Техническое обслуживание, ремонт и неисправности компрессора ГАЗ-66
На автомобилях ГАЗ-66 установлен компрессор (рис. 1), предназначенный для накачки шин воздухом
Компрессоры автомобилей с системой регулирования давления в шинах (ГАЗ-66-01, ГАЗ-66-02, ГАЗ-66-04, ГАЗ-66-05) отличаются от компрессоров автомобилей без этой системы (ГАЗ-66 и ГАЗ-66-03) тем, что в резьбовое отверстие головки компрессора над впускным клапаном вместо заглушки ввернут разгрузочный цилиндр (рис. 2).
Компрессор поршневого типа, одноцилиндровый, с воздушным охлаждением приводится во вращение через шкив вместе с насосом гидроусилителя рулевого управления двумя ремнями от шкива коленчатого вала двигателя.
На шлицах коленчатого вала компрессора установлена муфта включения компрессора.
Муфта перемещается вилкой, укрепленной на валике, положение которого фиксируется шариковым фиксатором.
Воздух в компрессор поступает от воздушного фильтра двигателя, К компрессору смазка поступает от двигателя автомобиля.
Периодически проверять натяжение ремней компрессора. Натяжение ремней осуществляется наклоном насоса гидроусилителя рулевого управления.
Угол наклона насоса должен обеспечить заливку масла до метки «уровень масла» на бачке насоса, а при отсутствии метки — до заливного фильтра бачка.
Если наклоном не обеспечивается натяжение ремней, то переставить насос.
При очень большой вытяжке ремней переставить и кронштейны насоса на дополнительные отверстия в них.
Натяжение считается нормальным, если при нажатии пальцем на ремни между шкивами насоса и коленчатого вала двигателя ремни прогнутся на 15—20 мм.
Неисправности компрессора и способы их устранения
— Причины неисправности
Способы устранения
Пониженная производительность:
— Утечка воздуха через клапаны или поршневые кольца
Отремонтировать компрессор
— Засорение воздушного фильтра компрессора (для автомобилей без системы регулирования давления в шинах)
Промыть набивку фильтра
— Слабое натяжение ремней привода
Отрегулировать натяжение ремней
Компрессор перегревается:
— Плохая подача масла
Прочистить маслопроводы и каналы в крышке картера и коленчатом валу компрессора
— Нагар на поршне и поршневых кольцах
Очистить детали от нагара
Выбрасывание масла с нагнетаемым воздухом:
- — Износ поршневых колен или цилиндра
- — Нарушение уплотнения подвода масла к компрессору
Отремонтировать компрессор
Заменить уплотнитель 14 (см. рис.1) или заднюю крышку компрессора
— Поломка пружины уплотнителя
Заменить пружину
— Засорение маслоотводящей трубки
прочистить трубку
Повышенный стук компрессора:
— Износ поршней, пальцев или подшипников
Отремонтировать компрессор
Ремонт компрессора
Снятие и разборку компрессора выполнить в следующем порядке.
- — отсоединить трубопроводы отвода и подвода масла, шланг подвода и трубопровод отвода воздуха. Снять компрессор с двигателя, после чего его разобрать
- — снять шкив 10 (рис. 1) компрессора с подшипниками в сборе;
- — отвернуть стопорный винт вилки компрессора, вынуть валик 7 и вилку 8 включения компрессора;
- — снять муфту 9 включения компрессора;
- — снять головку компрессора и кронштейн 12;
- — снять шатунную крышку и вынуть поршень З с шатуном 2 в сборе из цилиндра 4;
- — снять переднюю и заднюю крышки, вынуть уплотнитель 14 и пружину 13 из гнезда коленчатого вала;
- — снять цилиндр компрессора;
- — спрессовать подшипники коленчатого вала и вынуть коленчатый вал 1;
- — отвернуть пробку 8 (см.
рис. 2) нагнетательного клапана, снять пружину 9 и клапан 10;
- — вывернуть седло 11;
- — отвернуть корпус клапана 14 и вынуть пружину 13, клапан 12 и седло 15 клапана;
- — отвернуть заглушку 6 (см. рис. 1) или разгрузочный цилиндр; вынуть поршневой палец и отъединить поршень от шатуна;
- — снять поршневые кольца.
Проверка технического состояния и ремонт деталей компрессора
После разборки компрессора для устранения какой-либо неисправности проверить техническое состояние основных его деталей.
Если износ цилиндра превышает допустимый или его зеркало повреждено, отремонтировать цилиндр под один из ремонтных размеров, указанных в табл. 2.
Соответственно этим размерам выпускаются поршни и поршневые кольца ремонтных размеров.
Группа ремонтного размера поршня указана цифрами на днище поршня: «+ 0,4», «+ 0,8».
Поршневые кольца ремонтного размера имеют маркировку:
— одна полоса шириной 10 мм соответствует увеличению диаметра кольца по сравнению с номинальным на 0,4 мм и две полосы — на 0,8 мм.
При ремонте коленчатого вала использовать вкладыши ремонтных размеров, толщина которых увеличена на 0,15 и на 0,3 мм.
Группа ремонтного размера вкладыша указана цифрами на его наружной стороне: «—0,3» и «—0,6» (эти вкладыши имеют соответственно толщину 1,9-0,013 и 2,05-0,013 мм).
При обнаружении на пластинчатых клапанах головки цилиндра забоин или кольцевых канавок их заменить и притереть новые клапаны к седлам для получения непрерывного кольцевого контакта.
Поршневые пальцы, поршни и шатуны разбивают на четыре группы, которые сортируют по диаметрам сопрягаемых поверхностей через 0,003 мм (табл. 3).
Места маркировки:
- — поршня — на бобышке под палец;
- — поршневого пальца — на заглушке пальца;
- — шатуна — на головке под поршневой палец.
При сборке допускается установка пальца и шатуна соседней группы.
Пальцы к шатуну и поршню подбирают без смазки при температуре 10-30°С. Правильность подбора поршневого пальца к втулке шатуна проверяют на ощупь.
При нажатии большим пальцем руки поршневой палец без смазки должен с некоторым сопротивлением перемещаться во втулке верхней головки шатуна.
Сборка компрессора
При сборке поршня с комплектом палец—шатун смазать палец чистым моторным маслом.
При установке новых колец проверить зазор замка после установки в цилиндр.
Зазор должен быть равен 0,20—0,40 мм, а кольцо должно плотно прилегать к цилиндру по всей окружности (проверить на просвет).
Проверить соответствие высоты кольца и канавки поршня, зазор между стенкой канавки и кольцом должен находиться в пределах 0,035—0,080 мм.
Если зазор меньше и кольцо не прокатывается по всей канавке поршня, торец кольца можно слегка сточить на самой мелкой наждачной бумаге.
Компрессионные кольца устанавливать в канавках поршня выточками вверх, а стыки их разводить на 180°.
В процессе сборки компрессора проверить легкость вращения коленчатого вала.
Момент, необходимый для его проворачивания не должен превышать; 0,2 кГм — до установки шатунно-поршневой группы и 0,3 кГм — после установки этой группы и затяжки шатунных болтов (но до установки головки).
При постановке седла впускного клапана следить, чтобы более узкий поясок седла был обращен к клапану.
Через верхнее отверстие головки проверить ход клапана, который должен быть в пределах 0,7—1,5 мм, а нагнетательного клапана в пределах 1,5—3,2 мм.
Испытания компрессора после ремонта. Испытания должны включать приработку (без нагрузки), испытания на производительность, испытания на герметичность и проверку работы разгрузочной системы.
