоит собрать и настроить указанные выше узлы.
Схема
Чтобы было понятно, что вы будете создавать, расскажем, в общих чертах, о принципе действия осциллятора. Сетевое напряжение после повышающего трансформатора поступает на конденсатор колебательного контура и заряжает его. Когда конденсатор зарядился до оптимального значения, предусмотренного параметрами электросхемы, происходит его разряд через разрядник (пробой воздушного зазора).
Внешний вид самодельного разрядника приведён на рисунке.

Самодельный одноискровый разрядник. Ист. http://met-all.org/oborudovanie/svarochnye/svarochnyj-oscillyator-svoimi-rukami.html.
Импульс, возникший в этот момент на разряднике, возбуждает колебания в колебательном контуре (колебания представляют собой обмен энергией между ёмкостью конденсатора и индуктивностью обмотки высокочастотного трансформатора). В колебательном контуре возникают затухающие высокочастотные электрические колебания, соответствующие его резонансной частоте.
В момент резонанса на обкладках конденсатора колебательного контура образуется высокое напряжение (величина зависит от добротности «Q» колебательного контура), которое через разделительный конденсатор и обмотку катушки поступает на резак и производит поджиг. Параметры разделительного конденсатора подбираются таким образом, чтобы его реактивное сопротивление препятствовало прохождению тока низкой (сетевой) частоты и не препятствовало высокой частоте.
Вот один из вариантов принципиальной электрической схемы самодельного осциллятора.
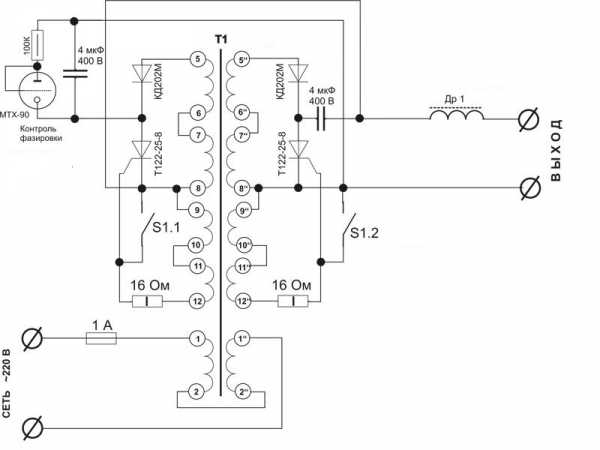
Принципиальная электрическая схема осциллятора, который можно собрать своими руками. Ист. http://ismith.ru/welding-equip/svarochnyj-oscillyator-svoimi-rukami/.
Пояснения к схеме:
1. Назначение индикатора «МТХ-90». В момент разряда накопительного конденсатора (при условии правильного подключения всего устройства) светится табло «Контроль фазировки».
2. S1- выключатель дугообразователя;
3. Дроссель Др1 представляет собой катушку из 15 витков провода сечением 2,5 кв. мм, намотанную на кольце R40 х 25 х 80 из феррита с магнитной проницаемостью M2000HM.
4. Т1 – импульсный трансформатор генератора строчной развёртки (на сленге — «строчник») типа «ТС180-2».
Большим «плюсом» этой электрической схемы служит тот факт, что для её реализации не требуются какие-либо дефицитные или дорогостоящие детали (материалы).
Следует учесть, что осциллятор в процессе работы, благодаря разряднику, создаёт большие электропомехи. Для их нейтрализации, необходимо осуществлять монтаж всех компонентов в «глухом» металлическом корпусе.
Пример конструкции приведён на рисунке.
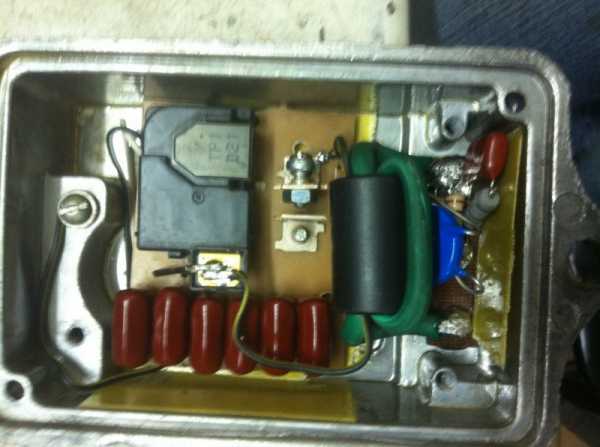
Пример монтажа осциллятора в «глухом» корпусе. Ист. http://m.radiokot.ru/forum/viewtopic.php?f=11&t=115840.
Настройка осциллятора должна осуществляться с тем плазморезом, с которым он будет в дальнейшем работать. Заключается она в подборе опытным путём терристоров. Ориентироваться следует на устойчивость сварочной дуги.
Внимание! При настройке и последующей работе с осциллятором следует строго соблюдать правила техники безопасности при работе с электроприборами. Гаджет – устройство непрерывного действия с импульсным питанием, и на его выходных контактах остаётся напряжение после отключения питания от сети.
Видео
Посмотрите небольшой ролик с описанием одного из вариантов осциллятора своими руками:
Полезная информация по теме:
Теперь, когда вы знаете, как сделать осциллятор для плазмы, будет легче сделать плазморез своими руками.
Рекомендуем ознакомиться и с другими материалами раздела «Своими руками» на нашем сайте.
Также вам может понадобиться для приобретения деталей и расходников список адресов и телефонов в разных городах, где можно приобрести комплектующие для плазменной резки.
Может быть, вам будет полезен также раздел контактов сервисных центров по плазменному оборудованию в разных городах.
plazmen.ru