Приработку компрессора проводят в течение 20 мин при 1200 — 1350 об/мин коленчатого вала.
Давление масла, поступающего в компрессор, должно быть 1,5—3,0 кГ/см2, температура не ниже +40˚С.
Напор воздуха, охлаждающего компрессор, должен обеспечивать температуру головки компрессора не выше 90˚.
Испытание на производительность проводят при 1200 — 1350 об/мин коленчатого вала и при нагнетании воздуха в резервуар емкостью 23 л.
При давлении в резервуаре 6,5 кГ/см2 полость резервуара сообщается с атмосферой калиброванным отверстием диаметром 1,0 и длиной 3 мм; в данных условиях компрессор должен поддерживать давление в резервуаре не менее 6 кГ/см2 при непрерывной работе в течение 3 мин.
При указанном режиме работы компрессора выбрасывание масла с нагнетаемым воздухом не должно превышать 1 см3 за 5 мин.
Герметичность проверяют на неработающем компрессоре подводом воздуха под давлением 5 — 5,5 кГ/см2 к нагнетательному патрубку головки компрессора из резервуара емкостью 1 л.
Падение давления в баллоне должно быть не более 0,3 кГ/см2 в течение 1 мин.
Работу разгрузочной системы (для компрессоров с разгрузочным цилиндром) проверяют подачей сжатого воздуха под давлением 5—5,5 кГ/см2 в разгрузочный цилиндр.
При этом поршень разгрузочного цилиндра должен опуститься и полностью открыть впускной клапан.
Одновременно проверяют герметичность уплотнения поршня разгрузочного цилиндра.
Падение давления в резервуаре емкостью 1 л и при давлении 5 — 5,5 кГ/см2 не должно превышать 0,25 кГ/см2 в течение 1 мин.
При снятии давления поршень под воздействием возвратной пружины должен четко возвратиться в исходное положение.
Таб. 2 Номинальный и ремонтные размеры цилиндра и поршня компрессора, мм |
|||
---|---|---|---|
Наименование размера |
Отклонение от номинального размера |
диаметр |
|
Цилиндра |
поршня |
||
номинал |
0,0 |
60+0,030 |
60-0,030 |
1-й ремонт |
+0,4 |
60,4+0,030 |
60,4-0,030 |
2-й ремонт |
+0,8 |
60,8+0,030 |
60,8-0,030 |
Таб. |
||||
---|---|---|---|---|
Номер группы |
Цвет маркировки |
Диаметр сопрягаемых деталей |
||
поршень |
Поршневой палец |
шатун | ||
I |
белый |
12,503—12,500 |
12,500—12,497 |
12,507—12,504 |
II |
зеленый |
12,500—12,497 |
12,497—12,494 |
12,504—12,501 |
III |
Синий |
12,497—12,494 |
12,494—12,491 |
12,501—12,498 |
IV |
Красный |
12,494—12,491 |
12,491—12,488 |
12,498—12,495 |
Места маркировки: поршня — на бобышке под палец; поршневого пальца — на заглушке пальца; шатуна — на головке под поршневой палец.
1.4. ГАЗ. Эксплуатация, обслуживание и ремонт автомобилей ГАЗ-53А и ГАЗ-66. Смазка автомобиля ГАЗ-66 — «ВАЖНО ВСЕМ»
1. Технические данные и эксплуатация1. Технические данные и эксплуатация 1.1. Общие технические данные. 1.2. Виды и периодичность технического обслуживания. 1.3. Смазка автомобиля ГАЗ-53А. 1.3.1. Смазка кабины автомобиля ГАЗ-53А. 1.4. Смазка автомобиля ГАЗ-66.
2. Двигатель
2. Двигатель
2.1. Техническое обслуживание двигателя.
2.2. Неисправности двигателя и способы устранения.
2.3. Ремонт двигателя.
2.3.1. Разборка двигателя.
2.3.2. Очистка деталей.
2.4. Ремонт отдельных деталей и узлов. Кривошипно-шатунный механизм.
2.4.1. Ремонт отдельных деталей и узлов. Газораспределительный механизм.
2.4.2. Ремонт отдельных деталей и узлов. Система смазки.
2.4.3. Ремонт отдельных деталей и узлов. Система охлаждения.
2.4.4. Ремонт отдельных деталей и узлов. Система питания.
2.5. Сборка двигателя.
2.5.1. Размеры основных деталей, зазоры и натяги в сопряжении.
2.6. Приработка и приёмка двигателя.
3. Сцепление. Техническое обслуживание. 3.1. Неисправности сцепления и их устранение. 3.2. Ремонт сцепления.
4. Коробка передач4. Коробка передач. Техническое обслуживание. 4.1. Неисправности и их устранение. 4.2. Ремонт коробки передач. Снятие и разборка. 4.2.1. Определение технического состояния деталей. 4.3. Сборка коробки передач. Установка на автомобиль.
5. Раздаточная коробка ГАЗ-66
5. Раздаточная коробка ГАЗ-66
5.1. Техническое обслуживание.
5.2. Ремонт раздаточной коробки. Разборка и определения тех.состояния деталей.
5.3. Ремонт раздаточной коробки. Сборка и регулировка раздаточной коробки.
6. Карданная передача 6.1. Тех.обслуживание карданной передачи. Неисправности и устранение. 6.2. Ремонт карданной передачи. Балансировка, замена кардана и подшипников.
7. Задний и передний мосты7. Задний и передний мосты 7.1. Задний мост. 7.1.1. Тех.обслуживание заднего моста. Неисправности и устранение. 7.2. Ремонт заднего моста. Разборка. 7.2.1. Ремонт заднего моста. Определение тех.состояния деталей. 7.2.2. Ремонт заднего моста. Сборка заднего моста, дифференциала и редуктора. 7.2.3. Ремонт заднего моста. Регулировка заднего моста. 7.3. Передний мост. Тех.обслуживание. 7.3.1. Ремонт переднего моста. Ремонт и регулировка. 7.4. Проверка установки передних колёс.
8.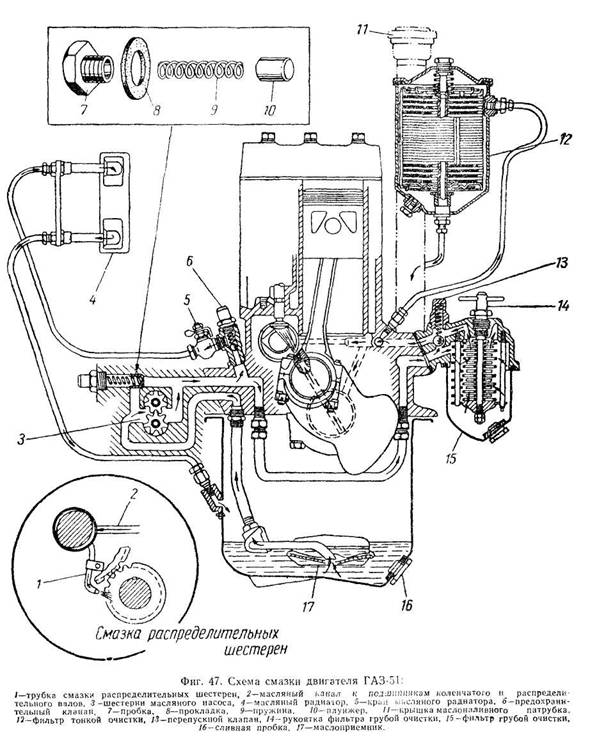
8. Подвеска 8.1. Подвески автомобилей. Тех.обслуживание подвески. 8.1.1. Ремонт подвески. Разборка подвески на узлы и её сборка. 8.1.2. Ремонт подвески. Разборка и сборка рессоры. 8.1.3. Ремонт подвески. Амортизатор. Ремонт амортизатора. 8.2. Передняя ось и рулевые тяги ГАЗ-53А. 8.2.1. Тех.обслуживание передней оси и рулевых тяг. 8.2.2. Ремонт передней оси и рулевых тяг. 8.3. Колёса и шины. Тех.обслуживание колёс и шин. Неисправности. 8.3.1. Ремонт колёс и шин.
9. Рулевой механизм
9. Рулевой механизм
9.1. Рулевой механизм. Техническое обслуживание и неисправности.
9.1.1. Ремонт рулевого механизма.
9.2 Гидроусилитель рулевого управления.
9.2.1. Тех.обслуживание, неисправности гидроусилителя рулевого управления и способы их устранения.
9.2.2. Ремонт гидроусилителя. Насос.
9.2.3. Ремонт гидроусилителя. Клапан управления.
9.2.4. Ремонт гидроусилителя. Силовой цилиндр.
10. Тормоза 10.1. Ножной тормоз. Неисправности и их устранение. 10.1.1. Техническое обслуживание. 10.2. Ремонт ножного тормоза. Главный тормозной цилиндр. 10.2.1. Гидровлический привод. Тормозной барабан. Тормозные колодки. 10.2.2. Колёсный тормозной цилиндр. 10.2.3. Гидровауукумный усилитель, клапан управления. 10.3. Ручной тормоз. Неисправности и их устранение. 10.3.1. Ремонт ручного тормоза.
11. Вспомогательное оборудование
11. Вспомогательное оборудование
11.1. Коробка отбора мощности ГАЗ-66-02. Тех.обслуживание и неисправности.
11.1.1. Ремонт коробки отбора мощности.
11.2. Лебёдка ГАЗ-66-02. Тех.обслуживание и неисправности.
11.2.1. Ремонт лебёдки.
11.2.2. Карданные валы, промежуточная опора и направляющее устройство троса лебёдки.
11.3. Компрессор. Тех.обслуживание и неисправности.
11.3.1. Ремонт компрессора.
11.4. Система регулирования давления в шинах. Тех.обслуживание и неисправности.
11.4.1. Ремонт системы регулирования давления в шинах.
12. Электросхемы и электрооборудование
12.1. Схемы электрооборудования.
12.2. Аккумуляторная батарея. Тех.обслуживание и неисправности.
12.3. Генератор. Тех.обслуживание и неисправности.
12.3.1. Ремонт и испытание генератор.
12.4. Реле-регулятор. Тех.обслуживание и неисправности.
12.4.1. Ремонт и регулировка реле-регулятора.
12.5. Стартер. Тех.обслуживание и неисправности.
12.5.1. Ремонт и регулировка стартера.
12.6. Прерыватель-распределитель. Тех.обслуживание и неисправности.
12.6.1. Ремонт прерывателя-распределителя.
12.7. Катушка зажигания. Свечи зажигания. Провода высокого напряжения. Включатель зажигания. Тех.обслуживание и неисправности.
12.8. Фары. Указатели поворотов. Переключатели и включатели освещения. Тех.обслуживание и неисправности.
12.9. Сигнал. Стеклоочиститель. Тех.обслуживание и неисправности.
12.10. Отопитель. Предохраниетели. Спидометр. Тех.обслуживание и неисправности.
13. Кабина. Платформа 13.1. Кабина ГАЗ-53А. 13.1.1. Установка дверей, стекла, сидений. 13.2.Кабина ГАЗ-66. 13.2.1. Установка и регилировка элементов кабины. 13.3. Платформа автомобиля ГАЗ-66.
14. Приложение14. Приложение 14.1. Подшипники ГАЗ-53А и ГАЗ-66. 14.2. Манжеты (сальники) ГАЗ-53А и ГАЗ-66.
ФОРУМ ГАЗ
Смазывать автомобиль надо своевременно, применяя масла, указанные в карте смазки.
Обычно смазку автомобиля совмещают с очередным техническим обслуживанием.
При смазочных работах необходимо соблюдать следующие правила:
- Перед смазкой тщательно удалить.
грязь с пресс-маслёнок, пробок и т. п., чтобы избежать попадания грязи в механизм автомобиля.
- Прессовать рычажно-плунжерным шприцем смазку до тех пор, пока она не покажется из мест стыков деталей узла, подвергающегося смазке.
- После каждой мойки автомобиля обязательно смазывать все шарнирные соединения шасси, так как при мойке смазка вымывается водой.
Сезонные смазки следует менять независимо от пробега автомобиля.
Рис. 5. Места смазки шасси автомобиля ГАЗ-66
№ позиции на рис.5 | Наименование узла | Кол-во точек | Наименование смазок | Периодичность | Рекомендации по смазке | |||||
ЕО | ТО-1 | ТО-2 | ||||||||
1 | Направляющие ролики троса лебёдки (см.![]() |
2 | Солидол УС-2 или УС-1 (ГОСТ 1033 — 51) | + | + | Смазать через пресс-маслёнки | ||||
2 | Редуктор лебёдки (см.эскиз 22) | 1 | Масло МТ-16п (ГОСТ 6360 — 58) | + | Проверить и при необходимости долить до уровня контрольной пробки | |||||
++ | Заменить масло | |||||||||
3 | Шлицы вала барабана лебёдки (см. эскиз 23) | Масло для двигателя | + | + | Смазать из маслёнки | |||||
4 | Карданы валов привода лебёдки (см.![]() |
4 | Летом масло ТАп-15, зимой ТАп-10 (ГОСТ 8412 -57) | + | + | Смазать через пресс-маслёнку до выдавливания смазки из клапана | ||||
5 | Подшипник водяного насоса (см. эскиз 25) | 1 | Смазка 1-13 жировая (ГОСТ 1631 — 61) | + | + | Смазать через пресс-маслёнку до выдавливания свежей смазки из контрольного отверстия | ||||
6 | Валик вилка включения компрессора, подшипник шкива компрессора (см.эскиз 26) | 2 | Солидол УС-2 или УС-1 (ГОСТ 1033 — 51) | + | Смазать через пресс-маслёнки | |||||
7 | Подшипник ступицы передних колёс (см.![]() |
2 | Смазка 1-13 жировая (ГОСТ 1631 — 61) | + | Промыть подшипники и ступицы керосином и заложить в каждую ступицу по 500г смазки | |||||
Шарниры поворотных цапф (см. эскиз 28) | 2 | Смесь 70% солидола УС-2 (ГОСТ 1033 — 51) и 30% масла ТАп-15 (ГОСТ 8412 — 57) | + | Добавить по 200г смазки в каждый шарнир | ||||||
++ | Промыть шарниры в заложить по 500г смазки | |||||||||
8 | Шарниры поперечной рулевой тяги (см.![]() |
2 | Солидол УС-2 или УС-1 (ГОСТ 1033 — 51) | + | + | Смазать через пресс-маслёнки | ||||
9 | Картер двигателя (см. эскиз 4 п.»1.3. ГАЗ-53А и ГАЗ-66. Смазка автомобиля ГАЗ-53А» ) | 1 | Масло АС-8 (ГОСТ 10541 — 63) | + | + | Проверить уровень масла и при необходимости долить | ||||
+ | Заменить масло | |||||||||
10 | Воздушный фильтр карбюратора (см.![]() |
1 | Масло применяемое для двигателя (можно работавшее, но отстоявшееся) | + | Промыть фильтрующий элемент и корпус фильтра керосином. Смочить фильтрующий элемент маслом и дать ему стечь. Залить в ванну чистое масло. При работе в условия сильной запылённости промывать фильтр и заменять масло через день | |||||
11 | Прерыватель-распределитель (см. эскиз 6 п.»1.3. ГАЗ-53А и ГАЗ-66. Смазка автомобиля ГАЗ-53А» ) | валик привода | 1 | Смазка ЦИАТИМ-201 (ГОСТ 6267 — 59) | + | Повернуть крышку колпачковой маслёнки на один оборот | ||||
ось рычага контактов | 1 | Масло применяемое для двигателя | + | Закапать 1 — 2 капли | ||||||
втулка кулачка | 1 | + | Закапать 3 — 4 капли | |||||||
фильц кулачка | 1 | + | Закапать 1 — 2 капли | |||||||
12 | Воздушный фильтр гидровакуумного усилителя тормозов (см.![]() |
1 | Масло для двигателя | + | Фильтрующий элемент промыть в керосине и, дав керосину стечь, окунуть в чистое масло | |||||
13 | Подшипник муфты выключения сцепления (см. эскиз 7 п.»1.3. ГАЗ-53А и ГАЗ-66. Смазка автомобиля ГАЗ-53А» ) | 1 | Смазка 1-13 жировая (ГОСТ 1631-61) | + | + | Выдавить полную заправку маслёнки и заполнить её свежей смазкой | ||||
14 | Игольчатые подшипники карданов (см. эскиз 12 п.»1.3. ГАЗ-53А и ГАЗ-66. Смазка автомобиля ГАЗ-53А» ) | 6 | Масло для коробки передач | + | + | Смазать через пресс-маслёнку до выхода масла из клапана | ||||
15 | Шлицы карданных валов (см.![]() |
3 | Смазка 1-13 жировая (ГОСТ 1631-61) | +++ | Вынуть шлицевую вилку, удалить старую смазку и заложить свежую | |||||
16 | Блоки сальников уплотнительного устройства1(см. эскиз 32) | 4 | Смазка 1-13 жировая (ГОСТ 1631-61) | ++ | Промыть полость около манжет и между ними и заложить свежую смазку | |||||
17 | Картер переднего и заднего мостов | 2 | Масло для гипоидных передач грузовых автомобилей ТС-14,5 с присадкой хлорэф-40 ( ТУ ТНЗ 123 — 68) | + | + | Проверить уровень масла и если требуется долить2 .![]() |
||||
18 | Стержень буксирного устройства | 1 | Солидол УС-2 или УС-1 (ГОСТ 1033 — 51) | + | + | Смазать через пресс-маслёнки при работе автомобиля с прицепом | ||||
+ | Смазать через пресс-маслёнки при работе автомобиля без прицепа | |||||||||
19 | Подшипники ступицы задних колёс2 (см. эскиз 33) | 2 | Смазка 1-13 жировая (ГОСТ 1631-61) | ++ | Промыть подшипники и ступицы керосином и заложить в каждую по 250 г смазки | |||||
20 | Разжимной механизм ручного тормоза (см.![]() |
1 | Солидол УС-2 или УС-1 (ГОСТ 1033 — 51) | ++ | Разобрать рабочий механизм и смазать рабочие детали тонким слоем | |||||
21 | Картер раздаточной коробки (см. эскиз 35) | 1 | Летом масло ТАп-15, зимой ТАп-10 (ГОСТ 8412 — 57) | + | + | Проверить масло и если потребуется долить до уровня контрольной пробки | ||||
++ | Слить отработавшее масло и залить новое до уровня контрольной пробки | |||||||||
22 | Картер коробки передач | 1 | Летом масло ТАп-15, зимой ТАп-10 (ГОСТ 8412 — 57) | + | + | Проверить масло и если потребуется долить до уровня контрольной пробки | ||||
++ | Слить отработавшее масло и залить новое до уровня контрольной пробки | |||||||||
23 | Аккумуляторная батарея | 1 | Вазелин технический (ГОСТ 782 — 59) | Два раза в год клеммы аккумуляторной батареи очищают от окислов и смазывают неконтактные поверхности и межэлементные перемычки | ||||||
24 | Валик рычагом управления раздаточной коробкой (см.![]() |
1 | Солидол УС-2 или УС-1 (ГОСТ 1033 — 51) | + | + | Смазать через пресс-маслёнку | ||||
25 | Шарнир силового цилиндра гидроусилителя рулевого управления (см. эскиз 37) | 1 | Солидол УС-2 или УС-1 (ГОСТ 1033 — 51) | + | + | Смазать через пресс-маслёнку | ||||
26 | Насос гидроусилителя рулевого управления (см. эскиз 38) | 1 | Летом турбинное масло 22 (ГОСТ 32 — 53), зимой — веретённое масло АУ ( ГОСТ 1642 — 50 или ВТУ — 1061) | + | + | Проверить уровень масла в бачке и при необходимости долить.![]() |
||||
27 | Шарнир продольной рулевой тяги (см. эскиз 39) | 2 | Смазка 1 — 13 жировая (ГОСТ 1631 — 61) | + | + | Смазать через пресс-маслёнку | ||||
28 | Шкворни поворотных цапф | 2 | Смесь 70% солидола УС-2 (ГОСТ 1033 — 51) и 30% масла ТАп-15 (ГОСТ 8412 — 57) | + | Смазка через пресс-маслёнка | |||||
++ | Промыть подшипники и заложить свежую смазку | |||||||||
29 | Карданы рулевого вала (см.![]() |
2 | Масло для коробки передач | Смазывать два раза в год (весной и осенью) | ||||||
30 | Картер рулевого механизма (см. эскиз 41) | 1 | Масло ТАп-10 (ГОСТ 8512 — 57) | + | Проверить уровень и при необходимости долить. Один раз в год сменить смазку | |||||
31 | Главный цилиндр гидравлического привода тормозов и сцепления (см. эскиз 42) | 1 | Жидкость для тормозов ГТЖ-22 (ТУ МХП 3959 — 53) | + | Проверить уровень жидкости, он должен быть на 20мм ниже кромки наливного отверстия.![]() |
|||||
+ | Заменить тормозную жидкость | |||||||||
32 | Датчик пневмоцентробежного ограничителя числа оборотов коленчатого вала (см. эскиз 43) | 1 | Масло для двигателя | + | + | Залить в трубку 25 — 30 капель | ||||
33 | Вал барабанной лебёдки (см. эскиз 44) | 2 | Солидол УС-2 или УС-1 (ГОСТ 1033 — 51) | + | + | Смазать через пресс-маслёнку | ||||
Петли дверей кабины | 4 | Солидол УС-2 или УС-1 (ГОСТ 1033 — 51) | Смазать через пресс-маслёнку два раза в год | |||||||
Шарнирное соединение привода стеклоочистителя | Масло для двигателя | + | После смазки муфту рычага повернуть несколько раз относительно держателя рычага | |||||||
Гибкий вал спидометра | Смазка ЦИАТИМ-201 (ГОСТ 6267 — 59) или ГОИ-54П (ГОСТ 3276 — 63) | +++ |
1 Только для автомобилей с системой регулирования давления воздуха в шинах.
2 В картер переднего моста масло заливать на 5 — 6 мм ниже уровня контрольной пробки, а в картер заднего моста — до уровня пробки.
В карте смазки применены следующие условные обозначения : + — смазать при каждом техническом обслуживании ; ++ — смазать через одно техническое обслуживание; +++ — смазать через два технических обслуживания.
Похожие статьи:
ГАЗ. Эксплуатация, обслуживание и ремонт, автомобилей произвоства ГАЗ → 2.3.1. ГАЗ. Эксплуатация, обслуживание и ремонт автомобилей ГАЗ-53А и ГАЗ-66. Разборка двигателя
ГАЗ. Эксплуатация, обслуживание и ремонт, автомобилей произвоства ГАЗ → 2.3.2. ГАЗ. Эксплуатация, обслуживание и ремонт автомобилей ГАЗ-53А и ГАЗ-66. Очистка деталей
ГАЗ. Эксплуатация, обслуживание и ремонт, автомобилей произвоства ГАЗ → 1. 2. ГАЗ. Эксплуатация, обслуживание и ремонт автомобилей ГАЗ-53А и ГАЗ-66. Виды и периодичность технического обслуживания
ГАЗ. Эксплуатация, обслуживание и ремонт, автомобилей произвоства ГАЗ → 2.4.1. ГАЗ. Эксплуатация, обслуживание и ремонт автомобилей ГАЗ-53А и ГАЗ-66. Определение технического состояния и ремонт отдельных деталей и узлов двигателя. Кривошипно-шатунный механизм
ГАЗ. Эксплуатация, обслуживание и ремонт, автомобилей произвоства ГАЗ → 2. ГАЗ. Эксплуатация, обслуживание и ремонт автомобилей ГАЗ-53А и ГАЗ-66. Двигатель
Emkarate RL Lubricant Nu-Calgon
Описание:
Семейство смазочных материалов Emkarate представляет собой широкий спектр холодильных масел на основе эфиров полиолов. Они разработаны специально для использования с хладагентами ГФУ, отвечающими требованиям холодильной промышленности. Эти превосходные характеристики достигаются с помощью базовых жидкостей, специально разработанных для обеспечения оптимальных характеристик при минимальном уровне присадок.
Требования к современным смазочным материалам для компрессоров холодильной техники и кондиционеров очень сложны. Они должны быть совместимы и смешиваться с хладагентами ГФУ, а также должны быть совместимы и смешиваться с ХФУ и ГХФУ, а также минеральными и алкилбензольными маслами. Смазочные материалы на основе сложных эфиров полиолов отвечают этим требованиям, и линейка EMKARATE RL является предпочтительным выбором. В тесном сотрудничестве с производителями компрессоров и систем эти смазочные материалы POE, одобренные OEM, охватывают широкий диапазон вязкости от 7 сСт (35–40 SUS) до 220 сСт (1100 SUS) и подходят для большинства областей применения. Смазки обладают отличной термической и химической стабильностью, совместимы с широким спектром эластомеров, полимерных материалов и других конструкционных материалов. Кроме того, более высокий индекс вязкости указывает на то, что их эффективная вязкость не будет резко меняться при широких колебаниях температуры, наблюдаемых в большинстве типичных систем охлаждения и кондиционирования воздуха. Они являются предпочтительным выбором для обслуживания и модернизации существующего оборудования, а также для зарядки OEM.
Размер упаковки | Номер детали | Дополнительная информация |
---|---|---|
1 кварта | 4314-64 | 32-3МАФ |
1 галлон | 4314-66 | 32-3МАФ |
5 галлонов | 4314-65 | 32-3МАФ |
53 галлона | 4314-67 | 32-3МАФ |
1 галлон | 4313-46 | 22ч |
1 кварта | 4314-44 | 32H |
1 галлон | 4314-46 | 32ч |
5 галлонов | 4314-45 | 32H |
53 галлона | 4314-41 | 32H |
5 галлонов | 4314-62 | 32ХБ |
1 галлон | 4315-46 | 46H |
53 галлона | 4315-41 | 46H |
1 кварта | 4316-44 | 68Х |
1 галлон | 4316-46 | 68Х |
5 галлонов | 4316-45 | 68ч |
53 галлона | 4316-41 | 68Х |
1 галлон | 4316-86 | 68ХБ |
5 галлонов | 4316-85 | 68ХБ |
1 галлон | 4316-76 | 68 л.![]() |
1 галлон | 4316-91 | РЛ85ХБ |
1 галлон | 4317-46 | 100Х |
1 галлон | 4317-66 | 100Е |
1 галлон | 4318-26 | 170Х |
5 галлонов | 4318-25 | 170Х |
1 галлон | 4318-66 | 220Х+ |
5 галлонов | 4318-65 | 220Х+ |
5 галлонов | 4318-75 | 220XL |
Проезд:
Этот продукт должен использоваться в соответствии со следующими указаниями только специалистами HVACR.
- Запустите цикл разморозки на всех испарителях, чтобы максимизировать перемещение (возврат) минерального масла в компрессор.
- Выключите охлаждение и изолируйте компрессор. Удалите хладагент из компрессора через доступные порты, используя соответствующие методы и оборудование для сбора. Оставшаяся часть хладагента CFC останется в остальной части системы.
- Это «время простоя», когда компрессор открыт для атмосферы, обеспечит прогрев масла в компрессоре и облегчит его последующий слив.
- Слейте минеральное масло из компрессора. По возможности слейте масло, оставшееся в других компонентах системы, таких как ресиверы, аккумуляторы и сепараторы. Рекомендуется не торопиться с этим шагом; достаточное время позволит полностью прогреть компрессор, а затем более полно слить минеральное масло из компрессора. Это важно, особенно в среднетемпературных системах, в которых может отсутствовать оттайка горячим газом, электрическая оттайка или подогрев.
- Замените равным объемом (равным тому, что было удалено) утвержденной смазки EMKARATE RL. Заправляйте с помощью соответствующего оборудования (герметичные насосы для охлаждающего масла и т. д.) и процедур.
- Замените фильтр-осушитель.
- С помощью того же ручного насоса (Robinair, Thermal Engineering и т. д.) добавьте дополнительный объем смазки EMKARATE RL (равный 1/2 объема, только что заправленного в компрессоры) в линию жидкости системы после конденсатора, и после приемника, если он есть
- Продолжайте использовать насос, чтобы надлежащим образом ввести эту дополнительную смазку в систему.
- При наличии нескольких испарителей убедитесь, что все автоматические разморозки отключены.
- Повторно заправьте часть фреона, удаленного из компрессора на втором этапе. Опять же, используйте соответствующие методы и оборудование.
- Повторно подайте питание или запустите систему, помня, что в системе имеется примерно 50 % лишней смазки.
Эта дополнительная смазка позволит «очистить» систему или более эффективно очистить ее от оставшегося минерального масла.
- Контролируйте уровень масла в картере компрессора и при необходимости сливайте масло из картера, чтобы поддерживать надлежащий уровень масла. Примерно через 15-30 минут из системы будет слита большая часть лишней смазки, включая большую часть оставшегося минерального масла.
- Через 30-40 минут снова запустите цикл(ы) разморозки, чтобы максимизировать возврат масла в компрессор(ы).
- Обесточить или отключить систему и взять пробу масла из картера компрессора; если компрессоров несколько, возьмите пробу с каждого.
- С помощью рефрактометра Nu-Calgon (P/N 4815-0) проверьте образцы на содержание остаточного минерального масла. Для этого первого теста не следует ожидать, что остаточное минеральное масло автоматически достигнет целевого уровня ≤5%. Если вы берете пробы более чем с одного компрессора, возьмите среднее значение результатов теста.
- Снова изолируйте компрессор и восстановите CFC в компрессоре, снова используя соответствующие процедуры.
- Слейте смазку из компрессора и залейте равный объем той же смазки EMKARATE RL.
- Замените фильтр-осушитель.
- Повторно заправьте часть фреона, удаленного из компрессора на втором этапе. Опять же, используйте соответствующие методы и оборудование.
- Повторно включите или запустите систему и дайте ей поработать, чтобы обеспечить полную циркуляцию смазочно-охлаждающей смеси.
- Проба масла и проверка с помощью рефрактометра.
a) Если остаточное содержание минерального масла ниже 5%, а оно должно быть, выключите систему и соответствующим образом восстановите CFC. Система заправки выбранным хладагентом HFC.
b) Если остаточное содержание минерального масла по-прежнему превышает 5%, а это очень необычно, повторите шаги 15–18 и повторите проверку.
Информация о продукте:
Загрузка литературы
Загрузите бюллетень продукта и другую соответствующую литературу здесь.
- EMKARATE RL32-3MAF 12X1 QT. Бюллетень продукта
- EMKARATE RL32-3MAF 4X1 ГАЛЛОН Бюллетень продукта
- EMKARATE RL32-3MAF 5 ГАЛ. Бюллетень продукта PAIL
- EMKARATE RL32-3MAF, БОЧКА НА 53 ГАЛЛОНА Бюллетень продукта
- EMKARATE 22H 4X1 GALLON CASE Бюллетень продукта
- EMKARATE RL32H QTS 12X1 CASE Бюллетень продукта
- EMKARATE 32H 4X1 GAL CS Product Bulletin
- EMKARATE 32H 5-GAL PL Бюллетень продукции
- БОЧКА EMKARATE 32H 53 ГАЛЛОНА Бюллетень продукта
- EMKARATE RL32HB 5-GAL PL Технический бюллетень
- EMKARATE RL46H 4X1 ГАЛЛОН Бюллетень продукта
- EMKARATE RL46H БОЧКА НА 53 ГАЛЛОНА Бюллетень продукта
- EMKARATE RL68H 12X1 КВАРТАЛ Бюллетень продукта
- EMKARATE RL68H 4X1 GAL CS Product Bulletin
- EMKARATE RL68H 5-GAL PL Бюллетень продукта
- EMKARATE RL 68H БОЧКА 53 ГАЛЛОНА Бюллетень продукта
- EMKARATE RL68HB 4 X 1 GAL CASE Бюллетень продукта
- EMKARATE RL68HB ВЕДРО НА 5 ГАЛЛОНОВ Бюллетень продукта
- EMKARATE 68HP 4X1 GAL CASE Бюллетень продукта
- EMKARATE RL85HB 4 X 1 GAL CASE Бюллетень продукта
- EMKARATE RL100H 4X1 GAL CS Product Bulletin
- EMKARATE RL100E 4X1 CASE Бюллетень продукта
- EMKARATE RL170H 4X1 ГАЛЛОН Бюллетень продукта
- EMKARATE RL170H ВЕДРО НА 5 ГАЛЛ.
Бюллетень продукта
- EMKARATE RL220H+ 4X1 CASE Бюллетень продукта
- EMKARATE RL220H+ 5 галлонов Бюллетень продукта
- EMKARATE RL220XL 5 ГАЛ. Бюллетень продукта
Этикетки
Загрузите файл этикетки продукта в низком разрешении здесь.
Безопасность продукта
- 4314-67_SDS_ENG_v5.0
- 4314-67_SDS_ENG_20211202
- 4314-67_SDS_ENG_20211202
- 4314-67_SDS_ENG_20211202
- 4314-41_SDS_ENG_20211211
- 4314-41_SDS_ENG_20211211
- 4314-41_SDS_ENG_20211211
- 4314-41_SDS_ENG_20211211
- 4314-62_SDS_ENG_20211228
- 4315-41_SDS_ENG_20211228
- 4315-41_SDS_ENG_20211228
- 4316-46_SDS_ENG_20211228
- 4316-46_SDS_ENG_20211228
- 4316-46_SDS_ENG_20211228
- 4316-46_SDS_ENG_20211228
- 4316-86_SDS_ENG_20210409
- 4316-86_SDS_ENG_20210409
- 4316-71_SDS_ENG_20211214
- 4316-91_SDS_ENG_20220104
- 4317-46_SDS_ENG_20211228
- 4317-61_SDS_ENG_20211228
- 4318-21_SDS_ENG_20211202
- 4318-21_SDS_ENG_20211202
- 4318-61_SDS_ENG_20211202
- 4318-61_SDS_ENG_20211202
- 4318-75_SDS_ENG_20211202
- 4313-46_SDS_ENG_20220711
- 4325-62_SDS_ENG_20220908
EMKARATE RL32-3MAF 12X1 QT.
EMKARATE RL32-3MAF 4X1 ГАЛЛОН
EMKARATE RL32-3MAF 5 ГАЛ. ВЕДРО
EMKARATE RL32-3MAF, БОЧКА 53 ГАЛЛОНА
КОРПУС EMKARATE RL32H QTS 12X1
EMKARATE 32H 4X1 GAL CS
EMKARATE 32H 5-GAL PL
EMKARATE 32H БОЧКА 53 ГАЛЛОНА
EMKARATE RL32HB 5-GAL PL
ЭМКАРАТЭ RL46H 4X1 ГАЛЛОН
EMKARATE RL46H БОЧКА НА 53 ГАЛЛОНА
EMKARATE RL68H 12X1 КВАРТАЛ
EMKARATE RL68H 4X1 GAL CS
EMKARATE RL68H 5-GAL PL
EMKARATE RL 68H БОЧКА 53 ГАЛЛОНА
EMKARATE RL68HB 4 X 1 ГАЛЛОННАЯ КОРОБКА
EMKARATE RL68HB ВЕДРО НА 5 ГАЛЛОНОВ
КЕЙС EMKARATE 68HP 4X1 GAL
EMKARATE RL85HB 4 X 1 ГАЛЛОННАЯ КОРОБКА
EMKARATE RL100H 4X1 GAL CS
КОРПУС EMKARATE RL100E 4X1
EMKARATE RL170H 4X1 ГАЛЛОН
EMKARATE RL170H ВЕДРО НА 5 ГАЛЛОВ
EMKARATE RL220H+ 4X1 ЧЕХОЛ
EMKARATE RL220H+ 5 галлонов
EMKARATE RL220XL 5 ГАЛ.
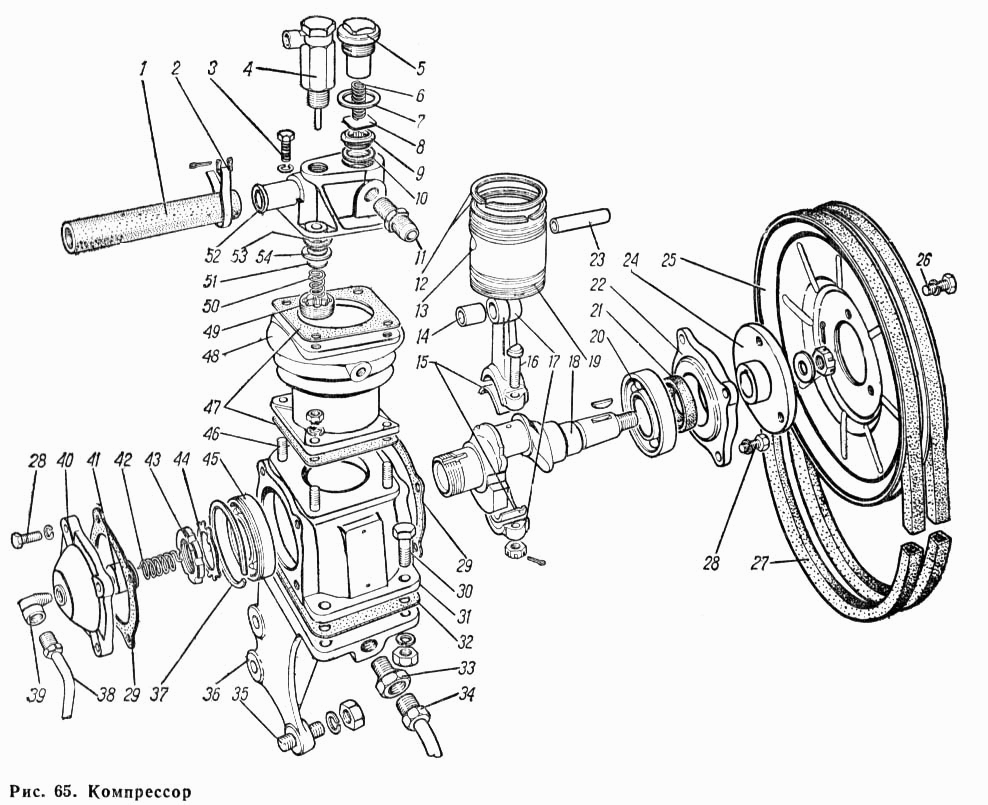
КОРПУС EMKARATE 22H 4X1 ГАЛЛОН
EMKARATE RL46HB ВЕДРО НА 5 ГАЛЛОНОВ
Информация РТК
Компрессоры природного газа и их смазка
G.E. Тоттен, Г.Э. ООО «Тоттен энд Ассошиэйтс»; Роланд Дж. Бишоп, Dow Chemical Company Природный газ широко используется для обогрева домов, выработки электроэнергии и в качестве основного материала для производства многих химических веществ. Природный газ, как и нефтяное масло, находится в больших подземных резервуарах и должен извлекаться из этих подземных ячеек и транспортироваться на перерабатывающие заводы, а затем в распределительные центры для окончательной доставки конечному потребителю.
Газ перемещается с использованием компрессоров многих типов и размеров, которые собирают, сжимают и проталкивают газ по распределительным трубам к различным центрам обработки и точкам использования. Компрессоры, которые перемещают газ, расположены на кораблях и буровых площадках, на химических и технологических заводах, а также в огромном лабиринте труб, образующих распределительную сеть, которая доставляет газ на рынок в чистом, пригодном для использования виде.
В этой статье объясняются различные аспекты газа, смазки газовых компрессоров и компрессоров, включая смазочные материалы для компрессоров, техническое обслуживание жидкостей и некоторые основные рекомендации по анализу отказов компрессоров.
Природный газ и нефтяное масло образовались в результате распада растений и животных, живших на земле миллионы лет назад. Впоследствии разлагающееся вещество оказалось в ловушке в огромных карманах, называемых газовыми резервуарами, в слоях горных пород под землей.
Эти карманы могут содержать преимущественно газ или они могут существовать вместе. Подсчитано, что количество извлекаемого природного газа только в Соединенных Штатах составляет 900 до 1300 триллионов кубических футов (Tcf).
Состав природного газа на устье скважины непостоянен и часто содержит различные составы летучих углеводородов в дополнение к загрязнителям, включая двуокись углерода, сероводород и азот. Промышленный трубопроводный природный газ содержит преимущественно метан и меньшее количество этана, пропана и иногда незначительное количество бутана, как показано в таблице 1.
Для транспортировки и хранения природный газ необходимо сжимать для экономии места. Давление газа в трубопроводах, используемых для транспортировки природного газа, обычно поддерживается на уровне от 1000 до 1500 фунтов на квадратный дюйм. Чтобы обеспечить поддержание этого давления, компрессорные станции размещаются вдоль трубопровода на расстоянии примерно 100 миль друг от друга. Для этого применения требуются компрессоры и смазочные материалы, специально предназначенные для этого использования.
Компрессоры можно разделить на две основные категории: поршневые и роторные. Поршневые компрессоры используются для сжатия природного газа и других технологических газов, когда желаемое давление является высоким, а скорость потока газа относительно низкой. Они также используются для сжатия воздуха.
Поршневые компрессоры
Поршневые компрессоры сжимают газ, физически уменьшая объем газа, содержащегося в цилиндре, с помощью поршня. При уменьшении объема газа происходит соответствующее увеличение давления. Этот тип компрессора называется поршневым. Поршневые компрессоры обычно представляют собой прямоточный процесс. То есть сжатие газа и отделение смазки происходят за один проход.
Поршневые компрессоры могут быть дополнительно классифицированы как одностороннего или двойного действия. Компрессоры одностороннего действия, также классифицируемые как автомобильные компрессоры или тронковые поршневые агрегаты, сжимают газ с одной стороны поршня в одном направлении. Компрессоры двойного действия сжимают газ с обеих сторон поршня.
Для рассмотрения процесса смазки детали, которые необходимо смазывать, удобно разделить на две категории: детали цилиндров и ходовые части. К деталям цилиндров относятся поршни, поршневые кольца, гильзы цилиндров, уплотнения цилиндров и клапаны. Все детали, связанные с ведущей частью (со стороны картера), направляющими крейцкопфа, коренным подшипником и шатуном, подшипниками шатунной шейки и шейки крейцкопфа, являются ходовыми частями.
Уравнение, рекомендованное Scales для оценки количества масла, впрыскиваемого в цилиндр для смазки:
Q = BxSxNx62,8 / 10 000 000
Где: B — размер отверстия (дюймы), S — ход поршня (дюймы), N — скорость вращения (об/мин), а Q — норма использования, выраженная в квартах масла за 24 часа в сутки.
Затем смазка подается непосредственно к цилиндрам и уплотнениям с помощью механического насоса и лубрикатора. В машинах одностороннего действия, которые обычно открыты для картера, для смазки цилиндров используется смазка разбрызгиванием. Клапаны компрессора смазываются распыляемым в системе газосмазочным веществом.
По сравнению со смазкой деталей цилиндра, смазка движущихся частей обычно намного проще, поскольку отсутствует контакт с газом. Производитель оборудования указывает необходимый класс вязкости.
Поскольку температура газа увеличивается с увеличением давления, если тепло не отводится, смазка будет подвергаться воздействию высоких температур и подвергнется серьезному разложению. Поэтому цилиндры компрессора снабжены рубашками охлаждения. Одной из наиболее важных ролей смазки цилиндра компрессора является охлаждающая жидкость.
В качестве хладагента обычно используется вода или водно-гликолевый хладагент. Хотя одна и та же смазка может использоваться для охлаждения как цилиндра, так и движущихся частей, во многих случаях используются разные смазки, потому что смазка цилиндра подвергается воздействию сжатого газа при высоких температурах. Поэтому смазка также должна обладать термической и окислительной стабильностью. В таблице 2 сравниваются рабочие температуры компрессора.
Ротационные компрессоры
Роторные компрессоры классифицируются как объемные или динамические компрессоры. Компрессор прямого вытеснения использует уменьшение объема газа для увеличения давления газа. Примеры компрессоров этого типа включают винтовые, лопастные и пластинчатые компрессоры (рис. 1, рис. 2 и рис. 3).
Рис. 1. Винтовой компрессор |
Рис. 2. Лопастной компрессор |
Рис. 3. Пластинчатый компрессор |
Винтовой компрессор, показанный на рисунке 1, состоит из двух сцепляющихся винтов или роторов, которые улавливают газ между роторами и корпусом компрессора. Двигатель приводит в движение охватываемый ротор, который, в свою очередь, приводит в движение охватывающий ротор. Оба ротора заключены в корпус, снабженный входными и выходными отверстиями для газа. Газ всасывается через входное отверстие в пустоты между роторами. По мере движения роторов объем захваченного газа последовательно уменьшается и сжимается роторами, входящими в зацепление.
Эти компрессоры бывают сухими или мокрыми (заполненными маслом) винтовыми типами. В винтовом типе роторы вращаются внутри статора без смазки (или охлаждающей жидкости). Теплота сжатия отводится за пределы компрессора, что ограничивает его работу до одноступенчатой.
В маслозаполненном винтовом компрессоре смазка впрыскивается в газ, который удерживается внутри статора. В этом случае смазка используется для охлаждения, уплотнения и смазки. Газ удаляется из сжатой газосмазочной смеси в сепараторе. Ротационные компрессоры, такие как винтовой компрессор, непрерывно рециркулируют (от 1 до 8 раз в минуту) смесь смазочного газа для облегчения охлаждения и разделения газа, в отличие от поршневых компрессоров, которые представляют собой прямоточные процессы.
В винтовом компрессоре смазка впрыскивается в корпус компрессора. Роторы подвергаются воздействию смеси газа и смазки. В дополнение к созданию тонкой пленки на роторах для предотвращения контакта металла с металлом, смазка также обеспечивает герметизирующую функцию для предотвращения рекомпрессии газа, которая происходит, когда горячий газ под высоким давлением выходит через уплотнение между роторами или другие зацепления. поверхности и снова сжимается.
Рекомпрессия приводит к тому, что температура газа на выходе превышает расчетный диапазон установки. Это часто приводит к потере пропускной способности и плохой надежности.
Смазка также служит охлаждающей жидкостью, отводя тепло, выделяющееся при сжатии газа. Например, для винтовых воздушных компрессоров температура воздуха на выходе может составлять от 80°C до 110°C (от 180°F до 230°F), что ускоряет окисление из-за турбулентного смешивания горячего воздуха и смазки.
В дополнение к этим функциям необходимо смазывать подшипники на входе и выходе компрессора. В ротационных винтовых компрессорах смазка находится в контакте с газом, сжимаемым при высоких температурах, и испытывает большую силу сдвига между зацепляющимися роторами. Это жесткие условия использования смазочного материала.
Упрощенная диаграмма потока смазки в типичном винтовом компрессоре показана на рис. 4.
Рис. 4. Поток смазки в винтовом компрессоре |
Смазочно-газовая смесь из линии нагнетания компрессора поступает в сепаратор газ/смазка, где сжатый газ отделяется от смазочного материала. После отделения смазка охлаждается и фильтруется, а затем перекачивается обратно в корпус компрессора и подшипники.
Принципиальная схема ротационного лопастного компрессора представлена на рисунке 2. Принцип работы аналогичен роторному винтовому компрессору, за исключением того, что в лопастном компрессоре сопрягаемые лопасти обычно не смазываются для работы с воздухом. При вращении лопастных крыльчаток газ задерживается между лопастными крыльчатками и корпусом компрессора, где газ сжимается за счет вращения лопастей, а затем выпускается. Подшипники и зубчатые колеса смазываются с помощью системы смазки под давлением или поддона.
Ротационно-пластинчатый компрессор схематично показан на рисунке 3. Ротационно-пластинчатые компрессоры состоят из ротора с несколькими скользящими лопастями, эксцентрично установленными в корпусе. При вращении ротора газ втягивается в области увеличивающегося объема (А) и выбрасывается в виде сжатого газа из областей малого объема (В).
Как и в случае с поршневыми компрессорами, смазка пластинчато-роторных компрессоров также является однократной операцией. Смазка впрыскивается в корпус компрессора и выходит со сжатым газом и обычно не рециркулируется. Смазка образует тонкую пленку между корпусом компрессора и скользящими лопастями, а также обеспечивает смазку пазов в роторе для лопастей. Скользящее движение лопастей по поверхности корпуса компрессора требует смазки, способной выдерживать высокое давление в системе компрессора.
Динамический компрессор, такой как центробежный компрессор, показанный на рис. 5, работает по другому принципу.
Энергия от набора лопастей, вращающихся с высокой скоростью, передается газу, который затем выбрасывается в диффузор, где скорость газа снижается, а его кинетическая энергия преобразуется в статическое давление. Одним из преимуществ этого типа компрессора является способность работать с большими объемами газов.
В центробежном компрессоре смазка и газ не соприкасаются друг с другом, что является основным отличием от поршневых, ротационно-винтовых и пластинчато-роторных компрессоров. Требования к смазочным материалам проще, и обычно хорошее масло с ингибиторами ржавчины и окисления обеспечивает удовлетворительную смазку подшипников, шестерен и уплотнений.
Выбор смазки для компрессора зависит от типа и конструкции компрессора, сжимаемого газа, степени сжатия и конечной температуры на выходе. Поршневые компрессоры обеспечивают самые высокие давления газа и являются одними из самых сложных с точки зрения смазки цилиндров и клапанов и надежности оборудования. Однако масла R&O (с защитой от ржавчины и окисления) часто бывает достаточно для смазки разбрызгиванием картера поршневого компрессора.
Ротационные компрессоры с конечным давлением ниже 1 МПа (примерно 145 фунтов на кв. дюйм) смазывать легче. Из-за потенциального контакта лопасти с цилиндром или лопасти с лопастью, винтовые и пластинчатые компрессоры требуют использования масла с защитой от износа (AW). Выбор надлежащего компрессора и смазочного материала с соответствующими физико-химическими свойствами в зависимости от применения имеет жизненно важное значение для успешного процесса и будет полностью рассмотрен во второй части этой серии, состоящей из двух частей, посвященной вопросам смазки газовых компрессоров и компрессоров.
Каталожные номера
- Оценка, полученная на «Неделе природного газа»
- «Учебный курс 2: Для компрессоров природного газа». Уортингтонская компрессия. Корпус-Кристи, Техас.
- Уиллс, Дж. (1980). «Глава 14 — Компрессоры».
Основы смазки. Marcel Dekker Inc., Нью-Йорк, шт. Нью-Йорк, с. 365-394.
- «Учебный курс 1 — Для компрессоров природного газа — Введение в основные функции и компоненты газового компрессорного агрегата». Компрессия Weatherford. Корпус-Кристи, Техас.
- Весы, В. (1997). «Глава 19 — Смазка воздушного компрессора». Справочник по трибологическим данным, под ред. Э. Р. Бузер. CRC Press, Бока-Ратон, Флорида, с. 242-247.
- Коэн, С. (1987). «Разработка синтетического компрессорного масла на основе двухступенчатой гидроочистки нефтяных базовых масел». Смазочная техника, Vol. 44, № 3, с. 230-238.
- Шорт, Г. (1983). «Разработка синтетических смазочных материалов для продления срока службы винтовых компрессоров». Смазочная техника, Vol. 40, № 8, с. 463-470.
- Миллер, Дж. (1989). «Синтетические и компрессорные масла HVI». Дж. Синтез. Смазочная техника, Vol. 6, № 2, с. 107-122.
- Толфа, Дж. (1990). «Синтетические смазочные материалы, пригодные для использования в технологических компрессорах и компрессорах углеводородного газа».